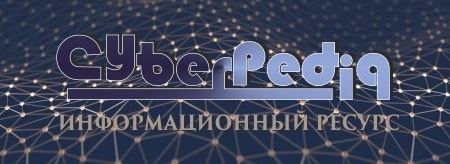
История развития пистолетов-пулеметов: Предпосылкой для возникновения пистолетов-пулеметов послужила давняя тенденция тяготения винтовок...
Индивидуальные и групповые автопоилки: для животных. Схемы и конструкции...
Топ:
Установка замедленного коксования: Чем выше температура и ниже давление, тем место разрыва углеродной цепи всё больше смещается к её концу и значительно возрастает...
Характеристика АТП и сварочно-жестяницкого участка: Транспорт в настоящее время является одной из важнейших отраслей народного хозяйства...
Интересное:
Инженерная защита территорий, зданий и сооружений от опасных геологических процессов: Изучение оползневых явлений, оценка устойчивости склонов и проектирование противооползневых сооружений — актуальнейшие задачи, стоящие перед отечественными...
Берегоукрепление оползневых склонов: На прибрежных склонах основной причиной развития оползневых процессов является подмыв водами рек естественных склонов...
Аура как энергетическое поле: многослойную ауру человека можно представить себе подобным...
Дисциплины:
![]() |
![]() |
5.00
из
|
Заказать работу |
|
|
1.Общие сведения об обрабатывающем оборудовании
Обрабатывающее оборудование представляет собой важнейшую часть основных средств предприятий, и является мощным технико-производственным потенциалом. Поэтому вопросы использования оборудования должны быть предметом постоянного внимания. В процессе эксплуатации машин, станков, оборудования их работоспособность снижается главным образом вследствие износа отдельных деталей. В результате этого снижается точность обработки изделий, уменьшается мощность и производительность. Эти эксплуатационные характеристики оборудования можно восстановить благодаря техническому обслуживанию, ремонту, замене деталей или узлов.
К основным видам обрабатывающего оборудования относят металло-, дерево-, камнеобрабатывающие и другие станки, а также металлообрабатывающие центры, деревообрабатывающие машины (кроме клеильно-сборочного и отделочного оборудования). Для обработки металлов давлением применяют оборудование, выполняющее такие операции: прокатку (прокатные станы и т. п.), прессование (прессы), волочение (волочильные станы), ковку и штамповку (молоты, штампы) и др.
В промышленности и сельском хозяйстве наиболее распространены металло- и деревообрабатывающие станки, ручной и механизированный (с электрическим или пневматическим приводом) инструмент, который используют для обработки металла, древесины, пластмасс и других материалов.
Особые группы составляют абразивный инструмент и материалы, а также измерительный инструмент и приборы.
2.Металлообрабатывающее оборудование
Основное оборудование механических цехов составляют металлообрабатывающие станки. В группу металлообрабатывающих входят металлорежущие станки для обработки режущим инструментом изделий из металлических материалов, а также пластмасс, стекла, керамики и др. Их классифицируют по таким признакам:
|
• назначению и конструктивным особенностям — на группы (0—9) и типы (0—9);
• степени специализации — на универсальные, специализированные и специальные;
• точности обработки — на классы нормальной (Н), повышенной (П), высокой (В), особо высокой (А) и особо точные (С);
• габаритным размерам и массе — легкие до 1 т, средние — до 10 т и тяжелые — более 10 т;
• степени автоматизации управления — на четыре категории: 1 — неавтоматизированные, 2 — полуавтоматизированные, 3 — автоматы и 4 — саморегулируемые.
Для обозначения типов и моделей принята система, в соответствии с которой все серийно выпускаемые станки подразделяют на девять групп, а каждую из групп — на девять типов.
В марке станка первая цифра обозначает номер группы, вторая — тип, последние — главные размеры станка или обрабатываемой детали. Буквы расшифровываются так: Г — горизонтальный, Ф — фрезерный, Р — расточной, С — сверлильный, Ф с цифрами 1—4 — система программного управления. Другие буквы обозначают модернизацию, класс точности и модификацию станка. Например, 16К20Ф3 — токарно-винторезный станок, модернизированный с программным управлением.
