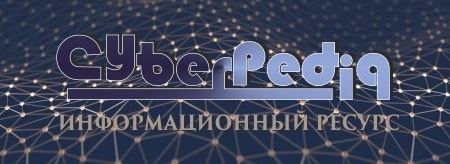
Своеобразие русской архитектуры: Основной материал – дерево – быстрота постройки, но недолговечность и необходимость деления...
История создания датчика движения: Первый прибор для обнаружения движения был изобретен немецким физиком Генрихом Герцем...
Топ:
Генеалогическое древо Султанов Османской империи: Османские правители, вначале, будучи еще бейлербеями Анатолии, женились на дочерях византийских императоров...
Организация стока поверхностных вод: Наибольшее количество влаги на земном шаре испаряется с поверхности морей и океанов...
Определение места расположения распределительного центра: Фирма реализует продукцию на рынках сбыта и имеет постоянных поставщиков в разных регионах. Увеличение объема продаж...
Интересное:
Искусственное повышение поверхности территории: Варианты искусственного повышения поверхности территории необходимо выбирать на основе анализа следующих характеристик защищаемой территории...
Берегоукрепление оползневых склонов: На прибрежных склонах основной причиной развития оползневых процессов является подмыв водами рек естественных склонов...
Инженерная защита территорий, зданий и сооружений от опасных геологических процессов: Изучение оползневых явлений, оценка устойчивости склонов и проектирование противооползневых сооружений — актуальнейшие задачи, стоящие перед отечественными...
Дисциплины:
![]() |
![]() |
5.00
из
|
Заказать работу |
|
|
Г л а в а 5
Машины и устройства непрерывного транспорта
Транспортируемый материал и его свойства
В качестве транспортирующих устройств непрерывного действия на строительстве применяются конвейеры различных типов (ленточные, скребковые, пластинчатые, винтовые, вибрационные), ковшовые элеваторы, установки пневматического транспорта. Эти устройства используются часто совместно с другими машинами, а иногда входят в состав более сложных машин, например экскаваторов непрерывного действия или самоходных погрузчиков. Средства непрерывного транспорта широко используются для перемещения штучных, мелкокусковых и сыпучих материалов (песка, щебня, гравия, цемента и др.) в карьерах, на дробильно-сортировочных и бетоносмесительных установках, на складах строительных материалов.
На процесс транспортирования и его производительность влияют физико- механические свойства транспортируемого материала. Для сыпучих материалов наиболее значимы следующие характеристики:
насыпной вес, т.е. вес 1 м3 материала в свободно насыпанном (без уплотнения) состоянии;
влажность – отношение (в процентах) веса содержащейся в материале
воды к весу сухого материала
g м – вес сухого материала;
ω = (g в
g м) ×100, где g в – вес воды в материале;
коэффициент трения материала по поверхности стенок бункеров и
лотков
f = tgρo, где ρº – угол трения;
|
|
конуса свободно насыпанного материала к неподвижной горизонтальной поверхности;
угол естественного откоса материала в движении на 20…30% меньше
|
|
|
|
коэффициента трения между частицами материала в процессе движения по сравнению с состоянием покоя.
Таблица 5.1
Характеристики транспортируемых материалов
Наименование материала | Насыпной вес в кг/м3 | Угол естественного откоса в град | Коэффициент трения материала о сталь | ||
в покое | в движении | в покое | в движении | ||
Гравий | 1700…1800 | 45 | 30 | 1 | 0,58 |
Щебень | 1800…2000 | 45 | 35 | 1 | 0,7 |
Песок | 1400…1700 | 45 | 30 | 1 | 0,58 |
Грунт сухой | 1200…1300 | 45 | 30 | 1 | 0,58 |
Глина сухая | 1100…1500 | 50 | 35 | 1,2 | 0,7 |
Цемент | 1100…1300 | 43 | 38 | 0,93 | 0,78 |
Рис. 5.3. Ленточный останов
Загрузка конвейеров происходит через подвижные или стационарные бункеры или воронки, а разгрузка производится через концевой барабан (рис.5.1) или с помощью плужковых сбрасывателей (5.4, а). При необходимости подачи материала в различные бункеры, он разгружается с помощью разгрузочных тележек (рис. 5.4, б), которые могут иметь перекидной затвор.
