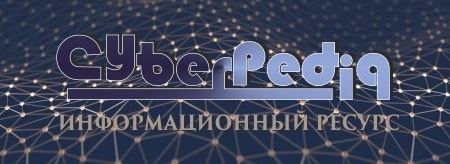
Биохимия спиртового брожения: Основу технологии получения пива составляет спиртовое брожение, - при котором сахар превращается...
Кормораздатчик мобильный электрифицированный: схема и процесс работы устройства...
Топ:
Определение места расположения распределительного центра: Фирма реализует продукцию на рынках сбыта и имеет постоянных поставщиков в разных регионах. Увеличение объема продаж...
Организация стока поверхностных вод: Наибольшее количество влаги на земном шаре испаряется с поверхности морей и океанов...
Эволюция кровеносной системы позвоночных животных: Биологическая эволюция – необратимый процесс исторического развития живой природы...
Интересное:
Как мы говорим и как мы слушаем: общение можно сравнить с огромным зонтиком, под которым скрыто все...
Уполаживание и террасирование склонов: Если глубина оврага более 5 м необходимо устройство берм. Варианты использования оврагов для градостроительных целей...
Влияние предпринимательской среды на эффективное функционирование предприятия: Предпринимательская среда – это совокупность внешних и внутренних факторов, оказывающих влияние на функционирование фирмы...
Дисциплины:
![]() |
![]() |
5.00
из
|
Заказать работу |
|
|
Существуют следующие схемы дробления:
А - операции предварительного грохочения, дробления и поверочного грохочения;
Б - операции предварительного грохочения и дробления;
В - операции дробления иповерочного грохочения;
Г - операция дробления.
Рисунок 1 – Разновидности схем дробления
В схемах дробления А можно совмещать операции предварительного и поверочного грохочения.
Число стадий дробления определяется начальной и конечной крупностью дробимого материала. В зависимости от общей степени дробления и производительности фабрики принимается двух-, трех- и четырехстадиальные схемы дробления.
Схема дробления выбирается по таблице 1. Исходные данные для выбора схемы в таблице 2. Выбор варианта по таблице 3.
Таблица 1 – Основные варианты схем дробления в зависимости от степени дробления (S), крупности дробимого (D) и дробленого продукта (d)
Обозначения схемы | Общая степень дробления, Sобщ | Наибольшая крупность исходной руды (D), мм | ||
1200 | 600 | 300 | ||
Крупность конечного продукта (d), мм | ||||
ББ | 12-20 | 55-60 | 50-55 | 45-50 |
БА | 20-30 | 40-45 | 35-40 | 30-35 |
БББ | 30-55 | 25-30 | 20-25 | 15-20 |
ББА | 55-200 | 13-15 | 10-13 | 6-10 |
Данные для расчета схемы дробления
Q, тыс. т/год – производительность фабрики;
D, мм – наибольшая крупность исходной руды;
d, мм – крупность дробленого продукта;
E, % – эффективность грохочения.
Насыпной вес руды принимается – 1,8 т/м³;
Количество дней работы фабрики в год – 330 дней;
Чистое время работы цеха в сутки – 15 часов.
Для приближенного расчета схемы дробления можно пользоваться типовыми характеристиками крупности (приложение). Характеристика крупности исходной руды при отсутствии практических данных принимается прямолинейной.
