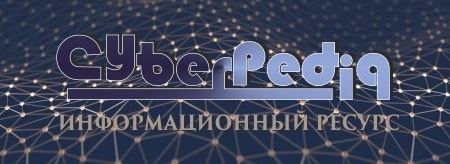
Семя – орган полового размножения и расселения растений: наружи у семян имеется плотный покров – кожура...
Кормораздатчик мобильный электрифицированный: схема и процесс работы устройства...
Топ:
Оснащения врачебно-сестринской бригады.
История развития методов оптимизации: теорема Куна-Таккера, метод Лагранжа, роль выпуклости в оптимизации...
Интересное:
Как мы говорим и как мы слушаем: общение можно сравнить с огромным зонтиком, под которым скрыто все...
Влияние предпринимательской среды на эффективное функционирование предприятия: Предпринимательская среда – это совокупность внешних и внутренних факторов, оказывающих влияние на функционирование фирмы...
Искусственное повышение поверхности территории: Варианты искусственного повышения поверхности территории необходимо выбирать на основе анализа следующих характеристик защищаемой территории...
Дисциплины:
![]() |
![]() |
5.00
из
|
Заказать работу |
|
|
Наряду с углеводородами С5+ конденсаты содержат также пропан, бутан и другие соединения. Одни конденсаты обладают ярко выраженным метановым характером, в других преобладают нафтеновые или ароматические углеводороды. Газовый конденсат одного и того же месторождения может иметь различные показатели. Это зависит, с одной стороны, от снижения пластового давления месторождения в ходе разработки, с другой - от режима эксплуатации установок, где производится выделение тяжелых углеводородов из газа. Углеводородные конденсаты, получаемые при добыче природного газа, необходимо подвергать стабилизации перед дальнейшей переработкой с целью извлечения низкокипящих углеводородов (до С4-С5), а при переработке сернистого конденсата - и сероводорода.
Для стабилизации газового конденсата используются три метода:
1. Ступенчатое выветривание (сепарация, дегазация);
2. Ректификация в стабилизационных колоннах;
3. Комбинирование сепарации и ректификации.
1. Технология стабилизации конденсата дегазацией
Стабилизация газового конденсата дегазацией или сепарацией основана на снижении растворимости низкокипящих углеводородов в конденсатах при повышении температуры и понижении давления. Обычно такая технология процесса стабилизации применяется на месторождениях, имеющих низкий конденсатный фактор. Для стабилизации конденсата можно применять одно-, двух- и трехступенчатые схемы дегазации. Выбор количества ступеней зависит от содержания низкокипящих углеводородов в конденсате: чем оно больше, тем необходимо большее число ступеней. Это объясняется тем, что при увеличении числа ступеней доля отгона на каждой из них уменьшается, а уменьшение доли отгона влечет за собой и уменьшение уноса в газовую сферу целевых углеводородов конденсата.
|
Принципиальная технологическая схема установки стабилизации газового конденсата двухступенчатой дегазацией приведена на рис. 1. При ступенчатой дегазации газа давление на последующей ступени всегда меньше давления на предыдущей.
Рис. 1. Принципиальная технологическая схема дегазации газового конденсата
1 - дроссели; 2,3 - сепараторы первой и второй ступени дегазации; 4 - товарная емкость; I - нестабильный конденсат; II - газы дегазации первой ступени;
III - разгазированный конденсат; IV - газы дегазации второй ступени;
V - конденсат в товарный парк; VI – вода
Основные преимущества схем дегазации - это простота технологии, низкие металло- и энергоемкость процесса. Основной недостаток - это нечеткое разделение углеводородов, одни из которых являются целевыми для газов стабилизации, а другие - для стабильного газового конденсата.
2. Технология стабилизации конденсата ректификацией
Сбор и утилизация газов дегазации конденсата связаны с большими энергетическими затратами, поэтому при больших объемах перерабатываемого конденсата применяют стабилизацию с использованием ректификационных колонн. Она имеет ряд преимуществ, в частности, энергия нестабильного конденсата рационально используется, полученный стабильный конденсат отличается низким давлением насыщенных паров и др. Ректификационная стабилизация газового конденсата проводится чаще всего в двух или трех колоннах, что дает возможность, кроме газов стабилизации и стабильного конденсата, получить пропан-бутановую фракцию (или пропан и бутан). На современных установках обычно применяют комбинирование процессов сепарации и ректификации, что позволяет повысить технологическую гибкость процесса и уменьшить энергозатраты. стабилизация конденсат дегазация ректификация
На рис. 2 представлена принципиальная схема типовой установки стабилизации конденсата с использованием двух ректификационных колонн.
|
Первой ступенью стабилизации по этой схеме является дегазация конденсата в сепараторе 1. Отсепарированная жидкость из сепаратора разделяется на два потока. Один из них нагревается в теплообменнике 2 и поступает в питательную секцию абсорбционно-отпарной колонны 3 (АОК); другой в качестве орошения подается на верхнюю тарелку АОК.
