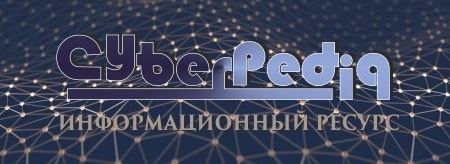
Таксономические единицы (категории) растений: Каждая система классификации состоит из определённых соподчиненных друг другу...
История развития хранилищ для нефти: Первые склады нефти появились в XVII веке. Они представляли собой землянные ямы-амбара глубиной 4…5 м...
Топ:
Организация стока поверхностных вод: Наибольшее количество влаги на земном шаре испаряется с поверхности морей и океанов...
Методика измерений сопротивления растеканию тока анодного заземления: Анодный заземлитель (анод) – проводник, погруженный в электролитическую среду (грунт, раствор электролита) и подключенный к положительному...
Установка замедленного коксования: Чем выше температура и ниже давление, тем место разрыва углеродной цепи всё больше смещается к её концу и значительно возрастает...
Интересное:
Искусственное повышение поверхности территории: Варианты искусственного повышения поверхности территории необходимо выбирать на основе анализа следующих характеристик защищаемой территории...
Берегоукрепление оползневых склонов: На прибрежных склонах основной причиной развития оползневых процессов является подмыв водами рек естественных склонов...
Отражение на счетах бухгалтерского учета процесса приобретения: Процесс заготовления представляет систему экономических событий, включающих приобретение организацией у поставщиков сырья...
Дисциплины:
![]() |
![]() |
5.00
из
|
Заказать работу |
|
|
ВВЕДЕНИЕ
В дипломном проекте рассматривается трубный элеватор ЭТА-П Ишимбайского машиностроительного завода, применяемый при спускоподъемных операциях подземного ремонта скважин.
При существующем уровне механизации и используемых технологиях спускоподъемных операций (СПО) они выполняются при всех видах подземного ремонта скважин с использованием ручного инструмента. К этому инструменту относятся: трубные элеваторы, трубные ключи, спайдеры, штанговые элеваторы и штанговые ключи. Количество операций, ежегодно выполняемых с помощью этих инструментов, измеряются многими десятками миллионов. Поэтому к спускоподъемному инструменту предъявляются высокие требования по надежности, удобству работы и, особенно, по обеспечению безопасности труда рабочего, пользующегося им.
Влияние спускоподъемного инструмента на темп и качество выполнения операций и процессов в целом, на безопасность работ является причиной конструирования, выпуска и эксплуатации большого числа типов и вариантов этого инструмента.
Элеватор ЭТА-П является усовершенствованной моделью трубного элеватора ЭТА-50.
ЛИТЕРАТУРНЫЙ ОБЗОР И ПАТЕНТНАЯ ПРОРАБОТКА ТРУБНЫХ ЭЛЕВАТОРОВ
Контроль качества грузоподъемного инструмента для подземного ремонта скважин
Общие положения
Система организации работ по неразрушающему контролю должна обеспечивать своевременное выявление дефектов деталей и узлов грузоподъемных машин пооперационного и приемочного неразрушающего контроля при их ремонте в соответствии с установленными правилами контроля. В своей деятельности подразделение неразрушающего контроля руководствуется государственными и отраслевыми стандартами, государственными и отраслевыми нормативными документами, разработанными ВНИИПТмаш и ВНИИстройдормаш. Входной, операционный и приемочный неразрушающий контроль всех заготовок, запасных частей, элементов деталей и узлов должен быть введен в обязательном порядке, в соответствии с нормативными документами в технологические процессы и учитываться в затратах на ремонт и в себестоимости ремонта, как средство повышения качества и надежности.
|
Структура и функции Подразделения неразрушающего контроля
Основными задачами Подразделения являются:
обеспечение и выполнение НК элементов деталей и узлов грузоподъемных машин в соответствии с действующими технологическими процессами ремонта и нормативной документацией на контроль;
введение рабочей документации по НК;
разработка технологических карт контроля на основе действующих технологических инструкций, методик, методических указаний на контроль;
регулярное проведение контрольно-профилактического обслуживания эксплуатируемых средств НК, а также организация работ по техническому обслуживанию, ремонту;
систематическое повышение квалификации работников подразделения.
Для подразделения НК должны быть выделены специально оборудованные помещения достаточные для хранения переносной дефектоскопической аппаратуры, комплектования, проверки и подготовки дефектоскопов перед выходом на участки контроля, оформление и хранение документации на контроль.
