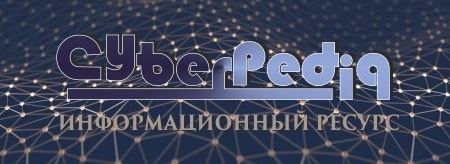
История создания датчика движения: Первый прибор для обнаружения движения был изобретен немецким физиком Генрихом Герцем...
Типы сооружений для обработки осадков: Септиками называются сооружения, в которых одновременно происходят осветление сточной жидкости...
Топ:
Генеалогическое древо Султанов Османской империи: Османские правители, вначале, будучи еще бейлербеями Анатолии, женились на дочерях византийских императоров...
История развития методов оптимизации: теорема Куна-Таккера, метод Лагранжа, роль выпуклости в оптимизации...
Определение места расположения распределительного центра: Фирма реализует продукцию на рынках сбыта и имеет постоянных поставщиков в разных регионах. Увеличение объема продаж...
Интересное:
Отражение на счетах бухгалтерского учета процесса приобретения: Процесс заготовления представляет систему экономических событий, включающих приобретение организацией у поставщиков сырья...
Мероприятия для защиты от морозного пучения грунтов: Инженерная защита от морозного (криогенного) пучения грунтов необходима для легких малоэтажных зданий и других сооружений...
Средства для ингаляционного наркоза: Наркоз наступает в результате вдыхания (ингаляции) средств, которое осуществляют или с помощью маски...
Дисциплины:
![]() |
![]() |
5.00
из
|
Заказать работу |
|
|
После разработки схем сборки устанавливают состав необходимых сборочных, регулировочных, пригоночных, подготовительных и контрольных работ и определяют содержание технологических операций и переходов.
В состав технологического процесса сборки в качестве технологических операций и переходов включают разнообразные сборочные работы. К технологическому процессу сборки относят также операции, связанные с проверкой правильности действия отдельных механизмов и узлов машины в целом (точность, бесшумность, плавность движений и т.п.); операции очистки, промывки, окраски и отделки изделия или составляющих его единиц.
В сборочных процессах, так же как в процессах изготовления деталей, применяют единую систему технологической документации.
Важной частью разработки технологического процесса является нормирование слесарно-сборочных работ.
Технологический процесс сборки включает следующие этапы:
– подготовка элементов конструкции к сборке;
– предварительная сборка (при необходимости);
– промежуточная сборка (при необходимости);
– сборка под сварку (при необходимости);
– окончательная сборка;
– регулировка;
– контроль;
– демонтаж (при необходимости).
Различные виды сборочных работ и их краткая характеристика приведены в табл. 7.1.
Технология соединения зависит от его вида (разборное, неразборное) и степени взаимной подвижности элементов конструкции (подвижные, неподвижные). Конкретное содержание операций соединения зависит от вида соединений, применяемых средств технологического оснащения, уровня механизации и автоматизации, организации производства и т.п.
Выбор технологического и вспомогательного оборудования, технологической оснастки.
|
Оборудование сборочных производств можно разделить на две группы.
Технологическое оборудование – предназначено для выполнения работ по соединению деталей, их регулировке и контролю (оборудование для сборки резьбовых соединений, нагревательные устройства, ванны, установки для охлаждения, прессы и др.).
Вспомогательное оборудование – предназначено для механизации вспомогательных работ (тельферы, поворотные краны, конвейеры, рольганги, домкраты, лебедки, тележки и др.). Для доставки к рабочим местам деталей и СЕ используют ручные тележки и электрокары, различного вида краны и конвейеры. Большие удобства создают конвейеры, оснащенные устройствами для адресной доставки транспортируемых деталей и СЕ.
Удельный вес вспомогательных работ в общей трудоемкости сборки, в серийном производстве, составляет 30…40 %, в массовом 10…15 %.
Наибольшие трудности вызывает механизация и автоматизация работ, связанных с координированием деталей и СЕ и их соединением с требуемой точностью. Операции и переходы, связанные с выполнением подобных работ, нуждаются в приспособлениях, устраняющих возможность возникновения отклонений в относительном положении соединяемых деталей.
Техническое нормирование работ и определение технико-экономических показателей.
