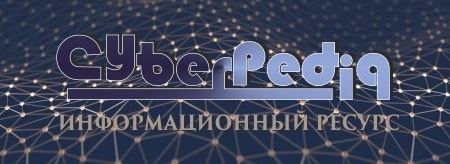
История создания датчика движения: Первый прибор для обнаружения движения был изобретен немецким физиком Генрихом Герцем...
Эмиссия газов от очистных сооружений канализации: В последние годы внимание мирового сообщества сосредоточено на экологических проблемах...
Топ:
Методика измерений сопротивления растеканию тока анодного заземления: Анодный заземлитель (анод) – проводник, погруженный в электролитическую среду (грунт, раствор электролита) и подключенный к положительному...
Оснащения врачебно-сестринской бригады.
Устройство и оснащение процедурного кабинета: Решающая роль в обеспечении правильного лечения пациентов отводится процедурной медсестре...
Интересное:
Аура как энергетическое поле: многослойную ауру человека можно представить себе подобным...
Распространение рака на другие отдаленные от желудка органы: Характерных симптомов рака желудка не существует. Выраженные симптомы появляются, когда опухоль...
Национальное богатство страны и его составляющие: для оценки элементов национального богатства используются...
Дисциплины:
![]() |
![]() |
5.00
из
|
Заказать работу |
|
|
Под пневматическим транспортом сыпучих материалов понимают перемещение по трубопроводу смеси воздуха с твердыми частицами [2, 7]. Основой работы любой пневмотранспортной системы является наличие разности давлений в начале и конце трубопровода. В зависимости от способа создания перепада давления и его значений пневмотранспортные установки для солода подразделяют на всасывающего типа, нагнетающего типа и смешанного (всасывающе-нагнетающего), а также на установки низкого (до 5.103 Па), среднего (от 5.103 до 5.104 Па) и высокого (свыше 5.104 Па) давления.
Во всасывающих установках (рисунок 3.29 а) воздух отсасывается воздуходувной машиной из системы, в которой создается разрежение. Вследствие этого воздух из атмосферы устремляется в загрузочное
устройство 1 и, проходя через слой солода или встречая на своем пути поступающий в трубопровод сыпучий материал, подхватывает его и перемещает по материалопроводу 2 в отделитель 3, откуда продукт выводится через шлюзовый затвор 8 и поступает по материалопроводу 4 в отделитель 5, откуда продукт выводится через шлюзовый затвор 8. Отработанный воздух выбрасывается воздуходувной машиной 6 через глушитель 7 в атмосферу.
Достоинствами всасывающих пневмотранспортных установок являются: простота конструкции, возможность забора солода из нескольких точек, обеспечение высоких санитарно-гигиенических условий
в рабочих помещениях. Поскольку в этих установках вся система находится под вакуумом, загрузочные устройства не требуют герметизации. К недостаткам этих установок следует отнести возможность создания высоких перепадов давлений (до 5.105 Па), наличие специальных герметизирующих устройств в местах вывода продукта из системы.
|
В нагнетающих установках (рисунок 3.29 б) воздуходувная машина нагнетает воздух в пневмосистему, создавая давление воздуха в ней выше атмосферного: наибольшее – в месте загрузки, наименьшее –
в отделителе. Достоинство нагнетающих пневмоустановок – возможность создания теоретически неограниченного давления, что позволяет использовать их при транспортировании солода потоками как низкой, так и высокой концентрации. К недостаткам нагнетающих пневмоустановок следует отнести сложность конструкции загрузочных устройств и повышенные требования, предъявляемые к герметичности пневмосистемы.
Всасывающе-нагнетающие установки (рисунок 3.29 в) включают
в себя положительные качества как всасывающих, так и нагнетающих установок. В зависимости от количества материалопроводов пневмоустановки бывают простыми (с одним материалопроводом) и разветвленными (с двумя и более материалопроводами). В разветвленных пневмоустановках по материалопроводам можно одновременно транспортировать различные сыпучие материалы из нескольких точек с разными производительностями. Недостатком разветвленных пневмоустановок является влияние изменения нагрузки в одном из материалопроводов на стабильность работы других материалопроводов.
Расчет пневмотранспортной установки. При проектировании установок пневматического транспорта солода чаще всего задают суточную производительность технологической линии. В этом случае при определении расчетной производительности (кг/ч) проектируемой установки необходимо учитывать коэффициент неравномерности работы линии
=1,1¸1,2.