В обязанности руководителя Подразделения входит:
разработка и представление на утверждение главному инженеру план-графика работы дефектоскопистов на основе заявок цехов, осуществление повседневного контроля за его выполнением;
укомплектование Подразделения дефектоскопистами, измерительными приборами, инструментами;
проверка оборудования постов контроля, организация и проведение инспекционного контроля;
организация технической учебы и подготовки дефектоскопистов к периодической переаттестации;
|
проведение ежемесячного анализа результатов НК и отчет перед главным инженером;
проведение контроля за правильным ведением документации по дефектоскопии.
В обязанности дефектоскописта входит:
проведение контроля в полном объеме в соответствии с НТД, технологическим процессом и установленным графиком;
осмотр, проверка работоспособности дефектоскопа;
оформление необходимой технической документации на контроль.
Условия контроля
Основанием для применения предприятием НК узлов и деталей грузоподъемных машин являются требования НТД на ремонт и техническое обслуживание, в которых определены объемы контроля и перечень недопустимых дефектов НК может быть введен на предприятиях, подразделения НК которых аттестованы и установленном порядке на право проведения контроля. При этом на предприятии должны иметься: НТД на неразрушающий контроль объектов конкретного типа, средства НК, специалисты, обладающие уровнем квалификации.
Организация контроля
Контроль осуществляется на стационарных постах, размещаемых в цехах. Контрольные посты должны быть огорожены, оборудованы индивидуальным освещением, столом, стулом, контрольными образцами с моделями дефектов, технологическими картами. При этом:
не должны проводится работы, загрязняющие воздух и вызывающие вибрацию контролируемого соединения;
должны быть приняты меры к защите экрана дефектоскопа.
Для обеспечения нормальных условий работы дефектоскописта, контроль должен производится при температуре не ниже +10° и не выше +40°.
Общие положения
Техническое диагностирование следует проводить после истечения назначенного (расчетного) срока службы, или после аварии. Назначенный (расчетный) срок службы устанавливает предприятие-изготовитель и указывает его в паспорте диагностируемого оборудования.
Оборудование считается пригодным к дальнейшей эксплуатации, если по результатам технического диагностирования подтверждается, что состояние основного металла удовлетворяют требованиям «Правил устройства и безопасной эксплуатации, (например: грузоподъемного инструмента)», настоящего Руководящего документа и действующей нормативно-технической документации: коррозионный и эрозионный износ, а также изменения геометрических размеров, обеспечивающих нормативные запасы прочности.
|
Техническое диагностирование оборудования, отработавшего назначенный срок службы, включает:
внешний осмотр и контроль геометрических размеров;
измерение выявленных дефектов (коррозионных язв или эрозионных повреждений, трещин, деформаций и т.д.);
измерение твердости с помощью переносных приборов;
лабораторные исследования (при необходимости) химического состава и структуры материала основных элементов;
испытания на прочность;
прогнозирование на основании анализа результатов технического диагностирования и расчетов на прочность возможности, допустимых рабочих параметров, условий и сроков дальнейшей эксплуатации.
После аварии следует проводить досрочное (внеочередное) техническое диагностирование.
Однако техническое диагностирование не заменяет проводящихся в установленном порядке технических освидетельствований оборудования. При положительных результатах технического диагностирования оборудование может быть допущено в дальнейшую эксплуатацию. Допускаемый срок продления эксплуатации устанавливает (с учетом результатов обследования) выполняющая техническое диагностирование организация. Разрешение на дальнейшую эксплуатацию оборудования на основании выводов и рекомендаций заключения по результатам технического диагностирования выдается инспектором местного Госгортехнадзора РФ.
Для элеваторов, отработавших назначенный срок службы и не подвергавшихся техническому диагностированию, его требуется провести в течение одного года с момента издания настоящего Руководящего документа.
Оформление результатов технического диагностирования
На выполнение работы при техническом диагностировании организация, их проводящая, составляет первичную документацию (акты, заключения, протоколы, таблицы, схемы, фотографии), в которой должны быть отражены все обнаруженные отклонения, особенности и дефекты. На основании' первичной документации о результатах технического диагностирования и выполненных расчетов на прочность должно быть составлено заключение или отчет. Первичная документация, включая формулы (схемы) с графическим изображением результатов контроля, прилагается к заключению. Заключение по результатам технического диагностирования должно быть составлено по типовой форме и включать в себя следующий текстовый материал:
|
Введение - краткая постановка задачи.
