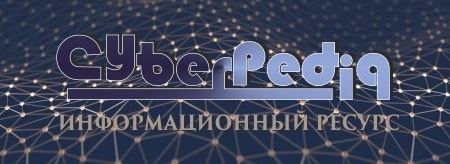
Общие условия выбора системы дренажа: Система дренажа выбирается в зависимости от характера защищаемого...
Организация стока поверхностных вод: Наибольшее количество влаги на земном шаре испаряется с поверхности морей и океанов (88‰)...
Топ:
Проблема типологии научных революций: Глобальные научные революции и типы научной рациональности...
История развития методов оптимизации: теорема Куна-Таккера, метод Лагранжа, роль выпуклости в оптимизации...
Интересное:
Влияние предпринимательской среды на эффективное функционирование предприятия: Предпринимательская среда – это совокупность внешних и внутренних факторов, оказывающих влияние на функционирование фирмы...
Берегоукрепление оползневых склонов: На прибрежных склонах основной причиной развития оползневых процессов является подмыв водами рек естественных склонов...
Отражение на счетах бухгалтерского учета процесса приобретения: Процесс заготовления представляет систему экономических событий, включающих приобретение организацией у поставщиков сырья...
Дисциплины:
![]() |
![]() |
5.00
из
|
Заказать работу |
|
|
Кафедра горного дела
Е.А.Чуева
Геология
Методические указания к выполнению курсовой работы по дисциплине «Свойства полезных ископаемых и принципы их обогащения»
для студентов, обучающихся по специальности
21.05.04 Горное дело
Губкин
2018г.
МИНИСТЕРСТВО ОБРАЗОВАНИЯ И НАУКИ РОССИЙСКОЙ ФЕДЕРАЦИИ
филиал федерального государственного автономного образовательного
учреждения высшего образования
«Национальный исследовательский технологический университет
«МИСиС» в г. Губкине Белгородской области
Кафедра горного дела
Е.А.Чуева
Геология
Методические указания к выполнению курсовой работы по дисциплине «Свойства полезных ископаемых и принципы их обогащения»
для студентов, обучающихся по специальности
21.05.04 Горное дело
Рассмотрено на заседании кафедры горного дела
(Протокол №2 от 01.06.2018г.),
рекомендовано Методическим советом
филиала НИТУ «МИСиС» в г. Губкине
(Протокол №2 от 04.06.2018г.)
Губкин
2018г.
I ОРГАНИЗАЦИОННО-МЕТОДИЧЕСКИЙ РАЗДЕЛ
Целью курсовой работы является выработка навыков научной обработки литературных геологических материалов, анализа геологических карт, выявления основных этапов геологической истории, расчет и обоснование схем обогащения полезных ископаемых.
Приобретённые знания и навыки будут использоваться при прохождении производственных практик, написании дипломных и научных работ, в процессе производственной деятельности.
Задачей курсовой работы является закрепление теоретических и практических знаний по геологии с учетом современных требований.
|
Курсовая работа является составной частью дисциплины «Геология» (Б1.Б.10), модуль «Свойства полезных ископаемых и принципы их обогащения» (Б1.Б.10.2) для студентов специальности 21.05.04 «Горное дело».
Требования к уровню выполнения курсовой работы сводятся к следующему:
Студент должен знать:
ü типы складчатых и разрывных нарушений;
ü признаки общих, региональных и местных стратиграфических подразделений;
ü названия и характеристику магматических, осадочных, метаморфических пород;
ü требования, предъявляемые к геологическим картам.
Студент должен уметь:
ü читать геологическую карту, выделять структурные этажи;
ü строить геологические разрезы;
ü составлять стратиграфические колонки;
ü обосновывать схему обогащения полезных ископаемых;
ü написать объяснительную записку к геологической карте.
II ЭТАПЫ ВЫПОЛНЕНИЯ КУРСОВОЙ РАБОТЫ
Введение
Курсовая работа во всех случаях имеет строго индивидуальный характер. В процессе выполнения курсовой работы следует:
1. Прочитать геологическую карту.
2. Произвести расчет схемы дробления.
3. Обосновать схему обогащения.
4. Оформить объяснительную записку.