Для определения длительности (цикла) сборки машин строят циклограмму процесса. В избранном масштабе циклограмма отражает не только последовательность затрат времени на выполнение операции, но и совмещение во времени этих затрат. Циклограмма позволяет найти пути сокращения цикла сборки.
Оформление технологической документации.
Состав документов и методы оформления рассматриваются в стандартах ЕСТПП. Машины и СЕ после их сборки подвергают различного рода испытаниям. Целью испытания является проверка качества изделия, достигнутого в результате всего производственного процесса его изготовления.
|
Технологическая документация процесса сборки включает маршрутные и операционные карты технологического процесса, операционные карты технического контроля, ведомости оснастки, инструкции и т.п. в соответствии с требованиями ЕСТД.
Сборочные работы при различных видах соединений
В процессах узловой и общей сборки соединяют разнообразные детали. Метод образования соединения назначает разработчик с учетом условий функционирования, возможностей производства и особенностей эксплуатации изделия.
Методы образования соединений разделяются в зависимости от наличия или отсутствия специальных соединительных элементов конструкции. К таким соединениям относятся шлицевые, прессовые, термоусаженные и т. п. соединения. При отсутствии таких элементов соединение осуществляется по сопрягаемым поверхностям.
Наибольшим разнообразием отличаются методы образования соединений с использованием специальных соединительных элементов – болтов, винтов, заклепок, шпилек и т. п. К этой же группе относятся клиновые, шпоночные, штифтовые и другие соединения. Для выполнения таких соединений предварительно необходимы операции образования контуров для постановки соединительных элементов. Например, в болтовых, винтовых и заклепочных соединениях необходимо образовать отверстия для постановки болтов, винтов и заклепок, нарезать резьбу (для винтов), обработать гнезда для потайных головок болтов, винтов или заклепок и т. д.
В сварных, паяных и клееных соединениях соединительным элементом является сварной, паяный или клеевой шов. Для выполнения таких соединений предварительно необходимы операции обработки кромок, механической и химической очистки соединяемых поверхностей в зоне соединительного шва.
Разновидности соединений приведены на рис. 17.3.
Рис. 17.3. Разновидности соединений:
а – цилиндрическое; б – шпоночное; в – шлицевое; г – клепаное; д – винтовое; е – болтовое; ж – шпилечное; з – резьбовое со стопорным элементом (шайбой с отгибными лапками); и – шплинтовое; к – штифтовое (со стопорением с разведением разрезного конца); л – фланцевое; м – ниппельное (с припаиванием ниппеля к концу трубопровода); н – накруткой; о – пружинное (с установкой разрезного пружинного кольца); п – пружинное (с установкой пружины)
|
По конструкции и условиям эксплуатации соединения подразделяют на подвижные и неподвижные. Первые характеризуются возможностью относительного перемещения соединяемых деталей или сборочных единиц, вторые такого перемещения не имеют. Неподвижные неразъемные соединения выполняют с гарантированным натягом, развальцовкой, клепкой, сваркой, пайкой и склеиванием.
Существующие соединения также можно подразделить на разъемные и неразъемные. К первым относят те, которые могут быть полностью разобраны без повреждения сопряженных элементов или крепежных деталей.
Неразъемными называют соединения, разборка которых при эксплуатации не предусмотрена, она вызывает повреждение сопряженных элементов или разрушение крепежных деталей или скрепляющего шва.
Разъемные соединения наиболее распространены, однако в последнее время во многих изделиях доля неразъемных соединений начинает расти в связи с более широким использованием неремонтируемых узлов.
Сочетая приведенные признаки, все соединения можно разделить на четыре класса (рис. 18.1): неподвижные разъемные; неподвижные неразъемные; подвижные разъемные; подвижные неразъемные. Число конструкций неподвижных разъемных соединений весьма велико, так как зависит от многих факторов: габаритов, конструкций и функций собираемых узлов, требований к быстроте сборки и точности соединения и т.д. Так, например, крупногабаритные тонкостенные оболочки соединяют фланцевыми, штифтовыми, клиновыми, шпажными или шпоночными соединениями. Они обеспечивают при минимальной массе не только прочность, но и герметичность стыков при высоких давлениях внутри оболочки.