Величина массовой концентрации смеси для зернистых материалов ( = 3,0¸8,0) зависит от размера частиц, их плотности, транспортабельности, конфигурации трассы и т.д. Причем большие значения следует брать для материалов с большей плотностью.
В зависимости от скорости витания (м/с) продукта
вычисляют рабочую скорость воздуха, обеспечивающую устойчивое
|
транспортирование в вертикальном (м/с) или в горизонтальном
(м/с) материалопроводе:
; (3.142)
, (3.143)
где – диаметр материалопровода, м;
– коэффициент трения;
– эквивалентный диаметр частиц, м.
По принятому значению диаметра материалопровода и скорости воздуха находят расход воздуха и уточняют значение концентрации.
Суммарные потери давления (Па) при транспортировании равны:
, (3.144)
где – потери давления в основных элементах установки (приемнике, материалопроводе и отделителе), Па;
– потери давления во вспомогательных элементах установки (пылеотделителях, воздуховодах), Па.
Потери давления в приемнике (Па) определяют по скорости воздуха в материалопроводе:
, (3.145)
где – коэффициент сопротивления приемника.
Потери давления в материалопроводе
, (3.146)
где – потери давления при движении чистого воздуха, Па;
– потери давления на разгон солода в начальном участке материалопровода, Па;
– потери давления на трение солода, Па;
– потери давления на подъем солода, Па;
– потери давления в местных сопротивлениях, Па.
Потери давления при движении чистого воздуха (Па):
, (3.147)
где – коэффициент гидравлического сопротивления для стальных бесшовных труб;
– критерий Рейнольдса;
– коэффициент динамической вязкости воздуха, Па.с;
– длина материалопровода, м.
Потери давления на разгон солода в начальном участке
, (3.148)
где – коэффициент потерь давления на разгон:
для вертикальных материалопроводов
; (3.149)
для горизонтальных материалопроводов
, (3.150)
где – критерий Фруда;
– плотность вещества частицы, кг/м3.
Потери давления на трение солода
, (3.151)
где – коэффициент потерь давления на трение солода:
для вертикальных материалопроводов
; (3.152)
для горизонтальных материалопроводов
.
Потери давления в местных сопротивлениях
, (3.153)
где – сумма коэффициентов местных сопротивлений.
Потери давления на подъем солода
, (3.154)
где – высота подъема солода, м.
По полученным расчетным значениям расхода воздуха и суммарным потерям давления в сети подбирают воздуходувную машину, которая обеспечила бы работу установки с расчетными параметрами при наибольшем КПД.
Потребную мощность электродвигателя воздуходувной машины (кВт) вычисляют по формуле
, (3.155)
где – общий расход воздуха в сети, м3/с;
|
– КПД воздуходувной машины;
– КПД привода воздуходувной машины.
Машины для обработки солода
Сухой горячий пивоваренный солод, выгруженный из сушилки, очищается от ростков, которые содержат горькие вещества, легко переходящие в пиво. Ростки очень гигроскопичны, поэтому их следует отделять от солода тотчас после сушки, пока они хрупкие. Очистка солода от ростков производится на росткоотбойной машине [1, 5].
Сухой солод после выдерживания на складе и перед подачей
в производство с целью удаления из него пыли, оставшихся ростков
и других примесей пропускают через солодополировочные машины, после которых он приобретает чистый вкус, а поверхность его становится блестящей [1, 2].
Дробление высушенного и отлежавшегося солода представляет собой тонкое измельчение солода для ускорения физиологических и биохимических процессов растворения зерна при затирании. Для этих целей используют солододробилки, вальцовые станки и мельницы.
Росткоотбойные машины. Простейшая росткоотбойная машина представляет собой ситчатый барабан с вращающимися в нем лопастями (рисунок3.30). Солод с ростками шнеком 1 подают внутрь барабана, где он подхватывается лопастями 2 и приводится во вращательное движение, тесно соприкасаясь с внутренней поверхностью барабана. Отделяющиеся вследствие энергичного перемешивания и трения ростки проваливаются сквозь отверстия в барабане и шнеком 3 удаляются; оставшийся внутри солод винтообразными лопастями продвигается
к противоположному концу машины. Образующаяся во время работы пыль отсасывается центробежным вентилятором 4 в приемник 5, откуда при накоплении выводится.
