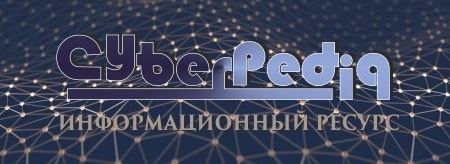
Таксономические единицы (категории) растений: Каждая система классификации состоит из определённых соподчиненных друг другу...
Опора деревянной одностоечной и способы укрепление угловых опор: Опоры ВЛ - конструкции, предназначенные для поддерживания проводов на необходимой высоте над землей, водой...
Топ:
Характеристика АТП и сварочно-жестяницкого участка: Транспорт в настоящее время является одной из важнейших отраслей народного хозяйства...
Определение места расположения распределительного центра: Фирма реализует продукцию на рынках сбыта и имеет постоянных поставщиков в разных регионах. Увеличение объема продаж...
Генеалогическое древо Султанов Османской империи: Османские правители, вначале, будучи еще бейлербеями Анатолии, женились на дочерях византийских императоров...
Интересное:
Наиболее распространенные виды рака: Раковая опухоль — это самостоятельное новообразование, которое может возникнуть и от повышенного давления...
Берегоукрепление оползневых склонов: На прибрежных склонах основной причиной развития оползневых процессов является подмыв водами рек естественных склонов...
Принципы управления денежными потоками: одним из методов контроля за состоянием денежной наличности является...
Дисциплины:
![]() |
![]() |
5.00
из
|
Заказать работу |
|
|
Расчет и выбор посадок с натягом
Посадки с натягом предназначены для получения неподвижных разъемных соединений без дополнительного крепления деталей. Относительная неподвижность деталей обеспечивается силами сцепления (трения), возникающими на контактирующих поверхностях вследствие их деформации, создаваемой натягом при сборке соединения.
Исходные данные:
Параметр | Обозначение | Значение |
Номинальный диаметр соединения | dn | 80 мм. |
Длина соединения | L | 60 мм. |
Внутренний диаметр вала | d1 | 20 мм. |
Наружный диаметр втулки | d2 | 160 мм. |
Осевая сила | Poc | 2,5 кН. |
Крутящий момент | M кр | 100 Н м. |
Материал изготовления вала | Сталь 40 | - |
Материал изготовления отверстия | СЧ 28 | - |
Рабочая температура деталей | tD =td | 1000C |
Система изготовления | CH | - |
Вид сборки – прессование с небольшим количеством смазки
Требования:
1. Выполнить эскиз соединения.
2. Определить предельные расчетные (функциональные) натяги.
3. Определить предельные технологические (конструктивные) натяги.
4. Выбрать посадку по таблице предельных натягов или таблице основных отклонений и допусков.
5. Построить схему расположения полей допусков с указанием всех параметров соединения.
6. Определить коэффициенты запаса прочности и сцепления соединения.
7. Выполнить эскизы соединения и отдельных деталей с обозначением посадки.
8. Определить усилие запрессовки или температуру ступицы для термической сборки соединения.
3.1. Определяю наименьшее придельное давление
Наименьшее давление на контактируемых поверхностях, необходимое для передачи крутящего момента и осевой силы без проворачивания или сдвига, равно:
|
где f - коэффициент трения. Для стали по чугуну f =0,07-0,12.
Схема соединения.
3.2. Определяю наименьший расчетный натяг
где Сd и СD – коэффициенты Ляме вала и втулки: Ed и ED – модули упругости материала вала и втулки,
где - коэффициенты Пуассона материала вала и втулки. Для стали
, для чугуна
(для отверстия)
(для вала).
3.3. Определяю наибольше допустимое давление
где и
- пределы текучести материалов валов и отверстия
3.4. Определяю наибольший придельный натяг
3.5. Определяю придельный технологический натяг
придельный технологический натяг нахожу по выражениям:
где -поправка на смятие шероховатости поверхности вала и втулки при сборке:
-поправка на температурное расширение деталей:
-поправка на уменьшение натяга при повторных запрессовках в процессе эксплуатации и ремонта (по экспериментальным данным
): x- коэффициент, учитывающий увеличения удельного давления у торцов втулки (определяю по графику в зависимости отношения
)
График
для определения
коэффициента x:
где -коэффициент смятия шероховатости поверхности (0,25…0,35 для запрессовки со смазкой), К- коэффициент квалитета точности.
