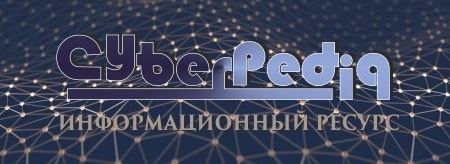
История развития пистолетов-пулеметов: Предпосылкой для возникновения пистолетов-пулеметов послужила давняя тенденция тяготения винтовок...
Двойное оплодотворение у цветковых растений: Оплодотворение - это процесс слияния мужской и женской половых клеток с образованием зиготы...
Топ:
Оценка эффективности инструментов коммуникационной политики: Внешние коммуникации - обмен информацией между организацией и её внешней средой...
Комплексной системы оценки состояния охраны труда на производственном объекте (КСОТ-П): Цели и задачи Комплексной системы оценки состояния охраны труда и определению факторов рисков по охране труда...
Устройство и оснащение процедурного кабинета: Решающая роль в обеспечении правильного лечения пациентов отводится процедурной медсестре...
Интересное:
Инженерная защита территорий, зданий и сооружений от опасных геологических процессов: Изучение оползневых явлений, оценка устойчивости склонов и проектирование противооползневых сооружений — актуальнейшие задачи, стоящие перед отечественными...
Национальное богатство страны и его составляющие: для оценки элементов национального богатства используются...
Подходы к решению темы фильма: Существует три основных типа исторического фильма, имеющих между собой много общего...
Дисциплины:
![]() |
![]() |
5.00
из
|
Заказать работу |
|
|
МИНИСТЕРСТВО ОБЩЕГО И ПРОФЕССИОНАЛЬНОГО ОБРАЗОВАНИЯ РОССИЙСКОЙ ФЕДЕРАЦИИ
МОСКОВСКИЙ ГОСУДАРСТВЕННЫЙ ТЕХНИЧЕСКИЙ УНИВЕРСИТЕТ "МАМИ"
Кафедра "Детали машин и ПТУ"
Белоглазов В.Г. Утверждено
Лукьянов А.С. методической комиссией факультета
Пустынцев Е.Н. "Автомобили и тракторы"
Рябов В.А.
РАСЧЕТ ЧЕРВЯЧНОЙ ПЕРЕДАЧИ
методические указания для студентов всех машиностроительных специальностей
Москва 2003
УДК: 621.867-83
Белоглазов В.Г., Лукьянов А.С., Пустынцев Евгений Николаевич, Рябов В.А.
ЧЕРВЯЧНЫЙ РЕДУКТОР (ПРИМЕР ПРОЕКТИРОВАНИЯ).
Методические указания к курсовому проектированию для студентов всех машиностроительных специальностей.
Стр. 1- 32, рис. 7, табл.12
МГТУ «МАМИ», 2003 г.
Рассмотрен пример расчета и конструирования червячного редуктора
СОДЕРЖАНИЕ
стр.
1. | ПРОЕКТИРОВОЧНЫЙ РАСЧЕТ ЗАКРЫТОЙ ЧЕРВЯЧНОЙ ПЕРЕДАЧИ | |
1.1 | Исходные данные для расчета червячной передачи...............…..... | |
1.2 | Установление основных данных …………………………….………. | |
1.3 | Определение допускаемых контактных напряжений...........…................ | |
1.4 | Определение основных размеров...............……………....................... | |
1.5 | Окружная скорость…………………………………………………….…… | |
1.6 | Скорость скольжения……………………………………..………….…… | |
1.7 | Уточнение КПД передачи, крутящего момента и мощности на червяке | |
1.8 | Силы в зацеплении.....……………….....................................…....…......... | |
2. | Проверочный расчет по контактным напряжениям……………………..… | |
3. | Проверочный расчет зубьев колеса на прочность при изгибе.................... | |
Проверочный расчет тела червяка на прочность и жесткость……...… | ||
5. | Тепловой расчет и охлаждение червячных передач………….…... | |
6. | Особенности проектировочного расчета червячной передачи по напряжениям изгиба в зубьях колеса | |
7. | Работа над чертежом червячного редуктора…………………………….. | |
Использованная литература..........................................…................…......... |
.
|
Ó Московский государственный технический университет "МАМИ", 2003г.