Рис. 2. Типовая схема стабилизации конденсата с ректификацией
I - нестабильный конденсат; II - стабильный конденсат; III - газы стабилизации; IV – ШФЛУ;
1 - сепаратор; 2 - теплообменник; 3 - АОК; 4,7 - трубчатые печи; 5 - стабилизатор; 6 - конденсатор-холодильник
Технологический режим в АОК следующий: давление 1,9-2,5 МПа; температура вверху 15-20°С, внизу - 170-180°С. Ректификатом АОК является фракция, состоящая в основном из метана и этана (III), остатком - деэтанизированный конденсат. Обычно газ сепарации из сепаратора 1 объединяют с верхним продуктом АОК и после дожатия направляют в магистральный газопровод.
Деэтанизированный конденсат из АОК направляют в стабилизатор 5, работающий по схеме полной ректификационной колонны. С верха стабилизатора 5 отбирают пропан-бутановую фракцию (ПБФ) или широкую фракцию легких углеводородов (ШФЛУ) IV, а из куба колонны отводят стабильный конденсат II. Давление в стабилизаторе 5 составляет 1,0-1,6 МПа. Для подвода тепла в кубы колонн 3 и 5 используют трубчатые печи.
На усовершенствованных установках стабилизации конденсата для повышения технологической гибкости и возможности переработки облегченного по фракционному составу конденсата из-за истощения месторождения газ сепарации из сепаратора 1 нагревают и подают в куб АОК как отдувочный газ (рис. 3).
Использование газа сепарации в качестве отдувочного позволяет в нижней части АОК снизить парциальное давление компонентов С3+, вследствие чего снижаются необходимое паровое число и количество тепла, подводимого в трубчатой печи.
Рис. 3. Схема установки стабилизации конденсата с подачей отдувочного газа
I - сырой конденсат; II - стабильный конденсат; III - газы стабилизации; IV – ШФЛУ;
1 - сепаратор; 2,3 - рекуперативные теплообменники; 4 - АОК; 5,8 - трубчатые печи;
6 - стабилизатор; 7 - конденсатор-холодильник
Требования отраслевого стандарта к качеству транспортируемого газа
|
Показатели качества товарного газа основаны на следующих требованиях: а) газ при транспорте не должен вызывать коррозию трубопровода, арматуры, приборов и т.д. б) качество газа должно обеспечить его транспортировку в однофазном состоянии, т.е. не должно произойти образование и выпадение в газопроводе углеводородной жидкости, водяного конденсата и газовых гидратов; в) товарный газ не должен вызывать осложнений у потребителей при его использовании. Для того, что бы газ удовлетворял соответствующим требованиям, необходимо определять т-ку росы по воде и углеводородам, содержание в газе сернистых соединений, механических примесей и кислорода.
Природный газ должен быть подготовлен к дальнему транспорту в соответствии с требованиями СТО 089-2010 “Газ горючие природный, поставляемый и транспортируемый по магистральным газопроводам. (Взамен: ОСТ 51-40-93 (отменен распоряжением ОАО "Газпром" от 25 октября 2010 г. № 359)
Для северных месторождений точка росы, -20 0С (в зимний период) и -14 0С (в летний период). Объемная доля кислорода, %, не более 1,0 Масса сероводорода, г/м3, не более 0,007 Масса меркаптановой серы, г/м3, не более 0,016. Точка росы по влаге, С,является температурой, выше которой при определенном давлении не происходит конденсации паров воды из газа.