Рис. 8.3. Распространенные виды соединений
Рис. 18.1. Типы соединений деталей и узлов:
а – неподвижные разъемные; б – неподвижные неразъемные; в – подвижные разъемные; г – подвижные неразъемные
Примерами подвижных неразъемных соединений могут служить телескопическая антенна (продольная подвижность звеньев между собой), карданный шарнир (угловая подвижность соединенных деталей, ограниченная допустимой зоной), радиальный подшипник (неограниченное осевое вращение сопрягаемых элементов).
|
Наибольшим разнообразием отличаются методы образования соединений с использованием специальных соединительных элементов – болтов, винтов, заклепок, шпилек и т.п. К этой же группе относятся клиновые, шпоночные, штифтовые и другие соединения.
Для их выполнения предварительно необходимы операции образования контуров для постановки соединительных элементов. Например, в болтовых, винтовых и заклепочных соединениях необходимо образовать отверстия для постановки болтов, винтов и заклепок, нарезать резьбу, обработать гнезда для потайных головок и т.д.
В сварных, паяных и клееных соединениях соединительным элементом является сварной, паяный или клеевой шов. Для их выполнения предварительно необходимы операции обработки кромок, механической и химической очистки соединяемых поверхностей в зоне соединительного шва.
Рассмотрим подробнее способы получения наиболее часто встречающихся в общем машиностроении неразъемных и разъемных соединений.
Технологические процессы сборки разъемных соединений. Наибольшим разнообразием отличаются методы образования разъемных соединений. Их осуществляют различными крепежными и фиксирующими деталями (резьбовыми, клиньями, цилиндрическими и коническими штифтами, стопорными шайбами). Наиболее распространены резьбовые соединения. Их выполняют отдельными (винтами, болтами, шпильками) и специальными крепежными деталями. При сборке обеспечивают требуемый натяг и стопорение резьбовых деталей различными способами.
Сборка резьбовых соединений. Резьбовые соединения в конструкциях машиностроительных изделий составляют 15–25% от общего числа. Такая распространенность объясняется их простотой и надежностью, удобством регулирования затяжки, возможностью разборки и повторной сборки соединения без замены детали.
Широко применяются следующие разновидности резьбовых соединений для:
• обеспечения неподвижности и прочности сопрягаемых деталей;
• правильности их установки;
• регулирования взаимного положения.
Трудоемкость сборки резьбовых соединений составляет 25–35% общей трудоемкости сборочных работ. Их осуществляют с помощью шпилек, болтов (рис. 18.2, а) и винтов (рис. 18.2, б).
Рис. 18.2. Принципиальные схемы соединений деталей:
а – болтовое соединение; б – винтовое соединение
В конструкциях изделий применяют болтовые и винтовые соединения, собираемые без затяжки и с предварительной затяжкой. Область использования соединений первого типа крайне ограничена, соединения второго типа распространены чрезвычайно широко. Предварительная затяжка при сборке играет существенную роль в повышении долговечности работы сборочных единиц или изделия и должна быть такой, чтобы упругие деформации деталей соединения при установившемся режиме работы находились в определенных пределах, обусловленных конструктивными особенностями. Степень предварительной затяжки болта или винта зависит от сил, нагружающих соединение.
|
В связи с наличием зазора в стыках, собираемых без затяжки, появляются дополнительные динамические нагрузки, которые могут резко сократить усталостную прочность резьбовых деталей.
Правильно выбранная затяжка играет большую роль в достижении работоспособности соединения. При уменьшении зазоров предел выносливости резьбовых соединений повышается. На прочность соединений, испытывающих переменные нагрузки, оказывают влияние точность параметров резьбы (особенного шага), концентрация напряжений, характер распределения нагрузки по виткам и пр. Но при этом влияние качества сборки и, прежде всего правильно выбранной посадки в резьбе, величины предварительной затяжки, отсутствия перекосов во многих тяжело нагруженных соединениях особенно заметны.
Гайки и винты при сборке нужно затягивать в определенном порядке. Произвольная затяжка может вызвать перекос или коробление затягиваемой детали.
