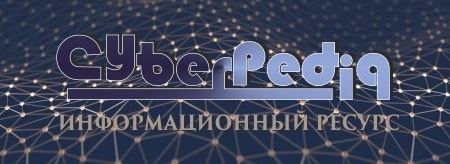
Таксономические единицы (категории) растений: Каждая система классификации состоит из определённых соподчиненных друг другу...
Кормораздатчик мобильный электрифицированный: схема и процесс работы устройства...
Топ:
Основы обеспечения единства измерений: Обеспечение единства измерений - деятельность метрологических служб, направленная на достижение...
Методика измерений сопротивления растеканию тока анодного заземления: Анодный заземлитель (анод) – проводник, погруженный в электролитическую среду (грунт, раствор электролита) и подключенный к положительному...
Интересное:
Как мы говорим и как мы слушаем: общение можно сравнить с огромным зонтиком, под которым скрыто все...
Что нужно делать при лейкемии: Прежде всего, необходимо выяснить, не страдаете ли вы каким-либо душевным недугом...
Подходы к решению темы фильма: Существует три основных типа исторического фильма, имеющих между собой много общего...
Дисциплины:
![]() |
![]() |
5.00
из
|
Заказать работу |
Содержание книги
Поиск на нашем сайте
|
|
Аннотация
В дипломной работе изложено подробное описание структуры кислородного цеха ПАО «НЛМК», в частности особое внимание уделено анализу теплообменного оборудования воздухоразделительной установки “Linde” (ВРУ). Произведен материальный и тепловой баланс основноготеплообменного оборудования. В результате детального изучения технологической схемы был найден участок, анализ которого позволит разработать оптимальный режим работы ВРУ. Был выполнен расчет испарителя азота, а также составлена математическая модель данного испарителя, которая позволяет делать сравнительный анализ режимом работы и выбирать оптимальный. В дипломной работе рассчитаны основные экономические показатели, приведен расчет одного режима работы испарителя азота.
Структура работы представлена введением, 5 главами, заключением, списком литературы.Объем дипломной работы - 50 страниц, на которых размещены 10 рисунков и 3 таблицы. При написании работы использовались 13 источников.
Ключевые слова: блок комплексной очистки, теплообменный аппарат, регенерация.
Графическая часть:
Схема участка БКО ВРУ «Linde»............. А1
Азотный испаритель Е2617………………А1
Графики......................................................А1
Экономическая часть............................... А1
____________________________________
Всего в листах формата А1А1 х 4
Введение
На ПАО «НЛМК» метод получения кислорода для промышленного производства основан на методе ректификации (процессе разделения жидких смесей на их составные части путём многократного испарения жидкости) – глубокого охлаждения. Метод основан на сжижении воздуха путём охлаждения его до температуры кипения и последующего разделения на отдельные составляющие.
На территории комбината кислород транспортируется в различных состояниях и при разном давлении, как один из продуктов процесса глубокого охлаждения. Согласно требуемым параметрам он подается на технологические нужды. Например, для процессов выплавки чугуна и стали, зачистки и резки слитков в сталепрокатном производстве, литейном производстве (для интенсификации процесса горения топлива и повышения температуры нагрева чугуна), а так же для сварки. За пределами ПАО «НЛМК» кислород используется в медицинских целях (создания лекарств от астмы).
Общие сведения о кислородном цехе
Технологический процесс разделения воздуха
Кислородный цех организационно состоит из:
а) кислородного отделения №1;
б) кислородного отделения №2;
в) служба сетей, сооружений и компрессорных станций.
|
Протяжённость сетей трубопроводов по комбинату:
а) сеть трубопроводов для транспортировки кислорода - 76,7 км;
б) сеть трубопроводов для транспортировки сжатого воздуха - 101,4км;
в) сеть трубопроводов для транспортировки азота - 70,7 км;
г) сеть трубопроводов для транспортировки аргона - 28,9 км;
Суммарная протяженность 277,7км.
