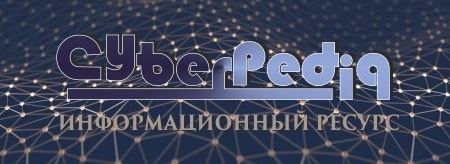
История создания датчика движения: Первый прибор для обнаружения движения был изобретен немецким физиком Генрихом Герцем...
Опора деревянной одностоечной и способы укрепление угловых опор: Опоры ВЛ - конструкции, предназначенные для поддерживания проводов на необходимой высоте над землей, водой...
Топ:
Теоретическая значимость работы: Описание теоретической значимости (ценности) результатов исследования должно присутствовать во введении...
Основы обеспечения единства измерений: Обеспечение единства измерений - деятельность метрологических служб, направленная на достижение...
Устройство и оснащение процедурного кабинета: Решающая роль в обеспечении правильного лечения пациентов отводится процедурной медсестре...
Интересное:
Аура как энергетическое поле: многослойную ауру человека можно представить себе подобным...
Национальное богатство страны и его составляющие: для оценки элементов национального богатства используются...
Что нужно делать при лейкемии: Прежде всего, необходимо выяснить, не страдаете ли вы каким-либо душевным недугом...
Дисциплины:
![]() |
![]() |
5.00
из
|
Заказать работу |
|
|
Роторная АЛ – комплекс рабочих машин, транспортных устройств, приборов, объединенных единой системой автоматического управления, в котором одновременно с обработкой заготовки перемещаются по дугам окружностей совместно с воздействующими на них орудиями.
Особенности:
- обработка деталей совершается в процессе совместного транспортного движения предмета обработки и инструмента;
- инструменты установлены на транспортном средстве (цепной конвейер, барабан-ротор), обеспечивающем непрерывное их движение по замкнутой траектории;
к каждому инструменту на определенном участке его пути поступает предмет обработки
- основные элементы роторной линии: рабочие и приемно-питающие роторы;
- коэффициент использования оборудования (загрузки) – 90-95%;
- одновременно можно изготавливать несколько различных типов изделий (происходит замена вспомогательного устройства);
- снижает трудовые и временные затраты;
- компактность РАЛ.
Промышленный робот – перепрограммируемая автоматическая машина, применяемая в производственном процессе для выполнения двигательных функций, аналогичных функциям человека, при перемещении предметов труда или технологической оснастки
Особенности:
- широкая универсальность (многофункциональность);
- гибкость (мобильность) при переходе на выполнение принципиально новых операций.
Роботы 1-ого поколения – работают по заранее заданной «жесткой» программе (сварочный робот).
Роботы 2-ого поколения – оснащены системой адаптивного управления, представленными различными сенсорными устройствами (техническое зрение, очувствленные схваты) и программами обработки сенсорной информации.
Роботы 3-ого поколения – обладают искусственным интеллектом, позволяющим выполнять самые сложные функции при замене в производстве человека.
|
Организация ремонтного хозяйства предприятия
Ремонтное хозяйство – комплексное понятие, характеризующее совокупность общепроизводственных и цеховых подразделений предприятия, осуществляющих мероприятия по техническому обслуживанию и ремонту оборудования.
Задачи ремонтного хозяйства:предупреждение преждевременного износа оборудования и поддержание его в постоянной технической готовности, сокращение простоев при выполнении технического обслуживания и ремонта;
повышение качества ремонтных работ и уменьшение затрат на их выполнение, внедрение прогрессивных форм, средств и методов ремонта.
Функции ремонтного хозяйства:
- планирование, контроль и учет выполняемых ремонтных работ;
- снижение трудоемкости и стоимости ремонтных работ, увеличение межремонтного периода оборудования предприятия;
- контроль правильности эксплуатации технологического оборудования и разработка инструкций по уходу за ним;
- ведение учета оборудования, его паспортизация и аттестация;
- планирование и контроль изготовления запасных частей;
- модернизация оборудования, повышение эффективности труда ремонтников.
Ремонтное хозяйство возглавляет главный механик завода, подчиненный непосредственно техническому директору (главному инженеру) завода.
