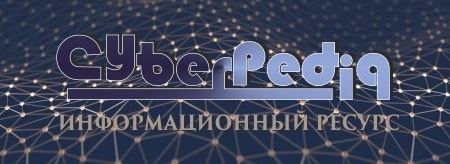
Историки об Елизавете Петровне: Елизавета попала между двумя встречными культурными течениями, воспитывалась среди новых европейских веяний и преданий...
Адаптации растений и животных к жизни в горах: Большое значение для жизни организмов в горах имеют степень расчленения, крутизна и экспозиционные различия склонов...
Топ:
Техника безопасности при работе на пароконвектомате: К обслуживанию пароконвектомата допускаются лица, прошедшие технический минимум по эксплуатации оборудования...
Методика измерений сопротивления растеканию тока анодного заземления: Анодный заземлитель (анод) – проводник, погруженный в электролитическую среду (грунт, раствор электролита) и подключенный к положительному...
Отражение на счетах бухгалтерского учета процесса приобретения: Процесс заготовления представляет систему экономических событий, включающих приобретение организацией у поставщиков сырья...
Интересное:
Национальное богатство страны и его составляющие: для оценки элементов национального богатства используются...
Подходы к решению темы фильма: Существует три основных типа исторического фильма, имеющих между собой много общего...
Финансовый рынок и его значение в управлении денежными потоками на современном этапе: любому предприятию для расширения производства и увеличения прибыли нужны...
Дисциплины:
![]() |
![]() |
5.00
из
|
Заказать работу |
|
|
2 Цель работы: Выбрать метод для изготовления печатного модуля c использованием SMT элементов и описать технологический маршрут изготовления печатного модуля.
3 Теоретические сведения
Surface-MountTechnology (SMT) - технология поверхностного монтажа.
В электронной промышленности существует шесть общих типов SMT сборки, каждому из которых соответствует свой порядок производства. Когда разработчик выбирает тип сборки, его целью должна быть минимизация числа операций, так как каждая операция может увеличивать промышленную стоимость. Существует специальный стандарт, в котором представлены основные виды сборок, разбитые по классам.
SMC и IPC документация по поверхностному монтажу на платы, IPC-7070, J-STD-013 и NationalTechnologyRoadmapforElectronicInterconnections включают следующие классификацию следующих схемы поверхностного монтажа:
Тип 1 - монтируемые компоненты установлены только на верхнюю сторону или interconnectingstructure
Тип 2 - монтируемые компоненты установлены на обе стороны платы или interconnectingstructure
Класс А - только through-hole (монтируемые в отверстия) компоненты
Класс В - только поверхностно монтируемые компоненты (SMD)
Класс С - смешанная: монтируемые в отверстия и поверхностно монтируемы компоненты
Класс Х - комплексно-смешанная сборка: through-hole, SMD, finepitch, BGA
Класс Y - комплексно-смешаннаясборка: through-hole, surface mount, Ultra fine pitch, CSP
Класс Z - комплексно-смешаннаясборка: through-hole, Ultra fine pitch, COB, Flip Chip, TCP
Операции используемы при различных типах сборки:
- нанесение пасты и установка SMT компонентов на верхнюю сторону платы.
- нанесение пасты и установка SMT на нижнюю сторону платы.
- нанесение клея и установка SMT компонентов на нижнюю сторону платы с последующем его высыханием.
|
- автоматическая установка DIP компонентов.
- автоматическая установка координатных компонентов (такие как светодиоды и т.п.).
- ручная установка других компонентов.
- пайка волной или пайка инфракрасным излучением.
- промывка плат.
- ручная пайка компонентов.
Рассмотрим основные варианты размещения компонентов на плате, применяемые разработчиками. Варианты, где используются корпуса компонентов типа: Ultrafinepitch, COB, FlipChip, TCP пока не рассматриваются, так как российскими разработчиками печатных плат они почти не используются.
Тип 1В: SMT Только верхняя сторона
Рисунок 3.1 – Расположение с одной стороны.
Тип 2B: SMT Верхние и нижние стороны
Рисунок 3.2 – Расположение с двух сторон.
На нижней стороне платы размещаются чип-резисторы и другие компоненты небольших размеров. При использовании пайки волной, они будут повторно оплавляться за счет верхнего (побочного) потока волны припоя. При размещение больших компонентов с обеих сторон, типа PLCC, увеличивают издержки производства, потому что компоненты нижней стороны должны устанавливаться на специальный токопроводящий клей. Данный тип называется IPC Type 2B.
