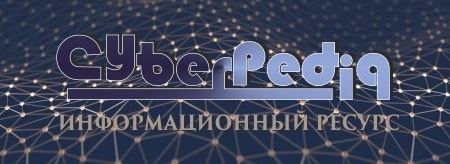
Адаптации растений и животных к жизни в горах: Большое значение для жизни организмов в горах имеют степень расчленения, крутизна и экспозиционные различия склонов...
Особенности сооружения опор в сложных условиях: Сооружение ВЛ в районах с суровыми климатическими и тяжелыми геологическими условиями...
Топ:
История развития методов оптимизации: теорема Куна-Таккера, метод Лагранжа, роль выпуклости в оптимизации...
Эволюция кровеносной системы позвоночных животных: Биологическая эволюция – необратимый процесс исторического развития живой природы...
Отражение на счетах бухгалтерского учета процесса приобретения: Процесс заготовления представляет систему экономических событий, включающих приобретение организацией у поставщиков сырья...
Интересное:
Искусственное повышение поверхности территории: Варианты искусственного повышения поверхности территории необходимо выбирать на основе анализа следующих характеристик защищаемой территории...
Как мы говорим и как мы слушаем: общение можно сравнить с огромным зонтиком, под которым скрыто все...
Распространение рака на другие отдаленные от желудка органы: Характерных симптомов рака желудка не существует. Выраженные симптомы появляются, когда опухоль...
Дисциплины:
![]() |
![]() |
5.00
из
|
Заказать работу |
|
|
Введение
Поддержание рабочего состояния оборудования обеспечивается планово-предупредительными ремонтами. Основанием для ограничения сроков эксплуатации являются экономические соображения. Сроки эксплуатации единицы оборудования могут различаться в зависимости от условий эксплуатации, от методов диагностики, обслуживания и ремонта [1].
Функция по выполнению работ по техническому обслуживанию и ремонту оборудования нефтегазодобывающего общества возложена на эксплуатационно-ремонтную базу, которая включает собственную эксплуатационно-ремонтную базу, ремонтные базы подрядных организаций (технический сервис) и ремонтные базы предприятий-изготовителей оборудования(фирменный сервис). На старых месторождениях они, по меньшей мере, удваиваются, а новое оборудование приобретается только для освоения новых месторождений [1].
Такая политика обеспечивает компаниям значительный экономический эффект, особенно, при ускоренном отборе нефти из скважин, когда сближаются сроки эксплуатации оборудования со сроками разработки месторождений [1].
Улучшение положения потребностей нефтегазовой отрасли в оборудовании возможно и целесообразно не только за счет увеличения количества выпускаемого оборудования, а за счет улучшения качества выпускаемого оборудования. Что возможно, если компании производители будут самостоятельно разрабатывать и развивать системы технического обслуживания и ремонта оборудования в течение всего срока эксплуатации вплоть до его списания. Так как компания производитель сможет сделать это наиболее эффективно, в связи с тем что испытания и производство оборудования были проведены на этапе разработки прототипов оборудования и следовательно сроки эксплуатации и промежутки времени через которые следует проводить техническое обслуживание будет более ясным для такой организации.
|
На данном этапе развития нефтегазовой промышленности в условиях ожесточающихся режимов эксплуатации оборудования должна быть поставлена задача повышения эффективности, качества и скорости работы ремонтных компаний. Целью этого направления является обеспечение должной надежности работы оборудования, а так же минимально возможных сроков обслуживания и ремонта оборудования для его повторного ввода в эксплуатацию.
Цели курсовой работы
- Систематизировать и закрепить теоретические знания, полученные при изучении дисциплины "Основы эксплуатации и ремонта бурового и нефтегазодобывающего оборудования";
- Углубить теоретические знания по теме работы;
- Сформировать умение использовать справочную и нормативную документацию;
- Подготовиться к государственной аттестации.
Задачи работы:
По выбранному совместно с руководителем по выполняемой курсовой работе чертежу детали, входящего в состав оборудования, разрабатываемого в 8-м семестре курсового проекта по дисциплине "Машины и оборудование для добычи и подготовки нефти и газа".
