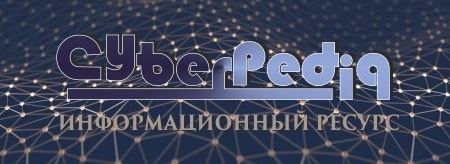
Семя – орган полового размножения и расселения растений: наружи у семян имеется плотный покров – кожура...
История создания датчика движения: Первый прибор для обнаружения движения был изобретен немецким физиком Генрихом Герцем...
Топ:
Марксистская теория происхождения государства: По мнению Маркса и Энгельса, в основе развития общества, происходящих в нем изменений лежит...
Когда производится ограждение поезда, остановившегося на перегоне: Во всех случаях немедленно должно быть ограждено место препятствия для движения поездов на смежном пути двухпутного...
Характеристика АТП и сварочно-жестяницкого участка: Транспорт в настоящее время является одной из важнейших отраслей народного хозяйства...
Интересное:
Уполаживание и террасирование склонов: Если глубина оврага более 5 м необходимо устройство берм. Варианты использования оврагов для градостроительных целей...
Принципы управления денежными потоками: одним из методов контроля за состоянием денежной наличности является...
Финансовый рынок и его значение в управлении денежными потоками на современном этапе: любому предприятию для расширения производства и увеличения прибыли нужны...
Дисциплины:
![]() |
![]() |
5.00
из
|
Заказать работу |
|
|
Вакуумная дуговая плавка
Дуговые печи, их виды и характеристики. Основы процесса вакуумной дуговой плавки с расходуемым электродом. Тепловые процессы, происходящие во время плавки. Преимущества вакуумных дуговых установок. Возможности вакуумного электродугового переплава.
Установки, в которых происходит превращение электрической энергии в другие виды с одновременным осуществлением технологических процессов, называют электротехнологическими. Эти установки имеют довольно сложную конструкцию и оборудование, Правильные монтаж, наладка и эксплуатация которого без знания выполняемого им технологического процесса затруднительны.
Технология вакуумно-дуговой выплавки широко используется для улучшения чистоты и структуры стандартных слитков, которые называются расходуемыми электродами, выплавленных в атмосфере либо в вакууме по технологии индукционной плавки. Стали и сплавы, а также титан и цирконий и их сплавы, имеют много областей применения, где решающее значение имеет чистота, однородность структуры, длительная прочность и прочность на срез. Авиакосмическая промышленность, производство энергии, оборонная, медицинская и атомная промышленность отдают предпочтение возможностям и характеристикам этих современных материалов.
При вакуумном дуговом переплаве под воздействием высоких температур, возникающих в зоне электрической дуги между переплавляемым электродом и поддоном кристаллизатора, сталь на нижнем торце электрода расплавляется и капли расплавленного металла падают в ванну, где под воздействием охлаждения кристаллизатора формируется слиток. До начала операции печь вакуумируют (остаточное давление обычно не более 1,33 Па); вакуумные насосы продолжают работать в течение всей плавки. Таким образом, капли металла падают через вакуумированное пространство, при этом обеспечивается очень полное очищение металла от газов, оксидных неметаллических включений (общее содержание кислорода снижается до очень низких пределов), от примесей некоторых цветных металлов и получается плотный слиток. Кристаллизация металла в водоохлаждаемом кристаллизаторе (обычно медном) имеет четко направленный характер, отвечающий направлению отвода тепла. В результате вакуумно дугового переплава механические характеристики металла улучшаются и становятся почти одинаковыми в различных направлениях. В современных установках вакуумно дугового переплава получают слитки массой от нескольких сотен килограммов до 40-50 т. Достоинством способа вакуумного дугового переплава является отсутствие контакта металла с огнеупорной футеровкой, недостатком -- невозможность снижения содержания серы (отсутствие шлаковой фазы). Дуговая выплавка отличается высокой концентрацией тепла в дуге, поэтому вакуумный дуговой переплав получил широкое распространение при производстве слитков из тугоплавких металлов (титана, циркония, ниобия, молибдена, вольфрама и др.).
|
В некоторых случаях изготовить расходуемый электрод невозможно (например, при переплаве титановой губки). В этих случаях губчатый или порошкообразный материал расплавляют, помещая его в зону дуги между постоянным (нерасходуемым) электродом и ванной. Такой метод называют вакуумный дуговой переплав с нерасходуемым электродом. Полученный таким образом слиток обычно еще раз переплавляют методом ВДП с расходуемым электродом. При вакуумном дуговом переплаве с нерасходуемым электродом вместо кристаллизатора иногда устанавливают металлический водоохлаждаемый тигель; во время плавки на стенках тигля образуется корочка переплавляемого металла (гарнисаж) и расплав контактирует с гарнисажем из этого же металла. Печи такого типа называют гарнисажными.
