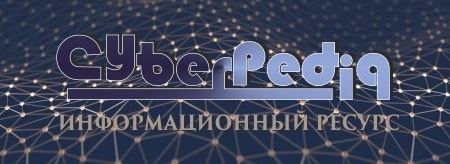
Археология об основании Рима: Новые раскопки проясняют и такой острый дискуссионный вопрос, как дата самого возникновения Рима...
Историки об Елизавете Петровне: Елизавета попала между двумя встречными культурными течениями, воспитывалась среди новых европейских веяний и преданий...
Топ:
Генеалогическое древо Султанов Османской империи: Османские правители, вначале, будучи еще бейлербеями Анатолии, женились на дочерях византийских императоров...
Особенности труда и отдыха в условиях низких температур: К работам при низких температурах на открытом воздухе и в не отапливаемых помещениях допускаются лица не моложе 18 лет, прошедшие...
Устройство и оснащение процедурного кабинета: Решающая роль в обеспечении правильного лечения пациентов отводится процедурной медсестре...
Интересное:
Национальное богатство страны и его составляющие: для оценки элементов национального богатства используются...
Как мы говорим и как мы слушаем: общение можно сравнить с огромным зонтиком, под которым скрыто все...
Искусственное повышение поверхности территории: Варианты искусственного повышения поверхности территории необходимо выбирать на основе анализа следующих характеристик защищаемой территории...
Дисциплины:
![]() |
![]() |
5.00
из
|
Заказать работу |
|
|
ТЕХНОЛОГИЧЕСКАЯ ИНСТРУКЦИЯ
ТИ ЭС6 - 04 - 2015
Введено в действие приказом технического директора
№ _ __ __ от «_ _ __» __ ____ ______ 2015 г.
Дата введения «_ _ __» __ ___ ______ 2015 г.
СОГЛАСОВАНО РАЗРАБОТАНА
Начальник ТУ Начальник ИТЦ
Д.В. Шабуров А.Г. Зырянов
Начальник ЭСПЦ-6
С.М. Фомченко
Начальник УТК
А.В. Комин
Начальник отдела метрологии
А.А. Черников
Начальник УОТПБ и ПД
С.И. Тетерев
г. Челябинск,
2015 г.
ОБЩИЕ ПОЛОЖЕНИЯ
1.1 Настоящая инструкция устанавливает основные принципы и технологические приемы производства углеродистых и легированных марок стали с суммарной массой легирующих материалов до 6,0 тонн по всем заказам. Марки стали, задаваемые в производство, должны соответствовать ГОСТам, технологическим условиям, протоколам, металлургическим спецификациям, международным стандартам (DIN, ASTM и др.). Дополнительные требования по химическому составу для конкретных марок определяются технологическим распоряжением или технологической картой.
1.2 Инструкция является руководством для технологического персонала цеха. Ответственность за выполнение настоящей инструкции возлагается на старших мастеров, сменных мастеров, сталеваров, бригадиров шихтового двора.
1.3 Контроль за выполнением настоящей инструкции возлагается на начальника цеха, его заместителей и помощников, старших мастеров, сменных мастеров, начальника УТК, начальника участка УТК и контролеров УТК ЭСПЦ-6.
|
1.4 Основные технологические схемы производства:
1.4.1 ДСП → АКП → ВКОиР;
1.4.2 ДСП → АКП;
1.4.3 ККЦ → ЭСПЦ-6;
1.4.4 ЭСПЦ-6 → ККЦ.
1.5 Обозначения и сокращения:
1.5.1 ЭСПЦ-6 – электросталеплавильный цех №6;
1.5.2 ДСП – дуговая сталеплавильная печь;
1.5.3 АКП – агрегат ковш-печь;
1.5.4 ВКОиР – установка вакуум-кислородного обезуглероживания и рафинирования;
1.5.5 ЦПШ – цех подготовки шихты;
1.5.6 ТК – технологическая карта;
1.5.7 ТР – технологическое распоряжение;
1.5.8 ВД – вакуумная дегазация;
1.5.9 ГКГ – газокислородные горелки;
1.5.10 СФГ - стеновые фурмы-горелки;
1.5.11 ККЦ – кислородно-конверторный цех.
1.5.12 УТК – управление технического контроля
МАТЕРИАЛЫ
2.1 МЕТАЛЛИЧЕСКАЯ ШИХТА
В качестве металлической шихты использовать стальной лом и отходы по ГОСТ 2787-75 со следующими дополнениями:
2.1.1 Стальной лом и отходы, подготовленные в соответствии с требованиями ГОСТ 2787-75, стандартами и комбинатскими инструкциями, поступают в шихтовый пролет цеха в контейнерах железнодорожным транспортом из ЦПШ.
2.1.2 Для загрузки в ДСП:
- размеры загружаемых кусков не более 1,0×0,5×0,5 м (обеспечивает поставщик, контроль визуальный), масса куска не более 1,5 т. В составе завалки использовать не более 20 % от общей массы шихты.
