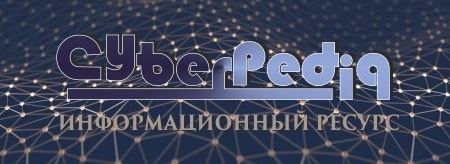
Типы оградительных сооружений в морском порту: По расположению оградительных сооружений в плане различают волноломы, обе оконечности...
Биохимия спиртового брожения: Основу технологии получения пива составляет спиртовое брожение, - при котором сахар превращается...
Топ:
Характеристика АТП и сварочно-жестяницкого участка: Транспорт в настоящее время является одной из важнейших отраслей народного хозяйства...
Отражение на счетах бухгалтерского учета процесса приобретения: Процесс заготовления представляет систему экономических событий, включающих приобретение организацией у поставщиков сырья...
Интересное:
Аура как энергетическое поле: многослойную ауру человека можно представить себе подобным...
Искусственное повышение поверхности территории: Варианты искусственного повышения поверхности территории необходимо выбирать на основе анализа следующих характеристик защищаемой территории...
Принципы управления денежными потоками: одним из методов контроля за состоянием денежной наличности является...
Дисциплины:
![]() |
![]() |
5.00
из
|
Заказать работу |
|
|
Введение
1.1. Настоящее Руководство распространяется на капитальный ремонт четырёхосных вагонов-самосвалов (думпкаров) (далее - Руководство) и устанавливает технические требования к организации ремонтного производства, ремонту и контролю узлов и деталей, испытаниям и приемки думпкаров после ремонта.
Настоящее Руководство разработано в соответствии с требованиями Руководящего документа "Руководство по капитальному ремонту грузовых вагонов" РД 32 ЦВ 168-2017, утвержденного протоколом Совета по железнодорожному транспорту государств - участников Содружества от 18 - 19 мая 2011 г. N 54 (далее - РД 32 ЦВ 168-2017).
1.2. При капитальном ремонте думпкаров в ОАО "РЖД", помимо настоящего Руководства, следует соблюдать требования нормативных правовых актов Российской Федерации, в том числе государственных стандартов, норм и правил, которые регулируют данные вопросы.
1.3. Капитальный ремонт предусматривает приведение в технически исправное состояние думпкаров, а также их узлов и деталей в целях обеспечения безаварийной работы вагона до следующего планового ремонта и соблюдения требований безопасности движения поездов.
1.4. Перечень нормативной и технической документации, на которые даны ссылки в настоящем Руководстве, приведены в приложении N 1.
1.5. Перечень стандартов, на которые даны ссылки в настоящем Руководстве, приведен в приложении N 2.
1.6. Общие виды думпкаров даны на рисунках 1.1 и 1.2.
1 - тележка; 2 - нижняя рама; 3 - кузов, состоящий из верхней рамы, продольных бортов и торцевых стенок; 4 - цилиндр подъема; 5 - тормозной цилиндр; 6 - автосцепное устройство
Рис. 1.1 - Вагон-самосвал (думпкар)
|
1 - тележка; 2 - нижняя рама; 3 - кузов, состоящий из верхней рамы, продольных бортов и торцевых стенок; 4 - цилиндр подъема; 5 - тормозной цилиндр; 6 - переходная площадка; 7 - автосцепное устройство
Рис. 1.2 - Вагон-самосвал (думпкар) с переходной площадкой
Организация ремонта
2.1. Указания по организации ремонта
2.1.1. Капитальный ремонт думпкаров следует проводить с периодичностью:
для вагонов принадлежности ОАО "РЖД" в соответствии с Положением о системе технического обслуживания и ремонта специальных вагонов грузового и пассажирского типов N 758-2016 ПКБ ЦВ, утвержденным распоряжением ОАО "РЖД" от 22 декабря 2016 г. N 2623р;
для вагонов независимо от формы их собственности, допущенных к эксплуатации на путях общего пользования в соответствии с требованиями Положения о системе технического обслуживания и ремонта грузовых вагонов, допущенных в обращение на железнодорожные пути общего пользования в международном сообщении, утвержденного протоколом Совета по железнодорожному транспорту государств - участников Содружества от 16 - 17 октября 2012 г. N 57.
2.1.2. Капитальный ремонт вагонов-самосвалов (думпкаров) должен выполняться на предприятиях, имеющих условный номер клеймения, полученный в соответствии с Положением об условных номерах клеймения железнодорожного подвижного состава и его составных частей, утвержденного протоколом Совета по железнодорожному транспорту государств - участников Содружества от 21 - 22 октября 2014 г. N 61.
Капитальный ремонт вагонов-самосвалов (думпкаров) выполняется для восстановления исправного состояния и полного или близкого к полному восстановлению ресурса вагона с заменой или восстановлением любых элементов его конструкции, включая базовые (ГОСТ 32884-2014).