|
Таблица 2 – Выбор варианта по двум последним цифрам в зачетной книжке
Вариант
Последняя цифра в зачетной книжке
Предпоследняя цифра в зачетной книжке
Таблица 3 – Задание для расчета по вариантам
Вариант |
Q, тыс. т/год |
D, мм |
D, мм | E, % |
Руда |
Фабрика | |
1 стадия | 2 стадия | ||||||
1 | 1000 | 1200 | 13 | 60 | 75 | мяг. | флотационная |
2 | 1100 | 600 | 10 | 61 | 76 | мяг. | флотационная |
3 | 1200 | 300 | 6 | 62 | 77 | сред. | флотационная |
4 | 1300 | 1200 | 15 | 63 | 78 | сред. | гравитационная |
5 | 1400 | 600 | 13 | 64 | 79 | тверд. | гравитационная |
6 | 1500 | 300 | 10 | 65 | 80 | тверд. | гравитационная |
7 | 1600 | 1200 | 25 | 66 | 81 | мяг. | прочие |
8 | 1700 | 600 | 20 | 67 | 82 | мяг. | флотационная |
9 | 1800 | 300 | 10 | 68 | 83 | сред. | флотационная |
10 | 1900 | 1200 | 30 | 69 | 84 | сред. | флотационная |
11 | 2000 | 600 | 25 | 70 | 85 | тверд. | гравитационная |
12 | 2100 | 300 | 15 | 60 | 86 | тверд. | гравитационная |
13 | 2200 | 1200 | 40 | 61 | 74 | мяг. | гравитационная |
14 | 2300 | 600 | 25 | 62 | 75 | мяг. | прочие |
15 | 2400 | 300 | 15 | 63 | 76 | сред. | флотационная |
16 | 2500 | 1200 | 45 | 64 | 77 | сред. | флотационная |
17 | 2600 | 600 | 35 | 65 | 78 | тверд. | флотационная |
18 | 2700 | 300 | 20 | 66 | 79 | тверд. | гравитационная |
19 | 2800 | 1200 | 45 | 67 | 80 | мяг. | гравитационная |
20 | 2900 | 600 | 35 | 68 | 81 | мяг. | гравитационная |
21 | 3000 | 300 | 30 | 69 | 82 | сред. | прочие |
22 | 3100 | 1200 | 55 | 70 | 83 | сред. | флотационная |
23 | 3200 | 600 | 40 | 60 | 84 | тверд. | флотационная |
24 | 3300 | 300 | 35 | 61 | 85 | тверд. | флотационная |
25 | 3400 | 1200 | 55 | 62 | 86 | мяг. | гравитационная |
Пример расчета схемы дробления
На рисунке 2 показана схема ББА, где все продукты нумеруются арабскими цифрами, а операции римскими цифрами.
Рисунок 2 – К расчету схемы дробления ББА
Данные для расчета схемы:
– производительность обогатительной фабрики – 1300 тыс.т/год;
|
– календарное время – 330 дней;
– руда относится к категории твердых руд;
– максимальная крупность исходной руды D=500 мм;
– максимальная крупность дробленого продукта d=10 мм;
– эффективность грохочения:
а) для первой стадии грохочения ЕI=70%;
б) для второй и третьей стадии ЕII=85%;
– насыпной вес руды 1,8 т/м³;
– чистое время работы цеха в сутки - 15 часов.
Схема дробления рассчитывается в следующем порядке:
1. Определяется суточная и часовая производительность оборудования по формулам:
Qс = Qг / Tраб ∙1000; (1)
Qч = k ∙ Qс / t; (2)
где Qг – годовая производительность, тыс.т/ч;
Qс – суточная производительность цеха, т/с;
Qч – часовая производительность, т/ч;
k – поправочный коэффициент, учитывающий неравномерность свойств сырья, влияющий на производительность оборудования данного цеха. Принимается для рудных фабрик К=1.1, для углеобогатительных (прочих) – 1.15;
t – чистое время работы цеха в сутки (15 часов);
Траб – время работы оборудования Траб= Ткал–Тпер;
Тпер – время перерывов на ремонт оборудования (24 –35 дней/год);
Ткал – календарное время (365 дней);
Траб = 365 – 35 = 330 дней;
т/с;
т/ч.
2. Определяется общая степень дробления Sобщ по формуле:
; (3)
где Dmax – максимальная крупность исходной руды, мм;
dmax – максимальная крупность дробленой руды, мм.
.
3. Устанавливается степень дробления на отдельных стадиях:
. (4)
Степень дробления в каждой стадии выбирается исходя из следующего:
– дробилки крупного дробления позволяют получить до 5;
– дробилки для среднего дробления при работе без поверочного грохочения – до 6;
– те же дробилки при работе в замкнутом цикле с поверочным грохочением – до 10;
– дробилки мелкого дробления при работе без поверочного грохочения – до 3;
– те же дробилки при работе в замкнутом цикле – до 5.
Таким образом поверочное грохочение в любой стадии дает повышение степени дробления почти в два раза.
Поэтому для первой стадии принимаем S1=3, для второй стадии дробления S2=3,33 и для третьей стадии
4. Определяется условная максимальная крупность дробленых продуктов после отдельных стадий дробления (D5, D9, D11) по формулам:
|
Для первой стадии дробления ; (5)
Для второй стадии дробления ; (6)
Для третьей стадии дробления ; (7)
где D1 – максимальная крупность исходной руды;
D5, D9, D11 – максимальная крупность руды после первой, второй и третьей стадии дробления соответственно, мм;
S1, S2, S3 - степени дробления первой, второй и третьей стадий.