Болтовые и винтовые соединения в единичном и мелкосерийном производстве собирают с помощью гаечных, торцевых, коловоротных, трещоточных, фрикционных и других ключей. Для обеспечения заданного момента затяжки гаек применяют тарированные и динамометрические ключи.
Механизация сборки резьбовых соединений в условиях массового и серийного производства достигается применением электрических и пневматических инструментов. В условиях массового производства используют многошпиндельные гайковерты, у которых все шпиндели приводятся во вращение либо от одного общего двигателя, либо от индивидуальных. Для облегчения работы механизированный инструмент подвешивают на пружинных блоках. Сборку резьбовых соединений в массовом производстве нередко автоматизируют.
Процесс сборки резьбового соединения в общем случае складывается из следующих элементов: подачи деталей, их установки и предварительного ввертывания (наживления), подвода и установки инструмента, завинчивания, затяжки, отвода инструмента, дотяжки, шплинтовки или выполнения иного процесса, необходимого для предохранения от самоотвинчивания. Из технологических работ в процессе завинчивания 12–17% идет на предварительное ввертывание, 18–20% на затяжку и 5–8% на дотяжку (от всего времени сборки). В случае автоматической сборки все эти три элемента процесса выполняются последовательно одним инструментом. Однако при механизированном выполнении работ предварительное ввертывание часто проводят вручную. Объясняется это тем, что от доброкачественности наживления зависит правильная первоначальная установка одной детали по резьбовому отверстию другой, а также возможность исключения срывов первых ниток резьбы, что нередко приводит к порче дорогостоящих корпусных деталей.
Примерно 80% энергии, расходуемой на весь процесс навинчивания, затрачивается на преодоление сил трения и около 20% на затяжку.
Собираемость винтовых или болтовых соединений зависит от точности или достаточности зазоров между винтом (болтом) и соответствующими поверхностями скрепляемых деталей. Это определяются путем расчета размерных цепей соединений.
Базирование завинчиваемой детали целесообразно осуществлять по резьбовой поверхности по двойной направляющей базе. В этом случае головку резьбовой детали используют в качестве двойной опорной базы. Короткие винты вынуждены базировать по торцу головки – установочная база, резьбовой поверхности – двойная опорная база, а шлиц или грань служит опорной базой. Упругие компенсаторы относительных поворотов соединяемых резьбовых деталей можно создать только при базировании винта или болта по резьбовой поверхности по двойной направляющей базе, в ином случае – при базировании по двойной опорной базе возможна лишь компенсация относительных смещений, поэтому завинчивание деталей будет затруднено из-за повышенных требований к точности технологической системы. Вследствие этого лучше ввинчивать болт в гайку, чем навинчивать гайку на болт.
Для облегчения соединения отверстия под крепеж в базовой детали должны размещаться равномерно и точность их положения необходимо регламентировать. Число типов посадочных и сопрягаемых поверхностей, а также применяемых видов соединений деталей должно быть минимальным. Длина стержней винтов и болтов должна быть по возможности одинаковой и превышать на 20–30% диаметр резьбы детали. Короткие винты желательно подавать в сборочную машину в виде стержней и отделять их по одному в процессе сборки
Если возможно, то целесообразно использовать самонарезающие винты, а также винты, осуществляющие сверление, нарезку или накатку резьбы в сопряженной детали и затем затяжку соединения.
Для правильности установки сопрягаемых деталей и регулирования их взаимного положения используют кольцевые гайки. На рис. 18.3 показана схема фиксации вала 1 в корпусе 2 с использованием кольцевых гаек 3 и контргаек 4.
Рис. 18.3. Схема сборки вала 1 с корпусом 2 с регулировкой взаимного положения кольцевыми гайками 3 и фиксацией контргайками 4:
а – наружной; б – внутренней
Сборка шпоночных соединений. Для передачи крутящего момента в конструкциях часто используют сборку валов с зубчатыми колесами (ступицами) с помощью шпонок. При неподвижных соединениях шпонку устанавливают в паз вала плотно или даже с натягом, в пазу ступицы посадка создается более свободная. Правильность сборки соединений со шпонками в значительной мере обеспечивает работоспособность и надежность работы сборочной единицы. Схема собранного соединения показана на рис. 18.4.