Порядок проведения процесса:
- нанесение припойной пасты, установка компонентов, пайка, промывка нижней стороны;
- нанесение припойной пасты на верхнюю сторону печатной платы, установка компонентов, повторная пайка, промывка верхней стороны.
Специальный тип: SMT верхняя сторона в первом случае и верхняя и нижняя во втором, но PTH только верхняя сторона.
Рисунок 3.3– Расположение с двух сторон, с установкой в отверстия с верхней стороны.
Этот метод установки используется, когда имеются DIP компоненты, в SMT сборке. Процесс включает размещение DIP компонентов, вставляемых в отверстия перед SMT пайкой. При использовании данного метода убирается лишняя операция пайки волной или ручной пайки PTH компонентов, что значительно уменьшает стоимость изделия. Первое требование - способность компонентов противостоять вторичной пайки. Кроме того, размеры отверстия платы, контактные площадки и геометрия трафарета должны быть точно совмещены, чтобы достичь качественной спайки. Плата должна иметь сквозные металлизированные отверстия и может быть односторонней или двухсторонний, то есть компоненты могут размещаться как с верхней так и с нижней стороны.
|
Обязательным требованием при использовании данного метода является наличие сквозных металлизированных отверстий.
Порядок обработки односторонней печатной платы:
- нанесение припойной пасты, установка SMT компонентов, установка PTH компонентов, пайка, промывка верхней стороны.
Порядок обработки двухсторонней печатной платы:
- нанесение припойной пасты, установка SMT компонентов, повторное оплавление, промывка нижней стороны;
- установка PTH компонентов, пайка, промывка верхней стороны.
Тип 1С: SMT только верхняя сторона и PTH только верхняя сторона.
Рисунок 3.4 – Установка с верхней стороны на поверхность и в отверстия.
Данный метод является смешанной технологией сборки. Все модули SMT и PTH установлены на верхней стороне платы. Допускается установка некоторых компонентов монтируемых в отверстия (PTH) на верхней стороне платы, где размещены SMT компоненты для увеличения плотности. Данный тип сборки называется IPC Type 1C.
Порядок проведения процесса:
- нанесение припойной пасты, установка, оплавление, промывка верхней части SMT;
- автоматическая установка DIP, затем осевых компонентов (такие как светодиоды);
- ручная установка других компонентов;
- пайка волной PTH компонентов, промывка.
Тип 2С: SMT верхняя и нижняя стороны или PTH на верхней и нижней стороне.
Рисунок 3.5 – Установка на поверхность с двух сторон, а также в отверстия.
Установка поверхносто-монтируемых и монтируемых в отверстия (DIP) компонентов с обеих сторон платы не рекомендуется из-за высокой стоимости сборки. Эта разработка может требовать большого объема ручной пайки. Также не применяется автоматическая установка PTH компонентов из-за возможных конфликтов с SMT компонентами на нижней стороне платы. Данный тип сборки называется IPC Type 2C.
Порядок проведения процесса:
- нанесение припойной пасты, установка, пайка, промывка верхней стороны SMT;
- нанесение специального токопроводящего клея через трафарет, установка, фиксация SMT;
|
- автоматическая установка DIP и осевых компоненты;
- маскирование всей нижней стороны PTH компонентов;
- ручная установка других компонентов;
- пайка волной PTH и SMT компонентов, промывка;
- ручная пайка нижней стороны PTH компонентов.
Тип 2C: SMT только нижняя сторона или PTH только верхняя.
Рисунок 3.6 – Установка на поверхность с нижней стороны, в отверстия - с верхней.
Данный тип предполагает размещение поверхностного крепления с нижней стороны платы и PTH на верхней стороне. Он также является одним из очень популярных видов размещения, т.к. позволяет значительно увеличить плотность размещения компонентов. Тип имеет название IPC Type 2C.
Порядок обработки (PTH конфликтов на нижней стороне нет):
- нанесения клея через трафарет, установка, высыхания клея на нижней стороны SMT;
- автоматическая установка DIP, затем осевых компонентов;
- ручная установка других компонентов;
- пайка волной PTH и SMT компонентов, промывка.
Альтернативный порядок обработки (PTH конфликтов на нижней стороне):
- автоматическая установка DIP, затем осевых компонентов;
- точечное нанесение клея (диспенсорный метод), установка, высыхания клея на нижней стороны SMT;
- ручная установка компонентов;
- пайка волной PTH и SMT компонентов, промывка.
Тип 2Y: SMT верхняя и нижняя стороны или PTH только на верхней стороне.
