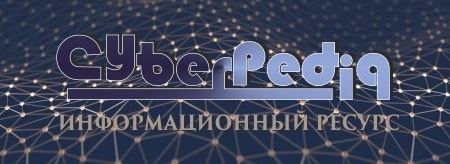
История развития пистолетов-пулеметов: Предпосылкой для возникновения пистолетов-пулеметов послужила давняя тенденция тяготения винтовок...
Особенности сооружения опор в сложных условиях: Сооружение ВЛ в районах с суровыми климатическими и тяжелыми геологическими условиями...
Топ:
Когда производится ограждение поезда, остановившегося на перегоне: Во всех случаях немедленно должно быть ограждено место препятствия для движения поездов на смежном пути двухпутного...
Определение места расположения распределительного центра: Фирма реализует продукцию на рынках сбыта и имеет постоянных поставщиков в разных регионах. Увеличение объема продаж...
Марксистская теория происхождения государства: По мнению Маркса и Энгельса, в основе развития общества, происходящих в нем изменений лежит...
Интересное:
Наиболее распространенные виды рака: Раковая опухоль — это самостоятельное новообразование, которое может возникнуть и от повышенного давления...
Искусственное повышение поверхности территории: Варианты искусственного повышения поверхности территории необходимо выбирать на основе анализа следующих характеристик защищаемой территории...
Как мы говорим и как мы слушаем: общение можно сравнить с огромным зонтиком, под которым скрыто все...
Дисциплины:
![]() |
![]() |
5.00
из
|
Заказать работу |
|
|
4..
Гусеничные машины предназначены для использования в качестветягачей-транспортеров в сложных климатических условиях.
Основные преимущества передвижения на гусеницах перед колесными транспортными средствами, в том, что они находятся в контакте с большей площадью, что позволяет обеспечить низкое давление 0,3-1,2 кгс /см2, чем колесное транспортное средство того же веса. Это делает их пригодными для использования на мягких поверхностях: грязь, лед, снег.
Основные узлы пневмоколесных и гусеничных тракторов — двигатель, силовая передача (трансмиссия), остов (рама), ходовое устройство, система управления, вспомогательное и рабочее оборудование.
Гусеничные тракторы оснащаются дизелями и карбюраторными двигателями, механическими, гидромеханическими и электромеханическими трансмиссиями.
Расположение двигателя может быть передним, средним и задним. Наибольшее распространение получили гусеничные тракторы с дизелями и передним расположением двигателя. Трансмиссия служит для передачи крутящего момента от вала двигателя к ведущим звездочкам гусеничных лент (гусениц), плавного трогания и остановки машины, изменения тягового усилия трактора в соответствии с условиями движения, изменения скорости и направления его движения, а также привода рабочего оборудования.
Пневмоколесные тягачи
Тягачи на пневмоколесном ходу приходят на смену гусеничным машинам. Такие тягачи и агрегатные шасси предназначены для работы с навесным и прицепным оборудованием различных видов.
Пневмоколесные тягачи по сравнению с гусеничными тракторами более просты по конструкции, имеют меньшую массу, дешевле в изготовлении и эксплуатации. Большие скорости тягачей, достигающие 40—50 км/ч, хорошая маневренность в значительной мере способствуют повышению производительности работающих с ними машин.
|
Предусматривается выпуск двухосных тягачей мощностью 12—500 кВт и одноосных тягачей мощностью от 60 до 1000 кВт. Приведены основные параметры пневмоколесных тягачей и колесных тракторов, выпускаемых в СССР.
Кинематические схемы двухосного и одноосного пневмоколесных тягачей. От двигателя внутреннего сгорания через гидротрансформатор и коробку перемены передач вращение передается переднему и заднему мостам колесного хода. Поворотными являются задние колеса тягача. Для гидравлического привода навесного оборудования служат гидронасосы.
В одноосном тягаче вращение от двигателя через коробку перемены передач, раздаточную коробку передается ведущему мосту тягача. Для привода гидронасосов служит коробка отбора мощности.
Рис. 2.5. Пневмоколесные тракторы: а — с передними управляемыми колеаами; б — с шарнирно-сочлененной рамой; в — схема поворота полурам
Пневмоколесные тягачи предназначены для работы с различными видами сменного навесного и прицепного строительного оборудования. В сравнении с гусеничными тракторами они более просты по конструкции, имеют меньшую массу, большую долговечность, дешевле в изготовлении и в эксплуатации. Большие скорости тягачей (до 50 км/ч), хорошая маневренность в значительной мере способствуют повышению производительности агре-гатированных с ними строительных машин.