Рис. 18.4. Схема соединения вала с зубчатым колесом
Большое значение при этом прежде всего имеет строгое соблюдение посадок в сопряжениях шпонки с валом и охватывающей деталью. Увеличенные зазоры – одна из основных причин нарушения распределения нагрузок, смятия и разрушения шпонки.
Технологические процессы сборки неразъемных соединений. Конструктивных разновидностей неподвижных неразъемных соединений чрезвычайно много. Большинство из них может быть отнесено к одной из трех групп:
• с силовым замыканием, относительная неподвижность деталей в которых обеспечивается механическими силами, возникающими в результате пластических деформаций;
• с геометрическим замыканием, осуществляемым благодаря форме сопрягаемых деталей;
• соединения, в основе которых лежат молекулярные силы сцепления или адгезии.
К наиболее распространенным процессам сборки неразъемных соединений относятся соединения с гарантированным натягом, сварные, паяные, склеиваемые и заклепочные.
По способу получения нормальных напряжений на сопрягаемых поверхностях соединения с гарантированным натягом условно делят на поперечно-прессовые и продольно-прессовые.
В первом случае сближение сопрягаемых поверхностей происходит радиально или нормально к поверхности. Такие соединения осуществляют одним из следующих способов: нагреванием охватывающей детали перед сборкой; охлаждением охватываемой детали; пластической деформацией (например, развальцовкой), приданием упругости охватываемой детали.
При продольно-прессовом соединении охватываемая деталь под действием прикладываемых вдоль оси сил запрессовывается в охватывающую с натягом, в результате чего возникают силы трения, обеспечивающие относительную неподвижность деталей.
Соединения, собираемые с использованием тепловых методов. Сборку с нагревом охватывающей детали или охлаждением охватываемой осуществляют чаще всего в тех случаях, когда конструкцией в соединении предусмотрены значительные натяги. При тепловых посадках создаются натяги, средняя величина которых примерно в два раза больше, чем при прессовых. Тепловые методы применяют при сборке тяжело нагруженных соединений, требующих высокой прочности, а также когда охватывающая деталь выполнена из материала, имеющего высокий коэффициент линейного расширения, а соединение подвергается в изделии воздействию повышенных температур. Если такое соединение собрать без нагрева, то в процессе эксплуатации его работоспособность может исчезнуть.
Надежность действия тепловых посадок при передаче крутящего момента больше, чем обычных при равных условиях. Объясняется это тем, что при тепловых посадках микронеровности сопрягаемых поверхностей не сглаживаются, как при холодной запрессовке, а сцепляются друг с другом. Время на запрессовку крупногабаритных деталей с нагревом или охлаждением сокращается в 2–4 раза. Кроме того, часто упрощается и удешевляется сборочное оборудование, так как отпадает необходимость в мощных прессах.
Приступать к охлаждению необходимо после того, как охватывающая деталь полностью подготовлена к сборке. Сопрягаемые поверхности обеих деталей должны быть тщательно протерты и обезжирены. При выемке охлажденных деталей следует обязательно пользоваться щипцами или специальными приспособлениями.
Соединения, собираемые путем пластической деформации деталей. Пластическую деформацию используют при сборке соединений, натяг в которых создается радиальным расширением охватываемой или сжатием охватывающей детали. Основное назначение таких соединений – обеспечение неподвижности и герметичности. В конструкциях машиностроительных изделий соединения этого типа широко распространены. Для создания неподвижности и плотности применяют вальцевание, раздачу, бортование, осадку, формирование, обжатие (рис. 18.10, 18.11).
Рис. 18.10. Примеры неразъемных соединений, полученных пластической деформацией:
а – внутренняя заглушка; б – завальцован шарик; в, г, д – запрессовано седло клапана
Рис. 18.11. Схема получения неразъемного соединения:
а – исходное состояние; б – полученное соединение; Ра, Рг – соответственно осевое и радиальное усилия
Поперечно-прессовые соединения, получаемые путем пластической деформации. Пластические деформации используют для неподвижного соединения тонкостенной втулки с корпусом раскаткой (см. рис. 18.10, в). Втулка, запрессованная с небольшим натягом, раздается роликами вращающейся раскатки до требуемого диаметра.