В ремонтное хозяйство входят:
отдел главного механика,
ремонтно-механический цех,
цеховые ремонтные базы (службы),
заточные, смазочные, ремонтные мастерские,
общезаводской склад запчастей и деталей.
Система и методы технического обслуживания и ремонта оборудования
Системапланово-предупредительного ремонта оборудования - совокупность организационно-технических мероприятий по уходу, надзору, обслуживанию и ремонту оборудования, проводимых профилактически по заранее составленному плану (графику) с целью предотвращения прогрессирующего износа, предупреждения аварий и поддержания оборудования в постоянной эксплуатационной готовности.
|
Сущность системы ППР – проведение через определенное число часов работы оборудования профилактических осмотров и различных видов плановых ремонтов
Виды работ, предусмотренных системой ППР:
1. Межремонтное обслуживание:
наблюдение за состоянием оборудования;
выполнение рабочими правил эксплуатации оборудования;
своевременная регулировка механизмов;
устранение мелких неисправностей.
Выполнение основными рабочими и дежурным ремонтным персоналом межремонтного обслуживания проводится в нерабочие часы.
2. Периодические ремонтные и профилактические работы:
промывку оборудования
(промывке подвергаются все виды оборудования, работающие в условиях загрязненности);
смену и пополнение масел
(проводится по специальному графику для всего оборудования);
проверку точности
(проводится после плановых ремонтов и профилактических операций по особому плану-графику для прецизионного и финишного оборудования);
профилактические испытания
(проводятся для проверки электрооборудования и электросетей на основе «Правил технической эксплуатации и безопасности обслуживания электроустановок промышленных предприятий».Профилактические испытания проводятся в нерабочее время).
3. Осмотры:
Производятся с целью проверки состояния оборудования, устранения мелких неисправностей, выявления объема подготовительных работ, подлежащих выполнению при очередном плановом ремонте.
При осмотре проводятся следующие работы:
наружный осмотр без разборки;
вскрытие крышек для осмотра и проверки состояния механизмов;
регулирование зазоров и подшипников;
проверка систем подведения энергии, охлаждающей жидкости и др.
При осмотре перед капитальным ремонтом выполняются все работы, как и при обычном осмотре, и, кроме того, выявляются детали, которые необходимо заменить при капитальном ремонте.
4. Плановые ремонты:
Малый ремонт (текущий) направлен на восстановление работоспособности оборудования посредством выполнения минимальных по объему работ, включающих регулировочные, наладочные операции, с заменой быстроизнашивающихся деталей;
Средний ремонт предназначен для восстановления исправности оборудования с проведением отдельных сборочно-разборочных работ;
|
Капитальный ремонт является наибольшим по объему проводимых работ, преследует цель восстановления исправности оборудования с выполнением ремонтных работ любого его узла и механизма.
5. Внеплановые ремонты включают виды ремонтов, связанных с устранением последствий аварий или не предусмотренных годовым планом.
Важнейшими нормативами системы ППР являются:
ремонтные циклы и их структуры;
длительность межремонтных и межосмотровых периодов;
категория сложности ремонта;
нормативы трудоемкости;
нормативы материалоемкости и др.
Ремонтный цикл
Ремонтным циклом называется период работы агрегата между двумя капитальными ремонтами (для оборудования, находящегося в эксплуатации).
Для вновь установленного оборудования
ремонтный цикл – это период работы агрегата от начала ввода его в эксплуатацию до первого капитального ремонта.
Продолжительность ремонтного цикла учитывается по количеству отработанных оборудованием часов.
Структура ремонтного цикла – перечень и последовательность выполнения ремонтных работ и работ по техническому уходу в период между капитальными ремонтами или между вводом в эксплуатацию и первым капитальным ремонтом.
Структура ремонтного цикла зависит от веса оборудования, срока службы деталей.
