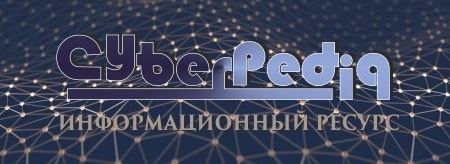
Типы оградительных сооружений в морском порту: По расположению оградительных сооружений в плане различают волноломы, обе оконечности...
Своеобразие русской архитектуры: Основной материал – дерево – быстрота постройки, но недолговечность и необходимость деления...
Топ:
Теоретическая значимость работы: Описание теоретической значимости (ценности) результатов исследования должно присутствовать во введении...
Комплексной системы оценки состояния охраны труда на производственном объекте (КСОТ-П): Цели и задачи Комплексной системы оценки состояния охраны труда и определению факторов рисков по охране труда...
Интересное:
Национальное богатство страны и его составляющие: для оценки элементов национального богатства используются...
Искусственное повышение поверхности территории: Варианты искусственного повышения поверхности территории необходимо выбирать на основе анализа следующих характеристик защищаемой территории...
Влияние предпринимательской среды на эффективное функционирование предприятия: Предпринимательская среда – это совокупность внешних и внутренних факторов, оказывающих влияние на функционирование фирмы...
Дисциплины:
![]() |
![]() |
5.00
из
|
Заказать работу |
|
|
Для очистки поверхности алюминиевой сварочной проволоки не-обходимо производить ее химическую обработку: обезжиривание, травление в 15 %-ном растворе едкого натрия технического в течение 5-10 минут при 1=60-70 °С, промывание в воде, сушку, дегазацию (прокалка при t = 300 °С в течение 10-30 минут на воздухе или в течение 5 часов в вакууме при 0,13 Па).
Окисная пленка на поверхности алюминия и его сплавов затрудняет процесс сварки. Обладая высокой температурой плавления (2050 ºС) она не растворяется в жидком металле в процессе сварки. Попадая в ванну, она затрудняет сплавление между собой частиц металла и ухудшает формирование шва.
Важной характеристикой окисной пленки алюминия является ее способность адсорбировать газы, в особенности водяной пар. Поэтому, окисная пленка является источником газов, растворяющихся в металле, и косвенной причиной возникновения в нем несплошностей различного рода.
Естественная защитная пленка имеет значительную толщину и ее удаление в процессе сварки весьма затруднительно. Поэтому поверхность соединяемых деталей и проволоки очищают от слоя окиси непосредственно перед сваркой и создают на ней искусственный слой окиси, который сохраняется достаточно тонким в течении 8-16 ч. Полученный тонкий слой окиси алюминия сравнительно легко удаляется электрической дугой или с помощью флюса во время сварки.
Обработка поверхности свариваемых деталей и проволоки производится следующим образом. Сначала производится механическая зачистка с помощью металлических щеток. Затем свариваемые детали и проволока обезжириваются в водном растворе следующего состава: 40-50 г/л тринатрийфосфата (Na3PO4, 12H2O), 35-50 г/л кальцинированной соды (Na2CO3) и 25-30 г/л жидкого стекла (Na2SiO3). Время обезжиривания примерно 5 минут, температура раствора 60-700 0С. Далее свариваемые детали и проволоку подвергают травлению в течении 1-3 мин в 5% растворе щелочи NaOH или KOH. После этого остатки щелочи и продукты реакции смывают сначала горячей, а потом холодной водой. После промывки детали пассивируют 20% азотной кислотой (HNO3), нагретой до температуры 600 0С. При этом детали покрываются новым тонким слоем окисной пленки. Извлеченные из азотной кислоты детали промывают холодной, затем горячей водой и сушат.
|
Так как в атмосферных условиях толщина образованной пленки, хотя и более медленно, но все же увеличивается, подготовленные к сварке детали необходимо сварить в течение 24 часов, а сварочную проволоку использовать в течение 8 часов. Различие в сроке хранения подготовленных к сварке деталей и проволоки обусловлено тем, что непосредственно перед сваркой соединяемые кромки деталей дополнительно очищают от окисных пленок механическим путем – проволочной щеткой, а затем шабером. Образовавшаяся после механической зачистки тончайшая пленка окиси легко удаляется сварочной дугой, горящей в среде инертных газов. Весьма эффективно происходит удаление окиси с поверхности металла, имеющего отрицательный потенциал. Присутствующие в дуге положительные ионы инертных газов разгоняются катодным напряжением и ударяют в поверхностный слой окисной пленки. Процесс обработки свариваемого металла положительными ионами называют катодным распылением. Результаты этого процесса остаются в виде беловатых полос по сторонам шва.
