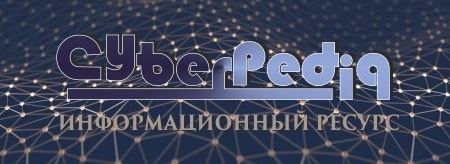
Таксономические единицы (категории) растений: Каждая система классификации состоит из определённых соподчиненных друг другу...
Семя – орган полового размножения и расселения растений: наружи у семян имеется плотный покров – кожура...
Топ:
Проблема типологии научных революций: Глобальные научные революции и типы научной рациональности...
Когда производится ограждение поезда, остановившегося на перегоне: Во всех случаях немедленно должно быть ограждено место препятствия для движения поездов на смежном пути двухпутного...
Марксистская теория происхождения государства: По мнению Маркса и Энгельса, в основе развития общества, происходящих в нем изменений лежит...
Интересное:
Финансовый рынок и его значение в управлении денежными потоками на современном этапе: любому предприятию для расширения производства и увеличения прибыли нужны...
Принципы управления денежными потоками: одним из методов контроля за состоянием денежной наличности является...
Аура как энергетическое поле: многослойную ауру человека можно представить себе подобным...
Дисциплины:
![]() |
![]() |
5.00
из
|
Заказать работу |
|
|
Процессов
Технико-экономические принципы и цель проектирова-
Ния технологических процессов изготовления деталей машин
Технико-экономические принципы проектирования. В основу
разработки технологических процессов кладутся два принципа: тех- нический и экономический. В соответствии с экономическим прин- ципом спроектированный технологический процесс должен полно- стью обеспечить выполнение всех требований рабочего чертежа и технических условий на изготовление заданного изделия.
В соответствии с экономическим принципом изготовление изде- лия должно вестись с минимальными затратами труда и с минималь- ными издержками производства. Технологический процесс изготов- ления изделий должен выполнятся с правильным и наиболее полным использованием всех технических возможностей оборудования, инст- румента и приспособления при наименьшей затрате времени и наи- меньшей себестоимости изделий.
Из нескольких возможных вариантов технологического процес- са изготовления одного и того же изделия, равноценных с позицией технического принципа проектирования, выбирается наиболее эффек- тивный производительный и рентабельный вариант. При равной про- изводительности сопоставляемых вариантов - выбирается наиболее рентабельный, а при равных рентабельностях - наиболее производи- тельный. При разных производительностях и рентабельностях выби- рается наиболее рентабельный при условии, что производительность всех сравниваемых вариантов не ниже заданной. В исключительных случаях (срочный выпуск особо важной продукции, расшивка «уз- ких» мест производства и пр.) в рамках данного завода и на опреде- ленный период времени за основу может быть принят наиболее про- изводительный вариант технологического процесса. Причем, выявле- ние эффективности и рентабельности проектируемого технологиче- ского процесса ведут по всем элементам, из которых они складыва- ются, либо определяют расчетом по укрупненным показателям.
|
Цель проектирования технологического процесса изготовления деталей машин. Проектирование технологических процессов изго- товления деталей машин имеет цель: установить тип производства с предварительным расчетом такта или размера партии деталей для од- новременного запуска в производство; выбрать метод получения за- готовки и сформировать предъявляемые к ней требования; составить план обработки детали с указанием принятых баз, последовательно-
сти и содержания технологических операций и переходов; определить промежуточные припуски и допуски на размеры заготовки по техно- логическим переходам; установить режимы резания и нормы времени на операции; определить потребное оборудование, приспособления и измерительные инструменты, а также профессию и квалификацию исполнителей.
На основе спроектированного технологического процесса уста- навливаются исходные данные для организации снабжения основны- ми и вспомогательными материалами, для календарного планирова- ния, технического контроля, инструментального и транспортного хо- зяйства.
Общая методика и последовательность проектирования
Технологических процессов
Проектирование технологического процесса - одна из основных
функций технологической подготовки производства изделий.
Задача проектирования технологических процессов характери- зуется многовариантностью возможных решений. Даже для сравни- тельно простых деталей может быть разработано несколько различ- ных технологических процессов, полностью обеспечивающих требо- вания рабочего чертежа и технических условий (ТУ). Методом после- довательного сопоставления этих вариантов по эффективности и рен- табельности окончательно отбирается один или небольшое число равноценных вариантов, из которых затем для конкретных производ- ственных условий выбирается один вариант.
|
Проектирование технологических процессов отличается слож- ностью и трудоемкостью. Как и многие виды проектирования, оно выполняется в несколько последовательных стадий. Вначале делают- ся предварительные наметки технологического процесса; на после- дующих стадиях они уточняются и конкретизируются на основе де- тальных технологических расчетов. В результате последовательного уточнения предварительных наметок получают законченные разра- ботки технологического процесса. Однако к правильному и приемле- мому решению обычно удается приблизится только после ряда попы- ток.
В условиях массового производства технологические процессы разрабатываются весьма подробно для всех деталей изделия. В еди- ничном производстве ограничиваются сокращенной разработкой, учитывая, что подробная разработка в данных условиях экономически
не оправдывается. Исключения составляют сложные и дорогие дета-
ли, особенно в тяжелом машиностроении. Для этих деталей техноло- гические процессы разрабатывается тщательно и подробно. В услови- ях серийного производства при широкой номенклатуре выпускаемых изделий проектируются обычно групповые технологические процес- сы.