5.
Основными показателями, характеризующими физико-механические свойства грунтов, являются следующие.
1. Гранулометрический состав, представляющий процентное содержание по весу частиц различной крупности: гальки и щебня (40 мм), гравия (2—40 мм), песка (0,25—2 мм), песчаной пыли (0,05— 0,25 мм), пылеватых частиц (0,005—0,05 мм) и глинистых частиц (менее 0,005 мм).
2. Влажность, характеризующая наличие в грунте воды, которая существенно влияет на сопротивляемость грунтов деформациям. Влажность определяется путем высушивания при t = 105° С пробы грунта до получения постоянного веса и вычисления в процентах заключающейся в ней воды по формуле w=(а-в)/в * 100%
|
где w — влажность пробы в %-; а — вес влажной пробы; в — вес высушенной пробы.
3. Плотность, представляющая собой отношение массы грунта к его объему при естественной влажности (р = 1,5—2 т/м3).
4. Пористость — объем пор, заполненный водой и воздухом, в процентах от общего объема грунта.
5. Связность — способность грунта сопротивляться разрушению (рассыпанию) на частицы под действием внешних нагрузок. Примером несвязных грунтов являются сухие пески, а связных — глина.
6. Пластичность — свойство грунта деформироваться под действием внешних сил и сохранять деформацию после прекращения действия последних.
7. Угол естественного откоса φ — угол у основания конуса, который образуется при отсыпании разрыхленного грунта с некоторой высоты. Величина этого угла зависит от коэффициента внутреннего трения и связности.
8.Способность грунта прилипать к поверхности различных предметов — липкость. При разработке липких грунтов (большинство пластичных грунтов при достаточной влажности) величина усилий, затрачиваемых на преодоление сопротивления налипанию грунта на рабочий ТРН2601орган, определяется следующим образом: РЛ= рл*F
где РЛ — сила сопротивления налипанию; рл — величина удельного сопротивления налипанию; F — площадь соприкосновения рабочего органа с грунтом.
9. Коэффициент трения грунта о сталь зависит от вида и состояния грунта, а также от состояния поверхности стали. Коэффициент трения стали по грунтам нарушенной структуры составляет приблизительно две трети величины коэффициента трения по грунтам ненарушенной структуры.
10.Коэффициент разрыхления крх равен отношению объема разрыхленного при разработке грунта к объему, который он занимал в естественном залегании. С течением времени разрыхленный грунт уплотняется, но первоначальную плотность восстанавливает очень долго.
11.Сопротивление грунта смятию определяется коэффициентом сопротивления смятию рс, представляющим собой величину нагрузки на 1 см2 поверхности грунта, под действием которой опорная поверхность погружается на 1 см.
ОСНОВНЫЕ СПОСОБЫ РАЗРУШЕНИЯ ГРУНТОВ
|
Получили распространение следующие способы разрушения грунтов:
1) механический, при котором отделение грунта от массива осуществляется ножевым или ковшовым рабочим органом машины;
2) гидравлический, при котором грунт разрушается и удаляется струей воды (размыв); при работе под водой применяется всасывание размытого грунта и его удаление из зоны забоя по пульпопроводу;
3) взрывной, при котором грунт разрушается давлением газов, выделяющихся при взрыве;
4) термический, основанный на растрескивании поверхности грунта в результате быстрого и неравномерного нагрева скоростной струей высокотемпературных газов.
Применяются и комбинированные методы разработки грунтов, например, гидравлический способ может комбинироваться с механическим, механический с термическим и т. д.
Механический способ наиболее распространен, с его помощью осуществляется не менее 80—85% всего объема земляных работ. Это объясняется его универсальностью — применимостью для всех типов грунтов.
Гидравлический способ получил широкое распространение при производстве подводно-технических работ, связанных с прокладкой трубопроводов по дну водоемов.
Взрывной и термический нашли применение при разработке мерзлых и скальных грунтов. Взрывной способ применяется также при производстве работ в сложных условиях на труднодоступных участках трассы, например, при сооружении полок в горах и разработке траншей на болотах.
Энергоемкость механического способа в среднем не превышает 0,3 квт*ч на 1 м3 грунта. Энергоемкость гидравлического способа выше энергоемкости механического и составляет в среднем от 0,2 до 3 квт-ч на 1 м3 грунта, зато применение этого способа для транспортирования разработанного грунта более эффективно. Этим объясняется широкое применение комбинированного гидромеханического способа, при котором разрушение грунта производится механическими средствами с гидравлической эвакуацией из зоны забоя.
