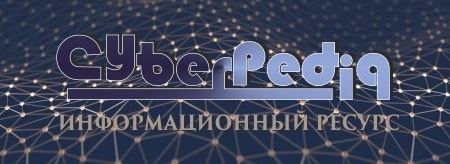
Индивидуальные очистные сооружения: К классу индивидуальных очистных сооружений относят сооружения, пропускная способность которых...
Биохимия спиртового брожения: Основу технологии получения пива составляет спиртовое брожение, - при котором сахар превращается...
Топ:
Методика измерений сопротивления растеканию тока анодного заземления: Анодный заземлитель (анод) – проводник, погруженный в электролитическую среду (грунт, раствор электролита) и подключенный к положительному...
Проблема типологии научных революций: Глобальные научные революции и типы научной рациональности...
Интересное:
Принципы управления денежными потоками: одним из методов контроля за состоянием денежной наличности является...
Инженерная защита территорий, зданий и сооружений от опасных геологических процессов: Изучение оползневых явлений, оценка устойчивости склонов и проектирование противооползневых сооружений — актуальнейшие задачи, стоящие перед отечественными...
Лечение прогрессирующих форм рака: Одним из наиболее важных достижений экспериментальной химиотерапии опухолей, начатой в 60-х и реализованной в 70-х годах, является...
Дисциплины:
![]() |
![]() |
5.00
из
|
Заказать работу |
|
|
Технического состояния СЭУ
Систему технической эксплуатации и требования к техническому состоянию судов, судовых конструкций и технических средств на морском флоте определяет Положение о технической эксплуатации морского флота. Общие требования по технической эксплуатации СЭУ, установленных на судах, определяют Правила технической эксплуатации судовых технических средств. В соответствии с этими документами под технической эксплуатацией понимается совокупность мероприятий по техническому использованию, техническому обслуживанию и ремонту СЭУ.
Совокупность свойств и характеристик СЭУ или отдельных ее элементов определяют техническое состояние СЭУ, свойства которой в процессе эксплуатации подвержены изменению и могут отличаться от установленных технической документации фирм-изготовителей.
В процессе технической эксплуатации СЭУ подвергаются воздействию многих эксплуатационных факторов, различным образом влияющих на их состояние. К таким факторам относятся условия и режим работы, действия обслуживающего персонала, например, влияние различных внешних условий, применение разных сортов топлива для ГД, нестабильность внешней нагрузки в условиях морского плавания. Все это приводит к увеличению эксплуатационных расходов топлива (топливная экономичность) судовых дизелей по сравнению с указанными фирмами-изготовителями в Правилах технической эксплуатации судовых технических средств. Это усугубляется появлением износов, снижением механического КПД (из-за нарушения геометрической формы деталей двигателя), изменения выходных параметров дизеля и др.
Оптимальные характеристики и параметры СЭУ восстанавливаются путем проведения соответствующих профилактик, ремонтных и регулировочных работ в сроки, указанные изготовителями на основе среднестатистических данных. Сроки не всегда отражают необходимость проведения данных мероприятий. Общепринятые традиционные методы технического обслуживания и контроля СЭУ оказываются недостаточно эффективными, что обусловило появление методов технического обслуживания по фактическому состоянию оборудования методами безразборной функциональной технической диагностики. Обеспечение эксплуатационной надежности СЭУ и повышение эффективности ее технической эксплуатации возможно при наличии достаточно точной и своевременной информации о состоянии диагностируемого объекта или системы.
|
Процесс определения технического состояния объекта с необходимой точностью называется техническим диагностированием. Оно осуществляется путем измерения и контроля количественных значений параметров и качественных признаков и дальнейших анализа и обработки результатов измерения и контроля.
Техническое состояние и дефекты судового оборудования определяют по ряду параметров и (или) признаков, прежде всего по значениям электрических величин (напряжение, ток, частота, сопротивление, индуктивность) и неэлектрических (температура, скорость, усилие, давление и т.п.), а также по косвенным признакам, например, появлению нагара, влаги, трещин, а также повышенных значений шума, искрения и др., явившимися следствием естественных, рабочих, воздействий. Указанные параметры и признаки являются диагностическими. Если значение некоторых диагностических параметров или признаков объекта не могут быть измерены, их находят путем обработки значений других измеряемых величин. Например, мощность дизеля может быть косвенно определена либо по положению рейки ТНВД, либо по температуре выхлопных газов, либо по измерению частоты вращения вала дизеля и значению момента на его валу. Также определяется КПД диагностируемого объекта, удельный эффективный расход топлива, коэффициенты теплопередачи, расстояние, проходимое судном в единицу времени, и др.
|
Выбор диагностируемых параметров, необходимых для построения диагностической модели объекта, зависит от вида диагностирования (проверка исправности, работоспособности, функционирования, поиск дефекта). При этом учитываются их информативность, доступность для измерения и контроля. Совокупность предписаний по проведению диагностирования называют алгоритмом технического диагностирования, который способствует решению следующих задач: определение технического состояния, поиск места неисправности, прогнозирование технического состояния.