Для легких и средних станков:
К −ТО −Т1 −ТО −Т2 −ТО −С1 −ТО −Т3 −ТО −Т4 −ТО − К1,
где К – капитальный ремонт; Т – текущий ремонт; ТО – техническое обслуживание, С – средний ремонт
При определении продолжительности цикла учитывается ряд факторов: тип производства, физико-механические свойства обрабатываемых материалов, эксплуатационные условия, размер оборудования.
Ремонтный цикл (Tр.ц) для легких и средних металлорежущих станков (массой до 10 т) определяют по формуле:
Т р.ц = А⋅βп ⋅βм ⋅βу ⋅βт,
где А – длительность ремонтного цикла при работе агрегата в условиях массового производства;
βn – коэффициент, учитывающий тип производства;
βм – коэффициент, учитывающий код обрабатываемого материала;
|
βу – коэффициент, учитывающий условия эксплуатации оборудования;
βт – коэффициент, учитывающий особенности весовой категории станков.
Межремонтный период
Межремонтным периодом называется период работы оборудования между двумя очередными ремонтами (t).
Продолжительность межремонтного периода определяется по формуле:
где пс – количество средних ремонтов, пм – количество малых ремонтов.
Межосмотровой период
Межосмотровым периодом называется период работы оборудования между двумя очередными осмотрами или между очередным плановым ремонтом и осмотром (to).
Продолжительность межосмотрового периода определяется по выражению:
где по – количество осмотров.
Трудоемкость ремонтных операций
Зависит от вида ремонта и его сложности, которая определяется конструктивными особенностями и размерами оборудования.
Для определения степени сложности ремонта вводится категория сложности ремонта, которая и оценивает степень сложности оборудования.
Обозначается категория сложности ремонта буквой R, а ее значение, присвоенное данному агрегату или машине, определяется коэффициентом, который ставится перед R, например, 10R.
Категория сложности ремонта R является качественной характеристикой конструктивных и технологических особенностей оборудования. Она определяется для каждого вида оборудования в зависимости от параметров, характеризующих сложность ремонта.
Для оценки ремонтных особенностей оборудования определенный вид его принимается в качестве эталона.
Ремонт может осуществляться следующими путями:
1. Централизованно на специализированных ремонтных заводах или в цехах, специализирующихся на ремонте определенных типомоделей оборудования.
2. Централизованно силами ремонтно-механических цехов предприятий.
3. Силами специализированных комплексных бригад службы цехового механика.
4. Силами выездных бригад, организованных при специализированных заводах или цехах для ремонта тяжелого, особо тяжелого, уникального и прецизионного оборудования.
Существует три формы организации ремонтных работ на предприятии:
1. Централизованная. Ремонт всех видов оборудования и его модернизация производится силами ремонтно-механического цеха.
Применяется на небольших предприятиях единичного мелкосерийного производства с общим количеством оборудования 2500-3000 единиц при наличии нескольких цехов, каждый из которых имеет оборудование не более 500 ремонтных единиц.
2. Децентрализованная. Все ремонты, включая межремонтное обслуживание, производятся силами цеховой ремонтной базы (ЦРБ) и специализированных ремонтных бригад под руководством механика цеха.
Применяется на заводах крупносерийного и массового производства с количеством оборудования свыше 5000 ремонтных единиц, цехи которых имеют оборудование свыше 800 ремонтных единиц.
|
3.Смешанная. Все ремонтные работы, кроме капитального, а иногда и среднего ремонтов, проводятся силами цеховых ремонтных баз. Капитальный и средний ремонт, а также модернизация оборудования производятся в РМЦ.
Применяется на заводах с количеством оборудования от 3000 до 5000 ремонтных единиц, цехи которых имеют оборудование от 500 до 800 ремонтных единиц.
Основными направлениями совершенствования ремонтного хозяйства являются:
организация централизованного ремонта оборудования;
создание ремонтных баз на предприятиях-изготовителях оборудования, что повышает их заинтересованность в повышении качества своего оборудования;
централизация ремонта и обслуживания оборудования непосредственно на промышленных предприятиях;
механизация ручных ремонтных работ;
применение современных средств технической диагностики состояния оборудования;
внедрение прогрессивных методов, технологических процессов и организационных форм выполнения ремонтных работ;
совершенствование технической подготовки ремонта;
совершенствование планирования ремонтных работ;
внедрение нормативной сдельно-премиальной системы оплаты труда;
внедрение автоматизированной системы управления ремонтным производством.