Для повышения производительности и улучшения условий труда используют обрабатывающие центры на базе многооперационных станков с ЧПУ, промышленные роботы, робототехнические комплексы и автоматизированные линии.
Металлорежущие станки комплектуются разнообразным металлообрабатывающим инструментом, который группируют по типам станков: резцы для токарных, фрезы, сверла, зуборезной, резьбонарезной, шлифовальный и т. д. Любой инструмент, связанный с обработкой материалов, должен превосходить их по твердости.
Резец — режущий инструмент в виде стержня прямоугольного, квадратного или круглого сечения, передняя режущая часть которого (головка) имеет определенную форму и затачивается под углом, зависящим от свойств обрабатываемого материала, режимов резания и других факторов.
|
Резцы классифицируют по таким признакам:
• технологическим группам станков — на токарные, строгальные, долбежные;
• выполняемым работам — на токарные проходные прямые, проходные упорные, подрезные прямые, подрезные упорные, подрезные торцевые, прорезные, канавочные, отрезные, расточные, гал-тельные, строгальные, строгальные чистовые, подрезные, долбежные проходные и прорезные, для нарезания наружной и внутренней резьбы и т. д.;
• направлению подачи — на продольные, радиальные, тангенциальные;
• обрабатываемому материалу — для металла, дерева, полимерных материалов и др.;
• конструкции — на цельные, составные, сварные, сборные с механическим креплением твердосплавных пластинок;
• направлению режущей кромки — на левые и правые;
• материалу режущей части — на углеродистые, легированные, быстрорежущие стали; твердосплавные; металлокерамические; композиционные и др.
Фреза — многолезвийный режущий инструмент для обработки материалов на фрезерных станках, в процессе которой он совершает вращательное движение, перпендикулярное оси вращения подачи.
Фрезы классифицируют по таким признакам:
• назначению — для обработки плоскостей, снятия фасок, нарезки зубьев и червячных колес, обработки пазов, канавок и шлицев;
• форме зубьев — на прямые, наклонные, винтовые, разнонаправленные, остроконечные;
• устройству — на цельные, составные, комплектные, сборные;
• способу крепления — на насадные и концевые;
• направлению винтовых канавок — на право- и леворежущие фрезы;
• виду поверхности, на которой имеются зубья, — на цилиндрические прямозубые, с винтовыми зубьями, концевые, дисковые двух-и трехсторонние; торцовые, концевые, пальцевые модульные, червячные.
Сверлильные и расточные станки комплектуют сверлами, зенкерами, зенковками, развертками и другим инструментом.
Сверло — стержень, рабочая часть которого имеет режущие элементы, а хвостовая служит для закрепления сверла в патроне или шпинделе станка. Сверла используют для образования отверстий в материале, а также для рассверливания отверстий. Их классифицируют по конструкции на спиральные (винтовые), кольцевые, конические, сверла-зенкеры, комбинированные, для глубокого сверления (ружейные, пушечные), перовые.
|
Зенкер — многолезвийный инструмент для зенкерования — чистовой обработки отверстия после сверления. Зенкеры классифицируют по конструкции на гладкие, зенкеры для ступенчатых отверстий, насадные, перовые и зенкеры-улитки.
Зенковка — многолезвийный режущий инструмент, который применяют для получения цилиндрических или конических углублений и отверстий, снятия фасок. Зенковки классифицируют по конструкции на зенковки и зенковки-подрезки.
Развертка — многолезвийный режущий инструмент для точной отделки отверстий круглого сечения. Развертки классифицируют по таким признакам:
• виду обрабатываемых отверстий — на цилиндрические и конические;
• виду обрабатываемых материалов — для обычных и нержавеющих сталей, легких сплавов;
• виду обработки — для черновой или чистовой;
• конструкции и назначению — на ручные цилиндрические, разжимные, регулируемые; машинные с цилиндрическим или коническим хвостиком; для глухих и сквозных отверстий.