2.1.3. Работы по капитальному ремонту думпкаров должны производиться в соответствии с технологическими процессами на капитальный ремонт и технологическими процессами работы производственных участков, разработанных вагоноремонтными предприятиями на основании настоящего Руководства и утвержденными в установленном порядке.
|
2.1.4. Техническое оснащение и метрологическое обеспечение вагоноремонтных предприятий, производящих капитальный ремонт думпкаров должны обеспечивать соблюдение требований технологических процессов разборки, мойки, дефектации, ремонта, контроля, сборки и испытания деталей и узлов думпкаров, установленных настоящим Руководством.
2.2. Требования к материалам и комплектующим изделиям
2.2.1. Применяемые в работе при капитальном ремонте думпкаров материалы, запасные части и комплектующее оборудование, должны отвечать установленным стандартам и техническим условиям, и выполнены в климатическом исполнении УХЛ категории 1 согласно ГОСТ 15150-69.
2.2.2. Масла и смазки, применяемые при ремонте думпкаров, приведены в приложении N 3.
2.3. Прием в ремонт
2.3.1. Направление думпкаров в капитальный ремонт осуществляется владельцем вагонов по истечении срока очередного планового ремонта в сроки, согласованные с вагоноремонтным предприятием, с оформлением сопроводительного листка формы ВУ-26М и уведомления формы ВУ-23М.
2.3.2. Перед подачей думпкаров в ремонт вагоны должны быть очищены от загрязнений и остатков грузов.
2.3.3. До постановки на ремонтную позицию думпкары осматриваются заместителем начальника ремонтного предприятия по ремонту, старшим мастером или мастером совместно с приемщиком вагонов, для определения объёма ремонтных работ и составления дефектной ведомости формы ВУ-22М.
2.3.4. Прием думпкаров в ремонт должен проводиться в соответствии с требованиями РД 32 ЦВ 168 - 2017 и разделом 2 настоящего Руководства.
2.4. Разборка, демонтаж оборудования
2.4.1. Принятый в ремонт думпкар подать на ремонтные позиции:
тележки из под вагона выкатить и подать на участок ремонта в тележечное отделение, ремонт выполняется в соответствии с требованиями РД 32 ЦВ 052-2009 Ремонт тележек грузовых вагонов тип 2 по ГОСТ 9246 с боковыми скользунами зазорного типа. Общее руководство по ремонту утвержденное протоколом Совета по железнодорожному транспорту государств - участников Содружества от 13 - 14 мая 2010 г. N 52 (далее - РД 32 ЦВ 052-2009);
колесные пары передать на позиции ремонта колесно-роликового отделения, осмотр и ремонт выполняется в соответствии с требованиями Руководящего документа по ремонту и техническому обслуживанию колесных пар с буксовыми узлами грузовых вагонов магистральных железных дорог колеи 1520 (1524) мм РД ВНИИЖТ 27.05.01-2017, утвержденного протоколом Совета по железнодорожному транспорту государств - участников Содружества от 19 - 20 октября 2017 г. N 67 (далее - РД ВНИИЖТ 27.05.01-2017);
|
снятое с вагона автосцепное устройство направляют на участок ремонта автосцепного устройства в (КПА), ремонт несъемных деталей автосцепного устройства: ударной розетки, передних и задних упоров, деталей расцепного привода производится непосредственно на вагоне в соответствии с требованиями Инструкции по ремонту и обслуживанию автосцепного устройства подвижного состава железных дорог, утвержденной протоколом Совета по железнодорожному транспорту государств - участников Содружества от 20 - 21 октября 2010 г. N 53;
снятое с вагона тормозное оборудование направляют на участок ремонта тормозного оборудования (АКП), где производят ремонт в соответствии с требованиями Общего руководства по ремонту тормозного оборудования вагонов N 732-ЦВ-ЦЛ, утвержденного протоколом Совета по железнодорожному транспорту государств - участников Содружества от 18 - 19 мая 2011 г. N 54 (далее - N 732-ЦВ-ЦЛ);
ремонт кузова и рамы вагона-самосвала (думпкара) производится в соответствии с требованиями Руководящего документа Руководство по капитальному ремонту грузовых вагонов РД 32 ЦВ 168-2017, Инструкции по сварке и наплавке при ремонте грузовых вагонов РД ВНИИЖТ 059/01-2019, утвержденной протоколом Совета по железнодорожному транспорту государств - участников Содружества от 4 - 5 ноября 2015 г. N 63 (далее - РД ВНИИЖТ 059/01-2019) и раздела 4 настоящего Руководства.
2.4.2. Демонтаж остального оборудования проводить по техническому состоянию, в соответствии с требованиями настоящего Руководства.
2.5. Очистка, мойка и сушка узлов и деталей
2.5.1. Мойку узлов и деталей думпкаров следует проводить в струйных моечных машинах с применением водных растворов технических моющих средств (ТМС), рекомендуемый перечень которых приведен в таблице 1.
