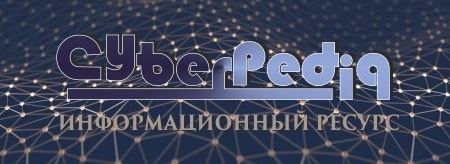
Историки об Елизавете Петровне: Елизавета попала между двумя встречными культурными течениями, воспитывалась среди новых европейских веяний и преданий...
Особенности сооружения опор в сложных условиях: Сооружение ВЛ в районах с суровыми климатическими и тяжелыми геологическими условиями...
Топ:
Основы обеспечения единства измерений: Обеспечение единства измерений - деятельность метрологических служб, направленная на достижение...
Генеалогическое древо Султанов Османской империи: Османские правители, вначале, будучи еще бейлербеями Анатолии, женились на дочерях византийских императоров...
Особенности труда и отдыха в условиях низких температур: К работам при низких температурах на открытом воздухе и в не отапливаемых помещениях допускаются лица не моложе 18 лет, прошедшие...
Интересное:
Финансовый рынок и его значение в управлении денежными потоками на современном этапе: любому предприятию для расширения производства и увеличения прибыли нужны...
Принципы управления денежными потоками: одним из методов контроля за состоянием денежной наличности является...
Распространение рака на другие отдаленные от желудка органы: Характерных симптомов рака желудка не существует. Выраженные симптомы появляются, когда опухоль...
Дисциплины:
![]() |
![]() |
5.00
из
|
Заказать работу |
|
|
Необходимым условием обеспечения стабильности технологического процесса измельчения является оптимальное наполнение бункеров мелкодробленой руды КПАК, которое должно составлять не менее 30% от объёма бункеров работающих мельниц.
Из бункера руда разгружается через челюстные затворы на реверсивные конвейеры и далее перегружается на сборные конвейеры, подающие руду в мельницы МШР 4,5х5,0
Таблица 2 - Характеристики конвейеров транспортировки руды КПАК
Позиция | Произво-дительность, т/ч | Ширина ленты, мм | Скорость ленты, м/с | Длина, м | Угол, град | Мощность, кВт | Лента | Высота подъема, м |
Б8.1÷Б8.2; Б9.1÷Б9.2; Б10.1÷Б10.2 | 300 | 1000 | 2 | 15 | 0 | 37 | EP300X4 | 0 |
Б11÷Б14 | 300 | 1000 | 2 | 29,16 | 16 | 37 | EP300X4 | 7 |
Измельчение осуществляется в четырех мельницах МШР 4,5х5,0 (№1÷№4 - поз. М1.1÷М4.1), работающих в замкнутом цикле с грохотами
Рисунок 1.2 - Схема цепи аппаратов измельчения руды в КПАК
Так как аппаратурно-технологические схемы измельчения для мельниц №1÷№4 по комплектации и компоновке оборудования принципиально не отличаются, ниже приводится описание только для одной мельницы – №1.
Дробленая руда, содержащая не более 17% материала крупностью более 18 мм, с помощью течки и улиткового питателя подается в шаровую мельницу МШР 4,5х5,0. Производительность мельницы по исходному питанию зависит от состава перерабатываемой руды и колеблется в диапазоне от 180 до 240 тонн в час.
Верхняя часть улиткового питателя мельницы закрыта кожухом, установленным на опорной раме.
Для поддержания оптимальной плотности пульпы в мельницу подается смешанная вода. Предусмотрена подача в измельчение раствора жидкого стекла. Также в мельницу возвращается надрешетный продукт грохотов, работающих совместно с данной мельницей.
|
Измельчающей средой в мельнице являются шары, коэффициент объемного заполнения ими мельницы 47-48 %. Применяются стальные помольные шары диаметром 100 мм и 80 мм. Шаровая загрузка разделяется на первоначальную (после капитального ремонта) и компенсационную, зависящую от количества переработанной руды, износа шаров и футеровки мельницы.
Догруз шаров в мельницы с целью компенсации их износа производится по показаниям датчика активной мощности электропривода мельницы. В случае невозможности корректно оценить дельту мощности необходимое количество шаров рассчитывается по утвержденной плановой норме расхода шаров на одну тонну перерабатываемой руды.
