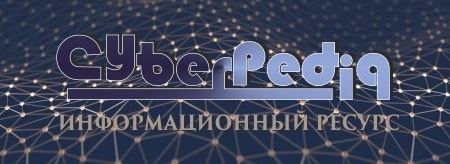
Таксономические единицы (категории) растений: Каждая система классификации состоит из определённых соподчиненных друг другу...
Индивидуальные и групповые автопоилки: для животных. Схемы и конструкции...
Топ:
Характеристика АТП и сварочно-жестяницкого участка: Транспорт в настоящее время является одной из важнейших отраслей народного...
Генеалогическое древо Султанов Османской империи: Османские правители, вначале, будучи еще бейлербеями Анатолии, женились на дочерях византийских императоров...
Интересное:
Искусственное повышение поверхности территории: Варианты искусственного повышения поверхности территории необходимо выбирать на основе анализа следующих характеристик защищаемой территории...
Что нужно делать при лейкемии: Прежде всего, необходимо выяснить, не страдаете ли вы каким-либо душевным недугом...
Национальное богатство страны и его составляющие: для оценки элементов национального богатства используются...
Дисциплины:
![]() |
![]() |
5.00
из
|
Заказать работу |
|
|
Для герметизации подшипниковых узлов различных машин и отдельных корпусов, осевой фиксации подшипников и восприятия осевых нагрузок применяют крышки. Крышки подшипников изготовляют из чугуна марок СЧ15, СЧ18, СЧ 40 и СЧ21. В малогабаритных редукторах при небольшие осевых нагрузках наряду с чугуном можно применять низкоуглеродистые стали, стеклопластики и другие синтетические материалы, а при ограничении массы редуктора — легкие сплавы.
Конструкция крышек зависит
· от способа уплотнения валов
- крышки с манжетным уплотнением табл. 1.1 и 1.2,
- крышки глухие — табл. 1.3;
· способа крепления подшипника на валу
- низкие применяют при закреплении без помощи гаек;
- средние — при креплении подшипника на закрепительной втулке, если крышка расположена со стороны ненарезанной части втулки;
- высокие — при закреплении внутреннего кольца подшипника гайкой;
· способа регулировки осевого зазора в подшипниках
- регулировка с помощью набора металлических прокладок,
- регулировка с помощью резьбовых деталей
· способа крепления крышек
- крепление болтами и винтами,
- врезные крышки.
Таблица 1.1
Крышки с манжетным уплотнением корпусов подшипников качения
(D от 62 до 100 мм)
Размеры высоких крышек, мм
Продолжение табл. 1.1
Размеры средних крышек, мм Размеры низких крышек, мм
Таблица 1.2
Крышки с манжетным уплотнением корпусов подшипников качения
(D от 110 до 150 мм)
Продолжение табл. 1.2
Размеры высоких крышек, мм
Таблица 1.3
Крышки глухие корпусов подшипников качения
(D от 62 до 150 мм)
Продолжение табл.1.3
При небольшом межосевом расстоянии фланцы двух крышек подшипников могут перекрывать друг друга. Тогда у обеих крышек срезают их фланцы на размер до посадочного диаметра D крышки. Зазор между срезами оставляют в пределах 1...2 мм (рис. 1.1, а).
|
Фланцы привертных крышек выполняют не только круглыми, но и других очертаний, например близкими к квадратной форме (рис. 1.1, 6)
Рис. 1.1. Фланцы привертных крышек
или фасонными (рис. 1.1, в). Исполнение фланцев крышек по рис.1, б характерно снижением расхода металла, что особенно целесообразно при крупносерийном и массовом производстве.
Закладные крышки. На рис. 1.2 показаны основные конструкции закладных крышек: глухих — рис. 1.2, а, 6; с отверстием для выходного конца вала — рис. 1.2, в; с резьбовым отверстием под нажимной винт — рис.1.2, г. Закладные крышки широко применяют в редукторах, имеющих плоскость разъема корпуса по осям валов. Эти крышки не требуют крепления к корпусу резьбовыми деталями: их удерживает кольцевой выступ, для которого в корпусе протачивают канавку. Чтобы обеспечить сопряжение торцов выступа крышки и канавки корпуса по плоскости, на наружной цилиндрической поверхности крышки перед торцом выступа желательно выполнять канавку шириной b.
Рис. 1.2.Закладные крышки
Наружный диаметр крышки выполняют с такими отклонениями, при которых в сопряжении с корпусом крышка образует очень малый зазор, препятствующий вытеканию масла из корпуса.
Таблица 1.4. Основные элементы крышек. Размеры в мм
Параметр | D | |||
50-62 | 63...95 | 100... 145 | 150...20О | |
δ | ||||
d | М6 | М8 | М10 | М12 |
z | 6 |
Размеры других, элементов крышки (рис. 1.2, а): δ1 = (0,9... 1)δ; S= (0,9... 1) δ; С= 0,5S; .
