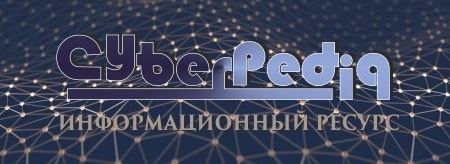
Эмиссия газов от очистных сооружений канализации: В последние годы внимание мирового сообщества сосредоточено на экологических проблемах...
История развития пистолетов-пулеметов: Предпосылкой для возникновения пистолетов-пулеметов послужила давняя тенденция тяготения винтовок...
Топ:
Техника безопасности при работе на пароконвектомате: К обслуживанию пароконвектомата допускаются лица, прошедшие технический минимум по эксплуатации оборудования...
Эволюция кровеносной системы позвоночных животных: Биологическая эволюция – необратимый процесс исторического развития живой природы...
Особенности труда и отдыха в условиях низких температур: К работам при низких температурах на открытом воздухе и в не отапливаемых помещениях допускаются лица не моложе 18 лет, прошедшие...
Интересное:
Влияние предпринимательской среды на эффективное функционирование предприятия: Предпринимательская среда – это совокупность внешних и внутренних факторов, оказывающих влияние на функционирование фирмы...
Искусственное повышение поверхности территории: Варианты искусственного повышения поверхности территории необходимо выбирать на основе анализа следующих характеристик защищаемой территории...
Уполаживание и террасирование склонов: Если глубина оврага более 5 м необходимо устройство берм. Варианты использования оврагов для градостроительных целей...
Дисциплины:
![]() |
![]() |
5.00
из
|
Заказать работу |
|
|
Распиливание и припасовка
Распиливание
Распиливанием называется обработка отверстий с целью придания им нужной формы. Обработка круглых отверстий производится круглыми и полукруглыми напильниками; трехгранных отверстий - трехгранными, ножовочными и ромбическими напильниками; квадратных - квадратными напильниками.
Подготовка к распиливанию начинается с разметки и накернивания разметочных рисок, затем сверлят отверстия по разметочным рискам и вырубают проймы, образованные высверливанием. Наилучшей получается разметка на металлической поверхности, отшлифованной наждачной бумагой.
Под распиливание сверлят одно отверстие, когда пройма небольшая; в больших проймах сверлят два или несколько отверстий в целях оставления наименьшего припуска на распиливание. Большие перемычки трудно удалить из просверленной проймы, однако нельзя располагать отверстия и слишком близко во избежание сдваивания, что может привести к поломке сверла.
Распиливание в заготовке воротка квадратного отверстия. Вначале размечают квадрат, а в нем - отверстие (рис. 334, а), затем
просверливают отверстие сверлом, диаметр которого на 0,5 мм меньше стороны квадрата. В просверленном отверстии пропиливают четыре угла квадратным напильником, не доходя 0,5 -0,7 мм до разметочных рисок, после чего распиливают отверстие до разметочных рисок в такой последовательности: вначале пропиливают стороны 7 и 3, затем 2 и 4 и производят подгонку отверстия по метчику так, чтобы он входил в отверстие только на глубину 2 - 3 мм.
Дальнейшую обработку сторон (рис. 334,6) производят до тех пор, пока квадратная головка легко, но плотно не войдет в отверстие.
Распиливание в заготовке трехгранного отверстия. Размечают контур треугольника, а в нем - отверстие и сверлят его сверлом, не касаясь разметочных рисок треугольника (рис. 335,а,б). Затем в круглом отверстии пропиливают три угла и последовательно распиливают стороны 7,2 и 3, не доходя 0,5 мм до разметочной риски, после чего подгоняют стороны треугольника (рис. 335,в).
|
Рис. 334. Распиливание квадратного отверстия: а - разметка, б - прием распиливания
Рис. 335. Распиливание трехгранного отверстия: а - разметка, б - высверленное отверстие, в - порядок распиливания, г - проверка вкладышем
При работе трехгранным напильником стремятся избежать поднутрения сторон, опиливают строго прямолинейно. Точность обработки проверяют вкладышем (рис. 335,г).
