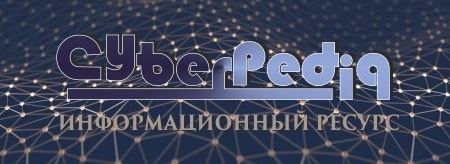
Биохимия спиртового брожения: Основу технологии получения пива составляет спиртовое брожение, - при котором сахар превращается...
Индивидуальные и групповые автопоилки: для животных. Схемы и конструкции...
Топ:
Особенности труда и отдыха в условиях низких температур: К работам при низких температурах на открытом воздухе и в не отапливаемых помещениях допускаются лица не моложе 18 лет, прошедшие...
Оснащения врачебно-сестринской бригады.
Выпускная квалификационная работа: Основная часть ВКР, как правило, состоит из двух-трех глав, каждая из которых, в свою очередь...
Интересное:
Отражение на счетах бухгалтерского учета процесса приобретения: Процесс заготовления представляет систему экономических событий, включающих приобретение организацией у поставщиков сырья...
Берегоукрепление оползневых склонов: На прибрежных склонах основной причиной развития оползневых процессов является подмыв водами рек естественных склонов...
Уполаживание и террасирование склонов: Если глубина оврага более 5 м необходимо устройство берм. Варианты использования оврагов для градостроительных целей...
Дисциплины:
![]() |
![]() |
5.00
из
|
Заказать работу |
|
|
ОАО «Беларуськалий» функционирует на базе одного из крупнейших в мире Старобинского месторождения калийных солей, открытого в 1949 году.
Освоение этого месторождения началось в 1958 году со строительства Первого Солигорского калийного комбината, первая очередь которого была введена в эксплуатацию в декабре 1963 года. В 1965 году был введен в эксплуатацию Второй, а в 1969 году – Третий Солигорские калийные комбинаты.
В 1970 году они были объединены в один комбинат "Беларуськалий", который в 1975 году был преобразован в ПО "Беларуськалий". В 1979 году в состав предприятия также вошел Четвертый Солигорский калийный завод. В 2001 г. ПО «Беларуськалий» преобразовано в Республиканское унитарное предприятие «ПО «Беларуськалий», в 2010 г. РУП «ПО «Беларуськалий» – в открытое акционерное общество «Беларуськалий».
Являясь одним из крупнейших в мире производителей хлористого калия
ОАО «Беларуськалий» оказывает определенное негативное воздействие на окружающую среду региона. Как любому горно-химическому предприятию, обществу присущ и ряд отрицательных факторов воздействия на окружающую среду. В первую очередь это:
- использование природных и энергетических ресурсов;
- оседание земной поверхности в результате ведения горных работ;
- образование значительного количества отходов обогащения с отчуждением земель для их хранения;
- выбросы и сбросы загрязняющих веществ в окружающую среду.
За весь период отработки месторождения добыто более 1,4 млрд. тонн руды. Добываемая руда имеет относительно невысокое содержание полезного компонента (хлористого калия), в среднем от 20 до 30%, в зависимости от отрабатываемого горизонта и системы разработки. Это определяет и образование значительного количества отходов при обогащении руды. Отходы переработки представлены двумя основными видами - твердыми галитовыми отходами, содержащими 92-95% хлористого натрия, и шламами галитовыми, глинисто-солевыми, представленными суспензией частиц хлористого калия, хлористого натрия и нерастворимого остатка в насыщенном водном растворе данных солей. Ежегодно, при существующем объеме производства в ОАО «Беларуськалий», образуется около 25 млн. тонн галитовых отходов и 3 млн. тонн шламов галитовых, глинисто-солевых, для складирования которых отведено под солеотвалы и шламохранилища свыше 2,1 тыс. га земель. В настоящее время общее количество складированных в солеотвалах и шламохранилищах отходов превышает 1000 млн. тонн. Такое количество отходов оказывает определенное негативное влияние на состояние окружающей среды, выражающееся в отчуждении земель, в загрязнении подземных вод солями, проникающими в водоносные горизонты в местах складирования отходов производства, образовании в результате воздействия атмосферных осадков значительного количества избыточных рассолов.
|
Для минимизации вредного воздействия производства на окружающую среду в обществе разработан и выполняется ряд мероприятий. В частности все более широко используется селективная отработка шахтных полей, при которой извлекаются продуктивные слои, а галитовый слой оставляется в выработанном пространстве, что позволяет уменьшить количество выдаваемой на поверхность пустой породы, и как следствие количества образующихся отходов, уменьшить площади отчуждаемых земель для создания хранилищ отходов, в определенной степени уменьшить оседание земной поверхности.