Рисунок 3.7–верхняя и нижняя на плоскость, верхняя - в отверстия.
Данный тип позволяет располагать поверхностно монтируемые компоненты с обеих сторон платы, а DIP компоненты только на верхней. Это очень популярный вид сборки у разработчиков, позволяющий разместить компоненты с высокой плотность. Нижняя сторона SMT компонентов остается свободной от осевых элементов и ножек DIP компонентов. Например, нельзя размещать микросхемы между ножками DIP компонента.
Порядок проведения процесса (без размещения поверхностно монтируемых (SMT) между ножками монтируемых в отверстия (PTH) компонентов на нижней стороне платы):
- нанесение припойной пасты, установка, пайка, промывка верхней стороны части SMT;
- нанесение клея через трафарет, размещение, высыхание клея SMT на нижней стороне;
- автоматическая установка DIP, а затем осевых компонентов;
|
- ручная установка других компонентов;
- пайка волной PTH и SMT компонентов, промывка;
Альтернативный порядок проведения процесса (на нижней стороне платы поверхностно монтируемых (SMT) компоненты размещены между ножек монтируемых в отверстия (PTH)):
- нанесение припойной пасты, размещение, пайка, промывка верхней стороны части SMT;
- автоматическая установка DIP, затем осевых компонентов;
- точечное нанесение клея (диспенсорным методом), установка, высыхание клея нанижней стороны платы;
- ручная установка других компонентов;
- пайка волной PTH и SMT компонентов, промывка.
Общий технологический маршрут сборки печатных плат представлен на рисунке 3.8.
Рисунок 3.8 - Технологический маршрут сборки печатных плат.
Трафаретный метод нанесения припойной пасты.
Наиболее важным в массовом производстве печатных плат, является метод трафаретного нанесения припойной пасты, в котором паста продавливается через трафарет (окна) на контактные площадки печатной платы. Припойная паста уже содержит в себе и припой, и флюс, а их пропорция одна из важных характеристик пасты. Материалом трафарета может быть как сплав никеля, так и нержавеющая сталь. Отверстия в трафарете обычно прорезаются лазером или протравливаются.
В массовом производстве этот метод эффективен, но относительно не гибок, так как свой собственный трафарет (причем несколько) требуется для каждой платы. Гибкость достигается только за счет быстрой смены трафарета и автоматического распределения пасты. Основные этапы этого метода показаны на рисунке.
При проведении скребком по поверхности трафарета припойная паста продавливается сквозь отверстия в трафарете на контактные площадки. Наиболее важной фазой этого процесса является продвижение пасты вдоль поверхности трафарета, она должна продвигаться с правильной силой, углом и скоростью. Трафарет и скребок должны быть чистыми и паста должна иметь строго определенные характеристики для этой силы, угла и скорости. Ошибки в этих параметрах приводят к плохим характеристикам пайки, такие как непропай и другие. Половина ошибок всего процесса сборки печатных плат приходятся именно на процесс нанесения припойной пасты. Преимуществом метода трафаретного нанесения припойной пасты является то, что паста может быть нанесена слоем до 300 мкм с очень высокой точностью. Также трафарет позволяет наносить пасту толщиной до 0,65 мм (рис.3.9).
Рисунок 3.9 – Трафаретный метод нанесения припойной пасты
Дисперсный метод нанесения припоя.
Довольно часто встречающимся методом нанесения припойной пасты, применяемым в штучном и мелкосерийном производстве, является диспенсорный метод, в котором используется диспенсер - шприц. На рисунке 2.2 показано: 1 - крышка; 2 - давящий воздух; 3 - поршень; 4 - припойная паста; 5 - цилиндр; 6 - сопло; 7 - контактная площадка. Автоматическая дозировка осуществляется в соответствии с данными САПР при помощи сжатого воздуха. Паста поступает в виде "капель" непосредственно на контактные площадки печатной платы. Преимуществом диспенсорного метода является высокая гибкость его применения. Этим методом можно наносить пасту на контактные площадки толщиной от 0,75 мм (рис.3.10).
|
Рисунок 3.10 – Устройство для нанесения припоя дисперсным методом.
Установка компонентов на плату:
- ручная;
- автоматическая.
Пайка.