Наименование показателя | Значение для макроклиматических районов | ||
умеренный | холодный | ||
1 Компонентный состав, молярная доля, % | Определение обязательно | ||
2 Температура точки росы по воде (ТТРв) при абсолютном давлении 3,92 МПа (40,0 кгс/см2), С, не выше: – зимний период – летний период | -10,0 -10,0 | -20,0 -14,0 | |
3 Температура точки росы по углеводородам (ТТРув) при абсолютном давлении от 2,5 до 7,5 МПа, С, не выше: – зимний период – летний период | -2,0 -2,0 | -10,0 -5,0 | |
4 Массовая концентрация сероводорода, г/м3, не более | 0,007 (0,020) | ||
5 Массовая концентрация меркаптановой серы, г/м3, не более | 0,016 (0,036) | ||
6 Массовая концентрация общей серы, г/м3, не более | 0,030 (0,070) | ||
7 Теплота сгорания низшая при стандартных условиях, МДж/м3 (ккал/м3), не менее | 31,80 (7600) | ||
8 Молярная доля кислорода, %, не более | 0,020
| ||
9 Молярная доля диоксида углерода, %, не более | 2,5 | ||
10 Массовая концентрация механических примесей, г/м3, не более | 0,001 | ||
11 Плотность при стандартных условиях, кг/м3 | Не нормируют, определение обязательно |
10. Дожимная компрессорная станция. Назначение и технологическая схема
ДКС предназначена: для повышения давления газа при его транспортировании по трубопроводу или осуществления необходимых технологических процессов, закачка газа в н. пласт, осуществления газлифта, подготовка газа компрессорным способом.
Компрессорные станции кроме самого здания, где размещаются компрессоры, должны иметь следующие сооружения и оборудование вспомогательного характера: группу сепараторов на приеме компрессоров для предварительной очистки газа от жидкости и механических примесей; маслоотделители; холодильники; сепараторы для отделения выпавшего в холодильнике конденсата; газозамерный и газораспределительный пункт; трубопроводную обвязку; механическую мастерскую; различные склады (для масел, запасных частей). ДКС предназначена: для повышения давления газа при его транспортировании по трубопроводу или осуществления необходимых технологических процессов, закачка газа в н. пласт, осуществления газлифта, подготовка газа компрессорным способом. ДКС состоит: один или несколько компрессорных цехов, система сбора, удаления и обезвреживания механических и жидких примесей, система эл-, тепло-, водоснабжения и др. Компрессорный цех включает: узел подключения, установку очистки газа, охлаждения, система топливного, пускового и импульсного газа, система подготовки и охлаждения смазочного масла, КИП и др.
При отборе газа из газовой (газоконденсатной) залежи давление в процессе разработки непрерывно уменьшается. В определённый момент собственного давления становится недостаточно для подачи газа потребителю (магистральный газопровод МГ, ТЭЦ и т.д.) с заданным расходом, хотя остаточные запасы газа в залежи значительны. Начинается период компрессорной эксплуатации газовой залежи с помощью промысловых дожимных компрессорных станций (ДКС), предназначенных для следующих целей:
1) Сжатия газа до необходимого давления. При подаче газа в МГ это давление может изменяться от 3,7 до 10 МПа. В процессе транспортировки газа на химические комбинаты, ТЭЦ, на технологические нужды промышленных предприятий давление у потребителя изменяется от 0,5 до 1,7 МПа. При работе УКПГ давление обрабатываемого газа может достигать 8 МПа.
2)Увеличения газоотдачи пласта понижением давления на всём пути движения газа из пласта до приёмного коллектора ДКС и в самой залежи; практика показывает, что в бескомпрессорный период эксплуатации газовых месторождений можно отобрать 50 – 60 % начальных запасов газа, в комрессорный период эксплуатации – ещё 20 – 30 %.
3) Увеличения дебитов добывающих скважин уменьшением забойного давления и, следовательно, увеличением депрессии.
4) Улучшения технико-экономических показателей начального участка МГ большой протяжённости или МГ небольшой длины.
|
|
Эмиссия газов от очистных сооружений канализации: В последние годы внимание мирового сообщества сосредоточено на экологических проблемах...
Таксономические единицы (категории) растений: Каждая система классификации состоит из определённых соподчиненных друг другу...
История развития хранилищ для нефти: Первые склады нефти появились в XVII веке. Они представляли собой землянные ямы-амбара глубиной 4…5 м...
Историки об Елизавете Петровне: Елизавета попала между двумя встречными культурными течениями, воспитывалась среди новых европейских веяний и преданий...
© cyberpedia.su 2017-2024 - Не является автором материалов. Исключительное право сохранено за автором текста.
Если вы не хотите, чтобы данный материал был у нас на сайте, перейдите по ссылке: Нарушение авторских прав. Мы поможем в написании вашей работы!