Исходным материалом для выполнения работы служат месторождения КМА (Курской магнитной аномалии). В индивидуальном порядке можно использовать другие месторождения РФ или зарубежных стран.
Если у студентов имеются материалы, собранные и частично оформленные в результате самостоятельных полевых исследований, то допускается выполнение курсовой работы не по общему плану, а с углублённой разработкой отдельных заданий, являющихся темой научно-исследовательской студенческой работы.
Методические указания к расчету схемы дробления
Данные для расчета схемы дробления
Q, тыс. т/год – производительность фабрики;
D, мм – наибольшая крупность исходной руды;
d, мм – крупность дробленого продукта;
E, % – эффективность грохочения.
Насыпной вес руды принимается – 1,8 т/м³;
|
Количество дней работы фабрики в год – 330 дней;
Чистое время работы цеха в сутки – 15 часов.
Для приближенного расчета схемы дробления можно пользоваться типовыми характеристиками крупности (приложение). Характеристика крупности исходной руды при отсутствии практических данных принимается прямолинейной.
Таблица 2 – Выбор варианта по двум последним цифрам в зачетной книжке
Вариант
Последняя цифра в зачетной книжке
Предпоследняя цифра в зачетной книжке
Таблица 3 – Задание для расчета по вариантам
Вариант |
Q, тыс. т/год |
D, мм |
D, мм | E, % |
Руда |
Фабрика | |
1 стадия | 2 стадия | ||||||
1 | 1000 | 1200 | 13 | 60 | 75 | мяг. | флотационная |
2 | 1100 | 600 | 10 | 61 | 76 | мяг. | флотационная |
3 | 1200 | 300 | 6 | 62 | 77 | сред. | флотационная |
4 | 1300 | 1200 | 15 | 63 | 78 | сред. | гравитационная |
5 | 1400 | 600 | 13 | 64 | 79 | тверд. | гравитационная |
6 | 1500 | 300 | 10 | 65 | 80 | тверд. | гравитационная |
7 | 1600 | 1200 | 25 | 66 | 81 | мяг. | прочие |
8 | 1700 | 600 | 20 | 67 | 82 | мяг. | флотационная |
9 | 1800 | 300 | 10 | 68 | 83 | сред. | флотационная |
10 | 1900 | 1200 | 30 | 69 | 84 | сред. | флотационная |
11 | 2000 | 600 | 25 | 70 | 85 | тверд. | гравитационная |
12 | 2100 | 300 | 15 | 60 | 86 | тверд. | гравитационная |
13 | 2200 | 1200 | 40 | 61 | 74 | мяг. | гравитационная |
14 | 2300 | 600 | 25 | 62 | 75 | мяг. | прочие |
15 | 2400 | 300 | 15 | 63 | 76 | сред. | флотационная |
16 | 2500 | 1200 | 45 | 64 | 77 | сред. | флотационная |
17 | 2600 | 600 | 35 | 65 | 78 | тверд. | флотационная |
18 | 2700 | 300 | 20 | 66 | 79 | тверд. | гравитационная |
19 | 2800 | 1200 | 45 | 67 | 80 | мяг. | гравитационная |
20 | 2900 | 600 | 35 | 68 | 81 | мяг. | гравитационная |
21 | 3000 | 300 | 30 | 69 | 82 | сред. | прочие |
22 | 3100 | 1200 | 55 | 70 | 83 | сред. | флотационная |
23 | 3200 | 600 | 40 | 60 | 84 | тверд. | флотационная |
24 | 3300 | 300 | 35 | 61 | 85 | тверд. | флотационная |
25 | 3400 | 1200 | 55 | 62 | 86 | мяг. | гравитационная |
Пример расчета схемы дробления
На рисунке 2 показана схема ББА, где все продукты нумеруются арабскими цифрами, а операции римскими цифрами.
Рисунок 2 – К расчету схемы дробления ББА
Данные для расчета схемы:
– производительность обогатительной фабрики – 1300 тыс.т/год;
|
– календарное время – 330 дней;
– руда относится к категории твердых руд;
– максимальная крупность исходной руды D=500 мм;
– максимальная крупность дробленого продукта d=10 мм;
– эффективность грохочения:
а) для первой стадии грохочения ЕI=70%;
б) для второй и третьей стадии ЕII=85%;
– насыпной вес руды 1,8 т/м³;
– чистое время работы цеха в сутки - 15 часов.
