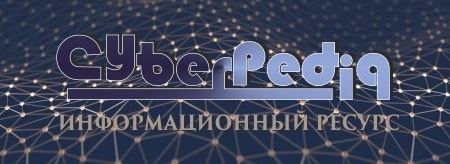
Археология об основании Рима: Новые раскопки проясняют и такой острый дискуссионный вопрос, как дата самого возникновения Рима...
Эмиссия газов от очистных сооружений канализации: В последние годы внимание мирового сообщества сосредоточено на экологических проблемах...
Топ:
Отражение на счетах бухгалтерского учета процесса приобретения: Процесс заготовления представляет систему экономических событий, включающих приобретение организацией у поставщиков сырья...
Основы обеспечения единства измерений: Обеспечение единства измерений - деятельность метрологических служб, направленная на достижение...
Процедура выполнения команд. Рабочий цикл процессора: Функционирование процессора в основном состоит из повторяющихся рабочих циклов, каждый из которых соответствует...
Интересное:
Аура как энергетическое поле: многослойную ауру человека можно представить себе подобным...
Наиболее распространенные виды рака: Раковая опухоль — это самостоятельное новообразование, которое может возникнуть и от повышенного давления...
Подходы к решению темы фильма: Существует три основных типа исторического фильма, имеющих между собой много общего...
Дисциплины:
![]() |
![]() |
5.00
из
|
Заказать работу |
|
|
МЕХАНИЧЕСКОЕ ОБОРУДОВАНИЕ
ВАГОНОВ МЕТРОПОЛИТЕНА
Введение
К подвижному составу относятся моторные вагоны, предназначенные для перевозки пассажиров, специальные вагоны (технического назначения) и моторно-рельсовый транспорт для перевозки хозяйственных грузов, приводимый в движение от собственного источника питания двигателя внутреннего сгорания. Моторный вагон приводится в движение электродвигателями, которые получают электроэнергию через токоприемники от контактного рельса. Каждый вагон метрополитена состоит из механического, пневматического оборудования, а также электрической части.
К механической части вагона относятся кузов, две двухосные поворотные тележки и автосцепные устройства.
Рисунок 1. Основные части вагона
1- кузов с внутривагонным оборудованием; 2- рама кузова вагона; 3- тележка;
4- автосцепка
Колесные пары вагона приводятся во вращение тяговыми двигателями. Валы тяговых двигателей соединены с осями колесных пар карданными муфтами и зубчатыми передачами (редукторами). На вагонах метрополитена получил применение индивидуальный тяговый привод, при котором каждая колесная пара приводится во вращение своим тяговым двигателем.
Для увеличения полезного объема пассажирского салона и безопасности пассажиров все основное оборудование подвешено под кузовом вагона на его раме. Тяговыми двигателями и другими электрическими аппаратами, находящимися под напряжением контактной сети, управляют дистанционно из кабины машиниста.Головные вагоны имеют кабину машиниста, в которой находятся основные аппараты управления поездом и кран машиниста.Пневматическое оборудование вагона создает запас сжатого воздуха, с помощью которого можно выполнять служебное и экстренное пневматическое торможение поезда, автоматическую работу раздвижных дверей, электрических аппаратов, звукового сигнала, стеклоочистителей и др.
|
Механическое оборудование вагонов.
Краткая техническая характеристика вагона.
Механическое оборудование вагонов метрополитена состоит из кузова, двух тележек, пятниковых опор, соединяющих кузов с тележкой, и двух автосцепок, позволяющих производить автоматическое сцепление вагонов в состав.
Все колесные пары вагона имеют тяговые двигатели, вращающий момент от которых передается к колесным парам через карданные муфты и одноступенчатые цилиндрические зубчатые передачи.
Для входа в пассажирский салон, вагон с каждой боковой стороны имеет по четыре дверных проема, которые закрываются раздвижными дверями с помощью привода с централизованным управлением.
