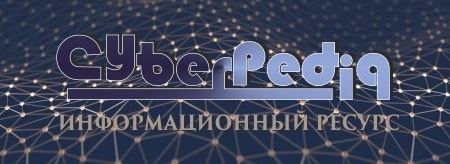
Организация стока поверхностных вод: Наибольшее количество влаги на земном шаре испаряется с поверхности морей и океанов (88‰)...
Состав сооружений: решетки и песколовки: Решетки – это первое устройство в схеме очистных сооружений. Они представляют...
Топ:
Характеристика АТП и сварочно-жестяницкого участка: Транспорт в настоящее время является одной из важнейших отраслей народного...
Методика измерений сопротивления растеканию тока анодного заземления: Анодный заземлитель (анод) – проводник, погруженный в электролитическую среду (грунт, раствор электролита) и подключенный к положительному...
Характеристика АТП и сварочно-жестяницкого участка: Транспорт в настоящее время является одной из важнейших отраслей народного хозяйства...
Интересное:
Мероприятия для защиты от морозного пучения грунтов: Инженерная защита от морозного (криогенного) пучения грунтов необходима для легких малоэтажных зданий и других сооружений...
Принципы управления денежными потоками: одним из методов контроля за состоянием денежной наличности является...
Национальное богатство страны и его составляющие: для оценки элементов национального богатства используются...
Дисциплины:
![]() |
![]() |
5.00
из
|
Заказать работу |
|
|
Автосцепное устройство полувагона. Четырехосные полувагоны оборудуются серийной автосцепкой СА-3 с поглощающим аппаратом Ш-1-ТМ с ходом 70 мм или аппаратом Ш-2-В с ходом 90 мм. Рассмотрим автосцепку СА-3.
Автосцепка СА-3 является тягово-ударной нежесткого типа.
Она состоит из корпуса 4 и деталей механизма сцепления: замка 5, замкодержателя 2, предохранителя 3, подъемника 6, валика подъемника 7.
Рисунок 1.7 - Автосцепка СА-3
Головная часть автосцепки (голова) переходит в удлиненный пустотелый хвостовик, в котором имеется отверстие 1 для соединения с тяговым хомутом.
Голова автосцепки имеет большой 10 и малый 9 зубья. В пространство между малым и большим зубьями, в так называемый зев автосцепки, выступают замок 5 и замкодержатель 2, взаимодействующие в сцепленном состоянии со смежной автосцепкой.
Большой зуб имеет три усиливающих ребра: верхнее, среднее и нижнее, плавно переходящие в хвостовик и соединенные между собой перемычкой.
Голова автосцепки заканчивается сзади упором 8, предназначенным для передачи в некоторых случаях жесткого удара на хребтовую балку через концевую балку рамы вагона и ударную розетку.
Очертание в плане малого 1 и большого 2 зубьев, а также выступающей в зев части замка 3 называется контуром зацепления автосцепки.
Для обеспечения взаимосцепляемости всех автосцепок СА-3 контур зацепления должен соответствовать ГОСТ 21447—75.
Поверхности контура зацепления корпуса в сцепленном состоянии взаимодействуют со смежной автосцепкой: при сжатии усилие воспринимается ударной 6 и боковой 7 поверхностями малого зуба, ударной стенкой 5 зева и боковой поверхностью 4 большого зуба, а при растяжении — тяговыми поверхностями 8 малого и 3 большого зубьев.
|
Тяговая, ударная и боковая поверхности малого зуба, а также тяговая поверхность большого зуба в средней части по высоте имеют вертикальную площадку длиной 160 мм (80 мм вверх и 80 мм вниз от продольной оси корпуса).
Эти поверхности выше и ниже вертикальной площадки скошены для улучшения условий работы сцепленных автосцепок, когда между их продольными осями в вертикальной плоскости возникает угол (при прохождении горба сортировочной горки).
Корпуса автосцепок ранних выпусков имеют сбоку со стороны малого зуба прилив 10 (ухо), на который в переходный период навешивали скобу винтовой упряжи смежного вагона во время маневровых работ, а также в передаточных поездах.
После перевода подвижного состава на автосцепку новые корпуса сначала изготовлялись с приливом вместо уха, а затем без прилива с утолщением стенки малого зуба.
У выпускаемых корпусов автосцепок высота малого зуба увеличена и его нижняя кромка 13 используется для приварки ограничителя вертикальных перемещений, необходимого для некоторых типов вагонов.
