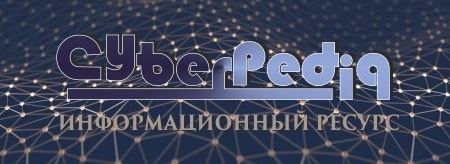
Своеобразие русской архитектуры: Основной материал – дерево – быстрота постройки, но недолговечность и необходимость деления...
История развития хранилищ для нефти: Первые склады нефти появились в XVII веке. Они представляли собой землянные ямы-амбара глубиной 4…5 м...
Топ:
Характеристика АТП и сварочно-жестяницкого участка: Транспорт в настоящее время является одной из важнейших отраслей народного...
Основы обеспечения единства измерений: Обеспечение единства измерений - деятельность метрологических служб, направленная на достижение...
Отражение на счетах бухгалтерского учета процесса приобретения: Процесс заготовления представляет систему экономических событий, включающих приобретение организацией у поставщиков сырья...
Интересное:
Национальное богатство страны и его составляющие: для оценки элементов национального богатства используются...
Что нужно делать при лейкемии: Прежде всего, необходимо выяснить, не страдаете ли вы каким-либо душевным недугом...
Влияние предпринимательской среды на эффективное функционирование предприятия: Предпринимательская среда – это совокупность внешних и внутренних факторов, оказывающих влияние на функционирование фирмы...
Дисциплины:
![]() |
![]() |
5.00
из
|
Заказать работу |
|
|
Расчет автоматической линии
Номинальный фонд работы оборудования:
Т0= (365-t0-tn)ּτ-τnn*t*n, (3.1.1)
где t0- число выходных дней;
tп- число праздничных дней;
τ- время работы оборудования в сутки, ч;
tпп- время сокращения смены,ч;
tп*- количество праздничных дней с учётом сдвоенных праздников;
Т0= (365-104-7)*16-1*7=3422 ч.
Действительный фонд работы оборудования:
Тд= Т0*(1-kп), (3.1.2)
где kп- коэффициент простоя (0,08);
Тд= 3422*(1-0,08)=3148,24 ч
Эффективный фонд работы оборудования:
Тэ= Тд- (365- t0- tп)*τп.о., (3.1.3)
где τп.о.- время подготовительно- заключительных операций, ч.
Tэ= 3148,24- (365-104-7)*1=2894,24 ч.
Темп выхода автомата примем равным 3,5 мин.
Выбираем ритм выдачи R.
Определим количество основных ванн, nосн:
где – время технологического цикла, мин;
– ритм выдачи, мин.
где – время основных операций;
– вспомогательное время, которое необходимо на загрузку разгрузку ванны, принимаем 2 мин.
Задаемся предполагаемым R и рассчитываем количество ванн. Рассчитанное количество ванн округляем до большего целого числа и определяем коэффициент использования ванн Кисп, %
где – принятое количество ванн.
Полученные данные о количестве ванн и коэффициенте использовании ванн сводим в таблицу 10.
Таблица 10 – Зависимость количества ванн от ритма выдачи
Операция | R, мин. | 7 | 8 | 9 | 10 | 11 | |
Цинкование (на подвесках)
| n | 8 | 7 | 6 | 5 | 3 | |
Кисп, % | 86 | 88 | 91 | 98,5 | 90 | ||
Электрохимическое обезжиривание анодное | n | 1 | 1 | 1 | 1 | 1 | |
Кисп, % | 71 | 63 | 55 | 50 | 45 | ||
Травление
| n | 2 | 2 | 1 | 1 | 1 | |
Кисп, % | 71,4 | 62,5 | 55,6 | 100 | 91 |
Принимаем наиболее оптимальный ритм выдачи равный 11 мин.
Sед.з.=Sгод* (1+α)*R/ Tэ*60, (3.1.4)
где Sгод- годовая программа попокрытию, м2;
Sед.з= [ 50000 · (1+0,03) · 11 ] / 2894,24 · 60 = 3,23 м2
где R-ритм выдачи;
Sгод – годовая производительность линии, м2/год;
a - коэффициент исправимого брака (0,03);
Тэф – эффективный фонд времени в году, ч.
