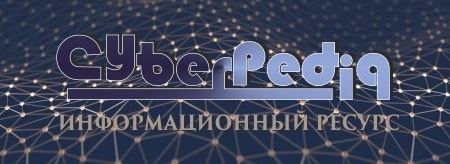
Автоматическое растормаживание колес: Тормозные устройства колес предназначены для уменьшения длины пробега и улучшения маневрирования ВС при...
Опора деревянной одностоечной и способы укрепление угловых опор: Опоры ВЛ - конструкции, предназначенные для поддерживания проводов на необходимой высоте над землей, водой...
Топ:
Эволюция кровеносной системы позвоночных животных: Биологическая эволюция – необратимый процесс исторического развития живой природы...
Процедура выполнения команд. Рабочий цикл процессора: Функционирование процессора в основном состоит из повторяющихся рабочих циклов, каждый из которых соответствует...
Основы обеспечения единства измерений: Обеспечение единства измерений - деятельность метрологических служб, направленная на достижение...
Интересное:
Что нужно делать при лейкемии: Прежде всего, необходимо выяснить, не страдаете ли вы каким-либо душевным недугом...
Уполаживание и террасирование склонов: Если глубина оврага более 5 м необходимо устройство берм. Варианты использования оврагов для градостроительных целей...
Средства для ингаляционного наркоза: Наркоз наступает в результате вдыхания (ингаляции) средств, которое осуществляют или с помощью маски...
Дисциплины:
![]() |
![]() |
5.00
из
|
Заказать работу |
Содержание книги
Поиск на нашем сайте
|
|
Содержание
Терминология
1 Номенклатура деталей, изготавливаемых механической обработкой – резанием
2 Характеристики и технологические свойства материалов
применяемых для изготовления деталей
3 Виды заготовок, используемых для изготовления деталей
4 Типовые технологические процессы механической обработки детали резанием
5 Металлорежущий инструмент, используемый при изготовлении детали
6 Мерительные инструменты, применяемые для контроля деталей в процессе изготовления
7 Материалы, применяемые для изготовления режущего инструмента
8 Основные виды приспособлений для механической обработки
9 Типовые представители металлорежущего оборудования
10 Основные требования безопасности для работ по изготовлению деталей
11 Изучение технологии изготовления заданной детали
Терминология
Производственный процесс – совокупность всех действий людей и орудий труда, необходимых на данном предприятии для изготовления или ремонта продукции.
Объем выпуска продукции – количество изделий определенных наименований, типоразмеров и исполнений, изготовляемых или ремонтируемых предприятием или его подразделением в течение планируемого периода времени.
Программа выпуска продукции – установленный для данного предприятия перечень изготавливаемых или ремонтируемых изделий с указанием объема выпуска по каждому наименованию на планируемый период времени.
Производственный цикл – интервал времени от начала до конца производственного процесса изготовления или ремонта изделия.
Технологический процесс – часть производственного процесса, содержащая целенаправленные действия по изменению и (или) определению состояния предмета труда.
|
Маршрутное описание технологического процесса – сокращенное описание всех технологических операций в маршрутной карте в последовательности их выполнения без указания переходов и технологических режимов.
Операционное описание технологического процесса - это полное описание всех технологических операций в последовательности их выполнения с указанием переходов и технологических режимов с выполнением иногда необходимых эскизов.
Технологическая операция – законченная часть технологического процесса, выполненная на одном рабочем месте.
Материа́л – вещество или смесь веществ, из которых изготавливается что-либо или которые способствуют каким-либо действиям. В последнем случае уточняют, что это вспомогательный или расходный материал.
Основной материал – материал исходной заготовки.
Полуфабрикат – предмет труда, подлежащий дальнейшей обработке на предприятии-потребителе.
Заготовка – предмет труда, из которого изменением формы, размеров, свойств поверхности и (или) материала изготавливают деталь.
Исходная заготовка – это заготовка перед первой технологической операцией
Установ – это часть технологической операции, выполняемая при неизменном закреплении обрабатываемых заготовок или собираемой сборочной единицы.
Установленный технологический переход – законченная часть технологической операции, выполняемая одним и тем же средством технологического оснащения при постоянных технологических режимах и установке.