Организация энергетического хозяйства предприятия
Задачи энергетического хозяйства:
- бесперебойное обеспечение всеми видами энергии объектов производства и бытового обслуживания предприятия;
- выполнение работ по обслуживанию и ремонту энергетического оборудования;
- планирование, учет расхода, контроль качества различных видов энергии на предприятии;
- обеспечение экономичных способов обеспечения предприятия энергией;
- организация безопасной эксплуатации энергетического оборудования и установок.
- бесперебойное обеспечение всеми видами энергии объектов производства и бытового обслуживания предприятия;
- выполнение работ по обслуживанию и ремонту энергетического оборудования;
- планирование, учет расхода, контроль качества различных видов энергии на предприятии;
- обеспечение экономичных способов обеспечения предприятия энергией;
- организация безопасной эксплуатации энергетического оборудования и установок.
Направления совершенствования энергетического хозяйства:
приобретение ресурсосберегающего оборудования;
использование наиболее экономичных видов энергоресурсов;
совершенствование схем энергопотребления;
совершенствование технологических процессов;
автоматизация технологических процессов;
учет и контроль использования ресурсов;
совершенствование конструкции энергооборудования;
применение расчетно-аналитических методов нормирования ресурсов;
упрощение структуры энергетического хозяйства предприятия;
стимулирование улучшения использования ресурсов.
Организация транспортного хозяйства предприятия
Транспортное хозяйство обеспечивает на предприятии внутрипроизводственную, и внешнюю транспортировку (если не применяется аутсорсинг)
Задачи транспортного хозяйства:
своевременное обеспечение транспортом основного производства, вспомогательных цехов, отделов и служб обеспечения материально-техническим имуществом предприятия и соответствующих складов;
определение потребностей предприятия в транспортных средствах;
снижение себестоимости транспортных работ на предприятии посредством выбора наиболее экономичной системы доставки, повышения коэффициентов использования грузоподъемности, увеличения технологической скорости, механизации работ.
Функции транспортного хозяйства:
- разработка нормативов, применяемых в транспортной службе;
- планирование потребностей во всех видах транспорта на основе расчетов грузопотоков и грузооборота;
- планирование ППР (планово-предупредительных ремонтов) транспортных средств;
- планирование потребности в запчастях и их приобретение;
- обеспечение производственных процессов транспортными средствами;
- организация безопасности движения;
- организация приобретения новых транспортных средств.
В состав транспортного хозяйства входят:
транспортный отдел и транспортный цех.
Транспортный цех является материальной базой транспортного хозяйства.
Цех, как правило, укомплектован различными транспортными средствами для осуществления межцеховых и внешних перевозок груза.
В состав транспортного отдела входят:
1. планово-экономическое бюро – разрабатывает план транспортно хозяйственной деятельности, определяет грузопотоки по заводу и объемы погрузочно-разгрузочных работ, рассчитывает потребность в транспортных средствах и погрузочно-разгрузочных работах составляет смету затрат транспортному хозяйству;
2. диспетчерское бюро – осуществляет оперативно-производственное планирование работы транспорта, которое сводится к составлению квартальных, месячных и суточных планов перевозок и оперативному регулированию транспортных работ;
3. техническое бюро – осуществляет техническую подготовку производства с целью комплексной механизации и автоматизации погрузочно-разгрузочных и транспортных операций, разрабатывает транспортно-технологические схемы, формирует альбомы чертежей по каждому виду транспортного средства;
4. бюро учета – ведет паспортизацию всех видов транспортных средств, осуществляет бухгалтерский учет и отчетность по транспортному хозяйству.
Потребность в транспорте складывается из решения следующих задач:
определение грузооборота производственных подразделений и всего предприятия;
определение грузопотоков предприятия;
выбор транспортных средств и расчет их производительности;
расчет потребности количества транспортных средств;
формирование маршрутов движения транспорта предприятия.