- в состав завалки также вводить от 30 % до 60 % (от общей массы шихтовых материалов) легковесного стального лома и отходов с насыпной плотностью от 0,7 до 1,2 т/м3 (по данным ЦПШ).
- стружка или отходы шлифования не более 5 % (от общей массы шихтовых материалов).
- скрап не более 5 % (от общей массы шихтовых материалов). Размеры кусков не более 1,0×1,0×0,4 м (обеспечивает поставщик, контроль визуальный).
2.3 ФЕРРОСПЛАВЫ и ДОБАВОЧНЫЕ МАТЕРИАЛЫ
2.3.1 Все ферросплавы и добавочные материалы должны соответствовать требованиям нормативной документации на сырье и материалы, применяемые при производстве продукции (приложение № 1).
|
В сертификатах на каждую партию легирующих и раскислителей должна быть указана массовая доля основных элементов, которая записывается в журнал ферросплавов.
2.3.2 Использование ферросплавов и добавочных материалов, не указанных в приложении №1, допускается после проведения испытания и наличия положительного заключения.
2.3.3 Ферросплавы, легирующие и раскислители, используемые для раскисления и корректировки химического анализа, поступающие в загрузочные бункера должны иметь размер кусков:
- для дуговой печи от 10 до 50 мм;
- для АКП от 10 до 50 мм;
- для установки ВКОиР от 10 до 50 мм.
2.3.4 Для производства стали использовать известь свежеобожженную из вращающихся печей, с массовой долей СаО + МgО более 92 %, менее 6 % МgО, менее 1,8 % SiО2, не более 0,06 % серы. Потери при прокаливании не более 5 %. Для ДСП допускается использование извести с шахтных печей.
Известь для ДСП должна иметь размер кусков от 10 до 50 мм.
Известь для установки ВКОиР и АКП должна иметь размер кусков от 20 до 50 мм.
2.3.5 Для разжижения шлака применять плавикошпатовые концентраты. Влажность материала не более 1,0 %.
Для АКП размер кусков КВЦ от 10 до 50 мм.
Для установки ВКОиР размер кусков от 10 до 20 мм.
2.3.6 Размеры кусков ферросплавов, легирующих, раскислителей и шлакообразующих материалов обеспечивает поставщик, контроль визуальный.
2.3.7 Виды ферросплавов и добавочных материалов для производства конкретных марок стали, при необходимости, указывают в технологической карте на производство конкретной марки стали.
2.4 ЭНЕРГОНОСИТЕЛИ
2.4.1 При выплавке в дуговой печи и установке ВКОиР применять кислород газообразный технический по ГОСТ 5583 - 78 с массовой долей кислорода не менее 99,5 %. Давление кислорода в магистрали должно быть от 1,6 до 2,2 МПа (от 16 до 22 кгс/см2). Влажность кислорода, контролируемая при его производстве, должна быть не более 0,07 г/м3.
2.4.2 На АКП и установке ВКОиР применять аргон или азот газообразный технический по ГОСТ 9293 - 74 с массовой долей аргона или азота не менее 99,5 %. Давление аргона или азота в магистрали для продувки стали в ковше не менее 1,2 МПа (12 кгс/см2).
2.4.3 Давление природного газа для продувки через комбинированные стеновые горелки на ДСП-100И7 не менее 0,3 МПа (3 кгс/см2).
|
2.5 ЭЛЕКТРОДЫ
2.5.1 Для ДСП и АКП использовать электроды с плотностью тока не менее 25 А/см2 и удельным электросопротивлением не более 6 мкОм•мм.
2.5.2 Электроды должны хранить на специально оборудованных стеллажах. Ниппели, во избежание повреждения резьбы, должны хранить в упакованном виде.
2.6 ХРАНЕНИЕ МАТЕРИАЛОВ
2.6.1 Для производства стали в цехе должен быть трехсуточный запас всех материалов, за исключением извести, стального лома и отходов. Срок хранения извести не более 24 часов.
2.6.2 Материалы хранятся в отдельных контейнерах и бункерах. В контейнере или бункере должны находиться материалы только одной марки (сорта) или группы.
На каждый контейнер снаружи прикрепляется табличка с указанием марки или группы материала. Таблички должны быть написаны масляной краской и прочно закреплены на контейнерах.
2.6.3 Материалы, вводимые в жидкий металл, должны быть воздушносухими (обеспечивается способом производства, доставки и хранения).
ВЫПЛАВКА ПОЛУПРОДУКТА В ДСП
3.1 ОБЩИЕ ПОЛОЖЕНИЯ
3.1.1 Выплавку полупродукта углеродистых и легированных марок стали проводить как на твердой шихте, так и с использованием жидкого чугуна.
