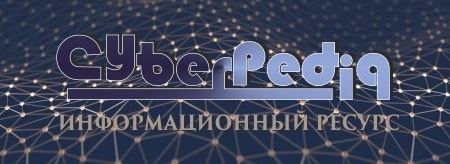
Адаптации растений и животных к жизни в горах: Большое значение для жизни организмов в горах имеют степень расчленения, крутизна и экспозиционные различия склонов...
Индивидуальные и групповые автопоилки: для животных. Схемы и конструкции...
Топ:
Марксистская теория происхождения государства: По мнению Маркса и Энгельса, в основе развития общества, происходящих в нем изменений лежит...
Оснащения врачебно-сестринской бригады.
Выпускная квалификационная работа: Основная часть ВКР, как правило, состоит из двух-трех глав, каждая из которых, в свою очередь...
Интересное:
Распространение рака на другие отдаленные от желудка органы: Характерных симптомов рака желудка не существует. Выраженные симптомы появляются, когда опухоль...
Уполаживание и террасирование склонов: Если глубина оврага более 5 м необходимо устройство берм. Варианты использования оврагов для градостроительных целей...
Искусственное повышение поверхности территории: Варианты искусственного повышения поверхности территории необходимо выбирать на основе анализа следующих характеристик защищаемой территории...
Дисциплины:
![]() |
![]() |
5.00
из
|
Заказать работу |
|
|
Металлизация — это процесс напыления предварительно расплавленного металла на специально подготовленную поверхность детали (подложку) струей сжатого газа или воздуха..
Частицы распыленного металла, находясь в пластическом состоянии, ударяются о поверхность детали с большой скоростью, деформируются и внедряются в неровности поверхности детали, образуя покрытие. Соединение металлических частиц с поверхностью детали и между собой носит в основном механический характер, и только в отдельных точках наблюдается сваривание нанесенного металла с подложкой. Перечислим общие преимущества и недостатки этого метода.
Преимущества: высокая производительность, небольшой нагрев детали (до температуры 120… 180 °С), высокая износостойкость покрытия; возможность нанесения покрытия толщиной от 0,1 до 10 мм и более из любых металлов и сплавов; простота технологического процесса и оборудования.
Недостатки: пониженная механическая прочность покрытия, невысокая прочность сцепления покрытия с подложкой.
В настоящее время применяется пять видов металлизации деталей автомобилей: газопламенная, высокочастотная, электродуговая, плазменно-дуговая и металлизация взрывом (детонационное напыление).
Газопламенная металлизация осуществляется с помощью аппаратов, в которых напыляемый металл (в виде электродной проволоки или металлического порошка) плавится ацетилено-кислородным пламенем и распыляется струей сжатого воздуха.
Дополнительные преимущества: слабое окисление металла, мелкий распыл, сравнительно высокая прочность покрытия.
Недостатком является сравнительно невысокая производительность процесса.
Высокочастотная металлизация осуществляется с применением аппаратов, в которых проволока расплавляется индукционным нагревом и распыляется сжатым воздухом.
Дополнительные преимущества: слабое окисление благодаря возможности регулирования температуры в зоне нагрева и сравнительно высокая механическая прочность покрытия.
Недостатки: невысокая производительность, сложность и высокая стоимость применяемого оборудования.
Электродуговая металлизация осуществляется с помощью аппаратов, в которых металл плавится электрической дугой, горящей между двумя электродными проволоками, и распыляется струей сжатого воздуха. В ручных металлизаторах подача электродной проволоки (ЭМ-3, -9 и -14) осуществляется от пневмотурбиных, в станочных — от электродвигателя со встроенным редуктором.
Дополнительные преимущества: высокая производительность процесса (3… 14 кг/ч); возможность обеспечения высокой температуры, что позволяет наносить на деталь тугоплавкие металлы; сравнительная простота конструкции металлизатора.
