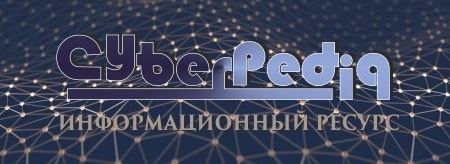
Типы сооружений для обработки осадков: Септиками называются сооружения, в которых одновременно происходят осветление сточной жидкости...
Индивидуальные очистные сооружения: К классу индивидуальных очистных сооружений относят сооружения, пропускная способность которых...
Топ:
Когда производится ограждение поезда, остановившегося на перегоне: Во всех случаях немедленно должно быть ограждено место препятствия для движения поездов на смежном пути двухпутного...
Генеалогическое древо Султанов Османской империи: Османские правители, вначале, будучи еще бейлербеями Анатолии, женились на дочерях византийских императоров...
Интересное:
Влияние предпринимательской среды на эффективное функционирование предприятия: Предпринимательская среда – это совокупность внешних и внутренних факторов, оказывающих влияние на функционирование фирмы...
Средства для ингаляционного наркоза: Наркоз наступает в результате вдыхания (ингаляции) средств, которое осуществляют или с помощью маски...
Искусственное повышение поверхности территории: Варианты искусственного повышения поверхности территории необходимо выбирать на основе анализа следующих характеристик защищаемой территории...
Дисциплины:
![]() |
![]() |
5.00
из
|
Заказать работу |
|
|
После изготовления отливки проходят окончательный контроль для определения соответствия их требованиям технических условий. В зависимости от назначения отливок производят контроль каждой отливки или выборочный контроль нескольких отливок от партии. Контролируют геометрические размеры отливки, химический состав, структуру и механические свойства; устанавливают отсутствие (наличие) внешних или внутренних дефектов в отливке.
Геометрические размеры проверяют при помощи шаблонов, приспособлений и контрольно-измерительного инструмента. Иногда производят разметку отливки на специальной разметочной плите, периодически отливки разрезают для определения размеров внутренних полостей. Таким контролем выявляют несоответствие размеров чертежу отливки вследствие износа модельно-опочной оснастки, неточности сборки, смещения стержней, коробления отливки под действием внутренних напряжений и др.
Химический состав определяют методом химического или спектрального анализа. При помощи спектрального анализа можно быстро определить содержание в сплаве марганца, кремния, хрома и других элементов. В спектральном приборе между электродом и образцом образуется электрическая искра (дуга), свет от которой разлагается оптической призмой на цветной спектр, характеризующий химический состав металла. Затем этот спектр сравнивается со спектром эталона и по интенсивности линий, характеризующих тот или иной элемент, судят о его содержании в металле.
Структуру металла определяют по излому специальных технологических проб (макроструктуру) или при рассмотрении под металлографическим микроскопом подготовленных образцов-шлифов при увеличении в 100—500 раз (микроструктуру).
|
Механические свойства (предел прочности, твердость, относительное удлинение, ударная вязкость и др.) определяют испытаниями отдельно изготовленных или прилитых к отливке образцов по методам, установленным стандартом.
Дефекты в отливках определяются визуальным способом (осмотром), люминесцентным, магнитным и ультразвуковым контролем, просвечиванием рентгеновскими и гамма-лучами, испытаниями на герметичность и другими способами. Наиболее распространенными дефектами в отливках являются: раковины различного происхождения — усадочные, газовые, шлаковые и песчаные; рыхлота и усадочная пористость; трещины — горячие и холодные, недоливы, пригар и др. (всего по ГОСТу классифицируется 22 наименования литейных дефектов; о дефектах, связанных с литейными свойствами).
![]() |
В процессе разработки литейной технологии сформирован комплект документов, содержащий:
1. Результаты расчётов:
· точность отливки,
· припуски на механическую обработку,
· формовочные уклоны,
· размеры и массы всех элементов ЛПС и металлоемкость формы.
2. Комплект документов ТЗ на модельно-стержневую оснастку:
· форма в сборе,
· модель низа,
· модель верха,
· расположение моделей на модельной плите низа,
· расположение моделей на модельной плите верха,
· сечение элементов литниковой системы и прибылей,
· теоретический чертеж и модель стержня.