Основные сведения о диагностируемых элеваторах (конструкция, материалы и технология изготовления, условия эксплуатации):
завод-изготовитель элеватора;
дата изготовления и дата ввода в эксплуатацию;
заводской номер элеватора;
адрес владельца;
регистрационный номер по реестру органа Госгортехнадзора РФ.
краткая характеристика конструкции и технологии изготовления элеватора;
разрешенные (фактические) параметры работы элеватора (если отличаются от проектных);
основные размеры элементов элеватора (диаметр, толщина, высота);
материалы основных элементов элеватора (использованные заводом-изготовителем);
сведения об эксплуатации;
сведения о ремонте.
Результаты анализа технической документации:
краткая информация о сертификатах качества материалов, используемых при изготовлении (если имеется), ремонте элеватора с оценкой соответствий действующей нормативно-технической документацией;
сводные данные по результатам предыдущих обследований и контроля;
причины, послужившие основанием для ремонта и реконструкции;
специфические особенности эксплуатации.
Индивидуальная программа технического диагностирования.
В индивидуальной программе указывают конкретные методы, объемы и зоны контроля. Если диагностирование проводиться по типовой программе данный раздел можно не приводить.
Результаты технического диагностирования (текущего).
В настоящем разделе приводятся обобщенные данные обследования элеватора по различным диагностическим операциям:
типы (марки) испытательного оборудования и дефектоскопической аппаратуры, использованной при данном техническом диагностировании, их заводской номер, основные характеристики искателей, эквивалентная площадь допустимого дефекта;
сведения, подтверждающие квалификацию дефектоскопистов;
сведения нормативно-технической документации, по которой производился дефектоскопический контроль;
сведения о дефектах, обнаруженных при осмотре элеватора;
результаты исследования механических свойств металла;
условия проведения.
По результатам выполненного обследования формулируются выводы и рекомендации с указанием возможности, разрешенных параметров, условий и сроков дальнейшей эксплуатации элеватора или объемов его ремонта.
К заключению прилагается копия лицензии от органов Госгортехнадзора РФ с перечнем разрешенных видов деятельности, выданная организации, проводившей обследование. Если работы по техническому диагностированию и составлению заключения выполнялись двумя разными организациями, к заключению прилагаются две копии лицензий от каждой из этих организаций. Заключение прилагается к паспорту элеватора. Его копия хранится в организации, проводившей техническое диагностирование.
|
Подготовка к контролю
Элеватор подвергается НК в разнообразном виде, к комплекту деталей должен быть приложен паспорт на элеватор. Детали элеватора перед контролем должны быть очищены от грязи, масел, ржавчины, отслаивающейся окалины и краски любыми способами (механическим, промывкой в керосине, в растворе каустической соды с последующим ополаскиванием). В случае, когда краска или окалина имеет хорошее сцепление с металлом и представляет собой плотную (без рыхлостей и пор) пленку или слой на поверхности или окалину. Острые выступы и неровности на поверхности, подвергаемой НК, удаляют с помощью ручной шлифовальной машинки с мелким наждачным камнем, напильником или наждачной бумагой. При зачистке контролируемых поверхностей следить за тем, чтобы размеры ее не вышли за пределы допусков размеров деталей.
Рисунок 4.3 - Образец для настройки чувствительности дефектоскопа нормальным преобразователем
элеватор диагностика дефектоскопия безопасность
Ультразвуковой контроль можно проводить при температуре окружающего воздуха от +5 до +40°С, температура деталей элеватора должна быть такой же, при несоблюдении этих условий снижается чувствительность метода. Для обеспечения акустического контакта между искателем и изделием подготовленную поверхность перед контролем тщательно протирают ветошью, а затем на нее наносят слой контактной смазки. Для получения надежного акустического контакта преобразователь - контролируемое изделие следует применять различные по вязкости масла. Выбор масла по вязкости зависит от чистоты контролируемой поверхности и температуры окружающей среды. Чем грубее поверхность и выше температура, тем более вязкие масла следует применять в качестве контактной жидкости. Наиболее подходящей контактной жидкостью для контроля деталей элеватора являются масла типа МС-20 ГОСТ 21743-76. Увеличение вязкости контактной жидкости снижает чувствительность к выявлению дефектов. Поэтому в каждом случае следует выбирать контактную жидкость с минимальной вязкостью, обеспечивающей надежный акустический контакт преобразователь-контролируемая деталь.