Кислородный цех один из самых энергоёмких производств комбината, потребляя 33,3% от общего объёма выработки электроэнергии. На ПАО «НЛМК» техника получения кислорода для промышленного производства основана на методе ректификации (процессе разделения жидких смесей на их составные части путём многократного испарения жидкости) – глубокого охлаждения. Метод основан на сжижении воздуха путём охлаждения его до криогенной температуры и последующего разделения на его составляющие.
Технологический процесс разделения воздуха состоит из следующих этапов:
а) очистка воздуха от пыли и других вредностей;
б) сжатие воздуха в компрессорах;
в) очистка сжатого воздуха от двуокиси углерода;
г) осушка сжатого воздуха и очистка его от углеводородов;
д) сжижение и ректификация воздуха для разделения на кислород, азот, аргона, криптон – ксенона, неон – гелия;
е) сбор полученных жидких продуктов разделения;
ж) наполнение газообразными сжатыми продуктами баллонов, подача сжатых продуктов потребителю по трубопроводам и наполнение цистерн жидкими продуктами разделения;
з) очистка редких газов от кислорода и азота и доведением их концентрации до требований ГОСТа и наполнение этих газов в баллоны.
Техническая оснащенность кислородного цеха
Отделение №1оснащено:
Участок разделения воздуха
На участке разделения воздуха функционирует следующее оборудование:
а) блок №1, 2 –установка АКт–30 (30000 м3/ч азота, технологического кислорода 17000 м3/ч, криптоноксенонового концентрата 20-25 м3/ч);
б) блок №4, 5 – установка «Linde» (40000 м3/ч азота, 34000 м3/ч кислорода, 1000 м3/ч аргона, 50 м3/ч криптоноксенонового концентрата, 6 м3/ч неоногелиевой смеси);
|
в) блок №9 – установка АКАр-40 (40000 м3/ч азота, 35000 м3/ч, криптоноксенонового концентра 25-50 м3/ч, неоно-гелиевой смеси 3-6 м3/ч);
г) блок №10– установка КААр-30М (34000 м3/ч кислорода, азота 40000м3/ч, аргона 500-990 м3/ч, криптоноксенонового концентра 25-50 м3/ч, неоногелиевой смеси 3-6 м3/ч);
д) установка очистки аргона от кислорода СОАр.
Участок компрессии воздуха
На участке компрессии воздуха эксплуатируются:
а) 5 компрессоров К-3000-61-1 с приводомот турбины;
б) 4 компрессора К-1500-62-2 с приводом от электродвигателя (ЭД);
в) 2 компрессора К-1700-62-2 с приводом от ЭД.
Участок редких газов
На участке редких газов функционирует:
а) установка УСК-1М для получения криптоноксеноновой смеси;
б) установка обогащения неоногелиевой смеси (УОНГС);
в) наполнители кислорода и аргона.
Основными потребителями кислорода являются: доменный цех-1 (ДЦ-1), доменный цех-2 (ДЦ-2), конвертерный цех-1 (КЦ-1), конверторный цех-2 (КЦ-2), ТЭЦ и др.
Технический кислород от ВРУ кислородного цеха №1 и кислородного цеха №2 поступает на всас кислородных компрессоров КТК – 12,5/35 и ЦКК – 400/40.
Кислород после кислородных компрессоров давлением до 3,2 МПа поступает в кислородо-распределительные пункты №1 и №2 (далее по тексту КРП-1 и КРП-2).
Кислород от КРП-1 давлением 1,7МПа подается в КЦ-1 и давлением 1,5МПа на автогенные нужды газового цеха; ДЦ-1; КЦ-1; коксохимического производства (КХП); КИПиА; теплосилового цеха (ТСЦ); производство горячего проката (ПГП). Технический кислород от КРП-2 давлением 1,6 МПа подается в КЦ-2 и на автогенные нужды КЦ-2, ДЦ-2,ремонтного цеха сталеплавильного оборудования-2 (РЦСО-2), ремонтного цеха прокатного оборудования (РЦПО-1-2), производства холодного проката и покрытий (ПХПП) и прочие.