Основные правила технической эксплуатации судового электрооборудования и средств автоматизации, методы определения и обеспечения эксплуатационных показателей надежности, прогнозирования технического состояния, поиска дефектов приведены в соответствующей литературе.
Программа диагностирования состоит из множества алгоритмов, объединенных с целью оценки состояния технического объекта.
При определении вида технического состояния анализируется возможность выполнения техническим объектом возложенных на него функций, т.е. определяется его работоспособность. Если объект утратил работоспособность или она значительно снизилась, то решают задачу поиска возникшего дефекта, после чего определяют возможность восстановления его функций, т.е. устранения возникшего дефекта. Устранить возникший дефект можно только тогда, когда объект ремонтопригоден.
При решении задачи прогнозирования анализируют состояние объекта, изучают характер изменения диагностических показателей под влиянием внешних и внутренних воздействий и на этой основе определяют тенденции, позволяющие прогнозировать значения показателей или характеристик объекта в определенные моменты времени. Из-за большого разнообразия судового оборудования как по назначению, режимам работы и эксплуатации, так и по принципам построения и конструктивного исполнения используется большое число различных диагностических моделей.
Диагностической моделью объекта называется формальное описание объекта, учитывающее возможность изменения его технического состояния со временем. Описание может быть в аналитической, табличной, векторной, графической или другой форме. При этом объект в общем случае представляется динамической системой, техническое состояние которой в каждый момент времени t определяется значениями входных, внутренних и выходных координат. При решении задач диагностирования широкое применение находят математические модели рабочих процессов в различных объектах. Их разрабатывают на основе механических, физических, термодинамических, газодинамических, химических и электрических закономерностей с учетом общих физических законов сохранения массы, импульса и энергии.
|
Математические модели можно подразделить на непрерывные, дискретные и специальные.
Непрерывные модели описываются алгебраическими и дифференциальными уравнениями, как правило, нелинейными, в функции непрерывного времени t. Линейные, или линеаризованные, уравнения могут быть представлены передаточными функциями.
Дискретные модели определяют состояние только для последовательности дискретных значений независимой переменной (времени), но без учета характера протекания процесса в промежутках. Эти модели можно представить конечно-разностными и логическими уравнениями или конечными автоматами (Мили или Мура). Дискретные модели в основном используют при описании импульсных и цифровых устройств.
Специальные модели подразделяют на две группы:
— информационные — описывают информационные потоки в системах;
— функциональные — отражают совокупность операций, выполняемых оборудованием и его отдельными частями в процессе функционирования.
В ряде практических случаев в качестве модели можно использовать характеристики оборудования, как статические, так и динамические.
Однако указанные модели не всегда могут привести к решению с достаточной степенью точности. Например, подобные модели неприемлемы при решении задач эффективности рабочих процессов судовых дизелей. Для их решения применяется численное моделирование на ЭВМ процессов в цилиндрах, системах топливоподачи, газообразования, наддува, а также для изучения процессов сгорания, газо- и теплообмена в ходе рабочего цикла дизеля.
|
Модели рабочих процессов дают возможность решать задачи оптимизации и разрабатывать алгоритмы диагностики технического состояния дизелей. Последние включают контроль параметров рабочих процессов для своевременного обнаружения отклонений в работе дизеля, которые могут привести к нарушению его работоспособности и снижению экономичности. Например, для определения экономии топлива по модели рабочих процессов дизеля устанавливают контрольные значения параметре» в конкретных условиях эксплуатации. Сравнение измеренных параметров на реальном дизеле в процессе эксплуатации со значениями, полученными на модели для тех же условий, дает возможность определить данные об отклонениях, вызванных изменением его технического состояния, и оценить возможность их компенсации. Основной и наиболее сложной задачей технической диагностики является получение достаточно точной модели дизеля. В реальных условиях ГД воспринимает непрерывные возмущения со стороны движителя, перемещения пера руля вследствие волнения моря и т. п. Эти возмущения отражаются на контролируемых параметрах и придают им стохастический характер. Поэтому модели, полученные при испытаниях дизелей на стенде, не могут быть использованы для диагностики.
Таким же недостатком обладают модели, разработанные на основе численного моделирования рабочих процессов на ЭВМ.
Наиболее типичными являются модели, полученные в результате обработки пассивного эксперимента на реальных объектах (судах). Однако математическая модель объекта диагностирования в результате пассивного эксперимента имеет ряд недостатков, которые делают более предпочтительным использование активного эксперимента. Основным недостатком пассивного эксперимента является необходимость большого статистического материала, сложность расчетных формул. Поэтому, если свойства объекта диагностирования позволяют, то проводят активный эксперимент, который предполагает разовых испытаний (экспериментов), где и n — число параметров х.