3.1.2 Применение жидкого чугуна допускается с хорошим состоянием футеровки откосов и подины электропечи. Оценку состояния футеровки производит старший мастер печи.
После капитального ремонта или замены футеровки подины выплавка первых 10 плавок производится без использования жидкого чугуна, паузы между плавками не более 60 минут. Выплавку полупродукта в ДСП после проведения капитального ремонта или замены подины производить в соответствии с существующим энерготехнологическим режимом, металл назначать по всем заказам.
3.1.3 Основной способ выплавки полупродукта углеродистых и легированных марок стали с использованием «болота». Серийность работы на «болоте» определяет старший мастер печи по состоянию футеровки.
3.1.4 Перед включением печи мастер обязан произвести расчет шихты, проверить наличие всех материалов для ведения плавки, а также убедиться в исправности агрегатов: ДСП, АКП и ВКОиР.
|
3.1.5 После выплавки кампании нержавеющих марок стали выплавку углеродистых марок стали начинать после одной или двух хромистых или хромоникелевых промывных плавок марок стали.
3.2 ПОДГОТОВКА ПЕЧИ
3.2.1 Выплавку полупродукта производить с твердым состоянием подины и откосов без углублений, защитным гарнисажем на водоохлаждаемых панелях стен и свода, хорошо очищенным и засыпанным эркерным отверстием, целыми электродами, при исправном состоянии и надежной работе охладительной системы, механизмов, электроаппаратуры и газоочистки.
3.2.2 После проведения холодного ремонта стен выплавлять одну плавку стали общего назначения.
3.2.3 Перед завалкой первой плавки электроды выставляются на 500 мм от подины (визуально) и фиксируется положение электрододержателей для исключения повреждения подины.
3.2.4 После капитального ремонта или замены подины для обеспечения качественного спекания массы первую плавку после выполнения капитального и планово-производственного ремонтов проводят по графику, указанному в таблице № 1.
Таблица № 1 График ведения первой плавки (разогрев)
Время работы «под током», мин | Время работы «без тока», мин |
7 | 13 |
5 | 10 |
9 | 19 |
6 | 12 |
10 | 17 |
5 | 34 |
5 | 28 |
5 | 18 |
37 | Выпуск |
Общее время плавки | 240 |
Режим работы стеновых горелок – дежурный: расход газа 100 м3/ч; расход кислорода 200 м3/ч.
В паузах при работе «без тока» работа стеновых горелок на первой ступени.
Перед завалкой выставить электроды на 500 мм от подины (визуально) и зафиксировать положение электрододержателей для исключения повреждения подины.
В паузах после проплавления завалки и подвалок проверить работу стеновых горелок во всех режимах.
Присадка извести: перед подвалкой от 1,0 до 1,5 т, остальное в процессе расплавления шихты при работе «под током». Суммарная масса извести от 4 до 5 тонн.
Работать от начала и до выпуска плавки, используя ступени не выше 16.
При получении в пробе массовой доли углерода выше марочного диапазона разрешается продувка ванны кислородом с расходом 1000 м3/ч (1 ступень рафинирования).
Температура металла в печи перед выпуском от 1630 оС до 1650 оС. Общее время плавки 240 мин (4 ч), время» под током» – 89 мин.
3.2.5 После слива первой плавки производят осмотр и оценку состояния футеровки подины, при отсутствии замечаний агрегат эксплуатируют в штатном режиме.
После капитального ремонта печи или замены подины выплавляют до трех обжиговых плавок, исходя из состояния футеровки печи. Выпуск первых десяти плавок осуществлять «насухо», с обязательным контролем состояния подины и откосов и их заправкой, паузы между плавками не должны превышать 60 минут.
3.2.6 В целях закрепления футеровки подины, использование жидкого чугуна в составе шихты разрешается после подвалки, начиная с десятой плавки, а после завалки с двадцатой плавки. Работа с «болотом» разрешается при температуре подины не менее 100 оС.
|
3.2.7 После выпуска плавки произвести удаление остатков шлака и настылей из канала эркера и торца концевой втулки эркерного выпуска. Отверстие снизу плотно заделать каолиновой ватой на высоту от 250 до 300 мм (контроль визуальный), после чего эркер закрыть затвором.
Эркерное отверстие засыпать крупным магнезитовым порошком марки ППК-85 (88). Для исключения попадания мелкой фракции, порошок предварительно просеивать через сито с длиной стороны ячейки 2 мм. Верхняя половина высоты эркерного отверстия засыпается до образования «горки» над уровнем футеровки подины стартовой смесью дунитового состава марки СС-46, либо периклазоуглеродистой стартовой смесью марок СС-1, СС-2 производства УОР.
3.2.8 Заправка подины и откосов.
3.2.8.1 Для заправки подины печи применять порошок магнезитовый марки ППЭ-88, для заправки откосов применять массу ремонтную Ankerfrit NX93 или порошок магнезитовый марки ППЭ-88. Массовая доля MgO не менее 88 %, размер зерна не более 3,0 мм.