Расчитаем количесво ванн:
t=
Необходимое количество ванн n:
n =3
Кисп=90%
Количество деталей на подвеске n, шт. определяется по формуле:
n = ,
n = шт.
Располагаем на 1 подвеску по 70 деталей. Выбираем подвеску с горизонтальным расположением стержней внутри рамы. Стержни изготовлены наклоненными в сторону краев рамы, что ускоряет стекание раствора с подвески, уменьшая тем самым унос раствора, а также позволяет избежать падение капель раствора с верхней зоны подвески на деталь.
Рассчитываем длину подвески по формуле:
![]() | (3.10) |
где – ширина деталей, мм;
bзаз – ширина зазора между деталями, мм;
– число деталей в одном ряду подвески, шт
мм
Рассчитываем высоту подвески:
![]() | (3.11) |
где hдет – высота деталей, мм;
hзаз – высота зазора между деталями, мм;Nдет. в. – число деталей по вертикали на подвеске, шт;
α – угол наклона поперечных перекладин подвески, град.
мм
Для расчета габаритных размеров ванны воспользуемся следующими формулами.
Длина ванны:
![]() | (3.12) |
где n1 – количество позиций в ванне, шт;
L1 – длина подвески, мм;
L2 – расстояние между подвесками (50-100), мм;
L3 – расстояние между торцом стенки и подвеской (100-150), мм.
L=1 мм
Принимаем длину ванны L= 950 мм.
Ширина ванны:
а) для электрохимических процессов:
![]() | (3.13) |
где n – число катодных штанг, шт;
b1 – расстояние от анода до внутренней стенки ванны (50), мм;
|
b2 – расстояние между анодам и катодом (150-200), мм;
B1 – ширина катодной штанги, мм;
d – толщина анода, мм.
мм
Принимаем ширину ванны для электрохимических процессов 830 мм.
б) для химических процессов:
![]() | (3.14) |
где n2 – число катодных штанг,
B1 – максимальный размер детали по ширине ванны, мм;
B3 – расстояние между внутренней стенкой ванны и подвеской, мм;
B4 – ширина подвески, мм.
B=830 мм
Принимаем ширину ванны для химических процессов 830 мм.
Высота ванны:
![]() | (3.15) |
Где Н2 – расстояние от дна до нижнего края подвески (150-300), мм;
Н3 – расстояние от зеркала электролита до верхнего края подвески (50), мм;
Н4 – расстояние от края ванны до зеркала электролита (100-150 мм без перемешивания, 150-250 мм с перемешиванием), мм
мм
Исходя из полученных расчетов, принимаем ванну по ГОСТ 23738 - 85 со следующими характеристиками:
Для ванн электрохимической обработки:
Длина: 950 мм
Ширина: 830 мм
Высота: 1270 мм
Для ванн химической обработки:
Длина: 950 мм
Ширина: 830 мм
Высота: 1270 мм
Полезный объем электролитов:
![]() | (3.16) |
Длина автооператорной линии LАОЛ, мм, рассчитывается по формуле:
![]() | (3.17) |
где Вван – внутренняя ширина ванны, мм;
Вс– ширина сушильной камеры, мм;
– ширина стойки загрузки-разгрузки, мм (600 мм);
– расстояние между сушильной камерой и стойкой загрузки-разгрузки, мм (400 мм);
n – количество ванн одного типа размера;
n0 – количество сопряжений ванн без бортовых отсосов;
n1– количество сопряжений ванн с односторонними бортовыми отсосами;
n2 – количество сопряжений ванн с двухсторонними бортовыми отсосами;
Δl0– зазор между ваннами без бортовых отсосов (160 мм), мм;
Δl1 – зазор между ваннами с односторонними бортовыми отсосами (290 мм), мм;
Δl2 – зазор между ваннами с двухсторонними бортовыми отсосами (390 мм), мм;
Δlб – расстояние от края бортового отсоса до ванны (212 мм), мм.