Вспомогательный переход – законченная часть технологической операции, состоящая из действий человека и (или) оборудования, которые не сопровождаются изменением свойств предмета труда, но необходимы для выполнения технологического перехода.
Рабочий ход – законченная часть технологического перехода, состоящая из однократного перемещения инструмента относительно заготовки, сопровождаемого изменением формы, размеров, качества поверхности и свойств заготовки.
|
Вспомогательный ход – законченная часть технологического перехода, состоящая их однократного перемещения инструмента относительно заготовки, необходимого для подготовки рабочего хода.
Обработка – это действие, направленное на изменение свойств предмета труда при выполнении технологического процесса
Механическая обработка — обработка заготовки из различных материалов при помощи механического воздействия различной природы с целью создания по заданным формам и размерам изделия или заготовки для последующих технологических операций.
Обработка давлением — технологический процесс получения заготовок или деталей в результате силового воздействия инструмента на обрабатываемый материал.
Обработка резанием — это технологический процесс, который осуществляется на металлорежущих станках путём внедрения режущего инструмента в тело заготовки с последующим выделением стружки и образованием новой поверхности.
Технологическое оборудование – средства технологического оснащения, в которых для выполнения определенной части технологического процесса размещают материалы или заготовки, средства воздействия на них, а так же технологическая оснастка.
Технологическая оснастка – средства технологического оснащения, дополняющие технологическое оборудование для выполнения определенной части технологического процесса.
Наладка – подготовка технологического оборудования и технологической оснастки к выполнению технологической операции.
Штучное время – интервал времени, равный отношению цикла технологической операции к числу одновременно изготавливаемых или ремонтируемых изделий или равный календарному времени сборочной операции.
Основное время – часть штучного времени, затрачиваемая на изменение и (или) последующего определения состояния предмета труда.
Вспомогательное время – часть штучного времени, затрачиваемая на выполнение проемов, необходимых для обеспечения изменения и последующего определения состояния предмета труда.
Оперативное время – часть штучного времени, равная сумме основного и вспомогательного времени.
Литые заготовки
Механические свойства материала в литых заготовках, как правило, ниже, чем у материала, подвергнутого деформации. Однако, изготовление фасонных деталей из литых заготовок с последующей механической обработкой отдельных поверхностей значительно экономичнее деталей, получаемых из поковок, штампованных заготовок, клепаных, сварных или паяных узлов (рис. 2.1, 2.2). Поэтому литые заготовки следует применять во всех случаях, когда полученные из них детали удовлетворяют условиям прочности и других эксплуатационных требований. Литые заготовки позволяют получать детали со сложными криволинейными поверхностями, отверстиями, полостями при минимальном количестве обрабатываемых поверхностей. Это особенно важно в том случае, если деталь изготавливается из труднообрабатываемого материала. Литые заготовки обладают повышенной жаростойкостью. Точность их размеров может достигать 11—12 квалитета, а шероховатость поверхности 5—6 класса. В литой детали имеется возможность рационального распределения металла по сечениям, что позволяет сравнительно просто регулировать общую конструктивную прочность и жесткость изделия. В ракетостроении широко используется большое количество литейных сплавов. Однако, для облегчения работы литейных цехов, возможности использования прогрессивного специализированного оборудования, целесообразно применять для конкретной конструкции PC, выпускаемого данным заводом, минимально возможную номенклатуру марок материалов. Краткие технологические сведения о литейных сплавах, наиболее часто встречающихся в ракетостроении, приведены в таблице 2.1. На ракетостроительных заводах нашли применение все основные способы литья: — литье в песчаные формы; — литье в кокиль; — литье в оболочковые формы; — литье по выплавляемым моделям; — литье под давлением. Эти методы широко известны из технологии общего машиностроения и не требуют дополнительного освещения. Для литья некоторых характерных для ракетостроения заготовок на заводах внедряются новые способы: — литье выжиманием; — литье под низким давлением; — вакуумное литье; — литье способом направленно-последовательной кристаллизации; — литье в керамические формы.
