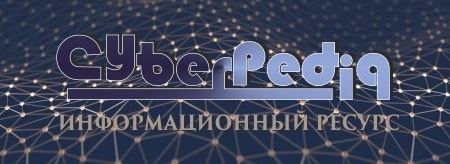
Кормораздатчик мобильный электрифицированный: схема и процесс работы устройства...
Биохимия спиртового брожения: Основу технологии получения пива составляет спиртовое брожение, - при котором сахар превращается...
Топ:
Отражение на счетах бухгалтерского учета процесса приобретения: Процесс заготовления представляет систему экономических событий, включающих приобретение организацией у поставщиков сырья...
Генеалогическое древо Султанов Османской империи: Османские правители, вначале, будучи еще бейлербеями Анатолии, женились на дочерях византийских императоров...
Интересное:
Лечение прогрессирующих форм рака: Одним из наиболее важных достижений экспериментальной химиотерапии опухолей, начатой в 60-х и реализованной в 70-х годах, является...
Наиболее распространенные виды рака: Раковая опухоль — это самостоятельное новообразование, которое может возникнуть и от повышенного давления...
Распространение рака на другие отдаленные от желудка органы: Характерных симптомов рака желудка не существует. Выраженные симптомы появляются, когда опухоль...
Дисциплины:
![]() |
![]() |
5.00
из
|
Заказать работу |
|
|
Подготовка дисперсной фазы
Размол Подготовка термопластичной связки
Сушка
Приготовление шликера
Загрузка
Расплавка
Вакуумирование
Подготовка формы к заполнению шликером
Заливка под давлением
Низкотемпературный отжиг, удаление связки
Высокотемпературный отжиг
Операция | Т, ᵒС | Время, t | Давление, Р | Оборудование | |
Подготовка дисперсной фазы | Размол | от нескольких часов до нескольких суток | - | ШВМ, планетарные центробежные мельницы, вихревые мельницы | |
Сушка | 100-150 оС | 2-3 ч. | - | Сушильные шкафы | |
Подготовка термопластичной связки (Парафин,воск,олеиновая кислота)-смешение | |||||
Подготовка шликера | Загрузка | - | - | - | Установка для вакуумирования шликера (емкость, оборудованная пропеллерной мешалкой, подключенная к ресиверу и вакуумному насосу) |
Расплавка |
60-80 оС | - | |||
Вакуумирование | 5-6 мин | 0,8 атм | |||
Подготовка формы к заполнению шликером | - | - | - | Форма собирается вручную. |
Заливка под давлением | 70-100 оС | до 60 мин | 0,3 – 0,6 МПа | Подается в форму от установки для вакуумирования шликера |
Низкотемпературный отжиг | 650-700 С | 3 - 4 ч | - | Печи различных типов |
Удаление связки | 1200 – 1300 оС | Будет зависеть от используемой связки-основы | - | Печи предварительного спекания |
Высокотемпературный отжиг | 1690 – 1700 оС | 2-4 ч | - | Печь с выкатным подом и высокотемпературные печи |
|
Шликерное формование позволяет получать изделия сложных форм, мало- и крупногабаритные, полые с равномерной толщиной стенок, с высокой чистотой поверхности и точных размеров.
К основным свойствам шликеров относят текучесть, характеризующую его способность течь, заполнять форму и увеличивать массу заготовки, и устойчивость, то есть способность не расслаиваться в течение длительного времени. Различают седиментационную и агрегативную устойчивость. Седиментационная устойчивость определяется скоростью оседания твердых частиц в жидкости. Она зависит от плотности материала порошка, формы и размера частиц (размера в большей степени), а также от концентрации твердой фазы в шликере. Чем тяжелее частицы, чем ближе их форма к сферической, тем быстрее произойдет расслоение.