Протяжки — многолезвийный (многорезцовый) металлорежущий инструмент для обработки сквозных отверстий и наружных поверхностей способом протягивания на протяжных станках. Их классифицируют по конструкции и назначению на круглые с продольной схемой резания или наклонного резания, для квадратных отверстий, шлицевые и шпоночные.
Зуборезный инструмент используют для изготовления и отделки зубчатых и червячных колес, зубчатых реек и других изделий на зубонарезных станках. В качестве зуборезного инструмента применяют фрезы, долбяки, резцы, гребенки, шеверы (зубчатые колеса или рейки с режущей кромкой) и головки (для нарезания конических зубчатых колес).
Для нарезания резьбы используют резьбонарезной инструмент: метчики ручные, машинные и машинно-ручные; головки; гребенки; фрезы резьбовые гребенчатые и дисковые; плашки; патроны муфтовые и трубонарезные; резцы для нарезания наружной и внутренней резьбы на токарных станках.
|
Для грубой и чистовой обработки поверхностей на шлифовальных и полировальных станках используют инструменты с абразивными материалами (кварцем, корундом и др.).
Шлифовальный круг — жесткий монолитный абразивный инструмент, изготовленный на основе абразивных материалов, неорганических и органических связок.
Для маркировки шлифовальных кругов на их торцевую поверхность несмываемой краской наносят следующие обозначения: изготовитель (например, ЗАК — Запорожский абразивный комбинат), абразивный материал (ЭБ — электрокорунд белый), зернистость (40 мкм), степень твердости шлифовального круга (СМ2), связка (К — керамическая), структура (№ 6), геометрическая форма (ПП — плоский прямой профиль), наружный диаметр (500 мм), высота круга (50 мм), диаметр отверстия (305 мм), возможная окружная скорость круга (35 м/с).
Широко применяются специальные цилиндрические, угловые, конические, сводчатые, шаровые шлифовальные головки, квадратные, плоские, трехгранные, круглые, полукруглые шлифовальные бруски, плоские, выпукло-вогнутые, вогнуто-выпуклые, выпукло-плоские, плоско-выпуклые, трапециевидные шлифовальные сегменты.
Инструмент для шлифовальных и полировальных станков поставляется в комплекте с запасными частями и хранится вместе со станками.
3.Деревообрабатывающее оборудование
К деревообрабатывающему оборудованию относят дереворежущие станки, клеильно-сборочное и отделочное оборудование для производства многочисленных полуфабрикатов и изделий (пиломатериалов, фанеры, древесностружечных и древесноволокнистых плит, строительных деталей, мебели, музыкальных инструментов, спортивного инвентаря, деталей транспортных средств и др.). Основную группу деревообрабатывающего оборудования составляют дереворежущие станки, предназначенные для механической обработки (резания) древесины и древесных материалов. Дереворежущие станки имеют ряд общих признаков с металлорежущими. Их классифицируют по таким признакам:
• назначению и степени универсальности — на общего назначения (универсальные), специализированные и специальные;
• степени автоматизации — на ручные, полуавтоматы и автоматы.
Основные узлы у дереворежущих станков — станина, шпиндель, рабочий стол и др. — подобны узлам металлорежущих. Однако эти станки имеют свою специфику, связанную с их назначением и свойствами обрабатываемого материала. Дереворежущие станки имеют свою систему условных обозначений. Она включает первые буквы наименования станка и цифры, обозначающие один из важнейших параметров станка или обрабатываемой детали, а также номер модели.
Виды дереворежущих станков при маркировке обозначают буквами:
|
• лесопильные вертикальные рамы: одноэтажная — Р; двухэтажная — 2Р;
• лесопильные горизонтальные рамы — РГ;
• ленточнопильные станки: столярные — ЛС; делительные — ЛД; для продольной распиловки бревен — ЛБ;
• круглопильные для продольной распиловки (деления) бревен (с подачей на тележке) — ЦДТ; пиломатериалов — ПД; прирезные — ЦДК;
• круглопильные для поперечной распиловки: балансирные — ЦКБ; маятниковые — ЦМЭ;
• суппортные (с прямолинейным перемещением пилы) — ЦПА;
• фуговальные — СФ;
• рейсмусовые — СР;
• фуговально-рейсмусовые — ФР;
• четырехсторонние продольно-фрезерные — С;
• шипорезные для рамного шипа: односторонние — ШО, двухсторонние — ШД; для обработки ящичного, прямого шипа — ШП; для шипа типа "ласточкин хвост" — ШЛХ;
• фрезерные — Ф;
• сверлильные — СВ;
• сверлильно-фрезерные (пазовальные) — СВП;
• цепно-долбежные — ДЦ;
• токарные — Т;
• круглопалочные — КП;
• шлифовальные — ШЛ.