3. Комплект документов на технологический процесс изготовления детали:
· титульный лист,
· карты технологической информации,
· маршрутно-операционные карты, карты эскизов.
Объект контроля | Метод и средства контроля | Исполнители | Техническая документация |
Поступающие исходные материалы - формовочные материалы. - шихтовый материал | - определение предела прочности на сжатие во влажном состоянии, влажности, предела прочности на растяжение в сухом состоянии, газопроницаемости. - контролируют по пределу прочности при растяжении отвержденных образцов, живучести, пределу прочности при сжатии - химический анализ | Контролер отдела технического контроля или службы управления качеством | ГОСТ 26645-85 «Отливки из металлов и сплавов допуски размеров, массы и припуски на механическую обработку» |
Приготовления формовочных и стержневых смесей. | - отбор проб от каждого замеса или серии нескольких замесов единой рецептуры. -Испытания на влажность, газопроницаемость, прочность на растяжение в сухом состоянии. | Контрольный мастер, формовщик | Маршрутно-операционные карты, карты эскизов. ГОСТ 26645-85 |
Модельный комплект | Контроль точности совмещения разъемных частей модели и стержневого ящика, соответствия размеров знаков моделей и стержневых ящиков с учетом необходимых уклонов и зазоров, обеспечивающих надежность сбоку формы, а также контроль качества отделки и окраски рабочих поверхностей модели и стержневого ящика. Средства контроля - усадочные метры, кронциркули и др. и визуальный осмотр. | Контрольный мастер, технолог или контролер ОТК | Чертеж детали, маршрутно-операционные карты, карты эскизов, ГОСТ 26645-85 Результаты расчётов. |
Литейные формы | -степень уплотнения смеси измерением поверхностной твердости формы, с помощью прибора - твердомера модели 071; визуально -отсутствие повреждений, равномерность нанесения на рабочую полость формы противопригарного покрытия | Контролер ОТК или службы управления качеством | ГОСТ 26645-85 маршрутно-операционные карты, карты эскизов. |
Стержни | целостность стержня и отсутствие трещин контролируется визуально, взаимное положение стержней контролируется шаблонами | Контролер ОТК или службы управления качеством | теоретический чертеж и модель стержня |
Заливка и выбивка форм | температура металла контролируется оптическими пирометрами и термопарами погружения | Контрольный мастер, технолог или контролер ОТК | форма в сборе, карты технологической информации |
Готовые отливки | геометрические размеры отливки, химический состав, структуру и механические свойства; устанавливают отсутствие (наличие) внешних или внутренних дефектов в отливке. Методом химического или спектрального анализа. | Контролер ОТК или службы управления качеством |
Таблица 2
|
|
II. Контроль качества штампованных заготовок
1. Исходные данные.
Рис. 4. Колесо зубчатое
Материал: Сталь 40Х ГОСТ 4543-71
2. Анализ служебного назначения
Зу́бчатое колесо́ (ше́стерня) — основная деталь зубчатой передачи в виде диска с зубьями на цилиндрической или конической поверхности, входящими в зацепление с зубьями другого зубчатого колеса. В машиностроении принято малое ведущее зубчатое колесо независимо от числа зубьев называть шестернёй, а большое ведомое — колесом. Однако часто все зубчатые колёса называют шестерня́ми.
Зубчатые колёса обычно используются па́рами с разным числом зубьев с целью преобразования вращающего момента и числа оборотов вала на выходе. Колесо, к которому вращающий момент подводится извне, называется ведущим, а колесо, с которого момент снимается — ведомым. Если диаметр ведущего колеса меньше, то вращающий момент ведомого колеса увеличивается за счёт пропорционального уменьшения скорости вращения, и наоборот. В соответствии с передаточным отношением, увеличение крутящего момента будет вызывать пропорциональное уменьшение угловой скорости вращения ведомой шестерни, а их произведение — механическая работа — останется неизменным. Данное соотношение справедливо для идеального случая, не учитывающего потери на трение и другие эффекты, характерные для реальных устройств.