Результатом активного эксперимента является аппроксимирование диагностируемого объекта моделью в виде полинома, представляющего полную квадратичную форму
, (8.17)
где bi, bii, bij — статистические коэффициенты.
На практике проведение активного эксперимента сопряжено со значительными трудностями.
Технико-экономический эффект от проведения технической диагностики дизеля выражается в уменьшении расходов на обслуживание и ремонт, повышении среднеэксплуатационной мощности, уменьшении расхода топлива.
|
Для диагностирования технического состояния дизеля разработаны модели рабочих процессов, полученные на основе обобщенного решения задач газовой динамики, рабочих режимов турбокомпрессоров и процессов в системе впуска, расчета характеристик сгорания топлива и т.д. В настоящее время разработаны и применяются различные системы диагностики, в том числе и главных судовых дизелей.
Диагностирование технического состояния сложных объектов обычно выполняют по принципу от целого к частному, т.е. прежде чем осуществить поэлементное диагностирование объекта, необходимо определить вначале его общее техническое состояние.
В общем случае технологический процесс диагностирования состоит из следующих операций:
— присоединение диагностической аппаратуры к дизелю или включение встроенной аппаратуры;
— задание и стабилизация необходимых режимов работы объекта и диагностической аппаратуры;
— измерение и регистрация диагностических параметров;
— сравнение диагностических параметров с нормативными значениями;
— выдача результатов диагноза.
Техническое состояние объекта диагностирования (ОД) (рисунок 8.13), в данном случае ГД, характеризуется параметрами х1, х2,.... хп. Во время работы или под влиянием тестовых воздействий происходят соответствующие изменения параметров y1, у2,.... уm. Диагностические параметры регистрируются механическими, электрическими, тепловыми или другими датчиками Д1, Д2,…,Д т. От них видоизмененные параметры (как правило, электрические) — поступают в ИУ, где' они нормируются и формируются признаки П1, П2,..., Пr. Получив экспериментально или теоретически зависимость параметров технического состояния X от диагностических параметров Y и измерив при диагностировании фактические значения Y', можно определить техническое состояние объекта по признакам П и решить вопрос о необходимости его технического обслуживания или ремонта.
В большинстве случаев для диагностирования технического состояния сложных объектов приходится использовать несколько диагностических параметров, что существенно затрудняет постановку задачи. Решением такой задачи должно быть, раскрытие множественных связей между п структурными параметрами х1, х2,.... хп и соответствующими т диагностическими параметрами y1, у2,.... уm. Для этого необходимо установить последовательность выполнения измерительных и логических операций, т.е. составить алгоритм диагностирования. При этом определяют всю совокупность проверок объекта и его узлов, а также правила анализа полученной информации.
Вследствие большого числа диагностических параметров и неисправностей и множественных связей между ними автоматизированные средства диагностирования технического состояния судовых дизелей создаются на базе ЭВМ (рисунок 8.14).
Это позволяет одновременно измерять несколько диагностических параметров или многократно измерять один и тот же параметр, осреднять результаты, анализировать параметры быстропротекающих рабочих процессов дизелей, производить вычислительные и логические операции с большим количеством данных и др. В настоящее время можно использовать методы диагностирования технического состояния дизелей, которые основаны на анализе изменения их теплотехнических показателей и параметров рабочих процессов, в том числе на неустановившихся режимах. К ним можно отнести методы диагностирования дизелей по индикаторным диаграммам, виброакустическим характеристикам и др.
![]() | ![]() |
Рисунок 8.13 - Обобщенная схема диагностирования дизеля | Рисунок 8.14 - Обобщенная функциональная схема автоматизированной системы диагностирования технического состояния судовых дизелей 1 — дизель; 2 — датчики; 3 — калибровочный прибор; 4 — блок логики; 5 —блок памяти; 6 — блок регистрации; 7— блок управления; 8 — блок самоконтроля; 9 — тестовое устройство |
В соответствии с обобщенной функциональной схемой (рисунок 8.14) на дизеле 1 устанавливаются датчики 2, которые регистрируют параметры рабочих и сопутствующих процессов. Весь поток информации от них поступает в устройство 3, преобразующее сигналы разной физической природы и уровня в стандартные электрические сигналы, удобные для дальнейшей автоматической обработки. В блоке памяти 5 хранится информация о допустимых нормативных значениях сигналов, соответствующих допустимым значениям параметров технического состояния дизеля, и запоминаются результаты сравнения.
Диагноз технического состояния дизеля автоматически осуществляется блоком логики 4, который обрабатывает, сравнивает и выдает информацию. В этом блоке информация обрабатывается в два этапа: сперва проверяется (периодически или постоянно) работоспособность дизеля в целом, затем проводится углубленный поиск конкретной неисправности при отрицательном исходе проверки на первом этапе.