Например, последовательность символов ЛД125-1 обозначает ленточнопильный делительный станок с пильными шкивами диаметром 125 см (первая модель); С2Р12-2 — рейсмусовый двухсторонний станок с максимальной шириной обработки 1250 мм (вторая модель).
По назначению деревообрабатывающие станки подразделяют на три группы для раскроя древесных материалов, черновой и чистовой обработки заготовок.
Раскроем называют распиловку пиловочного сырья (кряжей, бревен), пиломатериалов (брусьев, досок) и листовых материалов (фанеры, столярных плит) в продольном или поперечном направлении, а также удаление пороков и получение криволинейных заготовок. Для раскроя используют лесопильные рамы, лентопильные и круглопильные станки, которые обладают большой производительностью, имеют большие размеры и поставляются по специальным заказам.
Для механической обработки древесины используют также деревообрабатывающий инструмент. Его классифицируют по таким признакам:
• назначению — для продольной и поперечной распиловки: пилы — ручные поперечные двухсторонние, продольные односторонние; лучковые, машинные рамные; ленточные, поперечные, продольные, дисковые, ножовки по дереву узкие и широкие;
• для образования отверстий — долота, долбежники, буравы, коловороты, сверла для ручного и машинного сверления — спиральные, ложечковые, центровые, буравочные;
• для обработки поверхности — топоры, колуны, стамески, рубанки ручные и электрические; фуганки ручные; цикли, струги, железки — шерхебельные, цинубельные, зензубельные, фальц-гобельные, а также по способу обработки.
Некоторые виды деревообрабатывающего инструмента входят в комплект деревообрабатывающих станков.
Некоторые группы ручного и механизированного инструмента (слесарный, кузнечный абразивный), а также измерительный инструмент и приборы функционируют самостоятельно.
4.Ручной инструмент и измерительные приборы
В группу ручного входят слесарный, кузнечный и другие виды инструмента.
Слесарный инструмент предназначен для выполнения слесарных и сборочных (монтажных) работ:
• сборки разъемных винтовых соединений — отвертки, гаечные и раздвижные ключи, торцевые шпильковерты;
• удержания обрабатываемых изделий в рабочем положении — ручные стуловые и параллельные тиски, механические клещи, струбцины, домкраты, плоскогубцы и круглогубцы;
• "откусывания" проволоки — острогубцы, пассатижи, прямые и обковые кусачки;
• снятия слоя и рубки листового металла — зубила;
• рубки твердых металлов и вырубки узких канавок — крейцмейсели, бородки;
• разметки — кернеры, поверочные и разметочные плиты;
• поперечного распиливания, пропиливания и резания — ножовки по металлу, монтерские — нескладные ножи, труборезы, ножницы по металлу с разными ножами (параллельными, наклонными, дисковыми, высечными, вибрационными, летучими);
• снятия малых слоев металла, точной подгонки и заточки режущего инструмента — рашпили, напильники, надфили (разной конфигурации), шаберы, абразивные бруски;
• сборочно- и электромонтажных работ — ключи гаечные с трещоткой, шарнирный инструмент (плоскогубцы комбинированные; кусачки прямые и боковые), отвертки слесарно-монтажные с диэлектрическими ручками, паяльники, паяльные лампы;
• нарезания и накатывания резьбы — клуппы с резьбонарезными и резьбонакатными плашками (лерками), фрезы резьбонарезные гребенчатые и дисковые, головки резьбонарезные, резьбонакатные головки и метчиками с воротками.