При подгонке следует следить за тем, чтобы вкладыш входил в распиливаемое отверстие свободно, без перекоса и плотно. Зазор между сторонами треугольника и вкладышем при проверке щупом должен быть не более 0,05 мм.
Пригонка и припасовка
Пригонкой называется обработка одной детали по другой с тем, чтобы выполнить соединение. Для пригонки необходимо, чтобы одна из деталей была совершенно готовой, по ней ведут пригонку. Пригонка широко применяется при ремонтных работах, а также при сборке единичных изделий.
Пригонка напильником является одной из труднейших в работе слесаря, так как обрабатывать приходится в труднодоступных местах. Целесообразно эту операцию выполнять борнапильниками, шлифовальными борголовками, применяя опиловочно-зачистные станки.
При подгонке вкладыша по готовому отверстию работа сводится к обычному опиливанию. При пригонке по большому числу поверхностей сначала обрабатывают две сопряженные базовые стороны, затем подгоняют две остальные до получения нужного сопряжения. Детали должны входить одна в другую без качки, свободно. Если изделие на просвет не проглядывается, ведут припиливание по краске.
Иногда на подгоняемых поверхностях и без краски можно различить следы от трения одной поверхности по другой. Следы, имеющие вид блестящих пятен ("светлячки"), показывают, что данное место мешает движению одной детали по другой. Эти места (выступы) удаляют, добиваясь или отсутствия блеска, или равномерного блеска по всей поверхности.
|
При любых пригоночных работах нельзя оставлять острых ребер и заусенцев на деталях, их нужно сглаживать личным напильником. Насколько хорошо сглажено ребро, можно определить, проведя по нему пальцем.
Припасовкой называется точная взаимная пригонка деталей, соединяющихся без зазоров при любых перекантовках. Припасовка отличается высокой точностью обработки, что необходимо для беззазорного сопряжения деталей (световая щель более 0,002 мм просматривается).
Припасовывают как замкнутые, так и полузамкнутые контуры. Из двух припасовываемых деталей отверстие принято называть проймой, а деталь, входящую в пройму, - вкладышем.
Проймы бывают открытыми (рис. 336) и замкнутыми (см. рис. 335). Выполняется припасовка напильниками с мелкой и очень мелкой насечкой - № 2, 3, 4 и 5, а также абразивными порошками и пастами.
При изготовлении и припасовке шаблонов с полукруглыми наружным и внутренним контурами вначале изготовляют деталь с внутренним контуром - пройму (1-я операция) (рис. 336,а). К обработанной пройме подгоняют (припасовывают) вкладыш (рис. 336,6) (2-я операция).
При обработке проймы сначала точно опиливают широкие плоскости как базовые поверхности, затем начерно ребра (узкие грани) 1,2,3 и 4, после чего размечают циркулем полуокружность, вырезают ее ножовкой (как показано штрихом на рисунке); производят точное опиливание полукруглой выемки (рис. 336,в) и проверяют точность обработки вкладышем, а также на симметричность по отношению к оси при помощи штангенциркуля.
При обработке вкладыша сначала опиливают широкие поверхности, а потом ребра 1, 2 и 3. Далее размечают и вырезают ножовкой углы. После этого производят точное опиливание и припасовку ребер 5 и 6. Затем выполняется точное опиливание и припасовка вкладыша к пройме. Точность припасовки считается достаточной, если вкладыш входит в пройму без перекоса, качки и просветов (рис. 336,г).