|
Вакуумные дуговые гарнисажные печи (ВДГП) используют также для фасонного литья отливок особо ответственного назначения (трубы, швелера, арматура и прочий металлопрокат). На рис. 2 изображена схема современной гарнисажной печи емкостью 0,6 т с разливкой металла по желобу. Плавильная поворотная камера соединена с двумя стационарными заливочными камерами с помощью патрубков и поворотных вакуумных уплотнителей. Нерасходуемые электроды обычно делают из вольфрама.
дуговая плавка печь
Преобразование электрической энергии в тепловую в дуговых печах происходит в электрической дуге, являющейся одной из форм дугового разряда в газах. При таком разряде в сравнительно небольшом объеме дуги можно сконцентрировать огромные мощности и получить очень высокие температуры. Высокая концентрация тепла в дуге позволяет с большой скоростью плавить и нагревать металл в дуговых печах до высокой температуры. Нагрев металла дугой можно осуществлять непосредственно (если дуга горит между электродом и расплавленным металлом) или излучением, когда дуга горит между двумя электродами. Печи первого типа - это дуговые печи прямого действия, второго типа -- дуговые печи косвенного действия. В печах косвенного нагрева очаг высокой температуры удален от поверхности металла на некоторое расстояние и на поверхность металла первоначально попадает лишь часть тепла, излучаемого дугой. Значительная его часть достигает поверхности металла после отражения от стен и свода, поэтому футеровка печи испытывает большие тепловые нагрузки. Низкая стойкость футеровки ограничивает возможность проведения в таких дуговых печах процессов, требующих нагрева металла свыше 1300--1400 °С, и не позволяет применять их для плавления тугоплавких металлов. В черной металлургии такие дуговые печи иногда используют в небольших литейных цехах для расплавления чугуна.
Печи с нерасходуемым электродом в настоящее время для промышленных целей не применяются и используются главным образом для выплавки небольших слиточков в лабораторно условиях.
Наиболее широкое применение в промышленности получили ваакумные электродуговые печи с расходуемым электродом.
Существует несколько конструкций вакуумных дуговых печей с расходуемым электродом, но принцип их действия один и тот же, а именно электрод, изготовленный из расплавляемого металла или сплава, оплавляется в электрической дуге, а образующийся жидкий металл стекает в кристаллизатор, где и происходит формирование слитка. Конструктивно эти печи состоят из следующих основных элементов:
|
1) плавильной камеры;
2) механизма подачи электрода;
3) кристаллизатора;
4) механизма вытяжки слитка;
5) вакуумного блока.
Плавильная камера представляет собой цилиндрический или прямоугольный стальной кожух. Обычно камеру изготовляют из нержавеющей стали, так как она должна быть немагнитной и коррозиестойкой.
Размеры камеры должны быть такими, чтобы было удобно разместить механизм подачи электрода и кристаллизатор. Цилиндрическая форма камеры более удобна в эксплуатации, ее легче чистить и она прочнее. Камера имеет люк, позволяющий проникать внутрь для очистки и установки электрода. Внутренняя ее поверхность должку быть гладкой, без выступов, чтобы не сконцентрировать заряды. Обычно плавильная камера имеет смотровые окна или вводы для приборов наблюдения. Рабочие камеры промышленных печей большой мощности имеют охлаждаемые водяные рубашки.
Расходуемый электрод переплавляемого металла крепится к штоку, имеющему водяные охлаждения. Шток вводится в печь через верхние втулки с подвижным вакуумным уплотнением.
Механизм подачи электродов может быть роликовый или цанговый. Наиболее надежной является цанговая подача; при роликовой подаче может быть проскальзывание электрода и ограничен размер электродов. На крупных печах в целях обеспечения центровки электрода применяется гибкая подвеска электрода.
Кристаллизатор представляет собой цилиндрический медный кожух с водоохлаждаемой рубашкой с толщиной стенки 6--8 мм. Применяются два типа кристаллизаторов: глухие на полную высоту слитка и низкие проходные для вытягивания слитков. На кристаллизаторе размещают соленоид для фокусировки дуги и перемешивания металла в ванне. Число ампервитков соленоида можно регулировать.
