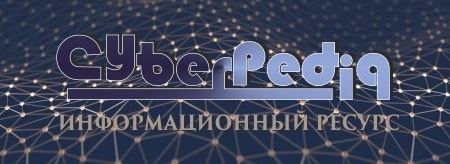
Биохимия спиртового брожения: Основу технологии получения пива составляет спиртовое брожение, - при котором сахар превращается...
Общие условия выбора системы дренажа: Система дренажа выбирается в зависимости от характера защищаемого...
Топ:
История развития методов оптимизации: теорема Куна-Таккера, метод Лагранжа, роль выпуклости в оптимизации...
Характеристика АТП и сварочно-жестяницкого участка: Транспорт в настоящее время является одной из важнейших отраслей народного хозяйства...
Организация стока поверхностных вод: Наибольшее количество влаги на земном шаре испаряется с поверхности морей и океанов...
Интересное:
Влияние предпринимательской среды на эффективное функционирование предприятия: Предпринимательская среда – это совокупность внешних и внутренних факторов, оказывающих влияние на функционирование фирмы...
Уполаживание и террасирование склонов: Если глубина оврага более 5 м необходимо устройство берм. Варианты использования оврагов для градостроительных целей...
Подходы к решению темы фильма: Существует три основных типа исторического фильма, имеющих между собой много общего...
Дисциплины:
![]() |
![]() |
5.00
из
|
Заказать работу |
|
|
Ф – Ц – А – П – Л
(фазан, цапля, аист - птицы летающие)
Ф – феррит (твердый раствор углерода в Feα)
Ц – цементит (химическое соединение карбид железа Fe3C)
А – аустенит (твердый раствор углерода в Feγ)
П – перлит (механическая смесь феррита и цементита)
Л – ледебурит (тонкая механическая смесь аустенита и цементита)
Компонент – вещества, образующие систему (могут быть чистые металлы, неметаллы, устойчивые химические соединения)
Система – группа сплавов, выд. для изучения
Фаза – однородная часть системы, отделенная от других частей поверхностью раздела, при переходе через которую химический состав меняется.
Пример оформления практической работы.
Провести анализ сплава с углеродосодержанием 3,6% с описанием процесса при медленном охлаждении.
При процентном содержании углерода 3,6% сплав – чугун доэвтектический.
Первичная кристаллизация доэвтектического чугуна происходит при t0 12500C – образуется аустенит.
Вторичная кристаллизация - при t0 11470C – образуется цементит вторичный и ледебурит, расп. Аустенит.
Окончательная структура образуется при t0 7270C - образуется перлит, ледебурит, цементит вторичный.
Примесь | Влияние | |
+ | - | |
Углерод | Возрастает твердость | Уменьшается сопротивление разрыву |
Кремний | Повышает предел текучести | Уменьшение пластичности |
Марганец | Повышает прочность | Уменьшает красноломкость стали |
Сера | Снижает развитие трещины | Ухудшает свариваемость |
Фосфор | Увеличивает временное сопротивление разрыву | Уменьшает пластичность и вязкость |
Классификация сталей. Углеродистые конструкционные стали. ГОСТ.
Сталь – сплав железа с углеродом, содержание углерода 0.02-2.14%
|
По назначению: - конструкционные
- инструментальные
По составу: - углеродистые(Fe,C)
- легированные (Fe,C,лег.элемент)
Углеродистые конструкционные стали.
Качество: - конструкционные качественные
- конструкционные обыкновенные
Инструментальные стали.
Качество: - инструментальные качественные
- инструментальные высококачественные
Углеродистые конструкционные стали
Обыкновенного качества.