На корпусе со стороны малого зуба сделан прилив 9 с отверстиями для валика подъемника и запорного болта.
В ударной стенке 5 зева имеются два окна: большое 11 для выхода в зев замка и малое 12 для выхода лапы замкодержателя.
Расцепной привод, ударно-центрирующий прибор, упряжное устройство и опорные части.
Расцепной привод автосцепки СА-3, как и других распространенных конструкций автоматических сцепок, предназначен для расцепления автосцепок без захода человека между вагонами и для установки механизма в выключенное положение. Такой привод (рисунок 1.8) состоит из, кронштейна с полкой 2, державки 10 и цепи 14 для соединения рычага с валиком подъемника.
Расцепление автосцепок осуществляется поднятием рукоятки вверх для выведения рычага 3 из паза кронштейна, поворотом рычага против часовой стрелки и последующим восстановлением его исходного положения. В результате этого натягивается цепь 14, поворачивается валик подъемника, и расцепление автосцепок происходит, как описано выше.
|
Для установки механизма автосцепки в выключенное положение рукоятку рычага после поворота не возвращают в первоначальное положение, а располагают его плоской частью на полке 2 кронштейна.
Ударно-центрирующий прибор воспринимает непосредственно от корпуса автосцепки большие сжимающие усилия (вызывающие полное сжатие поглощающего аппарата и деформации упряжного устройства), а также возвращает в центральное положение отклоненный корпус. Прибор состоит из ударной розетки 9, прикрепленной к концевой балке рамы вагона, двух маятниковых подвесок 11, опирающихся на розетку, и центрирующей балки 12, опирающейся на подвески и поддерживающей корпус автосцепки, при высоком отклонении корпус 13 вместе с центрирующей балкой несколько поднимается вверх, а после прекращения действия боковой силы под воздействием собственного веса возвращается в исходное нижнее (центральное) положение.
Рисунок 1.8 - Автосцепное устройство грузового вагона
Большие вертикальные силы могут возникнуть в результате зависания одного вагона на другом при возможном заклинивании сцепленных автосцепок во время прохода горба сортировочной горки, особенно у вагонов с большой длиной консольной части рамы кузова. Опирание корпуса на пружины предотвращает такое заклинивание и позволяет значительно уменьшить эти силы, передаваемые от автосцепки на раму кузова вагона.
Для возвращения отклоненного корпуса автосцепки в центральное положение предусмотрены удлиненные маятниковые подвески 6.
Упряжное устройство передает продольные растягивающие и сжимающие усилия от корпуса 13 поглощающему аппарату 5. Оно состоит из клина 8, тягового хомута 6, болтов с гайками, запорными шайбами, планкой и шплинтами для крепления клина, а также упорной плиты 1.
Клин соединяет корпус автосцепки с тяговым хомутом и передает последнему растягивающее усилие. Имеющийся внизу заплечик предотвращает выжимание клина вверх. Для повышения прочности клинья, а также маятниковые подвески и упорные плиты в последние годы изготовляют из низколегированной стали марки 38ХС вместо ранее применявшейся стали марки Ст5.
|
Тяговый хомут предназначен для передачи растягивающего усилия поглощающему аппарату. Он представляет собой стальную отливку, в головной части которой имеются окно для клина и приливы с отверстиями для прохода болтов, поддерживающих клин. Головная часть тягового хомута соединена с его хвостовой частью верхней и нижней полосами. В модернизированном автосцепном устройстве эти полосы имеют увеличенное поперечное сечение, а вертикальные отверстия в головной части выполнены круглыми (для валика). Для размещения поглощающего аппарата увеличенной энергоемкости, обычно имеющего большие габариты, увеличено расстояние между полосами (252 вместо 236 мм); обеспечивается также возможность большего поворота корпуса автосцепки в горизонтальной плоскости.
Упорная плита передает сжимающее усилие от корпуса автосцепки поглощающему аппарату и растягивающие усилия от последнего через передний упор раме кузова вагона. Плита имеет прямоугольную форму и цилиндрическое гнездо в середине, облегчающее повороты корпуса автосцепки в горизонтальной плоскости и обеспечивающее центральную передачу усилия.
Опорные части соединяют упряжное устройство и поглощающий аппарат с рамой кузова вагона. Они состоят из переднего 9 и заднего 1 упоров и поддерживающей планки 4. К ним относятся также верхние ограничительные планки, устанавливаемые в случаях, когда конструкция хребтовой балки или других частей вагона не препятствует перемещению тягового хомута вверх на расстояние более 24 мм.