Допускаются две подварки, при этом предел прочности снижается на 10-20%.
Сварные соединения имеют предел прочности 36-38 кгс/мм2 и угол изгиба 50-600 при толщине 1-3 мм. С увеличением толщины показатели прочности и пластичности сварных соединений снижаются.
Оптимальными значениями прочности обладают сварные соединения с коэффициентом формы шва, равным 1. Предел прочности сварных соединений при комнатной температуре составляет 80% от предела прочности основного материала.
|
Кромки под сварку подготавливают строганием или фрезерованием. В процессе сборки смещение кромок и зазор между ними не должен превышать 10% от толщины свариваемого металла, но не более 2 мм [1].
При понижении температуры в цехе увеличивается относительная влажность воздуха и образуется конденсат на поверхности свариваемого материала, что ведет к появлению пор в металле шва. Поэтому сборку и сварку изделий из алюминия и его сплавов допускается выполнять в помещениях с температурой не ниже +10 0С при отсутствии сквозняков и потоков воздуха, нарушающих защиту дуги. При температуре воздуха в помещении ниже +10 0С кромки свариваемого материала необходимо подогревать до температуры 80-100 0С. Если температура ниже +5 0С, сваривать алюминий и его сплавы не разрешается.
Сборку конструкций по возможности следует выполнять без прихваток в жестких кондукторах и других приспособлениях [1].
Расчет режимов сварки стыковых швов.
Выбирается форма и конструктивные элементы подготовки кромок под сварку, размеры сварных швов.
Рисунок.22 - Конструктивное исполнение сварной кромки и сварного шва по ГОСТ 14771-76
На основе заданного значения катета шва определяем площадь поперечного сечения металла шва:
, (1)
где - коэффициент увеличения, учитывающий наличие зазора и выпуклости шва,
- катет шва (принимаем k = 5 мм).
Выбираем диаметр электродной проволоки:
Определяем силу тока:
, (2)
где - плотность тока (принимаем
).
Принимаем силу сварочного тока
Определяем напряжение на дуге:
(3)
Определяем скорость сварки:
, (4)
где - коэффициент наплавки, принимаем
Определяем погонную энергию сварки:
, (5)
где - эффективный КПД дуги, для сварки в СО2
;
- скорость сварки в см/с;
Определяем скорость подачи электродной проволоки:
, (6)
где - скорость сварки, м/час;
- площадь наплавки, мм2;
- площадь поперечного сечения электрода, мм2.
|
Расчет размеров угловых сварных швов:
Определяют глубину провара, при сварке СО2:
При сварке постоянным током обратной полярности во всем диапазоне плотность тока =0,92.
Определяют ширину шва:
(7)
Оценивается высота выпуклости шва:
; (8)
Определяется общая высота шва:
(9)
|
|
Автоматическое растормаживание колес: Тормозные устройства колес предназначены для уменьшения длины пробега и улучшения маневрирования ВС при...
История создания датчика движения: Первый прибор для обнаружения движения был изобретен немецким физиком Генрихом Герцем...
Археология об основании Рима: Новые раскопки проясняют и такой острый дискуссионный вопрос, как дата самого возникновения Рима...
Двойное оплодотворение у цветковых растений: Оплодотворение - это процесс слияния мужской и женской половых клеток с образованием зиготы...
© cyberpedia.su 2017-2024 - Не является автором материалов. Исключительное право сохранено за автором текста.
Если вы не хотите, чтобы данный материал был у нас на сайте, перейдите по ссылке: Нарушение авторских прав. Мы поможем в написании вашей работы!