Технические данные вагонов
Наименование | 81-717 (81-717.5п) | 81-714 (81-714.5п) |
Масса вагона (т) | 34 | 33 |
Длинна вагона по центрам автосцепок (мм) | 19210 | 19210 |
Ширина вагона (мм) | 2800 | 2800 |
Высота порожнего вагона от уровня головок рельс (мм) | 3650 (3700) | 3650 (3700) |
Высота кузова (мм) | 2660(2710) | 2660(2710) |
Расстояние от уровня головок рельсов до рамы кузова (мм) | 990 +25 -15 | 990 +25 -15 |
Максимальная конструктивная скорость (км/час) | 90 | 90 |
Среднее ускорение при пуске (м/сек2) | 1,2 | 1,2 |
Среднее замедление при торможении (м/сек2) | -1,3 | -1,3 |
Мощность тяговых двигателей (кВт) | 110(114) | 110(114) |
Максимальная вместимость (человек) | 277(308) | 308(330) |
База вагона и тележки
Рис. 2 База вагона и тележки
Длина вагона (19210мм)- расстояние между ударными (буферными) плоскостями двух автосцепок вагонов.Данное расстояние берется без учета длины серег, выступающих из головок автосцепок, т.к. серьги уходят внутрь противоположных головок при сцеплении вагонов.
База вагона (12600мм)- расстояние между центрами опор кузова вагона на ходовые части тележки. В центре тележки установлен предохранительный шкворень. Поэтому базой вагона считается расстояние между центрами двух предохранительных шкворней (или что одно и то же - расстояние между центрами башмаков токоприемников соседних тележек вагона).
|
Базой тележки (2100мм) называется расстояние между центрами осей колесных пар одной тележки. Увеличение базы тележки приводит к ее утяжелению, а уменьшение - к ухудшению ходовых качеств вагона и затруднению размещения на тележке рычажно - тормозной передачи (РТП).
Тормозные устройства вагона включают в себя:
· рабочий тормоз - электродинамический реостатный действующий при переводе тяговых электродвигателей на генераторный режим;
· экстренный тормоз - пневматический колодочный;
· стояночный тормоз – (блок-тормоз), действующий на 1-ю и 4-ю колесную пару.
Кузов вагона 81 – 717(714).
Кузов предназначен для размещения и перевозки пассажиров, а также для размещения подвагонного и внутривагонного оборудования.Кузов вагона представляет собой сварнуюцельнометаллическую конструкцию, состоящую из сваренных в одно целое рамы, двух боковых стен, лобовой и концевой частей, крыши, и металлического настила пола. В оборудование кузова входят также внутренняя отделка и потолок, перегородка (кроме 81-714) кабины машиниста, двери, окна, вентиляция, поручни, диваны, освещение.
Рис. 3 Рама кузова
Рама кузова сварная, является основанием кузова и служит его опорой на ходовые части.Рама состоит из двух продольных балок(2), составляющих вместе с торцевыми балками(1) замкнутый контур (нижний обвязочный пояс кузова), набора из 13 поперечных балок(6), а также двух шкворневых(3) и четырех хребтовых балок(4), установленных между торцевыми и шкворневыми балками с целью передачи продольных нагрузок на боковые пояса рамы и стенки.
Продольные и торцевые балки, образующие нижний пояс кузова, имеют коробчатое сечение высотой 180 мм; ширина горизонтальных полок, гнутых из листа толщиной 6 мм, составляет 70 мм. В продольных балках сделаны овальные отверстия для приварки наружной обшивки стен.
Поперечные балки дополнительно имеют овальные отверстия для монтажа трубопроводов и прокладки кондуитов с проводами.
Шкворневые балки сварены из двух вертикальных листов толщиной 8 мм и двух горизонтальных листов толщиной 10 мм; верхние листы удлинены для сварки с боковинами. В местах установки пятников и скользунов установлены ребра жесткости. На шкворневых балках имеются отверстия для шкворня пятниковых опор, соединяющих кузов с тележками.
|
Хребтовые балки выполнены из гнутого швеллера 180 мм, в средней части к ним приваривают специальные косынки из листа толщиной 6 мм, между которыми находятся гнездо автосцепки.В гнездах установлены шарнирные подшипники ШС-60 на валике.Для крепления оборудования на раме имеются дополнительные балки и кронштейны.
Все несущие детали рамы выполнены из стали 20 или ст.3. Средние продольные балки отсутствуют. Вместо этого по всей длине кузова применяется гофрированный металлический настил пола (гофрами вдоль вагона).
