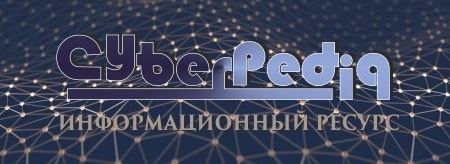
Архитектура электронного правительства: Единая архитектура – это методологический подход при создании системы управления государства, который строится...
Общие условия выбора системы дренажа: Система дренажа выбирается в зависимости от характера защищаемого...
Топ:
Устройство и оснащение процедурного кабинета: Решающая роль в обеспечении правильного лечения пациентов отводится процедурной медсестре...
Интересное:
Аура как энергетическое поле: многослойную ауру человека можно представить себе подобным...
Средства для ингаляционного наркоза: Наркоз наступает в результате вдыхания (ингаляции) средств, которое осуществляют или с помощью маски...
Искусственное повышение поверхности территории: Варианты искусственного повышения поверхности территории необходимо выбирать на основе анализа следующих характеристик защищаемой территории...
Дисциплины:
![]() |
![]() |
5.00
из
|
Заказать работу |
|
|
Погрешности обработки, вызываемые неточностью и износом инструмента.
Неточность мерного инструмента (свёрла, метчики, развертки, фасонные резцы, плашки, протяжки, зенкеры, концевые пазовые фрезы, модульные фрезы) непосредственно передаётся на обрабатываемые заготовки, создавая систематические погрешности, хотя, как правило, они незначительны.
Наиболее существенную переменную систематическую погрешность вызывает износ инструмента по задней поверхности при работе на настроенных станках по методу автоматического получения размеров. В процессе работы резца его вершина постепенно удаляется от оси вращения заготовки в связи с радиальным износом, что ведет к увеличению диаметра обточки. Зависимость размерного износа резца от пути резания показана на рис.10.
![]() |
Рис.10. Зависимость размерного износа резца от пути резания.
впадины на режущей кромке. Этот
|
На втором участке происходит нормальный износ инструмента, прямо пропорциональный пути резания. Угол наклона прямой износа характеризует интенсивность размерного изнашивания инструмента. Длина пути резания на этом участке составляет 30000...50000 м.
Третий участок характеризует критический износ инструмента, когда в любой момент возможно его разрушение. Работа инструмента при таком износе недопустима.
Износ режущего инструмента зависит от нескольких причин: жесткости технологической системы, режущего и обрабатываемого материалов и режимов резания.
|
С повышением жесткости технологической системы или с повышением демпфирования в ней, вибрации снижаются, и износ режущего инструмента значительно снижается. Так, например, при выполнении державок резцов из высоконаполненного композиционного материала на полимерной основе (синтеграна), обладающего высокими демпфирующими способностями, износ резцов снижается в 1,4...1,7 раза.
Износ инструмента зависит также и от условий его работы. Так при наружном точении износ значительно ниже, чем при растачивании, которое осуществляется в худших условиях (затруднен отвод стружки, подвод охлаждающей жидкости, большой вылет инструмента и т.д.).
При работе резцами, фрезами, шлифовальными кругами и т.д. возможна компенсация размерного износа инструмента путём поднастройки станка, но погрешности формы остаются.
ТОЧНОСТЬ ОБРАБОТКИ И МЕТОДЫ ЕЁ ДОСТИЖЕНИЯ
Под точностью реально существующей детали понимают степень её приближения по размерам, геометрической форме, правильности взаимного расположения обрабатываемых поверхностей и их шероховатости к аналогичным параметрам, заданным по чертежу.
От точности изготовления изделий зависит долговечность и надёжность их эксплуатации. Используемые в настоящее время мощные и высокоскоростные машины не могут функционировать, если они не обладают достаточной точностью, поскольку в местах сопряжения различных деталей будут иметь место зазоры и неправильное взаимодействие поверхностей, что вызовет дополнительные деформации, вибрации и преждевременный износ. Поэтому требования к точности изготовления деталей в машиностроении постоянно ужесточаются. В зависимости от назначения того или иного изделия допуски на детали могут изменяться от сотых долей миллиметра до десятых долей микрометра. Чем выше требования к точности изготовления деталей, тем сложнее технологический процесс механической обработки, выше его трудоёмкость и стоимость, но при этом обеспечивается взаимозаменяемость при сборке, появляются предпосылки её автоматизации, а также облегчается проведение ремонта машин в условиях их эксплуатации.
|
При разработке технологического процесса технолог должен обеспечить заданную по чертежу точность изготовления отдельных деталей при высокой производительности и экономичности их изготовления, выбрать необходимые измерительные инструменты для контроля точности обработки и сборки, назначить межоперационные технологические допуски и размеры и обеспечить возможность их выполнения.