В ДЦ-1 и ДЦ-2 кислород используется для интенсификации техно-логического процесса.
В КЦ-1 и КЦ-2 кислород нужен для получения стали и чугуна и резки слябов.
Исходные данные для расчета
Теплообменный аппарат (ТОА) это устройство, в котором осуществляется передача теплоты от горячего теплоносителя к холодному (нагреваемому). Теплоносителями могут быть газы, пары, жидкости. В зависимости от назначения теплообменные аппараты используют как нагреватели, испарители и как охладители. В данной выпускной квалификационной работе рассматривается азотный испаритель. В технологической схеме имеет обозначение Е2217. Схематично участок БКО ВРУ «Linde» представлен на рис.1.
Отличие расчета испарителей от расчета теплообменников (нагревате-лей) и холодильников связано в основном с изменением расчета коэффициентов теплоотдачи, поскольку теплообмен сопровождается изменением агрегатного состояния теплоносителей.
|
Рис.1 Схематическое изображение участка БКО ВРУ «Linde»
Подогрев азота на данном этапе технологической схемы ведется с целью его отвода для регенерации адсорберов, заполненных цеолитом. Поглощающая способность цеолитов зависит от адсорбируемого газа; она наименьшая для . Поэтому длительность цикла очистки воздуха и размеры адсорберов при использовании цеолитов определяются степенью очистки воздуха от двуокиси углерода. После насыщения адсорбционную способность цеолитов необходимо восстановить, т.е. провести их регенерацию. Регенерацию адсорбента проводят противотоком.
В целях экономии расхода чистого азота для регенерации цеолитов азот из блока, разделения воздуха поступает в подогреватель регенерирующего газа (E2617) и нагретый в нем до 160°С:170°С направляется на десорбцию цеолита в адсорбер (А2626B или А2626А). Из регенерирующего адсорбера азот выбрасывается в атмосферу, а конденсат перекачивается насосами обратно к источнику (котлу), для повторного превращения в пар.
Давление перегретого пара на входеp=15 кгс/см2;
Температура перегретого пара на входе
Давление конденсата на выходеp=15кгс/см2;
Температура конденсата на выходе
Расход греющий среды
Температура азота на входе
Давление азота на входе p=150мбар;
Температура азота на выходе
Давление азота на выходе p=150мбар;
Расход нагреваемой среды
Участок I:
Участок II:
Участок III:
4)Определим среднюю разность температур:
Для теплоносителя, температура которого изменяется в ТОА на меньшее число градусов, среднюю температуру определяют, как среднее арифметическое между начальной и конечной.
Участок I:
Рис.3. Изменение температур греющей и нагреваемой среды
Пар | 250 |
| 197,4 |
Азот | 165 |
| 156,6 |
Участок II:
Рис.4. Изменение температур греющей и нагреваемой среды
Пар | 197,4 |
| 197,4 |
Азот | 47,6 |
| 156,6 |
Участок III:
Рис.5. Изменение температур греющей и нагреваемой среды
Пар | 197,4 |
| 80 |
Азот | 16 |
| 47,6 |
Решение вопроса о том, какой теплоноситель направить в трубное пространство, обусловлено его температурой, давлением, коррозионной активностью, способностью загрязнять поверхности теплообмена, расходом и др. В рассматриваемом испарители в трубное пространство целесообразно направить теплоноситель с меньшим расходом, т. е. пар. Это позволит выровнять скорости движения теплоносителей и соответствующие коэффициенты теплоотдачи, увеличивая таким образом коэффициент теплопередачи.
5)Определим количество труб в ТОА:
Зададимся скоростью движения в трубах
Суммарная площадь сечения труб тогда будет равна:
|
где, - плотность пара, м3/кг.