Для пластического формования металла ручной или машинной ковки применяют кузнечный инструмент (наковальни, кувалды, ручники, клещи, зубила), а для вспомогательных работ при ковке — кантователи, подъемные краны и трансманипуляторы для больших поковок, а для средних и мелких — специальные клещи.
Все более широкое применение для облегчения ручной обработки различных материалов находят элоктрофицированные инструменты – переносные механизмы.
Электроинструменты относительно легки, снабжены мотором малой мощности, питающимся от бытовой электросети.
Любой электроинструмент состоит из электромотора, рабочей части и механизма управления, смонтированных в одном корпусе. Передача движения от мотора к режущему инструменту осуществляется двумя способами: рабочая часть соединена непосредственно с электромотором и имеет одинаковое с ним число оборотов или с помощью специального передаточного механизма, состоящего из системы шестеренок, - редуктора.
К электроинструменту относят:
- - электродрели - предназначены для сверления отверстий в металле, дереве, пластмассе, кирпиче, бетоне. В качестве рабочего режущего инструмента должны применяться сверла;
- электрошлифовальные и электро-виброшлифовальные машины – предназначены для обработки прямых и угловых поверхностей. Выпускают их в двух исполнениях: прямыми и угловыми. В качестве рабочего инструмента машин должны применяться шлифовальные круги;
- электропилы – используют для продольной и поперечной распиловки древесины. В качестве рабочего инструмента в пилах электрических должны применяться круглые плоские пилы. Конструкция электрических пил должна обеспечивать: смену пилы без снятия защитных ограждений, расклинивание при распиловке древесины, регулировку и фиксацию глубины пропила, распиловку древесины под углом от 90 до 450 к опорной поверхности с фиксацией установленного положения, стационарную установку;
- электроножницы – используют для резки листового металла;
- электрорубанки – предназначены для строгания древесины разных пород вдоль и поперек волокон. Рабочим инструментом рубанков должна быть цилиндрическая фреза со вставленными плоскими ножами;
- электрогайковерты, электролобзики, электрошуруповерты, электродолбежники, электроперфораторы, электроотбойные молотки, электротрамбовки и др.
Шкальный контрольно-измерительный инструмент предназначен для определения геометрических размеров деталей машин и изделий. Его классифицируют по таким признакам:
• назначению — для определения наружных размеров деталей (гладкие микрометры); измерения толщины листовых материалов (листовые с циферблатом); измерения длин, высот, глубины (трубные микрометры); измерения конусов (калибры, шаблоны); измерения внутренних размеров изделий и деталей (нутромеры или штих-массы); измерения глубины отверстий, полостей, пазов, высоты уступов (глубиномеры). Цена деления глубиномеров, как правило, 0,01 мм, пределы измерения 0—100 мм. Нутромеры бывают индикаторные, а глубиномеры подразделяются на индикаторные и штангенглубиномеры;
• конструктивным — на штриховые измерительные инструменты (измерительные линейки, угольники, метры длины, угломеры с нониусом, рулетки, штангенциркули, угломеры с конусом для измерения наружных углов от 0 до 180°) и универсальные инструменты с точным микрометрическим винтом и ценой деления 0,001— 0,1 мм (микрометры).
К бесшкальному измерительному инструменту относят калибры, пробки, втулки, скобы, профильные калибры-шаблоны, которые широко используются в машино- и приборостроении. Их применяют для проверки размеров и форм изделий и деталей или взаимного расположения их поверхностей. Бесшкальный инструмент классифицируют по таким признакам:
• назначению — для проверки валов (скобы), отверстий (пробки), конических соединений (пробки и втулки), линейных размеров, а также калибры;
• способу проверки изделий или деталей — нормальные для проверки номинального размера и предельные одно- и двухсторонние, имеющие два размера, отвечающие наименьшему и наибольшему допустимым размерам;
• измеряемому пределу — на проходные и непроходные;
• применению — для контрольных операций на рабочем месте, контроля ОТК, контроля представителя заказчика, а также эталонные калибры для проверки рабочих и приемных калибров;
• конструкции — на цельно-жесткие, составные, регулируемые, калибры толщины стенок труб, зубомерные.