Рис. 336. Припасовка: а - разметка, б - подгонка, в - подпиливание, г - проверка вкладышем
Рис. 337. Припасовка косоугольных вкладышей: а - схема разметки наружных углов, б - опиливание наружной поверхности, в - схема разметки внутренних углов, г - опиливание внутренних углов, д - проверка вкладышем
|
При изготовлении и припасовке косоугольных вкладышей и пройм типа "ласточкин хвост" (рис. 337,з, 6) сначала обрабатываю-*- вкладыш (обработка и проверка его проще). Обработку ведут в следующем порядке (рис. 337,6). Вначале точно опиливают широкие плоскости как базовые поверхности, затем все четыре узких грани (ребра) 1, 2, 3 и 4. Далее размечают острые углы (рис. 337,в), вырезают их ножовкой и точно опиливают. Сначала опиливают ребра 5 и 6 (рис. 337,в,г) в плоскости, параллельной ребру 7, затем ребрам 7 и 8 (рис. 337,а) по линейке и под углом 60° к ребру 4. Острый угол (60°) измеряют угловым шаблоном.
Пройма обрабатывается в следующем порядке. Вначале точно опиливают широкие плоскости, после чего опиливают все четыре ребра.
Далее производится разметка, вырезка ножовкой паза (на рис. 337,в показано штрихом) и опиливание ребер 5, 6 и 7. Сначала ширина паза делается меньше требуемой на 0,05 - 0,1 мм при сохранении строгой симметричности боковых ребер паза по отношению к оси проймы, глубина паза выполняется сразу точной по размеру. Затем при припасовке вкладыша и проймы ширина паза получает точный размер по форме выступа вкладыша. Точность припасовки считается достаточной, если вкладыш входит в пройму туго от руки, без просветов, качки и перекосов (рис. 337, д).
Ручное распиливание, пригонка и припасовка - очень трудоемкие операции. В современных условиях эти операции выполняют с использованием металлорежущего оборудования общего и специального назначения, при котором роль слесаря сводится к управлению машинами и контролю размеров.
Криволинейные и фасонные детали обрабатывают на шлифовальных станках специальными профилированными абразивными кругами. Широкое применение также находят электроискровые, химические и другие методы обработки, исключающие дополнительную отделку вручную.
Однако при выполнении слесарно-сборочных, ремонтных работ, а также при окончательной обработке деталей, полученных штамповкой, выполнять эти работы приходится вручную.
|
Применением специальных инструментов и приспособлений добиваются повышения производительности распиливания и припасовки. К числу таких инструментов и приспособлений относятся ручные напильники со сменными пластинками и напильники из проволоки, покрытые алмазной крошкой, опиловочные призмы, опиловочные наметки и т. д.
Шабрение
Основные приемы шабрения
Перед шабрением поверхности очищают, промывают, протирают, затем наносят на них краску.
Краски для шабрения. После очистки заготовки перед шабрением выявляют неровности путем окрашивания поверхностей краской. Шабровочная краска представляет собой смесь машинного масла с лазурью и (:еже с суриком и ультрамарином (синька), которые в отличие от лазури плохо смешиваются с маслом и нечетко видны на детали. Лазурь можно заменить сажей, замешанной на смеси автола с керосином.
Рис. 321. Окрашивание плоских поверхностей при шабрении: а - окрашивание плиты, б - перемещение детали по плите (окрашивание), в - окрашенная деталь, тампоном, г - перемещение плиты по детали
Краску измельчают так, чтобы между пальцами не ощущалось зерен. Затем краску насыпают в баночку (металлическую или стеклянную) и вливают туда масло. Количество машинного масла в смеси должно быть таким, чтобы краска имела консистенцию пасты, но не жидкой, так как излишек масла будет расплываться по контрольной плите и проверяемая поверхность при наложении ее на плиту вся покроется краской.
Окрашивание поверхности. Краску наносят на поверхность плиты тампоном (рис. 321, а) из чистых льняных тряпок, сложенных в несколько слоев. Удобно наносить краску также мешочком, изготовленным из чистого полотна (холста), в который накладывают краску.
Мешочек и тампоны в паузах между окрашиваниями кладут в чистую стеклянную посуду или жестяную баночку. Ни в коем случае не следует класть в мешочек сухую краску и обмакивать его в масло.
