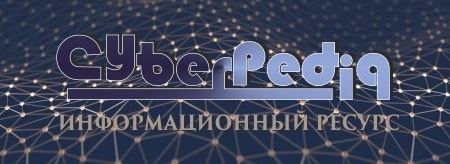
Механическое удерживание земляных масс: Механическое удерживание земляных масс на склоне обеспечивают контрфорсными сооружениями различных конструкций...
Семя – орган полового размножения и расселения растений: наружи у семян имеется плотный покров – кожура...
Топ:
Эволюция кровеносной системы позвоночных животных: Биологическая эволюция – необратимый процесс исторического развития живой природы...
Особенности труда и отдыха в условиях низких температур: К работам при низких температурах на открытом воздухе и в не отапливаемых помещениях допускаются лица не моложе 18 лет, прошедшие...
Организация стока поверхностных вод: Наибольшее количество влаги на земном шаре испаряется с поверхности морей и океанов...
Интересное:
Наиболее распространенные виды рака: Раковая опухоль — это самостоятельное новообразование, которое может возникнуть и от повышенного давления...
Влияние предпринимательской среды на эффективное функционирование предприятия: Предпринимательская среда – это совокупность внешних и внутренних факторов, оказывающих влияние на функционирование фирмы...
Уполаживание и террасирование склонов: Если глубина оврага более 5 м необходимо устройство берм. Варианты использования оврагов для градостроительных целей...
Дисциплины:
![]() |
![]() |
5.00
из
|
Заказать работу |
|
|
Аналитическим методом
В связи с тем, что расчетно-аналитический метод находит наи-
большее применение в серийном и массовом производстве, где работа ведется в основном на настроенных станках, поэтому рассмотрим бо- лее подробно порядок расчета припусков на обработку и предельных размеров заготовки по технологическим переходам для случая одно- проходной обработки.
Расчет выполняется в следующей последовательности:
1) для обрабатываемой заготовки намечаются установочные ба-
зы и технологический маршрут обработки;
2) записываются в расчетную карту (табл. 3.1) обрабатываемые элементарные поверхности и последовательный порядок технологи-
ческих переходов обработки по каждой элементарной поверхности;
3) записываются значения Rzi -1, Ti -1, r i -1, e i, иd i- * с использовани-
ем необходимых нормативных материалов;
4) определяются расчетные величины минимальных припусков
на обработку Zi min по всем технологическим переходам;
5) записываются для конечного перехода в графу «расчетный
размер»:
а) для наружных поверхностей - наименьший предельный раз-
мер детали по чертежу,
б) для внутренних поверхностей - наибольший предельный раз-
мер детали по чертежу;
6) для перехода, предшествующего конечному, определяется
расчетный размер путем:
а) для наружных поверхностей - прибавлением к наименьшему предельному размеру по чертежу величины расчетного минимального
припуска Zi min,
б) для внутренних поверхностей - вычитанием из наибольшего
предельного размера по чертежу величины расчетного минимального
припуска Zi min;
7) последовательно определяются расчетные размеры для каж-
дого предшествующего перехода путем:
|
а) для наружных поверхностей - прибавлением к расчетному
размеру величины расчетного припуска Zi *in следующего за ним
смежного перехода,
б) для внутренних поверхностей - вычитанием из расчетного
размера величины расчетного припуска Z* min следующего за ним
смежного перехода;
8) записываются:
а) для наружных поверхностей - наименьшие предельные раз-
меры, полученные путем увеличения наименьшего предельного раз- мера на величину расчетного припуска по всем технологическим пе- реходам с округлением результата до того же знака десятичной дро-
би, с каким дан допуск на размер,
б) для внутренних поверхностей - наибольшие предельные раз- меры, полученные путем вычитания величины расчетного припуска
из наибольшего предельного размера по всем технологическим пере-
ходам с округлением результата до того же знака десятичной дроби, с
каким дан допуск на размер;
9) определяются:
а) для наружных поверхностей - наибольшие предельные раз-
меры путем прибавления допуска к округленному наименьшему пре-
дельному размеру,
б) для внутренних поверхностей - наименьшие предельные раз- меры путем вычитания допуска из округленного наибольшего пре-
дельного размера;
10) записываются предельные размеры припусков:
а) для наружных поверхностей - * i m * x как разность наибольших
предельных размеров и Zi min как разность наименьших предельных
размеров предшествующего и выполняемого перехода,
б) для внутренних поверхностей - Zi m * x как разность наимень-
ших предельных размеров и Zi min как разность наибольших предель-
ных размеров выполняемого и предшествующего перехода;
11) определяются общие припуски Z * max и Zo m * n, суммированием
соответствующих припусков;
*2) проверяется правильность произведенных расчетов путем
сопоставления разности припусков Z * * in - Z * m * n и допусков. При этом
разность промежуточных припусков должна быть равна разности до-
пусков на промежуточные размеры, а разность общих припусков ** max
|
и Zo m * n должна быть равна разности допусков на размеры черновой за-
готовки и готовой детали.
