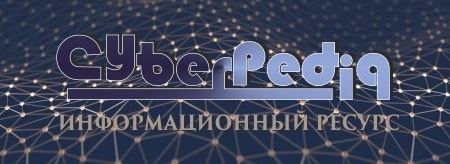
Индивидуальные очистные сооружения: К классу индивидуальных очистных сооружений относят сооружения, пропускная способность которых...
Особенности сооружения опор в сложных условиях: Сооружение ВЛ в районах с суровыми климатическими и тяжелыми геологическими условиями...
Топ:
Оценка эффективности инструментов коммуникационной политики: Внешние коммуникации - обмен информацией между организацией и её внешней средой...
Устройство и оснащение процедурного кабинета: Решающая роль в обеспечении правильного лечения пациентов отводится процедурной медсестре...
Характеристика АТП и сварочно-жестяницкого участка: Транспорт в настоящее время является одной из важнейших отраслей народного...
Интересное:
Национальное богатство страны и его составляющие: для оценки элементов национального богатства используются...
Подходы к решению темы фильма: Существует три основных типа исторического фильма, имеющих между собой много общего...
Влияние предпринимательской среды на эффективное функционирование предприятия: Предпринимательская среда – это совокупность внешних и внутренних факторов, оказывающих влияние на функционирование фирмы...
Дисциплины:
![]() |
![]() |
5.00
из
|
Заказать работу |
|
|
Содержание
Введение. 2
1. Исходные данные. 2
2. Выбор режущего инструмента. 3
3. Расчет режимов резания. 4
4. Выбор металлорежущего станка. 7
5. Кинематический анализ станка. 11
Вывод. 15
Список использованной литературы.. 16
Введение
Цель работы:
Провести кинематический анализ металлорежущего станка на примере обработки винтовой поверхности.
Для достижения поставленной цели необходимо выполнить следующие задачи:
1) По исходным данным осуществить подбор режущего инструмента;
2) Провести расчёт режимов резания;
3) Осуществить подбор технического оборудования;
4) Провести кинематический анализ оборудования.
Исходные данные
Номер варианта | |
Номер детали | |
Тип инструмента | Резец канавочный |
Масштабный коэффициент | |
Степень автоматизации | Ручное управление |
Материал детали | Конструкционная сталь |
![]() | |
Шероховатость обрабатываемой поверхности(Ra) | 16 мкм |
Вид обработки | точение |
Исходный эскиз детали представлен на рисунке 1.
Рисунок 1. Эскиз детали
Выбор режущего инструмента
Режущий инструмент: резец канавочный. Канавочные резцы с механическим креплением сменных перетачиваемых режущих пластин используют в первую очередь для прорезания канавок точных размеров. Наружную форму режущей части и требуемый размер обеспечивают заточкой.
Инструмент выбираем, исходя из материала обрабатываемой поверхности и размеров канавки. Эскиз резца представлен на рисунке 2 [3, стр.210].
Параметры канавочного резца (ОСТ 2И10-8-84 Резцы токарные для обработки внутренних прямых и угловых канавок. Типы и основные размеры):
d = 25; L1 = 150; f = 17; m = 29,5
Материал режущей части резца Р18 [3,стр.367].
|
Рисунок 2. Эскиз режущего инструмента
Расчет режимов резания
Для расчета скорости резания при точении нужно использовать формулу (1) [3, cтр.363]:
, м/мин (1)
где:
s= 0,05 мм/об (подача при чистовом точении) [3, табл.14, cтр.365];
T= 15 мин (значение стойкости) [3, cтр.363];
Значение коэффициента Cv (коэффициент, характеризующий условия обработки и материал) и показателей степени в формуле (1):
Cv= 23,7; m= 0,25; y= 0,66; [3, табл.17, cтр.367];
Kv – общий поправочный коэффициент на скорость резанья, учитывающий фактические условия резания, определяется по формуле (2) [3, стр. 358]:
, (2)
где KMV– коэффициент, учитывающий качество обрабатываемого материала [3, таб. 1, 358].
, где Kг=1 (коэффициент Kг, характеризующий группу стали по обрабатываемости) и nv=1[3, таб.2, стр.359].
KПV= 1 (коэффициент, отражающий состояние поверхности заготовки [3, стр. 361];
KИV=0,3 (коэффициент, учитывающий влияние инструментального материала) табл. 6 [3, стр. 361].
Подставив значения коэффициентов в формулу (1), получим скорость резания:
Для расчета силы резания нужно использовать формулу (3) [3,cтр.371]:
, Н (3)
где
Ср =247, коэффициент, характеризующий условия обработки и материал;
x =1;
y =1;
n =0 – показатели степеней [3, таб.22, стр.372];
t=4,5 – ширина режущей части резца;
Поправочный коэффициент Kp представляет собой произведение ряда коэффициентов, учитывающих фактические условия резания по формуле (4) [3,cтр.371]:
(4)
где - поправочный коэффициент, учитывающий влияние качества обрабатываемого материала на силовые зависимости [3, табл.9, стр. 362],
Kφp =1,08;
Kγp =1,15;
Kλp = 1;
Кrp =0,93 – поправочные коэффициенты, учитывающие влияние геометрических параметров режущей части инструмента на силу резания при обработки стали.