1. ПРОЕКТИРОВОЧНЫЙ РАСЧЕТ ЗАКРЫТОЙ ЧЕРВЯЧНОЙ ПЕРЕДАЧИ
Целью проектировочного расчета является предварительное определение размеров передачи из условия контактной выносливости рабочих поверхностей зубьев колеса.
1.1 Исходные данные:
- передаточное число u;
- частота вращения червяка n1 (мин-1)
- крутящий момент на валу колеса T2 (Н*м)
- ресурс передачи Lh, тыс. час.
- режим работы и условия нагружения;
1.2 выбор числа заходов червяка -
Передаточное отношение - ![]() | число витков червяка - ![]() |
31,5…80 | |
16..31,5 | |
8…16 |
1.3 Число зубьев червячного колеса - (1)
Полученное Z2 округлить до ближайшего целого числа и уточнить передаточное число u: (2)
Если червячный редуктор предназначен для среднего выпуска, то фактическое передаточное число не должно отличаться от стандартного более чем на 4%.
ГОСТ 2144-76 предусмотрены следующие номинальные передаточные числа:
1-ый ряд 8; 10; 12,5; 16; 20; 25; 31,5; 40; 50; 63; 80.
2-ой ряд 9; 11,5; 14; 18; 22,4; 28; 35,5; 45; 56.
1.4 Частота вращения колеса ,об/мин. (3)
1.5 Ориентировочная скорость скольжения в зацеплении
, м/с, (4)
где: - частота вращения вала червяка в мин-1 ;
, в Н*м - максимальный длительно действующий крутящий момент на валу колеса, число циклов действия которого за срок службы
,
1.6. Выбор профиля червяка
Выбор профиля червяка определяется требуемыми эксплуатационными свойствами и технологическими возможностями предполагаемого производства.
Различают следующие виды линейчатых цилиндрических червяков: архимедов (ZA), конволютные (ZN) и эвольвентные (ZI); нелинейные червяки, образованные конусом (ZК) и тором (ZT).
|
Передачи с червяками ZA; ZN; ZI и ZК обладают примерно одинаковыми эксплуатационными свойствами, однако достижение оптимального качества осуществляются при различных технологических возможностях.
Архимедовы червяки нашли наиболее широкое применение, что объясняется возможностью точного шлифования их рабочих поверхностей. Однако многозаходные червяки типа ZA отличаются большой сложностью изготовления и по точности уступают передачам с червяками типов ZI и ZK.
Эвольвентные червяки типa ZI позволяют удобно и весьма точно производить шлифование рабочих поверхностей плоской торцовой поверхностью дискового круга, однако применять их можно только при наличии специальных шлифовальных станков.
Червячные передачи с конволютными червяками типа ZN уступают по точности архимедовым передачам. Червяки применяют главным образом при отсутствии станков для шлифования эвольвентных червяков и при необходимости изготовления многозаходных передач со шлифованными червяками.
Передачи с червяками ZT обладают повышенными КПД и нагрузочной способностью, однако производство таких передач связано с определенными трудностями.
В настоящих методических указаниях даётся расчёт архимедовых и эвольвентных червячных передач.
1.7. Предварительный выбор материалов колеса и червяка.
Основным фактором, определяющим выбор материала венца колеса, является скорость скольжения в зацеплении. Применение дефицитных высокооловянных бронз может быть оправданно только для ответственных передач со скоростями скольжения , малооловянные бронзы применяют при
м/с, безоловянные бронзы и латуни используются при
м/с, чугуны – при
м/с.
В таблице 1 приведены основные материалы венцов червячных колёс.
Червяки силовых передач изготавливают из сталей, термически обработанных до высокой твёрдости, поверхность витков шлифуется и полируется.
Наилучшую стойкость передач обеспечивают червяки из цементуемых сталей (20Х; 12ХНЗА; 18ХГТ; 15ХФ), имеющие после закалки твёрдость рабочей поверхности 56…63. Возможно изготовление червяков и из среднеуглеродистых сталей (45; 40Х; 40ХН; 35ХГСА) с поверхностной или объёмной закалкой до твердости HRCэ 45…50.
При отсутствии оборудования для шлифования червяков для их изготовления применяют улучшенные стали. Эти же стали применяют при необходимости взаимной приработки колеса и червяка. Кроме того, стали в улучшенном и нормализованном состояниях применяют для червяков вспомогательных тихоходных и малонагруженных передач.
|
Для передач с колёсами весьма больших диаметров в целях экономии цветных сплавов применяют бронзовые червяки, позволяющие применять чугунные колёса.