В размер ширины ванны для обезжиривания, активации, промывки необходимо учесть сливной карман (80 мм).
мм
Ширина линии рассчитывается по формуле:
![]() | (3.18) |
где В1 – расстояние от наружной стенки ванны до наружной плоскости опорной стойки, мм (В1 = 650 мм);
В2– ширина площадки обслуживания, мм (В 2 = 2000
мм).
B=830+650+2000=3480мм.
Высота линии принимается в зависимости от типа автооператора и вида обработки деталей. Так как в линии детали обрабатываются на подвесках и высота ванн составляет 1270 мм, то высота линии будет равна 3890 мм.
|
Принимается линия размером 13790×3480×3890 мм.
Построение циклограммы
Циклограмма – это графическое или табличное изображение функциональных перемещений автооператора при выполнении им последовательности переноса технологических спутников по позициям с соблюдением заданной длительности технологических операций. Термин «циклограмма» означает, что по истечении времени, равного длительности цикла перемещения автооператора, последовательность ходов автооператора полностью начнет повторяться.
При построении циклограммы были использованы следующие условные обозначения:
▬▬ – рабочий ход автооператора – перемещение автооператора с технологическим спутником;
▬▬ – холостой ход автооператора – перемещение автооператора без технологического спутника;
► – разгрузка позиции;
◄ – загрузка позиции;
–
30 |
При построении циклограммы вначале необходимо определить длительность цикла работы автооператора:
tц = R · n = 11 · 1 = 11 мин.,
где R – ритм выдачи;n – количество позиций с максимальной длительностью операции.
Цикл работы автооператора состоит из подциклов, каждый из которых равен ритму выдачи. Цикл работы автооператора включает время, в течении которого автооператор должен выполнить операции по обслуживанию ванн, находящихся в зоне его действия, и вернуться на исходную позицию.
Построенная циклограмма позволяет определить следующие параметры:
1) уточненный ритм выдачи;
2) последовательность выполнения технологических операций;
3) последовательность выполнения транспортных операций;
4) фактическую длительность технологических операций.
Ванна тёплой промывки
Тепловые потери в период разогрева раствора ванны состоят из количества теплоты, необходимой для разогрева раствора до рабочей температуры, для покрытия потерь открытым зеркалом ванны, стенками ванны, для разогрева корпуса ванны и деталей.
Для определения тепла необходимого на разогрев ванны до рабочей температуры используется следующая формула:
|
Qразогрева=Q1+0,5. Q2 (2.65)
Q1=Qраз. эл-та+Qраз.ванны (2.66)
Qраз. эл-та+Qраз.ванны=[сэл-та . Gэл-та+смат. ванны. Gмат. ванны]. (tк-tн) (2.67)
Qраз. эл-та+Qраз.ванны=[4,18. 1160+0,5. 488,128](60-20)=203714,44 кДж
Суммарные потери в окружающую среду определяются:
Q2=Q21+Q211, (2.68)
где Q21 – потери теплоты через боковые стенки и дно ванны; Q211 – затраты теплоты на испарение жидкости.
Q21=q. F. tраз, (2.69)
tраз – должно составлять в зависимости от объема электролита и способа нагрева (0,5-1 ч); F – площадь стенок и дна ванны; q – потери тепла с 1 м2 поверхности стенки и дна ванны, кДж/м2*ч.
Q21=5,3. 3,488=18,48 кДж
Q211= (5,7+4,1. V). (tк-tн). Sзеркала. tраз, (2.70)
где V – скорость движения воздуха (6-7 м/с); Sзеркала – площадь поверхности зеркала ванны.
