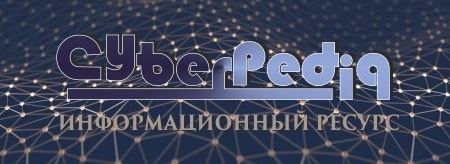
Автоматическое растормаживание колес: Тормозные устройства колес предназначены для уменьшения длины пробега и улучшения маневрирования ВС при...
Таксономические единицы (категории) растений: Каждая система классификации состоит из определённых соподчиненных друг другу...
Топ:
Проблема типологии научных революций: Глобальные научные революции и типы научной рациональности...
Оценка эффективности инструментов коммуникационной политики: Внешние коммуникации - обмен информацией между организацией и её внешней средой...
Выпускная квалификационная работа: Основная часть ВКР, как правило, состоит из двух-трех глав, каждая из которых, в свою очередь...
Интересное:
Отражение на счетах бухгалтерского учета процесса приобретения: Процесс заготовления представляет систему экономических событий, включающих приобретение организацией у поставщиков сырья...
Мероприятия для защиты от морозного пучения грунтов: Инженерная защита от морозного (криогенного) пучения грунтов необходима для легких малоэтажных зданий и других сооружений...
Лечение прогрессирующих форм рака: Одним из наиболее важных достижений экспериментальной химиотерапии опухолей, начатой в 60-х и реализованной в 70-х годах, является...
Дисциплины:
![]() |
![]() |
5.00
из
|
Заказать работу |
|
|
Токарная обработка
Токарный станок - станок для обработки преимущественно тел вращения путем снятия с них стружки при точении. Токарный станок один из древнейших станков в мире, на основе которого создавались другие станки (сверлильный, расточной и др.)
Токарь - одна из ведущих профессий в машиностроении и металлообработке, так как многие детали машин и механизмов изготовляются на токарных станках, являющихся наиболее распространенными в производстве среди станков других групп.
Токарная обработка является наиболее распространенным методом обработки резанием применяется при изготовлении деталей типа тел вращения (валов, дисков, осей, пальцев, цапф, фланцев, колец, втулок, гаек, муфт и др.). Основные виды токарных работ показаны на рисунке 1.
Рис. 1. Основные виды токарных работ:
a) - обработка наружных цилиндрических поверхностей, б) - обработка наружных конических поверхностей, в) - обработка торцов и уступов, г) - вытачивание пазов и канавок, отрезка заготовки, д) - обработка внутренних цилиндрических и конических поверхностей, е) - сверление, зенкерование и развертывание отверстий, ж) - нарезание наружной резьбы, з) - нарезание внутренней резьбы, и) - обработка фасонных поверхностей, к) - накатывание рифлений.
Стрелками показаны направления перемещения инструмента и вращения заготовки.
В машиностроении большинство деталей получают окончательные формы и размеры в результате механической обработки заготовки резанием, которое осуществляется путем последовательного удаления режущим инструментом (например, резцом) тонких слоев материала (в виде стружки) с поверхностей заготовки.
Основным элементом режущего инструмента, отделяющего стружку от заготовки, является заостренный клин. Схема работы клина (а) и резца (б) приведена на рисунке 2.
|
Рис. 2. Схема работы клина и резца
1 - стружка, 2 - резец, 3 - заготовка, 4 - снимаемый слой материала; Р - сила, действующая на резец и клин при работе, b - угол заострения
Процесс резания на токарных станках осуществляется при вращательном главном движении, сообщаемом обрабатываемой заготовке, и при прямолинейном (поступательном) движении подачи, сообщаемом резцу. Элементами режима резания при точении заготовки являются скорость резания, подача и глубина резания. Скоростью резания называется длина пути, пройденного режущей кромкой инструмента относительно обрабатываемой поверхности заготовки в единицу времени. Скорость резания измеряется в м/мин и обозначается буквой v.
Подачей называется величина перемещения режущей кромки инструмента за один оборот заготовки (в направлении подачи) или в единицу времени. Подача измеряется в мм/об или в мм/мин, обозначается буквой s и может быть продольной (если инструмент перемещается параллельно оси вращения заготовки) и поперечной (если инструмент перемещается перпендикулярно этой оси). Глубиной резания называется величина срезаемого за один проход резца слоя металла, измеренная по перпендикуляру к обработанной поверхности детали. Глубина резания измеряется в миллиметрах и обозначается буквой t.