ГОСТ 380-94
Маркировка: Ст0 …Ст6 (цифра-номер по ГОСТу)
Стали доэвтектоидные
Группы:
- гр.А Ст0 …Ст6 с гарантированными механическими свойствами
- гр.Б БСт0 …БСт6 с гарантированными химическими свойствами
- гр.В ВСт0 …ВСт6 с гарантированными механическими свойствами и хим. составом
Степень раскисления:
- кп – кипящие (Ст3кп)
- пс – полуспокойные (БСт5пс)
- сп –спокойные (ВСт6сп)
Ст3 – углеродистая конструкционная сталь обыкновенного качества, по ГОСТу номер 3, группы А, с гарантированными механическими свойствами
ВСт6сп – углеродистая конструкционная сталь обыкновенного качества, по ГОСТу номер 6, группы В, с гарантированными механическими свойствами и химическим составом, по степени раскисления спокойная.
Применение:
Ст0 | - Прокат сортовой и листовой, детали, изготавливаемые холодной штамповкой. Неответственные детали |
Ст1 | - Штампованные детали, не испытывающие больших нагрузок (болты, оси, валики) |
Ст3-5 | - Штыри, упоры, плиты, болты. Шпильки, рычаги, тяги. Ответственные болты, валы, оси, зубчатые колеса, штифты. |
Ст6 | - Шпонки, штифты конические, червяки, зубчатые колеса, валы, муфты, тормозные ленты. |
Углеродистые конструкционные качественные стали.
ГОСТ 1050-88
Маркировка: Сталь 05,08,10,15,20,25,…..85 пп
Стали доэвтектоидные.
Сталь 45- углеродистая конструкционная качественная сталь, содержание углерода 0,45%.
Применение:
Сталь 10 | - Детали, изготавливаемые холодной штамповкой, свариваемые детали, детали подлежащие цементации. Шайбы, прокладки, втулки. |
Сталь 20 | - Валы, оси, муфты, зубчатые колеса, болты. |
Сталь 30 | - Кованые и штампованные детали, зубчатые колеса. |
Сталь 65(65Г) | - Сталь с повышенным содержанием марганца. Шайбы, пружины, тормозные диски, кольца, рессоры. |
Сталь 88пп | - Повышенная прокаливаемость. |
|
Углеродистые интсрументальные стали.
ГОСТ 1435-90
Маркировка: У7-13 – качественные, У7А-13А – высококачественные
А-высококачественная сталь
Пониженное содержание серы и фосфора
У7- углеродистая инструментальная качественная сталь, содержание углерода 0,7%.
Применение:
У7,У7А | - Слесарный инструмент |
У8,У8А | - Мерительный инструмент |
У9,У9А | - Штампы, матрицы, зубила |
У10,У10А | - Хирургический инструмент |
У12,У12А | - Ножовочные полотна, ножи, пилы |
У13,У13А | - Сельскохозяйственные работы |
Углерод в чугуне может находиться в связанном состоянии (в виде цементита) или в свободном (в виде графита)
Классификация чугуна. ГОСТ.
- сплав железа с углеродом, содержание углерода 2,14-6,67%
- имеет хорошие литейные свойства, повышенные демпфирующие свойства (способность гасить колебания), меньшей, чем у стали чувствительностью к концентраторам напряжений, повышенные антифрикционные свойства за счет графитовых включений, хорошо работает на сжатие, кручение, изгиб.
Классификация:
1. по состоянию углерода
- белый
- отбеленный (половинчатый)
- серый
Белый чугун | - чугун, в котором углерод находится в связанном состоянии, по цвету излома белый |
Отбеленный чугун | - чугун, в котором углерод находится наполовину в связанном состоянии, наполовину в свободном |
Серый чугун | - чугун, в котором углерод находится в свободном состоянии |
2. по характеру металлической основы
- ферритные
- феррито-перлитные серый
- перлитные
3. по форме графитовых включений
- с глобулярной (червеобразной) формой графита
- с хлопьевидной (перьеобразной) формой графита
- с глобулярной (шаровидной) формой графита
Серый чугун
Серый (СЧ) ГОСТ-1412-85 СЧ20 | Ковкий (КЧ) ГОСТ-7293-85 КЧ30-4 | Высокопрочный (ВЧ) ВЧ80-2 |
СЧ20 - серый чугун, предел прочности на растяжение 200Н/м2
КЧ30-4 – ковкий чугун, предел прочности на растяжение 3000Н/м2, относительное удлинение 4%
|
Ковкий чугун получают из доэвтектического белого чугуна в результате длительного отжига. По свойствам похож на серый, но более пластичный, не куют.