Площадь сечения одной трубы:
6)Определим количество труб (n):
Уточним скорость движения в трубах:
7)Произведем расчет коэффициента теплоотдачи для трубного пространства.
Участок I:
Определим число Рейнольдса по формуле:
где,
Т.к. , режим течения турбулентный.
Коэффициент теплоотдачи при движении жидкости в трубах для тур-булентного режима движения найдем из уравнения:
где,
Nu– критерий Нуссельта:
где, - Критерий Прандтля.
Участок II:
Определим число Рейнольдса по формуле:
где,
Т.к. , режим течения турбулентный
Коэффициент теплоотдачи при конденсации насыщенного пара внутри горизонтальных и вертикальных труб определяется по следующему уравнению[3]:
где, - коэффициент теплоотдачи при сплошном потоке конденсата внутри трубы, Вт/(м2 ∙К);
– соответственно плотность пара и жидкости в состоянии насыщения, м3/кг.
Участок III:
Определим число Рейнольдса по формуле:
где,
Т.к. , режим течения турбулентный.
Коэффициент теплоотдачи при движении жидкости в трубах для тур-булентного режима движения найдем из уравнения:
где,
8) Произведем расчет коэффициента теплоотдачи в межтрубном пространстве:
Участок I:
Определим число Рейнольдса по формуле:
Задаемся скоростью азота
где, [5]
Т.к. , режим течения турбулентный.
Коэффициент теплоотдачи при движении жидкости в трубах для тур-булентного режима движения найдем из уравнения:
где,
где, ξ-угол атаки обтекания потока (для шахматного расположения труб =0,6)
Участок II:
Определим число Рейнольдса по формуле:
Задаемся скоростью азота
где,
Т.к. , режим течения турбулентный.
Коэффициент теплоотдачи при движении жидкости в трубах для тур-булентного режима движения найдем из уравнения:
Участок III:
Определим число Рейнольдса по формуле:
Задаемся скоростью азота
где,
Т.к. , режим течения турбулентный.
Коэффициент теплоотдачи при движении жидкости в трубах для тур-булентного режима движения найдем из уравнения:
Примечание:
Задались такими значениями скорости азота, так как с ростом температуры увеличивается и скорость, соответственно падает плотность азота, которая была посчитана для каждого участка:
r1=0,9035м3/кг;r2=1,01337м3/кг;r3=1,285 м3/кг.
9) Определение коэффициента теплопередачи.
где,dср,dвн,dнар – средний, внутренний и наружный диаметры трубы, м;
lст - коэффициент теплопроводности материала трубы, Вт/(м·К);
a1 ,a2 - коэффициенты теплоотдачи для внутренней и внешней стороны трубы, Вт/(с);
Rзаг- термическое сопротивление загрязнений с обеих сторон стенки, (м2·К)/Вт;
При вычислении dср необходимо руководствоваться следующим правилом:
а) если a1 ≥ a2, то dср = dнар;
|
б) если a1 = a2, то dср = 0,5(dнар +dвн);
в) если a1 ≤ a2, то dср = dвн.
Участок I:
=
Участок II:
=
Вт/м2
Участок III:
=
,442
10) Определим площадь поверхности теплообмена
Уравнение теплопередачи служит для определения площади поверхности теплообмена и имеет следующий вид:
Следовательно:
где,k – коэффициент теплопередачи в теплообменном аппарате, Вт/(м2·К);
F – поверхность теплообмена, м2;
Dtср.лог–логарифмический напор, оС.
Участок I:
Участок II:
Участок III:
Определим расчетную площадь поверхности теплообмена по формуле:
∑
11) Определим длину трубы каждого участка:
где, n-число труб в пучке, м;
z-число ходов.
Участок I:
Участок II:
Участок III:
Определим общую длину труб теплообменного аппарата по формуле:
∑
12) Уточним температуру стенки
Температуру стенки определим графическим методом, путем приравнивания тепловых потоков.