3.2.8.2 После выпуска металла печь наклонить в сторону рабочей площадки для осмотра футеровки мастером и сталеваром с целью общей оценки состояния откосов, подины и выявления на ней остатков металла и шлака. Одновременно оценивается состояние свода и стен.
Остатки металла с подины удалить повторным наклоном печи в сторону слива металла (операция выполняется после заделки эркерного отверстия). Остатки не-удаленного металла заморозить в эркерной зоне печи.
При выдувке остатков металла с подины обрез трубки держать на расстоянии от 150 до 200 мм от поверхности металла (определяется визуально), при этом для более полного удаления металла из углублений в подине до 100 мм (определяется визуально) рекомендуется давать под струю кислорода магнезитовый порошок. Массу порошка определяет мастер (старший мастер), порошок дается вручную. При углублении подины более 100 мм (определяется визуально) и наличии в углублении остатков жидкого металла, в металл опускается сляба с целью намораживания остатков металла. После выдержки и намораживания металла (определяется визуально) производится удаление слябы с намороженным металлом. Работа производится под руководством старшего мастера. После оценки состояния подины производится ремонт подины.
3.2.8.3 Заправка откосов производится механизированным способом с помощью центробежно-бросковой машины. Допускается заправка при помощи лотка. Заправку подины производят путем подсыпки порошка краном из мягкого контейнера. Для проведения локальных ремонтов футеровки откосов производится заправка их магнезитовым порошком на связке из водного раствора жидкого стекла или лигносульфанат технический в соотношении с водой 1:3 по объему.
При работе на «болоте» общий износ футеровки подины контролировать не реже одного раза в смену с помощью «шомпола», изогнутого на конце под углом 90о (по визуальной оценке), а так же контролируют по показаниям термоэлектрических преобразователей в зонах ванны. «Шомполом» прощупывается вся площадь подины. В случае нарушения твердости подины или обнаружения углублений, принимаются меры к сливу следующей плавки насухо, и подину ремонтируют.
Для закрепления исправленных участков подины и откосов, после усиленной заправки, рекомендуется выплавлять от 1 до 2 плавок без применения жидкого чугуна и без перегрева металла перед выпуском.
3.2.9 При значительном зарастании откосов или подины перед завалкой, увеличенные от проектных размеров, откосы и подину прокидать песком (кварцитом) массой от 3 до 4 кг/т совместно с ферросилицием массой от 2 до 3 кг/т. Массу завалки уменьшать, обеспечивая уровень шлака на откосах. Производить перегрев металла выше рекомендаций технологической инструкции на 30 оС. При повышенной температуре выдержка не менее 20 минут.
На последующих плавках (зависит от состояния подины и откосов) производить заправку зарощенных участков футеровки печи песком (кварцитом) массой от 1 до 3 кг/т и ферросилицием массой от 1 до 2 кг/т до достижения проектных размеров ванны печи.
Углубление ванны производить под руководством старшего мастера присадками кварцевого песка, кварцита и порошка ферросилиция.
3.2.10 Порог рабочего окна должен быть заправлен до уровня, обеспечивающего сход шлака.
3.2.11 Горячий ремонт узла эркерного выпуска (замена изделий) производится в следующих случаях: в случае превышения стойкости эркера более 100 плавок, либо при износе изделий более 70 % от первоначального диаметра (оценивается визуально).
Порядок проведения замены эркерной трубки следующий:
3.2.11.1 При сливе обеспечить отсутствие остатков металла и шлака на эркере.
3.2.11.2 После слива плавки произвести удаление остатков изношенной трубки выбиванием клиньев малого опорного кольца узла эркера.
3.2.11.3 Произвести очистку внутренней поверхности гнездовых блоков от остатков массы, шлака и металла.
3.2.11.4 Предварительно на специальной оправке произвести сборку эркерной трубки с концевой катушкой. Стыки промазывать периклазоуглеродистой клеевой композицией марки ПУКК.
3.2.11.5 Установку новой трубки производить втягиванием оправки с собранной эркерной трубкой через отверстие гнездовых блоков, после чего произвести жесткую фиксацию малого опорного кольца клиньями к большому опорному кольцу узла эркера.
3.2.11.6 Зазор между гнездовыми блоками и трубкой эркера послойно просыпать периклазовым порошком марки ППИ-92 или обожженным дунитовым порошком (слой засыпаемого порошка должен составлять 1,0 -1,5 высоты гнездового блока). Перед каждой засыпкой нового слоя, предыдущий слой штыкуется прутом (диаметр прута от 10 до 16 мм).
3.2.12 При остановке печи на холодный ремонт необходимо выполнить следующие мероприятия:
3.2.12.1 Перед сливом плавки навести жидкоподвижный шлак присадкой плавикового шпата (количество шпата определяется жидкоподвижностью шлака).