Рассчитываем тангенциальную силу резания:
Для расчета эффективной мощности резания нужно использовать формулу (5) [3, cтр.371]:
(5)
где Pz – тангенциальная сила резания, Н; V – скорость резания, м/мин.
Для определения основной мощности резания воспользуемся формулой (6):
|
(6)
где ŋ = 0,75
Рассчитаем частоту вращения шпинделя по формуле (7) [3, 386]
(7)
Назначение станка
Станок предназначен для токарной обработки сравнительно небольших деталей из различных материалов как быстрорежущими, так и твердосплавными инструментами в условиях индивидуального и серийного производства. На станке можно нарезать резцом метрические, дюймовые, модульные и питчевые резьбы. А так же на нём можно точить канавки. [2, с. 30].
Движения в станке
Движение резания — вращение шпинделя с обрабатываемой деталью. Движение подач — прямолинейное поступательное перемещение суппорта с резцом в продольном и поперечном направлениях от ходового валика. Движение образования винтовой поверхности — прямолинейное поступательное перемещение суппорта с резьбовым резцом в продольном направлении от ходового винта. Вспомогательные движения — ручные установочные перемещения суппорта, корпуса и пиноли задней бабки и поворот четырехпозиционного резцедержателя.
Принцип работы
Обрабатываемая деталь устанавливается в центрах или закрепляется в патроне. В резцедержателе суппорта могут быть закреплены четыре резца. Инструменты для обработки отверстий вставляются в конус пиноли задней бабки. Сочетанием вращательного движения детали с поступательным перемещением резца на станке можно обрабатывать цилиндрические, конические, винтовые и торцовые поверхности.
Конструктивные особенности
В станке модели 1А616 применен разделенный привод движения резания. Приводной шкив установлен на шпинделе между его опорами, однако конструкция задней опоры шпинделя допускает замену клиновых ремней без демонтажа шпинделя. Торможение привода станка достигается подключением постоянного тока в обмотку статора электродвигателя.
Вывод
Целью расчетно-графической работы являлось изучение кинематического анализа станка.
В процессе выполнения РГР был выбран режущий инструмент для обработки детали, по исходным данным, подобран станок 1А616, исходя из расчетов, произведенных в ходе работы.
В ходе работы ознакомилась с кинематической схемой станка, приобрела навыки расчета параметров исполнительных движений станка.
Список использованной литературы
1. Птицын С.В., Чёсов Ю.С. Скиба В.Ю. Металлорежущие станки и инструменты: Учебное пособие / Под ред. Иванцивского В.В. – Новосибирск, Изд-во НГТУ,2006. 18с.
|
2. Металлорежущие станки (альбом общих видов, кинематических схем и узлов). Кучер А.М., Киватицкий М.М., Покровский А.А. издательство «машиностроение», Ленинград 1971, стр. 308.
3. Справочник технолога-машиностроения. В двух томах С74 Т.2 Под редакцией А.Г. Косиловой и Р.К. Мещарикова – 4-е изд., перераб. и доп. – М.: Машиностроение, 1985. 496с.
4. Библиотека технической литературы / Internet. - http://delta-grup.ru/bibliot/10/47.htm
5. Интернет-ресурс: http://www.tehno-line.ru/files/theory/Turning/1-2-1.htm
Содержание
Введение. 2
1. Исходные данные. 2
2. Выбор режущего инструмента. 3
3. Расчет режимов резания. 4
4. Выбор металлорежущего станка. 7
5. Кинематический анализ станка. 11
Вывод. 15
Список использованной литературы.. 16
Введение
Цель работы:
Провести кинематический анализ металлорежущего станка на примере обработки винтовой поверхности.
Для достижения поставленной цели необходимо выполнить следующие задачи:
1) По исходным данным осуществить подбор режущего инструмента;
2) Провести расчёт режимов резания;
3) Осуществить подбор технического оборудования;
4) Провести кинематический анализ оборудования.
Исходные данные
Номер варианта | |
Номер детали | |
Тип инструмента | Резец канавочный |
Масштабный коэффициент | |
Степень автоматизации | Ручное управление |
Материал детали | Конструкционная сталь |
![]() | |
Шероховатость обрабатываемой поверхности(Ra) | 16 мкм |
Вид обработки | точение |
Исходный эскиз детали представлен на рисунке 1.
Рисунок 1. Эскиз детали
Выбор режущего инструмента
Режущий инструмент: резец канавочный. Канавочные резцы с механическим креплением сменных перетачиваемых режущих пластин используют в первую очередь для прорезания канавок точных размеров. Наружную форму режущей части и требуемый размер обеспечивают заточкой.
Инструмент выбираем, исходя из материала обрабатываемой поверхности и размеров канавки. Эскиз резца представлен на рисунке 2 [3, стр.210].