В устройство рамы кузова входят также рамки люков пола и различные кронштейны, угольники, скобы, ребра, косынки для подвески оборудования, электрических и пневматических аппаратов и для раскладки труб внизу рамы.
Раму кузова сваривают в специальных кондукторах, что исключает перекосы и обеспечивает большую точность изготовления.
Боковые стены и торцевые стенки кузова Боковые и торцевые стенки представляют собой металлический каркас, состоящий из вертикальных стоек и подоконных балок. Вверху вертикальные стойки связаны элементами жесткости, образующими верхний обвязочный пояс кузова. Внизу вертикальные стойки приварены к нижнему обвязочный поясу кузова. Каркас стен обшит стальными листами толщиной 2мм.
Сварка отдельных секций стенок кузова выполняется электроконтактной сваркой с последующим соединением отдельных секций боковин с торцевыми стенками и крышей электродуговой сваркой в специальном кондукторе.
Приварка стенок кузова к раме производится прерывистой электродуговой сваркой через овальные отверстия в боковых поясах рамы и сплошным швом по нижней кромке обшивки и вертикальной стенке бокового пояса.
Крыша Крыша выполнена из стальных омегообразных дуг толщиной 2мм, которые опираются на верхний пояс кузова. В продольном направлении дуги связаны параллельными рядами стальных полос (стрингеров). Проемы, расположенные между продольными боковыми полосами и дугами, закрываются специальными вентиляционными черпаками. Кровля изготовлена из листовой стали толщиной 1,5 мм. Конструкция крыши позволяет производить ее сборку как целиком, так и по секциям.
|
Внутреннее помещение кузова разделяется перегородкой на пассажирский салон и кабину управления (кроме вагонов 81-714).
Перегородка со стороны салона имеет дверь для прохода в кабину. Двойные стенки перегородки справа и слева дверного проема образуют отсеки для размещения оборудования АРС и радиовещания. Отсеки со стороны салона закрываются створками люков, которые навешиваются на петлях.
Пол салона
На раму кузова укладывается и приваривается к ней электросваркой гофрированный металлический настил, гофрами вдоль вагона. На настил (1) укладываются два слоя асбеста (2) и фанера (3) толщиной 10 мм. Листы фанеры прикрепляют к металлическому настилу самонарезающими винтами (4). Нижняя поверхность фанеры покрывается антисептической (противогнилостной) пастой. Верхняя поверхность фанеры окрашивается грунтом, и свободная от диванов плоскость покрывается линолеумом на тканевой основе толщиной 4мм (5).
Около шкворневых балок в полу имеются люки для осмотра и ухода за двигателями, редуктором и карданной муфтой. Кроме того, у каждой шкворневой балки в полу имеются отверстия, закрываемые резьбовыми крышками, для доступа к шкворню и масленке пятника. Там же расположены соединительные втулки (коннекторы) проводов силовой цепи, идущих от токоприемников к двигателям.
Рис. 4 Пол салона
1 - лист гофрированного железа
2 - два листа асбеста
3 - слой прессованной фанеры
4 - винт
5 - лист линолеума
Диваны
По обеим сторонам салона в промежутках между раздвижными дверями расположены диваны на шесть сидячих мест, между торцевыми стенками и дверными проемами - диваны на три сидячих места. Конструкция дивана представляет собой каркас, состоящий из боковин, продольных связей и щитков, закрывающих поддиванное пространство. Подушки и спинки диванов полумягкие.На деревянную рамку подушек устанавливается фанера толщиной 8 - 10 мм и на нее наклеивается пластина из пенорезины толщиной 20 мм. На деревянную рамку спинки крепится лист дюралюминия толщиной 1,5 мм с последующей наклейкой на него пластины пенорезины толщиной 10 мм. и обтягивается кожзаменителем.Также используются, антивандальные диваны, выполненные из пластика со съемными подушками и спинками. Каждый диван закрыт на трёхгранный замок.