3.2.12.2 При сливе плавки шлак выпускать в ковш как можно раньше, не допуская оставления его в печи. Металл и шлак слить полностью.
3.2.13 После проведения холодного ремонта печь очистить от огнеупорного мусора и передать в дальнейшую работу.
3.2.14 Горячий ремонт стен производить в случае местного износа футеровки более 70 % от первоначальной толщины (определяется визуально).
3.2.15 Выплавку полупродукта в ДСП после проведения холодного ремонта стен производить в соответствии с существующими энерготехнологическими режимами, металл назначать по всем заказам.
3.3 ШИХТОВКА И ЗАВАЛКА
3.3.1 Состав завалки:
- Обрезь тяжеловесная до 15 %;
- Металлический лом до 85 %;
- Жидкий чугун до 55 %.
Общая масса шихтовых материалов от 140 до 145 тонн.
При производстве стали с «болотом» общая масса шихтовых материалов:
- первая плавка в серии от 150 до 155 тонн;
- вторая и следующие плавки в серии от 140 до 145 тонн;
- последняя плавка в серии от 130 до 135 тонн.
3.3.2 В состав шихты вводить никель, медь, молибден на нижний предел марочного диапазона отходами, легированными никелем, медью и молибденом. Корректировку по никелю, меди, молибдену производить на АКП.
3.3.3 Разрешается использование железа горячего брикетирования до 20 тонн на плавку.
3.3.4 Шихтовку плавки по массовой доле углерода производить жидким (твердым) чугуном, коксом или антрацитом марки АМ.
3.3.5 Расчетная массовая доля углерода должна соответствовать таблице № 2.
Таблица № 2
В процентах
Массовая доля углерода в стали
| Шихтовка по углероду чугуном | Шихтовка по углероду коксом |
Среднее значение марочного диапазона плюс | ||
До 0,2 включ. | 1,1 | 1,2 |
Св. 0,2 до 0,5 включ. | 1,0 | 1,1 |
Св. 0,5 до 1,0 включ. | 0,8 | 0,9 |
Свыше 1,0 | 0,7 | 0,8 |
При шихтовке коксом учитывать усвоение углерода из кокса – 50 %, массовая доля углерода в коксе от 82 % до 85 %.
При шихтовке антрацитом марки АМ учитывать усвоение углерода из антрацита – 50 %, массовая доля углерода в антраците от 72 % до 75 %.
3.3.6 Заливку жидкого чугуна в печь осуществлять через верх печи краном из чугуновозного ковша.
3.3.7 Загрузку металлошихты производить корзиной в два приема (завалка, подвалка). Как исключение разрешается делать две подвалки.
Порядок погрузки шихты в корзину:
Завалка
- на дно корзины один совок мелкого лома или стружки;
- тяжелый лом от 10 до 20 тонн;
- кокс по расчету (при отсутствии чугуна в составе шихты);
- мелкий лом или стружка (насыпная плотность от 0,7 до 1,2 т/м3).
После завалки допускается заливка жидкого чугуна, если не производилась заправка подины и откосов. При наличии в составе завалки стружки заливка жидкого чугуна на завалку запрещена.
Подвалкашихты должна производиться на не полностью расплавленную шихту при закрытом завалочном окне печи.
- мелкий лом
- жидкий чугун (если заливается после подвалки).
3.3.8 В случае отсутствия чугуна в составе шихты вводить кокс с учетом усвоения углерода 50 %.
3.3.9 При необходимости после подвалки производится подварка изношенных участков футеровки стен печи.
3.3.10 Перед включением печи на плавку сталевар и ответственные лица обязаны проверить исправность оборудования, футеровки и свода печи.Расплавление полупродукта вести по утвержденным энерготехнологическим режимам (приложение № 2).
3.4 Плавление полупродукта с жидким чугуном (заливка после завалки).
3.4.1 Все СФГ включать перед началом завалки с постепенным выходом в течение 90 секунд (на каждой ступени отработать 30 секунд), на 3 ступень интенсивного горения и работают в этом режиме до израсходования от 5 до 6 МВт•ч электроэнергии, после чего переводятся в режим продувки кислородом. Во время работы газокислородной горелки крышка завалочного окна должна быть закрыта.
3.4.2 Включение печи после завалки и подвалок производится на 16 (19) ступени трансформатора в зависимости от характера шихты (16 ступень – при полном заполнении печного пространства шихтой) с переключением на повышенную ступень после отработки 1000 КВт•ч электроэнергии. По окончании периода расплавления производится переключение на 14 или 16 ступень трансформатора.
Все СФГ работают до подвалки шихты, после чего переводятся в дежурный режим горения.
3.4.3 До подвалки в печь присадить известь порциями по 300 кг общей массой 2 т, если присадка извести в завалку не производилась.