Механические характеристики материалов червячных колес Таблица 1.
Наименование и марка | ГОСТ | Способ отливки | Механические свойства | Макси-мальная ![]() | ||||
![]() | ![]() | Твердость НВ2 | Модуль упругости Е2, МПа | Коэф. Пуас-сона ![]() | ||||
Бр.010Ф1 | ГОСТ 613-79 | П | 216…294 | 137…147 | 80…100 | 0,74*105 | 0,335 | |
К | 245…431 | 196…225 | 100…120 | 1,01*105 | ||||
Бр.ОНФ | Ц | 100…120 | 0,98*105 | 0,335 | ||||
Бр 06Ц6С3 | П | 147…196 | 0,93*105 | 0,335 | ||||
К | 176…216 | 78…98 | 60…76 | |||||
Бр.05Ц5С5 | П | 79…98 | 60…68 | 0,88*105 | 0,335 | |||
К | 176…216 | 78…122 | 60…66 | |||||
Бр.СуТН2 | П | –– | 0,75*105 | 0,335 | ||||
Бр.Л9ЖЗЛ | ГОСТ 493-79 | П | 392…490 | –––– | ––– | 0,35 | ||
К | 490…588 | 196…343 | 110…140 | (0,88…1,14)105 | ||||
Ц | 490…588 | 196…343 | 120…140 | (1,13…1,27)105 | ||||
Бр.А10ЖЧН4Л | П | ––– | 156,8 | 0,35 | ||||
К, Ц | 588…755 | 398…588 | 170…225 | 0,98*105 | ||||
ЛЦ58Мц2С2 | ГОСТ 17711-80 | П | –– | (0,88…0,98)105 | 0,35 | |||
К | 294…343 | 127…235 | 80…95 | |||||
СЧ 15 | ГОСТ 1412-79 | П | ––– | 163-229 | (0,74…0,98)105 | 0,25 | ||
СЧ 18 | П | ––– | 170…241 | (0,95…1,0)*105 | 0,25 |
Примечание: Условные обозначения способа отливки:
П – в песчаные формы; К – в кокиль; Ц – центробежный.
1.8. Выбор степени точности передачи.
Для червячных передач по ГОСТ 3675-81 предусмотрено четыре степени точности: от 6-ой до 9-ой.
Требуемую степень точности редукторных силовых передач выбирают в зависимости от скорости скольжения (см. табл. 2).
Таблица 2.
![]() | < 1,5 | 1.5…7.5 | 7.5…12 | > 12 |
Степень точности ![]() |
1.9. Предварительное определение КПД передачи и мощности на червяке
КПД: (5)
где - приведённый коэффициент трения в зацеплении, определяемый как
Здесь - приведённый угол трения
(6)
где в м/с; большее значение в круглых скобках брать для безоловянных бронз, латуней и чугунов. Примечание: формула (6) даёт удовлетворительные результаты при
м/с
|
Мощность на червяке: ,кВт (7)
1.10. Выбор коэффициента диаметра червяка – q
Для обеспечения необходимой жёсткости червяка рекомендуется принимать коэффициент диаметра червяка c округлением до ближайшего стандартного значения из ряда:
q = 8; 10; 12,5; 14; 16; 20 (ГОСТ 19672-74).
1.11 Определение коэффициента нагрузки
Коэффициент нагрузки (8)
- коэффициент неравномерности распределения нагрузки по длине линии контакта вследствие деформации червяка равен
, (9)
где - коэффициент деформации червяка, определяемый по эмпирической формуле:
; (10)
- средняя относительная нагрузка передачи
Если частота вращения валов передачи одинакова на всех ступенях блока нагружения, то , где tбл - продолжительность блока нагружения.
При использовании в приводе коробки передач или вариатора,
, (11)
где - максимальный длительно-действующий (расчётный) крутящий момент;
;
и
- соответственно крутящий момент, время работы и частота вращения на ί -ой ступени блока нагружения.
При постоянной нагрузке, когда Ti=Tmax, получаем без расчета, что νср=1, Кβ=1
Если режим работы передачи соответствует типовому (рис.1), то средняя относительная нагрузка передачи νср. выбирается из таблицы 3.
Коэффициент , учитывающий динамическую нагрузку, возникающую в зацеплении, зависит от скорости скольжения рабочих поверхностей и точности изготовления передачи может быть определен по формуле
, где
- номер степени точности (табл.2);
в м/с.