· Сформулировать назначение выбранной детали в оборудовании, в состав которого оно входит
· Систематизировать характерные виды дефектов, возникающих при эксплуатации оборудования, в состав которого входит эта деталь, рассмотреть механизм процессов, вызывающих образование конкретных дефектов
винт диспергатор дефект ремонт
Назначение
Для выполнения данной курсовой работы был выбран винт диспергатора, входящий в состав газосепаратора-диспергатора (рисунок 1.1).
Рисунок 1.1. Винт диспергатора лабиринтно-винтового типа.
Функции
Диспергатор лабиринтно-винтового типа в конструкции газосепаратора-диспергатора предназначен для измельчения пузырьков свободного газа в газожидкостной смеси, растворения их в жидкости для расширения функциональных возможностей погружного насоса и создания более благоприятных условий его работы.
|
Специфика условий работы
Детали этого типа подвержены практически всем видам коррозии и износа, т.к. они работают в условиях быстродвижущейся агрессивной среды, перекачиваемой насосом, в которой присутствуют свободный газ, абразивные частицы, высокие температуры, химически активные элементы, контактирующие со всей площадью поверхности детали.
Виды дефектов
Для винта диспергатора, работающего в условиях быстродвижущейся коррозионно-активной среды, с повышенным содержанием механических примесей характерны следующие виды дефектов:
· Сквозные свищи (результат воздействия коррозионно-активной среды)
· Коррозионные отверстия (потеря материала в результате различных видов коррозии)
· Потеря металла (изменение геометрических параметров винта вследствие механических или коррозионных повреждений)
· Риски/царапины/задиры (произвольно направленные механические повреждения поверхности).
Процессы, вызывающие образование конкретных дефектов
Абразивное изнашивание - это разрушение поверхности детали в результате его взаимодействия с твердыми частицами (абразивом). Абразивным материалом называют материал естественного или искусственного происхождения, зерна которого имеют достаточную твердость и обладают способностью резания (царапания). В зависимости от структуры абразивного материала и среды зерна и, следовательно, типа его воздействия на поверхность детали абразивное изнашивание можно разделить на царапание и резание [2].
Механизм резания может рассматриваться как совокупность следующих элементарных процессов:
) упругое взаимодействие абразивной частицы с металлической поверхностью;
) пластическое деформирование изнашиваемого материала при внедрении абразивной частицы;
) процесс снятия (среза) доли металла абразивной частицей с поверхности изнашиваемого металла (рисунок 2.1).
В случае неглубокого проникновения абразива к радиусу скругления внедрившейся кромки процесс резания невозможен, в этом случае абразивная частица оттесняет часть материала в стороны. Образуются царапины и риски [2].
|
Рисунок 2.1. Образования деформированного слоя при абразивном износе пластичного материала: 1 - основная структура обрабатываемого металла; 2 - зона пластическй деформации; 3 - стружка; 4 - пластически деформированный поверхностный слой; 5 - абразивная частица.
Кавитационное изнашивание связано с нарушениями сплошности потока жидкости, движущейся с большой скоростью. На участках, где давление жидкости падает ниже давления насыщения паров, возникают пузырьки пара, воздуха, газа. В зоне повышенного давления кавитационные полости и пузырьки захлопываются с большой скоростью, вызывая микрогидравлические удары жидкости о поверхность детали и ее разрушение (рисунок 2.2). Нередко кавитационное изнашивание сочетается с эрозионным процессом, если поток жидкости загрязнен механическими частицами, как и происходит в случае винта диспергатора [2].
Рисунок 2.2. Схемы гидравлических ударов при сокращениях кавитационного пузыря.
Химической коррозией называют разрушение металлов вследствие химического или электрохимического взаимодействия их с коррозионной средой. Чистая металлическая поверхность легко подвергается химическому воздействию среды. Окружающая среда оказывает существенное влияние на характер протекания коррозионного процесса и, следовательно, обуславливает коррозию разных видов [2].