Результаты оценки и прогнозирования технического состояния дизеля поступают в блок регистрации 6. Блок управления 7 служит для задания программы и управления диагностированием. Необходимые сигналы тестового воздействия на дизель подает стимулирующие устройство 9. Контролирует правильность функционирования системы блок самоконтроля 8.
В настоящее время созданы и внедрены различные системы технической диагностики, в том числе и с использованием универсальных мини- и микроЭВМ для диагностирования ряда технических средств и систем судов морского флота по результатам непрерывного или периодического измерения и анализа соответствующих параметров. Диагностические системы разрабатываются как отечественными фирмами, так и зарубежными. Широкое применение на судах, кроме продукции отечественных фирм, нашли диагностические приборы и системы фирм «Аутроника» и «Норконтрол» (Норвегия), «Сименс» (Германия), ASEA (Швеция), СТЛ (Дания).
Для измерения диагностических параметров дизельной установки часто используют систему «Mediag 22» (фирма «Сименс»). Она снабжена вычислительным устройством, позволяющим прогнозировать сроки технического обслуживания, и осциллоскопом, дающим дополнительную информацию о процессах, происходящих в цилиндрах, и о состоянии форсунки.
Наиболее совершенной является система NK (фирма «Аутроника»), которая позволяет получать в цифровых значениях среднее индикаторное давление, частоту вращения коленчатого вала, максимальное давление сгорания, давление сжатия и другие параметры. Фирмой СТЛ созданы и установлены на морских судах системы диагностирования типа СС-10 для дизелей «Бурмейстер и Вайн». В системе «Data Trend» («Нор-контрол», Норвегия) диагностическим контролем охвачены следующие группы узлов дизеля: ЦПГ; система турбонаддува; охладителя воды и масла; топливная аппаратура. В ее состав входит ЭВМ, обрабатывающая информацию, полученную от датчиков, и хранящая в памяти информацию диагностирования. Система «CEDC» (фирма «Зульцер») создана для диагностирования дизелей RND и М. Центральный блок представляет свободно программирующуюся ЭВМ. Система «Чилдет-СМ» (ASEA) является электронной для сбора и обработки данных о техническом состоянии дизеля.
Система «Дизельдак» и «Чилдет» (ASEA) по выполняемым функциям и аппаратурным решениям аналогична системе «Data Trend».
Система PED (фирма «СЕМТ — Пилстик», Франция) предназначена для диагностирования среднеоборотных дизелей.
Возможности этой системы большие: она диагностирует, кроме Деталей ЦПГ, топливной аппаратуры и агрегатов воздухоснабжения, еще и рамовые подшипники коленчатого вала и выпускные клапаны. Состояние рамовых подшипников коленчатого кала контролируется по его перемещениям, регистрируемым индуктивными датчиками. Обрабатывается информация мини-ЭВМ.
Система МХМС-5800 создана фирмой «Ендевко» (США). Для диагностирования большого класса механизмов (центробежных и осевых компрессоров, паровых игазовых турбоагрегатов, редукторов, центробежных насосов и т.п.) предусмотрены физические методы измерений. Логические и вычислительные операции выполняет общая ЭВМ.
Диагностические системы многоцелевого назначения разработаны также фирмами Германии (например, МАК), Норвегии (система МЕКОМ фирмы «Статроник») и др. Использование новых технических средств контроля и диагностики рабочих процессов может быть эффективным только при наличии достаточно надежных алгоритмов распознавания и идентификации неисправностей.
Вопросы для самопроверки:
1. В чем заключаются основные задачи контроля, диагностики и прогнозирования технического состояния СЭУ?
2. Что называют диагностической моделью?
3. Математические модели САУ подразделяются на непрерывные, дискретные и специальные. В чем их различия?
4. В чем заключается технико-экономический эффект от проведения технической диагностики дизеля?
|
|
Организация стока поверхностных вод: Наибольшее количество влаги на земном шаре испаряется с поверхности морей и океанов (88‰)...
Историки об Елизавете Петровне: Елизавета попала между двумя встречными культурными течениями, воспитывалась среди новых европейских веяний и преданий...
Адаптации растений и животных к жизни в горах: Большое значение для жизни организмов в горах имеют степень расчленения, крутизна и экспозиционные различия склонов...
Опора деревянной одностоечной и способы укрепление угловых опор: Опоры ВЛ - конструкции, предназначенные для поддерживания проводов на необходимой высоте над землей, водой...
© cyberpedia.su 2017-2024 - Не является автором материалов. Исключительное право сохранено за автором текста.
Если вы не хотите, чтобы данный материал был у нас на сайте, перейдите по ссылке: Нарушение авторских прав. Мы поможем в написании вашей работы!