У заготовки различают следующие поверхности: обрабатываемую (с которой снимают стружку), обработанную (полученную после снятия стружки) и резания (которая является переходной между обрабатываемой и обработанной поверхностями и образуется режущим инструментом).
Основные поверхности заготовки и основные движения, осуществляющие процесс резания, показаны на рисунке 3.
Рис. 3. Основные поверхности и движения
|
1 - обрабатываемая поверхность, 2 - поверхность резания, 3 - обработанная поверхность, 4 - ось вращения заготовки, 5 - продольная подача, 6 - поперечная подача, 7 - резец, 8 - заготовка, 9 - главное (вращательное) движение, t - глубина резания
Токарно-винторезный станок
Устройство и классификация.
Рис. 4. Сборочные единицы (узлы) и механизмы токарно-винторезного станка:
1 - передняя бабка, 2 - суппорт, 3 - задняя бабка, 4 - станина, 5 и 9 - тумбы, 6 - фартук, 7 - ходовой винт, 8 - ходовой валик, 10 - коробка подач, 11 - гитары сменных шестерен, 12 - электро-пусковая аппаратура, 13 - коробка скоростей, 14 - шпиндель
Токарно-винторезные станки предназначены для обработки, включая нарезание резьбы, единичных деталей и малых групп деталей. Однако бывают станки без ходового винта. На таких станках можно выполнять все виды токарных работ, кроме нарезания резьбы резцом.
Техническими параметрами, по которым классифицируют токарно-винторезные станки, являются наибольший диаметр D обрабатываемой заготовки (детали) или высота Центров над станиной (равная 0,5 D), наибольшая длина L обрабатываемой заготовки (детали) и масса станка.
Ряд наибольших диаметров обработки для токарно-винторезных станков имеет вид: D = 100, 125, 160, 200, 250, 320, 400, 500, 630, 800, 1000, 1250, 1600, 2000 и далее до 4000 мм. Наибольшая длина L обрабатываемой детали определяется расстоянием между центрами станка. Выпускаемые станки при одном и том же значении D могут иметь различные значения L. По массе токарные станки делятся на легкие - до 500 кг (D = 100 - 200 мм), средние - до 4 т (D = 250 - 500 мм), крупные - до 15 т (D = 630 - 1250 мм) и тяжелые - до 400 т (D = 1600 - 4000 мм).
Легкие токарные станки применяются в инструментальном производстве, приборостроении, часовой промышленности, в экспериментальных и опытных цехах предприятий. Эти станки выпускаются как с механической подачей, так и без нее.
На средних станках производится 70 - 80% общего объема токарных работ. Эти станки предназначены для чистовой и получистовой обработки, а также для нарезания резьб разных типов и характеризуются высокой жесткостью, достаточной мощностью и широким диапазоном частот вращения шпинделя и подач инструмента, что позволяет обрабатывать детали на экономичных режимах с применением современных прогрессивных инструментов из твердых сплавов и сверхтвердых материалов. Средние станки оснащаются различными приспособлениями, расширяющими их технологические возможности, облегчающими труд рабочего и позволяющими повысить качество обработки, и имеют достаточно высокий уровень автоматизации.
|
Крупные и тяжелые токарные станки применяются в основном в тяжелом и энергетическом машиностроении, а также в других отраслях для обработки валков прокатных станов, железнодорожных колесных пар, роторов турбин и др.
Все сборочные единицы (узлы) и механизмы токарно-винторезных станков имеют одинаковое название, назначение и расположение (см. рис 4.).
Типичный токарно-винторезный станок 16К20 завода "Красный пролетарий" показан на рисунке 5.