Инструменты маркируют с помощью этикетки, бирки, оттиска товарного знака на изделии или тарном месте. На бирке указывают наименование завода-изготовителя, тип изделия, стандарт, дату изготовления, количество единиц изделий в упаковке и др.
Абразивы — твердые природные и искусственные материалы, предназначенные для разрушения (изменения) поверхности обрабатываемых материалов.
Природными абразивами являются алмазы, корунды, наждак, гранит, кремень, кварц, известь, крокус, а искусственными — электрокорунды, монокорунд, карбид кремния, карбид бора, борсиликокарбид, искусственные алмазы. Основные характеристики абразивных материалов — форма, зернистость, твердость, механическая прочность, состав, объемная масса, абразивная способность.
Эти материалы применяют для шлифования. В зависимости от размера зерен их подразделяют на такие группы: шлифзерно (160— 2500 мкм), шлифпорошки (28—160 мкм), микрошлифпорошки (14— 63 мкм) и тонкие микрошлифпорошки (3,5—10 мкм) (табл. 3.3).
Размеры зерен обозначают цифрами и сочетанием буквы "М" и числа, показывающего размер зерна (для абразивных материалов с наименьшими размерами зерен).
В зависимости от процентного содержания основной фракции обозначение зернистости дополняют буквенным индексом для обозначения микропорошков (например, В, М60 или И) и шлифовальных порошков (55, Н-45, Д-41).
Абразивные материалы используют в абразивном инструменте — шлифовальных кругах, головках и брусках. Шлифовальные круги и головки применяют для комплектации шлифовальных станков, относящихся к металлообрабатывающему оборудованию. Бруски — это инструмент для ручной заточки и отделки поверхностей. В зависимости от твердости шлифовальный инструмент обозначают индексом М (мягкий), СМ (среднемягкий), С (средний), СТ (среднетвердый), Т (твердый).
Для связывания частиц абразивного материала используют неорганические (керамические, магнезиальные, специальные) и органические (бакелитовые, глифталевые, вулканитовые) вещества.
Шлифовальная шкурка — это гибкий абразивный инструмент с основой из ткани или бумаги со слоем абразивного зерна, закрепленного клеем. Она может поставляться в рулонах и листах.
Шлифовальная шкурка маркируется буквами, обозначающими ее основу (БШ — бумажную, БТР — бязевую, НЛ — нанковую), после которых следуют размеры рулона или листа (соответственно в ммхм и ммхмм), масса бумаги в г/м2 (для шлифовальной шкурки на бумажной основе) и марка абразивного материала.
Например, шлифовальная шкурка на бязевой основе марки БТР 755x50360 или НЛ 775х595Э46, расшифровывается так: БТР — бязь рулонная; НЛ — нанка тяжелая, листовая; 755 мм х 50 м, Э — электрокорунд зернистостью № 60.
В настоящее время все больше применяют алмазные инструменты: правки, шлифовальные круги, мерительный инструмент, алмазные резцы, сверла и фрезы, коронки для буров, долот и другого инструмента на базе искусственных алмазов.
В технических товарных группах инструментов выделяют измерительные приборы. Их классифицируют по таким характеристикам:
• метрологическим — на рабочие и образцовые;
• точности — на приборы 1, 2 и 3-го разрядов, образцовые и эталоны;
• принципу действия (например, термометр жидкостный, манометр пружинный, ваттметр электродинамический и др.);
• способу получения числового значения — аналоговые (шкальные), цифровые, самопишущие и др.;
• в зависимости от рода измерений — для измерения температуры, давления, расхода жидкостей и газов, электрических величин и других параметров.
Для измерительных приборов разработана специальная система условных обозначений.
Приборы для измерения температуры характеризуют тепловое состояние вещества. Их подразделяют на две группы — контактные и бесконтактные. Контактные приборы бывают жидкостные (ртутные с диапазоном температур от —35 до 650 °С и не ртутные с диапазоном от —200 до 200 °С). К ним относятся жидкостные и манометрические термометры, а также термоэлектрические (термопары) и термометры сопротивления. Широко распространены контактные жидкостные термометры. Их классифицируют по назначению (для технических и лабораторных измерений) и расположению шкалы (палочной, в виде насечки по стеклу и вложенной). Для фиксации достигнутых за определенное время значений температуры (максимальных и минимальных), сигнализации и регулирования температуры используют термоконтакторы. Манометрические термометры передают показания температуры на расстояние. Они различаются по роду жидкости, области измерений, длине капилляра, классу точности. Термометры сопротивления применяются для измерения температуры различных сред в диапазоне —50—750 °С. Термоэлектрическими термометрами (термопарами) измеряют температуру в диапазоне —630—1600 °С в ограниченном объеме.