Рис. 5.4. Разгрузочные устройства ленточных конвейеров:
а – плужковый сбрасыватель; б – разгрузочная тележка
Вращение от двигателя к приводному барабану передается через редуктор, передаточное число которого определяется по формуле
n дв
i =
n б
n двπ D б
= ,
60 V л
где n дв – число оборотов вала двигателя в мин; n б – число оборотов приводного барабана; D б
– диаметр приводного барабана; V л – скорость движения ленты, м/с.
Скорость ленты принимается не более 2 м/с для отсутствия пыления некоторых сыпучих материалов и избежания проскальзывания материала при его разгоне (во время попадания на ленту). Высокоскоростные конвейеры, например, на роторных экскаваторах, а также конвейеры для вертикального подъема груза снабжаются прижимной лентой, опирающейся на гибкие ролики, выполненные в виде витых пружин (рис. 5.5). Угол наклона ленточного конвейера без прижимной ленты должен быть меньше угла трения (в движении) материала по ленте конвейера.
Рис. 5.5. Конвейер с прижимной лентой
|
Мощность, расходуемая на привод ленточного конвейера, определяется по формуле:
1 ⎛ QV 2 ⎞
N = ⎜ QH +
367 ⎝
fQL +
⎟ кВт,
2 g η ⎠
где Q – производительность конвейера в т/ч; Н – высота подъема материала в м (для наклонных конвейеров); L – длина конвейера в м; f – коэффициент сопротивления движения ленты с учетом трения в подшипниках (f = 0,05); V – скорость движения ленты в м/сек; η – к.п.д. конвейера η = 0,5…0,7.
Зная окружное усилие Р, можно при заданном угле (α) обхвата лентой приводного барабана определить натяжение концов ленты: сбегающего
t = P
(e μα -1)
и набегающего
T = Pe μα
(e μα - 1). Такой простой способ
определения мощности двигателя и натяжения ленты пригоден только для конвейеров прямолинейной формы и небольшой длины, в которых угол обхвата
α £ 250o заведомо обеспечивает передачу необходимого тягового усилия.
В конвейерах сложной формы и большой длины натяжение ленты следует определять на отдельных ее участках, обходя по контуру весь конвейер (рис. 5.6). Минимальное натяжение S 1 имеет место у холостой ветви, т.е. после схода ленты с приводного барабана. Минимальное натяжение рабочей ветви S4 определяют, исходя из нормального провеса ленты между роликовыми опорами. Усилие натяжения ленты должно обеспечить не только необходимую силу трения между лентой и приводным барабаном, но и определенную стрелку провеса груженой ленты между роликовыми опорами, не превышающую
значения
f = ξ × l р, где ξ – коэффициент провеса (0,03 для прорезиненных лент и 0,012 для
стальных лент); l р – расстояние между опорами.
Рис.5.6. Расчетная схема ленточного конвейера
Эпюра на роликах разгрузочного устройства не показана (кроме участка на верхнем ролике)
Для конвейера, показанного на рис. 5.5 натяжение в конце наклонного груженого участка составит
S 5 = S 4 + W 4 ,
где W 4
= W нг
= (q + q
) gL
(sin β + w cosβ)
– сопротивление перед входом на роликовую
|
|
Натяжение ленты после огибающего ролика
S 6 = S 5 + W ог,
|
где
W ог
= 2 S 5
(w sin γ
2 + ξ) – сопротивление на огибающем ролике (в данном случае
γ = β); w – коэффициент сопротивления огибающего ролика; ξ – коэффициент провеса.
Натяжение ленты перед разгрузочным устройством
|
где
W 6-7
= (q + q
6-7 w
– сопротивление на горизонтальном и наклонном участках до
|
Натяжение после разгрузочного устройства
S 8 = S 7 + W ру,
где W ру – сопротивление на разгрузочном устройстве, определяемое в зависимости от его типа.
Максимальное натяжение ленты перед приводным барабаном
S 9 = S 8 + W 8-9,
где
W 8-9 = q л gL 8-9 w
– сопротивление на горизонтальном порожнем участке перед
приводным барабаном.