Охлаждение кристаллизатора осуществляется подачей воды в межрубашечное пространство через зазор в 2--10 мм. В ряде конструкций кристаллизаторов охлаждение производится через зазор между стенкой и рубашкой в 40--60 мм.
|
Для вытяжки слитка из кристаллизатора применяется механизм, состоящий из траверсы на двух синхронно вращающихся винтах. Такой механизм гарантирует достаточную скорость вытягивания, исключает перекосы и вибрацию штока.
На вакуумных дуговых печах широко применяется автоматизация, охватывающая собой автоматическое регулирование процесса горения дуги, длины дуги, а также вытягивания слитка. Все это обеспечивает получение качественного слитка.
Так, например, немецкой компанией ALD разработана специальная система автоматического контроля плавки AMC, осуществляющая строгий контроль всех параметров процесса. Функция логического контроля, постоянное взвешивание расходуемого электрода, регулирование по замкнутому циклу (напр. скорость плавки, дуговой промежуток на основе напряжения дуги или скорость падения коротких импульсов), сбор и управление данными осуществляются компьютерной системой. Компьютер для связи оператора с установкой (OIP) иерархически является задающим устройством системы автоматического контроля плавки (АМС). OIP служит для визуализации процесса, представления данных процесса, графического отображения и функциональных клавиш для команд оператора, редактирования и управления рецептами плавки, сбора и хранения данных, а также для создания отчетов по плавке. В качестве опции OIP может быть оборудован устройством для подключения к сети для переноса данных на другие компьютеры, подключенные к локальной сети (напр. контрольный компьютер, центральный блок обработки данных и т.д.) Все заданные параметры плавки сохраняются на жестком диске.
При выплавке сплавов используются печи, оборудованные бункерами, посредством которых легирующие добавки вводятся непосредственно в ванну жидкого металла. Под бункером устанавливается ленточный питатель и количество подаваемых легирующих добавок или раскислителей регулируется движением ленты питателя, а также шириной разгрузочной щели у бункерного затвора.
4.2 Основы процесса вакуумной дуговой плавки с расходуемым электродом
При разряде в дуговом промежутке возникает плазма, представляющая собой ионизированный поток частиц, нагретых до высокой температуры. В этой плазме (дуге) и происходит расплавление электрода переплавляемого металла или сплава.
Для обеспечения нормальных условий плавки и получения качественного слитка необходимо в каждом отдельном случае в зависимости от чистоты металла и состава сплава подбирать соответствующие режимы плавки, зависящие от длины дуги, от силы тока и других факторов.
|
При большой длине дуги могут образовываться побочные дуги («паразитные» разряды), которые перебрасываются на стенку кристаллизатора и приводят к его прожогу. Применение излишне длинной дуги приводит также к распылению металла, получению плохо проплавленных слитков с поверхностными дефектами и, кроме того, вызывает снижение коэффициента полезного действия печи.
Плавка на короткой дуге приводит к уменьшению размера жидкой ванны и увеличивает вероятность короткого замыкания между электродом и расплавом. Слишком короткая дуга способствует образованию настылей и может привести к неоднородности кристаллической структуры слитка и в некоторых случаях к появлению «паразитных» разрядов.
При плавке ниобия промышленной чистоты и некоторых его сплавов, как показывают опытные данные, длину дуги следует поддерживать в пределах 13--19 мм.
При плавке в вакуумных дуговых печах с расходуемым электродом устойчивость горения дуги в значительной степени зависит не только от ее длины, но и от применяемой силы тока. С увеличением силы тока, устойчивость горения дуги повышается.
Однако при этом возрастает температура электрода и жидкой ванны и, следовательно, увеличивается испаряемость. В результате повышается концентрация ионизированных паров и там, где эта концентрация выше, возникают побочные разряды и поэтому также нарушается стабильность горения дуги. Следовательно, при плавке металлов в вакуумных дуговых печах необходимо выбирать оптимальную величину силы тока конкретно для каждого переплавляемого материала.
Обычно плавка в вакуумных дуговых печах ведется на постоянном токе, что обеспечивает более устойчивую дугу. При применении переменного тока температура катода нестабильна, что затрудняет процесс горения дуги и делает ее менее устойчивой. При переходе тока через нулевое значение и перемене полярности в начале и конце каждого периода дуга гаснет и температура дугового промежутка снижается.