|
Кованые заготовки
|
Горячая объёмная штамповка
Горячая объёмная штамповка — это вид обработки металлов давлением, при которой формообразование поковки из нагретой заготовки осуществляют с помощью специального инструмента — штампа. Течение металла ограничивается поверхностями полостей (а также выступов), изготовленных в отдельных частях штампа, так что в конечный момент штамповки они образуют единую замкнутую полость (ручей) по конфигурации поковки. В качестве заготовок для горячей штамповки применяют прокат круглого, квадратного, прямоугольного профилей, а также периодический. При этом прутки разрезают на отдельные (мерные) заготовки, хотя иногда штампуют из прутка с последующим отделением поковки непосредственно на штамповочной машине. Применение объемной штамповки оправдано при серийном и массовом производстве. При использовании этого способа значительно повышается производительность труда, снижаются отходы металла, обеспечиваются высокие точность формы изделия и качество поверхности. Штамповкой можно получать очень сложные по форме изделия, которые невозможно получить приемами свободной ковки. Штамповка в открытых штампах характеризуется переменным зазором между подвижной и неподвижной частями штампа. В этот зазор вытекает часть металла – облой, который закрывает выход из полости штампа и заставляет остальной металл заполнить всю полость. В конечный момент деформирования в облой выжимаются излишки металла, находящиеся в полости, что позволяет не предъявлять высокие требования к точности заготовок по массе. Штамповкой в открытых штампах можно получить поковки всех типов. Штамповка в закрытых штампах характеризуется тем, что полость штампа в процесс деформирования остается закрытой. Зазор между подвижной и неподвижной частями штампа постоянный и небольшой, образование в нем облоя не предусмотрено. Устройство таких штампов зависит от типа машины, на которой штампуют. Например, нижняя половина штампа может иметь полость, а верхняя – выступ (на прессах), или верхняя – полость, а нижняя – выступ (на молотах). Закрытый штамп может иметь две взаимно перпендикулярные плоскости разъема. При штамповке в закрытых штампах необходимо строго соблюдать равенство объемов заготовки и поковки, иначе при недостатке металла не заполняются углы полости штампа, а при избытке размер поковки по высоте будет больше требуемого. Отрезка заготовок должна обеспечивать высокую точность.
Прокатный материал
ТОЧЕНИЕ
Протачивание канавок
d1 – наименьший отверстия после обработки в мм
Растачивание
СВЕРИЛЬНЫЕ РАБОТЫ
|
Принятые обозначения:
Т0 - основное (технологическое) время в мин;ℓ-длина(глубина) обработки в мм;ℓ1–величина врезания инструмента в мм; ℓ2-величина перебега инструмента в мм; t- глубина резания вмм; s- подача в мм на оборот инструмента или детали; n-число оборотов инструмента или детали в минуту.
Центрование Сверление
Рассверливание
ЗЕНКЕРОВАНИЕ
Зенкерование
Зенкование фасок
Зенкование уступов
Зенкование бобышек
РАЗВЕРТЫВАНИЕ
НАРЕЗАНИЕ РЕЗЬБЫ
Принятые обозначения:
Т0 - основное (технологическое) время в мин; ℓ-длина нарезки в мм;ℓ1–врезание резьбонарезного инструмента в мм; ℓ2- перебегрезьбонарезного инструмента в мм; t–шаг резьбы;;s– подача в мм на оборот детали, равная шагу нарезаемой резьбы;n-число оборотов инструмента или деталив минуту; g – число заходов резьбы.
Нарезание резьбы плашкой
Нарезание резьбы метчиком
ШЛИФОВАНИЕ
Принятые обозначения:
Т0— основное (технологическое) время в минутах; L— длина хода стола или шлифовального круга в мм; h —припуск на сторону в мм; В — ширина шлифовального круга в мм; s —продольная подача в долях ширины круга; n — число оборотов детали в минуту;t—поперечная подача круга или глубина шлифования в мм; k —коэффициент, учитывающий доводку и износ круга
ПРОТЯГИВАНИЕ
Резцы
Сверла
Сверление - метод предварительной обработки отверстий на токарных станках.
Сверло — это режущий инструмент, с вращательным движением резания и осевым движением подачи, предназначенный для выполнения отверстий в сплошном слое материала. Свёрла могут также применяться для рассверливания, то есть увеличения уже имеющихся, предварительно просверленных отверстий, и засверливания то есть получения несквозных углублений.
