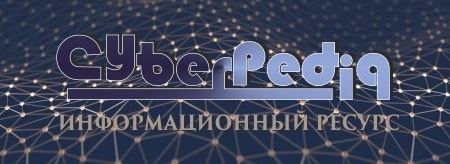
Археология об основании Рима: Новые раскопки проясняют и такой острый дискуссионный вопрос, как дата самого возникновения Рима...
Биохимия спиртового брожения: Основу технологии получения пива составляет спиртовое брожение, - при котором сахар превращается...
Топ:
Определение места расположения распределительного центра: Фирма реализует продукцию на рынках сбыта и имеет постоянных поставщиков в разных регионах. Увеличение объема продаж...
Проблема типологии научных революций: Глобальные научные революции и типы научной рациональности...
Отражение на счетах бухгалтерского учета процесса приобретения: Процесс заготовления представляет систему экономических событий, включающих приобретение организацией у поставщиков сырья...
Интересное:
Инженерная защита территорий, зданий и сооружений от опасных геологических процессов: Изучение оползневых явлений, оценка устойчивости склонов и проектирование противооползневых сооружений — актуальнейшие задачи, стоящие перед отечественными...
Средства для ингаляционного наркоза: Наркоз наступает в результате вдыхания (ингаляции) средств, которое осуществляют или с помощью маски...
Искусственное повышение поверхности территории: Варианты искусственного повышения поверхности территории необходимо выбирать на основе анализа следующих характеристик защищаемой территории...
Дисциплины:
![]() |
![]() |
5.00
из
|
Заказать работу |
|
|
Метод ремонта для цилиндра выбирают: ремонт цилиндра путем восстановления номинальных размеров вибродуговой наплавкой.
Наплавку широко применяют при восстановлении деталей полиграфических машин.
Наплавка – нанесение расплавленного металла на поверхность детали, нагретую до температуры плавления. Наплавка применяется для восстановления размеров, а также для повышения твердости и износостойкости рабочих поверхностей деталей. Вес наплавляемого металла обычно незначителен по отношению к весу детали.
Вибродуговая наплавка применяется для восстановления требуемых размеров детали и придания заданных свойств ее поверхности путем подбора химического состава и структуры наплавляемого металла.
Сущность вибродуговой наплавки состоит в следующем. Электрод с помощью специального устройства вибрирует, периодически касаясь наплавляемой детали. В момент короткого замыкания конец электрода плавится, и расплавленный металл переносится на деталь.
Для вибродуговой наплавки используется постоянный ток, вырабатываемый генератором 10. Сила тока регулируется дросселем 9. Вибратор электрода состоит из качающегося рычага 3 и электромагнита 4, питаемого переменным током. Пружины 8 способствуют созданию устойчивых колебаний рычага. Электродная проволока проходит через мундштук 2, укрепленный на качающемся рычаге. Автоматическая подача проволоки из кассеты 6 производится роликовым механизмом 5, приводимым в действие электродвигателем 7 на рисунке 5.1.
В зону наплавки охлаждающая жидкость подается насосом 1 по шлангу. Охлаждающая жидкость защищает металл от окисления кислородом воздуха, уменьшает зону термического воздействия, способствует быстрому формированию шва, повышает твердость наплавленного слоя. В качестве охлаждающей жидкости применяют 5…6%-ный раствор кальцинированной соды с добавкой 0,5…0,6% автола.
|
Рисунок 5.1 - Вибродуговая наплавка
Наплавляемая деталь устанавливается в центрах токарного станка. Головку для вибродуговой наплавки монтируют на суппорте вместо резцедержателя. В процессе наплавки деталь вращается со скоростью 0,2…0,4 м/мин. Каретке суппорта с головкой сообщается продольная подача 2…3 мм/об.
Вибродуговая наплавка применяется для восстановления изношенных цилиндрических поверхностей. Толщина слоя, наплавляемого за один проход, составляет 0,5…3,5 мм и зависит от диаметра электродной проволоки, который принимается 1,5…2,5 мм.
Технологический процесс вибродуговой наплавки включает:
· подготовку изношенной поверхности детали,
· наплавку слоя металла или сплава,
· механическую обработку.