Q211= (5,7+4,1. 7)(70-55). 0,78=402,48 кДж
Суммарные потери в окружающую среду:
Q2=26,23+402,48=428,71 кДж
Далее необходимо подобрать нагреватель в качестве, которого можно использовать ТЭН. Рассчитывается мощность ТЭНа по формуле:
N=Qразогрева/кпд. tраз, (2.71)
где кпд – принимается меньше либо равным 0,95.
Qразогрева=203714,44+0,5. 428,71=203928,79 кДж
N=203928,79 /0,95. 3600=59,2 кВт.
2.5.Выбор и расчет технологического оборудования
2.5.1. Гидравлический расчет ванны цинкования.
Целью гидравлического расчета является определение толщины стенок и днища ванн и рабочих емкостей.
Суммарное гидравлическое давление на боковые стенки аппарата определяется по формуле:
, (2.98)
где ρ – плотность раствора, кг/м3;
g – ускорение свободного давления, м/с;
Н – высота столба жидкости, м;
Fб – площадь боковой стенки, м2.
Суммарное гидравлическое давление на днище определяется по формуле:
, (2.99)
где Fд – площадь днища, м2.
Толщина дна , мм, определяется из условия максимально допустимого напряжения:
, (2.100)
где Р – распределение по всей поверхности постоянного давления, Па.
К = В / L ≤ 1
σмак – максимально допустимое напряжение.
Для ванны цинкования: Н = 1,45 м, B= 0,95 м, L = 0,83 м.
|
К = 0,5 / 1,6 = 0,3125
Суммарное давление на стенку составит:
Суммарное гидравлическое давление на днище:
Толщину дна:
Принимаем толщину стенки дна равной 4 мм и определяем величину перегиба днища fmax, мм, по формуле
fmax = , (2.101)
где Е – модуль Юнга, Па.
fmax = = 0,0081 м
2.5.2.Расчет и подбор вспомогательного оборудования.
Подбор вентилятора.
Для уменьшения количества вредных испарений в воздухе рабочей зоны на бортах гальванических ванн, ванны травления, активации, ванн хроматирования и ванн обезжиривания устанавливаются бортовые отсосы с горизонтальной щелью всасывания.
Объема воздуха L, м3/ч, отсасываемого от зеркала ванн, рассчитывается по формуле:
L = L0 · KΔt · Kт · K1 · K2 · K3 · K4, (2.102)
где L0 – удельный объем воздуха, отсасывания от ванн, м3/ч;
KΔt – коэффициент, учитывающий разность температур раствора и помещения;
Kт – коэффициент, учитывающий токсичность и интенсивность выделения вредных веществ;
K1 – коэффициент, учитывающий тип отсоса;
K2 – коэффициент, учитывающий воздушное перемешивание раствора, барботаж;
K3 – коэффициент, учитывающий укрытие зеркала электролита плавающими телами;
K4 – коэффициент, учитывающий укрытие зеркала электролита путем введения ПАВ.
Удельный объем отсасываемого воздуха L0, м3/ч, рассчитывается по формуле:
L0 = 1400 · (0,53 · + H1) · 0,66 · Bвн, (2.103)
где Ввн - внутренняя ширина ванны, м;
Lвн – внутренняя длина ванны, м;
Н1 – расстояние от зеркала электролита до борта ванны, м.
Для ванн химического обезжиривания, травления, активации, хроматирования, цинкования и электрохимического обезжиривания:
L0 = 1400 · (0,53 · + 0,15) · 0,66 · 0,5 = 127,6 м3/ч;
Рассчитаем объем воздуха.