Футеровка шаровых мельниц - плиточная, по профилю - волнистая.
Измельчение руды ведётся до крупности 26-39% класса +0,16 мм.
В КПАК АНОФ-2 действует автоматизированная система АСУТП МФО КПАК, состоящая из трех уровней комплекса технических средств (КПТС):
нижний уровень – измерительный датчики/первичные преобразователи, вторичные/нормирующие преобразователи, линии связи/контрольные кабели;
средний уровень – микропроцессорные контроллеры со специализированным программным обеспечением, осуществляющий функции сбора и обработки информации, регулирования технологического процесса, противоаварийной автоматической защиты, дистанционного пуска/остановки;
верхний уровень – автоматизированные рабочие места (АРМ) оператора, отображающие информацию о процессе в реальном времени, оповещающих о срабатывании сигнализации и аварийных ситуациях; база данных тревог и сообщений, позволяющая производить анализ пусков/остановок оборудования, раз-вития аварийных ситуаций; архив данных о состоянии технологического процесса.
Имеется непрерывно действующая защита от перегруза, кратковременно снимающая часть нагрузки.
Основное технологическое оборудование снабжено системами защиты (согласно паспорту) - по превышению температуры отдельных частей оборудования, падению давления и/или отсутствию масла.
|
При остановке основного оборудования по возникновению тревожных ситуаций, нарушению параметров технологического процесса или работы оборудования включается звуковая и световая сигнализация.
Блокировки оборудования технологических цепочек процесса измельчения:
по остановке оборудования;
по несоблюдению порядка запуска оборудования.
Флотация
Питанием апатитовой флотации является пульпа измельченной апатит-нефелиновой руды с содержанием P2O5 более 2%.
Апатитовая флотация включает (рисунок 4.3, 4.4, таблица 4.9): контактирование, основную и контрольную флотацию, а также перечистную флотацию.
Пульпа (исходное питание и промежуточный продукт флотации) поступают в трехструйный пульподелитель и далее распределяются по трем ниткам рудной флотации. Каждая нитка флотации включат: контактный чан, две двухкамерные флотационные машины "Outocumpu" OK-38-2U задействованные в основной флотации и одну двухкамерную флотационную машину "Outocumpu" OK-38-2U на контрольной флотации.
Рисунок 1.3 - Схема цепи аппаратов рудного цикла флотации в КПАК
Камерный продукт контрольной флотации является хвостами апатитовой флотации и самотеком, по хвостовому коллектору, удаляется из КПАК.
Пенный продукт основной флотации самотеком поступает в зумпф питания колонных флотационных машин.
С помощью насосов VS250 L150 пульпа поступает в четырехструйный пульподелитель и далее распределяется по двум колонным флотационным машинам KYZ4680. Два выхода четырехструйного пульподелителя питания второй группы колонных флотационных машин заглушены.
Пенный продукт колонных флотационных машин, являющийся флотационным апатитовым концентратом, самотеком транспортируется до зумпфа апатитового концентрата и далее, с помощью насосов центробежных ГрАК 350/40 перекачивается на сгущение. В работе могут находиться от одного до трех насосов. Для стабилизации объемов перекачиваемого концентрата предусмотрена подача в зумпф дренажей и переливов с фильтрации. Подача дренажей и переливов выполняется по мере необходимости по двум трубопроводам.
1.6 Обезвоживание
Обезвоживание апатитового концентрата включает три стадии:
|
1. Сгущение флотационного апатитового концентрата в радиальных сгустителях.
2. Фильтрация сгущенного апатитового концентрата (песков) с получением кека.
3. Сушка кека.