Но, несмотря на указанные трудности, плавка тугоплавких металлов, в том числе ниобия, на переменном токе возможна. В этом случае должны быть обеспечены достаточно большая плотность тока и непрерывным выход электронов для поддержания устойчивости дуги.
При плавке металлов в вакуумных дуговых печах происходят следующие процессы:
1) плавление металла;
2) удаление газовых летучих примесей, диссоциация неустойчивых соединений при высоких температурах в вакууме;
3) конденсация летучих компонентов на более холодной части печи или удаление их из печного пространства;
4) восстановление и раскисление металлов;
5) кристаллизация металла.
Рафинирование ниобия и других тугоплавких металлов от газов, неметаллических и металлических примесей происходит главным образом за счет испарения примесей и диссоциации соединений. Скорость испарения зависят от степени над расплавленным металлом, продолжительности выдержки его в этом состоянии и ряда других факторов.
При плавке на дуговых печах с расходуемым электродом в глубоком кристаллизаторе создается значительное сопротивление газовыделению из расплава, что способствует местному повышению давления в зоне плавления на 2-3 порядка.
Эффективность удаления газов и примесей путем испарения снижается в связи с ограниченным временем нахождения металла в расплавленном состоянии. Это связано с весьма высокими скоростями плавки на дуговых печах с расходуемым электродом, которые не могут быть снижены из-за сравнительно высокого значения минимально необходимой силы тока для поддержания дуги в стабильном состоянии.
По этим причинам рафинирование в дуговых вакуумных печах за счет испарения примесей затруднено. Но, несмотря на это, очистка ниобия при плавке в вакуумных дуговых печах может происходить за счет испарения низшего окисла, так как упругость паров NbO в 10 раз превышает упругость пара ниобия, а также за счет выделения СО при наличии в металле углерода.
Для того чтобы рафинирование проходило наиболее полно, при плавке необходимо соблюдать следующие условия:
1) ври выбранном размере кристаллизатора рекомендуется брать электроды наименьшего поперечного сечения, удовлетворяющие требованиям, необходимым для ведения плавки в данном кристаллизаторе;
2) режимы плавки должны быть такими, которые бы обеспечивали минимальную скорость плавления электрода;
3) давление в печи над зоной плавки должно быть по возможности более низким. Последнее, обеспечивается применением возможно коротких вакуумных присоединений и использованием вакуумных насосов высокой производительности.
ра.
СВОЙСТВА ВАКУУМНЫХ УСТАНОВОК
Преимущества вакуумных дуговых установок
Основные преимущества переплава расходуемых электродов в вакууме:
Удаление растворенных газов, напр. водорода, азота и СО;
Уменьшение нежелательных микроэлементов;
Уменьшение содержания оксидов;
Получение направленной структуры от нижней к верхней части слитка, что помогает избежать макроликвации и уменьшить микроликвацию.
Оксиды удаляются при помощи химических и физических процессов. Менее стабильные оксиды или нитриды термически разлагаются либо восстанавливаются при помощи углерода, входящего в состав сплава и удаляются во время газовой фазы. Однако в спецсплавах и высоколегированных сталях неметаллические включения, напр. карбонитриды титана или алюминия, очень стабильны. Эти включения удаляются в некотором количестве благодаря флотации во время плавки. Остающиеся включения разбиваются и равномерно распределяются в поперечном сечении слитка.
Возможности вакуумного электродугового переплава
1) Вес слитка до 50 тонн
2) Плавка электрода происходит в вакууме посредством дуги постоянного тока (заряд электрода отрицательный, расплав - положительный)
3) Величина тока до 40 кА
4) Значение вакуума: 1-0,1 Па (в некоторых случаях до 1000 Па)
5) Система контроля веса электрода
6) Неподвижная либо свободно стоящая конструкция подъемного крана
7) Система соосных подводов высокоамперного тока
8) Процесс плавки управляется при помощи компьютера в соответствии с заданной программой (контроль дугового промежутка, управление скоростью плавки, система сбора данных, распечатка протокола плавки)
Использование установок
1) Высокопрочные стали для колец ракетных ускрителей и труб высокого давления
2) Шарикоподшипниковые стали
3) Инструментальные стали для фрез, сверл, резцов и т.д.
4) Штамповые стали (горячие и холодные)
5) Плавление активных металлов (титан, цирконий и их сплавов) для авиакосмической, химической промышленности, для оборудования по добыче нефти на шельфе и для строительства реакторов.