На всех рудоуправлениях внедрено высотное складирование галитовых отходов (100 и более метров). Это позволяет уменьшить как количество земель, занимаемых под складирование отходов, так и количество образующихся в результате воздействия атмосферных осадков избыточных рассолов. Ложа и дамбы солеотвалов и шламохранилищ оборудованы противофильтрационными экранами из полиэтиленовой пленки. В процессе эксплуатации осуществляется постоянный контроль за техническим состоянием дамб шламохранилищ, в том числе и с использованием геофизических методов.
|
Проводятся научно-исследовательские и опытные работы по таким направлениям, как совместное складирование галитовых и шламовых отходов, складирование галитовых отходов на отработанных площадях шламохранилищ.
Наиболее рациональным решением проблемы охраны окружающей среды от воздействия избыточных рассолов и продления срока службы шламохранилищявляется закачка избыточных рассолов в глубокие поглощающие горизонты. В 1986 году было осуществлено строительство опытно-промышленной установки по закачке рассолов в глубокие поглощающие горизонты (на глубину порядка 2000 метров) на 2 РУ. В 1999 году запущена в эксплуатацию установка по закачке избыточных рассолов на 3 РУ. В настоящее время их суммарная мощность составляет 1,8 млн. м3/год.
Существенным фактором воздействия на окружающую среду является оседание земной поверхности в результате проведения горных работ. Учитывая природные особенности Солигорского региона, а именно высокие уровни залегания грунтовых вод и равнинный рельеф местности, в ряде случаев это может приводить к заболачиванию земель. За весь период эксплуатации месторождения на 8,5 тыс. га земель в той или иной мере возникла необходимость и были проведены работы по понижению уровней грунтовых вод (открытые осушительные сети и польдерные системы).
Наиболее сложным является защита от подтопления населенных пунктов. До последнего времени водоотведение в населенных пунктах производилось только с использованием открытой осушительной сети и канав вдоль улиц. В настоящее время разработан перспективный метод осушения населенных пунктов с использованием лучевого дренажа, который позволяет обеспечить требуемую норму осушения без нарушения поверхности земли и строений. Разработан ряд проектов мер защиты населенных пунктов, основанных на данном методе.
ОАО «Беларуськалий» является достаточно энергоемким. В обществе имеется ТЭС, расположенная на территории 1 РУ, котельные на 2-ом и 3-ем рудоуправлениях, ТЭС 4 РУ, модульные котельные Краснослободского рудника, Березовского участка, цех мембранного электролиза.Всего в ОАО «Беларуськалий» сосредоточено 36 паровых, 35 водогрейных котлов, 44 технологические топки сушильных установок.Количество стационарных источников выбросов составляет более 1300.
|
Основным видом применяемого топлива в настоящее время является природный газ. Перевод на природный газ ТЭС, являющуюся источником теплоснабжения не только 1 РУ, но и г. Солигорска, ТЭС 4 РУ, котельных Общества и топливопотребляющих установок СОФ 1-4 РУ позволил существенно снизить валовый выброс загрязняющих веществ в атмосферу и, в связи с этим, улучшить экологические показатели.
Значительный объем работ выполняется обществом и по рациональному использованию водных ресурсов и защите водных источников от засоления. Техническое водоснабжение общества осуществляется из Солигорского водохранилища, водой питьевого качества - из водопровода «Белевичи» через городской коммунальный водопровод и из собственных скважинных водозаборов, расположенных в районе промплощадок рудоуправлений.
В целях рационального использования водных ресурсов и уменьшения влияния производства на качество водных объектов в ОАО «Беларуськалий» реализуются схемы повторного использования ливневых сточных вод в техническом водоснабжении общества.
Для получения систематической оперативной и полной информации о состоянии окружающей среды и источников загрязнений общества проводится мониторинг за состоянием атмосферного воздуха на границах санитарно-защитных зон рудоуправлений, источников выбросов, поверхностных и подземных вод, почвы, деформаций земной поверхности и др. Все это позволяет иметь достаточно полную информацию о фактическом состоянии окружающей среды.
1.3 Информация о продукции
Основным продуктом деятельности общества является мелкий и гранулированный хлористый калий с массовой долей калия в пересчете на К2О не ниже 60%.