Перед окрашиванием с поверхности детали удаляют стружку и грязь волосяной щеткой или чистой тряпкой, деталь осторожно накладывают обрабатываемой поверхностью на поверхность плиты и медленно передвигают. Для достижения равномерного износа плиты необходимо использовать всю ее поверхность.
После двух-трех круговых движений по плите (рис. 321, б) деталь осторожно снимают. На хорошо обработанных поверхностях краска ложится равномерно по всей поверхности (рис. 321, в), на плохо подготовленных - неравномерно. В небольших углублениях краска будет скапливаться, а в местах более углубленных ее вообще не будет. Так возникают белые пятна - наиболее углубленные места, не покрытые краской; темные пятна - менее углубленные, в них скопилась краска; серые пятна - наиболее выступающие, на них краска ложится тонким слоем.
|
Рис. 322. Приемы шабрения плоских деталей: а - 'от себя', б - 'но себя'
При определении неровностей на поверхностях тяжелых деталей, не снимаемых с места, закрашенный поверочный инструмент - плиту (рис. 321, г) или линейку - перемещают по контролируемым поверхностям.
Легкие детали (изделия) при шабрении устанавливают на слесарном верстаке, а крупные и тяжелые - на козлах.
Процесс шабрения заключается в постепенном снятии металла с окрашенных участков (серые пятна). Шабер держат правой рукой за ручку, а левой нажимают на конец шабера (рис. 322, а). По отношению к обрабатываемой поверхности шабер устанавливают под углом 25 - 30°, а режущая кромка должна находиться на окрашенной поверхности. Металл снимают скоблением. Рабочим ходом при шабрении является движение вперед, т. е. "от себя", а при работе плоским шабером с отогнутым вниз концом -движение назад, т. е. "на себя". При движении назад (холостой ход) шабер приподнимают.
Распиливание и припасовка
Распиливание
Распиливанием называется обработка отверстий с целью придания им нужной формы. Обработка круглых отверстий производится круглыми и полукруглыми напильниками; трехгранных отверстий - трехгранными, ножовочными и ромбическими напильниками; квадратных - квадратными напильниками.
Подготовка к распиливанию начинается с разметки и накернивания разметочных рисок, затем сверлят отверстия по разметочным рискам и вырубают проймы, образованные высверливанием. Наилучшей получается разметка на металлической поверхности, отшлифованной наждачной бумагой.
Под распиливание сверлят одно отверстие, когда пройма небольшая; в больших проймах сверлят два или несколько отверстий в целях оставления наименьшего припуска на распиливание. Большие перемычки трудно удалить из просверленной проймы, однако нельзя располагать отверстия и слишком близко во избежание сдваивания, что может привести к поломке сверла.
Распиливание в заготовке воротка квадратного отверстия. Вначале размечают квадрат, а в нем - отверстие (рис. 334, а), затем
просверливают отверстие сверлом, диаметр которого на 0,5 мм меньше стороны квадрата. В просверленном отверстии пропиливают четыре угла квадратным напильником, не доходя 0,5 -0,7 мм до разметочных рисок, после чего распиливают отверстие до разметочных рисок в такой последовательности: вначале пропиливают стороны 7 и 3, затем 2 и 4 и производят подгонку отверстия по метчику так, чтобы он входил в отверстие только на глубину 2 - 3 мм.
Дальнейшую обработку сторон (рис. 334,6) производят до тех пор, пока квадратная головка легко, но плотно не войдет в отверстие.
Распиливание в заготовке трехгранного отверстия. Размечают контур треугольника, а в нем - отверстие и сверлят его сверлом, не касаясь разметочных рисок треугольника (рис. 335,а,б). Затем в круглом отверстии пропиливают три угла и последовательно распиливают стороны 7,2 и 3, не доходя 0,5 мм до разметочной риски, после чего подгоняют стороны треугольника (рис. 335,в).
Рис. 334. Распиливание квадратного отверстия: а - разметка, б - прием распиливания
Рис. 335. Распиливание трехгранного отверстия: а - разметка, б - высверленное отверстие, в - порядок распиливания, г - проверка вкладышем
При работе трехгранным напильником стремятся избежать поднутрения сторон, опиливают строго прямолинейно. Точность обработки проверяют вкладышем (рис. 335,г).
