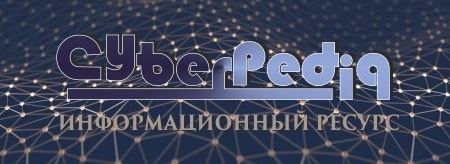
Типы сооружений для обработки осадков: Септиками называются сооружения, в которых одновременно происходят осветление сточной жидкости...
Эмиссия газов от очистных сооружений канализации: В последние годы внимание мирового сообщества сосредоточено на экологических проблемах...
Топ:
Процедура выполнения команд. Рабочий цикл процессора: Функционирование процессора в основном состоит из повторяющихся рабочих циклов, каждый из которых соответствует...
Техника безопасности при работе на пароконвектомате: К обслуживанию пароконвектомата допускаются лица, прошедшие технический минимум по эксплуатации оборудования...
Интересное:
Подходы к решению темы фильма: Существует три основных типа исторического фильма, имеющих между собой много общего...
Искусственное повышение поверхности территории: Варианты искусственного повышения поверхности территории необходимо выбирать на основе анализа следующих характеристик защищаемой территории...
Распространение рака на другие отдаленные от желудка органы: Характерных симптомов рака желудка не существует. Выраженные симптомы появляются, когда опухоль...
Дисциплины:
![]() |
![]() |
5.00
из
|
Заказать работу |
|
|
ОБЩЕРОССИЙСКИЕ НОВОСТИ БЕРЕЖЛИВОГО ПРОИЗВОДСТВА
ЭКСКУРСИЯ НА КАМСКИЙ КАБЕЛЬ: КАК ВНЕДРЯЮТ БЕРЕЖЛИВОЕ ПРОИЗВОДСТВО
Коллектив отдела развития производственной системы совместно с цехом 3 принимал гостей. На «Камском кабеле» побывали представители пермских предприятий.
3 апреля в актовом зале цеха 3 собрались представители ЗАО «Новомет-Пермь», ОАО «Стар», ОАО «Сорбент», ПГУ, ОАО «Авиадвигатель», ООО «ВНИИБТ-Буровой инструмент», НПО «Искра», ОАО «Редуктор-ПМ».
Гостей приветствовала директор по качеству и производственной системе С.И. Прокашева, отметившая, что сотрудничество на уровне города, обмен опытом, знакомство с результатами работы помогут коллегам из разных компаний в решении общих задач, уберегут их от повторения чужих ошибок.
Начальник ОРПС Гилина Наталия Ниязовна познакомила коллег с презентацией, наглядно демонстрирующей ход внедрения бережливого производства в корпусе по производству силовых кабелей. Именно с самого крупного цеха, обладающего к тому же большим парком старого оборудования, на заводе было начато внедрение бережливого производства. В успех верили не все, а сейчас сюда с гордостью водят высоких гостей. Фотографии «как было» и «как стало» наглядно демонстрируют динамику процесса.
Опытным экспертам многое было понятно без лишних слов, но они с интересом слушали детальный рассказ об этапах реализации проекта.
Все согласились, что начинать надо с обучения персонала, чтобы разговаривать на одном языке. Силами сотрудников ОРПС были разработаны обучающие программы для разных категорий работников: технологов, контролеров ОТК, ремонтного персонала, мастерского состава, выпущено учебное пособие. Этапы визуализации, разработка стандартов рабочего места, зонирование – за каждым словом скрывается очень большая работа сертифицированных экспертов ОРПС, членов рабочих групп.
|
Интересовал гостей вопрос о том, какие еще подразделения задействованы в процессе внедрения системы 5S.
- Производственная система – большой комплекс взаимодействия всех служб, - подчеркнула С.И. Прокашева.
Представители «Камского кабеля» отметили, что прежде всего важна поддержка генерального директора, она помогает решать многие вопросы. Обходы с участием директоров проходят ежеквартально. Помогает в тиражировании опыта корпоративная газета. Тесно строилось взаимодействие цеха 3 и ОРПС со смежными цехами, службами снабжения, логистики, планирования производства и др. Проделана глобальная работа.
Сейчас принципы бережливого производства тиражируются на другие цеха, и везде большое значение приобретают лидерские качества руководителей, навыки работы в команде – то, чем отличается цех 3.
На примере производства силовых кабелей удалось доказать, что внедрение системы 5S позволяет сокращать межпроцессное ожидание, попутно решать многие сложные проблемы, ускорять процессы, снижать себестоимость продукции, сокращать время изготовления КПП в днях. Сейчас это помогает экспертам находить взаимопонимание с руководителями других производственных подразделений. В настоящее время, когда перед коллективом поставлена задача оптимизации всех затрат, данная работа приобретает еще большую актуальность.
Стремление к идеалу
Дмитрий Бондаренко напомнил топ-менеджерам, что амбициозные задачи, стоящие перед РУСАЛом, прописаны в Приказе № 1: абсолютно безопасное производство,100-процентное качество выпускаемой продукции, абсолютная удовлетворенность клиентов, отсутствие аварийных простоев оборудования и т.п.