Натяжение ленты перед натяжным барабаном
S 3 = S 4 - W нб ,
⎛ d α ⎞
|
W нб
= (S + S)× ⎜⎜ D
μ sin + ζ⎟
2
– сопротивление на натяжном барабане; μ –
|
|
|
– геометрическая сумма натяжений ветвей
ленты, огибающих барабан (без большой погрешности она равна 2 S 4).
Натяжение в точке перегиба нижней ветви ленты
S 2 = S 3 - W нп,
где W нп = q л gL нп (sin β + w cosβ) – сопротивление на наклонном порожнем участке.
Натяжение сбегающей ветви
S 1 = S 2 - W гп,
где W гп = q л gL гп w
– сопротивление на горизонтальном порожнем участке.
Зная S 9 и S 1, определяют необходимое окружное усилие на приводном барабане
P = S 9 - S 1 = T - t
Необходимый угол охвата α определится из соотношения
|
S 1 = T t.
Для обеспечения необходимого угла охвата α можно применить прижимные ролики, увеличивающие угол охвата.
Если из выражения
e μα = S
S 1 = S н
S сб
угол охвата получается настолько
|
S - S
e μα¢
|
0,5 e
-1),
н сб
¢
где α′ – фактически используемый угол охвата барабана лентой.
Аналогичным методом могут быть определены натяжения ленты на различных участках, необходимый угол обхвата, окружное усилие, мощность привода и при других конфигурациях конвейеров.
|
Работоспособность всех элементов мощных конвейеров должна быть проверена при пусковом режиме.
В некоторых конструкциях погрузочных машин применяются скребковые конвейеры, перемещающие груз скребками по неподвижной поверхности, а также внутри трубы или желоба.
В тех случаях, когда необходимо транспортировать горячие и острокромочные материалы, а также кусковые или штучные грузы большой массы, применяют цепные пластинчатые транспортеры.
Элеваторы служат для перемещения грузов и материалов в вертикальном или круто наклонном (α ≈ 60º) направлениях. Для транспортирования сыпучих (цемент, песок) и мелкокусковых (щебень, гравий, шлак) материалов используют ковшовые элеваторы, а для штучных – полочные и люлечные. Несущим органом в элеваторе являются ковши или полки, а тяговым – втулочно-роликовая цепь или прорезиненная лента, на которой они смонтированы. Ковшовые элеваторы используются в дробильно-
сортировочных установках, растворных узлах, установках по приготовлению бетонных и асфальтобетонных смесей.
Рис.5.7. Ковшовые конвейеры (элеваторы):
а – ленточный; б – двухцепной; в – одноцепной; г – наклонный закрытый; д – наклонный открытый; е –
люлечный; ж – полочный; з – пассажирский кабинный
Ковшовый элеватор имеет бесконечный замкнутый тяговый орган 1 (рис. 5.6), на котором с равными интервалами укреплены ковши 2. Тяговым органом являются ленты (рис. 5.7, а), две или одна цепь (рис. 5,7, б и в). Лента огибает приводной 3 и натяжной 4 барабаны, укрепленные в крайних точках элеватора. Цепь огибает укрепленные в этих же точках звездочки. В пролете между крайними точками тяговый орган в вертикальных элеваторах небольшой высоты опор не имеет. В наклонных и высоких вертикальных элеваторах лента опирается на направляющие ролики. Цепи катятся роликами по направляющим (рис. 5.7, г) или опираются, так же как и лента, на направляющие ролики.
Элеватор защищен металлическим кожухом с окнами для осмотра, состоящим из отдельных секций. Наклонные элеваторы иногда бывают открытыми, без кожуха (рис. 5.7, д). С кожухом соединяют загрузочный и разгрузочный башмаки в местах загрузки и разгрузки. Привод барабана или звездочек устанавливают в верхней части элеватора. Вал нижнего барабана или звездочки вращается в передвигающихся подшипниках, связанных с винтовым натяжным устройством.
Элеваторы применяют для транспортирования материала на высоту до 50 м при производительности до 500 м3/ч. Они особенно удобны для заполнения высоких хранилищ – силосов или бункеров.
Различают элеваторы быстроходные, со скоростью тягового органа
|
1,25…2,0 м/с, тихоходные, со скоростью 0,4…1,0 м/с.
Быстроходные элеваторы применяют для транспортирования порошкообразных, мелко- и среднекусковых материалов; тихоходные – для транспортирования среднекусковых абразивных, крупнокусковых и плохо подвижных материалов.