Жидкостная коррозия - коррозия металлов и сплавов в жидкой среде, которая может обладать или, наоборот, не обладать электролитическими свойствами при полном, неполном или переменном погружении.
Газовая коррозия происходит при непосредственном контакте твердого тела с химически активным газом. Характеризуется образованием на поверхности тела пленки продуктов химической реакции между веществами, входящими в состав тела и адсорбируемыми из внешних газовых включений перекачиваемой газожидкостной смеси [2].
Методы выявления дефектов
Дефектоскопия является составной частью диагностики технического состояния оборудования и его составных частей. Работы, связанные я выявлением дефектов в материале элементов оборудования, совмещаются с ремонтами и техническим обслуживанием или выполняются самостоятельно в период технического осмотра. Для выявления скрытых дефектов в конструкционных материалах используются различные методы неразрушающего контроля.
|
Для выявления дефектов в теле винта диспергатора применяют такие методы дефектоскопии, как акустическая, магнитная, капилярная, оптическая.
Акустические методы (рисунок 2.1) основаны на регистрации параметров упругих колебаний, возбужденных в исследуемом объекте. На ремонтных мероприятиях нефтегазовой отрасли применяют ультразвуковую дефектоскопию, сущность которой заключается в способности ультразвуковых колебаний проникать вглубь материала контролируемого изделия и отражаться от дефектов, являющихся нарушением сплошности материала [3].
Рисунок 2.1. Схема ультразвукового эхо-дефектоскопа:
- контролируемая деталь, 2 - приемный преобразователь пьезоэлектрический, 3 - преобразователь пьезоэлектрический, 4 - усилитель, 5 - трубка электронно-лучевая, 6 - генератор импульсный, 7 - генератор основной развертки, 8 - дефект.
Магнитные методы основаны на регистрации магнитных полей рассеивания над дефектами или магнитных снов контролируемого объекта. Их применяют для обнаружения поверхностных и подповерхностных дефектов в деталях различной формы, изготовленных из ферромагнитных материалов. Магнитный потом, встречая на своем пути дефект с низкой магнитной проницаемостью по сравнению с ферромагнитным материалом детали, обтекает его, и часть магнитных силовых линий выходит за пределы детали (рисунок 2.2) [3].
Рисунок 2.2. Схемы возникновения магнитных полей рассеяния при намагничивании:
А - продольное; б - циркулярное; 1 - трещина; 2 - неметаллическое включение.
При контроле деталей, поступающих в ремонт, наиболее распространен металлопорошковый способ. Технология состоит из следующих операций: очистка поверхности, подготовка суспензии, намагничивания контролируемой детали, осмотра поверхности с целью выявления мест, покрытых отложениями порошка, размагничивание детали.
Капиллярный метод основан на капиллярном проникновении индикаторных жидкостей в полости поверхностных и сквозных несплошностей объекта и регистрации образующихся индикаторных следов визуально или с помощью преобразователя (рисунок 2.3). Эти методы позволяют обнаруживать дефекты производственно-технологического и эксплуатационного происхождения [3].
Рисунок 2.3. Последовательность капиллярного метода контроля:
а - трещина, заполненная проникающей жидкостью, б - жидкость с поверхности детали удалена, в - нанесен проявитель, трещина выявлена.
|
- контролируемая деталь, 2 - полость трещины, 3 - проникающая жидкость, 4 - проявитель, 5 - след трещины.
Заключение и выводы
Восстановление винтов диспергатора редко проводят в виду экономической нецелесообразности. Чаще всего вышедшую из работоспособного состояния деталь отправляют на переработку и заменяют новой.
Описанный выше технологический маршрут винт диспергатора проходит только в случае его высокой стоимости, которая должна превышать стоимость производства новой такой детали. В конструкции разрабатываемого мной газосепаратора-диспергатора винт имеет сложную форму и изготавливается из дорогостоящего материала, что частично оправдывает его ремонт.
