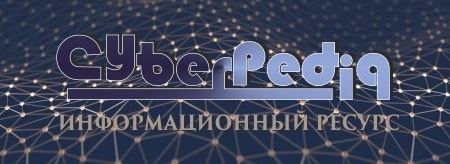
Биохимия спиртового брожения: Основу технологии получения пива составляет спиртовое брожение, - при котором сахар превращается...
Типы оградительных сооружений в морском порту: По расположению оградительных сооружений в плане различают волноломы, обе оконечности...
Топ:
Оснащения врачебно-сестринской бригады.
История развития методов оптимизации: теорема Куна-Таккера, метод Лагранжа, роль выпуклости в оптимизации...
Методика измерений сопротивления растеканию тока анодного заземления: Анодный заземлитель (анод) – проводник, погруженный в электролитическую среду (грунт, раствор электролита) и подключенный к положительному...
Интересное:
Аура как энергетическое поле: многослойную ауру человека можно представить себе подобным...
Отражение на счетах бухгалтерского учета процесса приобретения: Процесс заготовления представляет систему экономических событий, включающих приобретение организацией у поставщиков сырья...
Национальное богатство страны и его составляющие: для оценки элементов национального богатства используются...
Дисциплины:
![]() |
![]() |
5.00
из
|
Заказать работу |
|
|
Прокаткой изготовляют заготовки различной формы. Форму поперечного сечения проката называют профилем, который может быть по длине изделия либо постоянным, либо переменным (периодическим). Совокупность различных профилей и их размеров называют сортаментом. Сортамент проката делится на следующие основные группы: сортовой прокат, листовой прокат, трубы и профили специального назначения (рис. 29).
Рис. 29. Некоторые виды профилей, изготавливаемых прокаткой
Кроме сортового проката, прокаткой получают также заготовки для сортового проката в виде блюма, сляба, сутунки, которые получают из слитков прокаткой на блюмингах, слябингах или установках непрерывной разливки стали.
Блюм – заготовка квадратного сечения со стороной квадрата150– 400 мм, получается прокаткой на блюмингах или непрерывной разливкой стали.
Сляб – заготовка прямоугольного сечения высотой Н = 150 – 300 мм,
получается прокаткой на слябингах или непрерывной разливкой стали.
Сутунка – листовая заготовка толщиной Н = 6 – 50мм.
Заготовки в виде блюмов и слябов, полученные непрерывной разливкой стали, повышают эффективность производства за счет:
-снижения себестоимости из-за необходимости иметь прокатные станы, блюминги и слябинги.
-более благоприятной структуры металла.
Продольная прокатка
Продольная прокатка – наиболее распространенной вид прокатки.При продольной прокатке валки вращаются в разные стороны, а заготовка обжимается с уменьшением площади поперечного сечения и увеличением длины (рис. 30).
Рис. 30. Схема продольной прокатки
Высотное обжатие, или относительная степень деформации по высоте Н, является главной деформацией при прокатке:
|
где Н О, Н – высота заготовки до и после прокатки соответственно;
Н О – Н = Δ Н – абсолютное деформация по высоте;
Деформация по высоте характеризуется неравномерностью, которая вызывается силами трения, неравномерностью нагрева заготовки, структурной неоднородностью металла, а также отклонениями в процессах прокатки: не параллельностью валков (их выпуклостью или вогнутостью).
Во всех случаях неравномерность деформации вызывает появление дополнительных остаточных напряжений заготовки после прокатки.
Очаг деформации
При продольной прокатке деформируется не вся заготовка, а только ее часть, которая называется очагом деформации. При прокатке очаг деформации перемещается по длине заготовки, вызывая изменения в ее размерах и форме.
Очаг деформации подразделяется на геометрический и физический.
Геометрическим очагом деформации называется часть заготовки, находящаяся между цилиндрическими поверхностями валков AB и ED и плоскостями входа AE и выхода BD прокатки.
Физический очаг деформации значительно больше геометрического.