При подгонке следует следить за тем, чтобы вкладыш входил в распиливаемое отверстие свободно, без перекоса и плотно. Зазор между сторонами треугольника и вкладышем при проверке щупом должен быть не более 0,05 мм.
Пригонка и припасовка
Пригонкой называется обработка одной детали по другой с тем, чтобы выполнить соединение. Для пригонки необходимо, чтобы одна из деталей была совершенно готовой, по ней ведут пригонку. Пригонка широко применяется при ремонтных работах, а также при сборке единичных изделий.
Пригонка напильником является одной из труднейших в работе слесаря, так как обрабатывать приходится в труднодоступных местах. Целесообразно эту операцию выполнять борнапильниками, шлифовальными борголовками, применяя опиловочно-зачистные станки.
При подгонке вкладыша по готовому отверстию работа сводится к обычному опиливанию. При пригонке по большому числу поверхностей сначала обрабатывают две сопряженные базовые стороны, затем подгоняют две остальные до получения нужного сопряжения. Детали должны входить одна в другую без качки, свободно. Если изделие на просвет не проглядывается, ведут припиливание по краске.
Иногда на подгоняемых поверхностях и без краски можно различить следы от трения одной поверхности по другой. Следы, имеющие вид блестящих пятен ("светлячки"), показывают, что данное место мешает движению одной детали по другой. Эти места (выступы) удаляют, добиваясь или отсутствия блеска, или равномерного блеска по всей поверхности.
При любых пригоночных работах нельзя оставлять острых ребер и заусенцев на деталях, их нужно сглаживать личным напильником. Насколько хорошо сглажено ребро, можно определить, проведя по нему пальцем.
Припасовкой называется точная взаимная пригонка деталей, соединяющихся без зазоров при любых перекантовках. Припасовка отличается высокой точностью обработки, что необходимо для беззазорного сопряжения деталей (световая щель более 0,002 мм просматривается).
Припасовывают как замкнутые, так и полузамкнутые контуры. Из двух припасовываемых деталей отверстие принято называть проймой, а деталь, входящую в пройму, - вкладышем.
Проймы бывают открытыми (рис. 336) и замкнутыми (см. рис. 335). Выполняется припасовка напильниками с мелкой и очень мелкой насечкой - № 2, 3, 4 и 5, а также абразивными порошками и пастами.
При изготовлении и припасовке шаблонов с полукруглыми наружным и внутренним контурами вначале изготовляют деталь с внутренним контуром - пройму (1-я операция) (рис. 336,а). К обработанной пройме подгоняют (припасовывают) вкладыш (рис. 336,6) (2-я операция).
При обработке проймы сначала точно опиливают широкие плоскости как базовые поверхности, затем начерно ребра (узкие грани) 1,2,3 и 4, после чего размечают циркулем полуокружность, вырезают ее ножовкой (как показано штрихом на рисунке); производят точное опиливание полукруглой выемки (рис. 336,в) и проверяют точность обработки вкладышем, а также на симметричность по отношению к оси при помощи штангенциркуля.
При обработке вкладыша сначала опиливают широкие поверхности, а потом ребра 1, 2 и 3. Далее размечают и вырезают ножовкой углы. После этого производят точное опиливание и припасовку ребер 5 и 6. Затем выполняется точное опиливание и припасовка вкладыша к пройме. Точность припасовки считается достаточной, если вкладыш входит в пройму без перекоса, качки и просветов (рис. 336,г).