Окна
Окна застеклены полированным закаленным стеклом толщиной 6 мм. Все стекла с помощью специальных резиновых уплотнителей вставляют в оконные проемы, прижимают к буртику наружной обшивки внутренними алюминиевыми раскладками и крепят винтами с хромированными головками.
|
Данный тип стекла отличается своей прочностью и прозрачностью. Однако, при сильном ударе превышающим расчетную нагрузку, стекло распадается на мелкие осколки.Широкие окна салона оборудованы форточками толщиной 5 мм с задвижным или откидным стеклом.Правое боковое стекло в кабине управления имеет откидывающуюся или опускающуюся форточку.
Поручни
Поручни располагаются по всей длине вагона на высоте 1830 мм, от пола и крепятся через кронштейны к потолку вагона. Горизонтальные поручни изготовлены из хромированных труб диаметром 27 мм, вертикальные - диаметром 22 мм, а кронштейны (полированные из алюминиевого сплава) - литьем под давлением.Для улучшения условий перевозки пассажиров установлены горизонтальные и дополнительные вертикальные поручни.Для обслуживающего персонала установлены дополнительные вертикальные поручни на двери перегородки между салоном и кабиной, в концевой части вагона для облегчения перехода из вагона в вагон.
Вентиляция
|
Вагоны 81-540.1(541.1) оборудованы системой принудительной вентиляции.
Вентиляция кабины управления механическая. Она предназначена для подачи воздуха в кабину свежего воздуха как во время движения, так и во время его стоянок. Система вентиляции имеет возможность изменять направление воздушного потока и его скорость до приемлемой для машиниста в районе рабочего места. Вентиляционная установка состоит из заборного устройства с фильтрующим элементом, вентиляционного агрегата и раздаточного воздуховода. Вентилятор установлен под кабиной машиниста слева.
Двери
На вагоне применяется два вида дверей - створчатые и раздвижные.
Створчатые двери находятся по торцам кузова вагона и называются торцевыми. Они подвешены к дверным стойкам каркаса кузова при помощи стальных шарнирных петель, которые крепятся к стойкам при помощи болтов. Эти двери оборудованы поворотными ручками и запорными замками, приводимыми в действие трехгранным ключом. Конструкция всех дверей - бескаркасная, они изготовлены из листов алюминиевого сплава, между которыми вварены штампованные профили. Сборку штампованных профилей производят на одном из листов створки, затем сверху приваривают второй лист.Двери имеют стекла той же толщины, что и основные салонные. Они также установлены в проемы через резиновые уплотнители. Дверь из кабины в салон изготовлена из стального листа и профиля.
Раздвижные двери предусматривают восемь дверных проемов (по четыре с каждой стороны вагона).
Цепной механизм
Открытие и закрытие дверей производится при помощи пневматического дверного цилиндра жестко связанного с одной из створок.Вторая створка связана с первой при помощи цепного механизма, состоящего из следующих элементов:
Рис. 7. Цепной механизм
I, II - цепи
1, 2, 3, 4 - кронштейны подвески створок и соединения их с цепями
5 - звездочки
6 - натяжные винты цепей
7 - болты подвески
Работа цепного механизма
При открытии дверей левая створка (она же является правой с внешней стороны) вместе с кронштейнами (1) и (2) начинает перемещаться влево. При этом кронштейн (2) через вторую цепь воздействует на кронштейн (4), заставляя правую створку начать перемещаться вправо - так же на открытие, а ее кронштейн (3), перемещаясь вместе с ней вправо, не дает возможности провиснуть первой цепи.
При закрытии дверей левая створка вместе с кронштейнами (1) и (2) начинает перемещаться вправо. При этом кронштейн (1) через через первую цепь воздействует на кронштейн (3), заставляя правую створку начать перемещаться влево - также на закрытие, а ее кронштейн (4), перемещаясь вместе с ней влево, не дает возможности провиснуть второй цепи.
Рис. 3.15. Элементы цепного механизма
Рис. 3.16. Элементы цепного механизма
Рис. 3.17. Элементы цепного механизма
1 - звездочка
2 - кронштейн крепления звездочки
3 - шарикоподшипник
4 - цепь
5 - большой кронштейн
6 - натяжной винт цепи
7 - гайки натяжного винта цепи
8 - малый кронштейн
Работа дверей
Ведущая створка дверного проема жестко соединяется со штоком дверного цилиндра, и ее перемещение будет на прямую зависеть от перемещения поршня дверного цилиндра. Вторая (ведомая) створка приводится в движение при помощи цепного механизма (двух цепей и двух звездочек).