Ковши крепят к тяговому органу с зазорами (в элеваторах с расставленными ковшами) или вплотную один к другому (в элеваторах с сомкнутыми ковшами). Первые элеваторы быстроходные, вторые – тихоходные. Загрузка ковшей быстроходных элеваторов происходит при прохождении ими нижнего (загрузочного) башмака, путем зачерпывания рис. 5.7, а и б). В тихоходных элеваторах загрузка производится путем засыпания материала в ковш (рис. 5.7, в, г и д).
В тихоходных элеваторах разгрузка ковшей осуществляется гравитационным путем, т.е. естественным высыпанием транспортируемого материала в лоток, при повороте ковшей вокруг верхней звездочки. В быстроходных элеваторах разгрузка ковшей происходит путем выбрасывания материала из ковшей под действием возникающей при повороте ковша вокруг звездочки силы инерции. Промежуточным типом являются элеваторы с гравитационно-центробежной разгрузкой (рис. 5.6, б), в которых разгрузка происходит в основном путем высыпания, но некоторая часть материала, находящаяся на поверхности ковша, выбрасывается под действием силы инерции. В таких (преимущественно цепных) элеваторах целесообразно размещать ковши между цепями и отклонять их направляющими роликами (рис. 5.7, б).
Разновидностью ковшовых элеваторов являются подъемники непрерывного действия для штучных грузов. В этих устройствах к тяговым цепям крепят не ковши, а шарнирно подвешенные площадки – люльки (рис. 5.7, е), что дает возможность не только поднимать, но и опускать грузы. Такие элеваторы называют люлечными. При жестком креплении полок к тяговым цепям элеватор делают наклонным (рис. 5.7, ж), он используется преимущественно для подъема различных штучных грузов, подающихся самотеком на полки и самотеком скатывающихся с них. Такие элеваторы используются в основном как погрузочно-разгрузочные устройства.
Элеваторы применяют и как пассажирские подъемники непрерывного действия (рис. 5.7, з). Кабины для пассажиров подвешивают шарнирно к двум цепям, что обеспечивает свободное прохождение через верхние и нижние звездочки.
Производительность ковшовых элеваторов колеблется от 5…10 до
150…200 м3/ч, определяется по формуле:
П = 3600 v qk
t н
м3/ч;
П = 3600 v
t
qk н γ
т/ч,
где v – скорость движения ковшей (0,4…2 м/с); t – шаг ковшей в м; v / t – число ковшей, разгружаемых за 1 с; q – емкость одного ковша; (колеблется в пределах от 0,65 до 35 л); k н – коэффициент наполнения ковшей материалом, равный 0,75…0,8 (цемент, сухой песок);
0,6…0,9 (щебень, гравий) и 0,4…0,6 (влажный песок); γ – объемный (насыпной) вес транспортируемого материала в т/м3.
Рис. 5.8. Схема винтового конвейера
Производительность винтовых конвейеров обычно составляет от 15 до 60
м3/ч и определяется по формуле:
П = 60 × F × s × n,
м3⁄ч;
П = 60 × F × s × n × γ,
т⁄ч,
где F – площадь поперечного сечения слоя материала в желобе в м2;
F = π × D 2 k з k
4, D –
диаметр винта, обычно в пределах от 150 до 600 мм; k з – коэффициент заполнения поперечного сечения винта материалом, равный: 0,3…0,45 для хорошо сыпучих материалов (цемент, сухой песок); 0,25…0,4 для мелкокусковых материалов (гравий, шлак); 0,15…0,3 для тестообразных и мокрых материалов (раствор, мокрая глина); k – коэффициент снижения заполнения при наклонном расположении шнека (колеблется от 1 до 0,65 в зависимости от угла наклона); s – шаг винта, обычно (0,8…1) D в м; n – число оборотов винта (от 40 до 120 в мин).
Вибрационные конвейеры служат для горизонтального и наклонного (15…20°) транспортирования сыпучих материалов. Перемещение материала таким конвейером обеспечивается в результате направленных колебаний металлического желоба или трубы с частотой колебаний от 600 до 1500 в мин. и амплитудой от 2 до 7 мм. Плоскость колебаний вибратора расположена под углом 15…45° к плоскости транспортирующего органа.