Способы и методы обработки поверхностей
Деталей машин
Получение заданных форм, размеров и шероховатости поверх-
ностей деталей машин достигается обычно соответствующей обра- боткой заготовок. Доминирующее значение в современном машино- строении имеет удаление металла в виде стружки (обработка резани- ем); применяется также обработка пластическим деформированием, термическая и химико-термическая обработка. Наряду с обработкой на станках используется и слесарная обработка особенно в единичном и мелкосерийном производстве, а также при ремонтных работах для пригонки сопрягаемых деталей машин.
Предварительная обработка литых и кованых заготовок пре- дусматривает удаление заусенцев, пригара, прибылей и напусков. Очистка производится на обдирочно-шлифовальных станках, круп- ные заготовки обрубаются пневматическими зубилами, зачищаются шлифовальными машинками.
Очистку поверхностей производят также вращающимися прово- лочными щетками или в дробеструйных камерах. Мелкие заготовки очищают большей частью в очистных вращающихся барабанах, в струе рабочей жидкости, состоящей из кальцинированной соды, воды, и направляемой под давлением на поверхность обрабатываемой заго- товки. Поковки и штамповки из высокоуглеродистых сталей, чугун- ные и стальные отливки подвергают зачастую термической обработке (отжигу или нормализации) для улучшения структуры и обрабаты- ваемости.
Заготовки подвергаются обработке:
*) металлическими инструментами: резцами, в том числе вибро-
резанием, фрезами, сверлами, зенкерами, развертками, протяжками и т.д.
2) абразивными инструментами: шлифованием, в том числе об- работка алмазными кругами, хонингованием, суперфинишем, ульт- рофинишем, притиркой, полированием, шлифованием и полировани- ем лентами, обработкой абразивной струей.
3) без удаления металла: термической и химико-термической, пластическим деформированием (упрочняющая технология) - обкатывание поверхностей роликами и шариками; обработка отверстий
шариками, оправками и раскатками; а также дробеструйный наклеп.
Электромеханическая обработка подразделяется на электроме-
ханическое точение и электромеханическое сглаживание.
|
Электромеханическое точение осуществляется в условиях ме- стного нагрева снимаемого слоя металла при подводе в зону резания электротока большой силы (3*0-*000 А) и малого напряжения (1-* В). Нагревом охватывается зона перед режущей кромкой резца, что сни- жает силы резания и благоприятно сказывается на уменьшении шеро- ховатости обработанной поверхности.
Электромеханическое сглаживани е основано на деформирова- нии роликом или полировальником скользящего трения микронеров- ностей поверхности с подогревом ее электротоком. Получается шеро-
ховатость поверхности Ra =0,3*. Сочетание теплового (температура в
зоне контакта достигает 800-900C) и силового воздействия изменяет
структуру и механические свойства поверхностного слоя (на глубину 0,1-*,1* мм), повышая его твердость и износостойкость.
Электроэрозионная обработка предназначена для обработки особо труднообрабатываемых конструкционных материалов с помо- щью электрических разрядов, причем к заготовке подводится поло- жительный заряд, а к электроду - отрицательный заряд.