Сгущение
Пульпа флотационного концентрата из КПАК насосами подается в делительную коробку, расположенную в корпусе сгустителей. Также в делительную коробку поступает от 0 до 100% дренажей и фильтратов из фильтровально-сушильного пылеулавливающего отделения (ФСПО-2). Делительная коробка оснащена клапанами с ручным приводом. Из делительной коробки пульпа распределяется самотеком по двум сгустителям Ц-30ЭП-У3. В сгустители предусмотрена подача раствора флокулянта. С этой целью задействуется станция приготовления раствора флокулянта. Пески сгустителей, с помощью насосов ГрАК 350/40 направляются в центральный пульподелитель ФСПО-2 на фильтрацию. Приводы насосов оснащены частотными преобразователями. С каждым сгустителем одновременно работает один насос для перекачивания песков, второй насос является резервным. Слив сгустителя самотеком поступает в зумпф сбора сливов, откуда насосами ГрАК 350/40 подается в хвостовой коллектор или направляется в КПАК для снижения плотности хвостов флотации. Зумпф оснащен дискретным уровнемером, коробка делительная – датчиком предельного верхнего уровня. На линиях подачи песков сгустителя устанавливается расходомер, плотномер и датчик давления.
Для ускорения процесса осаждения и снижения потерь апатитового концентрата предусматривается подача в сгустители раствора флокулянта. Для этого задействуется станция приготовления раствора флокулянта, которая расположена в одном корпусе со сгустителями.
Дренажи корпуса сгущения собираются в зумпфы и, с помощью двух дренажных вертикальных насосов ПРВП 63/22,5, направляются в хвостовой коллектор или в делительную коробку питания сгустителей. Переключение потоков дренажей в хвостовой коллектор либо в делительную коробку осуществляется при помощи шланговых задвижек с ручным приводом. В приямках с дренажными насосами устанавливаются дискретные датчики уровня.
1.4 Схема цепи аппаратов корпуса сгустителей
|
Фильтрация
Из корпуса сгустителей сгущенный апатитовый концентрат (пески сгустителей) перекачивается в питание трехструйного центрального пульподелителя ФСПО-2. С помощью центрального пульподелителя материл по самотечным трубопроводам направляется на одну или две секции фильтрации и далее, с помощью пятиструйных секционных пульподелителей поступает в вакуум-фильтры дисковые ДОО-63-2,5. Все секции фильтрации имеют идентичную схему и набор основного технологического оборудования. Кек с фильтров выгружается на ленточные конвейеры (по одному конвейеру на секцию, ширина ленты – 1000 мм) и далее транспортируется на сушку, выполняемую в сушильных барабанах (по одному барабану на секцию фильтрации).
На каждой секции фильтрации фильтры разбиты на две группы, состоящие из, соответственно, двух и трех фильтров. Каждая группа фильтров обладает раздельной цепочкой оборудования отвода воздуха и фильтрата от вакуумных фильтров и отделения воздуха от фильтрата. Схема отделения фильтрата от воздуха для каждой группы фильтров идентична. Основное количество фильтрата, поступающего из вакуум-фильтров, отделяется от воздуха в вакуумресивере. Далее воздух проходит через вакуум-ловушку, жидкость, из которой удаляется через гидрозатвор. Из вакуум-ловушек воздух собирается в вакуум-коллекторе (общий для секций фильтрации) и поступает в вакуумнасосную №2. Фильтраты из вакуум-ресивера, с помощью насосов ФН1÷ФН8 (по два насоса на один вакуум-ресивер), перекачиваются в зумпфы НОВ 1, 2 или направляются в зумпфы дренажей №1 и №2.
В зумпф дренажей №1 поступает фильтрат, перекачиваемый насосами ФН1÷ФН7, и дренаж погрузки. В зумпф дренажей №2 поступает перекачиваемый насосами ФН8 фильтрат. На каждом дренажном зумпфе установлено по два насоса – ДН1÷ДН2 на дренажном зумпфе №1 и ДН3÷ДН4 на дренажном зумпфе №2. Насосами ДН1÷ДН4 дренажи и фильтраты направляются в зумпф НОВ 1,2 или в хвосты. Переключение осуществляется с помощью задвижек. Дренажи, направляемые в хвосты, объединяются в сборном баке диаметром 1020 мм и далее удаляются из цеха по трубопроводу.
Переливы секционных пульподелителей и переливы с вакуум-фильтров дисковых самотеком поступают в коробки сбора переливов (по одной коробки на секцию) и далее - в зумпф НОВ 1, 2, либо в зумпф НОВ 3, 4. В зумпф НОВ 3, 4 также поступают переливы центрального пульподелителя.