Пайка двойной волной припоя
Совершенствование конструкции платы оказалось недостаточным для достижения высокого уровня годных при традиционных способах изготовления изделий с простыми компонентами, монтируемыми на поверхность обратной стороны плат. Потребовалось изменить технологический процесс пайки волной, внедрив вторую волну припоя. Первая волна делается турбулентной и узкой, она исходит из сопла под большим давлением (рис. 1). Турбулентность и высокое давление потока припоя исключает формирование полостей с газообразными продуктами разложения флюса. Однако турбулентная волна все же образует перемычки припоя, которые разрушаются второй, более пологой ламинарной волной с малой скоростью истечения. Вторая волна обладает очищающей способностью и устраняет перемычки припоя, а также завершает формирование галтелей. Для обеспечения эффективности пайки все параметры каждой волны должны быть регулируемыми. Поэтому установки для пайки двойной волной должны иметь отдельные насосы, сопла, а также блоки управления для каждой волны. Установки для пайки двойной волной рекомендуется приобретать вместе с дешунтирующим ножом, служащим для разрушения перемычек из припоя (рис.3.11).
Рисунок 3.11 – Пайка двойной волной.
Пайка двойной волной припоя применяется в настоящее время для одного типа коммутационных плат: с традиционными компонентами на лицевой стороне и монтируемыми на поверхность простыми компонентами (чипами и транзисторами) на обратной. Некоторые компоненты для ТПМК (даже пассивные) могут быть повреждены при погружении в припой во время пайки. Поэтому важно учитывать их термостойкость.
Если пайка двойной волной применяется для монтажа плат с установленными на их поверхности компонентами сложной структуры, необходимы некоторые предосторожности:
- применять поверхностно монтируемые ИС, не чувствительные к тепловому воздействию;
- снизить скорость транспортера;
- проектировать коммутационную плату таким образом, чтобы исключить эффект затенения.
Хорошо разнесенные, не загораживающие друг друга компоненты способствуют попаданию припоя на каждый требуемый участок платы, но при этом снижается плотность монтажа. При высокой плотности монтажа, которую позволяет реализовать ТПМК, с помощью данного метода практически невозможно пропаять поверхностно монтируемые компоненты с четырехсторонней разводкой выводов (например, кристаллоносители с выводами). Чтобы уменьшить эффект затенения, прямоугольные чипы следует размещать перпендикулярно направлению движения волны. Трудно паять двойной волной припоя транзистор в корпусе 50Т-89, поскольку он имеет довольно массивный центральный вывод, что затрудняет его равномерное смачивание припоем (и растекание припоя) по всей поверхности.
Пайка расплавлением дозированного припоя с инфракрасным (ИК) нагревом.
Процесс пайки компонентов, собранных на коммутационной плате, с помощью ИК-нагрева аналогичен пайке в ПГФ, за исключением того, что нагрев платы с компонентами производится не парами жидкости, а ИК-излучением.
Основным механизмом передачи тепла, используемым в установках пайки с ИК-нагревом, является излучение. Передача тепла излучением имеет большое преимущество перед теплопередачей за счет теплопроводности и конвекции в описанных ранее методах, так как это единственный из механизмов теплопередачи, обеспечивающий передачу тепловой энергии по всему объему монтируемого устройства. Остальные механизмы теплопередачи обеспечивают передачу тепловой энергии только поверхности монтируемого изделия. В отличие от пайки в ПГФ, в процессе пайки с ИК-излучением скорость нагрева регулируется изменением мощности каждого излучателя и скорости движения транспортера с коммутационными платами. Поэтому термические напряжения в компонентах и платах могут быть снижены посредством постепенного нагрева микросборок.
Основным недостатком пайки с ИК-нагревом является то, что количество энергии излучения, поглощаемой компонентами и платами, зависит от поглощающей способности материалов, из которых они изготовлены. Поэтому нагрев осуществляется неравномерно в пределах монтируемого устройства. Пайка кристаллоносителей без выводов или с J-образными выводами может оказаться невозможной в установках с ИК-нагревом, если компонент непрозрачен для ИК-излучения.
В некоторых установках для пайки с ИК-нагревом вместо ламп ИК-излучения применяются панельные излучающие системы. В этом случае излучение имеет намного большую длину волны, чем излучение традиционных источников. Излучение такой излучающей системы не нагревает непосредственно микросборку, а поглощается технологической средой, которая в свою очередь передает тепло микросборке за счет конвекции. Этот способ пайки устраняет ряд недостатков, присущих традиционной пайке с ИК-нагревом, таких, как неравномерный прогрев отдельных частей микросборки и невозможность пайки компонентов в корпусах, непрозрачных для ИК-излучения.
Панельные излучатели имеют ограниченный срок службы и обеспечивают намного меньшую скорость нагрева, чем традиционные источники ИК-излучения. Однако при их использовании может не потребоваться технологическая среда из инертного газа.