Составные части сверла:
Виды сверл:
а - перовое
б - спиральные: 1 - режущая кромка, 2 - направляющая фаска, 3 - квадрат, 4 - лапка,
5 -хвостовая часть, 6 - шейка, 7 -канавка, 8 - рабочая часть, 9 - передний конус;
в - центровочное
г - с прямыми канавками и с режущей кромкой из твердого сплава,
д - спиральное с режущей кромкой из твердого сплава
е - пушечное для глубоких отверстий.
а - спиральное
б - чашечное с круговым подрезателем,
в - цилиндрическое с конической заточкой
г – ложечное
д – полое цилиндрическое
е – зенкер цилиндрический
ж – зенкер конический.
Сверло спиральное с цилиндрическим хвостовиком
Сверло спиральное с коническим хвостовиком
Сверло центровое
Сверло перовое
Применяются при обработке твердых поковок, а также ступенчатых и фасонных отверстий.
Сверло для кольцевого сверления:
Зенкеры
Зенкер - режущий инструмент для обработки отверстий. Зенкером называется режущий инструмент, предназначенный для обработки предварительно просверленных или отлитых отверстий и их торцевых поверхностей при двух совместных относительных движениях. Поступательном - вдоль оси инструмента. Вращательном – зенкера или детали.
Элементы рабочей части:
Виды зенкеров:
а- цилиндрические зенкеры, служащие для расширения на 1,0—8 мм цилиндрических отверстий,
б - цилиндрические зенкеры с направляющей цапфой, предназначенные для обработки цилиндрических углублений под головки винтов,
в - конические зенкеры для обработки конических углублений под головки винтов, гнезд под клапаны, снятия фасок и т. п.,
г - торцовые зенкеры для зачистки торцовых плоскостей бобышек, приливов и т. п.
Зенкер цилиндрический
Зенкер торцевой
Зенковка
Развертки
Развертки предназначены для изготовления точных отверстий и обеспечивают высокое качество обработанной поверхности
Виды разверток:
а - цилиндрическая: 1 - рабочая часть, 2 - шейка, 3 - хвостовик,
б - спиральные;
в - цилиндрическая насадная,
г, д - конические,
е - элементы рабочей части развертки: 1 - задняя поверхность, 2 - канавка, 3 - режущая кромка, 4- - передняя поверхность, 5 - ленточка, 6- режущее перо, 7 -канавка, 8 - зуб
Развертка цилиндрическая с прямым зубом
Развертка цилиндрическая со спиральным зубом
Развертка машинная
Метчик и плашка
Метчики предназначены для нарезания или калибрования резьбы в отверстиях
Плашкой называется режущий инструмент, предназначенный для нарезания наружной резьбы путем навинчивания инструмента на деталь.
Фрезы
Фрезой называется многорезцовый инструмент, предназначенный для обработки плоскостей и поверхностей.
Части и элементы фрезы:
В зависимости от формы, размеров и расположения обрабатываемых поверхностей применяют фрезы различных типов:
а — цилиндрическая;
б — торцовая насадная;
в — дисковая трехсторонняя;
г — концевая;
д — угловая;
е — шпоночная;
ж — фасонная;
з — пазовая
Прорезная (шлицевая)
Грибковая
Фреза концевая с цилиндрическим кончиком
Фреза концевая с коническим кончиком
Протяжка круглая
В процессе изготовления
Измерительный инструмент - инструмент, предназначенный для измерения линейных объектов.
Штангенинструмент
Штангенинструмент - инструмент для измерений и разметки линейных размеров:
а) отверстий и валов (штангенциркуль);
б) глубины и длины (штангенрейсмас, штангенглубиномер);
в) зубьев зубчатых колес (штангензубомер).
Точность его измерения — десятые доли миллиметра.
Штангенциркуль
Штангенциркуль - универсальный инструмент, предназначенный для высоко-точных измерений наружных и внутренних размеров, а также глубин отверстий.