Для ванны химического обезжиривания:
L = 127,6· 1,0 · 1,0 · 1,0 · 1,2 · 0,75 · 0,5 = 57,42 м3/ч
Для ванны электрохимического обезжиривания:
L = 127,6· 1,0 · 1,6 · 1,0 · 1,2 · 0,75 · 0,5 = 91,872 м3/ч
Для ванны травления и активации:
L = 127,6· 1,0 · 1,25 · 1,0 · 1,2 · 0,75 · 0,5 = 71,78м3/ч
Для ванны цинкования:
L = 127,6· 1,0 · 0,5 · 1,0 · 1,2 · 0,75 · 0,5 = 28,71м3/ч
Для ванны хроматирования:
L = 127,6· 1,0 · 0,5 · 1,0 · 1,2 · 0,75 · 0,5 = 28,71 м3/ч
Общий объем воздуха, который необходимо отсасывать от гальванической линии:
∑L = 57,42+91,872+2. 71,78+3. 28,71= 378,98 м3/ ч
Выбираем вентилятор среднего давления Ц4-70 марки 3,15. Его производительность 2800 м3/ч. Полное давление 116 Па, КПД = 0,755, мощность 1,5 кВт, габаритные размеры 605×637×605 мм.
Подбор насоса для ванны цинкования.
Часовой расход жидкости Q, м3/ч, рассчитывается по формуле:
Q = , (2.104)
где V – объем ванны, м3;
τ – время одного час в секундах.
Q = 1,16/ 3600 = 3,2· 10-4 м3/с.
Для всасывающего и нагнетающего трубопровода принимаем одинаковую скорость течения, равную 2 м/с.
Внутренний диаметр трубопровода d, м, определяется по формуле:
d = , (2.105)
где ω – скорость течения жидкости, м/с.
d = = 0,014 м
Выбирается стальная труба наружным диаметром 0,022 м с толщиной стенки 2 мм. Внутренний диаметр трубы d = 0,018 м. Фактическая скорость течения жидкости по трубе:
ω = 4 · Q / (π · d2) = 4 · 3,2 · 10-4 / (3,14· 0,0182 )= 1,26 м/с
Определение потерь на трение и местные сопротивления.
Число Рейнольдса Re рассчитывается по формуле:
Re = ω · d · ρ / μ, (2.106)
где ρ – плотность раствора, кг/м3;
μ – вязкость раствора, Н·с/м2.
Re = 1,26 · 0,018 · 1088/ 2,74 · 10-3 = 9005,8
т.е. режим течения турбулентный. Примем абсолютную шероховатость равной Δ = 2 · 10-4м.
Относительная шероховатость е рассчитывается по формуле
е = Δ / d (2.107)
е = 2 · 10-4 / 0,018 = 0,0111
Т.к. в трубопроводе имеет место смешанное трение, то расчет коэффициента трения λ следует проводить по формуле:
λ = 0,11 · (е + 68 / Re)0,25 (2.108)
λ = 0,11 · (0,0111 + 68 / 9005,8)0,25 = 0,041
Определим сумму коэффициентов местных сопротивлений Σξ
Для всасывающей линии:
ξ1 – вход в трубу (принимаем с острыми краями): ξ1 = 0,5;
ξ2 – прямоточные вентили: ξ2 = 1,04;
ξ3 – отводы: коэффициент А = 1, зависит от угла, на который изменяется направление потока в отводе; коэффициент В = 0,09; ξ3 = 0,09.
Σξ = ξ1 + 2ξ2 + 4 ξ3
Σξ = 0,5 + 2 · 1,04 + 4 · 0,09 = 2,94.
Потерянный напор во всасывающей линии находится по формуле:
hп.вс. = (λ · + Σξ) ·
, (2.109)
где l - длина трубопровода, м;
dэ – эквивалентный диаметр трубопровода, м;
g – скорость свободного падения, м/с.
hп.вс. = (0,041 · + 2,94) ·
= 1,53 м
Для нагнетательной линии:
ξ1 – отводы под углом 120º: А = 1,17; В = 0,09; ξ1 = 0,105;
ξ2 – отводы под углом 90º: А = 1; В = 0,09; ξ2 = 0,09;
ξ3 – нормальные вентили: ξ3 = 8;
ξ4 – выход из трубы ξ4 = 1.