3.4.4 После израсходования от 10 до 13 МВт•ч электроэнергии печь отключить и произвести подвалку шихты. При необходимости после подвалки производится подварка изношенных участков футеровки стен печи.
3.4.5 Во время подвалки производится включение всех СФГ. Режим работы СФГ аналогично пункту 3.4.1.
3.4.6 Газокислородные горелки стеновых фурм-горелок работают до израсходования от 14 до 15 МВт•ч, после этого через стеновые фурмы в печь подавать кислород.
3.4.7 ГКГ мультифурмы работает для очистки рабочего пространства печи в зоне рабочего окна.
3.4.8 В период плавления и во время окислительной продувки в печь присаживать известь порциями по 300 кг. При необходимости присаживать плавиковый шпат общей массой до 600 кг. Суммарная масса присаживаемой извести должна соответствовать таблице № 3.
Таблица № 3
Массовая доля фосфора в металле, %, не более | 0,025 | 0,015 | 0,010 | 0,005 |
Масса чугуна на тонну, кг | Масса извести на плавку, т | |||
0 | 5,5 | 6,5 | 7,5 | 8,5 |
300 | 5,5 | 6,5 | 7,5 | 10,0 |
400 | 6,0 | 7,0 | 8,0 | 11,0 |
500 | 6,5 | 8,0 | 9,0 | 12,0 |
600 | 7,0 | 9,0 | 10,0 | 13,0 |
3.4.9 Для вспенивания шлака во время окислительной продувки периодически присаживать науглероживатель с размером зерна не более 3 мм через установку вдувания или, как исключение, кокс с размером зерна от 3 до 8 мм через тракт сыпучих порциями общей массой до 500 кг.
3.4.10 Во время окислительной продувки шлак самотеком удалять из печи через порог рабочего окна.
3.4.11 Окислительное рафинирование продолжать до полного расплавления металлошихты, после чего произвести измерение температуры и отбор пробы металла для определения химического состава. Температура металла в ДСП должна быть не более 1720 оС.
3.4.12 При получении удовлетворительных результатов химического анализа и при температуре не ниже 1650 оС производится выпуск металла из печи при работе СФГ в режиме ГКГ. Разделка сталевыпускного отверстия должна производиться только при наличии ковша под печью.
3.4.13 Для снижения потерь тепла металлом продолжительность транспортировки ковша с металлом от выпуска из ДСП до постановки на АКП должна быть минимальна и определяется графиком производства. Рекомендуемая длительность передачи не более 30 минут.
3.5 Плавление полупродукта с жидким чугуном (заливка чугуна после подвалки).
3.5.1 Продувку кислородом начинать после израсходования от 7 до 8 МВт•ч электроэнергии. Остальные технологические параметры аналогично п.3.4.
3.6 Плавление полупродукта без жидкого чугуна.
3.6.1 В корзину с завалкой дается 2,5 т извести (допускается частичная замена на известняк).
3.6.2 Все СФГ включаются после заправки и до начала завалки металлошихты в режиме интенсивного горения с постепенным выходом в течение 90 секунд на 3 ступень и работают до израсходования от 8 до 9 МВт•ч, от 16 до 17 МВт•ч, от 25 до 26 МВт•ч электроэнергии соответственно с переходом по достижении этих значений в режим продувки кислородом. Во время работы газокислородной горелки крышка завалочного окна должна быть закрыта.
3.6.3 ГКГ мультифурмы включается после завалки и подвалок и работает в режиме максимального расхода природного газа до первой, второй подвалок и до израсходования от 26 до 30 МВт•ч электроэнергии.
3.6.4 В период плавления и во время окислительной продувки в печь присаживать известь порциями по 300 кг. Масса присаживаемой извести должна соответствовать таблице № 3. При необходимости присаживать плавиковый шпат общей массой до 600 кг.
3.6.5 В период плавления шлак вспенивать присадками науглероживателя с размером зерна не более 3 мм через установку вдувания порошков порциями или, как исключение, с размером зерна от 3 до 8 мм порциями через тракт подачи сыпучих материалов. Общая масса порошка до 500 кг.
3.6.6 При полном расплавлении металлошихты произвести измерение температуры и отбор пробы для определения химического состава металла.
3.6.7 При получении удовлетворительных результатов химического анализа и при температуре не ниже 1650 оС производится выпуск металла из печи при работе СФГ в режиме ГКГ. Разделка сталевыпускного отверстия должна производиться только при наличии ковша под печью.
3.6.8 Для снижения потерь тепла металлом продолжительность транспортировки ковша с металлом от выпуска из ДСП до постановки на АКП должна быть минимальна и определяется графиком производства. Рекомендуемая длительность передачи не более 30 минут.
3.7 Выпуск металла с отсечкой шлака (с «болотом»).