Рис. 336. Припасовка: а - разметка, б - подгонка, в - подпиливание, г - проверка вкладышем
Рис. 337. Припасовка косоугольных вкладышей: а - схема разметки наружных углов, б - опиливание наружной поверхности, в - схема разметки внутренних углов, г - опиливание внутренних углов, д - проверка вкладышем
При изготовлении и припасовке косоугольных вкладышей и пройм типа "ласточкин хвост" (рис. 337,з, 6) сначала обрабатываю-*- вкладыш (обработка и проверка его проще). Обработку ведут в следующем порядке (рис. 337,6). Вначале точно опиливают широкие плоскости как базовые поверхности, затем все четыре узких грани (ребра) 1, 2, 3 и 4. Далее размечают острые углы (рис. 337,в), вырезают их ножовкой и точно опиливают. Сначала опиливают ребра 5 и 6 (рис. 337,в,г) в плоскости, параллельной ребру 7, затем ребрам 7 и 8 (рис. 337,а) по линейке и под углом 60° к ребру 4. Острый угол (60°) измеряют угловым шаблоном.
Пройма обрабатывается в следующем порядке. Вначале точно опиливают широкие плоскости, после чего опиливают все четыре ребра.
Далее производится разметка, вырезка ножовкой паза (на рис. 337,в показано штрихом) и опиливание ребер 5, 6 и 7. Сначала ширина паза делается меньше требуемой на 0,05 - 0,1 мм при сохранении строгой симметричности боковых ребер паза по отношению к оси проймы, глубина паза выполняется сразу точной по размеру. Затем при припасовке вкладыша и проймы ширина паза получает точный размер по форме выступа вкладыша. Точность припасовки считается достаточной, если вкладыш входит в пройму туго от руки, без просветов, качки и перекосов (рис. 337, д).
Ручное распиливание, пригонка и припасовка - очень трудоемкие операции. В современных условиях эти операции выполняют с использованием металлорежущего оборудования общего и специального назначения, при котором роль слесаря сводится к управлению машинами и контролю размеров.
Криволинейные и фасонные детали обрабатывают на шлифовальных станках специальными профилированными абразивными кругами. Широкое применение также находят электроискровые, химические и другие методы обработки, исключающие дополнительную отделку вручную.
Однако при выполнении слесарно-сборочных, ремонтных работ, а также при окончательной обработке деталей, полученных штамповкой, выполнять эти работы приходится вручную.
Применением специальных инструментов и приспособлений добиваются повышения производительности распиливания и припасовки. К числу таких инструментов и приспособлений относятся ручные напильники со сменными пластинками и напильники из проволоки, покрытые алмазной крошкой, опиловочные призмы, опиловочные наметки и т. д.
Шабрение
Сущность и назначение шабрения. Шаберы
Шабрением называется операция по снятию (соскабливанию) с поверхностей деталей очень тонких частиц металла специальным режущим инструментом - шабером. Цель шабрения - обеспечение плотного прилегания сопрягаемых поверхностей и герметичности (непроницаемости) соединения. Шабрением обрабатывают прямолинейные и криволинейные поверхности, вручную или на станках.
За один проход шабером снимается слой металла толщиной 0,005 - 0,07 мм, шабрением достигается высокая точность - до 30 несущих пятен в квадрате 25 × 25 мм, шероховатость поверхности не более Ra 0,32.
Шабрение широко применяют в инструментальном производстве как окончательный процесс обработки незакаленных поверхностей.
Широкое применение шабрения объясняется особыми качествами полученной поверхности, которые состоят в следующем:
в отличие от шлифованной или полученной притиркой абразивами шабренная более износостойка, потому что не имеет шаржированных в ее поры остатков абразивных зерен, ускоряющих процесс износа;
шабренная поверхность лучше смачивается и дольше сохраняет смазывающие вещества благодаря наличию так называемой разбивки (соскабливанию) этой поверхности, что также повышает ее износостойкость и снижает величину коэффициента трения;
шабренная поверхность позволяет использовать самый простой и наиболее доступный метод оценки ее качества по числу пятен на единицу площади.
Ручное шабрение - трудоемкий процесс, поэтому его заменяют более производительными методами обработки на станках.
Шабрению предшествует чистовая обработка резанием.