Неисправности раздвижных дверей:
1. Ослабление натяжения цепи. 2. Излом кронштейна. 3. Разрушение звездочки. 4. Выход из строя регулировочных винтов. 5. Неисправности дверной блокировки. 6. Попадание под створку посторонних предметов.
Тележка вагона
Предназначена для формирования и реализации продольных сил, направления движения вагона, восприятия нагрузок с кузова вагона и перераспределение их на путь.
Каждая тележка - поворотная, шарнирно соединяется с кузовом вагона с помощью пятниковой опоры, вокруг которой она может поворачиваться в горизонтальной плоскости. При этом оси колесных пар будут устанавливаться по радиусу кривой поворота, что уменьшает угол набегания колес на рельсы и, следовательно, износ колеса и головки рельса. Все тележки делятся в соответствии с конструкцией их рам на поводковые и шпинтонные. При изготовлении тележки ей присваивается номер, который наносится при помощи электрической сварки на кронштейн правого тормозного цилиндра соседнего с блок-тормозом и на противоположных кронштейнах по диагонали, а также заводится техпаспорт, в котором указывается: завод - изготовитель тележки, дата изготовления, заводской номер тележки, основные технические данные и конструктивные изменения.
Рисунок 14. Тележка вагонов 81-717(714)
База вагона - 12600 мм, расстояние между центрами осей двух шкворней (расстояние между центрами осей башмаков токоприемников одного вагона с одной стороны).
База тележки - 2100 мм, расстояние между центрами осей колесных пар.
Тележка в сборе (рис.14, 15, 16)состоит из рамы тележки (1), 2 к/п. в сборе (2), 2 т/д (3), 2 карданных муфт (4), центрального подвешивания в комплекте с центральной балкой и 2 гидрогасителей (5), надбуксового подвешивания (7), 4 РТП (6), 3 тормозных цилиндров (8), блок – тормоза (10) и 2 бруса токоприемника (9).
Рисунок 15. Тележка Рисунок 16. Тележка
Работа тележки
Передача вертикальных нагрузок:
Передача весовых нагрузок от кузова передается через пятниковое устройство на центральное подвешивание, которое передает эти нагрузки на раму тележки. Далее нагрузка с рамы поступает на колесные пары через комплекты надбуксового подвешивания.
Формирование и реализация продольных сил:
Крутящие момент с якорей тяговых электродвигателей через карданные муфты передается на колесные пары, которые преобразуют эти моменты в поступательное движение. В дальнейшем продольная сила от буксовых узлов через шпинтоны или поводки передается на раму тележки и далее через центральное подвешивание и пятниковое устройство на кузов вагона.
Рама тележки
Рама воспринимает вес кузова и равномерно распределяет его между колесными парами. Рама воспринимает также тяговые и тормозные усилия от колесных пар и передает их кузову, а так же является связующим звеном между центральным и надбуксовым подвешиванием. Действующие на раму дополнительные нагрузки, обусловленные неровностями рельсового пути, извилистым движением колесных пар, центробежной силой, возникающей в кривых участках пути вызывают растяжение и изгиб ее элементов как в вертикальной, так и горизонтальной плоскостях, а также их кручение, поэтому конструкция рамы должна обладать достаточной прочностью.
Рисунок 17. Поводковая рама
Рама (рис. 17, 18) представляет собой цельносварную Н - образную конструкцию состоящую из двух продольных (1) и двух поперечных (3) балок. продольных и поперечных балок усиливаются косынками (2) листовой стали толщиной 6 мм.
Каждая балка состоит из двух профилей листовой стали 20 толщиной 10 мм. Места сварки Основным достоинством такой конструкции является относительно небольшой вес при одинаковой прочности по сравнению с рамами тележек других конструкций.
Недостаток – большое число сварных швов, которые являются концентраторами напряжений и характерными местами трещинообразований, поскольку рамы работают при переменной нагрузке, вызванной колебаниями рессорного подвешивания и неровностями рельсового пути.
Учитывая, что наиболее часто трещины образуются в местах соединения балок и сварных швах приварки кронштейнов, при конструировании рам этому обстоятельству должны уделять особое внимание.