Бесконтактные приборы (пирометры) подразделяют на оптические (визуальные), работающие в интервале температур 800—4000 °С, и радиационные, измеряющие температуру в интервале 400—2500 °С.
К специальным термометрам относятся термоглубомеры.
Для измерения давления жидкостей и газов используют манометры (для измерения абсолютного давления), дифмано-метры (для измерения перепадов или избыточного давления), барометры (для измерения атмосферного давления).
Для электроизмерений используют гальванометры, амперметры, вольтметры, омметры, ваттметры, осциллографы, магнитографы, логометры и другие приборы.
Хранение обрабатывающего оборудования и инструмента
Оборудование, комплектующие изделия к ним (запасные части) и инструмент содержат в сухих отапливаемых и неотапливаемых помещениях.
При поступлении на склад оборудование тщательно осматривают, проверяют комплектность, состояние консервации и крепления деталей, наличие механических повреждений, поломок и т. д.
Рабочую часть оборудования покрывают слоем солидола или технического вазелина и обертывают промасленной бумагой или пленкой. Затем оборудование укладывают на деревянных прокладках с комплектующими изделиями в одном месте склада.
Для предохранения от пыли и грязи оборудование покрывают чехлами. Съемные части оборудования, запасные части и инструмент к нему тщательно просматривают, при необходимости консервируют, завертывают в промасленную бумагу или пленку и укладывают в ящики по описи отдельно для каждого станка. На ящике и в описи необходимо указать инвентарный номер оборудования, к которому они предназначены. Помещение, в котором хранится оборудование, должно быть сухим и проветриваемым. Осмотр оборудования и комплектации проводят регулярно, а при выявлении недостатков принимают меры по их устранению.
Инструмент упаковывают в картонные коробки, деревянные неразборные ящики и другую приспособленную тару. Для защиты от коррозии применяют пергамент или специальную бумагу.
На складе инструмент хранят в соответствии с требованиями стандартов, инструкций, правилами техники безопасности, промышленной санитарии и противопожарной безопасности в закрытых, сухих, отапливаемых и проветриваемых помещениях при определенной влажности и температуре. Применяют штабельное хранение на ящичных поддонах и стеллажное.
Технологическое оборудование транспортируют, как правило, в закрытом специально оборудованном подвижном составе (крытых фургонах, автофургонах и т. п.), контейнерах в затаренном состоянии с указанием количества мест в соответствии с упаковочным листом и сопроводительными документами. Инструмент следует перевозить в таре или контейнерах, предохраняя от ударов, порчи, загрязнения и увлажнения.
Особые условия поставки, транспортировки, комплектации и хранения указывают в договорах поставки, сопроводительных документах, стандартах и технических условиях, инструкциях заводов-изготовителей на данный вид оборудования или инструмента.
|
|
Механическое удерживание земляных масс: Механическое удерживание земляных масс на склоне обеспечивают контрфорсными сооружениями различных конструкций...
Автоматическое растормаживание колес: Тормозные устройства колес предназначены для уменьшения длины пробега и улучшения маневрирования ВС при...
Типы оградительных сооружений в морском порту: По расположению оградительных сооружений в плане различают волноломы, обе оконечности...
История развития пистолетов-пулеметов: Предпосылкой для возникновения пистолетов-пулеметов послужила давняя тенденция тяготения винтовок...
© cyberpedia.su 2017-2024 - Не является автором материалов. Исключительное право сохранено за автором текста.
Если вы не хотите, чтобы данный материал был у нас на сайте, перейдите по ссылке: Нарушение авторских прав. Мы поможем в написании вашей работы!