3.7.1 Выпуск металла из ДСП производить с отсечкой печного шлака, возврат печи в «нулевое» положение производить со скоростью, максимально возможной по техническим характеристикам механизмов наклона. Возврат печи в нулевое положение начинается при наполнении ковша металлом (по показаниям весов сталевоза):
- на 120 т при стойкости эркера менее 50 плавок;
- на 115 т при стойкости эркера более 50 плавок.
Масса металла в ковше после выпуска должна составлять не менее 128 т.
В ДСП оставлять от 10 до 20 т металла и шлака.
3.7.2 При выпуске полупродукта в ковш присаживать следующие материалы:
- 70 кг алюминия на спокойном сортаменте, 150 кг – на полуспокойном и с регламентированной массовой долей алюминия (на дно ковша);
- науглероживатель на нижний предел марочного диапазона (ориентировочное усвоение 70 %);
- ферросилиций по расчету (без учета угара): на среднее значение марочного диапазона кремния в марке – на спокойном сортаменте; на полуспокойном сортаменте (массовая доля кремния в марке не более 0,15 %) от 150 до 200 кг на плавку; на кремнийсодержащих марках (массовая доля кремния в марке более 0,5 %) из расчета введения 0,35 % кремния;
- от 400 до 500 кг извести с вращающихся печей;
- 250 кг флюоритового концентрата марки ФК85.
3.7.3 Для обеспечения максимального контакта металла и шлака во время и после выпуска рекомендуется осуществлять продувку аргоном через донную фурму стальковша не менее 10 минут. По окончании продувки произвести отбор пробы металла (проба № 31). Свободный борт ковша должен быть не менее 400 мм (определяется визуально).
3.7.4 Для снижения потерь тепла металлом продолжительность транспортировки ковша с металлом от выпуска из ДСП до постановки на АКП должна быть минимальна и определяется графиком производства. Рекомендуемая длительность передачи не более 30 минут.
3.8 Выпуск без отсечки шлака (насухо)
3.8.1 Выпуск производить из «нулевого» положения печи до схода всего шлака, затем производить выпуск остатков металла.
3.8.2. Во время выпуска полупродукта в ковш присаживать:
- ферросилиций по расчету (без учета угара): на среднее значение марочного диапазона кремния в марке – на спокойном сортаменте; на полуспокойном сортаменте (массовая доля кремния в марке не более 0,15 %) от 150 до 200 кг на плавку; на кремнийсодержащих марках (массовая доля кремния в марке более 0,5 %) из расчета введения 0,35 % кремния.
3.8.3 При получении удовлетворительных результатов химического анализа и при температуре не ниже 1650 оС производится выпуск металла из печи при работе СФГ в дежурном режиме ГКГ. Осадка шлака на выпуске плавки влажными материалами и водой не допускается. Свободный борт ковша должен быть не менее 400 мм (определяется визуально).
3.8.4 Для снижения потерь тепла металлом продолжительность транспортировки ковша с металлом от выпуска из ДСП до скачивания шлака на МСШ АКП должна быть минимальна и определяется графиком производства. Рекомендуемая длительность передачи не более 30 минут.
3.9 Особенности выплавки полупродукта углеродистых и легированных марок стали с обеспечением низкой массовой доли азота
3.9.1 В составе шихтовых материалов использовать не менее 50 тонн чугуна.
3.9.2 При получении температуры металла от 1580 оС до 1610 оС печь отключить и продолжить окисление углерода. За время окислительной продувки без работы «под током» должно быть окислено не менее 0,15 % углерода.
3.9.3 После окончания окислительной продувки произвести измерение температуры металла и отобрать пробу металла.
3.9.4 При получении удовлетворительных результатов химического анализа и при температуре не ниже 1650 оС производится выпуск металла из печи при работе СФГ в дежурном режиме ГКГ. Свободный борт ковша должен быть не менее 400 мм (определяется визуально).
3.9.5 Для снижения потерь тепла металлом продолжительность транспортировки ковша с металлом от выпуска из ДСП до постановки на АКП должна быть минимальна и определяется графиком производства. Рекомендуемая длительность передачи не более 30 минут.
3.10 Особенности выплавки полупродукта углеродистых и легированных марок стали при использовании до 100 % чугуна (жидкого и твердого)
3.10.1 В составе шихтовых материалов использовать от 70 до 120 тонн жидкого чугуна, от 20 до 70 тонн твердого чугуна и до 4 тонн агломерата или окатышей. Оптимальный расход твердого чугуна от 20 до 30 тонн на плавку. Суммарная масса чугуна 140 – 145тонн.
3.10.1 Твердый чугун загружать в зависимости от массы заливаемого жидкого чугуна.
3.10.1 Порядок погрузки:
- твердый чугун от 10 до 15 тонн;
- агломерат или окатыши;
- остальная масса твердого чугуна;
3.10.1 После завалки в ДСП твердого чугуна производится заливка жидкого чугуна из одного или двух чугуновозных ковшей.