Плазменно-дуговые печи
В таких установках металл нагревается за счет проходящей вместе со струей плазмы инертного газа электрической дуги. Такой процесс обеспечивает чистоту расплавляемого материала, а также позволяет значительно увеличить производительность печного оборудования.
В плазменно-дуговых печах происходит выплавка металлов с невысоким содержанием кислорода. Процесс плавления осуществляется в нейтральной атмосфере, что позволяет создать все условия для максимального выхода газов. Выплавка металла происходит с высокой скоростью.
Пламенно–дуговые печи используют для изготовления стали и сплавов высокого качества. Их применение обходится намного дешевле выплавки металла в вакуумных печах.
Преимущества и недостатки
Применение электродуговых печей для выплавки стали широко используется в металлургической промышленности. Основными преимуществами использования такого оборудования является возможность проведения таких операций:
расплавка шихты независимо от ее состава;
быстрый нагрев металла в печи; регулировка температурного режима;
раскисление металла и получение в результате материала с низким содержанием примесей.
При переплавке стали в печном агрегате создаются все условия для снижения угара легирующих компонентов. Это обеспечивает снизить потери металлов в результате окисления при высоких температурах.
Электродуговые агрегаты широко используются в промышленных целях для переплавки различных металлов. С их помощью можно получить качественные крепкие стальные сплавы. Эффективность работы дуговой печи во многом зависит от качества теплового прибора. Поэтому приобретать следует надежное оборудование у известных и проверенных производителей.
Вакуумная дуговая плавка
Дуговые печи, их виды и характеристики. Основы процесса вакуумной дуговой плавки с расходуемым электродом. Тепловые процессы, происходящие во время плавки. Преимущества вакуумных дуговых установок. Возможности вакуумного электродугового переплава.
Установки, в которых происходит превращение электрической энергии в другие виды с одновременным осуществлением технологических процессов, называют электротехнологическими. Эти установки имеют довольно сложную конструкцию и оборудование, Правильные монтаж, наладка и эксплуатация которого без знания выполняемого им технологического процесса затруднительны.
Технология вакуумно-дуговой выплавки широко используется для улучшения чистоты и структуры стандартных слитков, которые называются расходуемыми электродами, выплавленных в атмосфере либо в вакууме по технологии индукционной плавки. Стали и сплавы, а также титан и цирконий и их сплавы, имеют много областей применения, где решающее значение имеет чистота, однородность структуры, длительная прочность и прочность на срез. Авиакосмическая промышленность, производство энергии, оборонная, медицинская и атомная промышленность отдают предпочтение возможностям и характеристикам этих современных материалов.
При вакуумном дуговом переплаве под воздействием высоких температур, возникающих в зоне электрической дуги между переплавляемым электродом и поддоном кристаллизатора, сталь на нижнем торце электрода расплавляется и капли расплавленного металла падают в ванну, где под воздействием охлаждения кристаллизатора формируется слиток. До начала операции печь вакуумируют (остаточное давление обычно не более 1,33 Па); вакуумные насосы продолжают работать в течение всей плавки. Таким образом, капли металла падают через вакуумированное пространство, при этом обеспечивается очень полное очищение металла от газов, оксидных неметаллических включений (общее содержание кислорода снижается до очень низких пределов), от примесей некоторых цветных металлов и получается плотный слиток. Кристаллизация металла в водоохлаждаемом кристаллизаторе (обычно медном) имеет четко направленный характер, отвечающий направлению отвода тепла. В результате вакуумно дугового переплава механические характеристики металла улучшаются и становятся почти одинаковыми в различных направлениях. В современных установках вакуумно дугового переплава получают слитки массой от нескольких сотен килограммов до 40-50 т. Достоинством способа вакуумного дугового переплава является отсутствие контакта металла с огнеупорной футеровкой, недостатком -- невозможность снижения содержания серы (отсутствие шлаковой фазы). Дуговая выплавка отличается высокой концентрацией тепла в дуге, поэтому вакуумный дуговой переплав получил широкое распространение при производстве слитков из тугоплавких металлов (титана, циркония, ниобия, молибдена, вольфрама и др.).