Сборку неразборных соединений в ряде случаев осуществляют обжатием одной из сопрягающихся деталей, выполненной из тонкостенного материала. Обжатие может быть местным или контурным (см. рис. 18.10, г).
Продольно-прессовые соединения. При продольно-прессовом соединении (рис. 18.12) охватывающая деталь под действием прикладываемых вдоль оси сил Рпр запрессовывается на охватываемую с натягом, в результате чего возникают силы трения обеспечивающие относительную неподвижность деталей.
Рис. 18.12. Осевая запрессовка шкива на вал:
а – начато прессования; б – результат прессования
Технологический контроль сборочных единиц
Сущность контроля в машиностроении – проверка соответствия свойств, параметров и характеристик материалов, полуфабрикатов и готовых изделий стандартам и техническим условиям на всех этапах изготовления изделий (разработки, производства, испытания).
Контролируемые параметры:
- физико-химико-механические свойства и химический состав сырья и исходных материалов;
- свойства, структура и внутренние дефекты материала изделий в ходе технологического процесса и готовых изделиях;
- геометрические параметры и дефекты поверхности деталей на стадии изготовления и в готовом изделии;
- динамические характеристики и техническое состояние деталей, узлов и конструкций в процессе изготовления и эксплуатации;
- технические параметры и свойства готовых изделий в процессе приемки, испытаний и эксплуатации.
Назначением производственного контроля является обеспечение качества выпускаемой продукции, под качеством продукции понимается совокупность свойств, обусловливающих ее пригодность удовлетворять определенные потребности в соответствии с ее назначением. Уровень свойств, которым должка удовлетворять продукция, оформлен в её технической характеристике. Для того чтобы обеспечить свойства изделий, заложенные в технической характеристике, при их проектировании формируются требования к геометрическим параметрам, структуре и свойствам отдельных деталей и сборочных единиц. Таким образом, на всех стадиях изготовления, приемки, испытания и эксплуатации изделий необходимо проверять свойства сырья, исходных материалов, полуфабрикатов; геометрические параметры, свойства и структуру деталей; параметры технической характеристики готовой продукции, т. е. осуществлять производственный контроль.
Сущность процесса контроля представляет собой определение того, находится ли значение контролируемого параметра между предельно допустимыми его значениями. Видом контроля является обнаружение нарушения целостности материала деталей (трещин, раковин), локальных нарушений структуры и других внутренних и поверхностных дефектов.
Результаты контроля используются для изъятия негодных материалов и изделий из технологического процесса или для прекращения эксплуатации дефектных изделий; для рассортировки деталей на различные группы качества; для управления технологическим процессом.
Виды контроля. Классификация видов контроля производится в зависимости от назначения, способов проведения, контролируемых параметров и других признаков. При входном контроле проверяются свойства сырья, исходных материалов, качество заготовок, полуфабрикатов и покупных изделий. В процессе пооперационного контроля проверяются параметры, свойства и дефекты деталей, сборочных единиц и изделий в ходе технологического процесса, а задачей приемочного контроля является контроль изделий на конечных этапах технологического процесса. При инспекционном контроле контролируется состояние и технические характеристики изделий в процессе эксплуатации.
Если контроль производится без воздействия на процесс производства, то имеет место так называемый пассивный контроль. При активном контроле проверку изделий или технологического процесса осуществляют в процессе изготовления и используют для управления процессом производства.
При визуальном контроле проверка ведется осмотром невооруженным взглядом. В зависимости от того, нарушается ли целостность изделий после контроля, различают разрушающие и неразрушающие методы контроля.
Сплошной контроль предусматривает 100%-ную проверку изделий, если же проверке подвергается часть изделий из партии, то имеет место статистический или нестатистический выборочный контроль.
В зависимости от контролируемых параметров различают контроль геометрических параметров, контроль поверхностных дефектов, контроль химического состава, контроль физико-механических свойств и т. п.
Особенности процесса контроля геометрических параметров. Сущность контроля геометрических параметров: сопоставление действительных значений геометрических параметров со значениями, определяемыми техническими требованиями к изделию. Контроль осуществляется методом измерений, т. е. с выражением параметра в числовой форме, либо сравнением параметра с мерой или с измерительными поверхностями приборов, настроенных по мере.
