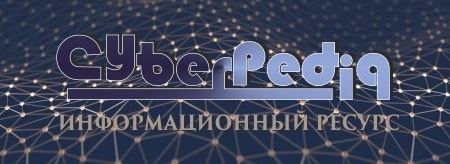
Состав сооружений: решетки и песколовки: Решетки – это первое устройство в схеме очистных сооружений. Они представляют...
Механическое удерживание земляных масс: Механическое удерживание земляных масс на склоне обеспечивают контрфорсными сооружениями различных конструкций...
Топ:
Оценка эффективности инструментов коммуникационной политики: Внешние коммуникации - обмен информацией между организацией и её внешней средой...
История развития методов оптимизации: теорема Куна-Таккера, метод Лагранжа, роль выпуклости в оптимизации...
Устройство и оснащение процедурного кабинета: Решающая роль в обеспечении правильного лечения пациентов отводится процедурной медсестре...
Интересное:
Отражение на счетах бухгалтерского учета процесса приобретения: Процесс заготовления представляет систему экономических событий, включающих приобретение организацией у поставщиков сырья...
Принципы управления денежными потоками: одним из методов контроля за состоянием денежной наличности является...
Подходы к решению темы фильма: Существует три основных типа исторического фильма, имеющих между собой много общего...
Дисциплины:
![]() |
![]() |
5.00
из
|
Заказать работу |
|
|
В зависимости от вида энергии, применяемой при сварке, различают три класса сварки: термический, термомеханический и механический (ГОСТ 19521-74).
К термическому классу относятся виды сварки, осуществляемой плавлением, т.е. местным расплавлением соединяемых частей с использованием тепловой энергии. Основными источниками теплоты при сварке плавлением являются сварочная дуга, газовое пламя, лучевые источники энергии и теплота, выделяемая при электрошлаковом процессе. Источники теплоты характеризуются температурой и концентрацией, определяемой наименьшей площадью нагрева (пятно нагрева) и наибольшей плотностью тепловой энергии в пятне нагрева. Эти показатели определяют технологические свойства источников нагрева при сварке, наплавке и резке.
Основные виды сварки термического класса – дуговая, газовая, электрошлаковая, электронно-лучевая, плазменная, лазерная, термитная и др.
Дуговая сварка. Необходимое для местного расплавления деталей и присадочного материала тепло образуется при горении электрической дуги между свариваемым металлом и электродом. По способу механизации сварка может быть ручная, механизированная и автоматическая. Механизированная и автоматическая сварка может быть под флюсом и в защитных газах.
Газовая сварка. Основной и присадочный металлы расплавляются высокотемпературным газокислородным пламенем (температура до 3200 °С).
Электрошлаковая сварка. Плавление основного металла и присадочного материала происходит за счет тепла, выделяющегося при прохождении электрического тока через расплавленный шлак (в период установившегося процесса).
Электроннолучевая сварка. Сварка выполняется в камерах с разряжением до 10-4–10-6 мм рт. ст. Тепло выделяется за счет бомбардировки зоны сварки электронным потоком, приобретающим высокие скорости в высоковольтной установке, имеющей мощность до 50 кВт. Анодом является свариваемая деталь, а катодом – вольфрамовая нить или спираль, нагретая до температуры 2300 °С.
|
Плазменная сварка. Плавление металлов осуществляется плазменно-дуговой струей, имеющей температуру выше 10 000 °С.
Лазерная сварка. Сварка основана на использовании фотоэлектронной энергии. При большом усилении световой луч способен плавить металл. Для получения такого луча применяют специальные устройства – лазеры. Термитная сварка. Процесс сварки заключается в том, что свариваемые детали закладываются в огнеупорную форму, а в установленный сверху тигель засыпается термит–порошок из алюминия и окиси железа. При горении термита окись железа восстанавливается, а образующийся при этом жидкий металл при заполнении формы оплавляет и соединяет кромки свариваемых изделий.
К термомеханическому классу относятся виды сварки, при которых используется тепловая энергия и давление, – контактная, диффузионная, газопрессовая, и др. Основным видом термомеханического класса является контактная сварка – сварка с применением давления, при которой нагрев осуществляют теплотой, выделяемой при прохождении электрического тока через находящиеся в контакте соединяемые части.