Вибрационный конвейер (рис. 5.9) состоит из неподвижной рамы 1, желоба или трубы 2, упругих элементов 3, вибрационного устройства 4. Такие конвейеры могут иметь вибрационные приводы: электромагнитные,
пневматические и механические. Последние делятся на дебалансные вибраторы с круговой траекторией или с направленными колебаниями и кривошипно- шатунные.
Рис.5.9. Схема вибрационного конвейера
Упругие элементы выполняются в виде рессор, спиральных пружин, резиновых конструкций или рычагов-качалок. У вуибрационных конвейеров трущиеся детали их привода полностью изолированы от соприкосновения с транспортируемым материалом.
Производительность вибрационных конвейеров колеблется от 4 до 60 т/ч, а дальность транспортирования от 1 до 10 м; максимальный угол наклона 18°. Производительность вибрационного конвейера определяется по формуле:
П = 3,6 × F × v × γ, т/ч,
где F – площадь поперечного сечения материала в желобе в м2.
При прямоугольном желобе
F = B × h,
где В – ширина желоба; h – высота слоя материала – для порошкообразных материалов и h ≈
20…30 мм; для мелкокусковых материалов h≈ 40…60 мм.
При трубчатом желобе
|
где k 3 – коэффициент заполнения; k 3≈0,25; D – диаметр трубы желоба.
Для транспортеров с электромагнитными вибраторами
v = 0,5 g × ctg α ω в м/с,
где v – скорость перемещения материала вдоль желоба; g – ускорение земного тяготения в м/с2; ω – частота вынужденных колебаний в Гц; α – угол перемещения материала в град.
Для качающихся вибрационных конвейеров средняя скорость перемещения груза в горизонтальном желобе зависит от величины коэффициента трения между транспортирующим материалом и материалом желоба (см. табл. 5.2).
Таблица 5.2.
Коэффициент трения | 0,2 | 0,3 | 0,4 | 0,5 | 0,6 | 0,7 | 0,8 |
Скорость в м/с | 0,13… 0,14 | 0,2… 0,25 | 0,27… 0,32 | 0,33… 0,38 | 0,35… 0,4 | 0,38… 0,42 | 0,4… 0,45 |
Мощность привода вибрационного конвейера:
N = Gfv 102η кВт,
где G – вес груза в желобе в кг; f – коэффициент трения материала о желоб; v – средняя скорость перемещения груза в м/с; η – к.п.д, η ≈ 0,5…0,6.
Рис. 5.10. Схема двухканатной подвесной дороги
У подвесных дорог значительной протяженности (свыше 2,5…3 км) применяются промежуточные натяжные станции. Высота опор, в зависимости от рельефа местности, колеблется от 8 до 12 м. При грузоподъемности тележек 250…1800 кг и скорости их движения 2,5 м/сек производительность подвесных дорог находится в пределах 20…300 т/ч.
Производительность подвесной дороги определяется по формуле:
Q = nG 1000 т/ч,
где n – число тележек, подаваемых в час; G – вес груза в кг.
Мощность двигателя для привода подвесных двухканатных дорог определяется по формуле:
N = N 1 + N 2 + N 3 + N 4
кВт
где N 1 – мощность, затрачиваемая на передвижение вагонеток по горизонтальному пути; N 2 – мощность, затрачиваемая на преодоление сопротивлений на конечных станциях (N 2 = 3…5 кВт); N 3 – мощность, затрачиваемая на преодоление сопротивлений в каждой
промежуточной станции (N 3 = 3…4 кВт); N 4 – мощность, затрачиваемая на подъем вагонеток:
N 4 = QH η
367
кВт,
где Q – производительность дороги в т/ч; Н – разность высот конечных станций в м; η –
к.п.д. привода (η = 0,7…0,8).
Ориентировочно при производительности 10 т/ч можно принять N 1 = 3 кВт. При увеличении производительности на каждые 10 т/ч затрачиваемая мощность увеличивается на 1 кВт.