Взрывной способ разрушения грунта ТРН2601требует энергии только на бурение подготовительных скважин от 0,8 до 1,1 квт-ч на 1 м3 грунта. Если учесть, что для последующей разработки 1 м3 грунта необходимо от 2 до 4 кг взрывчатки, то энергоемкость этого способа значительно возрастет. Поэтому взрывным способом выполняется только 1—3% всего объема земляных работ.
|
6.
Бульдозер является навесным оборудованием, состоящим из плоского отвала 3 с ножами, толкающих брусьев -(или рамы) 4 и системы управления отвалом 2, смонтированным на гусеничном тракторе / или двухосном пневмоколесном тягаче.
Бульдозеры предназначены для послойной, разработки и перемещения (на расстояние до 100 м) легких, средних и тяжелы (разрыхленных взрывом, скальных и смерзшихся) грунтов. Их применяют при возведении насыпей, дамб обвалования, рытье водоподйодящих каналов и широких траншей, засыпке рвов, ям, траншей, оврагов и котлованов, планировке строительных площадок и -трасс строительства трубопроводов с предварительной расчисткой их от камней, кустарника, пней, мелких деревьев и снега (в зимнее время).
Рабочий процесс бульдозера: при движении тяга-' ча вперед отвал механизмом управления опускается в рабочее положение, ножами срезает слой грунта и перемещает его волоком. Бульдозер с неповоротным поверхности земли к месту отвалом отсыпки; после выгрузки грунта отвал поднимается в транспортное положение и машина возвращается задним ходом к месту набора грунта.
Бульдозеры классифицируют: по способу установки рабочего органа в плане — на неповоротные (простые) с постоянным расположением отвала перпендикулярно продольной оси базовой машины и поворотные (универсальные) с переменным расположением отвала, по типу ходового устройства базовой машины — на гусеничные и пневмоколесные; по конструкции ТРН2601 системы управления отвалом — с канатно-блочным и гидравлическим управдением; по номинальному тяговому усилию базовой машины— малогабаритные (1,0—3,0 тс, 9,8—29,4 кН), легкие (3,0—6,0 тс, 29,4—58,8 кН), средние (6,0—15 тс, 58,8—147 кН) и тяжелые (15—35 тс, 147—343 кН). Наиболее распространены гусеничные бульдозеры с гидравлической системой управления отвалом.
Рыхлители применяют для послойного разрушения плотных каменистых, скальных и мерзлых грунтов перед разработкой их (или погрузкой) землеройными машинами, при отрывке котлованов и широких траншей, а также для взламывания покрытий дорог и улиц при прокладке через них трубопроводов и коммуникаций открытым способом. Рыхлитель представляет собой навесное оборудование с гидроприводом на мощный гусеничный трактор.
Рабочий орган рыхлителя имеет один или три сменных зуба 18 с литыми наконечниками 19 из износостойкой стали, установленных с шагом 800—1020 мм. Зубья однозубых рыхлителей выполняют обычно неповоротными и жестко закрепляют в кармане несущей рамы. Зубья трехзубых рыхлителей закрепляют в специальных кронштейнах-флюгерах 17, поворачивающихся в плане на угол 10±15°. Рама 20, тяга 13 и балка 15 навесного устройства рыхлителя составляют четырехшарнирную параллелограммную систему, обеспечивающую постоянный угол резания зуба при различной глубине рыхления. На средний зуб устанавливается буферное устройство 16 при работе рыхлителя с трактором-толкачом.
|
Разрушение грунтов и пород происходит при поступательном движений машины и одновременном принудительном заглублении зубьев до заданной отметки. Опускание, принудительное заглубление и фиксирование рыхлителя в определенном рабочем положении, а также подъем его при переводе в транспортное положение производится двумя гидроцилиндрами 14 двустороннего действия, работающими от гидросистемы трактора.
Трехзубый рыхлитель может производить рыхление одним средним зубом, двумя симметрично поставленными (или всеми тремя) в зависимости от физико-механических свойств грунта и заданной ширины и глубины рыхления.
Рабочую скорость движения и величину заглубления рыхлителя в грунт выбирают такими, чтобы обеспечивалась наибольшая выработка машины для данных конкретных грунтовых условий при наиболее полном использовании мощности двигателя.