Диффузионная сварка – сварка давлением, осуществляемая взаимной диффузией атомов контактирующих частей при относительно длительном воздействии повышенной температуры и при незначительной пластической деформации. При прессовых видах сварки соединяемые части могут нагреваться пламенем газов, сжигаемых на выходе сварочной горелки, дугой, электрошлаковым процессом, индукционным нагревом, термитом и т.п.
К механическому классу относятся виды сварки, осуществляемые с использованием механической энергии и давления: холодная, взры-вом, ультразвуковая, трением и др.
|
Холодная сварка – сварка давлением при значительной пластической деформации без внешнего нагрева соединяемых частей.
Сварка взрывом – сварка, при которой соединение осуществляется в результате вызванного взрывом соударения быстро движущихся частей.
Ультразвуковая сварка. Сварка осуществляется за счет превращения при помощи специального преобразователя ультразвуковых колебаний в механические высокой частоты и применения небольшого сдавливающего усилия.
Сварка трением. Сварка заключается в том, что вследствие трения одного из свариваемых стержней о другой место соединения разогревается; при приложении осевого усилия соединяемые металлы свариваются.
ВИДЫ СВАРКИ
Для получения неразъёмного соединения при сварке плавлением кромки металла свариваемых элементов (основной металл) и дополнительный металл (сварочная проволока и др.) в месте соединения расплавляются, самопроизвольно или принудительно сливаются в общую сварочную ванну, в которой происходят многие физико-химические процессы и устанавливаются металлические связи.
При удалении источника нагрева металл сварочной ванны кристаллизуется, образуя сварной шов, который и соединяет свариваемые элементы в одно целое. Металл сварного шва обычно значительно отличается от основного свариваемого металла по химическому составу и структуре, так как металл шва всегда имеет структуру литого металла. Рядом со швом в основном металле под действием термического цикла сварки образуется зона термического влияния различной протяженности. ЗТВ это участок основного металла, который нагревался в интервале температур плавления — температура критических точек и подвергся действию напряжений во время сварки, в результате чего в металле происходят структурные изменения.
Металл шва и основной металл зоны термического влияния, в котором произошли какие-либо структурные изменения, называются сварным соединением. Механические, коррозионные и другие свойства сварного соединения могут существенно отличаться от свойств основного металла. При равенстве показателей механических свойств сварного соединения и исходного металла, сварное соединение должно быть равнопрочно основному металлу.
В качестве источника теплоты при сварке плавлением можно использовать различные источники нагрева: электрическую дугу (электродуговая сварка), теплоту шлаковой ванны (электрошлаковая сварка); энергию струи ионизированных газов «холодной» плазмы (плазменная сварка); теплоту, выделяемую в изделии в результате преобразования кинетической энергии электронов (электронно-лучевая сварка); когерентный световой луч лазера (лазерная сварка); энергию при сжигании горючего газа в кислороде (газовая сварка) и другие.
|
Основной способ сварки плавлением — электродуговая сварка — имеет много разновидностей, связанных со степенью механизации: ручная, механизированная, автоматическая, с применением различных защитных веществ — толстого покрытия на электродах (при ручной сварке), флюсов, защитных газов или порошковой проволоки при механизированной сварке, контролируемой атмосферы (защитных газов или вакуума) при некоторых способах дуговой и электронно-лучевой сварки. Сварка плавлением применяется для весьма широкого спектра материалов: углеродистые, высокоуглеродистые, высоколегированные стали, цветные металлы и сплавы, а также неметаллы — стекло, керамика, графит.
Все указанные особенности значительно усложняют задачи, которые стоят перед инженерами-технологами, разрабатывающими технологический процесс сварки плавлением.
Разработанный технологический процесс сварки не только должен обеспечивать получение надёжных сварных соединений и конструкций, отвечающих всем эксплуатационным требованиям, но должен также допускать максимальную степень комплексной механизации и автоматизации всего производственного процесса изготовления изделия, должен также быть экономически обоснованным по расходу энергии, сварочных материалов, затрат человеческого труда.
Такие оптимизационные технологические задачи решаются на основе использования расчётных, аналитических методов проектирования технологического процесса сварки. При разработке технологического процесса изготовления сложной сварной конструкции целесообразен расчёт нескольких вариантов технологии на ЭВМ с последующим отбором оптимального варианта технологом-сварщиком.
|
Большое внимание к сварке обусловлено универсальностью этого технологического процесса получения неразъёмных соединений, возможностью экономии до 20% металла, повышением прочности и непроницаемости соединений, возможностью создания уникальных конструкций, которые при других способах изготовления конструкций создать не представляется возможным или экономически не выгодно.