Таблица 1
ПЕРЕЧЕНЬ
Технических моющих средств
|
Марка ТМС | Номер технических условий | Назначение |
О-БИС | ТУ 2381-001-00205357-99 | для обмывки подвагонного оборудования, тележек, колесных пар, корпусов крышек букс |
ВУК-Ф | ТУ 2499-002-31559149-2007 | для обмывки подвагонного оборудования, колесных пар, удаления смазки БУКСОЛ в подшипниках |
ТЕМП-100Д марки А | ТУ 2149-133-10968286-2001 | для обмывки корпусов, крышек букс |
РЕЙС | ТУ 2384-003-74827784-2005 | для ручной и автоматической обмывки вагонов и оборудования |
ТОР-ХС | ТУ 2385-002-74827784-2005 | для обмывки деталей машин и подшипников |
Допускается использование ТМС других марок аналогичного назначения, допущенных к применению в установленном порядке.
2.5.2. Детали автосцепного устройства, снятые с вагона-самосвала (думпкара) подлежащие проверке и ремонту, должны быть очищены от грязи средствами, имеющимися в распоряжении пункта ремонта в соответствии с требованиями пункта 1.9 Инструкции по ремонту и обслуживанию автосцепного устройства подвижного состава железных дорог, утвержденной протоколом Совета по железнодорожному транспорту государств - участников Содружества от 20 - 21 октября 2010 г. N 53.
2.5.3. Все детали тормозного оборудования промываются и продуваются сжатым воздухом, допускается:
промывка деталей регулятора в керосине с последующей обязательной просушкой их сжатым воздухом;
очистка авторежимов, воздухораспределителей, магистральных и главных частей рекомендуется способом струйной обмывки горячей водой (от 55 до 70 °С) под давлением в специальных моечных установках, при сильных загрязнениях производить наружную обмывку авторежимов 5% раствором кальцинированной соды, не допускается применение для наружной очистки керосина, бензина и других агрессивных веществ в соответствии с требованиями N 732-ЦВ-ЦЛ.
2.5.4. По окончании мойки детали и сборочные единицы следует подвергнуть сушке. Для ускорения процесса сушки детали обдуть сжатым воздухом давлением не более 0,15 МПа (1,5 кгс/см2).
2.6. Дефектация деталей и сборочных единиц
2.6.1. Дефектацию ходовой части, автосцепного и автотормозного оборудования, механизма разгрузки, цилиндров подъема думпкаров проводят методом визуального контроля с использованием контрольно-измерительных приборов, на специализированных рабочих местах, оснащенных специальным оборудованием.
Дефектация кузова и рамы вагона-самосвала (думпкара) выполняется в соответствии с требованиями РД 32 ЦВ 168 - 2017, РД ВНИИЖТ 059/01-2019 и настоящего Руководства.
Детали и сборочные единицы, подаваемые на дефектацию, должны быть чистыми и сухими.
Сборочные единицы и детали вагона подвергаются комплексному контролю и сортировке на следующие группы:
годные;
подлежащие ремонту (восстановлению);
|
негодные (брак).
У каждого рабочего места должна быть установлена тара для сбора негодных (отбракованных) деталей. Годные детали подаются на ремонтные и сборочные позиции.
2.6.2. Все шплинты и чеки крепления оборудования подлежат замене на новые, независимо от их технического состояния (без дефектации).
2.6.3. Контроль и диагностика деталей, сборочных единиц и комплектующего оборудования в общем случае предусматривает:
внешний осмотр визуально или с помощью лупы;
контроль размеров и геометрических форм с помощью средств измерений (СИ) и средств допускового контроля (СДК);
неразрушающий контроль ответственных деталей по п. 2.6.4;
стендовые испытания цилиндров подъёма на соответствие паспортным характеристикам.
2.6.4. Неразрушающий контроль деталей проводится в соответствии с требованиями:
Правил по неразрушающему контролю вагонов, их деталей и составных частей при ремонте. Общие положения. ПР НК В.1;
Правил неразрушающего контроля деталей и составных частей колесных пар вагонов при ремонте. Специальные требования. ПР НК В.2;
Правил неразрушающего контроля литых деталей тележек грузовых вагонов при ремонте. Специальные требования. ПР НК В.3;
Правил неразрушающего контроля деталей автосцепного устройства и тормозной рычажной передачи вагонов при ремонте. Специальные требования. ПР НК В.4;
Правил неразрушающего контроля сварных соединений при ремонте вагонов. Специальные требования. ПР НК В.5.
Детали и узлы грузовых вагонов. Руководство по испытанию на растяжение N 736-2010 ПКБ ЦВ, утвержденное протоколом Совета по железнодорожному транспорту государств - участников Содружества от 26 - 27 октября 2016 г. N 65.
2.6.5. Заклепочные соединения обстучать. При обнаружении признаков ослабления (дребезжании), а также трещин, сколов в головках, заклёпки заменить. Запрещается подчеканка или заварка ослабленных заклепок.
2.6.6. Болты, гайки, винты заменить при наличии следующих дефектов:
забоин, вмятин на резьбовой части;
срыва резьбы двух или более ниток;
смятия граней головок болтов, срыв шлицев под отвертку у винтов.