мм;
мм;
мм.
5. Подсчитывается для каждой стадии дробления ширину разгрузочной щели дробилки по формуле:
(8)
где Zp – относительная крупность дробленых продуктов, определяется по таблице 3;
D – наибольший размер куска руды после дробления, мм.
Таблица 3 – Значения относительной крупности дробленых продуктов Zp
Категория твердости руд | Крупное дробление, до 100 мм | Среднее дробление, до 25 мм | Мелкое дробление, до 6 мм |
Мягкие | 1,3 | 1,5 | 2,0 |
Средней твердости | 1,4 | 2,0 | 2,5 |
Твердые | 1,7 | 2,5 | 2,8 |
Для каждой стадии дробления рассчитывается ширина разгрузочного отверстия i:
iII = D5 / Zp = 167 / 1.7 ≈ 98 мм;
iIV = D9 / Zp = 50 / 2.5 ≈ 20 мм;
iVI = D11 / Zp = 10 / 2.8 ≈ 3,6 мм.
6. Подсчитывается ширина загрузочной щели дробилки В, мм по формуле:
В = 1,15 ∙ D, (9)
где D – максимальный размер куска руды перед дроблением, мм
Для первой стадии дробления – ВII = 1,15 ∙ 500 = 575 мм.
Для второй стадии дробления – ВIV = 1,15 ∙ 167 =192 мм.
Для третьей стадии дробления – ВVI = 1,15 ∙ 50 = 58 мм.
7. Выбираются размеры отверстий грохотов для первой, второй и третьей стадии дробления.
В операциях предварительного грохочения размеры отверстий сита грохотов «а» принимают в пределах i < a < D (где D – условная максимальная крупность дробленого продукта, поступающего на грохот).
В операциях поверочного грохочения и совмещенных операциях предварительного и поверочного грохочения размеры отверстий сита принимают немного меньшими или равными условной максимальной крупности дробленого продукта.
|
Для рассчитываемой схемы принимаем:
– в операциях предварительного грохочения:
iII < aI < D5 iIV < aIII < D9
98 < aI <167 20 < aIII < 50
аI = 133 мм aII = 35 мм
– в операциях поверочного грохочения:
iVI < aV < D11
3,6 < aV < 10
aIII = 10 мм.
8. Определяются приближенные значения весов продуктов
а) для первой стадии дробления
Рисунок 3 – Схема I стадии дробления
Вес нижнего продукта Q2 определяется по формуле:
Q2 = Q1 ∙ γ1 ∙ E1, (10)
где γ 1 – выход подрешетного продукта или количество продукта, прошедшего через сито грохота (определяется по характеристике крупности исходного продукта), %;
Е1 – эффективность грохочения, %.
Размер зерна, проходящего через сито грохота, равен отверстию в сите, поэтому для грохочения в первой стадии принимаем размер зерна равным 133 мм. По характеристике крупности (приложение) находим выход, соответствующий размеру зерна, равному 133 мм. Он будет равен 75 % или 0,75 у.е.
Q2 = 288,9 ∙ 0,75 ∙ 0,7 =151,7 т/ч.
Определяется вес верхнего продукта Q3 (Q4) из соотношения:
Q3 = Q4 = Q1 - Q2; (11)
Q3 = Q4 = 288,9 - 151,7 = 137,2 т/ч;
Q5 = Q1 = 288,9 т/ч.
б) для второй стадии дробления
Рисунок 4 – Схема II стадии дробления
Определяется вес нижнего продукта Q6, по формуле:
Q6 = Q5 ∙ γ2 ∙ Е2; (12)
Для зерна размером в 35 мм выход соответствует 93 % или 0,93 у.е.
Q6 = 288,9 ∙ 0,93 ∙ 0,85 = 228,4 т/ч
Определяется вес продукта Q7 (Q8), по формуле
Q7 = Q8 = Q5 - Q6; (13)
Q7 = Q8 = 288,9 - 228,4 = 60,5 т/ч;
Q9 = Q1 = Q5 = 288,9 т/ч.
в) для третьей стадии дробления
Рисунок 5 – Схема III стадии дробления
Для зерна размером в 10 мм выход подрешетного продукта соответствует 98 % или 0,98 у.е.