Объекты контроля: исходные материалы, заготовки, детали, сборочные единицы и готовые машины на разных стадиях изготовления, приемки и испытания.
Контролируемые параметры: линейные размеры (длина, высота, глубина, зазоры, расстояния, диаметры и т. п.); угловые размеры (углы между плоскостями, осями, между плоскостями и горизонтальной плоскостью, углы конусов и т. п.); геометрические параметры сложных поверхностей (расположение точек или участков относительно заданных баз и относительно друг друга; геометрические характеристики зубчатых и червячных зацеплений, резьбовых, шлицевых и шпоночных соединений; отклонения форм и расположения поверхностей (отклонения от цилиндричности, плоскостности, параллельности, перпендикулярности и т.п.).
Значение геометрических параметров изделий задаются при их проектировании, как правило, в числовой форме и проставляются на чертежах. В процессе изготовления изделий необходимо контролировать соответствие действительной величины и параметров значениям, установленным в технической документации. Большинство геометрических параметров представляют собой или оцениваются через числовые значения, линейных и угловых величин. Эти числовые значения называются размерами, а процесс их контроля - размерным контролем.
Таким образом, целью размерного контроля является сопоставление действительных геометрических параметров изделий, выраженных через размеры, со значениями этих параметров, которые определены при проектировании изделий. Размерный контроль завершается определением годности изделия или выдачей сигнала управления, который используют для отбраковки или для управления технологическим процессом.
Если в процессе контроля значение размера выражают в числовом виде, то такой процесс называют измерением. Определение числового значения размера производят с помощью мер и с помощью измерительных приборов. Специальные меры (калибры, шаблоны, угольники и др.) воспроизводят одно или несколько значений размеров и предназначаются, в основном, для контроля годности изделия без определения численного значения размера.
Особенности процесса выявления внутренних дефектов. Для выявления внутренних дефектов используют разрушающие и неразрушающие методы контроля. В разрушающих методах дефекты наблюдают и измеряют непосредственно на изломах и разрезах контролируемого объекта. В неразрушающих методах используют проникающие поля и излучения, взаимодействующие с материалом контролируемого объекта.
Внутренние дефекты, изменяя физические характеристики материала, будут тем самым изменять некоторые параметры прошедшего или отраженного излучения или поля. Преобразовывая прошедшую или отраженную часть излучения в видимые изображения или электрические сигналы, определяют вид дефекта, его размеры и месторасположение в объекте. Неразрушающие методы позволяют контролировать 100% изделий, проводить автоматическую отбраковку негодных изделий, осуществлять контроль непосредственно в ходе технологического процесса.
Комплекс контрольных операций, выполняемый в процессе узловой и общей сборки:
– комплектности деталей и сборочных единиц;
– использования одноименных размерных групп сопряженных деталей при сборке методом групповой взаимозаменяемости;
– точности посадок и взаимного расположения сопряженных деталей и сборочных единиц;
– герметичности соединений, в том числе качества притирки клапанов;
– выполнения технологических требований по сборке, регулировке, приработке и испытанию изделий;
– отсутствия прокладок и сальников, бывших в эксплуатации;
– смазки деталей сборочных единиц.
Осуществляется контроль технологических параметров и установление функциональных показателей собранных изделий (развиваемая мощность и удельный расход топлива, напор и подача масляного насоса, электрические параметры генератора и др.).
Контроль сборки выполняется с использованием надлежащих средств измерений, которые выбирают с учетом конструктивных характеристик и особенностей изделия, метрологических характеристик, а также себестоимости выполнения контрольной операции.
В качестве средств измерения используют:
– микрометрические и индикаторные инструменты;
– универсальные штангенинструменты;
– электрические и пневматические приборы;
– различные специальные контрольные приборы, приспособления, стенды и установки.
В зависимости от неизменности соблюдения качества собранных изделий используется выборочный или сплошной контроль. Вместе с операциями технологического процесса сборки изделий разрабатываются операции технического контроля, которые производят и определяют заданное качество, а также предоставляют возможность получения информации для регулирования технологического процесса и предотвращения брака.
Погрешности сборки по характеру и проявлению могут быть:
– случайными,
– периодическими.