Порядок контроля
После очистки поверхности детали элеватора подвергают визуальному контролю невооруженным глазом и с помощью оптических средств. При этом выявляют крупные трещины, задиры, остаточную деформацию, подрезы, следы наклепа. При обнаружении трещин и следов заварки трещин деталь бракуется.
Контроль размеров деталей производится в соответствии с технической документацией на ремонт элеватора. Измерительный инструмент для контроля размеров и критерии оценки годности деталей элеватора приводятся в картах контроля на ремонт.
Ультразвуковой контроль деталей элеватора осуществляется прямыми и призматическими преобразователями в соответствии с линиями сканирования, показанными на рисунках контролируемых деталей.Рабочую настройку, ультразвукового дефектоскопа проводят по испытательным образцам (рисунки 4.1, 4.2). Для настройки дефектоскопа ультразвуковой преобразователь с углом призмы 40°, 50° и рабочей частотой 1,8МГц или прямой преобразователь с рабочей частотой 2,5 МГц устанавливают на поверхность образца, на которую предварительно нанесена контактная смазка. Настройка скорости развертки должна соответствовать толщине прозвучиваемой детали элеватора или зоне прозвучивания. Чувствительность при контроле призматическим преобразователем настраивают по угловому отражателю (зарубке), выполненному на поверхности образца, противоположной той, на которой находится преобразователь. Чувствительность при контроле прямым преобразователем настраивают по плоскодонному сверлению диаметром 3 мм (см. рисунок 4.2).Добиваются на экране дефектоскопа максимальной амплитуды импульса от контрольного отражателя (дефекта) в виде "зарубки" или плоскодонного сверления, затем ручками "Чувствительность" и "Ослабление" доводят амплитуду импульса до 2/3 высоты экрана дефектоскопа. Мешающие сигналы при этом убрать с помощью ручки "Отсечка шумов".
Зону АСД устанавливают таким образом, чтобы ее начало находилось рядом с зондирующим импульсом, а конец - рядом с импульсом от контрольного отражателя. Зондирующий импульс должен быть вне зоны действия АСД. Настраивают чувствительность АСД так, чтобы он срабатывал при величине эхо-сигнала от контрольного дефекта, равной 2/3 высоты экрана дефектоскопа. Таким образом устанавливают чувствительность оценки при контроле деталей элеватора. Проводят повторный поиск контрольного отражателя на испытательном образце и при надежном его выявлении переходят к контролю деталей элеватора.
Ультразвуковой преобразователь устанавливают на контролируемую поверхность детали элеватора с предварительно нанесенной контактной смазкой и ведут контроль детали по линиям сканирования, показанным на рисунках контролируемых деталей, при этом с помощью переключателя "Ослабление" повышают чувствительность дефектоскопа на 3 - 5 дБ по сравнению с чувствительностью оценки и ведут поиск дефектов, следя за срабатыванием АСД.
При срабатывании АСД дефектоскоп из режима поисковой чувствительности переводят в режим чувствительности оценки (п.п.4.7 - 4.9) и определяют:
) местонахождение дефекта;
) максимальную амплитуду эхо-сигнала;
) условную протяженность дефекта.
При контроле необходимо отличать на экране ЭЛТ дефектоскопа ложные эхо-сигналы, появляющиеся вследствие особенностей конструкции деталей элеваторов. Эти сигналы следует фиксировать на экране ЭЛТ. Все эхо-сигналы, не совпадающие с ложными, следует считать сигналами от дефекта. Оценка характера дефектов производится по косвенным признакам:
интенсивное отражение от трещин наблюдается при направлении прозвучивания, перпендикулярном плоскости дефекта (при этом на экране ЭЛТ виден четкий импульс);
интенсивное отражение от дефекта круглой формы наблюдается при различных направлениях прозвучивания (при этом на экране ЭЛТ импульс более размытый).
Окончательное заключение о наличии дефекта или его отсутствии оператор-дефектоскопист дает после того, как предполагаемый дефект будет прозвучен во всех возможных направлениях и исследован в соответствии с п. 4.12. Через 0,5 ч после начала контроля, а затем через каждые 1,5 - 2 ч работы проверяют настройку дефектоскопа по испытательному образцу, согласно п.п. 4.5-4.9.