Дуги захвата при прокатке – дуги AB и ED, по которым валки соприкасаются с металлом.
Угол и условия захвата металла при прокатке
Центральный угол α, упирающийся на дугу захвата, называется углом захвата прокатки (см. рис. 27).
Угол захвата α можно определить по величине cos α или sin α:
где ∆ H = H O – H – абсолютное обжатие по высоте;
D – диаметр валка (D=2R);
В момент соударения заготовки с валками происходит снятие ее кромки и возникают силы трения F ТР и реактивная N. Под действием F ТР заготовка втягивается в валки, реактивная сила N выталкивает заготовку (рис.31).
Рис. 31. Схема захвата металла при прокатке
Для того чтобы произошло втягивание заготовки в валки необходимо, чтобы проекция сил трения F ТР на ось Х была больше проекции на эту ось реактивной силы N:
|
F ТР cos α > N sinj;
tg α < tg j;
α < j,
где φ – угол трения; α – угол захвата.
Захват металла валками произойдет в том случае, если угол захвата α будет меньше угла трения φ.
По мере заполнения металлом очага деформации увеличивается сила трения и в конце его заполнения появляется избыток сил трения, который приводит к опережению течения металла.
Обычно углы захвата составляют: для листопрокатных станов α=3-5О; для сортопрокатных станов α=17–20О.
Силы трения, благодаря которым осуществляется прокатка, зависят от скорости и температуры деформации. При увеличении температуры, деформация силы трения возрастает, а при увеличении скорости деформации уменьшаются.
В общем случае на захват металла влияют: угол захвата, коэффициент трения, исходная толщина полосы, диаметр валков, температура прокатываемого металла и др.
С увеличением диаметра валков при одной и той же толщине полосы уменьшается угол захвата, что облегчает захват металла.
Чем выше пластичность, тем лучше захват. Снижение температуры металла ухудшает условие захвата вследствие повышения сопротивления деформации металла.
В практических условиях с целью увеличения производительности прокатку необходимо производить с максимальными обжатиями, т.е. при максимальных углах захвата.
С целью увеличения угла захвата для обжимных прокатных станов часто применяют заталкивающие устройства, которые, оказывая мощное давление на торец заготовки, увеличивают силы трения в начале захвата металла.
Опережение
Представляет собой увеличение скорости течения металла при входе из валков по сравнению с окружной линейной скоростью валков (рис. 32).
Опережение определяется по формуле
где V M – скорость течения металла;
V B – линейная скорость валков.
Рис. 32. Схема опережения при прокатке
Обычно опережение составляет η =3–6%. Опережение увеличивается при увеличении сил трения и диаметра валков.
В очаге деформации различают: зоны опережения 1 и зоны отставания 2.
В зоне опережения 1 V M >V B. В зоне отставания 2 V M <V B. В нейтральной плоскости, разделяющей эти зоны, V M =V B.
Угол опережения γ – угол, упирающийся на дугу зоны опережения.
Опережение следует учитывать при определении линейных скоростей вращения валков, когда они расположены последовательно друг за другом (рис.33).
|
Рис. 33. Схема переднего Т 1 и заднего Т 22 натяжения при прокатке
Уширение
Уширение, или увеличение ширины, заметно проявляется при прокатке крупносортных изделий с поперечным сечением круга, квадрата и т.п. и почти не проявляется при листовой прокатке. Уширение возникает в результате неравномерного трехосного сжатия металла.
Уширение уменьшается при наличии переднего натяжения (Т 1 для валков 1 – 1), а также заднего натяжения (Т 22 для валков 2–2), Т 1 = Т 22. При этом для валка 2 уширение может быть отрицательным при одновременном действии переднего Т 2 и заднего натяжения Т 22.
Поперечно-винтовая прокатка
При поперечно-винтовой прокатке валки расположены под углом и, вращаясь в одну сторону, они придают заготовке одновременно вращательное и поступательное движения, вследствие чего заготовка втягивается в зазор между
валками (рис. 34).