Сварка классифицируется по: техническим, технологическим, физическим признакам, ГОСТ 19521–74. Классификация по физическим признакам представлена на рис. 1.1.
Термический класс сварки включает виды сварки, осуществляемые плавлением с использованием тепловой энергии.
Термомеханический класс включает в себя виды сварки, осуществляемые с использованием тепловой энергии и давления на свариваемые детали.
Механический класс включает виды сварки, осуществляемые с использованием механической энергии и давления.
Дуговая сварка классифицируется по следующим технологическим признакам.
1. По виду электрода:
● штучным,
● ленточным (сплошного сечения и порошковая),
● проволочным (сплошного сечения и порошковая),
● плавящимся,
● неплавящимся (с применением и без применения присадочной сварочной проволоки).
Рис. 1.1 Классификация по физическим признакам и видам сварки
2. По виду дуги:
● свободной,
● сжатой.
3. По роду и полярности тока:
● переменный ток (промышленной и повышенной частоты),
● постоянный ток прямой полярности,
● постоянный ток обратной полярности,
● пульсирующим током.
4. По характеру воздействия дуги на основной металл:
● прямого действия,
● косвенного действия,
● трехфазной дугой.
5. По степени погружения дуги:
● нормальной дугой,
● погружённой дугой.
6. По числу дуг с раздельным питанием:
● однодуговая,
● двухдуговая,
● многодуговая.
7. По числу электродов с общим подводом сварочного тока:
● одноэлектродная,
● двухэлектродная,
● многоэлектродная.
8. По наличию и направлению колебаний электрода относительно
шва:
● без колебаний,
● с продольными колебаниями,
● со сложными колебаниями,
● с поперечными колебаниями.
9. По наличию внешнего воздействия при формировании шва:
● со свободным формированием,
● с принудительным формированием.
Классификация сварки по техническим признакам представлена на рис. 1.2. В зависимости от условий проведения сварки её классифицируют по способу защиты сварочной ванны от окружающей среды.
Комбинированная защита представляет использование нескольких способов, например — газошлаковая.
Процесс сварки может быть непрерывным, подразумевается, что параметры режима постоянны во времени. Использование прерывистых (импульсных) процессов позволяет значительно расширить технологические возможности сварки. При использовании импульсных технологий можно уменьшить толщины свариваемых материалов, получить более благоприятную структуру сварного шва вследствие изменения термического цикла сварки, обеспечить управляемый перенос электродного металла при сварке и т. д.
|
При ручных способах сварки, как правило, подача электродной или присадочной проволоки, и перемещение источника нагрева производятся сварщиком. Поэтому ручная сварка остаётся самым сложным по технике исполнения способом. Изменение степени механизации с ручной на механизированную сварку подразумевает при ручных способах сварки, как правило, подача электродной или присадочной проволоки, и перемещение источника нагрева производятся сварщиком. Поэтому ручная сварка остаётся самым сложным по технике исполнения способом.
Рис. 1.2 Классификация сварки по техническим признакам
Изменение степени механизации с ручной на механизированную сварку подразумевает подачу электродного материала сварочным оборудованием (механизм подачи электродной проволоки), а перемещение сварочной горелки или головки осуществляется вручную. При автоматической сварке механизируются все операции процесса, включая подачу проволоки и перемещение автомата. При автоматизированной сварке дополнительно производят подачу, перемещение, отвод изделий или оборудования в автоматическом режиме, например автомобильный конвейер по сборке кузова. При этом роль человека сводится к наблюдению за протекающим технологическим процессом и контролю необходимых параметров и показателей.
|
|
Общие условия выбора системы дренажа: Система дренажа выбирается в зависимости от характера защищаемого...
Кормораздатчик мобильный электрифицированный: схема и процесс работы устройства...
Индивидуальные очистные сооружения: К классу индивидуальных очистных сооружений относят сооружения, пропускная способность которых...
Автоматическое растормаживание колес: Тормозные устройства колес предназначены для уменьшения длины пробега и улучшения маневрирования ВС при...
© cyberpedia.su 2017-2024 - Не является автором материалов. Исключительное право сохранено за автором текста.
Если вы не хотите, чтобы данный материал был у нас на сайте, перейдите по ссылке: Нарушение авторских прав. Мы поможем в написании вашей работы!