– Понятно, что это идеальные цели и достичь их сложно, а подчас почти невозможно, – сказал Дмитрий Бондаренко. – Но это те ориентиры, к которым мы должны стремиться, используя известную всем формулу: безопасность, качество, люди, себестоимость, взаимодействие. Что-то в достижении поставленных перед нами целей получилось, что-то – нет. Есть направления, над которыми надо более активно работать, которые требуют улучшений. Поэтому на 2015 год в Приказе № 1 остались те же самые идеальные цели. Но самое важное – это динамика: как мы будем их достигать, что будет меняться при достижении этих целей.
|
Одно из таких направлений – удовлетворенность потребителей. По итогам 2014 года этот показатель составил 82%. И хотя относительно 2013-го он вырос на 2%, говорить, что клиенты полностью удовлетворены продукцией РУСАЛа, пока не приходится. Свидетельствует об этом и количество рекламаций. Общий их объем сокращается, тем не менее претензии от покупателей продолжают поступать, и довольно часто они касаются одних и тех же видов продукции. В частности, катанки, производимой на ИркАЗе. Чаще всего клиенты выставляют рекламации относительно несоответствия заявленных характеристик данной продукции по сопротивлению, химическому составу, жалуются на разрывы. Кстати, проведение совещания именно в Шелехове стало хорошим поводом непосредственно на месте разобраться с причинами возникновения данных проблем.
Еще одно направление, по которому большинству предприятий Компании предстоит активизировать деятельность, – производительность труда. Так, по итогам прошлого года только предприятия Глиноземного дивизиона и порошковой металлургии продемонстрировали повышение производительности. А вот на заводах Алюминиевого дивизиона зафиксировано снижение.
Также большой проблемой с точки зрения производственной системы остается эксплуатационный контроль за оборудованием. Сейчас коэффициент технической готовности оборудования на заводах РУСАЛа достаточно высок, в среднем 93%. Тем не менее существующая система контроля несовершенна, о чем свидетельствует уровень аварийных простоев. Характерным примером здесь является АГК: при коэффициенте технической готовности практически 100% на комбинате периодически происходят аварийные простои оборудования. Поэтому для более объективного контроля предприятия Компании будут переходить от применения коэффициента технической готовности к расчетам эксплуатационной готовности оборудования.
|
– Я сейчас критикую не ремонтные службы, а, в первую очередь, наш линейный персонал, – отметил Дмитрий Бондаренко. – Он должен почувствовать себя хозяином оборудования, поэтому переход на расчет эксплуатационной готовности – это достаточно важная задача. Необходимо учитывать любые проблемы, любые простои, любые замечания, которые есть по нашим службам. Например, возьмем электролизное производство. В прошлом году было 106 аварийных отключений электролизеров. Значит, этому вопросу было уделено недостаточное внимание. А последствиями стали потери, которые формально за прошлый год составили 450 тонн металла, а фактически мы потеряли еще больше.
А вот проектная деятельность, которая сегодня ведется на всех без исключения заводах РУСАЛа, наоборот, помогает избежать потерь и демонстрирует отличные результаты.
– Если говорить об экономическом эффекте, который подтверждается финансовой дирекцией, то только за прошлый год по предприятиям Компании он составил 72 млн долларов, – сообщил Дмитрий Бондаренко топ-менеджерам. – Это ваша заслуга, но, в первую очередь, это, конечно, результат работы персонала. Вы прекрасно понимаете, что чем больше в проектную деятельность вовлекается людей, тем активней они занимаются решением проблем на своих рабочих местах. Естественно, от их активности зависит и снижение себестоимости продукции, и сокращение затрат. А значит, благодаря им Компания чувствует себя увереннее.
Реальная мотивация
Работать еще эффективней в рамках производственной системы работникам РУСАЛа помогает специализированное обучение. В 2014 году его прошли 274 человека. А в этом году подготовку и развитие персонала планируется проводить еще более активно и углубленно. На это направлена «Программа 250», утвержденная приказом по РУСАЛу.
250 – это предполагаемое число участников программы. На самом деле уже известно, что их будет больше – 358. Это представители практически всех подразделений заводов Компании. По мнению их руководителей, осуществлявших отбор, эти люди имеют хороший потенциал для развития, профессионального и карьерного роста. «Программа 250» предоставит им возможность полностью самореализоваться.
|
– Мы уже тоже порядка семи лет внедряем производственную систему для того, чтобы правильно обучать людей, развивать наших поставщиков, – отметил в заключение Дмитрий Бондаренко. – У нас сформированы эталонные участки практически по всем направлениям. Из них можно отметить ключевой участок на «Саянской фольге», где хорошо показаны инструменты работы по оборудованию, САЯНАЛ и Aughinish – самый лучший завод по обслуживанию оборудования в Компании. Фактически на всех предприятиях реализовываются проекты по снижению запасов внутри потока. Тем не менее бизнес-система РУСАЛа продолжает развиваться, она, как и производственная система, базируется на принципах TPS, мы от этого не отходим и придерживаемся всех основных постулатов.
ОБЩЕРОССИЙСКИЕ НОВОСТИ БЕРЕЖЛИВОГО ПРОИЗВОДСТВА
|
|
Биохимия спиртового брожения: Основу технологии получения пива составляет спиртовое брожение, - при котором сахар превращается...
Типы оградительных сооружений в морском порту: По расположению оградительных сооружений в плане различают волноломы, обе оконечности...
Автоматическое растормаживание колес: Тормозные устройства колес предназначены для уменьшения длины пробега и улучшения маневрирования ВС при...
Таксономические единицы (категории) растений: Каждая система классификации состоит из определённых соподчиненных друг другу...
© cyberpedia.su 2017-2024 - Не является автором материалов. Исключительное право сохранено за автором текста.
Если вы не хотите, чтобы данный материал был у нас на сайте, перейдите по ссылке: Нарушение авторских прав. Мы поможем в написании вашей работы!