Плотность теплового потока одинакова (q=const) следовательно:
qhвн=
qhнар= (
где,
Участок I:
qhвн= 174,088 Вт/м2;
qhнар= (
Вт/м2 .
∆ =
Участок II:
qhвн= 279,614 Вт/м2;
qhнар= (
Вт/м2 .
∆ =
В инженерных расчетах допускается погрешность до 5% от полученного ранее значения. Эта погрешность вызвана неточностью расчета, так как для учета тех или иных параметров мы вводим новые коэффициенты, которые помогают более детально и точно смоделировать исследуемый объект.
Рисунок.6 Графическое решение расчета для участка I
Таблица1.Результаты расчета для участка I
Таблица 2. Результаты расчета для участка II
Участок III:
qhвн= 165,009 Вт/м2;
qhнар= (
Вт/м2 .
∆ =
Таблица 3. Результаты расчета для участка III
Рис.10Графическое решение расчета для участка III
Экономический расчет
Экономический расчет является одним из важнейших, так как именно по данному расчету предприятие принимает решение о замене действующего или внедрение нового технологического оборудования. Если инженеры предлагают решение, которое позволит предприятию извлечь выгоду и не ухудшить технологический процесс, то оно будет непременно рассмотрено.
Произведем расчет приведенных затрат и на основании этих данных, проведя анализ, определим оптимальный вариант компоновки азотного испарителя, включенного в схему технологического цикла ВРУ «Linde».
Для расчета приведенных затрат воспользуемся зависимостью:
где, K– капитальные затраты, руб;
Э – эксплуатационные затраты, руб;
– нормативный коэффициент эффективности(
= 0,4).
Капитальные затраты рассчитываются по следующему уравнению:
![]() | |
![]() |
где – средняя стоимость килограмма труб диаметром 25х2 из стали 12Х18Н10Т, руб/кг
( = 400 руб/кг);
– металлоемкость поверхностей нагрева, кг;
- коэффициент, учитывающий прочие растраты, связанные с дополнительным оборудованием и монтажом (
=1,5);
Металлоемкость оборудования определяется по уравнению, представленному ниже:
![]() |
где, – плотность стали 12Х18Н10Т, кг/м3 (
= 7910 кг/м3).
Эксплуатационные затраты за год рассчитываются по следующей формуле:
![]() |
![]() |
где, - потери мощности потока, Вт;
P – стоимость 1 кВт ч, руб (P = 3,6руб);
Потери мощности потока рассчитываются по формуле:
![]() |
Энергосбережение
Потенциал энергосбережения на металлургических предприятиях заключается втом, что в настоящее время существует значительный физическийизнос основного оборудования и наблюдается существенное колебание работы металлургических комбинатов, связанное с особенностью современногорынка продукции.
Для металлургических заводов вопросы энергосбережения являются одними изосновных для снижения издержек производства и повышенияконкурентоспособности их продукции на рынке.
Металлургическое производство имеет следующую технологическую структуру:
а) производство чугуна:
1) коксохимическое производство;
2) агломерационный цех;
3) доменный цех;
б) производство стали:
1) кислородно-конвертерный цех;
2) мартеновский цех;
3) электросталеплавильный цех;
в) производство проката:
1) обжимной цех;
2) толстолистовой стан;
3)крупносортовой стан;
4) универсальный стан;
Так же, основными подразделениями являются:
а) теплоэлектроцентраль;
б)кислородно-компрессорное производство.
Кислородное отделение является одним из самых энергоёмких производств комбината, потребляя 40% от всего объёма используемой электроэнергии.В настоящее время напредприятиеимеетсябольшое подразделение, которое занимается вопросами по снижению энергетических затрат комбината, без убыли производительности.
Основными положениями повышения энергетической эффективности можно считать:
а) Выполнение комплекса организационно-технических мероприятий, большая частота профилактических ремонтов оборудования, повышение квалификации специалистов и т.п.