Рыхление грунта на каком-либо участке может осуществляться за один или несколько проходов. Послойное рыхление может производиться параллельными резами в двух взаимно перпендикулярных направлениях или под углом к первоначальным проходам (перекрестное рыхление). Для перемещения разрыхленного грунта, засыпки траншей и выполнения различных планировочных работ спереди трактора навешивается бульдозерный отвал 11, управляемый двумя гидроцилиндрами 12, работающими отгидросистемы базового тягача.
Отечественные рыхлители навешиваются на тягачи мощностью 108—540 л. с. (80—390 кВт), имеют наибольшую ширину захвата (при трех зубьях) 1480—2140 мм и рыхлят грунты высокой прочности на глубину 0,4—1,2 м. Производительность навесных рыхлителей на грунтах IV—V категорий составляет 60—130 м3/ч, средняя рабочая скорость движения 2,5—5 км/ч.
Кусторез – навесное оборудование к гусеничному трактору или мощному колесному тягачу. По конструкции рабочего органа разделяют кусторезы с активным или ТРН2601 пассивным рабочим органом. Наибольшее распространение получили машины с пассивным рабочим органом, что объясняется простотой их конструкции и надежностью в работе. Кусторез с пассивным рабочим органом (рис.1) представляет собой клинообразный отвал, вдоль нижних кромок, которого укреплены горизонтальные режущие ножи. Кусторез с пассивным рабочим органом состоит из следующих основных узлов: рабочего органа, толкающей рамы, передней стойки, ограждения и системы управления. Кусторезы могут иметь канатную или гидравлическую систему управления. При канатной системе рабочий орган поднимается и опускается однобарабанной лебедкой, которая крепится шпильками к задней стенке картера заднего моста трактора. Эту операцию производят и с помощью двух гидроцилиндров, работающих от гидросистемы трактора.
Корчеватель является навесным оборудованием к гусеничному трактору или мощному колесному тягачу. В зависимости от расположения рабочего органа на базовом тракторе или тягаче различают корчеватели переднего и заднего расположения. В зависимости от назначения рабочего органа выделяют корчеватели, корчеватели-собиратели и корчеватели-погрузчики. Последние способны выполнять операции по загрузке выкорчеванных пней и камней в транспортные средства. По типу системы управления разделяют корчеватели, имеющие канатно-блочную и гидравлический приводы. Наибольшее распространение получили корчеватели переднего расположения. При движении вперед и опущенном отвале зубья такого корчевателя врезаются в грунт и вычесывают корни растений на поверхность земли. Зубьями отвала корчевателя производится также корчевание пней диаметром до 45 см. Основными узлами корчевателя с передним расположением являются универсальная рама 2, рабочий орган 3 (отвал с зубьями), передняя стойка 4, толкатели 1 и лебедка 5. Корчевка пней может производиться различным способом: заглублением клыков и удалением пня под действием толкающего усилия трактора; заглублением клыков под пень и извлечением его только путем поворота рычагов при опущенной на грунт раме; заглублением клыков под пень и удалением его путем поворота рычагов с одновременным поступательным движением трактора.
Скрепер является самоходной или прицепной (к гусеничному трактору или колесному тягачу) землеройно-транспортной машиной, рабочим органом которой служит ковш на колесах, снабженный в нижней части ножами для срезания слоя грунта.
Скреперы предназначаются для послойного срезания, перемещения, послойной отсыпки, разравнивания и частичного уплотнения грунтов 1-3категории с ТРН2601каменистыми включениями до 300—600 мм при возведении насыпей, планировании строительных площадок, полей орошения или фильтрации, разработке траншей, выемок под резервуары, аэротенки и другие сооружения. Наиболее эффективно скреперы работают на непереувлажненных средних грунтах (супесях, суглинках, черноземах), не содержащих крупных каменистых включений. При разработке скреперами тяжелых грунтов их предварительно рыхлят на толщину срезаемой стружки.
Рабочий цикл скрепера включает ряд последовательно повторяющихся операций: резание грунта и наполнение ковша, при движении вперед ножи опущенного на грунт ковша 2 срезают слой грунта, который поступает в ковш при поднятой заслонке 3; транспортирование грунта к месту укладки — наполненный грунтом ковш 2 на ходу поднимается в транспортное положение, опущенная заслонка 3 препятствует высыпанию грунта из ковша; выгрузку и укладку грунта — при поднятой заслонке 2 задняя стенка 5 ковша принудительно выдвигается вперед и вытесняет грунт из приспущенного ковша, причем регулируемый зазор между режущей кромкой ковша и поверх ностью земли определяет толщину укладываемого слоя ТРН2601 грунта 4, который разравнивается (планируется) ножами ковша и частично уплотняется задними колесами скрепера; холостой (обратный) ход в забой — порожний, ковш 2 поднят в транспортное положение, заслонка 3 опущена.