Калийные руды – основное сырье для производства калийных, комплексных удобрений и других химических веществ.
|
Среди способов обогащения главное место занимают механический (флотация) и химический (галургия). В ОАО «Беларуськалий» применяются оба метода обогащения: 1 РУ, 2 РУ, 3 РУ – использует флотацию; 4 РУ – галургию.
Флотационным методом производится розово-красный мелкий и гранулированный хлористый калий. Массовая доля KCl в продукте составляет 95-96%. Извлечение полезного компонента при флотационном методе переработки составляет 85,5-87,2%. Технологический процесс переработки руды флотационным способом основан на различной способности поверхности сильвина и галита смачиваться водой, которое достигается их обработкой специфически действующими реагентами – поверхностно-активными веществами с последующим выделением в пену полезного компонента.Флотационный процесс состоит из следующих стадий:
- дробление руды с предварительнымгрохочением;
- измельчение руды с предварительной и поверочной классификацией;
- механическое и флотационное обесшламливание руды;
- флотация сильвина;
- выщелачивание хлорида натрия из флотационного концентрата;
- гидросгущение и обезвоживание хвостов флотации;
- гидроклассификация и обезвоживание концентрата;
- сгущение шламов;
- сушка концентрата;
- приготовление реагентов;
- гранулирование калия хлористого;
- облагораживание гранул;
- погрузка готовой продукции;
- складирование отходов производства.
Галургическим методом производится белый мелкокристаллический, крупнокристаллический и гранулированный хлористый калий. Крупнокристаллический продукт (при необходимости) может быть окрашен в розово-красный цвет. Массовая доля KCl в продукте составляет 96-99%. Извлечение полезного компонента при галургическом методе переработки составляет 88-89%.Технологический процесс переработки руды галургическим методом основан на физико-химических особенностях системы NaCl-KCl-H2O. В основе данного способа лежит различная зависимость растворимости составляющих минералов – сильвина и галита от температуры: повышенная растворимость хлористого калия из руды оборотным раствором при температуре +115оС и последующая кристаллизация полезного компонента при охлаждении.Галургический процесс состоит из следующих стадий:
- дробление руды с предварительнымгрохочением;
- подогрев щелоков;
- растворение руды;
- фильтрация галитовых отходов;
- осветление насыщенного щелока;
- кристаллизация хлористого калия;
- сгущение и центрифугирование хлоркалиевой суспензии;
- сушка калия хлористого;
- гранулирование калия хлористого;
- складирование, хранение и погрузка готовой продукции;
- охлаждение оборотной воды;
|
- приготовление реагентов;
- складирование отходов производства.
Кроме того, ОАО «Беларуськалий» выпускает пищевую поваренную, кормовую, техническую соли, азотно-фосфорно-калийные удобрения (в том числе тукосмеси), сильвинит.
Техническую соль получают по двум технологическим схемам:
- при добыче пищевой соли в условиях 1РУ;
- в процессе переработки сильвинитовой руды галургическим методом на 4РУ.
На 1РУ сырьем для производства соли технической, пищевой, кормовой рассыпной является соль каменная продуктивного пласта горизонта -305 м, представляющая собой физико-механическую смесь минералов галита (NaCl) с ограниченным количеством примесей нерастворимого в воде остатка, который представлен карбонатно-сульфатно-глинистым материалом природного происхождения. Каменная соль, в результате селективного метода добычи, классифицируется по содержанию нерастворимого остатка на техническую и пищевую для последующей раздельной переработки и получения продукции нормируемого качества.
Технологический процесс производства технической соли и соли поваренной кормовой рассыпной в условиях 1РУ состоит из следующих стадий:
- предварительное грохочение;
- дробление каменной соли;
- поверочное грохочение;
- приготовление реагента-антислеживателя и обработка продукции антислеживателем (по требованию потребителя);
- погрузка готовой продукции.
Технологический процесс производства соли каменной поваренной пищевой включает в себя следующие операции:
- измельчение каменной соли до необходимого помола;
- обеспыливание – классификация каменной соли;
- приготовление раствора йодата калия и обработка соли раствором йодата калия (для йодированной соли);
- упаковывание пищевой поваренной соли;
- складирование и погрузка готовой продукции.
Сырьем для производства соли поваренной кормовой брикетированной является пылевая фракция, полученная в результате обеспыливания поваренной пищевой соли. Технологический процесс производства кормовой брикетированной соли без добавок и с микроэлементами состоит из следующих стадий:
- сбор пылевой фракции;
- увлажнение пыли и внесение микроэлементов (для соли с микроэлементами);
- прессование;
- упаковка солебрикетов;
- складирование и погрузка готовой продукции.