ВЧ80-2 – высокопрочный чугун, на изгиб прочность 8000Н/м2, относительное удлинение 2%
Получают добавлением Mg к чугуну.
Белый и отбеленный маркировки не имеют.
Термическая обработка стали
- технологические процессы, при которых путем теплового воздействия целенаправленно изменяют структуру и свойства металлов и сплавов.
При термообработке не меняется химический состав.
Конструкторские стали обыкновенного качества СТ0-СТ6 и конструкторские качественные стали Сталь05,08,10,15,20,25 не подвергаются термообработке, так как выгорает верхний углеродный слой и меняется химический состав, что недопустимо. |
Сущность термообработки заключается в нагреве, выдержке и охлаждении сплава.
По длительности все три процесса равноценны.
t0С Нагрев Выдержка Охлаждение
t
- температура нагрева
- длительность выдержки
- скорость нагрева
- скорость охлаждения
Виды термообработки.
1. Закалка | - для повышения твердости, прочности, износостойкости |
2. Отпуск | - всегда проводится после закалки для снятия внутренних напряжений для устранения межузельных атомов для повышения пластичности и вязкости |
3. Отжиг | - предварительная термообработка для исправления структуры для улучшения обработки резанием, обработки давлением |
4. Нормализация | - назначение аналогично отжигу |
5. Термомеханическая | - совокупность операций пластического деформирования и термообработки для повышения прочности |
6. Химикотермическая | - совокупность операций диффузионного насыщения и термообработки |
Закалка.
-нагрев стали выше критических температур на 30-500С(выше линии Ст8К), выдержка и последующее охлаждение в воде или масле, при этом пластичность и вязкость снижаются.
Закалка
Полная Неполная
(аустенит) (аустенит + цементит ІІ)
Инструментальные стали закаливают в масле.
Поверхностная закалка (1935).
- деталь помещают внутрь медной спирали (индуктора)
|
нагрев токами высокой частоты
охлаждение снизу
Достоинства метода: высокая производительность, не образуется окалина, нет окисления и дкформации деталей, легко автоматизируется.
Применение: для зубчатых колес тепловозов и электровозов, шеек коленвалов.
Недостатки закалки: - остаточное внутреннее напряжение
- выгорание верхнего углеродного слоя (используется цементация)
Отпуск.
- для устранения вредного действия закалки
Отпуск
- низкий (150-2500С) Повышение твердости и прочности Подшипники, зубчатые колеса, валы | - средний (360-4500С) Повышение упругости Пружины, рессоры | -высокий (550-6500С) Повышение ударной вязкости Кондукторные плиты |
Ступенчатая закалка
При ступенчатой закалке деталь, нагретую до температуры закалки, переносят в жидкую среду, имеющую температуру на 50-100 °С выше мартенситной точки Мн закаливаемой стали, и выдерживают небольшое время, необходимое для выравнивания температуры но сечению, а затем окончательно охлаждают на спокойном воздухе
К ступенчатой закалке прибегают обычно при термической обработке инструментов небольшого сечения из низко- и среднелегированных сталей.
Закалка в двух средах.
После нагрева под закалку деталь погружается на определенное время в воду, а затем переносится в масло.
Твердые сплавы.
- сплавы, применяемые в качестве режущей части резцов.
вольфрамовые ВК ВК3 ВК3М | титано-вольфрамовые ТК Т15К6 | титано-тантало-вольфрамовые ТТК ТТ30К4 |
Литье под давлением
Виды обработки металлов давлением:
- Ковка
- Прокатка
- Штамповка
- Прессование
- Волочение
Схемы обработки:
Ковка
Р
Прокатка
Волочение
Заготовка
Волока
Прессование
матрица контейнер
заготовка
пуансон
Штамповка Р
Виды прокатки
а – продольная; б – поперечная; в – поперечно – винтовая
Виды прокатных изделий
Металлопрокат может изготавливаться из чёрной стали, легированной, нержавеющей, меди, алюминия и других металлов.