3.10.1 Расплав проводить на 14 или 16 ступени напряжения печного трансформатора. Продувку кислородом проводить:
- после отработки 2000 кВт*ч на первой ступени (1200 м3/час) кислородными фурмами № 2, 3 и 4;
- после отработки 7000 кВт*ч на четвертой ступени (2200 м3/час) кислородными фурмами № 3 и 4, допускается использование фурмы № 2 на третьей или 4 ступенях (1800 или 2200 м3/час).
3.10.1 Работу «под током» проводить до наработки мВт*часов в зависимости от доли твердого чугуна:
Доля твердого чугуна, % | Отработать под током, мВт*ч |
15 | 12 |
20 | 16 |
25 | 20 |
30 | 23 |
35 | 26 |
40 | 30 |
45 | 33 |
3.10.1 В период продувки металла кислородом производить удаление шлака из рабочего пространства печи. По ходу плавки после отработки 2000 кВт*ч присаживать порциями от 200 до 300 кг известь общей массой до 7 тонн и агломерат или окатыши общей массой до 7 тонн.
3.10.1 По ходу плавки контролировать температуру металла, не допуская перегрева. После полного расплавления твердого чугуна и достижения температуры металла не менее 1600 оС отобрать пробу металла. При получении удовлетворительного химического состава металла, при необходимости, произвести подогрев металла и слить металл в ковш.
3.11 Шлакоуборка
3.11.1 Удаление шлака из ДСП-100И7 при выплавке полупродукта производится в период проведения окисления в заранее подготовленную шлаковую канаву.
3.11.2 Уборка шлака.
3.11.2.1 Уборка шлака из шлакового коридора производится в период заправки, завалки и прогрева шихты до заливки чугуна.
3.11.2.2 Без уборки шлака, допускается сливать шлак не более чем с двух плавок. Без дальнейшей уборки шлака работа ДСП-100И7 должна быть прекращена.
3.11.2.3 Въезд погрузчика в шлаковый коридор разрешается при зеленом сигнале светофора. Включение зеленого разрешающего или красного запрещающего сигналов светофора и звуковой сигнализации производится с пульта управления печи сталеваром.
3.11.2.4 После каждого выпуска шлака из печи жидкий шлак в канаве охлаждается подсыпкой сухого охлажденного шлака, затем убирается погрузчиком согласно схеме движения. Транспортировка шлака производится частично на склад сухого шлака (до 30 % убираемой массы) для охлаждения, основная часть шлака (до 70 % от убираемой массы определяется визуально) грузится погрузчиком в совок для дальнейшей перегрузки.
3.11.2.5 Уборка шлака погрузчиком должна производиться не более 12 минут с восстановлением шлаковой канавы.
3.11.3 Формирование шлаковой канавы.
3.11.3.1 Для формирования шлаковой канавы подготавливается сухой шлак (образуется после дробления шлаковой массы гусеницами погрузчика на складе сухого шлака).
3.11.3.2 Погрузчиком формируется шлаковая канава длиной 10 м и шириной 3 м с боковыми откосами высотой не менее 1 м и валом-перегородкой высотой от 0,4 до 0,9 м, толщина слоя подсыпки в шлаковой канаве 0,2 м (определяется визуально). Высота подсыпки в районе подпорной стены не менее 1,8 м.
3.11.3.3 Шлаковый монолит в канаве не допускается.
3.11.4 Во время выпуска шлака из печи перелив жидкого шлака через сформированные откосы и вал-перегородку не допускается.
ПОДГОТОВКА СТАЛЕРАЗЛИВОЧНОГО КОВША К ПРИЕМУ МЕТАЛЛА
4.1 Для обработки металла на АКП использовать сталеразливочные ковши оборудованные двумя исправными продувочными узлами.
4.2 Для шиберных затворов использовать только стаканы-коллекторы диаметром 70 мм, на которые имеется положительное заключение ОГО или ИТЦ.
4.3 Канал стакана перед засыпкой тщательно просушить, очистить от остатков огнеупорной массы, мусора. Перед засыпкой, стартовую смесь необходимо предварительно нагреть в специальной таре для достижения влажности не более 0,5 %.
Засыпку стартовой смеси производить через специальное устройство. Засыпать стартовой смесью с образованием гор
|
|
Археология об основании Рима: Новые раскопки проясняют и такой острый дискуссионный вопрос, как дата самого возникновения Рима...
Кормораздатчик мобильный электрифицированный: схема и процесс работы устройства...
Семя – орган полового размножения и расселения растений: наружи у семян имеется плотный покров – кожура...
Индивидуальные и групповые автопоилки: для животных. Схемы и конструкции...
© cyberpedia.su 2017-2024 - Не является автором материалов. Исключительное право сохранено за автором текста.
Если вы не хотите, чтобы данный материал был у нас на сайте, перейдите по ссылке: Нарушение авторских прав. Мы поможем в написании вашей работы!