Контроль корпуса элеватора
Ультразвуковой дефектоскопией проверяют проушины корпуса, место перехода проушин в корпус на наличие трещин, раковин, внутренних пор. Для контроля применяется прямой преобразователь с рабочей частотой 2,5 МГц. Прозвучивание проводят с обеих торцевых поверхностей корпуса элеватора. Чувствительность дефектоскопа настраивают по испытательному образцу с плоскодонным сверлением. Сканируя корпус элеватора следят за срабатыванием АСД дефектоскопа.
При срабатывании АСД дефектоскоп из режима поисковой чувствительности переводят в режим чувствительности оценки и определяют:
) местонахождение дефекта;
) максимальную амплитуду эхо-сигнала;
) длину пути, пройденного преобразователем при включенном АСД (условную протяженность дефекта).
Контроль серьги
Контролируют серьгу ультразвуковым методом. Проверяются проушины, прямолинейная часть ее и зона закругления. Контроль серьги ведут преобразователем с учетом призмы 40° на частоте 1,8 МГц прямым лучом.
Проушины проверяют поочередным прозвучиванием всех плоских поверхностей. Преобразователь перемещают вокруг отверстия проушины. Направление прозвучивания совпадает с ходом движения преобразователя. Контроль ведется при прямом и обратном ходе. При настройке скорости развертки преобразователь располагают на внутренней плоскости поверхности проушины. Скорость развертки настраивают по прямому двугранному углу, одной из сторон которого является плоскость противоположная плоскости ввода УЗК. Глубина прозвучивания принимается равной толщине проушины. Чувствительность дефектоскопа настраивается по зарубке с эквивалентной площадью 5,1 мм² (3 мм ×1,7 мм).
При контроле прямолинейной части серьги преобразователь зигзагообразно перемещают вокруг ее цилиндрической поверхности. Направление прозвучивания при этом совпадает с ходом движения преобразователя. Контроль проводят при прямом и обратном ходе преобразователя. Величина продольного перемещения преобразователя определяется длинной прямолинейного участка серьги. При настройке скорости развертки преобразователь располагают на цилиндрической поверхности серьги. Скорость развертки настраивают по углу, образованному участком цилиндрической поверхности, противоположном участку ввода УЗК, и закруглением между плоской поверхностью проушины и цилиндрической поверхностью серьги. Глубины прозвучивания принимается равной диаметру серьги по цилиндрической части. Чувствительность настраивается по зарубке с эквивалентной площадью 6 мм² (3 мм × 2 мм). Шаг сканирования должен быть не более 1/2 ширины преобразователя. Настройка дефектоскопа, созданная при контроле цилиндрической части серьги полностью сохраняется и используется при контроле закругления серьги.
При контроле закругления серьги преобразователь перемещают по поверхности вдоль оси серьги. Направление прозвучивания совпадает с ходом движения преобразователя. Контроль ведут при прямом и обратном ходе. В процессе перемещения преобразователь слегка поворачивают на 10 - 15° в обе стороны. Закругление серьги проверяют поочередным прозвучиванием обоих плоских участков закругления.
Сканируя серьгу, следят за срабатыванием АСД дефектоскопа. При срабатывании АСД дефектоскоп из режима поисковой чувствительности переводят в режим чувствительности оценки и определяют:
местонахождение дефекта;
максимальную амплитуду эхо-сигнала;
условную протяженность дефекта.
Контроль челюстей
Челюсти контролируют ультразвуком при помощи преобразователя с углом призмы 40° на частоте 1,8 МГц прямым лучом. Проверка проводится с обеих плоских поверхностей челюсти последовательно. При контроле преобразователь зигзагообразно перемещают по плоской поверхности челюсти. Район отверстия под палец контролируют круговым движением преобразователя. Для надежности контроль ведут сначала при прямом ходе движения, затем при обратном. При контроле челюсти скорость развертки настраивают по нижнему ее углу (нижнему при таком положении челюсти, когда поверхность ввода УЗК верхняя). При этом преобразователь расположен на черновой поверхности челюсти. При контроле челюсти в районе отверстия под палец скорость развертки настраивается также по нижнему ее углу.
Глубина прозвучивания принимается равной толщине проушины челюсти. Чувствительность дефектоскопа в обоих случаях настраивается по зарубке с эквивалентной площадью 3,6 мм² (3 мм × 1,2 мм). Сканируя челюсть следят за срабатыванием АСД дефектоскопа. При срабатывании АСД дефектоскоп из режима поисковой чувствительности переводят на режим чувствительности оценки и определяют:
) местонахождение дефекта;
) максимальную амплитуду эхо-сигнала;
) условную протяженность дефекта.