Технологические установки пайки ИК излучением
В зависимости от соотношения температур источника излучения и нагреваемого объекта процессы нагрева можно разделить на термодинамически равновесные и неравновесные. При равновесном нагреве температура нагревателя и объекта близки друг к другу (например, нагрев в парах кипящей жидкости), при неравновесном - значительно отличаются. На практике желательно иметь равновесный режим нагрева, позволяющий устранить неравномерность нагрева и другие отрицательные факторы.
Конструктивно такие излучатели представляют собой керамические панели больщих размеров со значительным количеством воздушных камер, работающих при температуре 280-320° С. В таких устройствах до 60 % тепловой энергии доставляется к объекту за счет естественной конвекции, 40 % - при помощи средневолнового ИК излучения. Такие комбинированные установки производят нагрев объекта в режиме, близком к равновесному, и в настоящее время широко используются при монтаже ТМП ФУ.
Конструкция типичной установки ИК оплавления приведена на рисунке 3.12. Установка состоит из корпуса 1, внутри которого расположено несколько зон нагрева, в каждой из которых поддерживается заданный тепловой режим. В первой и второй зонах производят постепенный предварительный нагрев изделия 2 с помощью плоских нагревателей 3. Пайку производят в третьей зоне быстрым нагревом объекта выше температуры плавления припоя с помощью кварцевых ИК ламп 4, затем объект охлаждают с помощью устройства 5.
Рисунок 3.12 – Схема установки пайки ИК-излучением.
Печатные платы транспортируются через установку на ленточном (обычно сетка из нержавеющей стали) конвейере 6. Режимы работы нагревателя и скорость конвеера регулируются с помощью микропроцессорной системы 7, температурный профиль вдоль установки отображается в графической и цифровой форме на экране дисплея 8.
Характеристики температурного профиля, т. е. значения температур в каждой зоне, возможно изменять в широких пределах, также возможно иметь библиотеку типовых режимов оплавления для печатных плат различных типоразмеров.
Пайка расплавлением дозированного припоя в парогазовой фазе (ПГФ).
Пайка расплавлением дозированного припоя применима только к микросборкам с поверхностным монтажом. Процесс начинается с нанесения способом трафаретной печати припойной пасты на контактные площадки коммутационной платы. Затем на поверхность платы устанавливаются компоненты. В ряде случаев припойную пасту просушивают после нанесения, с целью удаления из ее состава летучих ингредиентов или предотвращения смещения компонентов непосредственно перед пайкой. После этого плата разогревается до температуры расплавления. В результате образуется паяное соединение между контактной площадкой платы и выводом компонента. Такая техника пайки применима к коммутационным платам без монтируемых в отверстия компонентов, т. е. с набором только поверхностно монтируемых компонентов любых типов.
Метод пайки в парогазовой фазе является разновидностью пайки расплавлением дозированного припоя, в ходе которой пары специальной жидкости конденсируются на коммутационной плате, отдавая скрытую теплоту парообразования открытым участкам микросборки. При этом припойная паста расплавляется и образует галтель между выводом компонента и контактной площадкой платы. Когда температура платы достигает температуры жидкости, процесс конденсации прекращается, тем самым заканчивается и нагрев пасты. Повышение температуры платы, от ее начальной температуры (например, окружающей среды перед пайкой) до температуры расплавления припоя, осуществляется очень быстро и не поддается регулированию. Поэтому необходим предварительный подогрев платы с компонентами для уменьшения термических напряжении в компонентах и местах их контактов с платой. Температура расплавления припоя также не регулируется и равна температуре кипения используемой при пайке жидкости. Такой жидкостью является инертныйфторуглерод, например РС-70 производства фирмы ЗМ.
Рисунок 3.13 – Схематическое представление пайки ПГФ с двумя технологическими средами.
Существуют два типа установок для пайки в парогазовой фазе: с применением одной либо двух рабочих жидкостей. В первых установках для пайки в ПГФ применялись две рабочих жидкости (рисунок 3.13), при этом использовались обычно несколько установок пайки в составе производственной линии. С целью предотвращения утечки паров дорогого фторуглерода и припоя поверх основной технологической среды из инертного фторуглерода создавалась дополнительная технологическая среда из более дешевого фреона. Основной недостаток этих установок состоял в том, что на границе двух технологических сред происходило образование различных кислот. Поэтому для защиты коммутационных плат (защита коммутационных плат необходима в первую очередь от разрушающего действия кислот на материал коммутации (химическая, а затем электрохимическая коррозия).Кроме того, рабочая часть контейнера установки пайки в ПГФ должна изготовляться из коррозионностойкого материала, что отражается на стоимости такого оборудования) требовались системы нейтрализации кислот.