Рис. 5. Общий вид и размещение органов управления токарно-винторезного станка мод. 16К20:
Рукоятки управления: 2 - сблокированная управление, 3,5,6 - установки подачи или шага нарезаемой резьбы, 7, 12 - управления частотой вращения шпинделя, 10 - установки нормального и увеличенного шага резьбы и для нарезания многозаходных резьб, 11 - изменения направления нарезания резьбы (лево- или правозаходной), 17 - перемещения верхних салазок, 18 - фиксации пиноли, 20 - фиксации задней бабки, 21 - штурвал перемещения пиноли, 23 - включения ускоренных перемещений суппорта, 24 - включения и выключения гайки ходового винта, 25 - управления изменением направления вращения шпинделя и его остановкой, 26 - включения и выключения подачи, 28 - поперечного перемещения салазок, 29 - включения продольной автоматической подачи, 27 - кнопка включения и выключения главного электродвигателя, 31 - продольного перемещения салазок; Узлы станка: 1 - станина, 4 - коробка подач, 8 - кожух ременной передачи главного привода, 9 - передняя бабка с главным приводом, 13 - электрошкаф, 14 - экран, 15 - защитный щиток, 16 - верхние салазки, 19 - задняя бабка, 22 - суппорт продольного перемещения, 30 - фартук, 32 - ходовой винт, 33 - направляющие станины
Таблица 1
Основные размеры метрической резьбы с крупным шагами
Диаметр, мм | Шаг P |
Высота профиля H1 | Диаметр, мм | Шаг P |
Высота профиля H1 | ||||
Наружный d | Средний d2, D2 | Внутренний d1 | Наружный d | Средний d2, D2 | Внутренний d1 | ||||
1,0 1,1 1,2 1,4 1,6 1,8 2,0 2,2 2,5 3,0 3,5 4,0 4,5 5 6 7 8 9 10 11 | 0,838 0,938 1,038 1,205 1,373 1,573 1,740 1,908 2,208 2,675 3,110 3,546 4,013 4,480 5,350 6,350 7,188 8,188 9,026 10,026 | 0,730 0,830 0,930 1,075 1,221 1,421 1,567 1,713 2,013 2,459 2,850 3,242 3,688 4,134 4,918 5,918 6,647 7,647 8,376 9,376 | 0,25 0,25 0,25 0,30 0,35 0,35 0,40 0,45 0,45 0,50 0,60 0,70 0,75 0,80 1,00 1,00 1,25 1,25 1,50 1,50 | 0,135 0,135 0,135 0,162 0,189 0,189 0,216 0,243 0,243 0,270 0,325 0,379 0,406 0,433 0,541 0,541 0,676 0,676 0,812 0,812 | 12 14 16 18 20 22 24 27 30 33 36 39 42 45 48 52 56 60 64 68 | 10,863 12,701 14,701 16,376 18,376 20,376 22,051 25,051 27,727 30,727 33,402 36,402 39,077 42,077 44,752 48,752 52,428 56,428 60,103 64,103 | 10,106 11,835 13,835 15,294 17,294 19,294 20,752 23,752 26,211 29,211 31,670 34,670 37,129 40,129 42,587 46,587 50,046 54,046 57,505 61,505 | 1,75 2,00 2,00 2,50 2,50 2,50 3,00 3,00 3,50 3,50 4,00 4,00 4,50 4,50 5,00 5,00 5,50 5,50 6,00 6,00 | 0,947 1,082 1,082 1,353 1,353 1,353 1,624 1,624 1,894 1,894 2,165 2,165 2,435 2,435 2,706 2,706 2,977 2,977 3,247 3,247 |
|
Таблица 2
Поля допусков резьб
Примечание:
Значения степени точности, помещенные в прямоугольниках являются предпочтительными.
Методы нарезания резьб
На токарно-винторезных станках применяются методы нарезания треугольных резьб, различающихся по видам режущего инструмента, по закреплению на станке и способам осуществления продольной подачи.