Реализация этих мер, как правило, требует малое вложение денежных средств, а окупается достаточно быстро, поэтому ихосуществление является главной задачей.
б) Ремонт, наладка и замена оборудования;
Осуществить работы по изоляции трубопроводов, автоматизациипроцессов подачи воздуха, модернизации основного энергоемкогооборудования, вывод оборудования на режим номинальной производительности и т.п.
в) модернизация системы обеспечения продуктами разделения воздуха с заменой устаревших воздухоразделительных установок на более совершенные;
г) модернизация собственных источников энергии с целью увеличения выработки электроэнергии на заводе.
Охрана труда
Изм. |
Лист |
№ докум. |
Подпись |
Дата |
Лист |
ОГАХ.ДП0.201.000.00.ПЗ |
Для обеспечения взрывобезопасности все усилия направляются на устранение горючих веществ. Примеси являются основной причиной взрыва.
Наиболее опасными из газообразных примесей воздуха являются: аце-тилен, кислородосодержащие углеводороды, сероуглерод. Также к взрыву может привести избыточное количество масла и плохое качество монтажных работ.
Основными способами защиты воздухоразделительных установок от взрыва являются: использование для переработки воздуха с наименьшей степенью загрязнения, очистка перерабатываемого воздуха от взрывоопасных примесей, постоянный контроль за их содержанием, организация режима кипения с необходимой степенью циркуляции.
Периодичность определения концентрации вредных веществ зависит от типа установки и цикла по которому она работает.
Используется также: очистка воздуха от опасных примесей в регенераторах, обеспечение проточности конденсаторов, выпаривание жидкого кисло-рода в выносном конденсаторе змеевикового типа, очистка воздуха методом каталитического окисления. Эти методы также ведут к избавлению вредных примесей и предотвращению взрывов.
Изм. |
Лист |
№ докум. |
Подпись |
Дата |
Лист |
ОГАХ.ДП0.201.000.00.ПЗ |
Требования к помещениям по размещению оборудования
Производство продуктов разделения воздуха должно размещаться в санитарной зоне длиной не менее 50 метров. Цеха разделения воздуха должны быть удалены от других цехов, загрязняющих воздух, на такое расстояние, чтобы в поступающем на переработку воздухе примесей было меньше допустимого предела.
Определение содержания вредных примесей в воздухе производитсякогда расстояние до загрязняющего цеха менее 2км.
Должны быть предусмотрены противопожарные разрывы между зданиями, аппаратами и емкостями для хранения криогенных продуктов. В зависимости от типа криогенного оборудования, здания проектируют 1-2-х этажными без чердачных перекрытий и цокольных этажей. Производственные здания и помещения должны обеспечить наиболее приятную производственную обстановку и устранить пожарную опасность, имея при этом любую форму и размеры. Но, исходя из санитарно-гигиенических условий (освещение, вентиляция) наиболее целесообразными считаются здания, имеющие форму прямоугольника. Конструкция производственных зданий, их протяженность и число этажей определяется технологическим процессом, степенью его пожаробезопасности и взрывоопасности, наличием вредных выделений.
Объём производственных помещений должен быть таким, чтобы на каждого работающего приходилось не менее 15м3, а площадь помещений – не менее4,5м2.Для безопасности движения рабочих и удобства транспортировки грузов в цеха необходимо предусмотреть раздельные входы (въезды) и выходы (выезды) для людей и транспорта. Двери и ворота должны открываться наружу, чтобы в случае массового движения рабочих из помещения двери не являлись препятствием для выхода. На
Изм. |
Лист |
№ докум. |
Подпись |
Дата |
Лист |
ОГАХ.ДП0.201.000.00.ПЗ |
Наружные стены отапливаемых производственных зданий должны иметь такую толщину, при которой исключилась бы возможность конденсации влаги на их внутренних поверхностях. Протяженность пристроенных к производственному помещению со значительными выделениями и естественным воздухообменом не должна превышать 40% от общей протяженности наружных стен донного помещения.