Выводы:
. Сформулировано назначение винта диспергатора и функции, которые он выполняет, учтена специфика его работы.
. Проанализированы виды дефектов и механизмы процессов, вызывающих их образование. Рассмотрены способы выявления дефектов в теле винта.
. Рассмотрены технологические методы устранения дефектов винта диспергатора. В качестве самого эффективного выбран и обоснован метод устранения дефектов наплавкой.
. Разработан технологический маршрут ремонта винта диаспергатора.
Список использованной литературы
1. Что мешает обновлению нефтегазового оборудования: http://www.promved.ru/articles/article.phtml?id=289&nomer=12
. Гаркунов Д.Н., Триботехника (износ и безызносность): Учебник. - 4-е изд., перераб. и доп. - М.: "Издательство МСХА", 2001. - 616 с.
. Протасов В.Н., Султанов Б.З., Кривенков С.В. "Эксплуатация оборудования для бурения скважин и нефтегазодобычи". Под общ. ред. Протасова В.Н.,: "Недра-Бизнесцентр", 2004. - 691 с.
. Способы и технологические процессы ремонта // http://stroy-technics.ru/article/sposoby-i-tekhnologicheskie-protsessy-remonta
Введение
Поддержание рабочего состояния оборудования обеспечивается планово-предупредительными ремонтами. Основанием для ограничения сроков эксплуатации являются экономические соображения. Сроки эксплуатации единицы оборудования могут различаться в зависимости от условий эксплуатации, от методов диагностики, обслуживания и ремонта [1].
Функция по выполнению работ по техническому обслуживанию и ремонту оборудования нефтегазодобывающего общества возложена на эксплуатационно-ремонтную базу, которая включает собственную эксплуатационно-ремонтную базу, ремонтные базы подрядных организаций (технический сервис) и ремонтные базы предприятий-изготовителей оборудования(фирменный сервис). На старых месторождениях они, по меньшей мере, удваиваются, а новое оборудование приобретается только для освоения новых месторождений [1].
Такая политика обеспечивает компаниям значительный экономический эффект, особенно, при ускоренном отборе нефти из скважин, когда сближаются сроки эксплуатации оборудования со сроками разработки месторождений [1].
Улучшение положения потребностей нефтегазовой отрасли в оборудовании возможно и целесообразно не только за счет увеличения количества выпускаемого оборудования, а за счет улучшения качества выпускаемого оборудования. Что возможно, если компании производители будут самостоятельно разрабатывать и развивать системы технического обслуживания и ремонта оборудования в течение всего срока эксплуатации вплоть до его списания. Так как компания производитель сможет сделать это наиболее эффективно, в связи с тем что испытания и производство оборудования были проведены на этапе разработки прототипов оборудования и следовательно сроки эксплуатации и промежутки времени через которые следует проводить техническое обслуживание будет более ясным для такой организации.
На данном этапе развития нефтегазовой промышленности в условиях ожесточающихся режимов эксплуатации оборудования должна быть поставлена задача повышения эффективности, качества и скорости работы ремонтных компаний. Целью этого направления является обеспечение должной надежности работы оборудования, а так же минимально возможных сроков обслуживания и ремонта оборудования для его повторного ввода в эксплуатацию.
Цели курсовой работы
- Систематизировать и закрепить теоретические знания, полученные при изучении дисциплины "Основы эксплуатации и ремонта бурового и нефтегазодобывающего оборудования";
- Углубить теоретические знания по теме работы;
- Сформировать умение использовать справочную и нормативную документацию;
- Подготовиться к государственной аттестации.
Задачи работы:
По выбранному совместно с руководителем по выполняемой курсовой работе чертежу детали, входящего в состав оборудования, разрабатываемого в 8-м семестре курсового проекта по дисциплине "Машины и оборудование для добычи и подготовки нефти и газа".