1)штанга
2)подвижная рамка
3)шкала штанги
4)губки для внутренних измерений
5)губки для наружных измерений
6)линейка глубиномера
7)нониус
8)винт для зажима рамки
Штангенглубиномер
Штангенглубиномер служит для измерений глубин выточек, канавок, уступов и т. д. Отличается от штангенциркуля тем, что не имеет на штанге подвижных губок.
Штангенрейсмус
Измерительный прибор. Предназначен для измерения глубины выемок и впадин.
Угломер
Угломер — угломерный прибор, предназначенный для измерения геометри-ческих углов в различных конструкциях (наружных и внутренних углов изделий.), в деталях и между поверхностями (в основном контактным методом) и между удаленными объектами (оптическим методом). Измерение производится в градусах, на основе линейчатой шкалы, линейчато-круговой шкалы (с механическим указателем или стрелкой), нониуса или в электронном виде, в зависимости от типа прибора.
Конструкция угломеров позволяет производить разметочные работы на плоскости.
Микрометрический инструмент
Микрометр гладкий
Микрометр гладкий — средство для измерения наружных линейных размеров.
Показания по шкалам гладкого микрометра отсчитывают в следующем порядке:
· по шкале стебля читают отметку около штриха, ближайшего к торцу скоса барабана;
· по шкале барабана читают отметку около штриха, ближайшего к продольному штриху стебля;
· складывают оба значения и получают показание микрометра.
Для удобства и ускорения отсчёта показаний имеются гладкий микрометр с цифровой индикацией.
Микрометр резьбовой
Резьбовой микрометр служит для измерения среднего диаметра метрической и дюймовой резьб и имеет такое же устройство, как и обычный микрометр, но отличается от последнего только наличием отверстия в пятке и шпинделе, куда вставляются специальные сменные вставки различной формы: призматические, конические,плоские,шаровые.
а – общий вид,
б – вставки,
в – приемы измерения;
1 – пятка,
2 – шпиндель,
3 и 5 – резьбовые вставки,
4 – измеряемая деталь
К каждому микрометру даются наборы таких вставок, которые укладываются в футляр парами и предназначаются для измерения резьбы с шагом 1 -1,75; 1,75-2,5 и т.д. Угол профиля вставок должен соответствовать углу профиля проверяемой резьбы.
Средний диаметр резьбы детали 4 проверяют призматической вставкой 5, вставляемой в один из витков резьбы; с другой стороны, перпендикулярно оси резьбы в впадину резьбы вставляется конусная вставка 3. Отсчет измерений производится по
шкалам микрометра.
Микрометрический глубиномер
Предназначен для измерения глубины пазов, отверстий и высоты уступов.
Микрометрические глубиномеры имеют такое же устройство, как и микрометры, только вместо скобы имеется основание (90x12 мм) 1 с измерительным стержнем 2. Основание и измерительный стержень закалены. Каждый микрометрический глубиномер снабжен тремя сменными стержнями с пределами измерения 0-25 мм; 25-50 мм; 50-75 мм; 75-100 мм.
1 - основание, 2 – стержень
Микрометрический нутромер
Микрометрический нутромер - это прибор, с помощью которого производят более точные измерения отверстий абсолютным методом, также имеет сменные удлинители.
4)Инструмент с измерительной головкой часового типа:
Стенкомер (толщиномер)
Стенкомер – прибор промышленного назначения, предназначен для контроля и измерения наружных и внутренних размеров, толщины стенок заготовок, канавок. Стенкометр удобен для измерения толщины стенок труб. Диапазон измерения стенкометра от 25 до 50мм. Цена деления 0,1мм до 1 мм, глубина измерения 160мм, наименьший диаметр отверстия 20мм. Пределы допускаемой погрешности ±0,10. Стенкомер индикаторный изготавливается из углеродистой или нержавеющей стали. Стенкомер индикаторный - измерительный прибор, применяемый для измерения линейных размеров контактным методом. Вид измерений – абсолютный.
Стенкомер индикаторный состоит из неподвижной верхней рамки (корпуса) с рукояткой, подвижной нижней рамки, которая прижимается к неподвижной с помощью возвращающей пружины. К верхней рамке прикреплен индикатор часового типа, измерительный стержень которого упирается в горизонтальный выступ нижней рамки. При отжатии нижней рамки, выступ нижней рамки перемещает стержень индикатора. Перемещение измерительного стержня преобразуется зубчатым механизмом измерительной головки часового типа в перемещение стрелки измерительной головки. Отсчет снимается со шкал головки: основной и вспомогательной.