Оценка результатов контроля
По результатам исследования дефектов определяют пригодность деталей элеватора к дальнейшей эксплуатации. Детали элеваторов отбраковывают в следующих случаях:
если амплитуда эхоимпульса обнаруженного дефекта равна по высоте амплитуде эхоимпульса от искусственного дефекта или превышает ее;
если обнаруженный на поисковой чувствительности дефект является протяженным, то есть если расстояние перемещения преобразователя по контролируемой поверхности между точками, соответствующими моментам исчезновения сигнала от дефекта составляет более 10 мм.
По результатам НК составляется акт (приложение А) в двух экземплярах, один из которых прилагается к паспортам элеваторов. В паспорте записывается номер акта и дата проведения контроля. Второй экземпляр хранится в службе неразрушающего контроля.
Требования и условия проведения испытаний
Испытания элеваторов ЭТА - 50 должны производиться на универсальном стенде испытания элеваторов растягивающей нагрузкой 62,5 тс при давлении 16,4 МПа.
Условия проведения испытаний:
атмосферное давление, Па 0,84 - 1,06х10
относительная влажность воздуха, %, не более 80
температура окружающей среды, °С +15 ÷ + 40
Требования безопасности
К работе на стенде допускаются лица, прошедшее соответствующее обучение, стажировку на рабочем месте, проверку практических навыков, инструктаж и при наличии удостоверения. Рабочая зона должна быть ограждена со всех сторон. Во время проведения испытаний на рабочем месте должны быть предупредительные знаки и надписи.
РАСЧЕТНАЯ ЧАСТЬ
Серьга элеватора
Материал 40ХН. Механические характеристики: σт = 785 МПа, σв = 980 МПа.
Серьга (рисунок 5.3) подвержена действию силы давления штропа Р и двух сил Р/2, приложенных к проушинам серьги. Вследствие наличия деформации серьга соприкасается со штропом по длине дуги, измеряемой углом α, а в проушинах серьги появляются горизонтальные распирающие усилия Q. Для определения усилий Q необходимо произвести сложные математические вычисления. Величина угла α и закон распределения давления по дуге, измеряемой углом α и закон распределения давления по дуге, измеряемой углом α, неизвестны. Их теоретическое определение представляет затруднение. Упрощенно рассчитываем серьгу без учета влияния деформаций от действия сил Q.
Рисунок 5.3 - Серьга элеватора
Проушины серьги, опасное сечение а-а
Растягивающие напряжения
σр = , МПа (5.9)
где с - толщина наружной части проушины, с = 17 мм;- толщина внутренней части проушины, d = 12 мм;- наружный радиус, R = 40 мм- внутренний радиус, r = 17,5 мм
σр
Определяем по формуле Ляме наибольшие растягивающие напряжения σр в точке b от сил внутреннего давления (давление пальца).
σр = , МПа (5.10)
где q - интенсивность сил внутреннего давления.
= , МПа (5.11)=
МПа.
По формуле 5.10 получаем
σр= МПа.
Прямолинейная часть I - I до II - II. В сечении II - II действуют растягивающие напряжения.
σр = , МПа (5.12)
где Д - диаметр прямолинейной части серьги, Д = 40 мм.
σр = МПа.
[σ] = σр/к = 785/1,3 = 604 МПа
[σ]ср = [σ]/2 = 604/2 = 302 МПа.
Таким образом, произведя расчеты элеватора на прочность, видно, что при превышении номинальной грузоподъемности на 25%, напряжения, а особенно в опасных сечениях, не превышают допустимые пределы прочности. Материал стали, использованный при изготовлении элеватора является наиболее оптимальным.
Расчет контура заземления
При расчете контура заземления используется схема, представленная на рисунке 6.1.
Рисунок 6.1- Схема для расчета контура заземления
Рассчитывается сопротивление одного электрода (длина 1=2,5м, диаметр d=0,05м, заложенный в грунт на глубину h=l,9 м до середины электрода) по формуле:
RT=0,366 · ρ/1·(lg 2·l/d+l/2·lg(4·h+l)/(4·h-1)),(6.1)
где ρ- удельное сопротивление почвы, Ом∙м(ρ=70 Ом·м);
- длина электрода, м; - глубина до половины электрода, м;- диаметр электрода, м.
=0,366 · 70/2,5·(lg2·2,25/0,05+l/2·lg(4·l,9+2,5)/(4·l,9-2,5))=22 Ом.