Запрещается устанавливать простые гайки вместо корончатых, предусмотренных чертежами завода-изготовителя.
2.6.7. Деревянные детали настила пола проверить на отсутствие механических повреждений и следов гнили, прочность соединений. Поврежденные деревянные брусья или швеллеры пола заменить. Допускается постановка деревянных брусьев встык, число стыков должно быть не более одного. Доски и бруски деревянного настила, в случае демонтажа верхнего металлического листа пола заменить.
Меры безопасности
3.1. Требования по охране труда
3.1.1. Общие требования по охране труда при ремонте думпкаров должны соответствовать ПОТ РЖД-4100612 ЦДИ-128-2018.
3.1.2. Меры безопасности при выполнении отдельных технологических операций при ремонте и испытаниях думпкаров должны быть указаны в технологических процессах, утвержденных на каждом вагоноремонтном предприятии в установленном порядке.
3.2. Экологические требования
3.2.1. Перечень нормативной документации, устанавливающей общие требования по охране окружающей среды от выбросов и сбросов загрязняющих веществ, правила обращения с отходами производства приведены в таблице 2.
Таблица 2
ПЕРЕЧЕНЬ
МЕРЫ
Ремонт
4.1. Общие требования
4.1.1. Новые детали и узлы, устанавливаемые на думпкары, взамен забракованных, при выполнении ремонтных работ должны быть изготовлены на вагоностроительных предприятиях или предприятиях, освоивших их производство в соответствии с требованиями действующих нормативных документов по постановке на производство продукции производственно-технического назначения. На запасные части и комплектующее оборудование, подлежащие обязательному подтверждению соответствия должны быть представлены соответствующие документы (сертификат, декларация и др.).
4.1.2. Восстановление деталей думпкаров сваркой и наплавкой, а также приемку после сварочных и наплавочных работ проводить в соответствии с требованиями РД ВНИИЖТ-059/01-2019.
4.1.3. Сварочные работы в местах, имеющих неогнестойкие элементы (деревянные, резиновые детали и т.д.), проводить с обязательной разборкой и удалением этих элементов из мест возможного соприкосновения с нагреваемым металлом, защитой от попадания брызг расплавленного металла, касания электродом.
4.1.4. Неогнестойкие элементы, расположенные вблизи места сварки, во избежание попадания на них брызг расплавленного металла или касания электродом, изолировать огнезащитным материалом.
4.1.5. Сопрягаемые плоскости металлических и деревянных деталей (не антисептированных) перед соединением их между собой прокрашивают или грунтуют.
4.1.6. При креплении деталей запрещается оставлять или устанавливать вновь болты и гайки, имеющие изношенную, или забитые грани, а также ставить болты, не соответствующие размерам отверстий и соединяемым частям или имеющие разнотипную с гайкой резьбу;
применять крепежные детали, не удовлетворяющие техническим требованиям, стандартам, комплекту конструкторской документации;
прожигать отверстия в деталях.
4.1.7. Шплинты и чеки на болты или валики ставят новые, типовые (стандартизированные).
При отсутствии специальных требований они должны отстоять от гайки или шайбы не более чем на 3 мм. Концы шплинтов и чек разводят под углом не менее 90°. Ослабшие и нестандартные заклепки и ШОГ (штифт с обжимной головкой) соединения заменяют.
Запрещается:
заменять предусмотренные конструкцией вагона заклепочные и ШОГ соединения на сварные или болтовые;
ставить простые гайки вместо корончатых, предусмотренных чертежом (техническими условиями);
производить подчеканку, заварку и подтягивание заклепок и ШОГ соединения;
оставлять без грунтовки металлические части кузова и рамы, в местах прилегания снятых для замены деталей;
применять материалы, не имеющие сертификата соответствия.
4.1.8. Заклепки должны соответствовать ГОСТ 10299-80, ГОСТ 10300-80, а также диаметру отверстия, и плотно скреплять соединяемые детали. Головки заклепок должны быть полномерными, без зарубок, трещин, вмятин, плотно прилегать к соединяемым деталям и располагаться центрально по отношению к оси стержня. Головки потайных заклепок не должны выступать над поверхностью листа более чем на 1мм.
4.1.9. Поврежденные доски пола заменить на новые, изготовленные из сосны, ели, лиственницы толщиной 60 - 75 мм. Доски настила пола должны быть плотно прижаты друг к другу. Бруски и доски должны быть пропитаны антисептиком по ОСТ 38.01117-76.
4.1.10. При ремонте деревянных деталей мелкие механические повреждения досок и брусьев, местные вмятины, отколы и т.п., не нарушающие сопряжения с другими деталями, допускается оставлять без ремонта.
4.2. Автосцепное устройство
4.2.1. Ремонт автосцепного устройства производить в соответствии с Инструкцией по ремонту и обслуживанию автосцепного устройства подвижного состава железных дорог, Типовым технологическим процессом ремонта автосцепного устройства ТК-289 и Инструкцией по сварке и наплавке при ремонте грузовых вагонов РД ВНИИЖТ-059/01-2019.