Агрегативная устойчивость связана со слипанием отдельных частиц в более крупные агломераты под действием электростатических сил Величина этих сил зависит от природы твердой и жидкой фаз, дисперсности порошка, формы частиц, величины удельной поверхности, поверхностных энергий обеих фаз, характера процессов на межфазных границах.
Обычно концентрация твердой фазы в шликерах от 40 до 70%, в данном случае около 80%.
Дисперсность порошка, используемого при приготовлении шликеров составляет от 1 – 3 мкм (W, Mo) до 5 – 10 мкм (Fe, Ni, Cu). Предельным значением видимо является 40 мкм (Al и другие легкие металлы).
Жидкая фаза шликера должна иметь низкую упругость пара, быть нетоксичной, пожаровзрывобезопасной (желательно), не должна активно взаимодействовать с твердой фазой, одновременно хорошо смачивая ее. Смачиванием можно управлять, добавляя в жидкость поверхностно-активные вещества (ПАВ). Наиболее часто в качестве основы жидкой фазы используют воду, которая обеспечивает шликеру достаточную жидкотекучесть, хорошее заполнение формы и даже возможность прокачки по трубопроводам. Для нашего случая используется олеиновая кислота.
|
Подготовка дисперсной фазы включает в себя получение или выделение порошка заданной дисперсности и формы, что призвано обеспечить максимальную плотность укладки без ухудшения технологических свойств шликера. Крупные порошки дают неустойчивые суспензии и заготовки с пониженной прочностью. Высокодисперсные порошки (обеспечивая шликеру хорошую седиментационную устойчивость, а заготовкам достаточную прочность) имеют низкую скорость набора массы; полученные формовки могут коробиться при спекании из-за анизотропии усадки. Измельчение порошка для шликера целесообразно проводить в жидкости во избежание адсорбции на его поверхности газов, ухудшающих смачивание. Затем идет просушка.
При приготовлении термопластичных шликеров (ТПШ) в качестве связки чаще (и в нашем случае тоже) всего используют парафины (предельные углеводороды) с общей формулой CnH2n+2: от нонадекана C19H40 до пентатриоктана C35H72. Температура плавления этих соединений меняется в диапазоне от 49 до 54 оС. Парафины легко растворяются в органических растворителях. Кроме них можно использовать церезины и полиэтилен. Последний хорошо смешивается с парафинами, и его применяют в качестве добавки, увеличивающей устойчивость шликеров. Есть упоминания об использовании при приготовлении ТПШ воска, твердых жиров, пеков, фенолформальдегидных смол.
Любая связка в расплавленном состоянии должна смачивать твердую дисперсную фазу и не должна образовывать вокруг ее частиц толстые структурированные оболочки с аномально высокой вязкостью.
Термопластичные шликеры готовят, перемешивая порошок с расплавленной связкой, причем частицы твердой фазы часто предварительно подогревают до 60 – 80 оС. Содержание связки (пластификатора) в ТПШ 8 – 15% (14,35%).
Обычно формы для этой разновидности шликерного формования изготавливают из стали; при производстве небольших партий изделий их делают из меди, алюминиевых сплавов, пластика и даже гипса. В нашем случае использовалась стальная форма.
Термопластичные шликеры на парафиновой основе формуют, предварительно разогревая их до 70 – 100 оС и заливая в равномерно подогретые резервуары, откуда шликеры будут перекачиваться в формы под избыточным давлением 0,3 – 0,6 МПа. Помимо перекачки это давление обеспечит хорошее заполнение всего объема формующей полости, особенно тонких каналов и сечений.
|
Важно, чтобы избыточное давление поддерживалось в системе до момента полного затвердевания шликера, чтобы естественно возникающая усадка не изменила геометрию заготовки.
Очень важной операцией при формовании ТПШ является отгонка пластификатора, которая в большинстве случае сочетается с начальным (неизотермическим) периодом спекания. Она осуществляется при медленном нагреве, с промежуточными изотермическими выдержками. В качестве поглотителя расплавленного пластификатора используют ламповую сажу, активированный уголь, оксид алюминия, прокаленный при 1200 – 1300 оС. В нашем случае изделие спекалось при 1150 оС при первом низкотемпературном отжиге для удаление связки.