Параметры канавочного резца (ОСТ 2И10-8-84 Резцы токарные для обработки внутренних прямых и угловых канавок. Типы и основные размеры):
|
d = 25; L1 = 150; f = 17; m = 29,5
Материал режущей части резца Р18 [3,стр.367].
Рисунок 2. Эскиз режущего инструмента
Расчет режимов резания
Для расчета скорости резания при точении нужно использовать формулу (1) [3, cтр.363]:
, м/мин (1)
где:
s= 0,05 мм/об (подача при чистовом точении) [3, табл.14, cтр.365];
T= 15 мин (значение стойкости) [3, cтр.363];
Значение коэффициента Cv (коэффициент, характеризующий условия обработки и материал) и показателей степени в формуле (1):
Cv= 23,7; m= 0,25; y= 0,66; [3, табл.17, cтр.367];
Kv – общий поправочный коэффициент на скорость резанья, учитывающий фактические условия резания, определяется по формуле (2) [3, стр. 358]:
, (2)
где KMV– коэффициент, учитывающий качество обрабатываемого материала [3, таб. 1, 358].
, где Kг=1 (коэффициент Kг, характеризующий группу стали по обрабатываемости) и nv=1[3, таб.2, стр.359].
KПV= 1 (коэффициент, отражающий состояние поверхности заготовки [3, стр. 361];
KИV=0,3 (коэффициент, учитывающий влияние инструментального материала) табл. 6 [3, стр. 361].
Подставив значения коэффициентов в формулу (1), получим скорость резания:
Для расчета силы резания нужно использовать формулу (3) [3,cтр.371]:
, Н (3)
где
Ср =247, коэффициент, характеризующий условия обработки и материал;
x =1;
y =1;
n =0 – показатели степеней [3, таб.22, стр.372];
t=4,5 – ширина режущей части резца;
Поправочный коэффициент Kp представляет собой произведение ряда коэффициентов, учитывающих фактические условия резания по формуле (4) [3,cтр.371]:
(4)
где - поправочный коэффициент, учитывающий влияние качества обрабатываемого материала на силовые зависимости [3, табл.9, стр. 362],
Kφp =1,08;
Kγp =1,15;
Kλp = 1;
Кrp =0,93 – поправочные коэффициенты, учитывающие влияние геометрических параметров режущей части инструмента на силу резания при обработки стали.
Рассчитываем тангенциальную силу резания:
Для расчета эффективной мощности резания нужно использовать формулу (5) [3, cтр.371]:
(5)
где Pz – тангенциальная сила резания, Н; V – скорость резания, м/мин.
Для определения основной мощности резания воспользуемся формулой (6):
(6)
где ŋ = 0,75
Рассчитаем частоту вращения шпинделя по формуле (7) [3, 386]
(7)
Выбор металлорежущего станка
Для того чтобы правильно выбрать станок, нужно проанализировать следующие характеристики: метод обработки, мощность, частоту вращения, диаметр заготовки, подачу. Самым главным параметром при выборе станка являются характер выполняемых работ и тип металлорежущего инструмента. Так как выполняемая работа - это точение канавки, то для этой работы лучше всего выбрать токарный станок.
Выбираем токарно-винторезный станок модели 1А616 (рис.3). Кинематическая схема токарно-винторезного станка 1А616 представлена на рисунке 4 [2, с. 33].
|
Рисунок 3. Общий вид токарно-винторезного станка 1А616
Основные узлы станка (рис.3): А - гитара сменных колес; Б - передняя бабка с переборным устройством, звеном увеличения шага и реверсивным механизмом; В - фартук с механизмом подач; Г - суппорт; Д - задняя бабка; Е - станина; Ж - встроенный шкаф с электрооборудованием; З - задняя тумба; И - система охлаждения; К - поддон для сбора охлаждающей жидкости и стружки; Л - коробка скоростей; М - передняя тумба; Н - коробка подач.
Рисунок 4. Кинематическая схема станка 1А616
Назначение станка
Станок предназначен для токарной обработки сравнительно небольших деталей из различных материалов как быстрорежущими, так и твердосплавными инструментами в условиях индивидуального и серийного производства. На станке можно нарезать резцом метрические, дюймовые, модульные и питчевые резьбы. А так же на нём можно точить канавки. [2, с. 30].
|
|
Организация стока поверхностных вод: Наибольшее количество влаги на земном шаре испаряется с поверхности морей и океанов (88‰)...
История развития хранилищ для нефти: Первые склады нефти появились в XVII веке. Они представляли собой землянные ямы-амбара глубиной 4…5 м...
Индивидуальные и групповые автопоилки: для животных. Схемы и конструкции...
Поперечные профили набережных и береговой полосы: На городских территориях берегоукрепление проектируют с учетом технических и экономических требований, но особое значение придают эстетическим...
© cyberpedia.su 2017-2024 - Не является автором материалов. Исключительное право сохранено за автором текста.
Если вы не хотите, чтобы данный материал был у нас на сайте, перейдите по ссылке: Нарушение авторских прав. Мы поможем в написании вашей работы!