4.3. Тормозное оборудование
4.3.1. Ремонт тормозного оборудования производить в соответствии с требованиями N 732-ЦВ-ЦЛ.
4.4. Ходовые части
4.4.1. Тележки из-под вагонов выкатить, промыть в моечной машине и разобрать. Детали тележек очистить от грязи, продуктов коррозии и осмотреть.
4.4.2. Ремонт тележек производить в соответствии с требованиями РД 32 ЦВ 052-2009 "Ремонт тележек грузовых вагонов тип 2 по ГОСТ 9246 с боковыми скользунами зазорного типа. Общее руководство по ремонту".
4.4.3. Ремонт тележек моделей 18-9855, 18-194-1 с осевой нагрузкой 25 тс не включенных в РД 32 ЦВ 052-2009 "Ремонт тележек грузовых вагонов тип 2 по ГОСТ 9246 с боковыми скользунами зазорного типа. Общее руководство по ремонту", выполняется в соответствии с требованиями Руководства по ремонту 4701-09.00.00.000 РК "Тележка двухосная 18-9855, тип 3 ГОСТ 9246-2013" и Руководства по ремонту 194.00.000-1 РК "Тележка двухосная модель 18-194-1".
4.4.4. Осмотр и ремонт колесных пар проводить в соответствии с требованиями Руководящего документа по ремонту и техническому обслуживанию колесных пар с буксовыми узлами грузовых вагонов магистральных железных дорог колеи 1520 (1524) мм РД ВНИИЖТ 27.05.01-2017.
4.5. Нижняя рама
4.5.1. Нижнюю раму вагона, показанную на рисунке 4.1, очистить от грязи, отслоившейся краски, ржавчины, проверить состояние всех элементов. Ослабленные заклепки заменить. Сварные швы, имеющие трещины, разделать и заварить вновь в соответствии с требованиями Инструкции по сварке и наплавке при ремонте грузовых вагонов РД ВНИИЖТ-059/01-2019 и Руководства по капитальному ремонту грузовых вагонов РД 32 ЦВ 168-2017.
4.5.2. Нижняя рама вагона не должна иметь трещин и изломов.
Допускается не ремонтировать хребтовую балку с прогибами в горизонтальной и вертикальной плоскостях не более 25 мм.
Допускается оставлять без исправления прогибы по всей длине шкворневых, цилиндровых и торцевых балок нижней рамы в горизонтальной и вертикальной плоскостях не более 10 мм, при этом прогибы их консольных частей не должны превышать 5 мм. Прогиб кронштейна тормозного цилиндра допускается не более 5 мм.
Балки нижней рамы, имеющие прогибы более допустимых критериев изложенных в разделе 3 Требований по исключению из инвентаря грузовых вагонов, согласованных протоколом заседания Комиссии Совета по железнодорожному транспорту полномочных специалистов вагонного хозяйства железнодорожных администраций от 16 - 17 декабря 2008 г., восстановлению не подлежат.
4.5.3. Трещины и повреждения коррозией хребтовой, шкворневых, цилиндровых и концевых балок ремонтировать в соответствии с требованиями Инструкции по сварке и наплавке при ремонте грузовых вагонов РД ВНИИЖТ-059/01-2019.
4.5.4. Ударные розетки, упорные угольники автосцепного устройства, имеющие трещины и износ поверхностей, отремонтировать сваркой и наплавкой в соответствии с Инструкцией по сварке и наплавке при ремонте грузовых вагонов РД ВНИИЖТ-059/01-2019.
4.5.5. Предохранительные планки хребтовых балок между упорными угольниками поглощающего аппарата с износом не более 3 мм допускается восстанавливать наплавкой с последующей механической обработкой до чертежных размеров. Планки с износом более 3 мм заменить на новые.
4.5.6. Трещины и изломы упоров кузова нижней рамы ремонтировать сваркой с последующей установкой усиливающих накладок в соответствии с требованиями Инструкции по сварке и наплавке при ремонте грузовых вагонов РД ВНИИЖТ-059/01-2019.
4.5.7. Проверить состояние шкворневых и цилиндровых опор кузова и их крепления на раме.
При наличии трещин или излома уха опор кузова допускается ремонтировать не более двух несмежных шкворневых и цилиндровых опор путем приварки с двух сторон усиливающих типовых накладок толщиной 20 мм.
4.5.8. Отверстия в кронштейнах для валиков упорных тяг открывания бортов, разработанные по диаметру, ремонтировать наплавкой или установкой стальных втулок, с обваркой по периметру сплошным швом и последующей механической обработкой.
4.5.9. Пятники демонтировать с думпкара, проверить на отсутствие трещин. Пятники, имеющие трещины, ремонтировать по технологии, изложенной в технологических инструкциях ТИ-ТНП-2010 или ТИ-ТНП/Ш-2011, в зависимости от материала пятника.
Износ рабочих поверхностей пятника ремонтировать наплавкой с последующей механической обработкой до чертежных размеров, при условии, что глубина износа не превышает 7 мм.