Процесс удаления связки включает в себя ее плавление, улетучивание легких фракций углеводородов, пиролиз (термическое разложение) тяжелых фракций, выгорание углеродного остатка. Общая продолжительность этого процесса, длительность отдельных его этапов, скорости подъема температуры, температуры и время изотермических выдержек будут зависеть от используемой связки-основы ТПШ.
Второй раз мы спекаем в печи высокотемпературного отжига при 1690 – 1700 оС.
Коэффициент усадки изделия в конечном итоге составляет 1,2-1,19.
Конечная плотность изделия 3,85 – 3,90 г/см3.
4.Основные производственные цеха и участки
1.Участок размола порошка Рис. 1, 2 | Содержит шаровые вращающиеся мельницы, гуммированные резиной, в которых осуществляется мокрый размол порошка. Производительность- 50 т в месяц. |
Рис. 1 Рис. 2
2.Участок приготовления смеси Рис. 3,4 | В результате размола получают пульпу, которая поступает на сушку. Полученную смесь просеивают на вибросите. В зависимости от дальнейшего цикла производства в порошок может быть добавлена связка (каучука в бензине, поливиниловые спирты, растворы ПВС в воде). После смешивания идет протирка и грануляция смеси, в результате которой уходит весь бензин и смесь становится очень пластичной. Количество связки зависит от способа формования порошка. Так, например, для прессования на гидравлическом прессе вводят 4-5 об. % связки, тогда как для шликерного формования необходимо 30-40 об. %. Приготовление шликера также происходит в этом цехе. |
![]() |
|
![]() |
3.Цех формования Рис. 5 Гидравлический пресс Рис. 6 Механический пресс Рис.7 Машина для литья ТПШ Рис.8 Пресс горячего прессования | Основным производственным помещением является цех формования, в котором установлены гидравлические пресса, гидравлический длинноходовой пресс мундштучного формования усилием 100т, механические пресса с автоматической подачей навески, на которых получают 1000-3000 изделий за смену, машина для литья термопластичного шликера и пресс горячего формования. |
Рис. 5 Рис. 6
Рис. 7 Рис. 8
4.Участок удаления связки и спекания Рис. 9,11 Рис.10 Печь с выкатным подом | После формования заготовки, необходимо удалить связку. Процесс проводят в печах предварительного спекания объемом 200 л. Температура удаления связки 1150°С. Если заготовки имеют небольшие размеры, то удаление связки происходит в капсуле. Засыпкой служит, в основном, глинозём. акже на этом участке установлена печь с выкатным подом и высокотемпературные печи, максимальная температура нагрева в которых 1700°С. |
Рис. 9 Рис. 10 Рис. 11
5. Цех механической обработки Рис. 12 | В этом цехе установлены шлифовальные машины для механической обработки изделий, фрезерные станки и др. |
Рис. 12
|
|
Организация стока поверхностных вод: Наибольшее количество влаги на земном шаре испаряется с поверхности морей и океанов (88‰)...
Механическое удерживание земляных масс: Механическое удерживание земляных масс на склоне обеспечивают контрфорсными сооружениями различных конструкций...
Индивидуальные очистные сооружения: К классу индивидуальных очистных сооружений относят сооружения, пропускная способность которых...
Историки об Елизавете Петровне: Елизавета попала между двумя встречными культурными течениями, воспитывалась среди новых европейских веяний и преданий...
© cyberpedia.su 2017-2024 - Не является автором материалов. Исключительное право сохранено за автором текста.
Если вы не хотите, чтобы данный материал был у нас на сайте, перейдите по ссылке: Нарушение авторских прав. Мы поможем в написании вашей работы!