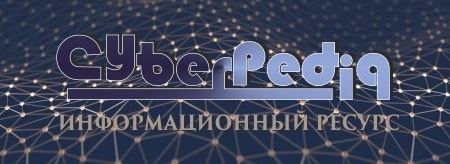
История создания датчика движения: Первый прибор для обнаружения движения был изобретен немецким физиком Генрихом Герцем...
Механическое удерживание земляных масс: Механическое удерживание земляных масс на склоне обеспечивают контрфорсными сооружениями различных конструкций...
Топ:
Проблема типологии научных революций: Глобальные научные революции и типы научной рациональности...
Выпускная квалификационная работа: Основная часть ВКР, как правило, состоит из двух-трех глав, каждая из которых, в свою очередь...
Особенности труда и отдыха в условиях низких температур: К работам при низких температурах на открытом воздухе и в не отапливаемых помещениях допускаются лица не моложе 18 лет, прошедшие...
Интересное:
Лечение прогрессирующих форм рака: Одним из наиболее важных достижений экспериментальной химиотерапии опухолей, начатой в 60-х и реализованной в 70-х годах, является...
Уполаживание и террасирование склонов: Если глубина оврага более 5 м необходимо устройство берм. Варианты использования оврагов для градостроительных целей...
Наиболее распространенные виды рака: Раковая опухоль — это самостоятельное новообразование, которое может возникнуть и от повышенного давления...
Дисциплины:
![]() |
![]() |
5.00
из
|
Заказать работу |
|
|
Вакуумные печи можно рассматривать как альтернативу повсеместного метода закалки в масле. Нагрев происходит конвективно с давлением газа до 3 бар и/или в вакууме. Хорошее расположение зоны вывода горячих газов из нагревательной камеры дает улучшение равномерности охлаждения и великолепные результаты скорости охлаждения. Закалка возможна различными газами: азотом, гелием, водородом до давления 20 бар.
Закалка газом вызывает существенно меньшие коробления. Оборудование позволяет выбирать скорость закалки. Следовательно, деталь закаливается с той скоростью, которая дает необходимую твердость, но не быстрее, так как повышенная скорость ведет к повышенной деформации.
Наиболее известные производители вакуумных печей в Европе немецкая фирма «ALD» и польская фирма «SEKO/WARWICK» производят горизонтальные, вертикальные вакуумные печи, печи с вращающимся подом во время цикла охлаждения. Диффузионный насос NH35 в печах с вращающимся подом позволяет работать с рабочим вакуумом 2∙10мбар.
Вакуумные печи SWL c круглой нагревательной камерой и нагревательными элементами из изогнутого графита, со вспомогательным оборудованием оборудованием конвекционного нагрева ConFlap в настоящее время являются авангардом конструкций вакуумных печей.
Вакуумная термическая обработка благоприятна с точки зрения окружающей среды. Отпадают такие экологические проблемы, как масло, моющие средства или закалочные соли.
Вакуумные установки для термической обработки работают:
1) с равномерным нагревом; 2) высокой равномерностью температуры; 3) равномерной закалкой; 4) изменяемой скоростью закалки; | 5) высокой мощностью закалки; 6) коротким временем циклов; 7) конвективным нагревом. |
Вакуумные печи гарантируют:
|
1) незначительные коробления;
2) надежность;
3) экономичность.
Вакуумная цементация и нитроцементация
Вакуумная цементация и нитроцементация представляют собой наиболее эффективные способы насыщения сталей. В качестве насыщающей атмосферы при цементации используют ацетилен, при нитроцементации ацетилен и аммиак.
Разработана уникальная технология вакуумной цементации FineCarb, которая основывается на смеси трех газов. Эта технология гарантирует чистый процесс без внутреннего окисления, которое можно наблюдать при технологии основанной на ацетилене.
Вакуумная цементация проводится в вакууме при давлении 1-15 Мбар в углеродсодержащей среде, где носителем является этилен с ацетиленом, смешанные с водородом или аммиаком в определенной запатентованной пропорции.
Возможно использование газов пропана (С2Н4), этилена(С22Н2) или ацетилене (С22Н2).
Ионное азотирование
Ионное азотирование (азотирование в тлеющем разряде) является новым высокоэффективным методом поверхностного упрочнения деталей.
Первые установки для ионного азотирования были созданы фирмой «Клокнер Ионен» в г.Кельне Германия. Широко используется в Швейцарии, Франции, США.
Методом ионного азотирования можно обрабатывать улучшаемые, специальные, инструментальные стали, а также чугуны.
Сущность ионного азотирования заключается в следующем. В разреженной азотсодержащей атмосфере между катодом (деталью) и стенками камеры электрической печи, которая заземлена и является анодом, возбуждается тлеющий разряд, и ионы газа, бомбардируя поверхность катода, нагревают его до температуры насыщения.
Рабочая температура процесса ионного азотирования выбирается в зависимости от обрабатываемого материала и может колебаться от 350 до 600°С (для улучшаемых сталей 500°С - 540°С). Напряжение 400-1100 В, разрежение 133-1330 Па.
Рабочее давление лимитируется свойствами тлеющего разряда. При давлении ниже 133 Па энергия ионов недостаточна для нагрева обрабатываемой детали до рабочей температуры, при давлении выше 1330 Па нарушается стабильность разряда, тлеющий разряд переходит в дуговой, что сопровождается появлением на поверхности оплавленных микрократеров
|
Выбор оптимального давления зависит от сложности конфигурации детали, так как с изменением давления изменяется протяженность каждой части разряда. С увеличением давления от 133 до 1330 Па область каждой части разряда уменьшается. Это необходимо учитывать для обеспечения равномерности диффузионного слоя по периметру изделия.
Плотность тока в больших пределах (0,5-20 мА/м2) не оказывает влияния на процесс азотирования.
В качестве азотсодержащих газов применяют аммиак, азот и смесь азота с водородом.
Глубина азотированного слоя может быть 0,2-0,8мм. Твердость 80-92 HRN15.
|
|
Археология об основании Рима: Новые раскопки проясняют и такой острый дискуссионный вопрос, как дата самого возникновения Рима...
Автоматическое растормаживание колес: Тормозные устройства колес предназначены для уменьшения длины пробега и улучшения маневрирования ВС при...
Индивидуальные очистные сооружения: К классу индивидуальных очистных сооружений относят сооружения, пропускная способность которых...
Биохимия спиртового брожения: Основу технологии получения пива составляет спиртовое брожение, - при котором сахар превращается...
© cyberpedia.su 2017-2024 - Не является автором материалов. Исключительное право сохранено за автором текста.
Если вы не хотите, чтобы данный материал был у нас на сайте, перейдите по ссылке: Нарушение авторских прав. Мы поможем в написании вашей работы!