Σξ = 2ξ1 + 10ξ2 + 2 ξ3 + ξ4
Σξ = 2 · 0,105 + 10 · 0,09 + 2 · 8 + 1 =18,11
Потерянный напор в нагнетательной линии находится:
hп.н. = (0,041· + 18,11) ·
= 2,39м
Общие потери напора:
hп = hп.вс. + hп.н. = 1,53+2,39=3,92м
Необходимый напор насоса рассчитывается по формуле:
H = + Hг + hп, (2.110)
где Р2 – давление в аппарате, в который подается жидкость, атм;
Р1 – давление в аппарате, из которого перекачивается жидкость, атм;
Нг – геометрическая высота подъема жидкости.
Т.к. установка работает при атмосферном давлении, то Р2 = Р1 = 1 атм, тогда
Н = 3 +3,92 = 6,92м
Полезная мощность насоса Nn, Вт, рассчитывается по формуле
Nn = ρ · g · Q · H (2.111)
Nn = 1088 · 9,81 · 3,2 · 10-4 · 6,92 = 23,63 Вт.
Мощность электродвигателя N, Вт, рассчитывается по формуле
N= , (2.112)
где ηп - коэффициенты полезного действия насоса
ηпер – коэффициенты полезного действия передачи от электродвигателя к насосу. Принимаем ηп = 0,8 и ηпер = 1 для центробежного насоса.
N = =29,54 Вт
Расчет штуцеров.
Для ванн, из которых жидкости вытекают самотеком, скорость ее движения в трубопроводе может быть принята до 0,5 м/с. Для ванн, из которых жидкости перекачиваются насосом, скорость ее движения в трубопроводе может быть принята до 2,0 м/с.
Часовой расход жидкости в ванне Q = 2,3 · 10-4 м3/с.
Внутренний диаметр штуцеров
d1 = = 0,024 м.
.
Расчет штуцеров
Поскольку жидкости из ванн электрохимического осаждения цинка, ванн обезжиривания, травления, улавливания и промывок вытекают самотеком, то скорость их движения в трубопроводе может быть принята до 0,5 м/с.
Расход жидкости в ванне нанесения цинка и обезжиривания 2,8 · 10-4 м3/с, а в ваннах пассивирования, травления, улавливания и промывок 2,3 · 10-4 м3/с.
Внутренний диаметр штуцеров определяется по формуле (3.4.4):
d1 = = 0,027м.
Принимаем наружный диаметр штуцера 30 мм, толщина стенки 3,5 мм, материал штуцера – углеродистая сталь.
D2 = = 0,024 м.
Принимаем наружный диаметр штуцера 30 мм, толщина стенки 3,5 мм, материал штуцера – углеродистая сталь.
Расчет автоматической линии
Номинальный фонд работы оборудования:
Т0= (365-t0-tn)ּτ-τnn*t*n, (3.1.1)
где t0- число выходных дней;
tп- число праздничных дней;
τ- время работы оборудования в сутки, ч;
tпп- время сокращения смены,ч;
tп*- количество праздничных дней с учётом сдвоенных праздников;
Т0= (365-104-7)*16-1*7=3422 ч.
Действительный фонд работы оборудования:
Тд= Т0*(1-kп), (3.1.2)
где kп- коэффициент простоя (0,08);
Тд= 3422*(1-0,08)=3148,24 ч
Эффективный фонд работы оборудования:
Тэ= Тд- (365- t0- tп)*τп.о., (3.1.3)
где τп.о.- время подготовительно- заключительных операций, ч.
Tэ= 3148,24- (365-104-7)*1=2894,24 ч.
Темп выхода автомата примем равным 3,5 мин.
Выбираем ритм выдачи R.
Определим количество основных ванн, nосн:
где – время технологического цикла, мин;
– ритм выдачи, мин.
где – время основных операций;
– вспомогательное время, которое необходимо на загрузку разгрузку ванны, принимаем 2 мин.
Задаемся предполагаемым R и рассчитываем количество ванн. Рассчитанное количество ванн округляем до большего целого числа и определяем коэффициент использования ванн Кисп, %
где – принятое количество ванн.