Необходимое число электродов n определяется по формуле:
n=(Rт·ηc)/(R3·ηэт),(6.2)
где Rдоп - допустимое сопротивление заземления, Ом (Rдоп =4 Ом);
ηc - коэффициент сезонности (ηс =2);
ηэт - коэффициент экранирования труб, (0,2< ηэт< 0,9).
Тогда по формуле находится необходимое число электродов:
=(22·2)/(4·0,55)=20.
Сопротивление соединительной полосы по формуле:
=0,366·p/ln· lg(2·ln2/l-hn),(6.3)
где 1n - длина соединительной полосы, м;- ширина соединительной полосы, м.
Длина соединительной полосы определяется по формуле:
п-(n-1)-2 -1.1,05;(6.4)
где n - необходимое число электродов;
п=(20-1) ·2·2,5·1,05=99,75 м.
По формуле (6.3):
=0,366 ·70/ 99,75 ·lg (2-99,752/2,5·0,04)=2,72 Ом.
Находим общее заземление контура по формуле:
RK = 1/ (ηэт / Rt · n + ηэт / Rn),(6.5)
где ηэт - коэффициент экранирования полосы, (ηэт = 0,15).
=l/(0,55/22·20 + 0,15/2,72)=1,8 Ом < 4 Ом, следовательно условие выполняется.
Расчетное сопротивление контура соответствует требованиям ПУЭ, так как RK=1,8 < 4 Oм.
Освещение
Для создания необходимого и достаточного уровня освещенности на рабочих местах необходимо руководствоваться "Отраслевыми нормами проектирования искусственного освещения предприятий нефтяной промышленности" ВСН 34-62, а также соблюдать требования СНиП 23-05-95 "Естественное и искусственное освещение. Нормы проектирования", "Инструкции по проектированию силового и осветительного электрооборудования промышленных предприятий".
Необходимо предусмотреть рабочее и аварийное освещение. Рабочее освещение должно быть предусмотрено во всех помещениях и на неосвещенных территориях для обеспечения нормальной работы. Аварийное освещение для продолжения работ должно быть предусмотрено для рабочих помещений, в случае непланового отключения рабочего освещения. Освещение должно равномерно распределять яркость, быть постоянным во времени, без пульсации.
Значения норм освещенности на рабочих местах должны составлять:
устье скважины 100 лк;
лебедка 50лк;
приемные мостки 10 лк;
автонаматыватель 15 лк;
шкалы КИП 50 лк;
площадки для производства погрузочно-разгрузочных работ 10 лк.
Для общего освещения помещений основного производственного назначения следует применять газоразрядные источники света, для административных и подсобных помещений - лампы накаливания или люминесцентные лампы.
Требования безопасности при эксплуатации элеваторов ЭТА-П
К работе элеватором ЭТА-П (далее элеватором) допускаются лица, достигшие 18-летнего возраста, изучившие и прошедшие проверку знаний в объеме инструкции по монтажу и эксплуатации элеватора ЭТА-П и данной инструкции, прошедшие практическое обучение приемам работы с элеватором.
Работник должен соблюдать правила внутреннего трудового распорядка и установленный режим труда и отдыха.
Выполнение работ с элеватором связано со следующими опасными факторами:
повреждение частей тела при установке элеватора на устье скважины грузоподъемными механизмами;
повреждение частей тела от вращающихся узлов.
Работник должен соблюдать требования пожарной безопасности:
не допускать разлива нефти и нефтепродуктов;
не курить на рабочем месте и не пользоваться открытым огнем;
При обнаружении неисправности элеватора доложить непосредственному руководителю работ или другому ИТР цеха.
Если работник окажется свидетелем несчастного случая, он обязан:
оказать первую доврачебную помощь пострадавшему;
сообщить о несчастном случаи непосредственному руководителю работ или другому ИТР цеха;
принять меры к сохранению обстановки, если это не угрожает аварией или здоровью других людей.
Работник несет полную ответственность за нарушение требований инструкции и вправе отказаться от выполнения работ при несоответствии рабочего места требованиям правил безопасности.
В паспорте на каждый элеватор должно быть приложение, где указываются, дата ввода в эксплуатацию и фамилия ответственного лица. На элеватор должны быть оформлены следующие документы:
Формуляр на элеватор;
Паспорт с указанием:
заводской и инвентарный номер;
тип оборудования и год выпуска.