Имеются три способа продольной подачи: принудительная, сообщающая режущему инструменту точное перемещение на шаг резьбы один оборот шпинделя; самозатягивающая (самонавинчивающая), сообщаемая режущему инструменту самим инструментом, в результате винтового врезания в металл заготовки; комбинированная, т.е. принудительная с некоторым допустимым отклонением её величины за один оборот заготовки от шага нарезаемой резьбы и самозатягивающая, допускающая небольшие продольные перемещения инструмента (выпускаемые опережением или запаздыванием принудительной подачи). Методы нарезания резьбы по видам инструмента приведены в табл. 3
Таблица 3
Нарезание резьбы
Эскиз | Метод нарезания резьбы | |
Плашками и метчиками | ||
![]() | Неточные, преимущественно крепёжные резьбы с шагом до 4 мм нарезают при помощи плашек (а) и метчиков (б). Эти же резьбонарезные инструменты применяют и для калибрования резьбы диаметром до 76 мм. Нарезание ведётся способом самозатягивающей или комбинированной подачи. Средняя точность нарезания резьбы плашками и метчиками 8 g и 7 H | |
Резьбовыми резцами | ||
![]() | Нарезание резьбы резцами – это универсальный способ, характерный для токарно-винторезного станка. Резцами нарезаются наружные (a) и внутренние (б) резьбы с мелким и крупным шагами, на упор и в глухих отверстиях. Точность нарезания винтов до 6 g степени, гаек – до 6 H степени. Продольная подача принудительная | |
Специальными резьбовыми гребенками
| ||
![]() | Отличается от нарезания резьбы резцом повышенной в два-три раза роизводительностью и возможностью применения только при обработке заготовок, допускающих полный выход гребёнки из резьбы. Средняя точность при нарезании гребёнками наружной резьбы 6 g, а внутренней- 7 H. |
Эскиз | Метод нарезания резьбы |
Резьбонарезными головками | |
![]() | Резьбы крепёжные и неточные с шагом резьбы до 4мм высокопроизводительно нарезаются невращаюшимися винторезными и гайконарезными головками 1. В специальной державке 2 головка устанавливается на резцедержатели станка. Налаживается упор 4, выключающий подачу суппорта 3. Диапазон значений диаметров внутренних резьб, нарезаемых гайко-нарезными головками, от 36 до 95 мм. Производительность нарезания резьбы резьбонарезными головками в 1,5-2 раза превосходит достигаемую при нарезании плашками и метчиками. Продольная подача самозатягивающая и комбинированная |
Резьбонакатными головками | |
![]() | Резьбы наружные с шагом резьбы Р=3 мм накатываются на токарно-винторезных станках одно-, двух-, и трех роликовыми специальными резьбонакатными головками 2. Резьба образуется в результате пластической деформации металла без снятия стружки. Заготовке 1 сообщается вращение, резьбонакатной головке – принудительная продольная подача. Производительность накатывания несколько превосходит достижимую при нарезании резьбы резьбонарезными головками. |
Таблица 4
Назначение
Диаметр
d, мм или дюймы
Шаг резьбы (мм) или число ниток на 1”
Длина, мм
Рабочей части l
Машинные метчики
(по ГОСТ 3226 – 71)
1 – 52
0,25 – 5,0
7 – 60
1 – 52
0,2 – 4,0
5 – 60
1/4 - 2”
20 – 4,5
20 – 60
1/8 – 2”
28 - 11
18 - 40
Гаечные метчики
(по ГОСТ 1604 – 71)
Для метрической резьбы с крупным шагом
(ГОСТ 9150 – 59)
3 – 33
90 – 280
(короткие)
120 – 360
(длинные)
То же с мелким шагом
(ГОСТ 9150 – 59)
3 – 52
90 – 280
(короткие)
120 – 360
(длинные)
Для дюймовой резьбы
(ОСТ НКТП – 1260)
1/4 - 1”
120 – 280
(короткие)
200 – 360
(длинные)
Примечание:
У одинарных метчиков для сквозных отверстий l = 6 нитками, а для глухих l = 3 нитками.
Токарная обработка
Токарный станок - станок для обработки преимущественно тел вращения путем снятия с них стружки при точении. Токарный станок один из древнейших станков в мире, на основе которого создавались другие станки (сверлильный, расточной и др.)
Токарь - одна из ведущих профессий в машиностроении и металлообработке, так как многие детали машин и механизмов изготовляются на токарных станках, являющихся наиболее распространенными в производстве среди станков других групп.
Токарная обработка является наиболее распространенным методом обработки резанием применяется при изготовлении деталей типа тел вращения (валов, дисков, осей, пальцев, цапф, фланцев, колец, втулок, гаек, муфт и др.). Основные виды токарных работ показаны на рисунке 1.