Полученные данные о количестве ванн и коэффициенте использовании ванн сводим в таблицу 10.
Таблица 10 – Зависимость количества ванн от ритма выдачи
Операция | R, мин. | 7 | 8 | 9 | 10 | 11 |
Цинкование (на подвесках) | n | 8 | 7 | 6 | 5 | 3 |
Кисп, % | 86 | 88 | 91 | 98,5 | 90 | |
Электрохимическое обезжиривание анодное | n | 1 | 1 | 1 | 1 | 1 |
Кисп, % | 71 | 63 | 55 | 50 | 45 | |
Травление
| n | 2 | 2 | 1 | 1 | 1 |
Кисп, % | 71,4 | 62,5 | 55,6 | 100 | 91 |
Принимаем наиболее оптимальный ритм выдачи равный 11 мин.
Sед.з.=Sгод* (1+α)*R/ Tэ*60, (3.1.4)
где Sгод- годовая программа попокрытию, м2;
Sед.з= [ 50000 · (1+0,03) · 11 ] / 2894,24 · 60 = 3,23 м2
где R-ритм выдачи;
Sгод – годовая производительность линии, м2/год;
a - коэффициент исправимого брака (0,03);
Тэф – эффективный фонд времени в году, ч.
Расчитаем количесво ванн:
t=
Необходимое количество ванн n:
n =3
Кисп=90%
Количество деталей на подвеске n, шт. определяется по формуле:
n = ,
n = шт.
Располагаем на 1 подвеску по 70 деталей. Выбираем подвеску с горизонтальным расположением стержней внутри рамы. Стержни изготовлены наклоненными в сторону краев рамы, что ускоряет стекание раствора с подвески, уменьшая тем самым унос раствора, а также позволяет избежать падение капель раствора с верхней зоны подвески на деталь.
Рассчитываем длину подвески по формуле:
![]() | (3.10) |
где – ширина деталей, мм;
bзаз – ширина зазора между деталями, мм;
– число деталей в одном ряду подвески, шт
мм
Рассчитываем высоту подвески:
![]() | (3.11) |
где hдет – высота деталей, мм;
hзаз – высота зазора между деталями, мм;Nдет. в. – число деталей по вертикали на подвеске, шт;
α – угол наклона поперечных перекладин подвески, град.
мм
Для расчета габаритных размеров ванны воспользуемся следующими формулами.
Длина ванны:
![]() | (3.12) |
где n1 – количество позиций в ванне, шт;
L1 – длина подвески, мм;
L2 – расстояние между подвесками (50-100), мм;
L3 – расстояние между торцом стенки и подвеской (100-150), мм.
L=1 мм
Принимаем длину ванны L= 950 мм.
Ширина ванны:
а) для электрохимических процессов:
![]() | (3.13) |
где n – число катодных штанг, шт;
b1 – расстояние от анода до внутренней стенки ванны (50), мм;
b2 – расстояние между анодам и катодом (150-200), мм;
B1 – ширина катодной штанги, мм;
d – толщина анода, мм.
мм
Принимаем ширину ванны для электрохимических процессов 830 мм.
б) для химических процессов:
![]() | (3.14) |
где n2 – число катодных штанг,
B1 – максимальный размер детали по ширине ванны, мм;
B3 – расстояние между внутренней стенкой ванны и подвеской, мм;
B4 – ширина подвески, мм.
B=830 мм
Принимаем ширину ванны для химических процессов 830 мм.