Направления совершенствования транспортного хозяйства:
• механизация и автоматизация транспортных операций в сочетании с высокой их организацией;
• применение унифицированной тары;
• внедрение единой производственно-транспортной технологии;
• специализация средств межцехового транспорта по роду перевозимых грузов;
• организация контейнерных перевозок;
внедрение автоматизированных систем управления транспортом.
Классификация транспортных средств, используемых на предприятиях
1. Внутрипроизводственные транспортировки: транспортные процедуры на складах и процесс транспортировки внутри производственных подразделений;
2. Внешняя транспортировка: транспортировка от поставщика к потребителю или между различными заводами или складами одного предприятия
Внутренние транспортные средства:
Стационарные:
транспортные устройства, с помощью которых продукты перемещаются по определенному горизонтальному, вертикальному или наклонному направлениям
потребляют малое количество энергии, отличаются небольшими затратами на обслуживание и обладают большей надежностью и безопасностью
Перемещающиеся:
транспортные средства, которые выполняют либо вертикальную транспортировку (подъемники, в том числе лифты, мостовые, портальные и другие краны), либо горизонтальное перемещение – как система на тележках (автокары, мотокары)
Стационарные транспортные средства:
С опорой на пол:
- скрытый под полом цепной транспортер;
- рольганги (холостые – работают на основе силы тяжести; с электроприводом)
- ременный транспортер.
Без опоры на пол:
- цепной подвесной транспортер;
- транспортер с электроприводом.
Дистанционные транспортные средства:
o Позволяют рационализировать логистические функции;
o Могут использоваться как на частично механизированных, так и на полностью автоматических линиях;
o Экономичность;
o Большая гибкость
· Высокая стоимостью;
· Проблемы загрузки и выгрузки;
· Низкая скоростью движения;
· Привязка к смонтированным путям;
· Затруднительность проезда в различных производственных ситуациях.
Внешние транспортные средства:
Задачами внешнего транспорта являются:
• - поставка материалов и продукции в установленные сроки;
• - снабжение промежуточных складов;
• - экономичная и сохранная доставка грузов.
Виды внешнего транспорта:
- автомобильный;
- железнодорожный;
- морской;
- внутренний водный (речной);
- воздушный;
- трубопроводный.
Организация складского хозяйства предприятия.
Задачи складского хозяйства:
- организация надлежащего хранения материальных ценностей;
- бесперебойное обслуживание производственного процесса;
- отгрузка готовой продукции.
Функции складского хозяйства:
- планирование работ;
- приемка и обработка грузов;
- организация надлежащего хранения;
-постоянный контроль и учет движения материальных ценностей;
- своевременное обеспечение производственного процесса материалами, комплектующими изделиями и другим;
- строгое соблюдение противопожарных мер безопасности;
- комплектование готовой продукции, ее консервация, упаковка, подготовка отгрузочной документации и отгрузка.
Классификация складов (в зависимости от функций):
- склады покупных комплектующих;
- склады материалов (сырья вспомогательного и производственного назначения);
- склады полуфабрикатов;
- промежуточные производственные склады;
- склады готовой продукции.
- оборотные склады – задачи оборотного склада включают перегрузку комплектных единиц хранения с одного транспортного средства на другое;
- склады хранения – задачи его состоят в обеспечении наличия материалов для соответствующего функционирования производства;
- склады комиссионирования, выполняющие посредническую деятельность – их задача состоит в реализации комиссионерских заказов в соответствии с заказами клиентов (подсчет, сортировка, проведение заказа);
- склады, осуществляющие временное сохранение, выдачу и возвратную приемку объектов;
- специальные склады – склады образцов, склады отходов.
Складское оборудвание:
- вспомогательные устройства для погрузки;
- транспортные средства;
- стеллажи и полки.
Организация инструментального хозяйства предприятия
Инструментальное хозяйство предприятия представляет собой совокупность отделов и цехов, занятых проектированием, приобретением, изготовлением, ремонтом и восстановлением технологической оснастки, а также ее учетом, хранением и выдачей в цехи и на рабочие места
Задачи инструментального хозяйства:
1. Создание запасов инструмента, при этом:
определяются текущая потребность и запас инструмента и оснастки;
организуется производство технологической оснастки и получение со стороны оснастки и инструмента;
организуется входной контроль инструмента.