Расчетный допуск посадки равен:
Предварительно квалитет точности равен:
где i- единица допуска, для i=1.9мкм. Ближайшее значение к=100 для 11-го квалитета, поэтому к=1.
Из-за уменьшения фактической площади контакта при увеличении шероховатости поверхности поправку на смятие шероховатости рекомендуется принимать не более
и
-предельно допустимые параметры шероховатости поверхности. Для размеров 18-120мм. ориентированно при прессовании можно принять
=1,25мкм. и
=2,5мкм.
Поправку на температурное расширение определяю по формуле
где и
-коэффициенты линейного расширения: где
и
-рабочие температуры отверстия и вала: t-200C- температура сборки.
|
Подставляю в формулу т.к. вал расширяется больше и необходимо компенсировать увеличение натяга.
Определяю x –l/d=60/80=0.75, поэтому х=0,9.
3.6. Выбираю посадку
предельные стандартные натяги
Технологический допуск посадки равен
Допуск на основную деталь –отверстие. равен:
Выбираю ближайший 10-го квалитета.
Основные отклонения равны
Принимаю что соответствует 9-му квалитету.
Предельные отклонения равны:
Предельные стандартные натяги:
Условия выбора посадок удовлетворяются:
Выбранная посадка записывается так:
Схема расположения полей допусков выбранной посадки.
3.7. Определяю коэффициенты запаса прочности и сцепления
коэффициенты запаса прочности равен:
- условия удовлетворяются.
коэффициенты запаса сцепления равен:
- условия удовлетворяются.
3.8. Определяю усилие запрессовки
Усилие запрессовки нахожу по формуле:
3.9. Определяю температуру нагрева втулки
В случае поперечного метода сборки необходимо определить температуру нагрева втулки по зависимости:
где -зазор при сборке,
-температура при сборке.
В современной технике очень широко применяются подшипники качения. Но даже правильно подобранный подшипник не будет обеспечивать заданную долговечность узла, если неправильно рассчитаны и выбраны посадки его наружного и внутренних колец.
Исходные данные
Параметр | Обозначение | Значение |
Условное обозначение подшипника | 114 | - |
Класс точности | 6 | - |
Радиальная нагрузка | Fr | 18 кН. |
Вид нагрузки | Спокойная | - |
Вращается кольцо | Наружное | - |
Корпус | Неразъемный | - |
Группа радиального зазора | 7 | - |
Требуется:
1. Записать и расшифровать условное обозначение подшипника.
2. Определить вид нагружения наружного и внутреннего колец.
3. Выписать основные геометрические параметры, предельные отклонения колец и радиальные зазоры подшипника.
4. Произвести расчет и выбор посадок для соединения внутренние кольцо – вал и наружное кольцо корпус.
5. Построить схемы расположения полей допусков выбранных посадок.
6. Дать пример обозначение посадок подшипниковых колец на эскизе подшипникового узла и допусков на эскизе сопрягаемых деталей с простановкой шероховатости и отклонений формы и расположения поверхностей.
|
Решение:
4.1. Запись и расшифровка условного обозначения подшипника
Подшипник шариковый радиальный однорядный с группой
Зазора 7, классом точности 6, легкой серии (1) и диаметром отверстия 70мм.
(14 5=70мм.). ГОСТ 520-85
4.1.2. Определение основных геометрических параметров, придельные радиальные зазоры и предельные отклонения на изготовление колец подшипника:
Выписываю технические и точностные характеристики подшипника:
-внутренний диаметр
-наружный диаметр
-ширина кольца В=20мм.=0.020м.
-радиус фасок r =2,0мм.=0,002мм.
-диаметр шарика dT = 12.30мм.
-число шариков в подшипнике z = 13.
4.1.3. Вычисляю дополнительные характеристики подшипника:
-диаметр дорожки качения внутр. и наружн. кольца.
d1=0.25(3d+D)=0.25(3 70+110)=80мм:
D1=0.25(3D+d)=0.25(3 110+70)=100мм:
-радиальные зазоры:
-приведенный диаметр внутреннего кольца:
4.1.4 Устанавливаем характер нагружения колец.