В зависимости от вида и объема выполняемых земляных работ применяют различные схемы движений скрепера в плане — по эллипсу, восьмеркой, челноч-но-поперечное и др. Схему движения по эллипсу применяют при разработке выемок и широких траншей, челночно-поперечное и восьмеркой—«при копании неглубоких, но больших по площади котлованов под резервуары, аэротенки и т. п.
Скреперы классифицируют: по способу загрузки ковша — с пассивной загрузкой движущим усилием срезаемого слоя грунта и с принудительной загрузкой элеватором;
по количеству осей — на одноосные и двухосные; по способу тяги— на прицепные (одноосные и двухосные) и полуприцепные (одноосные) к гусеничным тракторам и двухосным пневмоколесным тягачам, самоходные (одноосные), агрегатируемые с одноосными пневмоколесными тягачами;
по способу разгрузки ковша — с принудительной разгрузкой при выдвижении задней стенки ковша вперед (наиболее распространенный способ); с полупринудительной разгрузкой через донный проем или поворотом днища и задней стенки ковша вперед относительно неподвижных боковых стенок; со свободной (самосвальной) разгрузкой опрокидыванием ковша вперед или назад по ходу машины; по типу
управления рабочим органом — с канат-но-блочным и гидравлическим управлением.
Широкое распространение в строительстве получили самоходные скреперы с гидравлическим управлением, которые обладают более высокими мобильностью, маневренностью, транспортными скоростями и производительностью (в 1,5—2,5 раза) по сравнению с ТРН2601 прицепными машинами той же вместимости.
Самоходные скреперы эффективно используются при дальностях возки грунта на 300—5000 м, прицепные и полуприцепные к гусеничным тягачам—на 100—800 м.
Самоходный скрепер с гидравлическим управлением представляет собой двухосную пневмоколесную машину, состоя щую из одноосного тягача 1 и полуприцепного одноосного скреперного оборудования, соединенных между собой универсальным седельно-сцепным устройством 2. На тягаче смонтированы два гидроцилиндра для его поворота относительно скрепера в плане. Седельно-сцепное устройство обеспечивает возможность относительного поворота тягача и скрепера в вертикальной и горизонтальной плоскостях. В задней части машины имеется буферное устройство 10 для толкания скрепера вспомогательным трактором в процессе набора грунта.
Основным узлом скрепера является ковш 7 с двумя боковыми стенками и днищем, к подножевои плите которого крепят сменные двухлезвийные ножи 11. Ковш снабжен выдвижной ТРН2601задней стенкой 8 для принудительной разгрузки, а в передней части — заслонкой 6, поднимающейся при наборе и выгрузке грунта. Заслонка служит для регулирования щели при загрузке ковша и закрывает ковш при транспортировании грунта. Ковш шарнирно соединен с тяговой П-образной рамой 5, жестко соединенной с хоботом 3. Гидравлическая система управления рабочим оборудованием обеспечивает подъем и опускание ковша 7, заслонки 6, выдвижение задней стенки 8 и возврат ее в исходное положение с помощью трех пар гидроцилиндров 4, 9 и 12.
Шестеренные насосы гидросистемы приводятся в действие от коробки отбора мощности тягача. Раздельное управление гидроцилиндрами 4, 9 и 12 осуществляется золотниковым распределителем.
Вместимость 3,0—15 м3, работающие с тягачами мощностью 75—330 л. с., и самоходные скреперы с ковшами вместимостью 8—25 м3, агрегатируемые с тягачами мощностью 180—1100 л. с. При наполнении ковша скорость движения скреперов составляет 2—4 км/ч, при транспортном передвижении — 0,5—0,8 максимальной скорости трактора или тягача.
Подводные трубозаглубители
Машины, предназначенные для разработки подводных траншей непосредственно под выложенным по дну трубопроводом, называются подводными трубозаглубителями. Для успешной работы подводного трубозаглубителя поверхность уложенного по дну трубопровода должна быть обетонирована.
Подводный трубозаглубитель состоит из энергетической базы и рабочего органа. Энергетическая база предназначена для снабжения энергией рабочего органа и обеспечения передвижения по трубопроводу. В качестве ее используются существующие плавучие средства, оборудованные насосами необходимой подачи и рабочего давления для привода рабочего органа, оперативными лебедками для обеспечения перемещения и лебедкой для подъема рабочего органа на поверхность.