Из зумпфа НОВ 1, 2, с помощью насосов ГРаК 350/40 (НОВ1 и НОВ2), фильтрат и переливы подаются по галерее №61 в делительную коробку питания сгустителей или, по галерее №60, в зумпф апатитового концентрата. Переключение потоков выполняется с помощью запорной арматуры. Из зумпфа НОВ 3, 4, с помощью насосов ГРаК 350/40, фильтрат и переливы подаются в делительную коробку питания сгустителей.
|
Теплая вода, образующаяся после мокрой очистки газов, собирается в зумпфах №1 НТВ и №2 НТВ и далее, с помощью насосов НТВ10÷НТВ12, перекачивается в КПАК для формирования смешанной воды (с целью повешения ее температуры).
1.5 Схема цепи аппаратов фильтрации в ФСПО-2
Сушка
Сушка апатитового концентрата включает три идентичные секции.
Кек с секций фильтрации транспортируется в сушильные барабаны СБ-3,5-27-ЛС. Совместно с каждой секцией фильтрации задействуется по одному сушильному барабану.
Влажность кека после фильтрации составляет 11,0-11,3%. В качестве сушильного агента применяются горячие газы, поступающие прямоточно из топки, работающей на жидком топливе (мазуте).
Температура в топке поддерживается в пределах 700-1150С, на входе в сушильный барабан - не менее 600С, разряжение в топке 6-10 мм рт. ст. В целях обеспечения нормальных условий работы газопылеулавливающего оборудования температура газов, отходящих от сушильных барабанов, должна быть 100-160С.
После сушки готовый концентрат, через разгрузочную камеру сушильного барабана, поступает на ленточные сборные конвейера (В=1000 мм).
Газоочистка
Топочные газы, выходящие из сушильного барабана, перед выбросом в атмосферу проходят три стадии очистки от пыли. Первая стадия очистки выполняется в циклоне. Вторая стадия очистки топочного газа производится с помощью электрофильтра. Твердый материал из циклона и фильтра, через шлюзовые питатели, выгружается на сборный конвейер. Третья стадия очистки – мокрая. После электрофильтра установлены дымососы ДРА-150-0111.15-4К нагнетающие топочный газ в трубу Вентури и далее в скруббер. В трубе Вентури и в скруббере газ орошается раствором NaOH или оборотной водой. Сток со скруббера поступает в систему оборотного водоснабжения фабрики, а очищенные газы в атмосферу.
1.6 Схема цепи аппаратов сушки, пылеулавливание и очистка газов в
Погрузка
Готовый апатитовый концентрат из сушильных барабанов, батарейных циклонов и электрофильтров поступает на сборные ленточные конвейера КС №№ 15, 16, 17 с шириной ленты 1200 мм и транспортируется в силосный склад готовой продукции. Для каждого сушильного барабана установлены секции из трёх силосных банок диаметром 11300 мм и высотой 21300 мм. Вместимость каждой банки (ёмкости) по геометрическим размерам – 3350 тонн концентрата, фактически – 2800 тонн (подвижного концентрата). Загрузка секций из трёх силосных банок производится с помощью устройств переключения потоков и реверсивных конвейеров.
Апатитовый концентрат складируется в банки сушильных барабанов №№ 15, 16, 17.
Из банок силосного склада, через выпускные течки (по две на каждой банке), апатитовый концентрат самотёком через секторные затворы с пневматическим приводом подается на ленточные конвейеры КЛ №№ 1н, 2н, 3н (В-1400)
Далее апатитовый концентрат транспортируется, с помощью конвейеров 4н и 5н (В-1600), в погрузочный комплекс №3. Питатели силосов и конвейеры погрузочных линий включаются и отключаются дистанционно из операторного пункта (ОП-3). При пуске конвейерных линий включается звуковая и световая сигнализация на мнемосхеме операторного пульта.
Погрузочный комплекс №3 включает два отделения (южное и северное), оснащенные бункерами ёмкостью по 875 тонн. Из бункера, через четыре течки (d=425 мм), на которых установлены секторные затворы с ручным управлением (угол наклона течки по отношению к бункеру составляет 30°), производится погрузка концентрата в крытые вагоны (хопперы для цемента, зерна, минеральных удобрений, апатитового концентрата). Для откатки и подкатки вагонов используются лебёдки марки 100 ЛС-2С с тяговым усилием 8 тонн, что даёт возможность производить маневровые работы с пятнадцатью гружеными вагонами.