· Сформулировать назначение выбранной детали в оборудовании, в состав которого оно входит
· Систематизировать характерные виды дефектов, возникающих при эксплуатации оборудования, в состав которого входит эта деталь, рассмотреть механизм процессов, вызывающих образование конкретных дефектов
винт диспергатор дефект ремонт
Назначение
Для выполнения данной курсовой работы был выбран винт диспергатора, входящий в состав газосепаратора-диспергатора (рисунок 1.1).
Рисунок 1.1. Винт диспергатора лабиринтно-винтового типа.
Функции
Диспергатор лабиринтно-винтового типа в конструкции газосепаратора-диспергатора предназначен для измельчения пузырьков свободного газа в газожидкостной смеси, растворения их в жидкости для расширения функциональных возможностей погружного насоса и создания более благоприятных условий его работы.
Специфика условий работы
Детали этого типа подвержены практически всем видам коррозии и износа, т.к. они работают в условиях быстродвижущейся агрессивной среды, перекачиваемой насосом, в которой присутствуют свободный газ, абразивные частицы, высокие температуры, химически активные элементы, контактирующие со всей площадью поверхности детали.
Дефекты, возникающие при эксплуатации
Виды дефектов
Для винта диспергатора, работающего в условиях быстродвижущейся коррозионно-активной среды, с повышенным содержанием механических примесей характерны следующие виды дефектов:
· Сквозные свищи (результат воздействия коррозионно-активной среды)
· Коррозионные отверстия (потеря материала в результате различных видов коррозии)
· Потеря металла (изменение геометрических параметров винта вследствие механических или коррозионных повреждений)
· Риски/царапины/задиры (произвольно направленные механические повреждения поверхности).
Процессы, вызывающие образование конкретных дефектов
Абразивное изнашивание - это разрушение поверхности детали в результате его взаимодействия с твердыми частицами (абразивом). Абразивным материалом называют материал естественного или искусственного происхождения, зерна которого имеют достаточную твердость и обладают способностью резания (царапания). В зависимости от структуры абразивного материала и среды зерна и, следовательно, типа его воздействия на поверхность детали абразивное изнашивание можно разделить на царапание и резание [2].
Механизм резания может рассматриваться как совокупность следующих элементарных процессов:
) упругое взаимодействие абразивной частицы с металлической поверхностью;
) пластическое деформирование изнашиваемого материала при внедрении абразивной частицы;
) процесс снятия (среза) доли металла абразивной частицей с поверхности изнашиваемого металла (рисунок 2.1).
В случае неглубокого проникновения абразива к радиусу скругления внедрившейся кромки процесс резания невозможен, в этом случае абразивная частица оттесняет часть материала в стороны. Образуются царапины и риски [2].
Рисунок 2.1. Образования деформированного слоя при абразивном износе пластичного материала: 1 - основная структура обрабатываемого металла; 2 - зона пластическй деформации; 3 - стружка; 4 - пластически деформированный поверхностный слой; 5 - абразивная частица.
Кавитационное изнашивание связано с нарушениями сплошности потока жидкости, движущейся с большой скоростью. На участках, где давление жидкости падает ниже давления насыщения паров, возникают пузырьки пара, воздуха, газа. В зоне повышенного давления кавитационные полости и пузырьки захлопываются с большой скоростью, вызывая микрогидравлические удары жидкости о поверхность детали и ее разрушение (рисунок 2.2). Нередко кавитационное изнашивание сочетается с эрозионным процессом, если поток жидкости загрязнен механическими частицами, как и происходит в случае винта диспергатора [2].
Рисунок 2.2. Схемы гидравлических ударов при сокращениях кавитационного пузыря.
Химической коррозией называют разрушение металлов вследствие химического или электрохимического взаимодействия их с коррозионной средой. Чистая металлическая поверхность легко подвергается химическому воздействию среды. Окружающая среда оказывает существенное влияние на характер протекания коррозионного процесса и, следовательно, обуславливает коррозию разных видов [2].
Жидкостная коррозия - коррозия металлов и сплавов в жидкой среде, которая может обладать или, наоборот, не обладать электролитическими свойствами при полном, неполном или переменном погружении.