Схема дробления рассчитывается в следующем порядке:
1. Определяется суточная и часовая производительность оборудования по формулам:
Qс = Qг / Tраб ∙1000; (1)
Qч = k ∙ Qс / t; (2)
где Qг – годовая производительность, тыс.т/ч;
Qс – суточная производительность цеха, т/с;
Qч – часовая производительность, т/ч;
k – поправочный коэффициент, учитывающий неравномерность свойств сырья, влияющий на производительность оборудования данного цеха. Принимается для рудных фабрик К=1.1, для углеобогатительных (прочих) – 1.15;
t – чистое время работы цеха в сутки (15 часов);
Траб – время работы оборудования Траб= Ткал–Тпер;
Тпер – время перерывов на ремонт оборудования (24 –35 дней/год);
Ткал – календарное время (365 дней);
Траб = 365 – 35 = 330 дней;
т/с;
т/ч.
2. Определяется общая степень дробления Sобщ по формуле:
; (3)
где Dmax – максимальная крупность исходной руды, мм;
dmax – максимальная крупность дробленой руды, мм.
.
3. Устанавливается степень дробления на отдельных стадиях:
. (4)
Степень дробления в каждой стадии выбирается исходя из следующего:
– дробилки крупного дробления позволяют получить до 5;
– дробилки для среднего дробления при работе без поверочного грохочения – до 6;
– те же дробилки при работе в замкнутом цикле с поверочным грохочением – до 10;
– дробилки мелкого дробления при работе без поверочного грохочения – до 3;
– те же дробилки при работе в замкнутом цикле – до 5.
Таким образом поверочное грохочение в любой стадии дает повышение степени дробления почти в два раза.
|
Поэтому для первой стадии принимаем S1=3, для второй стадии дробления S2=3,33 и для третьей стадии
4. Определяется условная максимальная крупность дробленых продуктов после отдельных стадий дробления (D5, D9, D11) по формулам:
Для первой стадии дробления ; (5)
Для второй стадии дробления ; (6)
Для третьей стадии дробления ; (7)
где D1 – максимальная крупность исходной руды;
D5, D9, D11 – максимальная крупность руды после первой, второй и третьей стадии дробления соответственно, мм;
S1, S2, S3 - степени дробления первой, второй и третьей стадий.
мм;
мм;
мм.
5. Подсчитывается для каждой стадии дробления ширину разгрузочной щели дробилки по формуле:
(8)
где Zp – относительная крупность дробленых продуктов, определяется по таблице 3;
D – наибольший размер куска руды после дробления, мм.
Таблица 3 – Значения относительной крупности дробленых продуктов Zp
Категория твердости руд | Крупное дробление, до 100 мм | Среднее дробление, до 25 мм | Мелкое дробление, до 6 мм |
Мягкие | 1,3 | 1,5 | 2,0 |
Средней твердости | 1,4 | 2,0 | 2,5 |
Твердые | 1,7 | 2,5 | 2,8 |
Для каждой стадии дробления рассчитывается ширина разгрузочного отверстия i:
iII = D5 / Zp = 167 / 1.7 ≈ 98 мм;
iIV = D9 / Zp = 50 / 2.5 ≈ 20 мм;
iVI = D11 / Zp = 10 / 2.8 ≈ 3,6 мм.
6. Подсчитывается ширина загрузочной щели дробилки В, мм по формуле:
В = 1,15 ∙ D, (9)
где D – максимальный размер куска руды перед дроблением, мм
Для первой стадии дробления – ВII = 1,15 ∙ 500 = 575 мм.
Для второй стадии дробления – ВIV = 1,15 ∙ 167 =192 мм.
Для третьей стадии дробления – ВVI = 1,15 ∙ 50 = 58 мм.
7. Выбираются размеры отверстий грохотов для первой, второй и третьей стадии дробления.
В операциях предварительного грохочения размеры отверстий сита грохотов «а» принимают в пределах i < a < D (где D – условная максимальная крупность дробленого продукта, поступающего на грохот).
В операциях поверочного грохочения и совмещенных операциях предварительного и поверочного грохочения размеры отверстий сита принимают немного меньшими или равными условной максимальной крупности дробленого продукта.