В лопастной росткоотбойной машине (рисунок 3.31) вместо ситчатого барабана и отбивочного устройства установлены два вала 6 с девятью лопастями, вращающимися в цилиндрическом корпусе встречно и приводимыми во вращение через шестерню 7. Внутренняя полость лопастной росткоотбойной машины разделена на три зоны (I, II, III), в каждой из которых установлено по три лопасти. Угол расположения лопастей 5 в пространстве во всех трех зонах по отношению одна к другой составляет 900.
|
В лопастной росткоотбойной машине солод непрерывным потоком подается в зону I корпуса 4, где с помощью лопастей 5 интенсивно перемешивается и перемещается в зону II. В зоне II солод также перемешивается и направляется в зону III, где лопасти сдерживают перемещение и перемешивание потока солода. При прохождении солода через все три зоны происходит отделение ростков от зерен. Смесь ростков и солода поступает к выгрузочной воронке 3, на которой размещены воздуховод 2 и дисковый распылитель 1. Лопасти на распылителе
1 имеют определенную кривизну, благодаря чему солод приобретает вращательное движение. При этом происходит интенсивное распыление ростков, движущихся вместе с потоком солода вниз. К средней части вертикального воздуховода подключен вентилятор, который потоком воздуха увлекает ростки и направляет их в циклон. Интенсивность воздушного потока регулируется жалюзийной решеткой.
Для повышения производительности росткоотбойной машины
и качества очистки от ростков используются машины с большим ситовым путем прохождения солода. Схема этой более сложной машины показана на рисунке 3.32. Солод с ростками шнеком 1 подается внутрь вращающегося стального цилиндра 2, имеющего лопасти 3, расположенные в два ряда по всей длине цилиндра. При вращении цилиндра 2 солод энергично перемешивается лопастями, очищается от ростков
и постепенно перемещается вдоль цилиндра. На наружной поверхности цилиндра 2 прикреплены винтообразные лопасти, которые передвигают солод по неподвижному ситчатому цилиндру 4. Ростки проходят сквозь ситчатый цилиндр и шнеком 5 удаляются из машины; очищенный солод удаляется сходом в конце ситчатого цилиндра. Машина имеет вентилятор для очистки солода от мелких частиц и пыли.
К основным расчетным параметрам росткоотбойных машин относят: производительность, окружную скорость ситчатого барабана, размеры цилиндра (диаметр и длину) и потребную скорость электродвигателя.
Производительность росткоотбойной машины определяется по формуле
, (3.156)
где – коэффициент, учитывающий размеры рабочей поверхности цилиндра (
0,7¸0,95);
– диаметр цилиндра, м;
– длина рабочей части цилиндра, м;
– удельная зерновая нагрузка, т/(ч.м2).
Удельная нагрузка ( = 1,5¸8,0 т/(ч.м2)) зависит от особенностей обрабатываемого солода, режима работы машины, типа ситчатого барабана.
Потребная мощность электродвигателя росткоотбойной машины
, (3.157)
где – удельный расход электроэнергии, кВт.ч/т.
Значение удельного расхода электроэнергии зависит от перерабатываемого солода и составляет 0,5–1,2 кВт.ч/т.
Полировочная машина. Полировочная машина (рисунок 3.33) состоит из трех основных элементов: наклонных плоских сит 1, щеточного барабана 2 и центробежного вентилятора 3.
|
Очищаемый солод непрерывным потоком поступает на колеблющиеся сита; сходом с верхнего сита идут крупные примеси, сходом с нижнего сита – солод; проходом сквозь нижнее сито удаляются мелкие примеси. Пыль из оптовой коробки отсасывается вентилятором посредством трубы 4.
Очищенный на ситах солод поступает на быстровращающийся щеточный барабан 2 и многократно отбрасывается на волнистую деку 5. Под действием ударов и трения поверхность зерен солода очищается от загрязнений и солод полируется.
Рабочая щель между декой и щеточным барабаном регулируется установочным винтом 6, перемещающим деку в горизонтальном направлении. Полированный солод при выходе из машины вновь проветривается струей воздуха от того же вентилятора 3. Под вентилятором установлен расширительный конус 7 для улавливания захваченных воздухом зерен солода.
К основным расчетным параметрам щеточных полировочных машин относят производительность и потребную мощность.
Производительность определяют в зависимости от нагрузки на единицу внутренней поверхности щеточной деки, соприкасающейся
с наружным диаметром щеточного барабана:
, (3.158)
где – коэффициент, учитывающий длину дуги деки;
– внутренний радиус деки, м;
– длина деки, м;
– удельная нагрузка на деку, т/(ч.м2).
