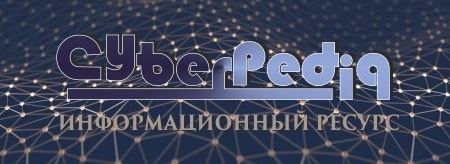
Опора деревянной одностоечной и способы укрепление угловых опор: Опоры ВЛ - конструкции, предназначенные для поддерживания проводов на необходимой высоте над землей, водой...
Состав сооружений: решетки и песколовки: Решетки – это первое устройство в схеме очистных сооружений. Они представляют...
Топ:
История развития методов оптимизации: теорема Куна-Таккера, метод Лагранжа, роль выпуклости в оптимизации...
Установка замедленного коксования: Чем выше температура и ниже давление, тем место разрыва углеродной цепи всё больше смещается к её концу и значительно возрастает...
Интересное:
Инженерная защита территорий, зданий и сооружений от опасных геологических процессов: Изучение оползневых явлений, оценка устойчивости склонов и проектирование противооползневых сооружений — актуальнейшие задачи, стоящие перед отечественными...
Наиболее распространенные виды рака: Раковая опухоль — это самостоятельное новообразование, которое может возникнуть и от повышенного давления...
Что нужно делать при лейкемии: Прежде всего, необходимо выяснить, не страдаете ли вы каким-либо душевным недугом...
Дисциплины:
![]() |
![]() |
5.00
из
|
Заказать работу |
|
|
Нормирование расхода сварочных материалов представляет собой установление плановой меры их производственного потребления. Основной задачей нормирования является обеспечение расчета технически и экономически обоснованных прогрессивных норм расхода сварочных материалов в целях рационального использования их в производстве.
Норма расхода - это максимально допустимое плановое количество материалов на производство единицы продукции установленного качества в планируемых условиях производства.
При сварке под флюсом нормируется проволока и флюс, при сварке в СО2 нормируется проволока и углекислый газ.
Норматив расхода электродной проволоки рассчитывается по формуле: Hпр = M ×kр, г;
где: М - масса наплавленного металла на суммарную длину сварного шва, г;
kр - коэффициент расхода, учитывающий технологические потери и отходы сварочных материалов;
M = M0 × L × 1000, г;
где: М0 - масса 1м шва, г;
L - суммарная длина шва, м.
MQ = F ×ρ × 103, г/мм;
где: F - площадь поперечного сечения наплавленного металла шва данного сварного соединения, мм2;
ρ- плотность металла, г/см3;
Коэффициент расхода электродной проволоки при автоматической сварке: kр=1,03, при полуавтоматической сварке kр= 1,05-1,06.
Произведём расчёт нормативов расхода сварочных материалов для шва №2:
М0 =80 · 7,85 · 10-3 = 0,628 кг
Нпр = 0,628 · 1,03 · 15 =9,9 кг
Нф = 0,950 · 1,1 · 14,4 =15 кг
M=0,63*15*1000=9461г
Норма расхода углекислого газа взята по справочным данным. Исходные данные и результаты расчета приведены в таблице 2.7.
Таблица. 2.7 - Исходные данные и результаты расчетов расхода сварочных материалов.
|
№ шва | F, мм2 | L, м | М0, г/мм | М, г | Нпр, г | Нф, г | Нг, л/мин | |
1 | 48,6 | 126 | 0,38 | 13187 | 13846 | 20769 | - | |
2 | 80 | 15 | 0,63 | 9461 | 9934 | 14901 | - | |
3 | 48,6 | 7,2 | 0,38 | 2447 | 2569 | 3853 | - | |
4 | 48,6 | 4,6 | 0,38 | 1755 | 1842 | 16-18 | ||
5 | 24,4 | 1,5 | 0,38 | 286,5 | 301 | 451 | - | |
6 | 56 | 63,15 | 0,38 | 13054 | 11600 | 18709 | - | |
7 | 78 | 21,05 | 0,36 | 8258 | 9100 | 12587 | - |
Норма расхода флюса рассчитывается по следующей эмпирической формуле: Hф = Hпр × kр, г;
Коэффициент расхода флюса для полуавтоматической сварки: kр=1,5, для автоматической сварки: kр=1,1 - на весу, kр= 1,18 - на флюсо-медной подушке, kр=1,23 - на флюсовой подушке.
Вывод: Для сварки конструкции требуется 47,35 кг проволоки Св-08-АА; 1,8 кг проволоки Св-08Г2С; 71,27 кг флюса АН-348-АМ; 16-18 л/мин углекислого газа. Это минимальное количество сварочных материалов для сварки данного изделия.
1.8 Расчет технической нормы времени
Задачей нормирования является установление необходимых затрат времени на выполнение заданной работы в определенных организационно-технических условиях.