При вращении вала внутреннее кольцо нагружено циркуляционно: наружное кольцо – местно нагруженное.
4.2. Расчет посадки внутреннего кольца на вал
4.2.1. Определяю радиальную нагрузку, приходящийся на наиболее нагруженный шарик в подшипнике:
4.2.2. Вычисляю величину увеличения зазора в подшипнике за счет увеличения деформации тел качения:
(деф. сжатия)
4.2.3. Определяю радиальный зазор в подшипнике с учетом упругой деформации тел качения:
4.2.4. Вычесляем натяг, необходимый для выбора радиального зазора и приведения его к нулю:
4.2.5. Принемаю квелитет изготавления вала.
Для подшипника 6-го класса величина допуска соответствует точности изготавления внутреннего кольца подшипника т.е. IT6
4.2.6. Определяю по ГОСТ 253446-89 допуск на изготовление вала по квалитету 6. Для номинального диаметра dn=70мм, Td=19мкм.
4.2.7. Определяю численное значение основного отклонения вала
|
-что соответствует буквенному отклонению вала m, при котором e i=+ 11мкм.
где -допуск внутреннего кольца подшипника
Вал , тогда запишу так:
4.2.8. Строю схему расположения полей допусков.
4.2.9. Вычисляю усилие запрессовки кольца подшипника на вал.
4.2.10. Выбранную посадку проверяю на соответствие ГОСТ 3325-85 по величине интенсивности нагрузки:
где R- радиальная нагрузка на подшипник:
К- динамический коэффициент посадки (К=1,8):
F- коэффициент, учитывающий степень ослабления при полом вале (F=1):
FA-коэффициент, учитывающий рядность подшипника (при однорядном FA=1):
4.2.11. Выбранную посадку проверяю по величине максимально допустимого натяга:
где
Кольцо работает в зоне упругих деформаций
4.3. Выбор посадки местно-нагруженнного кольца:
4.3.1. Посадка местно-нагруженного кольца выбирается в зависимости от вида нагружения и режима работы подшипникового узла.
Для чугунного неразъемного массивного корпуса при ударной нагрузке рекомендуется поле допуска H7, тогда посадочное место под подшипник:
4.3.2. Строю схему расположения полей допусков для соединение наружное кольцо подшипника – корпус:
4.3.4. Вычерчиваю соединение в сборе с указанием посадок колец.
Схема
центрирования
по внутреннему
диаметру.
7.2. Определение посадок для центрирующих элементов.
Допуски и посадки центрирующих элементов прямоточных соединений при центрировании по «d» выбираю из таблицы. При этом выбираю посадки в зависимости от характера работы изделия. Так, для подвижного соединения беру посадку с гарантированным зазором.
Таким образом получаю следующие посадки:
Для размера «d» - а для размера «b»-
7.3. Определение посадки для не центрирующего элемента
Допуски и посадки для не центрирующего элемента данного шлицевого соединения «D» выбираю из таблиц:
Принимаю для «D»-
Схемы располпжения полей допусков элиментов шлицевого соединения:
7.4. Обозначение шлицевого соединения.
Выбранное шлицевое соединения обозначается следующим образом:
Схема обозначения посадок прямобочного соединения.
Расчет вероятного процента брака
исходные данные
Наименование параметра | Обозначение | Значение |
Посадка | ![]() | - |
Коэффициенты относительного Рассеивания размеров: -отверстия -вала |
![]() ![]() | 0,8 1,0 |
Коэффициенты относительной Асимметрии размеров: -отверстия -вала |
![]() ![]() | -0,4 +0,2 |
Требуется:
1. Построить схему расположения полей допусков соединения с теоретическими кривыми распределения и зонами рассеяния действительных отверстий и валов.
|
2. Определить вероятный процент бракованных отверстий, валов и соединений.
3. Построить схему рассеяния действительных натягов в соединении.
4. Определить придельные вероятностные натяги.
5. Дать заключение о качестве технологических процессов обработки отверстий и валов.
Решение:
1,1. Построение схемы расположения полей допусков с теоретическими кривыми распределения и полями рассеивания действительных размеров отверстий и валов
Расшифровываю посадку:
-Допуск отверстия TD=ES-EI=18мкм.