Рабочий орган трубозаглубителя предназначен для выполнения основной операции — заглубления трубопровода. Применяются два типа рабочих органов — фрезерно-гидравлический и гидро-эжекционный.
13. Машины для засыпки траншей. Основные требования к ним, их сравнительные технико-эксплуатационные показатели.
Траншею после укладки в нее изолированного трубопровода засыпают грунтом. Засыпка траншеи является одной из важных технологических операций, от качества выполнения которой в значительной степени зависит срок службы трубопровода.
Для того чтобы не повредить изоляцию трубопровода, первый покрывающий его слой грунта должен быть мягким, не содержащим крупных камней' или мерзлых комьев.
Засыпка траншеи должна производиться по возможности равномерно, без мгновенного сбрасывания большого объема грунта, что может привести как к повреждению изоляции, так и к смещению участков трубопровода к стенкам траншей, вызывающему возникновение ТРН2601 в трубопроводе дополнительного изгибающего момента, ухудшающего доследующее его напряженное состояние в период эксплуатации.
Траншеезасыпатель скребковый ТС предназначендля засыпки траншеи с уложенным в нее трубопроводом на заболоченных участках трассы с грунтами, обладающими низкий несущей способностью, а также в лесистой и горной местности, где размеры строительной
полосы не позволяют производить работу бульдозером.
Кроме своего основного назначения трапшеезасыпатель этого типа может быть использован в качестве грузоподъемного крана,а также для рыхления мерзлого грунта клин-бабой.
Для непрерывной засыпки траншеи размельченным грунтом был создан шнековы траншеезасыпатель с рабочим органом в виде горизонтального шнека.
Вал шнека вращается в подшипниковых опорах, укрепленных по краям отвала, напоминающего бульдозерный. Отвал вместе со шнеком, цепной передачей и редуктором привода шпека, которые тоже крепятся к отвалу (с левой его части по ходу движения), представляет собой навесное оборудование, навешиваемое на базовый трактор, аналогично отвалу бульдозера.
Траншеезасыпатель роторного типа, так же как и шнекового, является машиной непрерывного действия и предназначен для засыпки траншеи (после укладки в нее трубопровода) разрыхленным грунтом. Он может быть использован также для присыпки
дна траншеи с целью создания мягкой подушки перед укладкой трубопровода в траншею.
Сваебойные машины
Существующие сваебойные молоты подразделяются по роду привода на механические или подвесные, пневманические, дизельные и электрические (вибромолоты).
По принципу использования энергии привода различают молоты простого и двойного действия. В молотах простого действия энергия привода (пар или ТРН2601сжатый воздух, газы, образующиеся при сгорании топлива, электроэнергия) необходима только для подъема ударной части, а падение ее совершается под действием собственного веса. В молотах двойного действия энергия привода идет и на движение ударной части вниз, увеличивая ее скорость и, следовательно, силу удара. К молотам простого действия относятся механические, дизельные и паровоздушные одиночного действия; к молотам двойного действия — паровоздушные двойного действия.
Главным определяющим параметром молотов простого действия является вес ударной части, молотов двойного действия и вибромолотов — энергия удара.
Механические или подвесные молоты являются простейшим типом сваебойных молотов. Молот представляет собой чугунную или стальную болванку, имеющую вверху петлю для сцепления с подъемным канатом и направляющие захваты для удержания и направления молота в стрелах копра. Принцип действия молота заключается в попеременном подъеме его с помощью лебедки на некоторую высоту и свободном падении на голову сваи.
В паровоздушных молотах в качестве источника энергии используется пар или сжатый воздух с давлением 0,7—0,8 МПа.
Паровоздушный молот простого действия с ручным управлением
В молотах простого действия пар или сжатый воздух только поднимает на некоторую высоту (1,5—2 м) ударную часть молота, т. е. цилиндр, затем происходит выхлоп пара или воздуха и цилиндр падает под действием собственного веса, нанося удар по свае.
В молотах простого действия с полуавтоматическим управлением в отличие от молотов с ручным управлением выхлоп пара или сжатого воздуха благодаря специальному устройству происходит автоматически. Управление впуском пара (сжатого воздуха) в цилиндр молота после выхлопа и удара цилиндра по свае остается ручным. В большинстве конструкций у паровоздушных ТРН2601молотов двойного действия ударной частью является поршень.