Электроэрозионная обработка может выполняться четырьмя
способами:
*) Электроискровая обработка основана на использовании кратковременных искровых зарядов с частичным их переходом в ду- говой разряд получаемых от электрического генератора импульсов. Деталь и инструмент помещаются в диэлектрическую жидкость, ко- торая препятствует расширению зоны действия разряда, способствуя концентрации тепловой энергии на малом участке поверхности. Тем-
пература достигает 10000C и вызывает быстрый износ электродов-
инструментов. Метод малопроизводителен, т.к. продолжительность паузы между разрядами в *-10 раз превышает продолжительность са- мого разряда.
2) При электроимпульсной обработке специальный генератор дает более продолжительный и мощный разряд, что снижает темпера-
туру до 40*0-5000C и уменьшает износ инструмента. Производи-
тельность повышается в десятки раз. Этим методом можно обрабатывать сложные фасонные поверхности с точностью до 0,*3-0,05 мм и
отверстия с точностью 0,01-0,0* мм.
3) При анодно-механической обработке для создания кратко- временных разрядов используется быстрое перемещение инструмента относительно обрабатываемой заготовки. Инструментом служит либо вращающийся металлический диск, либо движущаяся бесконечная металлическая лента или проволока, к которой подводиться отрица- тельный заряд. В зону обработки подается электролит, который соз- дает на поверхности заготовки токонепроводящую изолирующую пленку. При соприкосновении заготовки с инструментом он на не- больших участках удаляет пленку и в этих местах возникают кратко- временные дуговые разряды.
|
4) При электроконтактном способе для создания кратковре- менных разрядов также используется быстрое перемещение инстру- мента относительно обрабатываемой заготовки. Однако электролит не применяется, и процесс осуществляется преимущественно в воздухе. Скорость перемещения инструмента в 2,5-3 раза больше, чем при анодно-механическом способе. Этот способ позволяет подводить к месту обработки очень большие мощности, измеряемые сотнями кВт. Однако на заготовке остается слой оплавленного металла (глубиной 1-1,5 мм), для удаления которого требуется дополнительная механи- ческая обработка.
Электрогидравлическая обработка основана на анодном рас- творении металла с прокачкой электролита между заготовкой и элек- тродом. Этот метод характерен применением постоянного тока на- пряжения 12-25 В, дешевизной электролита (водный раствор пова- ренной соли), отсутствием износа электродов (прокачка электролита предупреждает оседание металла на инструменте-катоде) и большой производительностью обработки, не зависящей от размеров и мате- риала заготовок. Электрогидравлическая обработка обеспечивает точность сложных заготовок - 0,1 мм при глубине дефектного слоя приблизительно равном 0,005-0,05 мм и шероховатость обработан-
ной поверхности * a =2,5-1,25.
Электроабразивная обработка основана на электрохимическом
растворении твердого материала при механическом удалении продук- тов растворения из зоны обработки. Отличается этот метод от анодно- механической обработки тем, что используется только один инстру- мент - электропроводный абразив, являющийся одновременно и ка- тодом, и инструментом, удаляющим анодную пленку. Э лектро-абразивная обработка обеспечивает Ra =0,08-0,04 и производитель-
ность 20-25 мм3/мм при обработке твердосплавных материалов.
При ультрозвуковой обработке вибрирующий с определенной амплитудой и частотой инструмент перемещается перпендикулярно к обрабатываемой поверхности. В зону обработки вводится суспензия абразива. Ультразвуковые колебания образуют в жидкости кавитаци- онные пузырьки, захлюпывание которых вызывает гидравлические удары, разрушающие твердые и хрупкие материалы. Наличие абрази- ва ускоряет разрушение материала. Разрушенный материал удаляется из зоны обработки вместе с циркулирующей суспензией абразива. Инструмент внедряется в обрабатываемую заготовку и воспроизводит в ней отверстие соответствующей формы и размера. Применяется также ультразвуковое шлифование и хонингование.
|
Для ведения ультразвуковой обработки применяют станки, ра- ботающие в диапазоне частот 15-30 кГц с амплитудой колебаний - 0,05 мм и выходной мощностью 0,*-10 кВт. Этим методом обрабаты- вают сложные профили в твердых и хрупких материалах (тантал, мо- либден, алмаз, стекло, фарфор и т.д.), при этом обеспечивается 6-7
квалитет точности и шероховатость Ra =0,16-0,04.