Удельная зерновая нагрузка на деку в солодополировочных машинах составляет от 6,4 до 10,0 т/(ч.м2).
Потребную мощность для привода щеточного барабана определяют по формуле
, (3.159)
где – удельный расход электроэнергии, кВт.ч/т.
Удельный расход электроэнергии для привода солодополировочных машин составляет от 0,7 до 0,9 кВт.ч/т.
3.5 Контрольные вопросы
1. Машинно-аппаратурная схема производства солода.
2. Назовите основное оборудование для изготовления солода.
3. Какова цель замачивания зерна перед солодоращением?
4. Основные факторы, влияющие на процесс замачивания зерна.
5. Какие вы знаете способы замачивания зерна?
6. Для чего производят сортирование зерна перед замачиванием?
7. Устройство и принцип работы замочного аппарата.
8. Назовите основные параметры расчета замочного оборудования.
9. Цель проращивания зерна.
10. Какие существуют системы солодовен?
11. Каков режим проращивания зерна в токовых солодовнях?
12. Каковы устройство и расчет площади сит пневматической солодовни?
13. Какова последовательность расчета основных размеров солодовенного аппарата ящичного типа?
14. Какие вы знаете конструкции ящичных солодовен?
15. Какие преимущества имеют барабанные солодовни перед ящичными?
16. Как устроена барабанная солодовня?
17. Опишите конструкцию ворошителей в ящичной солодовне и солодовне с передвижной грядкой.
18. Как определяется требуемый расход воздуха на проветривание солода при ращении?
19. Устройство и принцип работы солодовни с передвижной грядкой.
20. Назовите типы сушильных аппаратов солода.
21. Расскажите по схеме, из чего складывается тепловой баланс сушилки. Назначение процесса сушки свежепроросшего солода.
22. Назовите и охарактеризуйте три стадии сушки солода.
23. Устройство и принцип действия одноярусной сушилки.
24. Устройство и принцип действия двухъярусной сушилки.
25. Устройство и принцип действия вертикальной сушилки.
26. Сушилка непрерывного действия ЛСХА, устройство и принцип действия.
27. Чем отличается режим сушки темного солода от светлого?
28. Для чего и как отделяют ростки от сухого солода?
29. Каков принцип действия росткоотбойной машины?
30. Каков принцип действия полировочной машины?
ТИПОВЫЕ ЗАДАЧИ
4.1 Расчет оборудования для разделения зерновой смеси
по линейным размерам зерна
Задача 1.1 В ситовой цилиндр с плоским наклонным ситом поступает на очистку 15 т/ч ячменя. Определить геометрические размеры сита при удельной нагрузке на сито 2200 кг/(ч.м) и удельной производительности 900 кг/ (при b =10 % и W =15 %). Засоренность поступающего зерна 17 %, влажность 21 %.
Задача 1.2 Определить рабочий диапазон частоты колебаний
и максимальную амплитуду колебаний расположенного под углом наклона 14 ° плоского сита. На сите происходит очистка зерен ржи от примесей. Кинематическая система сита характеризуется условным кинематическим параметром 1,2. Радиус малого кривошипа 50 мм.
Задача 1.3 На плоском наклонном сите сепаратора подвергаются очистке 150 кг пшеницы. Угол наклона сита 10°, радиус малого кривошипа кинематической системы 75 мм. Необходимо определить мощность электродвигателя, затрачиваемую на работу сита весом
95 кг. Мгновенный угол поворота кривошипа 25,8 °.
Задача 1.4 Для выделения длинных примесей из риса используется цилиндрический триер, производительность которого равна
2000 кг/ч. Частота вращения цилиндра триера равна 50 об/мин. Требуется определить угол, на который поднимаются частицы риса при вращении цилиндра, а также число ячеек на поверхности триера при условии, что шаг расположения ячеек равен 1,2 d (d – диаметр ячейки).
Задача 1.5 На первой и второй стадиях очистки кукурузы используются соответственно тихоходные и быстроходные триеры. Известно, что угол подъема зерен основной культуры в триерах составляет 60 ° и 170 °. Определить частоту вращения триер. Производительность триер 4500 кг/ч.
Задача 1.6 Кинематический режим цилиндрического триера характеризуется показателем к= 0,6. Определить рабочую и предельную скорость вращения цилиндра, если в триере происходит очистка
1000 кг/ч гречихи от коротких примесей. Если площадь ячеистой поверхности цилиндра занимает 70 % общей поверхности, подобрать длину стандартного триера.