Норма штучного времени для всех видов дуговой сварки рассчитывается по формуле:
Тшт = Тнш-к × L + tвн
где: Тнш.к - неполное штучно-калькуляционное время сварки 1м шва;
L - длина свариваемого шва, м;
tвн - вспомогательное время, зависящее от изделия и типа оборудования, включает в себя время на установку, поворот, снятие изделия, закрепление и открепление деталей, перемещение сварщика.
Тнш-к = (Т0 + tвш) × (1 + (аабс + аот + ап з ) / 100),
где: Т0 - основное время сварки 1 м шва,
tвш- вспомогательное время, зависящее от длины свариваемого шва.
Основное время электросварочных работ - это время, затрачиваемое непосредственно на образование сварного шва путем расплавления металла электрода. Его определяют в зависимости от вида и способа сварки.
Основное время для автоматической и полуавтоматической сварки под флюсом и в среде защитных газов:
|
To = 60 / Vce 1 + 60 × n / Vcв п;
где: Vсв 1, Vсв n - скорость сварки для первого и последующих проходов, м/ч;
n - количество проходов.
Время на обслуживание рабочего места - аабс, на отдых и личные надобности - аот, на подготовительно-заключительные работы - апз, задаются в процентах от оперативного времени - ton.
ton = To + tвш
tвш = 0,35×L
С учетом этого можно записать:
Тнш-к = ton × k + tnз / n
k = 1,13 - при сварке в удобном положении;
k = 1,19 - при сварке в неудобном положении.
Подготовительно-заключительное время зависит от сложности сварки и сборки:
простое tnз = 11-12 мин;
среднее tп з= 17 мин;
сложное tпз = 27 мин.
Исходные данные и результаты расчета приведены в таблице 2.8.
Таблица 2.8 - Результаты расчетов нормы времени
№ шва | L, м | Vсв, м/ч | To, мин | tвш, мин | ton, мин | tвн, мин | Тнш-к, мин | Тшт, мин |
1 | 20,8 | 30 | 2 | 7,28 | 9,28 | 11,5 | 28 | 594 |
2 | 24,8 | 30 | 2 | 8,68 | 10,68 | 1,6 | 29,3 | 728 |
3 | 7,2 | 28 | 2,14 | 2,52 | 4,66 | ид | 24,6 | 188 |
4 | 4,6 | 28 | 2,14 | 1,61 | 3,75 | пд | 24,6 | 124 |
5 | 1,5 | 28 | 2,14 | 0,525 | 2,665 | 9,2 | 19 | 37,7 |
6* | 63,15 | 30 | 2 | 22,1 | 24,1 | 10 | 42,23 | 838 |
7 | 21,05 | 30 | 2 | 7,36 | 9,36 | 12 | 27,5 | 590 |
Примечание: 1.Расчеты выполнены при t пз = 17 мин, k = 1,13.
2. 6* - шов варится двухдуговым автоматом, следовательно, время на сварку снижается вдвое.
Для того чтобы назначить число рабочих, требуемых для изготовления данной конструкции, нужно определить общее время, требуемое для изготовления конструкции.
Тобщ = Σ Тшт-к = 594 + 728 + 188 + 124 + 37,7 + 838 + 590 = 3100,7 мин.
Общее время, требующееся на сварку данной конструкции 51,6 ч.
2 Разработка технологического плана участка
Разработка технологической планировки (плана расположения оборудования и рабочих мест в цехе) является одной из наиболее ответственных работ при проектировании. От того, насколько удачно выполнена планировка, во многом зависит нормальная работа цеха и его участков.
Исходными данными для разработки планировки служат; карты технологического процесса, расчет потребного количества оборудования и рабочих мест, В зависимости от количества потоков выбирают ширину здания, она может быть 12, 18, 24, 30, 36 м или кратной этим значениям. Длину здания получают делением значения его производственной площади на ширину. Размеры здания по длине должны быть кратными 6 м. План здания вычерчивается с изображением основных строительных элементов в масштабе 1:100. Отдельно в принятом масштабе вычерчиваются также условные изображения принятого оборудования и рабочих мест (темплеты), которые располагаются на плане цеха в соответствии со схемой (картой) технологического процесса и действующими нормами проектирования.