Для рассчитываемой схемы принимаем:
– в операциях предварительного грохочения:
iII < aI < D5 iIV < aIII < D9
98 < aI <167 20 < aIII < 50
аI = 133 мм aII = 35 мм
– в операциях поверочного грохочения:
iVI < aV < D11
3,6 < aV < 10
aIII = 10 мм.
8. Определяются приближенные значения весов продуктов
|
а) для первой стадии дробления
Рисунок 3 – Схема I стадии дробления
Вес нижнего продукта Q2 определяется по формуле:
Q2 = Q1 ∙ γ1 ∙ E1, (10)
где γ 1 – выход подрешетного продукта или количество продукта, прошедшего через сито грохота (определяется по характеристике крупности исходного продукта), %;
Е1 – эффективность грохочения, %.
Размер зерна, проходящего через сито грохота, равен отверстию в сите, поэтому для грохочения в первой стадии принимаем размер зерна равным 133 мм. По характеристике крупности (приложение) находим выход, соответствующий размеру зерна, равному 133 мм. Он будет равен 75 % или 0,75 у.е.
Q2 = 288,9 ∙ 0,75 ∙ 0,7 =151,7 т/ч.
Определяется вес верхнего продукта Q3 (Q4) из соотношения:
Q3 = Q4 = Q1 - Q2; (11)
Q3 = Q4 = 288,9 - 151,7 = 137,2 т/ч;
Q5 = Q1 = 288,9 т/ч.
б) для второй стадии дробления
Рисунок 4 – Схема II стадии дробления
Определяется вес нижнего продукта Q6, по формуле:
Q6 = Q5 ∙ γ2 ∙ Е2; (12)
Для зерна размером в 35 мм выход соответствует 93 % или 0,93 у.е.
Q6 = 288,9 ∙ 0,93 ∙ 0,85 = 228,4 т/ч
Определяется вес продукта Q7 (Q8), по формуле
Q7 = Q8 = Q5 - Q6; (13)
Q7 = Q8 = 288,9 - 228,4 = 60,5 т/ч;
Q9 = Q1 = Q5 = 288,9 т/ч.
в) для третьей стадии дробления
Рисунок 5 – Схема III стадии дробления
Для зерна размером в 10 мм выход подрешетного продукта соответствует 98 % или 0,98 у.е.
Вес подрешетного продукта может быть определен по формуле
Q11 = Q10 ∙ γ3 ∙ E2; (14)
Выразив Q10 через Q11, получим:
Q10 = Q11 / (γ3 ∙ E2); (15)
Для рассчитываемой схемы
Q11 = Q9 = 288,9 т/ч;
Q10 = 288,9 / (0,98 ∙ 0,85) = 346,8;
Определяется вес продуктов Q12 (Q13) т/ч по формуле:
Q12 = Q13 = Q10 - Q11; (16)
Q12 =Q13 = 346,8 – 288,9 = 57,9 т/ч.
г) рассчитывается объемная производительность дробилок по формуле:
Θn = Qn / δн, (17)
где δн – насыпной вес руды, т/м³.
Для первой стадии Θ3 = Q3 / 1,8 = 137,2 / 1,8 = 76,2 м3/ч;
Для второй стадии Θ7 = Q7 / 1,8 = 60,5 / 1,8 = 33,6 м3/ч;
Для третьей стадии Θ12 = Q12 / 1,8 = 57,9 / 1,8 = 32,2 м3/ч.
Требования, которым должны удовлетворять дробилки, согласно результатам предварительного расчета схемы дробления, сводим в таблицу 4.
Таблица 4 – Требования, которым должны удовлетворять дробилки
Показатели | Стадии дробления | ||
I | II | III | |
Крупность куска, мм Размер загрузочной щели, мм Ширина разгрузочной щели, мм Требуемая производительность, т/ч Объемная производительность, м³/ч | 500 575 98 137,2 76,2 | 167 192 20 60,5 33,6 | 50 58 3,6 57,9 32,2 |
Результаты расчета количественной схемы сводится в таблицу 5.