Установки для пайки с двумя рабочими жидкостями оказались непригодны для линий сборки электронной аппаратуры. Поэтому в 1981 г. фирмой НТС стали выпускаться установки для пайки в ПГФ, встраиваемые в технологические сборочно-монтажные линии. Такие установки имеют относительно небольшие входное и выходное отверстия, позволяющие реализовать систему с одной технологической средой (рис. 2). Приведенная на рисунке 3.14 конструкция обеспечивает возможность включения установки в состав технологической линии.
Рисунок 3.14 – Схематическое представление пайки в ПГФ с использованием одной технологической среды.
При использовании установки для пайки в ПГФ таких компонентов, как чип-конденсаторы и чип-резисторы, может возникнуть проблема, известная как "эффект опрокидывания компонента". Причина опрокидывания компонентов до конца не изучена, и универсальных средств, для избежания этого в настоящее время не существует.
Необходимо варьировать параметры процесса пайки до тех пор, пока не прекратится опрокидывание компонентов.
Лазерная пайка.
Лазерная пайка (пайка лучом лазера) не относится кгрупповым методом пайки, поскольку монтаж ведется по каждому отдельному выводу либо по ряду выводов. Однако бесконтактность приложения тепловой энергии позволяет повысить скорость монтажа до 10 соединений в секунду и приблизиться по производительности к пайке в паровой фазе и ИК излучением
По сравнению с другими методами лазерная пайка обладает рядом следующих преимуществ. Во время пайки печатная плата и корпуса элементов практически не нагреваются, что позволяет монтировать элементы, чувствительные к тепловым воздействиям. В связи с низкой температурой пайки и ограниченной областью приложения тепла резко снижаются температурные механические напряжения между выводом и корпусом. Выбор материала основания не является критическим. Кратковременные действия тепла - 20...30 мс, резко снижаются толщина слоя интерметаллидов, припой имеет мелкозернистую структуру, что положительно сказывается на надежности ПС. Установки лазерной пайки могут быть полностью автоматизированы, при этом возможно использовать данные САПР для печатных плат.
Возможна пайка плат с высокой плотностью компоновки элементов, с размерами контактных площадок до 25 мкм, без образования перемычек на соседние соединения или их повреждения.
При использовании хорошо просушенной паяльной пасты выполненные с помощью лазерной пайки ПС не образуют шариков припоя или перемычек, в результате чего отпадает необходимость применять паяльные маски.
При использовании лазерной пайки нет необходимости в предварительном подогреве многослойной печатной платы, что обычно необходимо делать при пайке в паровой фазе для предотвращения расслоения платы. Не требуется также создавать какую-либо специальную газовую среду. Процесс пайки ведется в нормальной атмосфере без применения инертных газов.
Пайка в глухие отверстия.
Компоненты с планарными выводами являются более компактными по габаритам, чем со штыревыми выводами, расположенными по краям корпуса. Однако компоненты с планарными выводами при типовой формовке выводов и установке на ПП требует значительных площадей для расположения ламелей. Так, микросхема с 14-ю планарными выводами и корпусом шириной 10мм (рис. 3.15), имеет габарит установочного места 18 мм. Это объясняется формовкой выводов, нижняя горизонтальная часть которых имеет длину 2,1 мм. Для рельефных плат можно изменить формовку выводов таких микросхем так, как это показано на рисунке, и проводить их установку в "глухие отверстия". "Глухие отверстия" имеют диаметр на поверхности диэлектрика, равный ширине ламели. Такое конструктивное решение сокращает площадь установочного места на 20-25%. Учитывая высокие трассировочные возможности РМ это повышает степень интеграции компонентов на РП на 18-20%.
Рисунок 3.15 – Пример монтажа МС с планарными выводами.
4 Порядок выполнения работы
4.1 Выбрать метод нанесения припойной пасты на ПП.
4.2 Выбрать метод установки элементов на ПП.
4.3 Выбрать метод пайки элементов.
4.4 Описать технологический маршрут изготовления печатного модуля.
5 Содержание отчета
5.1 Представить краткое описание по выполнению пп.4. 1– 4.4.
6 Контрольные вопросы
6.1 В чем суть процесса пайки ПГФ метода?
6.2 В чем суть процесса пайки ИК методом?
6.3 Что такое фоторезист?
6.4 В чем суть процесса пайки лазером?
6.5 Особенности пайки двойной волной?