В некоторых случаях изготовить расходуемый электрод невозможно (например, при переплаве титановой губки). В этих случаях губчатый или порошкообразный материал расплавляют, помещая его в зону дуги между постоянным (нерасходуемым) электродом и ванной. Такой метод называют вакуумный дуговой переплав с нерасходуемым электродом. Полученный таким образом слиток обычно еще раз переплавляют методом ВДП с расходуемым электродом. При вакуумном дуговом переплаве с нерасходуемым электродом вместо кристаллизатора иногда устанавливают металлический водоохлаждаемый тигель; во время плавки на стенках тигля образуется корочка переплавляемого металла (гарнисаж) и расплав контактирует с гарнисажем из этого же металла. Печи такого типа называют гарнисажными.
Вакуумные дуговые гарнисажные печи (ВДГП) используют также для фасонного литья отливок особо ответственного назначения (трубы, швелера, арматура и прочий металлопрокат). На рис. 2 изображена схема современной гарнисажной печи емкостью 0,6 т с разливкой металла по желобу. Плавильная поворотная камера соединена с двумя стационарными заливочными камерами с помощью патрубков и поворотных вакуумных уплотнителей. Нерасходуемые электроды обычно делают из вольфрама.
дуговая плавка печь
Преобразование электрической энергии в тепловую в дуговых печах происходит в электрической дуге, являющейся одной из форм дугового разряда в газах. При таком разряде в сравнительно небольшом объеме дуги можно сконцентрировать огромные мощности и получить очень высокие температуры. Высокая концентрация тепла в дуге позволяет с большой скоростью плавить и нагревать металл в дуговых печах до высокой температуры. Нагрев металла дугой можно осуществлять непосредственно (если дуга горит между электродом и расплавленным металлом) или излучением, когда дуга горит между двумя электродами. Печи первого типа - это дуговые печи прямого действия, второго типа -- дуговые печи косвенного действия. В печах косвенного нагрева очаг высокой температуры удален от поверхности металла на некоторое расстояние и на поверхность металла первоначально попадает лишь часть тепла, излучаемого дугой. Значительная его часть достигает поверхности металла после отражения от стен и свода, поэтому футеровка печи испытывает большие тепловые нагрузки. Низкая стойкость футеровки ограничивает возможность проведения в таких дуговых печах процессов, требующих нагрева металла свыше 1300--1400 °С, и не позволяет применять их для плавления тугоплавких металлов. В черной металлургии такие дуговые печи иногда используют в небольших литейных цехах для расплавления чугуна.
Печи с нерасходуемым электродом в настоящее время для промышленных целей не применяются и используются главным образом для выплавки небольших слиточков в лабораторно условиях.
Наиболее широкое применение в промышленности получили ваакумные электродуговые печи с расходуемым электродом.
Существует несколько конструкций вакуумных дуговых печей с расходуемым электродом, но принцип их действия один и тот же, а именно электрод, изготовленный из расплавляемого металла или сплава, оплавляется в электрической дуге, а образующийся жидкий металл стекает в кристаллизатор, где и происходит формирование слитка. Конструктивно эти печи состоят из следующих основных элементов:
1) плавильной камеры;
2) механизма подачи электрода;
3) кристаллизатора;
4) механизма вытяжки слитка;
5) вакуумного блока.
Плавильная камера представляет собой цилиндрический или прямоугольный стальной кожух. Обычно камеру изготовляют из нержавеющей стали, так как она должна быть немагнитной и коррозиестойкой.
Размеры камеры должны быть такими, чтобы было удобно разместить механизм подачи электрода и кристаллизатор. Цилиндрическая форма камеры более удобна в эксплуатации, ее легче чистить и она прочнее. Камера имеет люк, позволяющий проникать внутрь для очистки и установки электрода. Внутренняя ее поверхность должку быть гладкой, без выступов, чтобы не сконцентрировать заряды. Обычно плавильная камера имеет смотровые окна или вводы для приборов наблюдения. Рабочие камеры промышленных печей большой мощности имеют охлаждаемые водяные рубашки.
Расходуемый электрод переплавляемого металла крепится к штоку, имеющему водяные охлаждения. Шток вводится в печь через верхние втулки с подвижным вакуумным уплотнением.
Механизм подачи электродов может быть роликовый или цанговый. Наиболее надежной является цанговая подача; при роликовой подаче может быть проскальзывание электрода и ограничен размер электродов. На крупных печах в целях обеспечения центровки электрода применяется гибкая подвеска электрода.
Кристаллизатор представляет собой цилиндрический медный кожух с водоохлаждаемой рубашкой с толщиной стенки 6--8 мм. Применяются два типа кристаллизаторов: глухие на полную высоту слитка и низкие проходные для вытягивания слитков. На кристаллизаторе размещают соленоид для фокусировки дуги и перемешивания металла в ванне. Число ампервитков соленоида можно регулировать.