Классы сварки
Термический Дуговая сварка - ручная - полуавтоматическая - автоматическая Электро-лучевая Газовая Плазменная Электрошлаковая | Термомеханический Контактная - точечная - стыковая - шовная Сварка аккумулированной энергией Конденсаторная Электромагнитная Диффузионная | Механический Холодная сварка - точечная - стыковая - шовная Сварка трением Ультразвуковая сварка Взрывная |
Пайка и резка металлов
|
Припои
Мягкие - легкоплавкие (до 200-4000С) паяльник или газовая горелка (олово, свинец) ПОС-90 | Твердые - флюсы (800-9000С) горелка,ТВЧ, пена (сплав меди с цинком Л-62, Л-68 листовая и прутковая) ПМЦ-36 |
ТВЧ - токи высокой частоты
ПОС-92 – припой оловянисто-свинцовый, содержание олова 90%
ПМЦ-36 – припой медно-цинковый, содержащий 36% меди
Газовая сварка и резка.
Газовая сварка - сварка плавлением, при которой нагрев кромок соединяемых частей производят пламенем газов, сжигаемых на выходе горелки.
Металлорежущие станки
Станок Петра I
ДИП –(догнать и перегнать)
А62
К62
1981 – составлена классификация ЭНИИМС (экспериментальный НИИ металлорежущих станков)
А62 1К62
Группа (токарные)
Тип (токарно-винтовой)
Высота центра над столом
А – базовая модель
Н125 2М112
Группа (сверлильные)
Тип (вертикальный)
Наибольший диаметр сверла
Н – базовая модель
Группа (шлифовальные)
П80Г
Группа(фрезерный)
Тип (горизонтальный)
Встречное
S
Магнитные материалы
Магнитомягкие
Нс < 760
Электротехническая сталь (Fe, C, Si)
- сердечники трансформаторов, электромагнитов, якоря и статоры электротехнических машин, измерительные приборы
Пермаллой (Fe, C, Ni)
- сердечники малогабаритных силовых трансформаторов, дросселей, реле
Альсифер (Fe, C, Al, Si)
- магнитные экраны, корпуса приборов, прессованные сердечники из порошка
Магнитотвердые
Нс > 24000
- изготовление постоянных магнитов
Сплавы | Магниты из порошков | |
Альни (Al-Ni-Fe) Альниси (Al-Ni-Fe-Si) Альнико (Al-Ni-Fe- Со) | Металлокерамические сплавы Cu-Ni-Со Cu-Ni-Fe прессование и спекание при высоких t0 | Металлопластические сплавы Cu-Ni-Со Cu-Ni-Fe Формальдегидовая смола под давлением 500МПа и t0 1800С |
Ферриты (оксиферы) — химические соединения оксида железа Fe2O3 с оксидами других металлов
Ферриты
Магнитомягкие Ni-Zn Mn-Zn | Для приборов с СВЧ | с ППГ (прямоугольной петлей гистерезиса) | Магнитотвердые BaO·6Fe2O3 |
Магнитодиэлектрики – соединение альсифера, пермаллоя с фенолформальдегидной смолой, стеклом.
Экипировочные материалы
Смазочные материалы
- применяются для уменьшения потерь энергии на трение и снижение износа трущихся деталей, масло охлаждает и очищает от продуктов износа трущиеся поверхности, а также защищает их от коррозии.