2. Хранение инструмента и технологической оснастки.
3. Организация учета инструмента и оснастки.
4. Организация выдачи инструмента и оснастки.
5. Снижение затрат на единицу продукции.
6. Организация ремонта инструмента.
7. Организация заточки инструмента и надзора за его эксплуатацией.
Инструментальное хозяйство в зависимости от величины и особенностей предприятия может подчиняться главному технологу или главному инженеру предприятия и существовать в виде инструментального отдела, бюро инструментального хозяйства или инструментальной группы, инструментального цеха и центрального инструментального склада.
Централизованное управление инструментальным хозяйством предприятия осуществляет инструментальный отдел, подчиненный главному технологу или непосредственно главному инженеру.
Состав инструментального хозяйства зависит от размера предприятия, типа производства, особенностей производственной структуры, технологических процессов и оборудования.
Инструментальный отдел обычно включает в себя следующие группы:
конструкторскотехнологическую (разрабатывает конструкцию и технологию изготовления инструмента);
плановоэкономическую (определяет потребность в инструментах в целом по предприятию и по отдельным цехам, планирует закупки инструмента на стороне, контролирует выполнение этих планов);
нормативов (классифицирует и индексирует инструмент, устанавливает нормы расхода и оборотный фонд по различным видам инструмента, отдельным цехам и заводу в целом; контролирует соблюдение норм расхода и запасов инструмента);
технадзора (контролирует правильность хранения и использования инструмента, норм его стойкости, износа и запаса; разрабатывает мероприятия по сокращению расхода и запасов инструмента, проверяет правильность его заточки, ремонта и восстановления, контролирует измерительный инструмент).
Понятие качества продукции предприятия и показатели оценки затрат на обеспечение качества
Проблема качества продукции во всем мире рассматривается как наиболее важная, поскольку она определяет престиж конкретных производителей и страны в целом на мировом рынке, а также научно-технический потенциал и степень развития экономики.
Качество продукции – это совокупность свойств, определяющих её пригодность удовлетворять потребности в соответствии с её назначением.
Эти свойства продукции интерпретировались в определенные параметры, которые фиксировались в нормативной документации на продукцию. Однако в условиях рынка предприятию важно не только произвести продукцию в соответствии с установленными заранее требованиями, но и реализовать ее. В этом случае главным критерием качества продукции становятся не сами технико-экономические параметры продукции, отражающие ее качество, а предпочтении реального потребителя, основанные на ценности для него этой продукции. Сложность данной проблемы состоит в том, что у каждого отдельно взятого потребителя свой взгляд на то, какой должна быть удовлетворяющая его продукция. Более того, очень часто предпочтения потребителя меняются со временем: то, что кажется сегодня привлекательным, завтра таковым может не быть. Поэтому в мировой практике, и это закреплено в международных стандартах, качество интерпретируется как совокупность характеристик объекта, относящихся к его способности удовлетворять установленные и ожидаемые потребности. В этом случае устанавливается прямая зависимость между качеством продукции и объемом продаж, что в свою очередь увеличивает положительный результат деятельности предприятия и скорее всего приводит к росту эффективности его производства.
Экономические категории качества проявляются двояко: через прибыль производителя от продажи качественно изготовленного продукта и через его затраты на обеспечение ожидаемого покупателем качества.
При оценке и анализе затрат на обеспечение качества необходимо учитывать две составляющие: затраты на соответствие и издержки на несоответствие.