Индикаторный нутромер
Индикаторный нутромер – устройство для внутренних измерений. Индикаторы предназначаются для относительного или сравнительного измерения и проверки отклонений от формы, размеров, а также взаимного расположения поверхностей детали. Этими инструментами проверяют горизонтальность и вертикальность положения плоскостей отдельных деталей (столов, станков и т. п.), а также овальность, конусность валов, цилиндров и др.
1-индикатор часового типа
2-винт
4-движок
5-втулка
6-тройник головки нутромера
7-гайка
8- измерительный стержень
9- рычажок
10-стержнь
11- спиральная пружина
Кроме того, индикаторы применяются для проверки биения зубчатых колес, шкивов, шпинделей и других вращающихся деталей. Еще они бывают часового и рычажного типа.
Наибольшее распространение имеют индикаторы часового типа, которые в сочетании с другими инструментами (нутромерами, глубиной мерами и др.) используются для измерения внутренних и наружных размеров, параллельности, плоскостности и т. д.
Часовой индикатор
Он состоит из корпуса 4, в котором через всю длинную втулку 6 проходит измерительный стержень 7 (шпиндель) с зубчатой рейкой, нарезанной на его поверхности.
5)Предельные калибры
Измерительные пробки
Для проверки диаметров отверстий. Непроходная сторона отличается от проходной меньшей длиной измерительной части или наличием проточки у ручки или вставки
Измерительные скобы
Для проверки диаметров валов и длин.
6)Шаблоны
Шаблон — пластина (лекало, трафарет) с вырезами, по контуру которых изготовляются чертежи или изделия либо инструмент для измерения размеров.
Для измерения наружных и внутренних углов. Проверка отклонения от угла производится наблюдением «на просвет».
Лекальные линейки
Линейка предназначена для проверки прямолинейности методом световой щели «на просвет» и применяется при лекальных, слесарных и контрольных операциях.
Лекальные линейки изготовляются из инструментальной углеродистой или легированной стали с высокой точностью и имеют тонкие рабочие грани, называемые ребрами или лезвиями, с радиусом закругления 0,1-0,2 мм, благодаря чему можно весьма точно определять отклонения от прямолинейности.
Поверочная плита
Поверочная плита — металлическая плита с нормированной плоскостностью и чистотой поверхности: предназначенная для контроля плоскостности деталей и разметочных работ; используемая в качестве установочной поверхности при сборке, измерениях и поверках.
Угольники
Угольники поверочные лекальные плоские предназначены для проверки прямых углов (90°) и применяются при слесарно-сборочных и лекальных работах для контроля взаимной перпендикулярности деталей.
Радиусные шаблоны
Радиусные шаблоны предназначены для оценки радиусов выпуклых и вогнутых поверхностей. Изготавливаются три набора радиусных шаблонов. В каждом наборе скомплектованы пластины для контроля, как наружного, так и внутреннего радиусов. Конструкция обоймы набора обеспечивает возможность свободной замены шаблона, а также регулирования плавности вращения их на оси.
Шаблоны резьбовые
Шаблоны резьбовые используются для определения шага и угла профиля резьбы. Шаблоны резьбовые – это стальные пластины с зубцами, расположенными по осевому профилю резьбы. Шаблоны резьбовые бывают для измерения дюймовой или метрической резьбы.
Для определения шага и угла профиля резьбы шаблон резьбовой совмещают с резьбой проверяемой детали так, чтобы зубцы шаблона поместились во впадины резьбы. Далее по плотности прилегания граней шаблона резьбового к резьбе и определяют соответствие шага и угла профиля резьбы шагу и углу профиля шаблона резьбового.
Виды делительных головок
а) Упрощенные.
б) Универсальные.
в) Оптические (для особо точных работ).
Люнет
Люнет - приспособление для металлорежущих станков, служащее дополнительной опорой вращающимся при обработке деталям. Люнет предотвращает прогиб деталей от усилий резания и собственного веса, повышает их виброустойчивость; применяется при обработке длинных нежёстких валов, деталей, имеющих длинные выступающие части, и тому подобное на токарных, круглошлифовальных, резьбо- и шлицефрезерных станках.