Требования безопасности перед началом работы
До передачи элеватора в эксплуатацию необходимо проверить взаимодействие его узлов и деталей: свободное перемещение челюстей захватов, серьги, надежность фиксации и свободное перемещение фиксатора. Все случаи отказов, поломок или преждевременный износ деталей должны оформляться актом и заноситься в паспорт и в журнал, а также сообщаться в отдел главного механика. Перед началом смены элеватор проверить по следующим критериям предельного состояния:
износ торцевой опорной поверхности под муфту трубы более 2 мм;
увеличение проходного отверстия под трубу более 3 мм на диаметр;
зазор по диаметру между наружной боковой поверхностью захвата и корпусом элеватора более 2 мм;
трещины и деформации корпуса, серьги, направляющих;
износ по диаметру отверстий проушин под пальцы более 2 мм;
износ по диаметру пальцев более 1,5 мм;
износ радиальной поверхности серьги под крюком (штоком) более 8 мм;
износ по диаметру отверстий серьги под пальцы более 1 мм;
поломка пружин и усадка до 25 мм в свободном состоянии;
износ окошечной части направляющих более 2,5 мм;
износ нижней торцевой части направляющих более 2 мм;
Требования безопасности при работе
Строго запрещается производить спускоподъемные операции, не убедившись в надежной фиксации захвата в элеваторе.
Запрещается:
использовать элеватор на грузоподъемность, превышающую паспортную величину;
работать с неисправным фиксатором;
работать с элеватором, не устанавливая фиксатор за стойку;
производить какие-либо работы по устранению неисправностей в полевых условиях.
Требования безопасности в аварийных ситуациях
Вывод из эксплуатации элеватора (для ремонта, списания и т.д.) проводится при несоответствии его фактических технических характеристик паспортным данным, данным карт обследования и требованиям техники безопасности. Нормативный срок службы элеваторов - 1,5 года.
После ремонта провести стендовые испытания на прочность под нагрузкой, превышающей на 25 % его номинальную грузоподъемность. Продолжительность испытания 10 мин. Испытание в обязательном порядке проводятся при определении возможности эксплуатации элеваторов сверх нормативного срока службы. После снятия нагрузки проверяются:
отсутствие трещин и надрывов при помощи лупы 10-ти кратного увеличения.
отсутствие остаточных деформаций в корпусе элеватора- при помощи универсального измерительного инструмента;
свободное перемещение и поворот относительно осей створки, защелки, рукоятки и предохранителей штропов - опробованием.
Дефектоскопии подвергаются детали: корпус, серьга, захват - не реже одного раза в год.
Требования безопасности по окончании работ
После окончания работ элеватор должен очищаться и смазываться (смазке подлежат все шарнирные соединения и челюсти захвата). Элеватор на сохранность укладывать в инструментальной будке.
Записать в паспорте и формуляре:
время наработки;
выявленные недостатки.
Таким образом, в заключение раздела можно сделать вывод, что безопасность и экологичность данного дипломного проекта находится на высоком уровне. В результате мероприятий по обеспечению пожаробезопасности, электробезопасности, защиты от токсических выбросов, безопасность эксплуатации машин и механизмов и другие мероприятия снижается количество производственных травм и дней нетрудоспособности в НГДУ «Арланнефть».
Благодаря правильной организации работы по обеспечению безопасности и экологичности производственных процессов, а также обучение работников безопасным методам работы предупреждаются производственный травматизм, дорожно-транспортные происшествия, аварии, пожары и другие происшествия на предприятии.
По статистике надежность защиты работников и инженерно-технического комплекса НГДУ «Арланнефть» в ЧС находится на высоком уровне.
|
|
Общие условия выбора системы дренажа: Система дренажа выбирается в зависимости от характера защищаемого...
Поперечные профили набережных и береговой полосы: На городских территориях берегоукрепление проектируют с учетом технических и экономических требований, но особое значение придают эстетическим...
Особенности сооружения опор в сложных условиях: Сооружение ВЛ в районах с суровыми климатическими и тяжелыми геологическими условиями...
Эмиссия газов от очистных сооружений канализации: В последние годы внимание мирового сообщества сосредоточено на экологических проблемах...
© cyberpedia.su 2017-2024 - Не является автором материалов. Исключительное право сохранено за автором текста.
Если вы не хотите, чтобы данный материал был у нас на сайте, перейдите по ссылке: Нарушение авторских прав. Мы поможем в написании вашей работы!