Молоты двойного действия весьма эффективны при забивке элементов с малым лобовым сопротивлением, каковыми являются деревянный и стальной шпунт, балки, железобетонные трубчатые сваи с открытым концом, металлические трубы.
Большим преимуществом молотов двойного действия является их способность забивать сваи под водой. Для этого молот снабжается шлангом для выхлопа отработанного воздуха (пар в этом случае неприменим), один конец которого крепится к выхлопному отверстию молота, а другой—выводится выше уровня воды.
Дизель-молот работает по принципу двухтактного двигателя внутреннего сгорания. Источником энергии служит маловязкое дизельное топливо.
Выпускаются дизель-молоты двух типов — трубчатые и штанговые.
Вибромолоты относятся к молотам ударно-вибрационного действия, в которых вертикально направленные колебания, создаваемые вибровозбудителем и передаваемые погружаемой свае, сочетаются с периодическими ударами по ней. Известны конструкции, в которых в качестве привода вибровозбудителя используются электродвигатели и двигатели внутреннего ТРН2601 сгорания. Однако преимущественное распространение получили вибромолоты с электроприводом. Вибромолоты применяются главным образом на забивке металлического шпунта, стальных труб и в отдельных случаях железобетонных свай в слабые грунты.
Башенные краны
Башенным краном называют поворотный кран со стрелой, закрепленной в верхней части вертикально расположенной башни. Вследствие Г-образной компоновки кран этого типа полностью охватывает строящееся здание, обеспечивая подачу материалов и оборудования в любую его точку (рис. 3).
Рис. 3. Общий вид башенного крана:
1 — ходовая тележка; 2 — поворотная платформа; 3 — башня; 4 — стрела; 5 — противовес
Стреловые самоходные краны
Стреловые самоходные краны представляют собой стреловое крановое оборудование (чаще всего полноповоротного типа), смонтированное на самоходном гусеничном или пневмоколесном ходу.
По типу ходового оборудования краны классифицируют на гусеничные и пневмоколесные.
Управление крановыми механизмами осуществляется из кабины машиниста, расположенной на поворотной платформе, а их привод — от двигателя автомобиля. При включении трансмиссии крановых механизмов трансмиссия автомобиля отключается.
Все большее распространение получают автокраны с многомоторным приводом крановых механизмов. Им свойственны следующие преимущества: способность совмещать любые рабочие операции, обеспечение малых скоростей посадки груза, простота и легкость управления краном.
В качестве приводных индивидуальных двигателей применяются электро - и гидродвигатели.
Дополнительные характеристики:
- основная стрела крана (14м) удлиняется решетчатыми вставками длиной 2,5; 5 и 8,75м до 32,75м с помощью пальцевых безрезьбовых соединений;
- для увеличения высоты подъема и подстрелового пространства кран может комплектоваться: решетчатым гуськом длиной 5м (Hmax = 36м)
- возможно передвижение крана с грузом;
Краны-трубоукладчики..
Трубоукладчиком называется самоходная грузоподъемная машина, способная перемещаться с грузом на крюке и служащая для подъема и укладки трубопровода в траншее, а также для выполнения различных грузоподъемных и монтажных работ (погрузка и разгрузка труб и плетей, центровка труб при сварке и пр.). Основное назначение трубоукладчика — сопровождение очистных и изоляционных машин и укладка изолированного трубопровода в траншею. Рабочими движениями трубоукладчика- являются подъем и спуск груза, перемещение трубоукладчика вместе с грузом и изменение вылета стрелы с грузом. Надежное сцепление гусениц с грунтом в сочетании с большим тяговым усилием позволяет использовать трубоукладчик в качестве тягача.
Трубоукладчик состоит из базовой машины и навесного оборудования. В состав базовой машины (базы) входит двигатель, трансмиссия, ходовая часть и нижняя рама (шасси) трубоукладчика. Навесное оборудование включает стрелу, верхнюю раму (портал), блочно-талевую систему с крюком, контргруз и лебедку.
База трубоукладчика. Трубоукладчики создаются как на базе серийных гусеничных тракторов без существенного изменения их конструкции Технико-эксплуатационные показатели трубоукладчиков, основными из которых являются грузовая, собственная и продольная устойчивость, тяговое усилие, удельное давление на грунт, масса и некоторые другие.
Навесное оборудование трубоукладчика состоит из верхней рамы, стрелы лебедки с трансмиссией, блочно-талевой системы с грузовым и стреловым полиспастами и крюком, контргруза с механизмом откидывания его и гидросистемы.