Люнет бывает: неподвижным (обычно прикрепляется к направляющим станины) и
подвижным (перемещается вместе с суппортом, кареткой и тому подобным), являются технологической оснасткой для токарных станков. Применяются в качестве дополнительной опоры при обработке нежестких валов. В зависимости от исполнения люнет оснащается кулачками скольжения или качения.
9. Типовые представители металлорежущего оборудования
Вертикально сверлильные станки
Вертикально сверлильные станки применяются для проведения сверления, расточки и развёртки отверстий в различных материалах.
Шпиндель расположен вертикально, им же производится подача – вручную или включением механической подачи. Такие сверлильные станки просты, имеют минимальное число узлов, поэтому они наиболее надежны и долговечны. Они позволяют вручную вести нарезку резьбы на дереве.
Бывают еще настольные сверлильные, радиально-сверлильные станки.
Токарно-винторезный станок
Применяются для обработки преимущественно тел вращения путём снятия с них стружки при точении. На данном станке можно выполнять различные виды токарной обработки: обтачивание цилиндрических, конических, фасонных поверхностей, подрезку торцов, отрезку, растачивание, а также сверление и развёртывание отверстий, нарезание резьбы и накатку рифлений, притирку и т. п. На специализированных токарных станках обрабатывают колёсные пары, муфты, трубы и др. изделия. На винторезном станке в процессе резания вращение заготовки, закрепляемой в патроне зажимном или в центрах, осуществляется от привода главного движения, обеспечивающего ступенчатое или бесступенчатое регулирование частоты вращения шпинделя для настройки на требуемую скорость резания. Поступательное перемещение режущего инструмента обеспечивается кинематической цепью движения подачи, первое звено которой — шпиндель, последнее — зубчато-реечная передача (при точении) или кинематическая пара ходовой винт — маточная гайка (при нарезании резьбы на токарно-винторезном станке). Настройка подачи производится с помощью коробки подач. Универсальные токарно-винторезные станки применяют в основном в условиях единичного и мелкосерийного производства. При оснащении токарного станка специальными приспособлениями (гидро- или электрокопировальными суппортами, быстрозажимными автоматизированными патронами и т. п.) область их применения распространяется на серийное производство.
Горизонтально фрезерный станок
Применяется для фрезеровки горизонтальных и вертикальных элементов, спиралей, рамок, штампов и пр. При этом станок горизонтально фрезерный может использоваться для обработки изделий из стали, чугуна, металлических сплавов и цветного металла.
Станок имеет ряд технических особенностей:
· Инструмент закрепляется в шпинделе механически;
· Подача замедляется пропорционально;
· Ширина зазора регулируется при помощи специального устройства;
· Привод подачи защищён муфтой;
· При остановке электромагнитной муфты происходит торможение шпинделя.
Станок горизонтально фрезерный нашёл своё применение как в секторе массового производства, так и при изготовлении единичных изделий.
Вертикально фрезерный станок
![]() |
Кругло-шлифовальный станок
Круглошлифовальный станок предназначен для наружного шлифования цилиндрических и пологих конических поверхностей деталей методом врезного и продольного шлифования в условиях единичного, серийного и крупносерийного производства.
Круглошлифовальные станки обладают следующими функции:
а) врезной и прод
|
|
Таксономические единицы (категории) растений: Каждая система классификации состоит из определённых соподчиненных друг другу...
Механическое удерживание земляных масс: Механическое удерживание земляных масс на склоне обеспечивают контрфорсными сооружениями различных конструкций...
Индивидуальные очистные сооружения: К классу индивидуальных очистных сооружений относят сооружения, пропускная способность которых...
Поперечные профили набережных и береговой полосы: На городских территориях берегоукрепление проектируют с учетом технических и экономических требований, но особое значение придают эстетическим...
© cyberpedia.su 2017-2024 - Не является автором материалов. Исключительное право сохранено за автором текста.
Если вы не хотите, чтобы данный материал был у нас на сайте, перейдите по ссылке: Нарушение авторских прав. Мы поможем в написании вашей работы!