6.6 В чем заключается метод трафаретного нанесения пасты?
6.7 Опишите основные этапы технологического маршрута сборки печатных плат.
6.8 Перечислите все варианты размещения компонентов на плате.
Лабораторная работа 13
Основные правила ЕСКД выполнения чертежа печатной платы
2 Цель работы: Оформить чертеж печатной платы (ПП) в соответствии с требованиями ЕСКД.
3 Теоретические сведения
Оформление чертежа печатной платы (деталь)
Чертеж печатной платы является основным конструкторским документом. Он содержит графическую и текстовую части.
Текстовая часть в виде технических требований к чертежу располагается над рамкой (основной надписью).
Графическая часть состоит из двух видов:
- главного, на котором изображены контур платы, трасса (рисунок) проводников и отверстия;
- вида сверху или сбоку, на котором указывается толщина материала платы и способ обработки фронтальных поверхностей.
Чертеж на печатные платы выполнять в соответствии с требованиями ГОСТ 2.417-78 «ЕСКД. Правила выполнения чертежей, печатных плат» в масштабе 2:1; 4:1.
При оформлении главного вида чертежа печатной платы необходимо руководствоваться следующими основными рекомендациями:
1. На чертеже печатной платы в соответствии с требованиями ГОСТ 2.307-63 «ЕСКД. Нанесение размеров и предельных отклонений» необходимо указывать размеры одним из следующих способов:
– нанесением размерных и выносных линий с указанием размерных чисел;
– с помощью координатной сетки в прямоугольной системе координат;
– комбинированным способом, используя размерные и выносные линии и координатную сетку в прямоугольной системе координат.
При выполнении чертежей печатных плат лучше всего использовать комбинированный способ нанесения размеров.
2. Нумеровать линии сетки, нанося шаги координатной сетки. Шаг нумерации определять конструктивно с учетом насыщенности и масштаба изображения платы. Можно шаги нумеровать через два или пять.
3. Координатную сетку на главном виде чертежа ПП наноситьсплошными тонкими линиями. Допускается выделять на чертеже отдельные линии координатной сетки, чередующиеся через определенные интервалы, либо их не наносить. При этом на чертеже следует применять указания типа «Линии координатной сетки нанесены через
одну».
4. Принимать за нуль начало отсчета координатной сетки в прямоугольной системе координат на главном виде печатной платы:
– центр крайнего левого нижнего отверстия, находящегося на поле платы;
– левый нижний угол печатной платы.
5. Размерные линии на сборочных чертежах располагают на расстоянии не менее 10 мм от линии наружного контура ФУ.
6. Выносные линии должны выходить за концы стрелок размерной линии на 1–5 мм.
7. Указывать предельные отклонения для всех размеров, нанесенных на чертеже печатной платы.
8. Допуски на линейные размеры установить согласно СТ СЭВ 145-75, СТ СЭВ 144-78 для сопрягаемых размеров по12 квалитету, а для свободных – по 14 квалитету. Для поверхностей типа «вала» квалитет обозначается буквой h, а для поверхностей типа «отверстия» –буквой H. После буквы проставляют номер квалитета. Во всех других
случаях желательно проставить не квалитет, а отклонение от размера.
Для этого нужно воспользоваться приложением 40.
9. Печатные проводники на чертеже изображать одной линией, являющейся осью симметрии проводника (в технических требованиях указывать численное значение ширины проводника). Ширина линии должна быть больше в 2–3 раза ширины линии контура платы. Печатные проводники шириной более 2,5 мм изображают двумя линиями
со штриховкой под углом 45°. При этом, если они совпадают с линиями координатной сетки, численные значения ширины на чертеже не указывают.
10. Печатные проводники изображать в виде отрезков линий, проведённых параллельно линиям координатной сетки или по ним, при необходимости угол наклона проводника выполнять кратным 15°.
11. Те участки на печатной плате, которые нельзя занимать проводниками и контактными площадками, на чертеже выделить штрихпунктирной линией.
12. Допускаются элементы печатного рисунка изображать условно, а их размеры и конфигурацию оговаривать в технических требованиях чертежа, например, монтажные отверстия, близкие по диаметру, выполнять в виде окружности одного размера с обязательным показом условного обозначения диаметра отверстия. Пример условного обозначения представлен в лабораторной работе 9 (табл. 3.4).
13. Изображать в виде одной окружности круглые отверстия, имеющие зенковку, и круглые контактные площадки с круглыми отверстиями (в том числе и с зенковкой). Их формы и размеры оговаривать на поле чертежа в технических требованиях.
