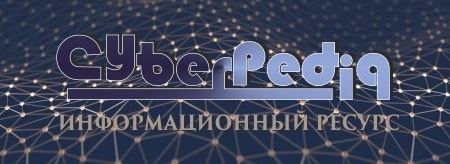
Двойное оплодотворение у цветковых растений: Оплодотворение - это процесс слияния мужской и женской половых клеток с образованием зиготы...
Биохимия спиртового брожения: Основу технологии получения пива составляет спиртовое брожение, - при котором сахар превращается...
Топ:
Характеристика АТП и сварочно-жестяницкого участка: Транспорт в настоящее время является одной из важнейших отраслей народного...
Определение места расположения распределительного центра: Фирма реализует продукцию на рынках сбыта и имеет постоянных поставщиков в разных регионах. Увеличение объема продаж...
Особенности труда и отдыха в условиях низких температур: К работам при низких температурах на открытом воздухе и в не отапливаемых помещениях допускаются лица не моложе 18 лет, прошедшие...
Интересное:
Мероприятия для защиты от морозного пучения грунтов: Инженерная защита от морозного (криогенного) пучения грунтов необходима для легких малоэтажных зданий и других сооружений...
Влияние предпринимательской среды на эффективное функционирование предприятия: Предпринимательская среда – это совокупность внешних и внутренних факторов, оказывающих влияние на функционирование фирмы...
Искусственное повышение поверхности территории: Варианты искусственного повышения поверхности территории необходимо выбирать на основе анализа следующих характеристик защищаемой территории...
Дисциплины:
![]() |
![]() |
5.00
из
|
Заказать работу |
|
|
Кирпич и камни изготовляют из чистых глин либо из глин с добавкой непластичных материалов (при высоком значении числа пластичности). В ряде случаев в состав шихты вводят выгорающие добавки в качестве порообразователя.
Основным сырьем для производства керамических эффективных стеновых материалов служат глины и глинистые суглинки, представляющие собой горную породу осадочного происхождения. При затворении водой они образуют массу, пластичность которой в известной мере зависит от состава и количества содержащихся в них примесей, главным образом от содержания Al2O3.
Глинистое сырье легкоплавкое, кислое, с высоким содержанием красящих окислов о водорастворимых солей, полиминеральное, низкодисперсное, среднепластичное, низкотемпературного спекания с высоким содержанием свободного кремнезема.
По результатам технологических и полузаводских испытаний глинистое сырье пригодно для выпуска облицовочной плитки, отвечающий требованиям ГОСТа 6141 «Плитки керамические глазурованные для внутренней облицовки стен»,
Выгорающими добавками обычно служат древесные опилки, торф, молотый уголь, а также другие органические вещества и отходы производств. Преимущественное применение опилок объясняется распространенностью лесопильных и деревообрабатывающих предприятий, отходом которых они являются. Опилки твердых лиственных пород лучше опилок хвойных пород, так как последние вследствие содержания большого количества летучих веществ в древесине при обжиге изделий образует в них микротрещины, понижающие прочность изделий. Для обеспечения прочности и обеспечения хороших теплоизоляционных свойств изделий наиболее желательна мелкая и равномерная пористость. Поэтому опилки просеивают и в качестве выгорающей добавки используют фракции с размерами частиц не более 7-8 мм. Для данной технологии производства также используется отходы сельскохозяйственной промышленности - солома. Это объясняется тем, что район строительства завода расположен в благоприятной зоне для выращивания и реализации большинства видов злаковых. Соответственно отходы данной отрасли сельского хозяйства могут быть использованы в качестве выгорающей добавки при производстве эффективных керамических изделий.
|
Опока. Опоки - легкие плотные тонкопористые кремнистые опал-кристобалитовые породы. Средняя плотность их составляет 1200-1500 кг/м3, пористость достигает 50% (обычно 30-40%).
Опоки - это не чистые силициты, а многокомпонентные системы. Постоянной составляющей их наряду с аморфным кремнеземом являются минералы слюд и гидрослюд, содержащиеся в нормальных разностях до 10-15%. В качестве примеси могут присутствовать песчано-алевритовый и карбонатный материал, частички которого обычно не превышают 0,01 мм. В связи с этим выделяются различные литологические разности кремнистых пород - песчанистые, карбонатные и смешанные. Разнообразие состава обуславливает широкий диапазон физико-технических и технологических свойств.
Характеристика топлива
Топливо - углеродистые и углеводородистые горючие вещества, специально сжигаемые в промышленных установках для получения тепла. Различают три вида топлива: твердое, жидкое и газообразное, которые находят применение в промышленности керамических материалов и изделий. Топливо состоит из горючих веществ - углерода, водорода, летучей серы и негорючих, влаги и называемых балластом - золы, представляющих собой минеральный остаток после сгорания топлива.
Для обжига сырца выбирают наиболее оптимальный и локальный (из экономических соображений) вид топлива. Из твердых видов топлива в основном применяют торф, бурый и каменный уголь, антрацит и иногда кокс; из жидких видов топлива - нефть, мазут; из газообразных - генераторный и природный газы.
|
Для более полного и быстрого сгорания топлива рекомендуется в зону обжига подавать достаточное количество воздуха.
В керамическую массу можно вводить как длиннопламенное, так и короткопламенное топливо. Расход топлива при обжиге сырца по нормам составляет 150-180 кг условного топлива на 1000 шт. кирпича.
Поскольку площадка для строительства находится на районе, где ведется активная добыча и переработка нефтяных и газовых месторождений, в данном курсовом проекте в качестве топлива используется мазут - остаточный продукт переработки нефти, при сжигании которого отсутствует выброс золы, достигаются высокая надежность тепловой установки и возможность полной ее автоматизации. Жидкие виды топлива - нефть, мазут и другие нефтяные отходы успешно применяются для обжига сырца в туннельных печах и поэтому в качестве топлива при проектировании будем использовать мазут со следующим химическим составом.