На продольных балках тележки расположены: кронштейны крепления рычагов РТП (5) и оттормаживающих устройств (8), ТЦ (8), блок – тормоза (4), вварены втулки под запрессовку шпинтонов (для рам со шпинтонным подвешиванием), вварены втулки под предохранительные штыри букс (15) и кронштейны для крепления поводков(13) (для рам с поводковым подвешиванием), гидравлического гасителя колебаний (14). На тележках головных вагонов располагаются приемные катушки АРС и рельсосмазыватели РСЧ (8).
Рисунок 18. Шпинтонная рама
На поперечных балках тележки расположены: кронштейны крепления т/д (10), подвески редукторов (7) (кронштейны выполнены литыми вставлены в балки и проварены), крепления комплексного предохранения (12), крепления предохранительных скоб центрального подвешивания (11), реактивных тяг (16), технологические отверстия для валиков серег (9), проушины для серег центрального подвешивания. На второй тележке расположена плита авторежима.
Рисунок 19. Плоские скользуны
Для передачи тяговых и тормозных усилий с рамы тележки на центральную балку установлены сменные наличники(плоские скользуны) (6) состоящие из двух пластин, последняя из пластин имеет термообработанную шлифованную поверхность с каналами для смазки трущихся поверхностей. Зазор должен быть 0,4 – 5 мм (рис.19). При выработке скользунов зазор регулируют сменой сменных наличников или восстановлением поверхности.
Пятниковое устройство
Предназначено для опоры кузова и передачи вертикальной нагрузки на раму тележки через шкворневую балку на центральную балку, а также для передачи тяговых и тормозных усилий и обеспечение поворота тележки относительно кузова.
Рисунок 20. Пятниковое устройство
Состоит (рис.20) из пятника (рис. 21), который выполнен из стального литья в форме выпуклой полусферы с фланцем для крепления 4 болтами к шкворневой балке
В пятнике имеются 6 отверстий для перетекания смазки в подпятник. Подпятник (вогнутая полусфера в середине сферы имеется центрирующий выступ, который входит в отверстие в резиновом амортизаторе. В подпятнике имеются кольцевые и радиальные канавки для равномерного распределения смазки поступающей через отверстия в пятнике). Резинометаллический амортизатор (резиновая шайба, армированная с обеих сторон стальными листами. Толщина амортизатора 36 – 2 мм, но не менее 30 мм.). Предохранительный шкворень (стальной стержень диаметром 55 мм, и длиной 550 мм. В верхней части шкворень имеет головку, которой он опирается на пружину, на головке шкворня приварено ушко для постановки и извлечения шкворня. В нижней части чека для фиксации шкворня.
Боковые роликовые или чечевичные опоры (скользуны) обеспечивают устойчивость кузова, ограничивая его продольные перемещения при прохождении вагоном кривых участков пути, чем обеспечивается равномерное распределение нагрузки на к/п. Суммарный зазор между скользунами кузова и тележки в эксплуатации 3 – 8 мм. Регулировка зазора производиться путем изменения числа 2 мм, стальных пластин под сменными наличниками на шкворневой балке (рис.22).
Рисунок 21. Пятник Рисунок 22. Сменные наличники
Рессорное подвешивание
Это упругое устройство, которое служит для смягчения и частичного гашения колебаний, вызываемых изменением профиля пути, для сохранения плавности хода вагона и возвращение его в изначальное положение. На составах метрополитена в качестве рессор применяют цилиндрические пружины, изготовленные путем завивки стального прута.
Надбуксовое подвешивание
Предназначено для подрессоривания рамы тележки относительно колесной пары и передачи тяговых и тормозных усилий и вертикальной нагрузки.
Используется двух видов шпинтонное и поводковое.
В связи с большим количеством дефектов, образующихся в поводковом буксовом подвешивании (трещины и изломы поводков, крепежных деталей, износы гребенок, трещины в кронштейнах крепления буксовых поводков и продольных балках рамы в зоне приварки этих кронштейнов), было принято решение о разработке модернизированного шпинтонного буксового подвешивания.