Для повышения износостойкости наплавленного слоя рекомендуется использовать наплавочную проволоку марки СВ-10ХГ2 СМФ ТУ 0805-001-18486807-99 в среде углекислого газа.
1 - хребтовая балка; 2 - шкворневая балка; 3 - цилиндровая балка; 4 - торцевая балка; 5 - упор верхней рамы; 6 - шкворневая опора; 7 - цилиндровая опора; 8 - цилиндровый подшипник; 9 - цилиндровая скоба; 10 - кронштейн цилиндра; 11 - пятник; 12 - скользун; 13 - кронштейн упорной тяги механизма открывания бортов; 14 - кронштейн тормозного цилиндра
Рис. 4.1 - Нижняя рама
4.6. Верхняя рама
4.6.1. Верхнюю раму, показанную на рисунке 4.2, очистить от грязи, отслоившейся краски, ржавчины, проверить состояние металлических балок, кронштейнов, упоров, нижнего и верхнего металлических листов пола. Сварные швы, имеющие трещины, разделать и заварить в соответствии с требованиями Инструкции по сварке и наплавке при ремонте грузовых вагонов РД ВНИИЖТ-059/01-2019.
4.6.2. Трещины и изломы боковых, шкворневых, цилиндровых, упорных, продольных, поперечных балок и кронштейнов ремонтировать сваркой с последующей постановкой усиливающих накладок в соответствии с требованиями Инструкции по сварке и наплавке при ремонте грузовых вагонов РД ВНИИЖТ-059/01-2019.
4.6.3. Прогибы боковых и продольных балок верхней рамы в горизонтальной и вертикальной плоскости допускаются не более 25 мм. Прогибы по всей длине шкворневых, цилиндровых и поперечных балок в вертикальной и горизонтальной плоскостях должны быть не более 10 мм, при этом прогибы их консольных частей не должны превышать 5 мм.
Балки верхней рамы, имеющие прогибы более допустимых критериев изложенных в разделе 3 Требований по исключению из инвентаря грузовых вагонов, согласованных протоколом заседания Комиссии Совета по железнодорожному транспорту полномочных специалистов вагонного хозяйства железнодорожных администраций от 16 - 17 декабря 2008 г., восстановлению не подлежат.
4.6.4. Шкворневые и цилиндровые опорные оси (трубы) и оси подъёма кузова не должны иметь продольных и поперечных трещин и износов рабочей поверхности.
Оси с износом рабочих поверхностей по диаметру ремонтировать наплавкой с последующей механической обработкой или заменять новыми.
4.6.5. Отверстия петель для осей подъёма кузова и петель осей крепления продольных бортов, имеющие износ по диаметру ремонтировать наплавкой или установкой и обваркой втулок с последующей механической обработкой.
1 - балка боковая; 2 - балка шкворневая; 3 - балка цилиндровая; 4 - балка поперечная; 5 - балка поперечная; 6 - ось опорная шкворневая; 7 - ось опорная цилиндровая; 8 - петля бортов; 9 - деревянный настил; 10 - лист верхний; 11 - лист нижний; 12 - балка продольная; 13 - кронштейн; 14 - ось подъема кузова; 15 - козырек; 16 - балка упорная
Рис 4.2 - Рама верхняя
4.6.6. Верхний металлический лист верхней рамы демонтировать.
Доски и бруски деревянного настила перебрать, не отвечающие требованиям п. 4.1.9, 4.1.10, заменить.
4.6.7. Вмятины глубиной более 20 мм и разрывы верхнего и нижнего металлических листов пола выправить или ремонтировать установкой накладок с обваркой их сплошным швом по периметру.
Трещины зачистить, заварить и усилить накладками с обваркой сплошным швом по периметру. Накладки должны перекрывать поврежденное место не менее чем на 50 мм.
Края пробоин выправить. Лучевые трещины, идущие от пробоин, вырезать. Образовавшиеся отверстия закрыть с наружной стороны накладками, перекрывающими их не менее чем на 50 мм. Накладки приварить с наружной стороны сплошным, с внутренней стороны прерывистым швом.
4.7. Продольные борта
4.7.1. Трещины и изломы верхнего козырька, нижней обвязки, стоек и листов обшивки продольных бортов, приведенных на рисунке 4.3, ремонтировать сваркой с постановкой усиливающих накладок.
Допускается оставлять без исправления горизонтальные и вертикальные прогибы продольных бортов не более 50 мм.
4.7.2. Отверстия петель для крепления бортов на верхней раме и концевых петель механизма открывания бортов, имеющие износ более 3 мм, ремонтировать наплавкой или установкой втулок с последующей их обваркой и механической обработкой.
4.7.3. Отклонение от перпендикулярности концевых петель относительно листа обшивки борта допускается не более 3 мм.