Газовая коррозия происходит при непосредственном контакте твердого тела с химически активным газом. Характеризуется образованием на поверхности тела пленки продуктов химической реакции между веществами, входящими в состав тела и адсорбируемыми из внешних газовых включений перекачиваемой газожидкостной смеси [2].
Методы выявления дефектов
Дефектоскопия является составной частью диагностики технического состояния оборудования и его составных частей. Работы, связанные я выявлением дефектов в материале элементов оборудования, совмещаются с ремонтами и техническим обслуживанием или выполняются самостоятельно в период технического осмотра. Для выявления скрытых дефектов в конструкционных материалах используются различные методы неразрушающего контроля.
Для выявления дефектов в теле винта диспергатора применяют такие методы дефектоскопии, как акустическая, магнитная, капилярная, оптическая.
Акустические методы (рисунок 2.1) основаны на регистрации параметров упругих колебаний, возбужденных в исследуемом объекте. На ремонтных мероприятиях нефтегазовой отрасли применяют ультразвуковую дефектоскопию, сущность которой заключается в способности ультразвуковых колебаний проникать вглубь материала контролируемого изделия и отражаться от дефектов, являющихся нарушением сплошности материала [3].
Рисунок 2.1. Схема ультразвукового эхо-дефектоскопа:
- контролируемая деталь, 2 - приемный преобразователь пьезоэлектрический, 3 - преобразователь пьезоэлектрический, 4 - усилитель, 5 - трубка электронно-лучевая, 6 - генератор импульсный, 7 - генератор основной развертки, 8 - дефект.
Магнитные методы основаны на регистрации магнитных полей рассеивания над дефектами или магнитных снов контролируемого объекта. Их применяют для обнаружения поверхностных и подповерхностных дефектов в деталях различной формы, изготовленных из ферромагнитных материалов. Магнитный потом, встречая на своем пути дефект с низкой магнитной проницаемостью по сравнению с ферромагнитным материалом детали, обтекает его, и часть магнитных силовых линий выходит за пределы детали (рисунок 2.2) [3].
Рисунок 2.2. Схемы возникновения магнитных полей рассеяния при намагничивании:
А - продольное; б - циркулярное; 1 - трещина; 2 - неметаллическое включение.
При контроле деталей, поступающих в ремонт, наиболее распространен металлопорошковый способ. Технология состоит из следующих операций: очистка поверхности, подготовка суспензии, намагничивания контролируемой детали, осмотра поверхности с целью выявления мест, покрытых отложениями порошка, размагничивание детали.
Капиллярный метод основан на капиллярном проникновении индикаторных жидкостей в полости поверхностных и сквозных несплошностей объекта и регистрации образующихся индикаторных следов визуально или с помощью преобразователя (рисунок 2.3). Эти методы позволяют обнаруживать дефекты производственно-технологического и эксплуатационного происхождения [3].
Рисунок 2.3. Последовательность капиллярного метода контроля:
а - трещина, заполненная проникающей жидкостью, б - жидкость с поверхности детали удалена, в - нанесен проявитель, трещина выявлена.
- контролируемая деталь, 2 - полость трещины, 3 - проникающая жидкость, 4 - проявитель, 5 - след трещины.
|
|
Наброски и зарисовки растений, плодов, цветов: Освоить конструктивное построение структуры дерева через зарисовки отдельных деревьев, группы деревьев...
Архитектура электронного правительства: Единая архитектура – это методологический подход при создании системы управления государства, который строится...
Автоматическое растормаживание колес: Тормозные устройства колес предназначены для уменьшения длины пробега и улучшения маневрирования ВС при...
Организация стока поверхностных вод: Наибольшее количество влаги на земном шаре испаряется с поверхности морей и океанов (88‰)...
© cyberpedia.su 2017-2024 - Не является автором материалов. Исключительное право сохранено за автором текста.
Если вы не хотите, чтобы данный материал был у нас на сайте, перейдите по ссылке: Нарушение авторских прав. Мы поможем в написании вашей работы!