Технологический процесс производства натрия хлористого технического и концентрата минерального - галита в условиях 4РУ включает следующие стадии:
- транспортировка обезвоженных твердых галитовых отходов на металлоулавливание;
- дробление до регламентной крупности;
- погрузка готовой продукции.
Тукосмеси азотно-фосфорно-калийные, производимые на 1 РУ, представляют собой механическую смесь готовых форм гранулированных азотных, фосфорных и калийных удобрений.
Технологический процесс производства удобрений азотно-фосфорно-калийных комплексных методом паровой грануляции основан на окатывании измельченных, увлажненных и подогретых исходных компонентов (кек калия хлористого, аммофос, диаммофос, карбамид, сульфат аммония).Удобренияазотно-фосфорно-калийные комплексные представляют собой гранулы круглой или овальной формы от светло-серого до красноватого цвета. В состав каждой гранулы одновременно входят три основных питательных элемента: азот (N), фосфор (Р2О5) и калий (К2О). Технологический процесс производства NPK удобрений состоит из следующих стадий:
- прием и складирование исходного сырья;
- дозирование, измельчение и подача исходных компонентов в технологический процесс;
- гранулирование методом окатывания;
- сушка продуктов окатывания;
- классификация горячей продукции с отделением ретура и охлаждениемнадрешетного продукта;
- контрольная классификация;
- складирование и отгрузка готовой продукции.
В цехе мембранного электролиза 4 РУ производятся гипохлорит натрия, гидроксид калия и соляная кислота.
Метод производства продукции заключается в получении гидроксида калия, хлора и водорода посредством электролиза очищенного раствора хлористого калия в электролизере мембранного типа. Газообразный хлор и водород используются для синтеза соляной кислоты, часть хлора абсорбируется раствором гидроксида натрия с получением гипохлорита натрия. Раствор гидроксида калия выпаривается до получения товарной концентрации или выпаривается и гранулируется с получением твердого (чешуированного) продукта.
Технологический процесс производства гипохлорита натрия, гидроксида калия и соляной кислоты состоит из следующих операций:
- солерастворение;
- очистка рассола (химическая, фильтрация, тонкая очистка в ионообменнике);
- мембранный электролиз;
- обработка анолита с охлаждением хлора (система анолита, дехлорированиеанолита, охлаждение хлора);
- обработка католита с охлаждением водорода;
- производство гипохлорита натрия (аварийная абсорбция, производство NaOCl);
- выпаривание и чешуирование гидроксида калия, фасовка чешуированного КОН;
- синтез соляной кислоты;
- хранение, погрузка готовых продуктов и вспомогательных материалов;
- производство деминерализованной воды;
- охлаждение оборотной воды,подготовка подпиточной воды;
- получение захоложенной воды;
- производство сжатого воздуха и воздуха, подаваемого наконтрольно-измерительные приборы;
- производство азота;
- нейтрализация и очистка сточных вод;
- удаление и складирование шламов галитовых, глинисто-солевых;
- солерастворение.
Калий хлористый и натрий хлористый, удобрения азотно-фосфорно-калийные, в окружающей среде не трансформируются. Возможно загрязнение атмосферного воздуха, почвы и водных объектов при нарушении правил транспортирования, обращения, хранения, превышении агрохимических норм внесения удобрений, в результате аварийных ситуаций.
Гипохлорит натрия, гидроксид калия и соляная кислота могут загрязнять окружающую среду при нарушении правил обращения, транспортирования, хранения, авариях и чрезвычайных ситуациях, размещения отходов в несанкционированных местах.
Информация по безопасному обращению, транспортированию, хранению приведена в технических условиях и стандартах на продукцию, паспортах безопасности, тарных этикетках.
|
|
История развития пистолетов-пулеметов: Предпосылкой для возникновения пистолетов-пулеметов послужила давняя тенденция тяготения винтовок...
Своеобразие русской архитектуры: Основной материал – дерево – быстрота постройки, но недолговечность и необходимость деления...
Эмиссия газов от очистных сооружений канализации: В последние годы внимание мирового сообщества сосредоточено на экологических проблемах...
Биохимия спиртового брожения: Основу технологии получения пива составляет спиртовое брожение, - при котором сахар превращается...
© cyberpedia.su 2017-2024 - Не является автором материалов. Исключительное право сохранено за автором текста.
Если вы не хотите, чтобы данный материал был у нас на сайте, перейдите по ссылке: Нарушение авторских прав. Мы поможем в написании вашей работы!