Обработка металлов электронным лучом осуществляется в ва-
кууме на установках, позволяющих создавать концентрированный поток электронов по направлению к обрабатываемой заготовке. На- правление потока электронов корректируется электромагнитными ка- тушками и собирается в фокус электромагнитной линзой. Рабочая
температура достигает 6000C, что приводит к испарению металла,
образуя в заготовке отверстие диаметром 0,001 мм или прорезь ши- риной до 0,0* мм с ровными краями. Метод позволяет обрабатывать разнообразные материалы с высокой степенью точности.
При обработке дуговой плазменной струей температура дости-
гает 15000C. Этим методом можно резать, наносить покрытия и вы-
полнять другую обработку заготовок из разнообразных материалов- проводников, полупроводников и диэлектриков. Кроме разделитель- ной резки, можно осуществлять строгание плоскостей, подготовку под сварку кромок листов из нержавеющей стали и других металлов и сплавов.
Обработка с применением квантовых генераторов (лазеров). Оптический квантовый генератор (лазер) состоит из активного веще- ства (например, кристалла синтетического рубина с примесью хрома длинной 50 мм и диаметром 5 мм), объемного резонатора, образованного двумя полупрозрачными зеркалами, источника питания и источ-
ника возбуждения - спиральной стеклянной трубки, мощной газораз- рядной лампы, которая обвивает кристалл рубина.
Чередующимися вспышками лампы атомы хрома в рубиновом кристалле возбуждаются и переводятся на более высокий энергетиче- ский уровень. В рубине возникает избыток возбужденных атомов. Посторонний квант, встретившись с насыщенным энергией атомом, выбивает у него квант, и вдоль кристалла летят уже два кванта, кото- рые по дороге выбивают все новые и новые кванты, т.е. процесс при- обретает характер лавины. Торцы кристалла рубина тщательно отпо- лированы, и один из них полупосеребрен, а второй посеребрен и яв- ляется зеркалом. Кванты со скоростью света летят от торца к торцу и, благодаря все нарастающей мощности, наконец, прорываются через полупосеребренный торец в виде тонкого красного луча, обладающе- го высокой монохроматичностью (одноцветностью). С помощью линз при непрозрачной преграде возникает световое давление, достигаю- щее миллиона атмосфер. Лазер работает импульсами продолжитель- ностью 1,5 тысячной доли секунды. Лазером прошиваются алмазы, сапфиры толщиной в несколько миллиметров. Луч лазера использует- ся для сварки, плавки, испарения вещества, разрезки и т.д. Конструк- тивным недостатком существующих лазеров является низкий КПД - 0,5%.
Электрохимическая обработка. В технологии машиностроения все более тесным становится содружество электричества, химии и механики. Химические реактивы создают на обрабатываемой поверх- ности более мягкую, чем основной металл пленку, электричество ин- тенсифицирует процесс ее образования, а механические установки удаляют нарастающий поляризационный слой. Таким образом, осу- ществляется электрохимические точение, фрезерование, сверление, шлифование.
При электрохимическом шлифовании 9/10 металла снимается за счет электрохимического растворения и 1/10 - абразивом. Обработка удешевляется в 5-10 раз. Повышается качество шлифуемой поверхно- сти, т.к. в зоне резания не возникает больших температур.
|
|
Архитектура электронного правительства: Единая архитектура – это методологический подход при создании системы управления государства, который строится...
Опора деревянной одностоечной и способы укрепление угловых опор: Опоры ВЛ - конструкции, предназначенные для поддерживания проводов на необходимой высоте над землей, водой...
Индивидуальные очистные сооружения: К классу индивидуальных очистных сооружений относят сооружения, пропускная способность которых...
Особенности сооружения опор в сложных условиях: Сооружение ВЛ в районах с суровыми климатическими и тяжелыми геологическими условиями...
© cyberpedia.su 2017-2024 - Не является автором материалов. Исключительное право сохранено за автором текста.
Если вы не хотите, чтобы данный материал был у нас на сайте, перейдите по ссылке: Нарушение авторских прав. Мы поможем в написании вашей работы!