Рис. 1. Основные виды токарных работ:
a) - обработка наружных цилиндрических поверхностей, б) - обработка наружных конических поверхностей, в) - обработка торцов и уступов, г) - вытачивание пазов и канавок, отрезка заготовки, д) - обработка внутренних цилиндрических и конических поверхностей, е) - сверление, зенкерование и развертывание отверстий, ж) - нарезание наружной резьбы, з) - нарезание внутренней резьбы, и) - обработка фасонных поверхностей, к) - накатывание рифлений.
Стрелками показаны направления перемещения инструмента и вращения заготовки.
В машиностроении большинство деталей получают окончательные формы и размеры в результате механической обработки заготовки резанием, которое осуществляется путем последовательного удаления режущим инструментом (например, резцом) тонких слоев материала (в виде стружки) с поверхностей заготовки.
Основным элементом режущего инструмента, отделяющего стружку от заготовки, является заостренный клин. Схема работы клина (а) и резца (б) приведена на рисунке 2.
Рис. 2. Схема работы клина и резца
1 - стружка, 2 - резец, 3 - заготовка, 4 - снимаемый слой материала; Р - сила, действующая на резец и клин при работе, b - угол заострения
Процесс резания на токарных станках осуществляется при вращательном главном движении, сообщаемом обрабатываемой заготовке, и при прямолинейном (поступательном) движении подачи, сообщаемом резцу. Элементами режима резания при точении заготовки являются скорость резания, подача и глубина резания. Скоростью резания называется длина пути, пройденного режущей кромкой инструмента относительно обрабатываемой поверхности заготовки в единицу времени. Скорость резания измеряется в м/мин и обозначается буквой v.
Подачей называется величина перемещения режущей кромки инструмента за один оборот заготовки (в направлении подачи) или в единицу времени. Подача измеряется в мм/об или в мм/мин, обозначается буквой s и может быть продольной (если инструмент перемещается параллельно оси вращения заготовки) и поперечной (если инструмент перемещается перпендикулярно этой оси). Глубиной резания называется величина срезаемого за один проход резца слоя металла, измеренная по перпендикуляру к обработанной поверхности детали. Глубина резания измеряется в миллиметрах и обозначается буквой t.
У заготовки различают следующие поверхности: обрабатываемую (с которой снимают стружку), обработанную (полученную после снятия стружки) и резания (которая является переходной между обрабатываемой и обработанной поверхностями и образуется режущим инструментом).
Основные поверхности заготовки и основные движения, осуществляющие процесс резания, показаны на рисунке 3.
Рис. 3. Основные поверхности и движения
1 - обрабатываемая поверхность, 2 - поверхность резания, 3 - обработанная поверхность, 4 - ось вращения заготовки, 5 - продольная подача, 6 - поперечная подача, 7 - резец, 8 - заготовка, 9 - главное (вращательное) движение, t - глубина резания
Токарно-винторезный станок
Устройство и классификация.
Рис. 4. Сборочные единицы (узлы) и механизмы токарно-винторезного станка:
1 - передняя бабка, 2 - суппорт, 3 - задняя бабка, 4 - станина, 5 и 9 - тумбы, 6 - фартук, 7 - ходовой винт, 8 - ходовой валик, 10 - коробка подач, 11 - гитары сменных шестерен, 12 - электро-пусковая аппаратура, 13 - коробка скоростей, 14 - шпиндель
Токарно-винторезные станки предназначены для обработки, включая нарезание резьбы, единичных деталей и малых групп деталей. Однако бывают станки без ходового винта. На таких станках можно выполнять все виды токарных работ, кроме нарезания резьбы резцом.
Техническими параметрами, по которым классифицируют токарно-винторезные станки, являются наибольший диаметр D обрабатываемой заготовки (детали) или высота Центров над станиной (равная 0,5 D), наибольшая длина L обрабатываемой заготовки (детали) и масса станка.
Ряд наибольших диаметров обработки для токарно-винторезных станков имеет вид: D = 100, 125, 160, 200, 250, 320, 400, 500, 630, 800, 1000, 1250, 1600, 2000 и далее до 4000 мм. Наибольшая длина L обрабатываемой детали определяется расстоянием между центрами станка. Выпускаемые станки при одном и том же значении D могут иметь различные значения L. По массе токарные станки делятся на легкие - до 500 кг (D = 100 - 200 мм), средние - до 4 т (D = 250 - 500 мм), крупные - до 15 т (D = 630 - 1250 мм) и тяжелые - до 400 т (D = 1600 - 4000 мм).