Некачественные посадки – основные из них. Они вызывают появление других неисправностей. Распространенными дефектами являются:
– отклонения от точности взаимного расположения деталей и узлов;
– неравномерная и беспорядочная затяжка групп резьбовых соединений;
– неплотность прилегания сопрягаемых поверхностей и др.
Большинство погрешностей сборки возникает:
– из-за низкого качества деталей и узлов, поступающих на сборку;
– нарушения технологической дисциплины.
Технологическое оснащение сборки
Технологическое оснащение определяет состав и содержание сборочных операций и включает в себя оборудование, различные приспособления, средства механизации и автоматизации, измерительный и режущий инструмент.
Оборудование сборочных цехов условно можно разделить на две группы: технологическое, предназначенное непосредственно для выполнения работ по осуществлению различных сопряжений деталей, их регулировке и контролю в процессе узловой и общей сборки; вспомогательное – для механизации вспомогательных работ, объем которых при сборке достаточно большой. Удельный вес вспомогательных работ в общей трудоемкости сборки в серийном производстве составляет 30-40% и в массовом – 10-15%.
К технологическому оборудованию при сборке неподвижных разъемных соединений относят одно- и многошпиндельные стационарные установки для навинчивания гаек и затяжки их на болтах, шпильках и т.п.
Сборку неподвижных неразъемных соединений осуществляют механически, а также путем термического воздействия. При сборке неподвижных неразъемных соединений с нагревом охватывающей детали применяют электропечи для нагрева мелких деталей в масляной ванне, индукционные печи и другие нагревательные устройства. Сборку неразъемных соединений с охлаждением охватываемой детали также производят на специальном оборудовании, для чего применяют установки для охлаждения деталей сжиженным газом (кислородом, азотом), твердой углекислотой и т.п. Прочность соединений, собранных с охлаждением охватываемой детали, при прочих равных условиях в 2-2,5 раза выше их прочности после обычной запрессовки и на 10-15% выше, чем при нагреве охватывающей детали.
Обычную запрессовку производят на универсальных и специальных сборочных прессах.
Оборудованием при ручной сборке является верстак. Приспособления разделяют на универсальные и специальные. Первые могут быть применены на любой операции, а вторые проектируют и изготовляют для конкретной операции. Типы привода приспособлений подразделяют на механические, гидравлические, пневматические и пневмогидравлические.
Приспособления в зависимости от назначения можно разделить на следующие группы:
• зажимы, которые служат для закрепления собираемых изделий, сборочных единиц или деталей в требуемом для сборки положении, придания устойчивости сборочной единице и облегчения ее сборки;
• установочные, предназначенные для правильной и точной установки соединяемых деталей или сборочных единиц относительно друг друга, что гарантирует получение требуемых размеров в сборочных цепях;
• рабочие, используемые при выполнении отдельных операций технологического процесса сборки, например вальцевания, запрессовки, постановки и снятия пружин и т.д;
• контрольные, изготовленные применительно к конфигурации, формам, размерам и другим особенностям проверяемых сопряжений сборочных единиц и изделий для контроля конструктивных параметров, получающихся в процессе сборки.
Вспомогательное оборудование включает в себя транспортное, подъемное, установочное и другое оборудование.
Основные виды подъемно-транспортных средств, применяемых в сборочном производстве, приведены на рис. 17.8.
Рис. 17.8. Подъемно-транспортные средства для сборочных производств
Транспортные средства служат главным образом для подвижной сборки. Наиболее распрост
|
|
Типы оградительных сооружений в морском порту: По расположению оградительных сооружений в плане различают волноломы, обе оконечности...
Особенности сооружения опор в сложных условиях: Сооружение ВЛ в районах с суровыми климатическими и тяжелыми геологическими условиями...
Архитектура электронного правительства: Единая архитектура – это методологический подход при создании системы управления государства, который строится...
Общие условия выбора системы дренажа: Система дренажа выбирается в зависимости от характера защищаемого...
© cyberpedia.su 2017-2024 - Не является автором материалов. Исключительное право сохранено за автором текста.
Если вы не хотите, чтобы данный материал был у нас на сайте, перейдите по ссылке: Нарушение авторских прав. Мы поможем в написании вашей работы!