Основными составляющими затрат являются:
* затраты на превентивные меры, отражающие часть стоимость продукта для потребителя, которые включают затраты производителя на снижение риска потребителя получить продукт или услугу, не соответствующие его ожиданиям;
* затраты на инспекцию, включающие издержки производителя на обнаружение несоответствия и дефектов в процессе проектирования и производства или оказания услуг с целью их исключения;
* издержки на внутренний брак, которые включают затраты производителя на устранение в процессе производства или оказания услуг выявленных им ошибок и дефектов. Эти затраты являются издержками изготовителя, которые он не может вернуть в дальнейшем за счет потребителя;
* издержки на внешний брак, включают дополнительные затраты производителя на исправление дефектов переданного потребителю продукта или оказанных услуг. Внешний брак связан с дефектами, обнаруженными покупателями и торговой сетью. Поэтому кроме издержек на устранение этого брака, производитель несет неизмеримо большие моральные издержки, отражающиеся на его имидже и репутации на рынке.
Система управления качеством продукции. Принципы построения системы качества в соответствии с международными стандартами по управлению качеством.
Управление качеством продукции – деятельность, осуществляемая при создании и эксплуатации или потреблении продукции с целью установления, обеспечения и поддержания необходимого уровня ее качества.
Как всякое управление, управление качеством продукции осуществляется поэтапно:
* разработка плана повышения качества, включая разработку новых требований к качеству продукции и мероприятия, обеспечивающие создание новой продукции с желаемыми свойствами;
* оценка соответствия свойств изготовляемой продукции требованиям, которые были предусмотрены в плане;
* принятие необходимых мер воздействия на процесс создания ценности продукции в тех случаях, когда не удалось обеспечить соответствие;
* изучение условий эксплуатации с целью определения направлений дальнейшего повышения качества продукции.
Система управления качеством продукции представляет собой совокупность управленческих органов и объектов управления, мероприятий, методов и средств, направленных на установление, обеспечение и поддержание высокого уровня качества продукции. Система управления качеством продукции включает следующие функции:
§ Функции стратегического, тактического и оперативного управления.
§ Функции принятия решений, управляющих воздействий, анализа и учета, информационно-контрольные.
§ Функции специализированные и общие для всех стадий жизненного цикла продукции.
§ Функции управления по научно-техническим, производственным, экономическим и социальным факторам и условиям.
В соответствии с международными стандартами ИСО серии 9000 (см. ниже) выделяются политика в области качества и непосредственно система качества, включающая обеспечение, улучшение и управление качеством продукции.
Политика в области качества может быть сформулирована в виде направления деятельности или долгосрочной цели и может предусматривать:
§ улучшение экономического положения предприятия;
§ расширение или завоевание новых рынков сбыта;
§ достижение технического уровня продукции, превышающего уровень ведущих фирм;
§ ориентацию на удовлетворение требований потребителей определенных отраслей или регионов;
§ освоение изделий, функциональные возможности которых реализуются на новых принципах;
§ улучшение важнейших показателей качества продукции;
§ снижение уровня дефектности изготавливаемой продукции;
§ увеличение сроков гарантии на продукцию;
§ развитие сервиса.
В соответствии со стандартами ИСО жизненный цикл продукции обозначается как петля качества. С помощью петли качества осуществляется взаимосвязь изготовителя продукции с потребителем, со всей системой, обеспечивающей решение задачи управления качеством продукции.
Таким образом, обеспечение качества продукции - это совокупность планируемых и систематически проводимых мероприятий, создающих необходимые условия для выполнения каждого этапа "петли качества", чтобы продукция удовлетворяла требованиям к качеству.
В мировой практике сегодня выделяют четыре уровня деятельности, направленной на достижение гарантированного качества продукции:
1. Управление качеством как деятельность оперативного характера для выполнения установленных требований по качеству.
2. Обеспечение качества как деятельность, направленная на достижение уверенности в том, что требования по качеству будут выполнены как внутри предприятия, так и вне его – у потребителя, в том числе в процессе всех видов деятельности, соответствующих модели «петля качества».
3. Общее руководство качеством включает деятельность по управлению качеством и обеспечению качества, а также предусматривает разработку и реализацию политики предприятия в области качества.
4. Всеобщее управление качеством подразумевает долговременную стратегию общего руководства и управления предприятием, направленную на обеспечение качества и эффективности деятельности предприятия в целом с участием в этом процессе всех заинтересованных лиц – сотрудников предприятия и его партнеров, потребителей и общества в целом.