Легкие токарные станки применяются в инструментальном производстве, приборостроении, часовой промышленности, в экспериментальных и опытных цехах предприятий. Эти станки выпускаются как с механической подачей, так и без нее.
На средних станках производится 70 - 80% общего объема токарных работ. Эти станки предназначены для чистовой и получистовой обработки, а также для нарезания резьб разных типов и характеризуются высокой жесткостью, достаточной мощностью и широким диапазоном частот вращения шпинделя и подач инструмента, что позволяет обрабатывать детали на экономичных режимах с применением современных прогрессивных инструментов из твердых сплавов и сверхтвердых материалов. Средние станки оснащаются различными приспособлениями, расширяющими их технологические возможности, облегчающими труд рабочего и позволяющими повысить качество обработки, и имеют достаточно высокий уровень автоматизации.
Крупные и тяжелые токарные станки применяются в основном в тяжелом и энергетическом машиностроении, а также в других отраслях для обработки валков прокатных станов, железнодорожных колесных пар, роторов турбин и др.
Все сборочные единицы (узлы) и механизмы токарно-винторезных станков имеют одинаковое название, назначение и расположение (см. рис 4.).
Типичный токарно-винторезный станок 16К20 завода "Красный пролетарий" показан на рисунке 5.
Рис. 5. Общий вид и размещение органов управления токарно-винторезного станка мод. 16К20:
Рукоятки управления: 2 - сблокированная управление, 3,5,6 - установки подачи или шага нарезаемой резьбы, 7, 12 - управления частотой вращения шпинделя, 10 - установки нормального и увеличенного шага резьбы и для нарезания многозаходных резьб, 11 - изменения направления нарезания резьбы (лево- или правозаходной), 17 - перемещения верхних салазок, 18 - фиксации пиноли, 20 - фиксации задней бабки, 21 - штурвал перемещения пиноли, 23 - включения ускоренных перемещений суппорта, 24 - включения и выключения гайки ходового винта, 25 - управления изменением направления вращения шпинделя и его остановкой, 26 - включения и выключения подачи, 28 - поперечного перемещения салазок, 29 - включения продольной автоматической подачи, 27 - кнопка включения и выключения главного электродвигателя, 31 - продольного перемещения салазок; Узлы станка: 1 - станина, 4 - коробка подач, 8 - кожух ременной передачи главного привода, 9 - передняя бабка с главным приводом, 13 - электрошкаф, 14 - экран, 15 - защитный щиток, 16 - верхние салазки, 19 - задняя бабка, 22 - суппорт продольного перемещения, 30 - фартук, 32 - ходовой винт, 33 - направляющие станины
Сведения о технологическом процессе обработки деталей (заготовок)
Заготовки и документы
Технологическим процессом называется часть производственного процесса, связанная с последовательным изменением формы, размеров и качества поверхности заготовки от момента поступления ее в обработку до получения готовой детали. Элементами технологического процесса при обработке деталей резанием являются операции, установки, переходы и проходы.
Операция - законченная часть технологического процесса обработки заготовки, выполняемая на одном рабочем месте (на одном станке) непрерывно до перехода к обработке следующей заготовки.
Установка - часть операции, выполняемая при одном неизменном закреплении обрабатываемой заготовки.
Переход - законченная часть операции, характеризующаяся постоянством обрабатываемой поверхности, рабочего инструмента и режима работы станка. Одновременную обработку нескольких поверхностей детали несколькими инструментами принято считать за один переход.
Проход - часть перехода, осуществляемая при одном рабочем перемещении инструмента в направлении подачи; за один проход снимают один слой металла.
При изучении технологических процессов и при техническом нормировании выделяют в операции рабочие приемы.
Рабочий прием - определенное законченное действие рабочего из числа необходимых для выполнения данной операции (например, установка заготовки, пуск станка и т. п.).
Заготовки для получения деталей. Заготовки деталей получают литьем, ковкой, штамповкой, сваркой, прессованием, прокаткой, волочением. Заготовки бывают металлические и неметаллические. Неметаллические заготовки в основном получают из пластмасс (синтетических веществ органического происхождения) методом литья, прессования и выдавливания. К металлическим заготовкам относятся прокат из стали и цветных металлов (простых и сложных профилей) в виде прутков и труб, поковки, листовая штамповка, отливки.