Поверхность, подлежащую шабрению, чисто и точно обрабатывают, опиливают личным напильником, строгают или фрезеруют. На шабрение оставляют припуск 0,1 -0,4 мм в зависимости от ширины и длины поверхности. При больших припусках и значительных неровностях сначала припиливают личным напильником с проверкой "на краску" (рис. 306). При этом напильник предварительно натирают мелом для устранения скольжения по краске и засаливания насечки.
Напильник двигают вкруговую, снимая металл с окрашенных мест. В целях предотвращения образования глубоких рисок напильник очищают стальной щеткой.
Опиливание ведут осторожно, так как при излишних проходах напильник может оставить глубокие впадины.
После опиливания окрашенных пятен заготовку (деталь) освобождают из тисков и вторично проверяют плоскости на окрашенной поверочной плите, затем продолжают опиливать слой металла по новым пятнам краски. Чередование опиливания и проверки повторяют до тех пор, пока не будет получена ровная поверхность с большим количеством равномерно расположенных пятен на всей плоскости детали (особенно по краям).
Шаберы - металлические стержни различной формы с режущими кромками. Изготовляют шаберы из инструментальной углеродистой стали У10 и У12А. Режущий конец шабера закаливают без отпуска до твердости HRC 56 - 64.
По форме режущей части шаберы подразделяют на плоские,трехгранные, фасонные; по числу режущих концов (граней) на односторонние и двусторонние; по конструкции - на цельные и со вставными пластинками.
Рис. 306. Припиливание поверхности с проверкой 'на краску'
Плоские шаберы применяют для шабрения плоских поверхностей - открытых, пазов, канавок и т. д.
По числу режущих концов плоские шаберы могут быть односторонними (рис. 307, а) и двусторонними (рис. 307, 6). Рациональной является выпуклая форма лезвия, очерченная дугой радиусом 30 - 40 мм для получ истового шабрения и 40 - 55 мм для чистового.
Плоские шаберы изготовляют с прямыми (рис. 307) и изогнутыми (рис. 308) концами. Открытые плоскости шабрят шаберами с прямым концом; стенки пазов, канавок и смежных плоскостей, а также мягкие металлы (алюминий, цинк, баббит и др.) - шаберами с отогнутым концом.
Длина плоских двусторонних шаберов составляет 350 - 400 мм. Ширина шабера для грубого шабрения принимается от 20 до 25 мм, для точного - 5 - 10 мм. Толщина конца режущей части колеблется от 2 до 4 мм. Угол заострения у шаберов (рис. 307, 308, 309) принимают для чернового шабрения 70 - 75°, для чистового - 90°.
Двусторонний плоский шабер (рис. 307, б) благодаря наличию двух режущих концов имеет большой срок службы.
Рис. 307. Плоские односторонний (а) и двусторонний (б) шаберы и углы заточки их
Рис. 308. Шаберы с изогнутым концом и углы заточки их
Трехгранные шаберы (рис. 309) применяют для шабрения вогнутых и цилиндрических поверхностей. Трехгранные шаберы иногда изготовляют из старых трехгранных напильников.
Как правило, их изготовляют только односторонними. Трехгранные шаберы имеют длину 190, 280, 380 и 510 мм.
Рис. 309. Трех- четырехгранные шаберы и углы заточки их
Для облегчения заточки плоскостей шабер имеет желобки, образующие режущие кромки с углом заострения 60 - 75° для стали.
Составные шаберы значительно легче целых шаберов тех же размеров. По форме режущей части они делятся на плоские, трехгранные прямые и трехгранные изогнутые (рис. 310, а, б, в). Такие шаберы при работе пружинят, а это повышает чувствительность рук шабровщика и способствует повышению точности шабрения.
Шабер с радиусной заточкой (рис. 311) благодаря плавности и легкости проникновения в металл значительно облегчает шабрение, так как требует приложения меньших усилий, чем при шабрении плоским шабером. Для предварительного шабрения радиус заточки составляет 30 - 40 мм, а для окончательного 40 - 55 мм.