Через передний упор на раму кузова вагона передаются растягивающие продольные усилия, а через задний - сжимающие. Раньше эти упоры (упорные угольники) выполняли раздельными, а в последние годы - объединен. Объединенный передний упор отливают вместе с розеткой (рисунок 1.4.2, а), а задний при коротких консолях рамы кузова - заодно с надпятниковым усилением этой рамы или так, как изображено на (рисунок 1.4.2, б).
Переход к объединенным упорам обусловлен тем, что они в отличие от раздельных усиливают хребтовую балку и уменьшают перекос поглощающего аппарата, возможный при неточной установке раздельных угольников. Такой перекос перегружает отдельные элементы хребтовой балки и вызывает ненормальный износ ее и деталей упряжного устройства.
|
Рисунок 1.9 - Объединенные унифицированные упоры:
а - передний; б - задний
Поглощающие аппараты автосцепки предназначены для уменьшения продольных растягивающих и сжимающих сил в поезде за счет преобразования кинетической энергии соударяющихся вагонов в работу сил трения и потенциальную энергию деформации упругих элементов аппарата. В автосцепке применяются следующие основные типы поглощающих аппаратов: пружинные, пружинно-фрикционные, резинометаллические, резино-фрикционные, гидравлические, газовые, гидрогазовые, гидрофрикционные и эластомерные. Пружинные аппараты устанавливаются лишь в буферах и межвагонных амортизаторах пассажирских вагонов с упругими переходными торцевыми площадками. В автосцепках грузовых вагонов наибольшее распространение получили пружинно-фрикционные аппараты с простыми в исполненииупорами, имеющими удовлетворительные параметры (энергоемкость, полный ход аппарата, сила сопротивления при сжатии, сила начальной затяжки, коэффициент необратимого поглощения энергии удара, статическая сила закрытия аппарата). Для грузовых вагонов разработаны пружинно-фрикционные поглощающие аппараты нескольких типов.
Аппараты Ш-1-ТМ, Ш-2-Т(рисунок 1.10), Ш-2-В сходны между собой по конструкции и отличаются в основном параметрами.
Рисунок 1.10 – Поглощающий аппарат типа Ш-1-ТМ:
1 – нажимной корпус; 2 – фрикцтонный клин; 3 – корпус аппарата; 4 – стяжной болт; 5,6– двухрядная пружина; 7 – стяжной болт
Сила трения в аппаратах возникает на соприкасающихся поверхностях трех штампованных закаленных фрикционных клиньев (сталь марки 38ХС или марки 30) и литого шестигранного корпуса (сталь ЗОГМЛ-Б или 30Х06Л-У).
Аппарат Ш-6-ТО-4 для 4-осных грузовых вагонов взаимозаменяем с аппаратами Ш-1-ТМ, Ш-2-В, однако у вагонов более ранней постройки требуется модернизация упоров на хребтовой балке.
Аппарат ПМК-110А применяется в автосцепках рефрижераторных вагонов, платформ для перевозки контейнеров и иногда у 8-осных вагонов. Фрикционными элементами в нем являются износостойкие металлокерамические пластины.
Гидрофрикционный аппарат ПГФ-4 имеет в основном аналогичную конструкцию с аппаратом ПФ-4, отличается от него наличием в наружной силовой пружине удлинителя гидрогасителя клапанного типа с автоматической подстройкой сопротивления в за- висимости от скорости соударения вагонов при работе в квазистатическом и динамическом режимах нагружения. Поглощение энергии удара в аппарате происходит благодаря
рассеиванию работы сил трения во фрикционном узле и сопротивления гидрогасителя.
|
|
Индивидуальные очистные сооружения: К классу индивидуальных очистных сооружений относят сооружения, пропускная способность которых...
Организация стока поверхностных вод: Наибольшее количество влаги на земном шаре испаряется с поверхности морей и океанов (88‰)...
Поперечные профили набережных и береговой полосы: На городских территориях берегоукрепление проектируют с учетом технических и экономических требований, но особое значение придают эстетическим...
История развития пистолетов-пулеметов: Предпосылкой для возникновения пистолетов-пулеметов послужила давняя тенденция тяготения винтовок...
© cyberpedia.su 2017-2024 - Не является автором материалов. Исключительное право сохранено за автором текста.
Если вы не хотите, чтобы данный материал был у нас на сайте, перейдите по ссылке: Нарушение авторских прав. Мы поможем в написании вашей работы!