4.7.4. Продольный борт в закрытом положении должен вплотную прилегать к полу и торцевым стенкам. Допускается зазор между полом кузова и бортом не более 20 мм, а бортом и торцовой стенкой у основания борта не более 10 мм. Для обеспечения зазора между торцовой стенкой и закрытым бортом допускается приварка к кромкам листа торцевой стенки на всю высоту борта планок шириной 30 - 40 мм и толщиной 8 - 10 мм; планки ставят с наружной стороны кузова и приваривают с двух сторон, катет шва 6 мм.
1 - козырек; 2 - гнутый профиль; 3 - внутренний лист; 4 - петля; 5 - концевая петля; 6 - нижняя обвязка; 7 - стойка
Рис. 4.3 - Борт продольный
4.8. Торцевые стенки
4.8.1. Листы торцевых стенок кузова, показанных на рисунке 4.4, имеющие прогиб до 50 мм, допускается не править. Поврежденные листы, козырек и стойки ремонтировать сваркой с постановкой усиливающих накладок.
4.8.2. Отверстия внутренних и наружных кронштейнов механизма открывания бортов, имеющие износ более 3 мм, ремонтировать наплавкой или запрессовкой втулок.
4.9. Механизм открывания бортов
4.9.1. Механизм открывания бортов, показанный на рисунке 4.5, разобрать. Погнутые рычаги и тяги выправить или заменить новыми, имеющие изломы, трещины и надрывы заменить. Валики шарниров с трещинами и изгибами заменить.
4.9.2. Износ валиков свыше 3 мм при суммарном зазоре между валиком и отверстием свыше 5 мм не допускается. Валики подлежат замене, а отверстия наплавке и механической обработке или запрессовке стальных втулок. Резьбу регулировочных тяг проверить и смазать универсальной смазкой УС-2 ГОСТ 1033. Пазы головок тяг, имеющие износ свыше 3 мм, наплавляют и обрабатывают.
Резьбу регулировочных тяг проверяют и смазывают графитной смазкой ГОСТ 3333.
4.9.3. Отремонтированные регулировочные тяги с головками испытать на растяжение под нагрузкой 196 кН (20 тс) в течение времени необходимого для осмотра. При этом осуществлять остукивание деталей легкими ударами молотка по ГОСТ 2310-77. При испытаниях длина навинчивания головки на тягу должна быть не более 55 мм (не далее контрольного отверстия 5 мм на головке). Испытания проводить на стенде, отвечающем требованиям N 736-2010 ПКБ ЦВ.
4.9.4. Кронштейны торцевых стенок для механизма открывания бортов осмотреть, проверить на прочность крепления к раме. Между опорной поверхностью упорного кронштейна и нижней кромкой горизонтального рычага при закрытом борте должен быть зазор от 2 до 5 мм.
1 - крайняя стойка; 2 - съемный лист; 3 - козырек; 4 - внутренний лист;
5 - внутренний кронштейн; 6 - средняя стойка; 7 - поручень-ступенька;
8 - наружный кронштейн
Рис. 4.4 - Стенка торцевая
1 - тяга упорная; 2 - рычаг; 3 - тяга регулировочная; 4, 5, 6, 7, 8 - валики
Рис. 4.5 - Механизм открывания бортов
4.10. Цилиндры подъёма
4.10.1 Показанные на рисунке 4.6 цилиндры подъёма, демонтировать с вагона, разобрать и промыть.
4.10.2. На корпусе цилиндра подъема не допускаются:
риски и задиры на рабочей поверхности (зеркала) рубашек и корпусов цилиндров;
овальность и износ по внутреннему диаметру более 3 мм;
коррозия, неравномерный износ рабочей поверхности;
механические повреждения элементов (трещины, отколы, вмятины и т.д.);
осевшие или лопнувшие пружины штоков;
отклонение рабочей поверхности от цилиндричности более 3 мм;
износы опорных приливов более 5 мм по диаметру.
4.10.3. Допускается производить восстановление корпусов, крышек и днищ цилиндров правкой, сваркой, наплавкой с последующей механической обработкой.
4.10.4. Отклонение от цилиндричности рабочих поверхностей и износ поверхностей наружного диаметра поршня более 3 мм ремонтировать наплавкой с последующей механической обработкой.
4.10.5. Овальные отверстия в штоке поршня, имеющие износ более 3 мм, ремонтировать наплавкой с последующей механической обработкой.
4.10.6. Поршень цилиндра со штоком и пружиной разобрать, осевшие более чем на 10 мм или лопнувшие пружины заменить. Изношенные направляющие ребра и поверхности штоков поршня, упирающиеся в рога опрокидывания и запоры, а также направляющие трубы поршня восстановить наплавкой с последующей механической обработкой до размеров, указанных в рабочих чертежах.
4.10.7. Заусеницы на штоке поршня зачистить шлифовальной шкуркой 2С П1 15А М40 ГОСТ 6456.
4.10.8. Зазор между штоком поршня и горловиной крышки цилиндра не должен превышать 6 мм. При большем зазоре отверстие горловины наплавить и обработать до чертежных размеров.