Канатно-ковшовые установки применяют для перемещения кусковых и сыпучих материалов внутри склада. Они могут быть передвижными и стационарными. Производительность передвижных установок до 100 т/ч, а стационарных до 500 т/ч. Канатно-ковшовая установка (рис. 5.11) состоит из головной башни 1, на которой укреплены блоки 2 для направления головного каната 3 и хвостового 4, идущих с двухбарабанной лебедки. К канатам прикреплен бездонный ковш 5. Хвостовой канат проходит через блок 6 передвижной хвостовой башни 7, блок 8 и возвращается на другой барабан лебедки. Емкость ковшей от 0,5 до 5,0 м3.
Рис. 5.11. Схема канатно-ковшевой установки
Перемещение материалов по складу осуществляется возвратно- поступательным движением ковша. При рабочем движении ковш врезается в материал, захватывает его и перемещает волоком до места разгрузки. При обратном движении ковш не захватывает материал. Скорость движения ковша 1,2…2,5 м/с.
Достоинством канатно-ковшовых установок является простота работы и обслуживания, относительно малые затраты на их устройство и содержание; недостатком – быстрый износ канатов.
Производительность канатно-ковшовой установки определяется по формуле:
Q = 3,6 V γ S t т/ч,
где V – емкость ковша. м; γ – объемный вес материала. кг/м3; ∑ t – продолжительность цикла, с:
S t = l
v гр + l
v пор + t,
где l – средняя длина перемещения ковша, м; v гр и v пор – скорости движения груженого и порожнего ковша, м/с; t – время, расходуемое на изменение направления движения (t =10 с).
Мощность двигателя привода лебедки определяют по формуле:
N = S Wv гр
102η
кВт,
где ∑ W – тяговое усилие в канате при рабочем ходе ковша; η – к.п.д. канатно-ковшовой установки (η = 0,7…0,75). Тяговое усилие в канате ориентировочно можно определить по эмпирической формуле:
å W = 1,5 V ψγ
кг,
где Ψ – коэффициент заполнения ковша (Ψ = 0,9…1,2).
Рис. 5.13. Пневматический транспортный желоб
Конструктивная схема аэрожелоба приведена на рис. 5.13. Он состоит из двух частей 1 и 3, изготовленных из листовой стали и соединенных болтами. Между частями желоба помещают пористую перегородку 2, которая может быть керамической или матерчатой – тканой, цельной или составной. Материал поступает из бункера 8 и движется в желобе по поверхности перегородки. Вентилятором 5 с двигателем 10 через всасывающий фильтр 9 и гибкий шланг 7 подают воздух в нижнюю часть желоба, который равномерно распределяется по всей поверхности перегородки и, проходя сквозь нее, аэрирует слой материала, приводя его в состояние текучести. Далее воздух проходит сквозь слой материала и пропускается через матерчатые фильтры 4, расположенные в окнах по всей длине крышки желоба. Подача воздуха регулируется дросселем
6. Пневматический желоб в ряде случаев выгоднее винтового конвейера, так как в нем отсутствуют движущиеся изнашивающиеся части и он менее энергоемок. Давление сжатого воздуха составляет 0,005 МПа, скорость
перемещения частиц материала – не более 4…7 м/с, а концентрация до
600…800 кг/кг.
В последнее время на ряде промышленных предприятий успешно применяют контейнерный пневмотранспорт (рис. 5.11, е). Материал при таком пневмотранспортировании перемещается по трубопроводам в специальных емкостях под действием давления воздуха. Высоконапорное импульсное пневмотранспортирование (рис. 5.14) осуществляется в установках пульсирующего действия. В них материал перемещается импульсами в виде пробок с промежутками, заполненными сжатым воздухом. Материал подается с высокой концентрацией, и его можно транспортировать, даже если он имеет плохую текучесть, склонен к налипанию на стенки трубопровода. Также можно перемещать без разрушения частиц гранулированные и зернистые материалы. Импульсное транспортирование со скоростями от 2 до 6 м/с отличается высокой экономичностью, так как при минимальном расходе воздуха достигается высокая производительность. Малые скорости материаловоздушных потоков дают возможность снижать общие энергетические затраты, сокращать абразивный износ элементов установки, транспортировать чувствительные к истиранию продукты, ликвидировать расслоение подаваемой смеси и применять фильтрующие установки с малой поверхностью фильтров.