Требования:
- разделять трущиеся детали масляным слоем для обеспечения жидкостного трения, создавать на поверхности прочную масляную пленку, предохраняя детали от сухого трения
- удерживаться на поверхности неработающих деталей для предохранения от коррозии
- отводить тепло от трущихся деталей
- обладать способностью смывать продукты износа и легко отделяться от них
- не изменять длительное время свои свойства в процессе работы и хранения
- должно быть экономным и не дефицитным
Свойства масел:
влияющие на смазывающие и вязкостно-температурные качества
зависит образование нагара и отложений в двигателе
влияющие на коррозионный износ деталей
контрольные показатели, характеризующие однородность продукции разной партии и разных заводов
Смазывающие материалы
- моторные масла
- трансмиссионные масла
- пластичные смазки
Моторные масла должны обладать:
- антифрикционными и противоизносными свойствами во всем интервале рабочих температур
- минимальной склонностью к образованию различных отложений и пенообразованию при работе двигателя
- антикоррозионными и моющими свойствами
Трансмиссионные масла применяются для смазывания сборных соединений трансмиссий различных механизмов – коробок передач, рулевого управления, трущихся деталей задних мостов, раздаточных коробок, различных редукторов.
Пластичные смазки – находятся в пластичном мазеобразном состоянии
Применяются в узлах трения, где трудно создать герметичность для жидкого масла и трудно защитить поверхности от пыли, влаги, грязи.
Обладают более низкими смазывающими качествами, поэтому применяются там, где невелики потери от трения.
Иногда применяют только как защиту от коррозий
Требования:
- разделять трущиеся детали прочной слизистой пленкой для уменьшения износа и потерь на трение.
- удерживаться в узлах трения не вытекая из них
- защищать трущиеся детали от пыли, влаги, грязи
- не вызывать коррозионного износа деталей
- легко прокачиваться, не требуя больших давлений
Основа любой пластичной смазки -75-90% минерального масла.
Второй компонент – загуститель.
(мыльный, не мыльный)
кальциевые натриевые литиевые бариевые | парафин церезин петролатум воск |
Применяют пластичные смазки по назначению:
- антифрикционные (прессолидол, литол, консталин)
- защитные, консервационные (мастики, пленкообразующие нефтяные составы)
- уплотнительные (бензиноупорные)
Электроды.
Плавящиеся - стержни из специально сварочной проволоки | Неплавящиеся - вольфрамовые - угольные - графитовые (изготавливают из порошка кокса с последующим отжигом при t0 14000С) |
Сварочный флюс.
- неметаллический материал, расплав которого необходим для сварки и улучшения качества шва.
Флюс – место сварки слоем 50-60мм
АН-348А, ОЦС-45
Композиционные материалы
Композиционные материалы – искусственно созданные материалы, которые состоят из двух или более компонентов, различающихся по составу и разделенных выраженной границей, и которые имеют новые свойства, запроектированные заранее.
Состоят: мартица, уплотнитель (арматура, наполнитель)
непрерывный компонент в объеме композитного материала | другие компоненты, расположенные в объеме матрицы | |||
2 | 1- матрица 2- уплотнитель 3- зона раздела фаз | |||
Классификация
По типу матрицы - полимерные - металлические - неорганические - комбинированные | По виду армирующего элемента - геометрические размеры - порядок расположения в матрице - целей армирования | По особенности макростроения | По месту получения - в твердой и жидкой фазах - с использованием газофазных процессов - в вязкотекучем состоянии - в разных комбинациях |
Наполнитель вводят для повышения твердости, прочности, пластичности; для изменения физических свойств.
Полимерная матрица
- пластмассы, металлопласты, сотопласты, наполненные пластики, конструкционные пластики, металлонаполненные пластики, графитопласты, саженаполненные резины, противокоррозионные пластики, пенопласт, армированные пластики, волкнистые (стеклопласт), асбопластики (тормозные колодки), волокниты, слоистые пластики, гетинакс, металлопласт, ДСП, на основе спеченного алюминиевого порошка (электрические контакты), на основе никеля, вольфрама (детали, имеющие высокую прочность), на основе железа (ударные нагрузки), на основе свинца, серебра (подшипники).