Таблица 5 – Результаты расчета количественной схемы дробления
№ | Наименование операции и продукта | Обоз-начение | Производи-тельность, т/ч | Выход, % | |
I | Предварительное грохочение Поступает: исходная руда Всего: Выходит: подрешетный продукт надрешетный продукт Всего: | Q1 Q2 Q3 |
288,9 288,9
151,7 137,2 288,9 | 100,0 100,0 52,5 47,5 100,0 | |
II | Дробление 1 стадия Поступает: надрешетный продукт Всего: Выходит: Выходит: дробленый продукт Всего | Q3 Q4 |
137,2 137,2
137,2 137,2 | 47,5 47,5 47,5 47,5 | |
III | Предварительное грохочение Поступает: подрешетный продукт дробленый продукт Всего: Выходит: подрешетный продукт надрешетный продукт Всего: |
Q2 Q4
Q6 Q7 | 151,7 137,2 288,9 228,4 60,5 288,9 | 52,5 47,5 100,0 88,5 11,5 100,0 | |
IV | Дробление 2 стадия Поступает: надрешетный продукт Всего: Выходит: дробленый продукт Всего: |
Q7
Q8 | 33,0 33,0 33,0 33,0 | 11,5 11,5 11,5 11,5 | |
V | Предварительное и поверочное грохочение Поступает: подрешетный продукт дробленый продукт дробленый продукт Всего: Выходит: подрешетный продукт надрешетный продукт Всего: |
Q6 Q8 Q13
Q11 Q12
| 255,9 33 38,1 327 288,9 38,1 327,0 | 88,5 11,5 13,2 113,2 100,0 13,2 113,2 | |
VI | Дробление 3 стадия Поступает: надрешетный продукт Всего: Выходит: дробленый продукт Всего: |
Q12
Q13
| 38,1 38,1 38,1 38,1 | 13,2 13,2 13,2 13,2 | |
Исходные данные для расчета
Рассчитать схему обогащения, предложенную в приложении В с данными по вариантам из таблицы 6.
Таблица 6 – Исходные данные для самостоятельного расчета
№ варианта | Производительность | Извлечение свинца | Извлечение цинка | Содержание в исходном Pb | Содержание в исходном Zn | Содержание свинца | Содержание цинка | Содержание в хвостах Pb | Содержание в хвостах Zn | |
Q1,т/ч | e11Pb,% | e17Zn,% | αPb,% | αZn,% | b11Pb,% | b17Zn,% | b20Pb,% | b20Zn,% | ||
1 | 100 | 77 | 85 | 0,32 | 3,1 | 40 | 47 | 0,03 | 0,08 | |
2 | 110 | 78 | 86 | 0,33 | 3,2 | 41 | 48 | 0,04 | 0,09 | |
3 | 120 | 79 | 87 | 0,34 | 3,3 | 42 | 49 | 0,05 | 0,1 | |
4 | 130 | 80 | 88 | 0,35 | 3,4 | 43 | 50 | 0,03 | 0,11 | |
5 | 140 | 81 | 89 | 0,36 | 3,5 | 44 | 51 | 0,04 | 0,08 | |
6 | 150 | 82 | 90 | 0,37 | 3,1 | 45 | 47 | 0,05 | 0,09 | |
7 | 160 | 83 | 85 | 0,38 | 3,2 | 40 | 48 | 0,03 | 0,1 | |
8 | 170 | 84 | 86 | 0,32 | 3,3 | 41 | 49 | 0,04 | 0,11 | |
9 | 180 | 77 | 87 | 0,33 | 3,4 | 42 | 50 | 0,05 | 0,08 | |
10 | 190 | 78 | 88 | 0,34 | 3,5 | 43 | 51 | 0,03 | 0,09 | |
11 | 200 | 79 | 89 | 0,35 | 3,1 | 44 | 47 | 0,04 | 0,1 | |
12 | 100 | 80 | 90 | 0,36 | 3,2 | 45 | 48 | 0,05 | 0,11 | |
13 | 110 | 81 | 85 | 0,37 | 3,3 | 40 | 49 | 0,03 | 0,08 | |
14 | 120 | 82 | 86 | 0,38 | 3,4 | 41 | 50 | 0,04 | 0,09 | |
15 | 130 | 83 | 87 | 0,32 | 3,5 | 42 | 51 | 0,05 | 0,1 | |