Задача 1.7 Выполнить проверочный расчет производительности цилиндрического триера для очистки длинных примесей из ячменя при коэффициенте использования ячеистой поверхности 0,85. Рабочая частота вращения цилиндра определяется подъемом зерен на угол 150 °,
длина цилиндра 750 мм. Подача мелкой фракции 225 кг/ч, ячейки располагаются с шагом 0,8 d (d – диаметр ячейки).
Задача 1.8 На поверхности цилиндрического триера располагаются ячейки с шагом t=0,9 d, проекцию сечения ячейки в приближении можно считать квадратной. В триер на очистку от длинных примесей подается пшеница. Определить производительность триера и потребную мощность.
Задача 1.9 Радиусы диска триера по внешним и внутренним ячейкам составляют 450 мм и 270 мм соответственно. В триере происходит очистка 5 т/ч зерна от коротких примесей. Требуется определить необходимое количество дисков триера. Рассчитать затраты мощности.
Задача 1.10 Выполнить проверочный расчет производительности дискового триера с подачей мелкой фракции 152 кг/ч. В триере происходит очистка ржи от длинных примесей. Диаметр диска по внешним ячейкам 650 мм. Работа триера характеризуется кинематическим показателем 1,5. Ширина перемычки между ячейками диска 0,8 d (d – диаметр ячейки). Коэффициент использования ячеистой поверхности 0,9. Количество рабочих дисков триера 25.
Задача 1.11 В дисковый триер на очистку от коротких примесей подается ячмень. В триере установлены диски диаметром 380 мм. Рассчитать рабочую частоту вращения. В триере установлены 11 рабочих дисков.
Задача 1.12 При работе цилиндрического сита происходит подъем зерновой массы на угол 140 °. Определить производительность сита. Цилиндр характеризуется следующими показателями: диаметр 800 мм, длина 2250 мм, предельный наклон цилиндра составляет 0,1 м на 1 м длины. На сортировку подается овес. Внутренний объем заполняется зерновой массой наполовину.
4.2 Расчет оборудования для разделения зерновой смеси
по аэродинамическим свойствам
Задача 2.1 Определить скорость воздушного потока в пневмосепарирующем канале сепаратора, необходимую для очистки ячменя первого сорта. Воздух нагнетается в сепаратор под давлением
0,23 МПа при температуре 22 ° С. Масса 1000 зерен составляет 45 г, коэффициент сопротивления частицы ячменя 0,43.
Задача 2.2 Удельная зерновая нагрузка для воздушного сепаратора составляет 220 кг /() при ширине сепарирующего канала
330 мм. Требуется определить эффективность пневмосепарирования
ржи размером 3,2 мм. Масса 1000 зерен составляет 40 г, коэффициент сопротивления частиц 0,67. Температура воздуха в канале 24 ° С, давление 1,8 МПа.
Задача 2.3 В воздушном сепараторе достигается эффективность пневмосепарирования 70 % при удельной нагрузке на канал
100 кг /(). Определить геометрические параметры и начертить схему пневмосепарирующего канала. В сепараторе очищается 5,4 т/ч зерна.
Задача 2.4 Для очистки 7 т/ч пшеницы с размером частиц
2,8 мм в воздушном сепараторе необходимо подобрать вентилятор. Удельная нагрузка на канал сепаратора 400 кг /(), при которой достигается максимальная степень очистки. Коэффициент сопротивления сепаратора 0,05. Масса 1000 зерен равна 60 г, коэффициент сопротивления частиц 0,25. Воздух подается в канал при температуре 18 ° С под давлением 0,32 МПа.
|
|
Биохимия спиртового брожения: Основу технологии получения пива составляет спиртовое брожение, - при котором сахар превращается...
Организация стока поверхностных вод: Наибольшее количество влаги на земном шаре испаряется с поверхности морей и океанов (88‰)...
Своеобразие русской архитектуры: Основной материал – дерево – быстрота постройки, но недолговечность и необходимость деления...
История создания датчика движения: Первый прибор для обнаружения движения был изобретен немецким физиком Генрихом Герцем...
© cyberpedia.su 2017-2024 - Не является автором материалов. Исключительное право сохранено за автором текста.
Если вы не хотите, чтобы данный материал был у нас на сайте, перейдите по ссылке: Нарушение авторских прав. Мы поможем в написании вашей работы!