Подготовка деталей под вибродуговую наплавку предусматривает выполнение следующих операций:
· очистка детали от грязи, ржавчины и масел;
· механическую обработку деталей с неравномерным износом для придания наплавляемой поверхности правильной геометрической формы; местные дефекты на наплавляемой поверхности (выбоины, вмятины) глубиной более 2 мм заделывают электродуговой сваркой;
· изоляцию поверхностей детали (отверстий, пазов), которые не подлежат наплавке путем постановки медных, графитовых или стальных вставок.
Для удаления вставок после наплавки они должны выступать над поверхностью детали на величину несколько большую толщины наплавляемого слоя.
Механическая обработка после вибродуговой наплавки для получения требуемых размеров, классов точности, посадок и шероховатости поверхностей деталей производится точением твердосплавными режущими инструментами и шлифованием.
Вибродуговую наплавку выбирают потому, что (она) находит широкое применение в ремонтном деле благодаря следующим своим достоинствам:
|
· малая величина деформации деталей;
· возможность получения относительно твердых слоев без термической обработке (НRC38…56);
· высокое качество наплавляемого слоя;
· высокая производительность процесса;
· не требует высоких денежных затрат.
Метод ремонта для кронштейна выбирают: ремонт деталей с применением компенсаторов износа.
Долговечность полиграфических машин, возможность сокращения объемов ремонтных работ во многом зависит от того, применяются ли устройства, компенсирующие износ деталей.
Этими устройствами чаще всего являются детали – компенсаторы тем, или иным способом погашающие износ основных деталей полиграфических машин, называются деталями – компенсаторами.
Детали – компенсаторы применяют при восстановлении:
· отверстий малого диаметра;
· поверхностей, имеющих значительный износ;
· плоских поверхностей большой протяженности;
· поверхностей, механические свойства которых должны быть выше, чем при наплавке металла.
Компенсаторы износа применяют при необходимости увеличить размеры деталей в связи с тем, что сопряженные с ним другие детали в процессе ремонта потеряли первоначальные размеры.
Используя детали – компенсаторы, можно сохранить в соединениях частично изношенные детали, не нарушая точности этих соединений.
Компенсаторы износа изготавливают в виде различных втулок (гильз), колец, резьбовых ввертышей, зубчатых венцов колес.
Существуют детали – компенсаторы сменные (при ремонте кронштейна). Сменные компенсаторы износа устанавливают в сопряжении, в котором износ появился к моменту ремонта. К этой группе деталей – компенсаторов относят, например, неполадки цилиндрической фрикционной муфты, втулки 1 на рисунке 4.2. Сменные компенсаторы износа закрепляют на одной из сопрягаемых деталей при помощи прессовой посадки, винтов, сварки, клеев.
Рисунок5.2 - Метод компенсаторов износа
Ремонт деталей с применением компенсаторов износа я выбрал потому, что (метод ремонта с применением компенсаторов износа) находит широкое применение в ремонтном деле благодаря следующим своим достоинствам:
· высокая производительность;
· простота ремонта;
· очень экономичен;
· не требует высокой квалификации рабочего;
· не требует высоких денежных затрат.
|
6 РАСЧЁТНАЯ ЧАСТЬ ПРОЕКТА.
6.1 Расчёт ремонтного размера деталей.
Расчет ремонтного размера цилиндра.
Определяется ремонтный размер цилиндра при износе поверхностей диаметром 38f7.
Расчет ремонтного размера цилиндра выполняется по табличным значениям величины предельного износа и припуска на обработку. Ремонтный размер цилиндра определяется по формуле ([1], с.80, формула (8)):
, (6.1)
Где - номинальный размер поверхности трения цилиндра, мм.
= 38мм.
- ремонтный интервал. определяется по формуле ([1], с.81,формула (9)):
, (6.2)
где - предельная величина износа поверхности цилиндра, мм.
мм ([1],таблица 16, с.78);
- припуск на шлифование цилиндра, мм; при длине свыше 250 до 500
мм ([1], с.134).
Подстановкой вышеуказанных значений в формулу (6.2), а затем в формулу (6.1) получаем:
,
,
Ремонтный размер цилиндра диаметром 37.43f7 мм.
Расчет ремонтного размера кронштейна.
Выполняется расчет ремонтного размера отверстий детали кронштейн диаметр 25Н7 при условии что деталь в механизме неподвижна.
Ремонтный размер отверстия кронштейна Ø25Н7 определяют для подвижного соединения вал – кронштейн Ø25 .