Охлаждение кристаллизатора осуществляется подачей воды в межрубашечное пространство через зазор в 2--10 мм. В ряде конструкций кристаллизаторов охлаждение производится через зазор между стенкой и рубашкой в 40--60 мм.
Для вытяжки слитка из кристаллизатора применяется механизм, состоящий из траверсы на двух синхронно вращающихся винтах. Такой механизм гарантирует достаточную скорость вытягивания, исключает перекосы и вибрацию штока.
На вакуумных дуговых печах широко применяется автоматизация, охватывающая собой автоматическое регулирование процесса горения дуги, длины дуги, а также вытягивания слитка. Все это обеспечивает получение качественного слитка.
Так, например, немецкой компанией ALD разработана специальная система автоматического контроля плавки AMC, осуществляющая строгий контроль всех параметров процесса. Функция логического контроля, постоянное взвешивание расходуемого электрода, регулирование по замкнутому циклу (напр. скорость плавки, дуговой промежуток на основе напряжения дуги или скорость падения коротких импульсов), сбор и управление данными осуществляются компьютерной системой. Компьютер для связи оператора с установкой (OIP) иерархически является задающим устройством системы автоматического контроля плавки (АМС). OIP служит для визуализации процесса, представления данных процесса, графического отображения и функциональных клавиш для команд оператора, редактирования и управления рецептами плавки, сбора и хранения данных, а также для создания отчетов по плавке. В качестве опции OIP может быть оборудован устройством для подключения к сети для переноса данных на другие компьютеры, подключенные к локальной сети (напр. контрольный компьютер, центральный блок обработки данных и т.д.) Все заданные параметры плавки сохраняются на жестком диске.
При выплавке сплавов используются печи, оборудованные бункерами, посредством которых легирующие добавки вводятся непосредственно в ванну жидкого металла. Под бункером устанавливается ленточный питатель и количество подаваемых легирующих добавок или раскислителей регулируется движением ленты питателя, а также шириной разгрузочной щели у бункерного затвора.
4.2 Основы процесса вакуумной дуговой плавки с расходуемым электродом
При разряде в дуговом промежутке возникает плазма, представляющая собой ионизированный поток частиц, нагретых до высокой температуры. В этой плазме (дуге) и происходит расплавление электрода переплавляемого металла или сплава.
Для обеспечения нормальных условий плавки и получения качественного слитка необходимо в каждом отдельном случае в зависимости от чистоты металла и состава сплава подбирать соответствующие режимы плавки, зависящие от длины дуги, от силы тока и других факторов.
При большой длине дуги могут образовываться побочные дуги («паразитные» разряды), которые перебрасываются на стенку кристаллизатора и приводят к его прожогу. Применение излишне длинной дуги приводит также к распылению металла, получению плохо проплавленных слитков с поверхностными дефектами и, кроме того, вызывает снижение коэффициента полезного действия печи.
Плавка на короткой дуге приводит к уменьшению размера жидкой ванны и увеличивает вероятность короткого замыкания между электродом и расплавом. Слишком короткая дуга способствует образованию настылей и может привести к неоднородности кристаллической структуры слитка и в некоторых случаях к появлению «паразитных» разрядов.
При плавке ниобия промышленной чистоты и некоторых его сплавов, как показывают опытные данные, длину дуги следует поддерживать в пределах 13--19 мм.
При плавке в вакуумных дуговых печах с расходуемым электродом устойчивость горения дуги в значительной степени зависит не только от ее длины, но и от применяемой силы тока. С увеличением силы тока, устойчивость горения дуги повышается.
Однако при этом возрастает температура электрода и жидкой ванны и, следовательно, увеличивается испаряемость. В результате повышается концентрация ионизированных паров и там, где эта концентрация выше, возникают побочные разряды и поэтому также нарушается стабильность горения дуги. Следовательно, при плавке металлов в вакуумных дуговых печах необходимо выбирать оптимальную величину силы тока конкретно для каждого переплавляемого материала.
Обычно плавка в вакуумных дуговых печах ведется на постоянном токе, что обеспечивает более устойчивую дугу. При применении переменного тока температура катода нестабильна, что затрудняет процесс горения дуги и делает ее менее устойчивой. При переходе тока через нулевое значение и перемене полярности в начале и конце каждого периода дуга гаснет и температура дугового промежутка снижается.