Рис. 34. Схема поперечно–винтовой прокатки
Поперечно-винтовая прокатка применяется для получения периодических профилей, шаров, втулок с наружным диаметром, винтовых деталей, фрез, оребренных труб и др.
Особенно эффективна поперечно-винтовая прокатка при производстве винтовых заготовок (ходовых винтов и т.п.): наряду с высокой производительностью, превышающей нарезание резьбы на токарных станках в 30 – 40 раз, значительно улучшается качество металла в резьбе, создавая волокнистую структуру по контуру резьбы вместо перерезанных волокон при точении. Большая эффективность достигается поперечно-винтовой прокаткой ребристых труб, используемых в теплообменной аппаратуре. По сравнению с горячей штамповкой, поперечно-винтовая прокатка позволяет снизить расход металла на заготовку, повысить производительность труда и обеспечивает более высокую стойкость инструмента.
Производство труб прокаткой
Прокаткой изготавливаются трубы бесшовные и сварные. Для прокатки труб применяют полые или сплошные заготовки. Полые заготовки получают на прошивных станах или методом поперечной прокатки.
В поперечно-винтовых станах оси валков не параллельны, что обеспечивает поступательное движение заготовки, наряду с ее вращением между валками, а оправка формирует внутреннюю полость трубы. После поперечно-винтовой прокатки трубы прокатываются на трубно-раскатных и отделочных станах, на которых они приобретают необходимую толщину и качество.
|
Сварные трубы изготавливают прокаткой с использованием печной, электро- и газосварки. Сварные стальные трубы изготовляют из прокатанных полос, называемых штрипсами, или листов. Процесс изготовления сварных труб состоит из операций: свертывания заготовки в трубу, сварки (электрической, газовой, газоэлектрической), правки, калибровки и отделки.
Перед деформацией заготовка в виде ленты нагревается до температуры 1250 – 1300О С. Перед заходом в матрицу она обдувается сжатым воздухом и по линии стыка происходит сварка ленты за счет пластинчатой деформации (диффузионная сварка). Вместо матрицы применяются ролики (валки).
Сварные трубы изготовляют формовкой из полосы (штрипса) и соединением кромок различными способами сварки.
Электрическая сварка кромок после формовки трубы позволяет получать трубы с тонкой стенкой и высоким качеством шва. Наиболее широко распространена сварка сопротивлением. Труба формуется в непрерывном стане из 5 – 12 клетей (рис. 35).
Рис. 35. Схема непрерывной формовки трубы на трубосварочном стане
Кромки полосы разогреваются электрическим током, прижимаются друг к другу приводными роликами и свариваются.
В последние годы при производстве труб применяют индукционную сварку. При индукционной сварке кромки нагревают вихревыми токами.
При производстве труб большого диаметра для газа и нефтепродуктов применяют электрическую сварку под слоем флюса. Трубы большого диаметра с прямым швом формуют на прессе или вальцегибочном стане.
Сварные трубы значительно дешевле бесшовных, их производство расширяется с каждым годом. Пониженная прочность и коррозионная стойкость сварного шва являются недостатком таких труб.
|
|
Двойное оплодотворение у цветковых растений: Оплодотворение - это процесс слияния мужской и женской половых клеток с образованием зиготы...
История развития хранилищ для нефти: Первые склады нефти появились в XVII веке. Они представляли собой землянные ямы-амбара глубиной 4…5 м...
Автоматическое растормаживание колес: Тормозные устройства колес предназначены для уменьшения длины пробега и улучшения маневрирования ВС при...
Типы оградительных сооружений в морском порту: По расположению оградительных сооружений в плане различают волноломы, обе оконечности...
© cyberpedia.su 2017-2024 - Не является автором материалов. Исключительное право сохранено за автором текста.
Если вы не хотите, чтобы данный материал был у нас на сайте, перейдите по ссылке: Нарушение авторских прав. Мы поможем в написании вашей работы!