Расчет ремонтного размера отверстия кронштейна выполняют по табличным значениям величин предельного износа, припуска на обработку и предельных отклонений поверхностей трения.
Ремонтный размер отверстия кронштейна определяют по формуле ([1], с.82, формула (10)):
, (6.3)
где - номинальный размер, мм;
мм (в Приложении А);
- межремонтный интервал, мм; определяется по формуле ([1], с.82, формула (11)):
, (6.4)
где - величина предельного износа отверстия, мм; определяется по формуле ([1], с.82, формула (12)):
|
, (6.5)
где - предельная величина зазора в изношенном сопряжении, мм;
мм ([1], с.76);
- предельная величина износа по поверхности, мм;
мм ([1], с.76);
- предельная величина зазора при посадке Ø
, мм; определяется по формуле ([1], с.80, формула (7)):
, (6.6)
где - наибольший предельный диаметр вала, мм;
мм (в Приложении А);
- наименьший предельный диаметр отверстия кронштейна, мм;
мм (в Приложении А);
- припуск на обработку отверстия, мм;
мм ([1], с.135).
Подстановкой вышеуказанных значений в формулы (6.6), (6.5), (6.4) и (6.3) получаем:
мм,
мм,
мм,
мм
Ремонтный размер отверстия кронштейна Ø25,506 Н7 и соединения после ремонта Ø 25,506 .
6.2 Расчет усилия запрессовки втулки при ремонте деталей
Определить усилие запрессовки бронзовой втулки длиной L, мм; L =20 мм и внешним диаметром Ø36 мм в чугунный кронштейн Ø36 , если шероховатость сопряженных поверхностей
мм.
Усилие запрессовки (в Приложении Б).
Схема полей допусков соединяемых деталей на рисунке 6.1.
Рисунок 6.1 – Схема полей допусков соединяемых деталей
Усилие запрессовки, , Н; определяется по формуле ([1], с.90 формула (23)):
, (6.7)
где - коэффициент трения при запрессовке
([1], с.92 таблица 21);
D – Номинальный диаметр поверхности сопряжения
D=36 мм=3.6∙10-2 м (Приложение Б);
L – Длина запрессовки L=20 мм=2∙10-2 м (Приложение Б);
p – Напряжения сжатия, Па; на контактные поверхности определяется по формуле ([1], с.90, формула (24)):
, (6.8)
где - максимальный натяг, мм; для посадки Ø36
определяется по формуле ([1], с.90, формула (20)):
, (6.9)
где - наибольший предельный диаметр втулки, мм (на рисунке 6.1);
- наименьший предельный диаметр отверстия кронштейна, мм (на рисунке 6.1);
- сумма среднеарифметических отклонений профиля определяется по формуле ([1], с.90, формула (21)):
, (6.10)
где и
- среднее арифметическое отклонение профиля сопрягаемых поверхностей соответственно охватываемой и охватывающих деталей, мм;
мм (в Приложении Б);
|
Е1 и Е1 - модули упругости материала втулки и кронштейна Па;
Е1 =1,1∙10 11 Па; Е2=1,2∙10 11 Па ([1], с.93 (таблица 22));
С1 и С1 – коэффициенты С1=1.87; С2=4.8 ([1], с.91 таблица 20).
Подстановкой вышеуказанных значений в формулу (6.9), (6.10), (6.8), а затем в формулу (6.7) получаем:
,
,
,
.
Усилие, которое необходимо приложить при запрессовке бронзовой втулки в чугунный кронштейн составляет 5652 Н.
|
|
Автоматическое растормаживание колес: Тормозные устройства колес предназначены для уменьшения длины пробега и улучшения маневрирования ВС при...
Общие условия выбора системы дренажа: Система дренажа выбирается в зависимости от характера защищаемого...
Двойное оплодотворение у цветковых растений: Оплодотворение - это процесс слияния мужской и женской половых клеток с образованием зиготы...
История развития пистолетов-пулеметов: Предпосылкой для возникновения пистолетов-пулеметов послужила давняя тенденция тяготения винтовок...
© cyberpedia.su 2017-2024 - Не является автором материалов. Исключительное право сохранено за автором текста.
Если вы не хотите, чтобы данный материал был у нас на сайте, перейдите по ссылке: Нарушение авторских прав. Мы поможем в написании вашей работы!