4.10.9. Резиновые манжеты поршня, имеющие трещины и разрывы, заменить. Новые и исправные резиновые манжеты перед постановкой на поршни смазать смазкой ЖТ-79Л ТУ 0254-002-01055954-01 или ПЛАСТМА-75 ТУ 0254-006.1742726-05.
4.10.10. Уплотнительные прокладки потерявшие упругость или имеющие вырывы, разрывы и трещины заменить новыми. Перед постановкой прокладки покрыть смазкой ЖТ-79Л или ПЛАСТМА-75 или универсальной смазкой УС-2 ГОСТ 1033.
1 - корпус; 2 - крышка; 3 - днище; 4 - поршень; 5 - шток; 6 - манжета;
7 - цапфа; 8, 9, 10 - прокладка
Рис. 4.6 - Цилиндр подъема
4.10.11. Отремонтированные цилиндры разгрузки одинарного или двойного действия, перед постановкой на вагон должны подвергаться гидравлическим испытаниям на прочность давлением не менее 0,9 МПа (9 кгс/см2) в следующем порядке:
установить цилиндр на стенд, обеспечивающий выход штока не более 930 мм, подключить к жидкостной линии и плавно поднять давление до 0,9 МПа (9 кгс/см2), выдерживая его не менее 3 мин;
снизить давление до рабочего 0,6 МПа (6 кгс/см2) и осмотреть цилиндр, обстукивая сварные швы деревянным молотком массой до 1 кг. Увеличение давления и снижение его до рабочего производить постепенно;
давление, равное рабочему, поддерживать в течение времени, необходимого для осмотра цилиндра.
Цилиндр считается выдержавшим испытание, если:
в элементах цилиндра не оказалось признаков разрыва;
отсутствует утечка в разъёмных соединениях.
4.10.12. После испытания на цилиндр разгрузки нанести трафарет о проведённых гидравлических испытаниях с последующей записью в журнале произвольной формы, согласованном с местным органом Госгортехнадзора.
4.11. Пневмосистема разгрузки
4.11.1. Пневматическое устройство механизма опрокидывания демонтировать с вагона, разобрать при необходимости гидравлического испытания давлением 0,9 МПа (9 кгс/см2) в течение 5 минут. При испытании не допускается просачивание воды через стенки резервуара и швы. Запрещается заварка пороков в сварных швах. Заварка трещин по основному металлу резервуаров и приварка накладок запрещаются.
4.11.2. Трубопроводы магистрали системы разгрузки, показанные на рисунке 4.7, разобрать и осмотреть. Трубы, имеющиеся трещины, разрывы и срывы резьбы заменить. Допускается приварка новых частей стальных труб взамен поврежденных при условии, что расстояние между сварными стыками труб не менее 0,5 м.
Новые части трубопроводов изготавливать из стальных усиленных оцинкованных труб по ГОСТ 3262-75.
Радиусы гиба труб должны быть не менее:
70 мм для труб диаметром 3/4";
120 мм для труб диаметром 1";
500 мм для труб диаметром 11/4".
4.11.3. Соединительные рукава, имеющие трещины, надрывы, расслоение, потертости и прорыв слоя матерчатой прокладки, заменить на новые. После ремонта соединительные рукава для проверки на прочность должны подвергаться гидравлическому испытанию под давлением воды в них (1,2 0,02) Мпа (12
0,2) кгс/см2 с выдержкой под давлением от 1,5 до 2 минут.
Соединительный рукав считается выдержавшим испытание если не было обнаружено:
срыва деталей;
просачивания воды во время испытания;
надрывов резинотекстильной трубки.
Для проверки на герметичность соединительные рукава подлежат пневматическому испытанию с выдержкой под давлением воздуха в них (0,6+0,05) Мпа (6+0,5) кгс/см2 при полном их погружении в ванну с водой.
Соединительный рукав считается выдержавшим испытание, если в течение 1 минуты не было обнаружено выделения пузырьков воздуха в любой части соединительного рукава. При обнаружении пузырьков воздуха на поверхности резинотекстильной трубки необходимо соединительный рукав выдержать под давлением в ванне с водой до 10 минут и, если выделение пузырьков на поверхности резинотекстильной прекратится, считать его выдержавшим испытание, в ином случае соединительные рукав считается не выдержавшим испытание.
4.11.4. Снятое с ва<
|
|
Эмиссия газов от очистных сооружений канализации: В последние годы внимание мирового сообщества сосредоточено на экологических проблемах...
Семя – орган полового размножения и расселения растений: наружи у семян имеется плотный покров – кожура...
Автоматическое растормаживание колес: Тормозные устройства колес предназначены для уменьшения длины пробега и улучшения маневрирования ВС при...
Организация стока поверхностных вод: Наибольшее количество влаги на земном шаре испаряется с поверхности морей и океанов (88‰)...
© cyberpedia.su 2017-2024 - Не является автором материалов. Исключительное право сохранено за автором текста.
Если вы не хотите, чтобы данный материал был у нас на сайте, перейдите по ссылке: Нарушение авторских прав. Мы поможем в написании вашей работы!