В машиностроении существуют два метода достижения заданной точности обработки: метод "пробных ходов и промеров" и метод автоматического получения размеров на настроенных станках.
Сущность первого метода заключается в том, что к обрабатываемой поверхности заготовки рабочий подводит инструмент и с короткого участка снимает стружку. По еле этого станок выключают и производят замер частично обработанной поверхности. Определяется величина отклонения размера от заданного чертежом и положение инструмента корректируется путём отсчета по лимбу станка. Затем снова осуществляют пробную обработку участка заготовки, производят замер и корректировку инструмента до тех пор, пока не будет получен необходимый размер, заданный чертежом. После этого производят обработку заготовки по всей её длине. При обработке следующей заготовки весь процесс настройки инструмента повторяют.
При использовании этого метода широко используется разметка, когда на поверхность заготовки наносятся контуры будущей детали, положения осевых- линий отверстий, а рабочий старается совместить положение и направление движения инструмента с линиями разметки, обеспечивая при этом заданную форму обрабатываемых поверхностей.
Метод пробных ходов и промеров имеет следующие достоинства:
- на неточном оборудовании существует возможность получения высокой точности обработки;
- при неточной заготовке путем правильного распределения припуска исключается появление брака;
- износ режущего инструмента не влияет на точность обрабатываемых поверхностей;
- отсутствует необходимость наличия сложных и дорогостоящих приспособлений.
|
Метод имеет и ряд серьёзных недостатков:
- низкая производительность из-за большого числа вспомогательных ходов;
- возможность появления брака по вине рабочего;
- высокая себестоимость обработки и трудоёмкость;
- зависимость достигаемой точности обработки от минимально возможной толщины снимаемой стружки на используемом станке (на токарном станке при работе обычным резцом минимальная толщина снимаемой стружки 0,02 мм - гарантировать получение размера с погрешностью меньше этой величины невозможно).
Метод пробных ходов и промеров используется в единичном, опытном и мелкосерийном производствах, при обработке деталей тяжёлого машиностроения, а также для получения годных деталей из бракованных заготовок. В крупносерийном производстве метод используется в шлифовании для компенсации износа шлифовального круга.
Метод автоматического получения размеров на настроенных станках заключается в том, что станок предварительно настраивается на определенный размер, и точность обработки достигается автоматически без участия рабочего. На настроенном станке обрабатывается вся партия заготовок без какой-либо корректировки положения инструмента.
Метод имеет следующие преимущества:
- повышается точность обработки, которая не зависит от минимально возможной толщины снимаемой стружки и квалификации рабочего;
- снижается величина брака;
- повышается производительность обработки за счет снижения потерь времени на вспомогательные движения и разметку;
- рабочие высокой квалификации заняты на ответственных операциях настройки станка; на самих же станках работают рабочие низкой квалификации;
- повышается экономичность производства.
Метод автоматического получения размеров используется в крупносерийном и массовом производстве, когда затраты на настройку станков окупаются большим количеством выпускаемой продукции.
Степени точности по ЕСДП называются квалитетами, которых установлено 19: 01, О, I, 2, 3, 4, 5, 6, 7, 8, 9, 10, II,-12, 13, 14, 15, 16, 17. Точность от квалитета 01 убывает к квалитету 17.
Каким бы методом не обрабатывались детали, их размеры и формы поверхностей не могут быть идеально точными, и будут отличаться между собой и от заданных по чертежу на величину погрешности, которая зависит от многих параметров.
Погрешность - это разница между реальным размером детали и заданным по чертежу.
Все погрешности, возникающие в процессе обработки изделий подразделяются на систематические и случайные. В общем виде погрешности обработки могут быть классифицированы следующим образом: Dd - погрешности размера; Dр - погрешности взаимного расположения поверхностей; Dф - погрешности формы поверхности; Dв - волнистость поверхности; Dш - шероховатость поверхности.
Рис. 8. Погрешности обработки
|
|
Папиллярные узоры пальцев рук - маркер спортивных способностей: дерматоглифические признаки формируются на 3-5 месяце беременности, не изменяются в течение жизни...
Организация стока поверхностных вод: Наибольшее количество влаги на земном шаре испаряется с поверхности морей и океанов (88‰)...
Автоматическое растормаживание колес: Тормозные устройства колес предназначены для уменьшения длины пробега и улучшения маневрирования ВС при...
Своеобразие русской архитектуры: Основной материал – дерево – быстрота постройки, но недолговечность и необходимость деления...
© cyberpedia.su 2017-2024 - Не является автором материалов. Исключительное право сохранено за автором текста.
Если вы не хотите, чтобы данный материал был у нас на сайте, перейдите по ссылке: Нарушение авторских прав. Мы поможем в написании вашей работы!