Рис. 5.14. Схемы импульсного пневмотранспортирования:
а – импульсная подача с образованием пробок в начале транспортного трубопровода;
б – импульсная подача с прокладкой перфорированного транспортного трубопровода;
в – импульсная подача с прокладкой параллельного воздухопровода с форсунками
Разгрузчики цемента. В последние годы созданы разнообразные машины для выгрузки цемента из крытых железнодорожных вагонов, судов и барж. Наиболее широко применяются вакуумные разгрузчики (рис. 5.15) производительностью 15…90 т/ч.
В состав разгрузчика входят: самоходное заборное устройство 1, гибкий цементопровод 2, осадительная камера 3, водокольцевой вакуум-насос 5, шкаф
с электроаппаратурой 4.
Заборное устройство серийных разгрузчиков цемента (рис 5.16) представляет собой самоходную тележку безрамной конструкции на двух ребристых металлических колесах 9 с приводом от индивидуальных электродвигателей 7 через специальные червячные редукторы 8. В центральной части тележки смонтирован редуктор 4 с электродвигателем 5 привода
253
подгребающих дисков 1, расположенных под углом 3° к плоскости пола вагона. В дисках выполнены пазы (перфорации) заданной формы со скошенными внутренними стенками. С помощью перфорации разгружаемый сыпучий материал подается вращающимися дисками к заборной кромке всасывающего сопла. Режим работы дискового питателя обеспечивает дозированную подачу материала к соплу, причем в процессе перемещения разгружаемый материал частично насыщается воздухом, что способствует интенсификации его поступления во всасывающее сопло. Для обрушения цементной массы на диски к передней стенке редуктора прикреплен штыревой рушитель 3. В ряде конструкций применяются приводные рушители. Над подгребающими дисками расположено всасывающее сопло 2, конфигурация которого обеспечивает введение материала во всасывающую линию при сравнительно небольших потерях давления на разгонном участке трубопровода. К верхней части сопла крепится поворотный патрубок 10, на который насаживается гибкий резинотканевый рукав 6. К нижней части сопла крепится зачистное устройство, улучшающее зачистку пола вагона от разгружаемого материала. Оператор с переносного пульта включением соответствующих кнопок может перемещать заборное устройство вперед, назад и разворачивать его на месте. Основные параметры, определяющие производительность заборного устройства, – диаметр перфорированных дисков и соответствующее сечение всасывающего сопла.
Рис. 5.15. Общий вид пневматического разгрузчика цемента всасывающего типа
Цементопровод разгрузчика состоит из трех секций резинотканевых рукавов общей длиной 12 м, что достаточно для забора материала из всех частей железнодорожного вагона. Увеличение длины всасывающей линии нежелательно, так как вследствие увеличения потерь давления ухудшается работа разгрузчика.
![]() |
Рис. 5.16. Заборное устройство пневматического разгрузчика всасывающего типа
Осадительная камера (рис. 5.17) состоит из камеры фильтров 4, механизма выгрузки 1 и механизма продувки фильтров 5. Камера фильтров представляет собой металлический бункер цилиндрической формы с коническим днищем, установленный на корпусе шнека 8 механизма выгрузки. В камере фильтров, разделенной на два отсека перегородкой, размещены рукавные фильтры 3. Фильтровальная рукавная ткань надета на проволочный каркас, предотвращающий сплющивание фильтра во время работы, и закреплена на нем хомутами. Собранные фильтры устанавливают и закрепляют в верхней части камеры. На конической части камеры фильтров расположены два люка для монтажа и ревизии фильтров. Под фильтрами смонтирован металлический отбойник 2, предохраняющий ткань фильтров от пробоя посторонними предметами, загрязняющими цемент, и отбрасываемыми лопастями шнека.
Фильтры очищаются во время кратковременного поочередного сообщения отсеков осадительной камеры с атмосферой. Механизм очистки (продувки) состоит из сварного корпуса, в котором расположены закрепленные на штоках тарелки клапанов. Закрываются наружные клапаны пружинами. Во время работы разгрузчика весь отсасываемый воздух проходит через фильтры в вакуум-насос. Для очистки фильтров шток клапана перемещается тросовой
системой вручную, при этом атмосферный воздух проходит с большой скоростью через фильтровальную ткань в обратном направлении.