Шпинтонное подвешивание
Шпинтоны (1) запрессованы в продольные балки рамы тележки и зафиксированы гайками (2) со стопорными планками, которые стопорятся болтами. Для защиты трущихся поверхностей от попадания абразивных частиц (песка, грязи и т.д.) шпинтонный узел закрыт резиновым колпачком (14),который крепиться хомутиком (13) и защитным резиновым чехлом (6) закрепленным при помощи проволоки.
Рисунок 23. Шпинтонное подвешивание Рисунок 24. Шпинтонное подвешивание
Работа шпинтонного узла
Передача вертикальной нагрузки: · продольная балка рамы тележки · запрессовочная втулка · резиновое кольцо · верхняя опора пружины · пружина · нижняя опора пружины · резиновое кольцо · крыло буксы · букса (корпус буксы | Передача горизонтальных усилий: · корпус буксы · крыло буксы · нижняя опора пружины · резиновая втулка · стакан · пластмассовая втулка · шпинтон · запрессовочная втулка · продольная балка рамы тележки |
Неисправности узла - появление трещин в продольных балках рамы тележки, излом пружин.
Поводковое подвешивание
Состоит (рис. 25) из двух комплектов пружин (две пружины вставленные друг в друга различной навивки (3) внешняя пружина - из стальной проволоки диаметром 27 мм, и внутренняя пружина - из стальной проволоки диаметром 17 мм. (высота комплекта пружин под тарой вагона 249 мм.) Комплекты пружин опираются на нижние (13) и верхние направляющие опоры (7). Для устранения металлического контакта между верхней опорой и продольной балкой устанавливаются резиновые прокладки (6)толщиной 33 мм.
В качестве рессор на тележках вагонов используют цилиндрические пружины, изготавливаемые из прутков круглого сечения пружинной стали марки 60С2А-3В-Б. Пружины характеризуют их жесткостью или обратной ее величиной – гибкостью.
Рисунок 25. Поводковое подвешивание
Правильный выбор этих параметров позволяет обеспечить безопасность движения и плавный ход подвижного состава. При изготовлении пружин верхний и нижний витки выполняют так, чтобы их опорные поверхности были плоскими и перпендикулярными оси пружины. Жесткость пружин зависит от их диаметра, числа витков, толщины прутка, а также от высоты пружин в свободном состоянии.
На тележках вагонов 81-717, 81-714 в буксовом подвешивании установлены пружины более жесткие по сравнению с пружинами тележек типа Е. Жесткость пружин увеличена за счет применения при их изготовлении прутков большего диаметра: для наружных пружин 28 мм вместо 27 мм; для внутренних пружин 18 мм вместо 17 мм, а также за счет увеличения высоты пружин в свободном состоянии до 290 мм вместо 275 мм. На вагонах Е установлены прокладки толщиной 33 мм, наружный диаметр которых соответствует наружному диаметру пружин.
На тележках вагонов 81-717, 81-714 толщина прокладок уменьшена до 23 мм за счет увеличения высоты пружин. Большое значение на работу буксового подвешивания оказывает положение гребенок на кронштейнах рамы, а также положение самих кронштейнов крепления поводков. При монтаже буксового подвешивания гребенки поводков должны точно совпадать с гребенками рамы. При отклонениях положения гребенок, а также в результате деформации или извернутости рамы, которую она может получить в процессе эксплуатации, для обеспечения прочного соединения (зубья гребенок поводков должны попасть во впадины гребенок рамы) поводки приходится упруго деформировать, т.е. еще до начала эксплуатации поводки находятся в напряженном состоянии, что отрицательно сказывается на их работе и работе всего буксового подвешивания.
Поводки предназначены для передачи тяговых и тормозных усилий, а также для связи колесной пары с рамой тележки.
Каждое колесо связывают три поводка: два прямых (11, 14) один из которых крепится к тумбе (10) и угловой (2) компенсационный. В местах соединения поводков нарезаны зубья (гребенки), которые обеспечивают плотное и прочное соединение. На верхней части корпуса буксы наварен предохранительный штырь (4), который необходим для исключения потери связи к.п. с рамой тележки (9) в случае излома поводков.