Процесс проектирования состоит из комплекса взаимосвязанных и выполняемых в определенной последовательности этапов. К ним относятся: определения типа производства или темпа выпуска; анализ технологичности изделия и детали; выбор метода получения заготов- ки и установление предъявляемых к ней требований, выбор баз, вы- бор последовательности выполняемых методов (маршрута) обработки отдельных поверхностей, составление маршрута обработки детали в целом, предварительная наметка содержания операций, расчет про- межуточных пропусков, установление технологических допусков и предельных размеров заготовки по технологическим переходам, уточнение содержания и степени концентрации операций, выбор обо- рудования, инструментов и приспособлений, установление режимов резания, определение настроечных размеров, уточнение схемы уста- новки и закрепления заготовки для разработки задания на проектиро- вание специальных приспособлений, установление норм времени и квалификации исполнителей, оформление документации.
|
7. * Проектирование технологических процессов изго-
Товления деталей машин
7.4.1 Необходимые исходные данные для проектирования
Технологических процессов
Исходными данными для проектирования технологического
процесса являются:
1) рабочий чертеж, определяющий материал, конструктивные
формы и размеры детали;
2) технические условия на изготовление детали, характеризую- щие точность и качество обработки ее поверхностей, а также особые требования (твердость, структура, термообработка, балансировка и
пр.);
3) размер программного задания;
4) срок, в течение которого выполняется выпуск изделий;
5) дополнительные условия проектирования, такие как наличие
или отсутствие оборудования, возможности модернизации оборудо-
вания, наличие производственных площадей для расширения произ-
водства и возможности применения современных видов заготовок.
При проектировании используются справочные и нормативные материалы; каталоги и паспорта оборудования; альбомы приспособ- лений; ГОСТы и нормали на режущий и измерительный инструмент, нормативы по точности, шероховатости, расчету припусков, режимам резания и техническому нормированию времени; тарифно- квалификационные справочники и другие вспомогательные материа- лы.
При традиционном (неавтоматизированном) проектировании технологических процессов для оформления его результатов необхо- димо иметь бланки технологической документации.
Определения типа производства. Технологический кон- троль рабочего чертежа и технологических условий изготовления
Детали
Проектированию технологического процесса предшествует под-
робное изучение рабочего чертежа детали, технических условий на ее изготовление и условий ее работы в изделии. Проверяется достаточ- ность проекций, правильность простановки размеров, изучаются тре- бования по точности и шероховатости обработки поверхностей, а также другие требования технических условий. Нередко конструкто- ры ужесточают точность и шероховатость поверхностей детали, что усложняют технологический процесс ее изготовления. В таких случа- ях технологом могут быть предложены соответствующие коррективы и на основе совместного с конструктором обсуждения вопроса нахо- дится правильное решение.
|
При контроле рабочего чертежа выявляются возможности улучшения технологичности конструкции детали. В результате чего может быть получен значительный эффект в части снижения трудо- емкости и металлоемкости, возможности обработки детали высоко- производительными методами с обеспечением снижения себестоимо- сти и повышения рентабельности процессов обработки без ущерба для служебного назначения детали.
Типы производства. Типы производства определяются после
расчета такта выпуска tв [мин/шт.] заданной детали по формуле
tв F д ,
N
где Fд - действительный фонд рабочего времени (годовой, за смену
или другой период времени), в час; N - объем выпуска деталей за тот
же период времени, в шт.
Затем определяются коэффициенты загрузки оборудования на
каждой операцииh З i по формуле
h З * t штi ,
tв
где tштi - штучное время на i-ой операции.
Еслиh З i ³0,4, то Q * =1,0
Еслиh З i £0,4, то Qi 0,8.
h З i
Коэффициент закрепления операций определяется по формуле
Kз. о. å Qi ,
*
где * - число рабочих мест (операций).
По коэффициенту закрепления операций Кз.о определяется тип
производства:
если Кз.о. £ 10 - крупносерийное и массовое производство;
если 10< Кз.о. £ 20 - среднесерийное; если *0< Кз.о.. £ 4* - мелкосерийное; если 4*< Кз.о.. - единичное.
Величины tштi определяются либо по действующим на произ-
водстве технологическим процессам аналогичных деталей, либо по
предварительному укрупненному нормированию разрабатываемого
вновь технологического процесса. Величины tштi берутся для основ-
ных операций, исключая промывку детали, снятие фасок, зачистку и
т.п. Если * шт i > tв, то работа выполняется с использованием станков-
дублеров.
Для серийного производства рассчитывается оптимальное коли- чество деталей в партии для одновременного запуска в производство
по следующей формуле
nП N ⋅ a [шт],
F
где * - объем выпуска деталей в год шт.; F - число рабочих дней в
году (можно принять 2*0 дней); а - необходимый запас деталей на складе (для крупных деталей *¼3 дня, для мелких 5¼10 дней).
Величина партии деталей nП в дальнейших расчетах корректи-
руется с учетом удобства планирования и организации производства.
С этой целью размер партии устанавливается исходя из полной за- грузки оборудования или рабочих мест в течение целого числа смен,
кратного числу рабочих дней в планируемом периоде.
Для крупных деталей целесообразно размер партии деталей увя- зывать с имеющимися рабочими площадями рабочего места, необхо- димыми для размещения обрабатываемых деталей.
|
|
Типы оградительных сооружений в морском порту: По расположению оградительных сооружений в плане различают волноломы, обе оконечности...
Особенности сооружения опор в сложных условиях: Сооружение ВЛ в районах с суровыми климатическими и тяжелыми геологическими условиями...
Архитектура электронного правительства: Единая архитектура – это методологический подход при создании системы управления государства, который строится...
Папиллярные узоры пальцев рук - маркер спортивных способностей: дерматоглифические признаки формируются на 3-5 месяце беременности, не изменяются в течение жизни...
© cyberpedia.su 2017-2024 - Не является автором материалов. Исключительное право сохранено за автором текста.
Если вы не хотите, чтобы данный материал был у нас на сайте, перейдите по ссылке: Нарушение авторских прав. Мы поможем в написании вашей работы!