Используют вместо тормозных колодок из высокопрочного чугуна тормозные колодки из композитных материалов
Защитные покрытия металлов
- должно быть сплошным, равномерно распределенным по всей поверхности, непроницаемым для окружающей среды, иметь высокую адгезию (прочность сцепления с металлом), быть твердым и износостойким. Коэффициент теплового расширения должен быть близким к коэффициенту теплового расширения металла защищаемого изделия
Существуют
Неметаллические Металлические
органические неорганические катодные анодные
Нанесение защитных металлических покрытий – один из самых распространенных методов борьбы с коррозией. Эти покрытия не только защищают от коррозии, но и придают их поверхности ряд ценных физико-механических свойств:
- твердость
- износоустойчивость
- электропроводность
- паяемость
- отражательную способность
По способу защитного действия металлические покрытия делят на катодные и анодные.
Катодные покрытия имеют более положительный, а анодные - более электроотрицательный электродные потенциалы по сравнению с потенциалом металла, на который они нанесены. Так, например, медь, никель, серебро, золото, осажденные на сталь, являются катодными покрытиями, а цинк и кадмий по отношению к этой же стали – анодными покрытиями.
Антикоррозионные цинковые покрытия (катодные) являются эффективным способом защиты металлических конструкций от коррозии в пресной и морской водах.
Основное требование к катодным покрытиям – беспористость.
Анодное покрытие – одно из самых эффективных способов защиты металла от ржавления в воде.
Нанесение осуществляется металлизацией, напылением или горячим цинкованием.
В отдельных случаях защита может иметь место при нанесении катодных покрытий.
Защитные покрытия важны.
Ф – Ц – А – П – Л
(фазан, цапля, аист - птицы летающие)
Ф – феррит (твердый раствор углерода в Feα)
Ц – цементит (химическое соединение карбид железа Fe3C)
А – аустенит (твердый раствор углерода в Feγ)
П – перлит (механическая смесь феррита и цементита)
Л – ледебурит (тонкая механическая смесь аустенита и цементита)
Компонент – вещества, образующие систему (могут быть чистые металлы, неметаллы, устойчивые химические соединения)
Система – группа сплавов, выд. для изучения
Фаза – однородная часть системы, отделенная от других частей поверхностью раздела, при переходе через которую химический состав меняется.
Пример оформления практической работы.
Провести анализ сплава с углеродосодержанием 3,6% с описанием процесса при медленном охлаждении.
При процентном содержании углерода 3,6% сплав – чугун доэвтектический.
Первичная кристаллизация доэвтектического чугуна происходит при t0 12500C – образуется аустенит.
Вторичная кристаллизация - при t0 11470C – образуется цементит вторичный и ледебурит, расп. Аустенит.
Окончательная структура образуется при t0 7270C - образуется перлит, ледебурит, цементит вторичный.
Примесь | Влияние | |
+ | - | |
Углерод | Возрастает твердость | Уменьшается сопротивление разрыву |
Кремний | Повышает предел текучести | Уменьшение пластичности |
Марганец | Повышает прочность | Уменьшает красноломкость стали |
Сера | Снижает развитие трещины | Ухудшает свариваемость |
Фосфор | Увеличивает временное сопротивление разрыву | Уменьшает пластичность и вязкость |
Классификация сталей. Углеродистые конструкционные стали. ГОСТ.
Сталь – сплав железа с углеродом, содержание углерода 0.02-2.14%
По назначению: - конструкционные
- инструментальные
По составу: - углеродистые(Fe,C)
- легированные (Fe,C,лег.элемент)
|
|
Наброски и зарисовки растений, плодов, цветов: Освоить конструктивное построение структуры дерева через зарисовки отдельных деревьев, группы деревьев...
Своеобразие русской архитектуры: Основной материал – дерево – быстрота постройки, но недолговечность и необходимость деления...
Таксономические единицы (категории) растений: Каждая система классификации состоит из определённых соподчиненных друг другу...
История развития пистолетов-пулеметов: Предпосылкой для возникновения пистолетов-пулеметов послужила давняя тенденция тяготения винтовок...
© cyberpedia.su 2017-2024 - Не является автором материалов. Исключительное право сохранено за автором текста.
Если вы не хотите, чтобы данный материал был у нас на сайте, перейдите по ссылке: Нарушение авторских прав. Мы поможем в написании вашей работы!