1.7 Схема цепи аппаратов погрузки апатитового концентрата
2. Индивидуальное задание
1. Перечислите технологическое оборудование участка, приведите его технические характеристики
2. Создайте презентацию с помощью программы MS PowerPoint, в которой отразите устройство, принцип действия ленточного конвейера с разгрузочной тележкой (например №№ 5,6,7).
3. Перечислите параметры контроля процесса измельчения и опишите принципы его регулирования.
Тех. Оборудование участка
Схема цепи аппаратов измельчения руды в КПАК
Табл. Оборудование измельчения КПАК
Поз. | Наименование | Кол. |
М1.1, М2.1, М3.1, М4.1 | Мельница МШР 4,5х5,0 | 4 |
М1.1.1, М2.1.1 | Течка для загрузки руды СПБ.770.05.00.00.00 | 2 |
М3.1.1, М4.1.1 | Течка для загрузки руды СПБ.770.06.00.00.00 | 2 |
М1.1.2, М2.1.2, М3.1.2, М4.1.2 | Воронка загрузочная для шаров с опорной рамой СПБ.181.08.00.00.00 | 4 |
М1.1.3, М2.1.3, М3.1.3, М3.1.3 | Опорная рама кожуха улиткового питателя СПБ.691.03.00.00.00 | 4 |
М1.1.4, М2.1.4 | Узел загрузки мельницы СПБ.822.02.00.00.00 | 2 |
М3.1.4, М4.1.4 | Узел загрузки мельницы СПБ.822.03.00.00.00 | 2 |
М1.1.5, М2.1.5, М3.1.5, М3.1.5 | Электродвигатель СДС-19-56-40 УХЛ4 | 4 |
М1.1.6, М2.1.6 | Вспомогательный привод N=30 кВт | 2 |
М3.1.6, М4.1.6 | Вспомогательный привод N=30 кВт | 2 |
М1.1.7, М2.1.7, М3.1.7, М4.1.7 | Бутара скрапоуловитель | 4 |
М1.1.8, М2.1.8, М3.1.8, М4.1.8 | Укрытие бутары с желобом СПБ.821.02.00.00.00 | 4 |
М1.1.9, М2.1.9, М3.1.9, М4.1.9 | Маслостанция SKF FL1000 | 4 |
М1.2.1, М2.2.1, М3.2.1, М4.2.1 | Зумпф слива мельниц | |
М1.2.3, М2.2.3, М3.2.3, М4.2.3 | Насос центробежный шламовый HM 250 N=250 кВт | 4 |
М1.3, М2.3, М3.3, М4.3 | Пульподелитель шестиструйный СПБ.641.02.00.00.00 | 4 |
М1.4.1÷М1.4.6, М2.4.1÷М2.4.6, М3.4.1÷М3.4.6, М4.4.1÷М4.4.6 | Пятипоточный пульподелитель 8FK0502 | 24 |
М1.5.1÷М1.5.6, М2.5.1÷М2.5.6, М3.5.1÷М3.5.6, М4.5.1÷М4.5.6 | Грохот вибрационный пятидечный D5Z101402-2 | 24 |
М1.6.1÷М1.6.2, М2.6.1÷М2.6.2, М3.6.1÷М3.6.2, М4.6.1÷М4.6.2 | Желоб песковый СПБ.300.02.00.00.00 | 8 |
М1.7, М2.7, М3.7, М4.7 | Коробка сборная шестиходовая | 4 |
М1.8.1 | Зумпф питания флотации | 1 |
М2.8.1 | Зумпф питания флотации | 1 |
М1.8.2, М2.8.2 | Коробка распределительная с пробоотборником СПБ.411.22.00.00.00 | 2 |
М1.8.3, М1.8.4, М2.8.3, М2.8.4 | Насос центробежный шламовый ГРАТ 1400/40 N=500 кВт | 4 |
М1.9 | Кран-балка грузоподъемностью 5 т, Нпод.= 27 м | 1 |
М1.10 | Кран-балка грузоподъемностью 5 т, Нпод.= 8 м | 1 |
М1.11 | Кран-балка грузоподъемностью 80 т, Нпод.= 9 м | 1 |
М1.12 | Таль электрическая г/п 6,3 т, Нпод.= 18 м | 1 |
Дробленая руда, содержащая не более 17% материала крупностью более 18 мм, с помощью течки и улиткового питателя подается в шаровую мельницуМШР 4,5х5,0. Производительность мельницы по исходному питанию зависит от состава перерабатываемой руды и колеблется в диапазоне от 180 до 240 тонн в час.