Механизм выгрузки состоит из корпуса шнека 8, электродвигателя 6 с установленным и закрепленным на его валу напорным шнеком 12, узла уплотнения 7, обратного клапана 15, выгрузочного патрубка 14 и рамы 17. Напорный шнек плотно насажен на конусный конец винтовой втулки 10, напрессованной на вал электродвигателя, и закреплен с помощью шпильки 11. Уплотнение вала шнека обеспечивается вращающейся в гильзе 9 винтовой втулкой 10 в сочетании с сальниковой набивкой, выполненной из асбестографитового шнура диаметром 8 мм, поджатого в гнезде грундбуксой.
Рис. 5.17. Осадительная камера пневморазгрузчика цемента всасывающего типа
Основная масса цемента отбрасывается винтовой частью уплотнения, остальная часть задерживается сальниковой набивкой. Между винтовой втулкой и гильзой предусмотрен зазор 0,5…0,6 мм на сторону. При увеличении этого зазора надежность работы уплотнения снижается.
Для предотвращения проникновения атмосферного воздуха в полость шнека в патрубке механизма выгрузки устанавливается обратный клапан 15, создающий цементную пробку в гильзе. Для этого в конструкции шнека часто предусматривается уменьшение шага витков в направлении движения материала, но это увеличивало потребляемую мощность и износ шнека и гильзы 13. Выполнение шнека с большим шагом на конце, как показано на рис.
5.17, обеспечивает создание надежной цементной пробки в конце гильзы даже в разгрузчиках цемента всасывающе-нагнетательного и нагнетательного действия, а также в пневмоподъемниках, когда вместо выгрузочного патрубка 14 имеется смесительная камера, в которой цемент перемешивается с воздухом, подаваемым под давлением. Ось клапана смонтирована на шарикоподшипниках в выносных опорах. Для обеспечения необходимой износостойкости витки шнека наплавляются по торцовой и рабочей поверхности износостойкой порошковой лентой.
Для создания разрежения в системе пневматического разгрузчика цемента применяют водокольцевой вакуум-насос соответствующей производительности по воздуху. В комплект электрооборудования входят шкаф с электроаппаратурой; две клеммные коробки, одна из которых устанавливается в помещении склада цемента, а вторая – на заборном устройстве; переносной пульт управления и комплект электрокабелей. В системе дистанционного управления заборным устройством применено безопасное напряжение 40 В. В пластмассовом корпусе пульта управления смонтированы кнопки управления заборным устройством и тумблер включения дискового питателя. В электрошкафу расположена вся пусковая аппаратура и приборы контроля. Открывающаяся передняя дверца и съемная задняя стенка обеспечивают удобство монтажа и обслуживания электроаппаратуры. Заборное устройство через распределительную коробку соединено с электрошкафом и пультом управления кабелями.
С переносного пульта управления включаются и выключаются электродвигатели привода перфорированных дисков и колес.
Все агрегаты разгрузчика и клеммные коробки для заземления присоединены к общему заземляющему контуру склада цемента.
Агрегаты пневморазгрузчика устанавливают на месте эксплуатации в соответствии с типовой схемой прирельсового склада цемента силосного типа (рис. 5.18) в целях повышения эксплуатационной производительности пневморазгрузчика осадительную камеру целесообразно располагать возможно ближе к рельсовому пути над приемным бункером вместимостью не ниже 1,5…2 т.
Под приемным бункером монтируют пневматический подъемник цемента соответствующего типоразмера, обеспечивающий подачу разгружаемого материала в силосные емкости склада.
Вакуум-насос с водоотделительным бачком и шкаф с э
|
|
Историки об Елизавете Петровне: Елизавета попала между двумя встречными культурными течениями, воспитывалась среди новых европейских веяний и преданий...
Наброски и зарисовки растений, плодов, цветов: Освоить конструктивное построение структуры дерева через зарисовки отдельных деревьев, группы деревьев...
Автоматическое растормаживание колес: Тормозные устройства колес предназначены для уменьшения длины пробега и улучшения маневрирования ВС при...
Опора деревянной одностоечной и способы укрепление угловых опор: Опоры ВЛ - конструкции, предназначенные для поддерживания проводов на необходимой высоте над землей, водой...
© cyberpedia.su 2017-2024 - Не является автором материалов. Исключительное право сохранено за автором текста.
Если вы не хотите, чтобы данный материал был у нас на сайте, перейдите по ссылке: Нарушение авторских прав. Мы поможем в написании вашей работы!