Вес подрешетного продукта может быть определен по формуле
Q11 = Q10 ∙ γ3 ∙ E2; (14)
Выразив Q10 через Q11, получим:
Q10 = Q11 / (γ3 ∙ E2); (15)
Для рассчитываемой схемы
Q11 = Q9 = 288,9 т/ч;
Q10 = 288,9 / (0,98 ∙ 0,85) = 346,8;
Определяется вес продуктов Q12 (Q13) т/ч по формуле:
Q12 = Q13 = Q10 - Q11; (16)
Q12 =Q13 = 346,8 – 288,9 = 57,9 т/ч.
г) рассчитывается объемная производительность дробилок по формуле:
|
Θn = Qn / δн, (17)
где δн – насыпной вес руды, т/м³.
Для первой стадии Θ3 = Q3 / 1,8 = 137,2 / 1,8 = 76,2 м3/ч;
Для второй стадии Θ7 = Q7 / 1,8 = 60,5 / 1,8 = 33,6 м3/ч;
Для третьей стадии Θ12 = Q12 / 1,8 = 57,9 / 1,8 = 32,2 м3/ч.
Требования, которым должны удовлетворять дробилки, согласно результатам предварительного расчета схемы дробления, сводим в таблицу 4.
Таблица 4 – Требования, которым должны удовлетворять дробилки
Показатели | Стадии дробления | ||
I | II | III | |
Крупность куска, мм Размер загрузочной щели, мм Ширина разгрузочной щели, мм Требуемая производительность, т/ч Объемная производительность, м³/ч | 500 575 98 137,2 76,2 | 167 192 20 60,5 33,6 | 50 58 3,6 57,9 32,2 |
Результаты расчета количественной схемы сводится в таблицу 5.
Таблица 5 – Результаты расчета количественной схемы дробления
№ | Наименование операции и продукта | Обоз-начение | Производи-тельность, т/ч | Выход, % | |
I | Предварительное грохочение Поступает: исходная руда Всего: Выходит: подрешетный продукт надрешетный продукт Всего: | Q1 Q2 Q3 |
288,9 288,9
151,7 137,2 288,9 | 100,0 100,0 52,5 47,5 100,0 | |
II | Дробление 1 стадия Поступает: надрешетный продукт Всего: Выходит: Выходит: дробленый продукт Всего | Q3 Q4 |
137,2 137,2
137,2 137,2 | 47,5 47,5 47,5 47,5 | |
III | Предварительное грохочение Поступает: подрешетный продукт дробленый продукт Всего: Выходит: подрешетный продукт надрешетный продукт Всего: |
Q2 Q4
Q6 Q7 | 151,7 137,2 288,9 228,4 60,5 288,9 | 52,5 47,5 100,0 88,5 11,5 100,0 | |
IV | Дробление 2 стадия Поступает: надрешетный продукт Всего: Выходит: дробленый продукт Всего: |
Q7
Q8 | 33,0 33,0 33,0 33,0 | 11,5 11,5 11,5 11,5 | |
V | Предварительное и поверочное грохочение Поступает: подрешетный продукт дробленый продукт дробленый продукт Всего: Выходит: подрешетный продукт надрешетный продукт Всего: |
Q6 Q8 Q13
Q11 Q12
| 255,9 33 38,1 327 288,9 38,1 327,0 | 88,5 11,5 13,2 113,2 100,0 13,2 113,2 | |
VI | Дробление 3 стадия Поступает: надрешетный продукт Всего: Выходит: дробленый продукт Всего: |
Q12
Q13
| 38,1 38,1 38,1 38,1 | 13,2 13,2 13,2 13,2 | |
|
|
Общие условия выбора системы дренажа: Система дренажа выбирается в зависимости от характера защищаемого...
Механическое удерживание земляных масс: Механическое удерживание земляных масс на склоне обеспечивают контрфорсными сооружениями различных конструкций...
Индивидуальные и групповые автопоилки: для животных. Схемы и конструкции...
Кормораздатчик мобильный электрифицированный: схема и процесс работы устройства...
© cyberpedia.su 2017-2024 - Не является автором материалов. Исключительное право сохранено за автором текста.
Если вы не хотите, чтобы данный материал был у нас на сайте, перейдите по ссылке: Нарушение авторских прав. Мы поможем в написании вашей работы!