16 | 140 | 84 | 88 | 0,33 | 3,1 | 43 | 47 | 0,03 | 0,11 | |
17 | 150 | 77 | 89 | 0,34 | 3,2 | 44 | 48 | 0,04 | 0,08 | |
18 | 160 | 78 | 90 | 0,35 | 3,3 | 45 | 49 | 0,05 | 0,09 | |
19 | 170 | 79 | 85 | 0,36 | 3,4 | 40 | 50 | 0,03 | 0,1 | |
20 | 180 | 80 | 86 | 0,37 | 3,5 | 41 | 51 | 0,04 | 0,11 | |
21 | 190 | 81 | 87 | 0,38 | 3,1 | 42 | 47 | 0,05 | 0,08 | |
22 | 200 | 82 | 88 | 0,32 | 3,2 | 43 | 48 | 0,03 | 0,09 | |
23 | 100 | 83 | 89 | 0,33 | 3,3 | 44 | 49 | 0,04 | 0,1 | |
24 | 110 | 84 | 90 | 0,34 | 3,4 | 45 | 50 | 0,05 | 0,11 | |
25 | 120 | 77 | 85 | 0,35 | 3,5 | 40 | 51 | 0,03 | 0,08 |
Пример расчета качественно-количественной схемы
Предположим, что для расчета качественно-количественной схемы флотации мы имеем следующие данные:
– Производительность Q1 = 150 т/час;
– Извлечение свинца e9Pb = 77 %;
– Извлечение цинка e15Zn = 85 %;
– Исходное содержание свинца b1 Pb = aPb = 0,4 %;
– Исходное содержание цинка b1 Zn = aZn = 3,3 %;
– Содержание свинца в хвостах b18Pb = 0,03 %;
– Содержание цинка в хвостах b18Zn = 0,09 %;
– Содержание свинца в концентрате b9 Pb = 40 %;
– Содержание цинка в концентрате b15 Zn = 51 %.
Выход и извлечение в первом продукте приравниваем к 100 %, т.е.
g1 = 100 %; e1Pb = 100 %; e12Zn = 100 %.
Расчет баланса
Расчет качественно–количественной схемы начинается с расчета баланса схемы. Приведем, предложенную в приложении Б, схему флотации к упрощенному варианту (а), а полученную схему разобьем еще на две (б и в):
![]() |
а)
|
|
| |||||||
![]() |
б)
![]() |
в)
Порядок расчета:
– по формуле a × en = bn × gn находим выход 9–го продукта:
g9 = (aPb × e9 Pb) / b9 Pb = (0,4 × 77) / 40 = 0,77 %;
– из баланса схемы (б) находим выход 12–го продукта:
g12 = g1 – g9 = 100 – 0,77 = 99,23 %;
– аналогично находим извлечение свинца 12–го продукта:
e12Pb = e1Pb – e9Pb = 100 – 77 = 23 %;
– по формуле a × en = bn × gn находим содержание свинца в 12–ом продукте:
b12 Pb = (aPb × e12 Pb) / g12 = (0,4 × 23) / 99,23 = 0,092 %;
– по формуле a × en = bn × gn находим выход 15–го продукта:
g15 = (aZn × e15 Zn) / b15 Zn = (3,3 × 85) / 51 = 5,5 %;
– из баланса схемы (б) находим выход 18–го продукта:
g18 = g12 – g15 = 99,23 – 5,5 = 93,73 %;
– находим извлечение свинца и цинка 18–го продукта:
e18 Pb = (b18 Pb × g18) / aPb = (0,03 × 93,73) / 0,4 = 7,03 %;
e18 Zn = (b18 Zn × g18) / a Zn = (0,09 × 93,73) / 3,3 = 2,6 %;
– из баланса схемы (в) находим извлечение свинца в 15–ом продукте:
e15Pb = e12Pb – e18Pb = 23 – 7,03 = 15,97 %;
– по формуле a × en = bn × gn находим содержание свинца в 15–ом продукте:
b15 Pb = (aPb × e15 Pb) / g15 = (0,4 × 15,97) / 5,5 = 1,16 %;
– из баланса схемы (в) находим извлечение цинка в 12–ом продукте:
e12 Zn = e15 Zn + e18 Zn = 85 + 2,6 = 87,6 %;
– по формуле a × en = bn × gn находим содержание цинка в 12–ом продукте:
b12 Zn = (aZn × e12 Zn) / g12 = (3,3 × 87,6) / 99,23 = 2,9 %;
– из баланса схемы (б) находим извлечение цинка в 9–ом продукте:
e9 Zn = e1 Zn – e12 Zn = 100 – 87,6 = 12,4 %;
– по формуле a × en = bn × gn находим содержание цинка в 9–ом продукте:
b9 Zn = (aZn × e9 Zn) / g9 = (3,3 × 12,4) / 0,77 = 53,14 %;
Баланс металлов
Для проверки правильности расчета баланса схемы (а) находят баланс металла по свинцу и цинку по формуле:
a × g1 = b9 × g9 + b15 × g15 + b18 × g18. (19)
– для свинца:
a Pb × g1 = b9 Pb × g9 + b15 Pb × g15 + b18 Pb × g18
0,4 × 100 = 40 × 0,77 + 1,16 × 5,5 + 0,03 × 93,73
40 = 39,98;
– для цинка:
a Zn × g1 = b9 Zn × g9 + b15 Zn × g15 + b18 Zn × g18
3,3 × 100 = 53,14 × 0,77 + 51 × 5,5 + 0,09 × 93,73
330 = 329,97.
Расхождение между правой и левой сторонами не должно превышать 0,03, в противном случае производится проверка расчета или перерасчет баланса схемы.
Расчет схемы измельчения
![]() |
При измельчении продукта не происходит процесса обогащения, поэтому во всех продуктах схемы измельчения (1, 2, 3, 4) содержание ценного компонента остается одинаковым и равно исходному, т.е.:
b1 Pb = b2 Pb = b3 Pb = b4 Pb = 0,4 %;
b1 Zn = b2 Zn = b3 Zn = b4 Zn = 3,3 %;
Расчет схемы измельчения производится по циркулирующей нагрузке, которую устанавливают в зависимости от твердости руды от 150 до 500 % (мягкие 150 %, средние 230 %, твердые 300 % и более). Твердость руды необходимо принять по предыдущей работе. Таким образом для данной схемы циркулирующую нагрузку принимаем – 300 %, т.е. g4 = 300 %.
Исходя из этого, выходы продуктов получатся:
g3 = g1 = 100 %;
g2 = g1 + g4 = 100 + 300 = 400 %.
Соответственно извлечение в данных продуктах будет следующим:
e4 Pb = 300 %;
e4 Zn = 300 %;
e3 Pb = e1 Pb = 100 %;
e3 Zn = e1 Zn = 100 %;
e2 Pb = e1 Pb + e4 Pb = 100 + 300 = 400 %;
e2 Zn = e1 Zn + e4 Zn = 100 + 300 = 400 %.
Пооперационный расчет схемы
Расчет качественно-количественных схем обогащения производится «снизу – вверх», т.е. в следующем порядке:
1. Первая перечистка цинка;
2. Контрольная флотация цинка;
3. Контрольная флотация свинца;
4. Вторая перечистка свинца;
5. Первая перечистка свинца.
По основной свинцовой и основной цинковой флотациях проверяют правильность осуществленного расчета.
IV УЧЕБНО-МЕТОДИЧЕСКОЕ ОБЕСПЕЧЕНИЕ
Рекомендуемая литература по курсовой работе
1. Основы геологии: Учеб.для вузов / Под ред. В.А. Ермолова. – 3-е изд., стер. – М.: Издательство Московского государственного горного университета, 2012. – 598 с.: ил. (ГЕОЛОГИЯ).
2. Булгакова А.П. Геология железорудного бассейна КМА. Учебное пособие (с грифом «УМО»). Губкинский институт (филиал) МГОУ, 2008.
3. Короновский Н.В., Старостин В.И., Авдонин В.В. Геология для горного дела. М. Изд. Центр «Академия», 2007.