Поводки изготовляют из полосовой рессорной стали марки 60С2А шириной 90 мм. На концах имеются гребенки с четырьмя отверстиями диаметром 17,6 мм. Высота зубьев гребенок 2,7 мм. Нарезку гребенок производят методом фрезерования гребенчатой фрезой. Минимальная толщина гребенок – 12,5 мм, а средней части поводка – 7 мм. С целью увеличения срока службы поводков и более надежной его работы на тележках вагонов 81-717, 81-714 применяют буксовые поводки переменного сечения. Эти поводки изготавливают из более широкой полосовой стали – 110 мм, т.е. зона трещинообразований усилена.
Рисунок 26. Тумба с поводком Рисунок 27. Поводковое подвешивание
Рабочая, средняя часть поводка выполнена более узкой, что делает его гибче и способствует более равномерному распределению нагрузок по всей длине поводка.
Работа поводкового узла
Передача вертикальной нагрузки: · продольная балка рамы тележки · резиновые кольца · компенсирующие прокладки · верхние опоры пружин · комплекты пружин · нижние опоры пружин · крылья буксы · корпус буксы | Передача горизонтальной нагрузки: · корпус буксы · крылья буксы · гребенки · поводки · кронштейны на продольной балке · продольная балка рамы тележки |
Центральное подвешивание
Предназначено для подрессоривания кузова вагона относительно рамы тележки и передачи тяговых и тормозных усилий и вертикальной нагрузки.
Состоит (рис. 28) из центральной балки центрального подвешивания (1), резиновых прокладок (16)(которые снижают шум при прохождении составом неровностей рельсового пути), верхние (15) и нижние (12)опоры пружин (направляющие внутренние пружины), комплекта пружин (13,14) внешней пружины – из стальной
проволоки диаметром 30 мм правой навивки; внутренней пружины – из стальной проволоки диаметром 20 мм, пружины разной навивки применяются для исключения попадания витков одной пружины между витков другой пружины, высота пружин под тарой вагона 285 мм, поддон - балансир (11) фасонная плита, на верхней плоскости имеющая два гнезда для пружин.
Рисунок 28. Центральное подвешивание
На боковых частях поддона по два выступа, рамки (6)(вертикальные стороны диаметром 24 мм, и горизонтальные стороны прямоугольного сечения высотой 33 мм, и шириной 13 мм. Горизонтальными сторонами рамки размещаются в выемках головок валиков), комбинированных валиков (5)(каждый валик имеет прямоугольную головку толщиной 23 мм, стержневую и резьбовую части. Валик вставляют до упора головки и с другой стороны на выступающую часть надевают шайбу – опору и закрепляют ее корончатой гайкой и шплинтуют), серег (4)(штампованная, двухшарнирная с верхним фасонным отверстием, повернутым относительно нижнего под углом 90º), седлообразных валиков (3)(имеет рабочую поверхность в виде седла и двух головок цилиндрической формы) и гидравлических гасителей колебаний (10). На центральной балке расположены сменные наличники (скользуны) (3), боковые скользуны (4), пятник (5) и резинометаллический амортизатор (6).
Центральное подвешивание имеет предохранительное устройство (рис. 30), предназначенное для предотвращения падения узлов и деталей при обрыве подвески. Состоит из стальных скоб (2),закрепленных на кронштейнах рамы тележки, которые проходят под выступами поддона (1). Зазор должен быть 10-30 мм, регулируется деревянными накладками, уложенными на скобы.
Передача динамических ударных усилий, возникающих при движении вагона от контакта колес с ходовыми рельса (проезд стрелочного перевода) происходит по тем же самым элементам подвешивания, но только в обратной последовательности - от продольны
|
|
Типы сооружений для обработки осадков: Септиками называются сооружения, в которых одновременно происходят осветление сточной жидкости...
Состав сооружений: решетки и песколовки: Решетки – это первое устройство в схеме очистных сооружений. Они представляют...
Археология об основании Рима: Новые раскопки проясняют и такой острый дискуссионный вопрос, как дата самого возникновения Рима...
Механическое удерживание земляных масс: Механическое удерживание земляных масс на склоне обеспечивают контрфорсными сооружениями различных конструкций...
© cyberpedia.su 2017-2024 - Не является автором материалов. Исключительное право сохранено за автором текста.
Если вы не хотите, чтобы данный материал был у нас на сайте, перейдите по ссылке: Нарушение авторских прав. Мы поможем в написании вашей работы!