Иногда торец крышки, контактирующий с подшипником, не совпадает с торцом выступа (рис. 1.2, 6). Чтобы наружная цилиндрическая поверхность этого участка не нарушала точности центрирования крышки, ее диаметр уменьшают на 0,5... 1 мм.
Конструктивные формы крышек с отверстиями для прохода вала зависят от типа уплотнений, при выборе которых учитывают вид смазывания, рабочую температуру, окружную скорость вала и характер внешней среды.
|
![]() |
![]() |
Наиболее распространены контактные уплотнения, в которых уплотняющие элементы соприкасаются по цилиндрическим или торцевым
поверхностям. Особенно часто применяются манжетные армированные уплотнения из синтетической резины. Они предназначены для работы в минеральных маслах, пластичных смазках и воде при избыточном давлении до 50 МПа. Допускаемая температура от 45°С до 120°С и кратковременно (не более 2 ч) до 130° С.
Рис. 1.3. Резиновая манжета
Манжета (рис. 1.3 и табл. 1.5) состоит из корпуса 2, изготовленного из бензомаслостойкой резины, каркаса 3, представляющего собой стальное кольцо Г-образного сечения, и браслетной пружины. Каркас придает корпусу манжеты жесткость и может находиться внутри корпуса или на поверхности. Браслетная пружина стягивает уплотняющую часть манжеты. Благодаря этому образуется рабочая кромка манжеты шириной b = 0,4...0,8 мм, плотно охватывающая поверхность вала. Нормальная работа манжеты возможна лишь при смазывании поверхностей трения.
Таблица 1.5. Резиновые армированные манжеты (ГОСТ 8752-79).
![]() |
![]() |
![]() |
![]() |
![]() |
![]() |
![]() |
Диаметр вала d | D | h | h1 не более | Диаметр вала d | D | h | h1 не более |
1-го ряда | 1-го ряда | ||||||
20, 21, 22 | 60, 62 | ||||||
48, 50 | |||||||
30, 32 | 55, 56, 58 | ||||||
35, 36 | |||||||
63, 65 | |||||||
70, 71 |
Конструирование стаканов
Стаканы обычно выполняют из чугунного литья марки СЧ 15, реже из стали. Толщину стенки δ, диаметр d и число z винтов крепления стакана к корпусу принимают в зависимости от диаметра D отверстия стакана под подшипник по следующим зависимостям:
D мм... До 52 Св. 52до80 Св. 80до 120 Св. 120 до 170
δ, мм.... 4...5 6...8 8...10 1О...12,5
d, мм..... 6 6 8 10
Z......... 4 4 6 6
Толщину упорного буртика δ1, и толщину фланца δ2 (рис. 1.4) принимают δ1 ≈ δ; δ2 ≈1,2δ
Высоту t упорного буртика назначают по той же зависимости, что и высоту заплечика вала h (табл. 1.6), диаметр буртика D1 = D – 2t.
Диаметр фланца Dф следует выполнять минимальным. Для этого принимают с ≈d: h = (1,0... 1,2)d;Dф = Dа + (4,0... 4,4) d, где d — диаметр винта (рис. 1.4).
|
Таблица 1.6
r, мм | 0,5 | 1,0 | 1,5 | 2,0 | 2,5 | 3,0 | 3,5 | 4,0 |
t, мм | 1,0 | 1,8 | 2,5 | 3,0 | 4,0 | 4,8 | 5,5 | 6,5 |
![]() |
Рис. 1.4. Стаканы подшипников
Иногда на наружной поверхности стакана делают проточку для уменьшения длины посадочного участка (см. рис. 1.4, а). Глубину проточки принимают равной 1,0 мм.
Длину посадочных участков принимают равной ширине кольца подшипника. Канавки в отверстиях стаканов делать не следует, поскольку выполнять их сложнее, чем на наружной поверхности. Кроме того, они затрудняют установку подшипников.
Стаканы для подшипников вала конической шестерни перемешают при сборке для регулирования осевого положения конической шестерни. В этом случае посадка стакана в корпус — H7js6. Другие стаканы после их установки в корпус остаются неподвижными, для них применяют посадки Н7/k6 или Н7/m6.
|
|
Семя – орган полового размножения и расселения растений: наружи у семян имеется плотный покров – кожура...
Архитектура электронного правительства: Единая архитектура – это методологический подход при создании системы управления государства, который строится...
Наброски и зарисовки растений, плодов, цветов: Освоить конструктивное построение структуры дерева через зарисовки отдельных деревьев, группы деревьев...
Опора деревянной одностоечной и способы укрепление угловых опор: Опоры ВЛ - конструкции, предназначенные для поддерживания проводов на необходимой высоте над землей, водой...
© cyberpedia.su 2017-2024 - Не является автором материалов. Исключительное право сохранено за автором текста.
Если вы не хотите, чтобы данный материал был у нас на сайте, перейдите по ссылке: Нарушение авторских прав. Мы поможем в написании вашей работы!