Приложение 1
ТИТУЛЬНЫЙ ЛИСТ
Министерство образования и науки российской федерации
Им. А.А. Угарова
(филиал) федерального государственного автономного
образовательного учреждения высшего образования
«Национальный исследовательский технологический университет «МИСиС»
Кафедра горного дела
КУРСОВАЯ РАБОТА
СВОЙСТВА ПОЛЕЗНЫХ ИСКОПАЕМЫХ И ПРИНЦИП ИХ ОБОГАЩЕНИЯ НА ПРИМЕРЕ ГОРНО-ОБОГАТИТЕЛЬНОГО КОМБИНАТА
Выполнил: студент очной (заочной) формы обучения
группы _________, шифр ____________
________________________________(И.О.Фамилия)
_______________ Подпись
Руководитель (должность) _______________
________________________________ (И.О.Фамилия)
________________ Подпись
«____»_____________ 2017 г.
Старый Оскол – 2017
Приложение 2
ПРИМЕР ОФОРМЛЕНИЯ СОДЕРЖАНИЯ
Стр.
Введение …………………………………………………………............. | 3 |
1. Географический очерк ………………………………………………….. | 4 |
2. Геологическая изученность района ……………………………………. | 5 |
3. Стратиграфия ……………………………………………………………. | 6 |
4. Интрузивные образования ……………………………………………… | 7 |
5. Тектоника ………………………………………………………………… | 8 |
6. История геологического развития …………………………………….. | 9 |
7. Гидрогеология …………………………………………………………… | 11 |
8. Полезные ископаемые …………………………………………………… 9. Обоснование и выбор схемы дробления руды. …………………………. 10. Качественно-количественная схема обогащения………………………. | 12 13 14 |
Заключение ………………………………………………………………. | 15 |
Список литературы ……………………………………………………… | 16 |
Приложение 1. Геологическая карта | |
Приложение 3
ПРИМЕР
Приложение 4
ПРИМЕР
Приложение 5
ПРИМЕР
Стратиграфическая колонка к геологической карте Лебединского месторождения КМА
Приложение 6
ПРИМЕР ОФОРМЛЕНИЯ СПИСКА ИСПОЛЬЗОВАННОЙ ЛИТЕРАТУРЫ
СПИСОК ЛИТЕРАТУРЫ
1. Короновский Н.В., Старостин В.И., Авдонин В.В. Геология для горного дела. М. Изд. Центр «Академия», 2007.
2. Ермолов В.А., Ларичев Л.Н., Мосейкин В.В. Основы геологии. М. Изд. МГГУ, 2004.
3. Булгакова А.П. Геология железорудного бассейна КМА. Учебное пособие (с грифом «УМО»). Губкинский институт (филиал) МГОУ, 2008.
4. Милютин А.Г. Геология. М. «Высшая школа», 2004.
5. Рапацкая Л.А. Общая геология. М. «Высшая школа», 2005.
6. Карпенков С.Х. Концепции современного естествознания. Справочник для студентов Вузов. М. «Высшая школа», 2004.
Кафедра горного дела
Е.А.Чуева
Геология
Методические указания к выполнению курсовой работы по дисциплине «Свойства полезных ископаемых и принципы их обогащения»
для студентов, обучающихся по специальности
21.05.04 Горное дело
Губкин
2018г.
МИНИСТЕРСТВО ОБРАЗОВАНИЯ И НАУКИ РОССИЙСКОЙ ФЕДЕРАЦИИ
филиал федерального государственного автономного образовательного
учреждения высшего образования
«Национальный исследовательский технологический университет
«МИСиС» в г. Губкине Белгородской области
Кафедра горного дела
Е.А.Чуева
Геология
Методические ук
|
|
Состав сооружений: решетки и песколовки: Решетки – это первое устройство в схеме очистных сооружений. Они представляют...
Таксономические единицы (категории) растений: Каждая система классификации состоит из определённых соподчиненных друг другу...
Автоматическое растормаживание колес: Тормозные устройства колес предназначены для уменьшения длины пробега и улучшения маневрирования ВС при...
Эмиссия газов от очистных сооружений канализации: В последние годы внимание мирового сообщества сосредоточено на экологических проблемах...
© cyberpedia.su 2017-2024 - Не является автором материалов. Исключительное право сохранено за автором текста.
Если вы не хотите, чтобы данный материал был у нас на сайте, перейдите по ссылке: Нарушение авторских прав. Мы поможем в написании вашей работы!