Цилиндрическая шестерня является важным элементом в работе строительной, грузоподъемной, конвейерной и горно-шахтной техники. От того, насколько качественно и точно она будет изготовлена, зависит не только непосредственно ее долговечность, но и то, сколько времени прослужит ваша техника. Ведь поломка одной детали, ведет за собой повреждения и других частей механизма.
3. ОПРЕДЕЛЕНИЕ ТИПА ПРОИЗВОДСТВА
Тип производства предварительно определяется по массе и программе выпуска изделия. Масса изделия равна 12 кг., выпуск изделия 16 тысяч штук в год.
Таблица № 1
Тип производства | Число обрабатываемых деталей одного типоразмера в год | ||
Тяжелых (масса свыше 100 кг) | Средних (масса от 10 до 100 кг) | Легких (масса менее 10 кг) | |
Единичное | до 5 | до 10 | до 100 |
Мелкосерийное | 5 – 100 | 10 – 200 | 100 – 500 |
Среднесерийное | 100 – 300 | 200 – 500 | 500 – 5000 |
Крупносерийное | 300 – 1000 | 500 – 5000 | 5000 – 50000 |
Массовое | свыше 1000 | свыше 5000 | свыше 50000 |
Число обрабатываемых деталей одного типоразмера в год 16 тысяч штук. Обрабатываемые детали средние так как масса от 10 до 100 кг. Следовательно тип производства -массовое.
|
![]() |
Анализ физико-химических свойств и химического состава
стали 40Х ГОСТ 4543-71
Сталь 40Х – углеродистая конструкционная качественная сталь, легированная хромом. обладает высокой конструкционной прочностью, что обеспечивает длительную и надежную работу конструкции в условиях эксплуатации. имеет высокую сопротивляемость ударным нагрузкам, усталости, а при трении – износу, а так же коррозии. Хорошо обрабатывается давлением, резанием, трудно сваривается. В составе присутствуют дефицитные легирующие элементы.
![]() |
Технический контроль сварочного производства
Технический контроль в сварочном производстве разделяют на входной, операционный и приемочный. К входному контролю относят контроль основных и сварочных материалов и полуфабрикатов, предназначенных для использования при изготовлении изделий, а также предварительный контроль сварочного оборудования и квалификации сварщиков.
Входной контроль основных и сварочных материалов имеет целью не допустить использование некачественной продукции поставщика, поступившей к изготовителю сварных изделий.
Целью предварительного контроля является оценка работоспособности сварочного оборудования и допуск производственного персонала к выполнению сварочных работ.
Система операционного контроля предусматривает контроль технологического процесса и продукции во время выполнения или после завершения технологической операции. Контроль технологического процесса сварки включает контроль подготовки свариваемых деталей, их сборки под сварку, непосредственно процесса сварки и полученных сварных соединений.
Приемочный контроль сварных изделий включает внешний осмотр изделия и определение его размеров, а также испытания. При приемочном контроле проверяется соответствие изготовленной продукции требованиям НТД и принимается решение о ее пригодности к использованию.
Таким образом, учитывая особые требования к изготовлению сварных изделий, организация технического контроля в сварочном производстве должна быть направлена не только на приемочный контроль продукции, но и на контроль всех стадий производственного процесса ее изготовления, а также всех факторов, влияющих на качество продукции.
|
|
|
Папиллярные узоры пальцев рук - маркер спортивных способностей: дерматоглифические признаки формируются на 3-5 месяце беременности, не изменяются в течение жизни...
Историки об Елизавете Петровне: Елизавета попала между двумя встречными культурными течениями, воспитывалась среди новых европейских веяний и преданий...
Индивидуальные и групповые автопоилки: для животных. Схемы и конструкции...
Кормораздатчик мобильный электрифицированный: схема и процесс работы устройства...
© cyberpedia.su 2017-2024 - Не является автором материалов. Исключительное право сохранено за автором текста.
Если вы не хотите, чтобы данный материал был у нас на сайте, перейдите по ссылке: Нарушение авторских прав. Мы поможем в написании вашей работы!