Но, несмотря на указанные трудности, плавка тугоплавких металлов, в том числе ниобия, на переменном токе возможна. В этом случае должны быть обеспечены достаточно большая плотность тока и непрерывным выход электронов для поддержания устойчивости дуги.
При плавке металлов в вакуумных дуговых печах происходят следующие процессы:
1) плавление металла;
2) удаление газовых летучих примесей, диссоциация неустойчивых соединений при высоких температурах в вакууме;
3) конденсация летучих компонентов на более холодной части печи или удаление их из печного пространства;
4) восстановление и раскисление металлов;
5) кристаллизация металла.
Рафинирование ниобия и других тугоплавких металлов от газов, неметаллических и металлических примесей происходит главным образом за счет испарения примесей и диссоциации соединений. Скорость испарения зависят от степени над расплавленным металлом, продолжительности выдержки его в этом состоянии и ряда других факторов.
При плавке на дуговых печах с расходуемым электродом в глубоком кристаллизаторе создается значительное сопротивление газовыделению из расплава, что способствует местному повышению давления в зоне плавления на 2-3 порядка.
Эффективность удаления газов и примесей путем испарения снижается в связи с ограниченным временем нахождения металла в расплавленном состоянии. Это связано с весьма высокими скоростями плавки на дуговых печах с расходуемым электродом, которые не могут быть снижены из-за сравнительно высокого значения минимально необходимой силы тока для поддержания дуги в стабильном состоянии.
По этим причинам рафинирование в дуговых вакуумных печах за счет испарения примесей затруднено. Но, несмотря на это, очистка ниобия при плавке в вакуумных дуговых печах может происходить за счет испарения низшего окисла, так как упругость паров NbO в 10 раз превышает упругость пара ниобия, а также за счет выделения СО при наличии в металле углерода.
Для того чтобы рафинирование проходило наиболее полно, при плавке необходимо соблюдать следующие условия:
1) ври выбранном размере кристаллизатора рекомендуется брать электроды наименьшего поперечного сечения, удовлетворяющие требованиям, необходимым для ведения плавки в данном кристаллизаторе;
2) режимы плавки должны быть такими, которые бы обеспечивали минимальную скорость плавления электрода;
3) давление в печи над зоной плавки должно быть по возможности более низким. Последнее, обеспечивается применением возможно коротких вакуумных присоединений и использованием вакуумных насосов высокой производительности.
ра.
СВОЙСТВА ВАКУУМНЫХ УСТАНОВОК
Преимущества вакуумных дуговых установок
Основные преимущества переплава расходуемых электродов в вакууме:
Удаление растворенных газов, напр. водорода, азота и СО;
Уменьшение нежелательных микроэлементов;
Уменьшение содержания оксидов;
Получение направленной структуры от нижней к верхней части слитка, что помогает избежать макроликвации и уменьшить микроликвацию.
Оксиды удаляются при помощи химических и физических процессов. Менее стабильные оксиды или нитриды термически разлагаются либо восстанавливаются при помощи углерода, входящего в состав сплава и удаляются во время газовой фазы. Однако в спецсплавах и высоколегированных сталях неметаллические включения, напр. карбонитриды титана или алюминия, очень стабильны. Эти включения удаляются в некотором количестве благодаря флотации во время плавки. Остающиеся включения разбиваются и равномерно распределяются в поперечном сечении слитка.
Возможности вакуумного электродугового переплава
1) Вес слитка до 50 тонн
2) Плавка электрода происходит в вакууме посредством дуги постоянно
|
|
Механическое удерживание земляных масс: Механическое удерживание земляных масс на склоне обеспечивают контрфорсными сооружениями различных конструкций...
Папиллярные узоры пальцев рук - маркер спортивных способностей: дерматоглифические признаки формируются на 3-5 месяце беременности, не изменяются в течение жизни...
Археология об основании Рима: Новые раскопки проясняют и такой острый дискуссионный вопрос, как дата самого возникновения Рима...
История развития пистолетов-пулеметов: Предпосылкой для возникновения пистолетов-пулеметов послужила давняя тенденция тяготения винтовок...
© cyberpedia.su 2017-2024 - Не является автором материалов. Исключительное право сохранено за автором текста.
Если вы не хотите, чтобы данный материал был у нас на сайте, перейдите по ссылке: Нарушение авторских прав. Мы поможем в написании вашей работы!