Рис. 310. Составные шаберы: а - плоский, б - трехгранный, прямой, в - трехгранный изогнутый
Рис. 311. Составной шабер с радиусной заточкой В. А. Алексеева
Рис. 312. Шабер со сменными режущими пластинками
Рис. 313. Шабер усовершенствованный
Рис. 314. Шабер с зажимным патроном: а - шабер, б - набор пластин
Рис. 315. Дисковый шабер: 1 - режущий диск, 2 - гайка, 3 - державка
На рис. 312 показан универсальный шабер со сменными режущими пластинками. Он состоит из корпуса 3, держателя 2, рукоятки 5, зажимного винта 4, сменной режущей пластинки 7 из быстрорежущей стали или твердого сплава. Пластинка, вставленная в держатель, зажимается винтом при вращении ручки (рукоятки) шабера по часовой стрелке (для снятия пластинки ручку вращают против часовой стрелки).
Усовершенствованный шабер состоит из трех частей: державки, деревянной рукоятки и сменной пластинки (рис. 313). Сменная пластинка с хвостовиком типа "ласточкин хвост" вставлена в паз державки, это обеспечивает надежное ее крепление.
На рис. 314 показан наиболее совершенный шабер, состоящий из сменной пластинки 7, зажимного патрона 2 и стержня 3. Пластинки 4 таких шаберов изготовляют размером 3 × 16 × 50 мм из стали У12А, а стержень - из стали 45.
Если шабер предназначен для работы по белому чугуну или другому твердому металлу, то применяют пластинки из твердого сплава, например ВК6 или Т15К6. Замену затупленной пластинки производят путем по ворота рукоятки (стержня), так как губка зажимной части патрона соединена с корпусом шарнирно. Такая конструкция шабера допускает применение комплекта пластинок, заточенных под разными углами.
Дисковый шабер (рис. 315) применяется для шабрения широких плоскостей. Режущая часть 7 представляет собой стальной закаленный диск, закрепленный на державке 3 гайкой 2. Диск диаметром 50 - 60 мм, толщиной 3 - 4 мм затачивают на круглошлифовальном станке. По мере затупления его поворачивают на некоторый угол и работают не затупившимся участком. Таким образом используется весь диск шабера, что значительно экономит время на заточку, повышает производительность труда.
Рис. 316. Фасонный шабер: 1 - набор пластин, 2 - стержень, 3 - рукоятка
Рис. 317. Шаберы-кольца и их заточка: 1 - шлифовальный круг, 2 - доводочный (мелкозернистый) круг
фасонный шабер (рис. 316) представляет собой набор сменных стальных закаленных пластин 7, закрепленных на стержне 2 с рукояткой 3. Эти шаберы предназначены для шабрения в труднодоступных местах - впадин, замкнутых контуров, желобков, канавок и других фасонных поверхностей. Торцовые грани пластинок затачивают в соответствии с формой обрабатываемых поверхностей.
Шаберы-кольца изготовляют из изношенных конических роликовых подшипников или больших поршневых колец, эти шаберы заменяют трехгранный и изогнутый шабер и уменьшают количество переточек. Их затачивают на шлифовальном круге 7 (рис. 317) и доводят торец на мелкозернистом круге 2. Эти шаберы обеспечивают значительно большую производительность, чем трехгранные.
|
|
Состав сооружений: решетки и песколовки: Решетки – это первое устройство в схеме очистных сооружений. Они представляют...
Автоматическое растормаживание колес: Тормозные устройства колес предназначены для уменьшения длины пробега и улучшения маневрирования ВС при...
Архитектура электронного правительства: Единая архитектура – это методологический подход при создании системы управления государства, который строится...
Таксономические единицы (категории) растений: Каждая система классификации состоит из определённых соподчиненных друг другу...
© cyberpedia.su 2017-2024 - Не является автором материалов. Исключительное право сохранено за автором текста.
Если вы не хотите, чтобы данный материал был у нас на сайте, перейдите по ссылке: Нарушение авторских прав. Мы поможем в написании вашей работы!