14. Выделять отдельные элементы рисунка печатной платы (проводники, экраны, изоляционные участки и т. п.) на чертеже штриховкой, зачернением, растиранием и т. п.
15. На чертеже показывать форму вырезов в широких проводниках и экранах с помощью выносного элемента на поле чертежа. Размеры вырезов и расстояния между ними обязательно указывать.
16. Значение диаметров отверстий, их условные обозначения, значения диаметров зенковки, наличие металлизации и количество отверстий сводить в таблицу. Пример ее заполнения приведен в таблице 3.1. Отдельные графы этой таблицы допускается не заполнять, если отверстия выполняются без зенковки или без металлизации.
Таблица 3.1 – Пример заполнения таблицы
17. Обозначать шероховатость поверхности на чертежах печатных плат в соответствии с ГОСТ 2.309–73 «ЕСКД. Обозначения шероховатости поверхностей» и ГОСТ 2.789–73 «Параметры и характеристики шероховатости».
Согласно ГОСТ 2.309–73 для обозначения шероховатости поверхности печатной платы применяют знаки, приведённые на рисунке 3.1.
Рисунок 3.1.- Изображение знаков, обозначающих шероховатость поверхностей.
Знак используется в тех случаях, когда метод (вид) обработки данной поверхности печатной платы не устанавливают (допустим, печатную плату получают вырубкой на штампе, прессованием и т. д.).
Знак применяется в тех случаях, когда поверхность платы образована удалением слоя материала, например, точением, сверлением, фрезерованием, полированием и т. п.
Знак обозначает, что поверхность образована без удаления слоя материала, например, прокатом, волочением, объёмной штамповкой и т.п. Этим же знаком указывают поверхности, не обрабатываемые по данному чертежу печатной платы.
Высота h знака должна быть приблизительно равна применяемой на чертеже печатной платы высоте цифр размерных чисел.
Высота H знака равна (1,5-3) h. Толщина линий знаков приблизительно равна половине толщины сплошной основной линии, применяемой на чертеже печатной платы.
18. Располагать знак шероховатости печатной платы на линии контура платы или выносных линиях (по возможности ближе к размерной линии).
19. Для обозначения одинаковой шероховатости всех обрабатываемых поверхностей печатной платы в правом верхнем углу чертежа помещают знак одинаковой шероховатости (). Это означает, что все обрабатываемые поверхности печатной платы, на которых нет указания шероховатости или знака, имеют шероховатость, рас
положенную перед обозначением (). Размеры знака, взятого в скобках, изображают одинаковыми с размерами знаков шероховатости, нанесённых на чертеже печатной платы.
Размеры и толщина линий знака в обозначении шероховатости, вынесенном в правый верхний угол чертежа, должны быть приблизительно в 1,5 раза больше, чем в обозначениях, нанесённых на изображение печатной платы.
Параметры шероховатости (один или несколько) выбираются из приведенной номенклатуры:
Ra – среднее арифметическое отклонение профиля, мкм;
Rz – высота неровностей профиля по десяти точкам, мкм;
Rmax – наибольшая высота профиля;
Sm – средний шаг неровностей;
S – средний шаг местных выступов профиля;
tp – относительная опорная длина профиля, где р – значения уровня сечения профиля.
Параметр Ra является предпочтительным.
Числовые значения всех параметров приведены в ГОСТ 2.789–73.
20. Шероховатость проставлять для всех поверхностей: торцов, отверстий, самих плат. Состояние поверхности со знаком должно удовлетворять требованиям, установленным соответствующим стандартом, или техническим условиям, причём на этот документ даётся ссылка в виде указания материала печатной платы в графе 3 основной надписи чертежа.
21. Требования к маркировке печатных плат следующие:
– на свободном ме
|
|
Общие условия выбора системы дренажа: Система дренажа выбирается в зависимости от характера защищаемого...
Особенности сооружения опор в сложных условиях: Сооружение ВЛ в районах с суровыми климатическими и тяжелыми геологическими условиями...
Опора деревянной одностоечной и способы укрепление угловых опор: Опоры ВЛ - конструкции, предназначенные для поддерживания проводов на необходимой высоте над землей, водой...
Состав сооружений: решетки и песколовки: Решетки – это первое устройство в схеме очистных сооружений. Они представляют...
© cyberpedia.su 2017-2024 - Не является автором материалов. Исключительное право сохранено за автором текста.
Если вы не хотите, чтобы данный материал был у нас на сайте, перейдите по ссылке: Нарушение авторских прав. Мы поможем в написании вашей работы!