Пожарная профилактика
Протекание технологических процессов в ВРУ не способствует возникновению пожара. Однако,при её эксплуатации могут возникать условия его вызывающие, а именно: неисправность в электропроводке, перегрузки электродвигателей, возгорание промасленной ветоши, проведение сварочных работ при ремонте и др.
Для предотвращения пожара в цеху должны находиться первичные средства пожаротушения и пожарный инвентарь, существовать сигнализация и противопожарное водоснабжение. Степень огнестойкости зданий ВРУ категории «ΙΙа».
4.5. Испытание сосудов работающих под давлением
При конструировании сосудов и аппаратов установки производится расчет на их прочность, в результате которого определяется толщины стенок соcудов, безопасные для заданного внутреннего избыточного давления. Помимо этого на многие такие сосуды распространяются «Правила устройства и безопасной эксплуатации сосудов, работающих под давлением». К сосуду прилагаются: паспорт сосуда; акт удостоверяющий, что монтаж и установка сосуда производится в соответствии с правилами и подписана руководителем пред-приятия-владельца сосуда; схема выключения сосуда с указанием рабочих параметров арматуры и контрольно-измерительных приборов.
Сосуды работающие под внутренним избыточным давлением подвергаются техническому освидетельствованию. Техническое освидетельствование представляет собой внутренний осмотр и гидравлические испытания, которые производятся перед пуском в работу и периодически при эксплуатации. Гидравлическое испытание вновь устанавливаемых сосудов при техническом освидетельствовании разрешается не производить, если с момента проведения такого испытания на заводе-изготовителе прошло не более 12 месяцев. При эксплуатации, зарегистрированные сосуды подвергаются внутреннему осмотру не реже одного раза в 2 года, гидравлическим испытаниям один раз в 8 месяцев.
Оценка устойчивости здания
С учетом полученных данных и степени разрушения зданий и оборудования ударной взрывной волны приведенных в табл.3 производим оценку степени разрушения четырехэтажного здания из железобетонных конструкций.
Таблица 3Степени разрушения зданий и оборудования ударной взрывной волной.
Здания, оборудования, инженерные системы | Степень разрушений при | ||
слабые | средние | сильные | |
Многоэтажные здания из железобетонных конструкций | 8-20 | 20-40 | 40-90 |
При воздействии на здание избыточного давления во фронте ударной волны оно получит сильные разрушения части стен и перекрытий нижних этажей и подвалов. Сильное разрушение оборудования и инженерных систем характеризуется разрушением навесного оборудования, оснастки и контрольно-измерительных приборов.
Заключение
На первом этапе выпускной квалификационной работы была проанализирована работа воздухоразделительная установка фирмы «Linde»,выявлен узел для проработки, произведены тепловые балансы основного теплообменного оборудования блока комплексной очистки.
Вторым этапом выпускной квалификационной работы явился расчет испарителяотбросного азота Е2617. Задачей было составления модели конструктивного расчета, с целью составления оптимальной режимной кар
|
|
Опора деревянной одностоечной и способы укрепление угловых опор: Опоры ВЛ - конструкции, предназначенные для поддерживания проводов на необходимой высоте над землей, водой...
Состав сооружений: решетки и песколовки: Решетки – это первое устройство в схеме очистных сооружений. Они представляют...
Своеобразие русской архитектуры: Основной материал – дерево – быстрота постройки, но недолговечность и необходимость деления...
Наброски и зарисовки растений, плодов, цветов: Освоить конструктивное построение структуры дерева через зарисовки отдельных деревьев, группы деревьев...
© cyberpedia.su 2017-2024 - Не является автором материалов. Исключительное право сохранено за автором текста.
Если вы не хотите, чтобы данный материал был у нас на сайте, перейдите по ссылке: Нарушение авторских прав. Мы поможем в написании вашей работы!