Таблица - Технические характеристики мельницы МШР 4,5х5,0
Наименование параметра | Значение |
Тип мельниц | Мельница шаровая МШР 4,5х5,0 |
Размеры, мм | D=4500, L=5000 |
Частота вращения, об./мин. | 16,7 |
Рабочий объём мельницы, м3 | 71 |
Шаровая загрузка, тонн | 157 |
Производительность мельницы по сырой руде, т/час | 180-240 |
Электродвигатель | СДС-19-56-40 УХЛ4 |
Мощность электродвигателя, кВт | 2500 |
Напряжение, В | 6000 |
1 - цилиндрический барабан
2,3 - торцевые крышки
4,5 - пустотелыми цапфами
6,7 – подшипники
8 - зубчатый венец
9 – улитковый питатель
Футеровка шаровых мельниц - плиточная, по профилю - волнистая.
Догруз шаров в мельницы с целью компенсации их износа производится по показаниям датчика активной мощности электропривода мельницы. В случае невозможности корректно оценить дельту мощности необходимое количество шаров рассчитывается по утвержденной плановой норме расхода шаров на одну тонну перерабатываемой руды.
Табл. Состав первоначальной шаровой загрузки и догрузки шаров в мельницу МШР 4,5х5,0
Начальная шаровая загрузка, % | Догрузка шаров на износ, % | |||
Сортированные шары, кл. -100+45 мм, % | Новые шары - 5-10 %, в т.ч.: | |||
Æ100 мм | Æ80 мм | Æ100 мм | Æ80 мм | |
90-95 | 30 | 70 | 55 | 45 |
Схема. Грохот вибрационный пятидечный
Из зумпфа насосом центробежным Metso HM250 пульпа по напорному трубопроводу подается в шестиструйный пульподелитель. На трубопроводе установлен расходомер и плотномер. Из пульподелителя материал самотеком распределяется по шести пятиструйным пульподелителям и далее поступает на деки грохотов. Грохота оснащены пятью деками, каждая дека запитывается отдельно через пятиструйный пульподелитель. На грохота подается смешанная вода.
Табл. Характеристики конвейеров транспортировки руды КПАК
Позиция | Произво-дительность, т/ч | Ширина ленты, мм | Скорость ленты, м/с | Длина, м | Угол, град | Мощность, кВт | Лента | Высота подъема, м |
Б8.1÷Б8.2; Б9.1÷Б9.2; Б10.1÷Б10.2 | 300 | 1000 | 2 | 15 | 0 | 37 | EP300X4 | 0 |
Б11÷Б14 | 300 | 1000 | 2 | 29,16 | 16 | 37 | EP300X4 | 7 |
Из бункера руда разгружается через челюстные затворы на реверсивные конвейеры и далее перегружается на сборные конвейеры, подающие руду в мельницы МШР 4,5х5,0.
|
|
Индивидуальные очистные сооружения: К классу индивидуальных очистных сооружений относят сооружения, пропускная способность которых...
Состав сооружений: решетки и песколовки: Решетки – это первое устройство в схеме очистных сооружений. Они представляют...
Эмиссия газов от очистных сооружений канализации: В последние годы внимание мирового сообщества сосредоточено на экологических проблемах...
Автоматическое растормаживание колес: Тормозные устройства колес предназначены для уменьшения длины пробега и улучшения маневрирования ВС при...
© cyberpedia.su 2017-2024 - Не является автором материалов. Исключительное право сохранено за автором текста.
Если вы не хотите, чтобы данный материал был у нас на сайте, перейдите по ссылке: Нарушение авторских прав. Мы поможем в написании вашей работы!