Верхняя рама представляет собой пространственную сварную ферму, которая крепится к рамам тележек и раме трактора болтами и служит основанием для установки ТРН2601навесного оборудования.
Стрела трубоукладчика — А-образная сварная, состоит из двух балок (подкосов) коробчатого сечения, соединенных в верхней и нижней частях поперечными связями. Расположение стрелы — боковое, что диктуется технологией производства работ. На стреле устанавливается указатель грузоподъемности, показывающий водителю, какой максимальный груз можно поднимать на данном вылете стрелы (крюка).
Контргруз (противовес) служит для увеличения устойчивости трубоукладчика при подъеме груза, располагается с правой стороны трубоукладчика и выполняется в двух вариантах: неподвижном — в трубоукладчиках, предназначенных для укладки трубопроводов малых диаметров, и откидном — для более мощных трубоукладчиков. Откидывание контргруза и возвращение его в исходное положение производятся гидроцилиндром, который шарнирно крепится к верхней раме трубоукладчика.
Лебедка трубоукладчика служит для подъема груза и изменения вылета (наклона) стрелы. Имеет два барабана, сидящих на одной оси. Один барабан предназначен для навивки грузового каната, другой — стрелового.
Все трубоукладчики оснащены указателем грузового момента, обеспечивающим контроль изменения его величины, и прибором контроля нагрузки, что позволяет автоматически поддерживать нагрузку на крюке в заданном диапазоне при работе трубоукладчика в составе изоляционно-укладочной колонны. Указатель грузового момента предназначен для предотвращения опрокидывания трубоукладчика и позволяет надежно работать машине на характеристиках в режиме крана и трубоукладчика.
• Основными техническими показателями трубоукладчика являются максимальная грузоподъемность и максимально допустимый грузовой момент, гарантируемый устойчивостью трубоукладчика. Необходимая грузоподъемность трубоукладчика ТРН2601определяется диаметром укладываемого трубопровода, высотой его подъема, взаимным расположением (расстановкой) машин, зависящим от способа производства изоляционно-укладочных работ.
• Другой важный показатель трубоукладчика — максимально допустимый грузовой момент — характеризует возможный вылет при работе с данным грузом или максимальный груз при работе с данным вылетом. Этот показатель равен произведению, максимально допустимых величин вылета стрелы и веса груза на этом вылете.
• Важным условием надежной работы трубоукладчика является обеспечение его устойчивости, т. е. способность работать без опрокидывания. Различают: грузовую, собственную и продольную устойчивость трубоукладчика. Под грузовой понимают устойчивость против опрокидывания, в сторону стрелы (груза), под собственной — в сторону контргруза, а под продольной — взад или вперед по ходу. Показателем этого важного параметра является коэффициент запаса устойчивости.
Троллейные подвески
Троллейные подвески (тележки) предназначены для поддержания на весу трубопровода трубоукладчиком в процессе непрерывной укладки при сопровождении очистной и изоляционной машин. Троллейная подвеска состоит из катков, осей, соединительных щек, скоб и подвесок с петлями. Катки имеют форму усеченного конуса и выполнены из стального литья. В зависимости от диаметра трубопровода, который поддерживают подвески, число пар катков в них бывает равно двум, трем, четырем. Современные подвески такого типа имеют грузоподъемность от 60 до 350 кН и предназначены для поддержания и укладки трубопровода диаметром от 89 до 1020 мм.
Эластичные захваты
Эластичные захваты (полотенца) предназначены для подъема, поддержания и опуска в траншею изолированного трубопровода или отдельных труб и плетей. По конструкции различают полотенца тросовые и мягкие. Полотенца мягкие предназначены для подъема и укладки в траншею изолированного трубо
|
|
Своеобразие русской архитектуры: Основной материал – дерево – быстрота постройки, но недолговечность и необходимость деления...
Семя – орган полового размножения и расселения растений: наружи у семян имеется плотный покров – кожура...
История развития хранилищ для нефти: Первые склады нефти появились в XVII веке. Они представляли собой землянные ямы-амбара глубиной 4…5 м...
Таксономические единицы (категории) растений: Каждая система классификации состоит из определённых соподчиненных друг другу...
© cyberpedia.su 2017-2024 - Не является автором материалов. Исключительное право сохранено за автором текста.
Если вы не хотите, чтобы данный материал был у нас на сайте, перейдите по ссылке: Нарушение авторских прав. Мы поможем в написании вашей работы!