Большинство деталей типа валов, втулок, шайб и колец изготовляют из заготовок, поставляемых в виде круглых, шестигранных и квадратных прутков. Крупные и сложные по форме детали получают из штучных заготовок, полученных литьем, ковкой или штамповкой. Выбор вида заготовки зависит от конструктивных особенностей детали (например, болт с шестигранной головкой целесообразно изготовлять из шестигранного прутка, а не из круглого).
Заготовка должна иметь несколько большие размеры, чем готовая деталь, т. е. предусматривается слой металла, снимаемый при механической обработке, который называется припуском на обработку. Величина припуска должна быть наименьшей (т. е. заготовка по форме и размерам должна приближаться к форме и размерам готовой детали), но при этом должно быть обеспечено получение годной детали.
Технологический процесс изготовления какого-либо изделия оформляется специальными документами, на основе Единой системы технологической документации (ЕСТД), которая устанавливает основные виды технологических документов. Основная цель ЕСТД, - установить на всех предприятиях единые правила оформления, выполнения и обращения технологической документации, что дает возможность обмена технологическими документами между предприятиями без переоформления этих документов. К основным технологическим документам относят маршрутные и операционные карты, карты эскизов и рабочие чертежи.
Маршрутная карта содержит последовательное описание технологического процесса изготовления изделия по всем операциям с указанием данных об оборудовании, оснастке, материальных и трудовых нормативах.
Операционная карта содержит описание операций с расчленением их по переходам и с указанием режимов обработки и данных о режущем, вспомогательном, измерительном инструменте, оснастке и т. д.
Карта эскизов содержит эскизы, схемы, таблицы, необходимые для выполнения технологического процесса, операции, перехода. При вычерчивании эскиза соблюдаются следующие правила и условия: деталь на эскизе располагают в рабочем положении, т. е. так, как она расположена на станке; при многопозиционной обработке эскиз выполняют для каждой позиции отдельно; инструменты показывают на обрабатываемой поверхности в конечном положении обработки; в каждой позиции обрабатываемые поверхности заготовки изображают толстыми линиями черным (или красным) цветом, а базовые поверхности, на которых заготовка устанавливается, - условными обозначениями; на обрабатываемых поверхностях обязательно указывают размеры с допусками и расстояния от баз; направления перемещения заготовки и инструментов показывают стрелками; при выполнении эскизов револьверных операций указывают позиции револьверной головки с соответствующими инструментами.
Исходными данными при составлении маршрутной и операционной карт являются производственная программа, чертежи, спецификация, технические условия, паспорт станка, альбомы режущих и вспомогательных инструментов, альбомы приспособлений, руководящие материалы по режимам резания, нормативы подготовительно-заключительного и вспомогательного времени, тарифно-квалификационный справочник.
Маршрутная карта состоит из двух основных частей - верхней и нижней. В верхней части помещают сведения об изготовляемой детали и ее заготовке, а в нижней - описание технологического процесса с разделением на операции и с указанием необходимых станков, приспособлений, режущего, вспомогательного и измерительного инструмента, а также указания профессий, разрядов работы, тарифной сетки, норм времени и расценок.
Основным условием, обеспечивающим выполнение производственного задания, является наличие подробно разработанной технологической документации, внимательное изучение ее рабочим, строгое соблюдение указаний, предусмотренных в ней.
Технологические базы
В машине, механизме, станке, детали соединяются между собой, обеспечивая передачу и преобразование движений. В процессе обработки заготовки (детали) закрепляются. Для ориентации заготовок во время обработки на станках, расположения готовых деталей в сборочных единицах (узлах) машин, измерения деталей служат поверхности, линии, точки и их совокупности, которые называются базами. Различают технологические и конструкторские базы. Технологические базы разделяются на установочные и измерительные.
Рис. 6. Установочные базы
Установочные базы - поверхности (а также линии и точки), служащие для установки заготовки на станке и ориентирующие ее относительно режущего инструмента. Например, торцовая 3 и цилиндрическая 4 поверхности кулачков патрона рисунок 6. а) справа, или торцовая поверхность 7 патрона и цилиндрическая поверхность 8 кулачков рисунок 6 б), или конические поверхности 5 и 6 центров станка рисунок 6 в) и др.