Верхнее отклонение отверстия ES=-18мкм.+ мкм.=-11мкм.
мкм.=7мкм. (поправка)
Нижнее отклонение отверстия EI=ES-TD=-11+(-18)=-29 мкм.
-Допуск вала Td=es-ei=11мкм.
Верхнее отклонение вала es=0 мкм.
Нижнее отклонение вала ei=-11 мкм.
-Зоны рассеяния размеров отверстия и вала:
-Определяю величины смещения средних действительных размеров отверстия и вала относительно середины допуска
Схема к расчету вероятного процента брака отверстий и валов.
1,2. Определение вероятного процента бракованных отверстий
-Среднее квадратическое отклонение размеров отверстий равно:
-Величины интервалов от центра группирования размеров до границ допуска определяем исходя из рис.1,1:
-Коэффициенты риска определяем по зависимостям:
-Значение интеграла вероятности Ф(t) определяем по таблицам:
Ф(t1)=Ф(5.25)=0.499999
Ф(t2)=Ф(2.25)=0.4878
- Вероятный процент исправимого и неисправимого брака размеров отверстия равен:
Qбр={0.5- Ф(t) } 100%.
Qбр(и)={0.5-0,499999} 100=0,0001%=0
Qбр(не)={0.5-0,4878} 100=1,22%
Полный брак по отверстиям равен:
QбрD= Qбр(и) +Qбр(не)=0+1.22=1.22%
1,3. Определение вероятного процента бракованных валов
-Среднее квадратическое отклонение размеров валов равно:
-Величины интервалов от центра группирования размеров до границ допуска определяем исходя из рис.1,1:
-Коэффициенты риска определяем по зависимостям:
-Значение интеграла вероятности Ф(t) определяем по таблицам:
Ф(t1)=Ф(3,6)=0.499841
Ф(t2)=Ф(2,4)=0.4981
- Вероятный процент исправимого и неисправимого брака размеров валов равен:
Qбр={0.5- Ф(t) } 100%.
Qбр(и)={0.5-0,499841} 100=0,0159%
Qбр(не)={0.5-0,4981} 100=0,19%
Полный брак по валам равен:
QбрD= Qбр(и) +Qбр(не)=0,0159+0,19=0,2059%
1,4 Определение вероятного процента бракованных соединений
-Среднее квадратическое отклонение натягов равно:
-Средний действительный натяг определяем по формуле:
где -средний действительный размер отверстия:
-средний действительный размер вала.
Тогда:
-Предельные натяги соединения определяю из вырожения:
-Строю схему рассеяния действительных натягов в посадке (рис.1,2)
определяю величины интервалов от центра группирования до границ предельных натягов исходя из рис.1,2:
Коэффициенты риска
Значение интервала вероятности Ф(t):
Ф(t1)=Ф(7,6)=0.5214
Ф(t2)=Ф(2.98)=0.4986
- Вероятный процент браковых соединений равен:
1.5 Определение вероятных предельных натягов:
Предельные вероятные зазоры равны:
1.6 Заключение о качестве технологических процессов обработки
Проведенная оценка вероятного процента брака показывает, что технологический процесс обработки отверстия и вала в целом удовлетворителен (вероятный процент брака отверстия–1,22%, вала-0,2059%). Вероятный процент бракованных соединений составляет -0%. Следовательно используемая технология и оборудование могут и должны быть использованы в данном производстве.
|
|
История развития хранилищ для нефти: Первые склады нефти появились в XVII веке. Они представляли собой землянные ямы-амбара глубиной 4…5 м...
Общие условия выбора системы дренажа: Система дренажа выбирается в зависимости от характера защищаемого...
Архитектура электронного правительства: Единая архитектура – это методологический подход при создании системы управления государства, который строится...
Типы сооружений для обработки осадков: Септиками называются сооружения, в которых одновременно происходят осветление сточной жидкости...
© cyberpedia.su 2017-2024 - Не является автором материалов. Исключительное право сохранено за автором текста.
Если вы не хотите, чтобы данный материал был у нас на сайте, перейдите по ссылке: Нарушение авторских прав. Мы поможем в написании вашей работы!