ISO 9000 — серия стандартов ISO, которые применяются при создании и совершенствовании систем менеджмента качества организаций.
Серия стандартов по системному менеджменту качества разработана Техническим комитетом ТК 176 Международной Организации по Стандартизации (ISO, InternationalOrganizationforStandardization). Комитет руководствовался предварительными разработками Британского института стандартов, нашедшими своё отражение в Британском стандарте BS 5750.
Стандарты серии ISO 9000, принятые более чем 90 странами мира в качестве национальных, применимы к любым предприятиям, независимо от их размера, форм собственности и сферы деятельности.
Сертификация производится по единственному стандарту из этой серии, содержащему требования: ISO 9001. Организация ISO не проводит сертификацию по ISO 9001. Действует двухуровневая система подтверждения соответствия. Сертификацией систем менеджмента качества отдельных организаций занимаются специально сформированные аудиторские организации (органы по сертификации). Они, в свою очередь, аккредитуются национальными аккредитационными обществами. Впрочем, существуют и независимые системы аккредитации.
Важно понимать, что соответствие стандарту ISO 9001 не гарантирует высокое качество продукции. Соответствие требованиям и рекомендациям этих стандартов говорит о способности предприятия поддерживать стабильность качества и улучшать результативность своей работы. Также соответствие требованиям ISO 9001 свидетельствует о некотором уровне надежности поставщика. С точки зрения многих западных и японских компаний, соответствие требованиям ISO 9001 — это тот минимальный уровень, который даёт возможность вхождения в рынок. Сам сертификат соответствия ISO 9001 является внешним независимым подтверждением достижения требований стандарта.
Цель серии стандартов ISO 9000 — стабильное функционирование документированной системы менеджмента качества предприятия-поставщика. Исходная направленность стандартов серии ISO 9000 была именно на отношения между компаниями в форме потребитель/поставщик. С принятием в 2000 году очередной версии стандартов ISO серии 9000 большее внимание стало уделяться способностям организации удовлетворять требования всех заинтересованных сторон: собственников, сотрудников, общества, потребителей, поставщиков. ISO 9004 делает акцент на достижение устойчивого успеха. Указанные стандарты помогают предприятиям формализовать их систему менеджмента, вводя, в частности, такие системообразующие понятия, как внутренний аудит, процессный подход, корректирующие и предупреждающие действия.
Стандарт ISO 9000 является фундаментальным, принятые в нем термины и определения используются во всех стандартах серии 9000. Этот стандарт закладывает основу для понимания базовых элементов системы менеджмента качества согласно стандартов ISO. ISO 9000 определяют Восемь Принципов менеджмента качества, а также использование процессного подхода с целью постоянного улучшения
Стандарты, входящие в серию
ISO 9001. Содержит набор требований к системам менеджмента качества. Текущая версия — «ISO 9001:2008. Системы менеджмента качества. Требования».
ISO 9000. Словарь терминов о системе менеджмента, свод принципов менеджмента качества. Текущая версия — «ISO 9000:2008. Системы менеджмента качества. Основные положения и словарь».
ISO 9004. Cодержит руководство по достижению устойчивого успеха любой организацией в сложной, требовательной и постоянно изменяющейся среде, путем использования подхода с позиции менеджмента качества. Текущая версия - «ISO 9004:2009. Мен
|
|
История создания датчика движения: Первый прибор для обнаружения движения был изобретен немецким физиком Генрихом Герцем...
Индивидуальные и групповые автопоилки: для животных. Схемы и конструкции...
Индивидуальные очистные сооружения: К классу индивидуальных очистных сооружений относят сооружения, пропускная способность которых...
Эмиссия газов от очистных сооружений канализации: В последние годы внимание мирового сообщества сосредоточено на экологических проблемах...
© cyberpedia.su 2017-2024 - Не является автором материалов. Исключительное право сохранено за автором текста.
Если вы не хотите, чтобы данный материал был у нас на сайте, перейдите по ссылке: Нарушение авторских прав. Мы поможем в написании вашей работы!