Материальный баланс
Материальный баланс завода по производству эффективных стеновых керамических изделий мощностью 15 млн. шт. методом пластического формования.
Исходные данные:
1. Состав массы (%):
Глинистый суглинок месторождения - 63,05;
Глина - 24,25;
Опока - 9,7;
Солома и опилки - 3;
2. Влажность сырья (%):
Глинистый суглинок месторождения - 8
Глина - 9
Опока - 3
Солома и опилки - 8
Средневзвешенная влажность сырья составит:
W= 8 * 0,6305 + 9 * 0,2425 + 3 * 0,097 + 8 * 0,03 = 7,76%
3. Потери при прокаливании сырья (%):
Глинистый суглинок месторождения - 7,74;
Глина - 5,25;
Опока - 5;
Средневзвешенные потери при прокаливании:
П.П.П.=7,74 * 0,6305 + 5,25 * 0,2425 + 5 * 0,097 = 6,64%
4. Технологические параметры производства:
Формовочная влажность шихты - 20%
Влажность изделий после сушки - 4,5%
5. Брак и потери производства:
Брак при обжиге - 2%
Брак при сушке - 3%
При дозировании и транспортировке - 1%
Для сопоставимости статей прихода и расхода материального баланса выхода продукции и полуфабриката рассчитываем в тоннах в год.
Мощность завода 15 млн. шт. кирпича или 37500 т/год соответственно.
Расчет материального баланса.
1. Должно выходить кирпича из печей готовой продукции по обожженной массе с учетом брака при обжиге:
Q1 = П*100/100 - К1 = 37500 * 100/ 98 = 38265 т/год
|
К1- брак при обжиге.
Брак при обжиге:
Q1 - П = 38265 - 37500 = 765 т
2. Поступает кирпича в печи с учетом потерь при прокаливании по абсолютно сухой массе:
Q2 = Q1 * 100/100 - Wс..в
Q2 = 38265 * 100/100 - 7, 76 = 41484 т/год
Потери при прокаливании:
Q2 - Q1 = 41484 - 38265 = 3219 т
3. Поступает кирпича в печи по фактической массе с учетом остаточной влажности:
Q3 = Q2 * 100/100 * Wo = 41484 * 100/100 - 6= 44132 т/год
Испаряется влаги в печах:
Q3 - Q2 = 44132 - 41484 = 2648 т
4. Должно выходить кирпича из сушил по абсолютно сухой массе с учетомбрака при сушке:
Q4 = Q2 * 100/100 - K3 = 44132 * 100/100 - 3 = 45497 т/год
Кз- брак при сушке - 3%.
Брак при сушке:
Q4 - Q2 = 45497 - 44132 = 1365 т
5. Должно выходить кирпича из сушил по фактической массе с учетом остаточной влажности:
Q5 = Q4* 100/100 - Wo = 45497 * 100/100 - 6 = 48400 т/год
6. Поступает в сушила по фактической массе:
Q6 = Q4 * 100/100 - Wф = 45497 * 100/100 - 20 = 56870 т/год
Wф- формовочная влажность 20%.
Испаряется влаги в сушилах:
Q6 - Q5 = 56870 - 45497 = 11373 т
7. Потребность в технологической воде для приготовления шихты:
Q7= Q6 - (Q4 * 100/100 - Wcp) = 56870 - (45497 * 100/100-7,76) = 7546 т/год
Потребность в технологической воде с учетом 10% потерь составит:
Q7 = 7546 + (7546 * 0.1) = 6790 м т/год
8. Требуется сырья для стабильной работы дозаторов по абсолютно сухой массе при транспортировке 1%.
Q8= Q4 * 100/100 - К4= 45497 * 100/100 - 1= 45956 т/год
К4- потери при транспортировки 1 %
Потери при транспортировке:
Q8- Q4= 45956 - 45497 = 460 т
9. Требуется сырья по фактической массе:
суглинок:
Qф = Q8 * Ac /100 - Wф= 45956 * 63,05/(100-8) = 31495 т/год
Qrл = Q8* Aгл /100 - Wr= 45956 * 24,25/(100-9) = 12246 т/год
Опока: Qоп = Q8* Aоп /100 - Wоп= 45956 * 9,7/(100-3) = 4595 т/год
Солома и опилки:
Qсо = Q8* Aсо /100 - Wсо= 45956 * 3/(100-8) = 1498 т/год
Ас, Агл, Аоп, Асо- содержание соответственно суглинка, глины, опоки, а также соломы и опилок.
Невязка баланса составляет 45907 - 45800 = 107 т/год т.е. 0,23%. Допустимая невязка составляет 0,5%.
Технология производства
|
|
Автоматическое растормаживание колес: Тормозные устройства колес предназначены для уменьшения длины пробега и улучшения маневрирования ВС при...
Своеобразие русской архитектуры: Основной материал – дерево – быстрота постройки, но недолговечность и необходимость деления...
Организация стока поверхностных вод: Наибольшее количество влаги на земном шаре испаряется с поверхности морей и океанов (88‰)...
Эмиссия газов от очистных сооружений канализации: В последние годы внимание мирового сообщества сосредоточено на экологических проблемах...
© cyberpedia.su 2017-2024 - Не является автором материалов. Исключительное право сохранено за автором текста.
Если вы не хотите, чтобы данный материал был у нас на сайте, перейдите по ссылке: Нарушение авторских прав. Мы поможем в написании вашей работы!