Установочными базами могут быть различные поверхности заготовок, а также центровые гнезда и плоскости. Например, установочными базами для втулки могут быть наружная поверхность 1 и торец 2 см. рисунок 6 а) справа, наружная 9 или внутренняя 10 цилиндрические поверхности и торец 11 рисунок 6 г). В качестве баз при первоначальной обработке используют необработанные поверхности (черновые базы), при последующей обработке - обработанные поверхности (чистовые базы). Установочные базы делятся на основные и вспомогательные. Основные установочные базы - это поверхности, которые ориентируют заготовки (обрабатываемые детали) на станке и положение готовых деталей в машине относительно других сопрягаемых деталей при ее работе. Например, основными установочными базами для втулки могут являться торец 11 и внутренняя поверхность 10 рисунок 6 г), если втулка монтируется на вал. Вспомогательные установочные базы - это поверхности, которые используют только для установки заготовок (деталей) на станке; они не имеют особого значения для работы машины. Примерами вспомогательной базы могут служить центровые гнезда вала, обтачиваемого и шлифуемого с установкой в центрах рисунок 6 в), необработанная шестигранная поверхность головки болта и др.
Рис. 7. Измерительные базы
Измерительная база - поверхность (линия или точка), от которой производят отсчет размеров. Например, на рисунке 7 а) заданы размеры А и С, а размер В – свободный, следовательно, поверхность 2 - измерительная.
Конструкторская база - совокупность поверхностей, линий, точек, от которых заданы размеры и положение деталей при разработке конструкции. Конструкторские базы могут быть реальными (материальная поверхность) или геометрическими (осевые линии, точки). При выборе черновых установочных баз руководствуются следующими правилами: базовые поверхности должны быть по возможности ровными и чистыми (не следует, например, принимать за базы поверхности, на которых располагаются литники, линии разъема моделей или заусенцы), базовые поверхности не должны изменяться относительно других поверхностей (не следует, например, брать за базу поверхность литого отверстия, так как его положение может изменяться), за базы рекомендуется принимать поверхности с минимальными припусками или вообще не подвергаемые
Рис.8. Обработка сырых кулачков
обработке. При переустановке заготовки черновые базы заменяются чистовыми. При выборе чистовых установочных баз следует: выбирать основные базы, так как это обеспечивает большую точность обработки; соблюдать при обработке принцип постоянства баз; совмещать при возможности установочные и измерительные базы. Например, на рисунке 7а) измерительной базой является поверхность 2, станок настроен от установочной базы 1 на размер В, а размер С получен на предыдущей операции. Следовательно, установочная и измерительная базы не совпадают. Для получения размера А в пределах допуска нужно определить отклонения размера В, как это сделано на рисунке 7б); при этом установочная и измерительные базы будут совмещены (совпадут). В качестве базирующих поверхностей при точении применяют наружную (или внутреннюю), цилиндрическую поверхность и торец, два центровых гнезда, наружную (или внутреннюю) цилиндрическую поверхность и центровое гнездо. Для повышения точности обработки в самоцентрирующих патронах применяют сырые кулачки, которые протачиваются непосредственно перед обработкой заготовки (детали) или партии деталей. Обработка кулачков производится под наг
|
|
Таксономические единицы (категории) растений: Каждая система классификации состоит из определённых соподчиненных друг другу...
Биохимия спиртового брожения: Основу технологии получения пива составляет спиртовое брожение, - при котором сахар превращается...
Наброски и зарисовки растений, плодов, цветов: Освоить конструктивное построение структуры дерева через зарисовки отдельных деревьев, группы деревьев...
Адаптации растений и животных к жизни в горах: Большое значение для жизни организмов в горах имеют степень расчленения, крутизна и экспозиционные различия склонов...
© cyberpedia.su 2017-2024 - Не является автором материалов. Исключительное право сохранено за автором текста.
Если вы не хотите, чтобы данный материал был у нас на сайте, перейдите по ссылке: Нарушение авторских прав. Мы поможем в написании вашей работы!