|
При разработке планировки необходимо соблюдать следующие основные требования и правила: размещать оборудование и рабочие места в порядке последовательности выполнения технологических операций, не допуская возвратных и петлеобразных движений обрабатываемого материала, создающих встречные потоки; оборудование и рабочие места располагать по возможности так, чтобы материал для обработки поступал справа налево по отношению к работающему; предусмотрены удобства наладки оборудования, смены инструмента, обеспечена хоровая освещённость рабочего места; после участков с высокопроизводительным оборудованием необходимо предусматривать межоперационные запасы заготовок, а также места технологических выдержек; все основные внутрицеховые транспортные операции целесообразно производить с помощью приводных и неприводных конвейеров и траверсных тележек; расстояния между оборудованием, складочными местами и элементами здания должны быть не менее следующих значений: от стены до тыльной или боковой стороны станка - 600 мм; до продольной стороны складочного места - 1000 мм; между тыльными сторонами станков - 700 мм; ширина постоянных проходов, свободных от оборудования и коммуникаций, должна быть не менее 1000 мм, их количество определяется расположением технологического оборудования; ширина проездов при одностороннем движении транспорта - 2-3 м и двухстороннем - не менее 4 м; через каждые 50 м длины цеха должны быть предусмотрены поперечные проезды шириной 3-4 м и т.д.
|
Вспомогательные помещения размещают сообразуясь с производственным процессом. Например, лакоприготовительное отделение вблизи потребителей лакокрасочных материалов и т.п.
На планировке должны быть проставлены основные размеры плана здания, осуществлена привязка осей основного оборудования к колоннам или стенам здания и составлена спецификация технологического и транспортного оборудования.
В цех отделки с помощью электропогрузчика привозят стулья. Рабочиий вручную навешивает эти стулья на цепной конвейер линии крашения и грунтования 948-00-00
ВПКТИМ. Изделия подвешивают на высоте 400 мм от уровня пола под углом 20°.На конвейере, движущимся со скоростью 0,7 м/мин, изделия поступают в камеру 1, где стуйным обливом наносится краситель ХМ 8000. Краситель имеет вязкость по вискозиметру ВЗ-4 30 с, расход составляет 155 г/м2. После нанесения красителя, изделия в течение 1 минуты выдерживают в парах растворителя.
Далее изделия поступают в конвекционную сушильную камеру 2, где сушат 2 минуты при температуре 20 °С.
После этого изделия переносятся в камеру 1, где обливом наносят грунтовку Целлонит Г 1010 вязкостью по ВЗ-4 60 с, расход составляет 200 г/м3. Далее выдержка в парах растворителя. Данный слой грунтовки сушат в трёхходовой конвекционной камере 4 при температуре 45 °С в течение 20 мину. Охлаждаются изделия при перемещении на следующую позицию, всё так же двигаясь на подвесном конвейере, над которым установлен вытяжной зонт 5. Уже охлаждённые изделия рабочий вручную снимает с конвейера.
Далее стулья поступают на рабочее место, где их шлифуют вручную шлифовальной шкуркой №5.
Затем изделия поступают к линии лакирования А-242. Рабочиий вручную навешивает эти стулья на цепной конвейер линии. Изделия подвешивают на высоте 400 мм от уровня пола под углом 20°. На конвейере, движущимся со скоростью 1 м/мин, изделия поступают в камеру 7, где наносится токопроводящий состав (раствор алкомона в уайт-спирте). Данный состав имеет вязкость по вискозиметру ВЗ-4 50 с, расход составляет 40 г/м2. После нанесения красителя, изделия поступают в трёхходовую конвекционную камеру 8, сушка длится 20 минут при температуре 50°С. Подсушенные изделия поступают в камеру 9, где методом электрораспыления наносится первый слой лака Мерит Электра 50 «Tikkurila». При этом вязкость лака составляет 30 с (по ВЗ-4), а расход - 150 г/м2. Далее для устранения дефектов (непрокрашенных мест) стулья поступают в ремонтную распылительную кабину 10. После этого изделия выдерживаются при перемещении на следующую позицию, затем сушатся в конвекционной камере 20 минут при температуре 20 °С. Охлаждаются изделия в процессе движения на следующую позицию.
|
Для нанесения второго слоя лака данный цикл повторяют, а после охлаждения рабочий вручную снимает стулья с конвейера.
Далее визуально проводят контроль качества образцов, сравнивая их с эталоном. Стулья хорошего качества электропогрузчиком вывозят из цеха. Стулья, имеющие дефекты, переносят к рабочему месту 11, где их устраняют. Затем их также вывозят из цеха.
|
|
Биохимия спиртового брожения: Основу технологии получения пива составляет спиртовое брожение, - при котором сахар превращается...
Поперечные профили набережных и береговой полосы: На городских территориях берегоукрепление проектируют с учетом технических и экономических требований, но особое значение придают эстетическим...
Типы оградительных сооружений в морском порту: По расположению оградительных сооружений в плане различают волноломы, обе оконечности...
История развития пистолетов-пулеметов: Предпосылкой для возникновения пистолетов-пулеметов послужила давняя тенденция тяготения винтовок...
© cyberpedia.su 2017-2024 - Не является автором материалов. Исключительное право сохранено за автором текста.
Если вы не хотите, чтобы данный материал был у нас на сайте, перейдите по ссылке: Нарушение авторских прав. Мы поможем в написании вашей работы!