Недостатки: повышенное окисление металла, значительное выгорание легирующих элементов, пониженная плотность покрытия.
Плазменно-дуговая металлизация осуществляется посредством расплавления и переноса металла на поверхность детали под воздействием плазменной струи.
Плазменная струя — это частично или полностью ионизированный газ, обладающий электропроводностью и имеющий высокую температуру. Она получается при нагреве плазмообразующего газа в электрической дуге, горящей в закрытом пространстве.
Для получения плазменной струи между катодом и анодом возбуждают электрическую дугу от источника постоянного тока напряжением 60…70 В. В качестве плазмообразующих газов используются аргон, азот, гелий, водород и их смеси.
Процесс образования плазмы при подаче азота состоит из двух стадий (у газа типа аргона только одна стадия):
- диссоциации;
- ионизации.
Обе стадии образования плазмы протекают с поглощением теплоты. Используемый газ после подачи в зону горения электрической дуги и ионизации проходит через сопло плазмотрона в виде струи небольшого сечения. Обжатие струи обеспечивают холодные стенки канала сопла плазмотрона, непрерывно охлаждаемого проточной водой, и электромагнитное поле. Канал плазмотрона имеет положительный потенциал, ионизированный газ заряжен тоже положительно, что создает взаимное отталкивающее действие и сохраняет плазмотрон от возможного взрыва.
Температура плазменной струи в зависимости от силы тока дуги и расхода плазмообразующего газа достигает (1… 3) * 104°С при скорости истечения 1000… 1500 м/с. В качестве присадочного материала применяют гранулированные порошки с размером частиц 50… 150 мкм.
Дополнительные преимущества:
высокая производительность — 3… 12 кг/ч;
высокая скорость частиц — 150 …200 м/с, наибольшая скорость достигается на расстоянии 50…80мм от плазмотрона;
возможность наносить на поверхность детали любой металл или сплав толщиной 0,1… 10 мм;
сравнительно высокая прочность сцепления покрытия с подложкой.
Основным недостатком является значительный шум.
Металлизация взрывом (детонационное напыление) осуществляется путем расплавления, распыления и переноса металла на поверхность детали за счет энергии взрыва смеси ацетилена и кислорода.
После очередной продувки азотом ствола металлизатора, охлаждаемого проточной водой, в него подаются в определенной пропорции ацетилен и кислород. После этого вводится через дозатор напыляемый порошок с размерами гранул 50… 100 мкм. Газовая смесь поджигается от свечи электрической искрой. Взрывная волна сообщает частицам порошка скорость до 800 м/с (на расстоянии 75 мм от среза ствола). В результате за один цикл наносится слой металла толщиной до 6 мкм. Процесс повторяется автоматически с частотой 3—4 раза в секунду.
Дополнительные преимущества:
сравнительно высокая производительность — при диаметре ствола 20…25 мм наносится покрытие на поверхность площадью 5 см2 толщиной 1,2 мм;
высокая прочность сцепления покрытия с подложкой;
невысокая температура поверхности детали (не более 200 °С).
Недостатком является высокий уровень шума (до 140 дБ), поэтому процесс осуществляется в специальных шумопоглощающих камерах.
|
|
|
|
Организация стока поверхностных вод: Наибольшее количество влаги на земном шаре испаряется с поверхности морей и океанов (88‰)...
Общие условия выбора системы дренажа: Система дренажа выбирается в зависимости от характера защищаемого...
Эмиссия газов от очистных сооружений канализации: В последние годы внимание мирового сообщества сосредоточено на экологических проблемах...
Архитектура электронного правительства: Единая архитектура – это методологический подход при создании системы управления государства, который строится...
© cyberpedia.su 2017-2024 - Не является автором материалов. Исключительное право сохранено за автором текста.
Если вы не хотите, чтобы данный материал был у нас на сайте, перейдите по ссылке: Нарушение авторских прав. Мы поможем в написании вашей работы!