Высота ванны:
![]() | (3.15) |
Где Н2 – расстояние от дна до нижнего края подвески (150-300), мм;
Н3 – расстояние от зеркала электролита до верхнего края подвески (50), мм;
Н4 – расстояние от края ванны до зеркала электролита (100-150 мм без перемешивания, 150-250 мм с перемешиванием), мм
мм
Исходя из полученных расчетов, принимаем ванну по ГОСТ 23738 - 85 со следующими характеристиками:
Для ванн электрохимической обработки:
Длина: 950 мм
Ширина: 830 мм
Высота: 1270 мм
Для ванн химической обработки:
Длина: 950 мм
Ширина: 830 мм
Высота: 1270 мм
Полезный объем электролитов:
![]() | (3.16) |
Длина автооператорной линии LАОЛ, мм, рассчитывается по формуле:
![]() | (3.17) |
где Вван – внутренняя ширина ванны, мм;
Вс– ширина сушильной камеры, мм;
– ширина стойки загрузки-разгрузки, мм (600 мм);
– расстояние между сушильной камерой и стойкой загрузки-разгрузки, мм (400 мм);
n – количество ванн одного типа размера;
n0 – количество сопряжений ванн без бортовых отсосов;
n1– количество сопряжений ванн с односторонними бортовыми отсосами;
n2 – количество сопряжений ванн с двухсторонними бортовыми отсосами;
Δl0– зазор между ваннами без бортовых отсосов (160 мм), мм;
Δl1 – зазор между ваннами с односторонними бортовыми отсосами (290 мм), мм;
Δl2 – зазор между ваннами с двухсторонними бортовыми отсосами (390 мм), мм;
Δlб – расстояние от края бортового отсоса до ванны (212 мм), мм.
В размер ширины ванны для обезжиривания, активации, промывки необходимо учесть сливной карман (80 мм).
мм
Ширина линии рассчитывается по формуле:
![]() | (3.18) |
где В1 – расстояние от наружной стенки ванны до наружной плоскости опорной стойки, мм (В1 = 650 мм);
В2– ширина площадки обслуживания, мм (В 2 = 2000
мм).
B=830+650+2000=3480мм.
Высота линии принимается в зависимости от типа автооператора и вида обработки деталей. Так как в линии детали обрабатываются на подвесках и высота ванн составляет 1270 мм, то высота линии будет равна 3890 мм.
Принимается линия размером 13790×3480×3890 мм.
Расчет числа автооператоров.
Выбирается подвесной автооператор.
Технические характеристики:
грузоподъёмность, кг | 50 |
скорость горизонтального движения, м/с | 0,41/0,14 |
скорость вертикального движения грузозахватов, м/с | 0,3/0,15 |
наибольшая длина обслуживания ванн, мм | 900-1100 |
масса, кг | 40 |
габариты манипулятора | 3150×1210×2985 |
(3.1.20.)
где Т1 – суммарное время горизонтального перемещения, сек:
T′1.= L / n (3.1.21.)
где n1 – количество позиций в линии; ν1 – скорость горизонтального перемещения автооператора, м/с; L – длина линии.
Т′1 = 19352 / 0,22 ∙ 100= 879,6
Т″1 = 0,8796 / 0,22 = 4
T1 = 4 ∙ (14 – 1) = 52сек.
Т2 – суммарное время на подъем и опускание, сек:
, (3.1.22.)
где – среднее время подъема и опускания, сек; n2, n3, n4 – количество позиций с однократным, двукратным, трехкратным обслуживанием ванны соответственно (n2 = 10, n3=6, n4 = 1).
, (3.1.23.)
где h – геометрическая высота подъема, м;
Организация стока поверхностных вод: Наибольшее количество влаги на земном шаре испаряется с поверхности морей и океанов (88‰)...
Адаптации растений и животных к жизни в горах: Большое значение для жизни организмов в горах имеют степень расчленения, крутизна и экспозиционные различия склонов...
История создания датчика движения: Первый прибор для обнаружения движения был изобретен немецким физиком Генрихом Герцем...
Эмиссия газов от очистных сооружений канализации: В последние годы внимание мирового сообщества сосредоточено на экологических проблемах...
© cyberpedia.su 2017-2024 - Не является автором материалов. Исключительное право сохранено за автором текста.
Если вы не хотите, чтобы данный материал был у нас на сайте, перейдите по ссылке: Нарушение авторских прав. Мы поможем в написании вашей работы!