1.12. Допускаемые контактные напряжения.
1.12.1 Материал колеса – оловянная бронза
, (14)
где - допускаемое контактное напряжение при базовом числе циклов NНО =107
при шлифованных и полированных червяках с твердостью HRC
45
при шлифованных червяках с твердостью
.
(Кп=1,5)
- коэффициент, учитывающий интенсивность изнашивания поверхности зуба определяется в зависимости от скорости скольжения:
При
м/с
;
При м/с
;
При м/с
коэффициент долговечности
(15);
предел текучести бронзы (по таблице 1).
Эквивалентное число циклов нагружений зубьев колеса , (16)
где: - суммарное число нагружений зубьев колеса за весь срок службы передачи.
n2 - частота вращения колеса в мин-1, Lh - ресурс работы передачи в часах.
Примечание: если частота вращения колеса вращения на каждой ступени блока нагружения различная, то
n2i-частота вращения колеса на i-ой ступени нагружения.
Коэффициент эквивалентного режима при постоянной частоте вращения колеса:
(17)
в случае применения в приводе механизма коробки передач или вариатора,
(18).
Обозначения в формулах (17) и (18) те же,что и в формулах (11) и (12).
Если режим нагружения передачи соответствует типовому (рис.1), то значение можно взять из табл.3.
|
![]() |
Коэффициент эквивалентного режима и средняя относительная нагрузка передачи Таблица 3
Режим | |||||
μ4 | 0,38 | 0,20 | 0,107 | 0,036 | |
μ9 | 0.175 | 0,10 | 0,042 | 0,019 | |
nср | 0.75 | 0,5 | 0,5 | 0,3 |
Рис.1
1.12.2 Материал колеса - безоловянная бронза или латунь
Допускаемое контактное напряжение из условия отсутствия заедания , где
- исходные допускаемые напряжения;
- коэффициент, учитывающий влияние скорости скольжение на заедание.
Для шлифованных и полированных червяков с твердостью
=300Мпа;
, где Vcк в м/с
Для шлифованных червяков с твердостью
в м/с
1.12.3 Материал колеса – чугун
где исходное допускаемое напряжение
=175 МПа, а коэффициент, учитывающий влияние скорости скольжения,
1.13. Определение размеров передачи
1.13.1 Межосевое расстояние
мм (22)
где - момент на червячном колесе в
в
Если проектируемая передача предназначена для серийного выпуска, то полученное округляют до ближайшего стандартного по 1 или 2 ряду ГОСТ 2144-76.
Следует предпочитать первый ряд второму.
1-ый ряд … 40, 50, 63, 80, 100, 125, 160, 200, 250, 400, 500 мм …
2-ой ряд … 140, 180, 225, 280, 355, 450 мм …
Для нестандартных червячных передач округляют до ближайшего целого числа с окончанием на 0 или 5.
1.13.3. Окончательный выбор q и определение коэффициента смещения червяка x.
Коэффициент диаметра червяка выбирается из ряда по ГОСТ 19672-76 в пределах, определённых формулой: . (24)
Сочетание модулей m и коэффициента диаметра червяка q определяется рекомендациями ГОСТ 2144-76 (см. табл. 4).
Сочетание модулей m и коэффициентов диаметров червяка q
при =1; 2; 4 (по ГОСТ 2144-76) Таблица 4
![]() | q | ![]() | q | |
16*; 20 | 8; 10; 12,5; 16; 20 | |||
1,25 | 12,5; 16; 20 | (6) | 9**; 10** | |
(1,50) | 14**; 16*; 16** | 6,3 | 8; 10; 12,5; 14; 16; 20 | |
1,6 | 10; 12.5; 16;20 | (7) | 12** | |
8; 12**; 15.5; 16;20 | 8; 10; 12,5; 16; 20 | |||
2,5 | 8; 10; 12**; 15.5; 16; 20 | 8; 10; 12,5; 16; 20 | ||
(3) | 10**; 12** | (12) | 10**; 10** | |
3,15 | 8; 10; 12.5; 16; 20 | 12,5 | 8; 10; 12,5; 16; 20 | |
(3,5) | 10**; 12*; 12**; 14*; 14** | 8; 10; 12,5; 16 | ||
8; 8**; 10; 12*, 12,5; 16; 20 | 8; 10 | |||
Примечание: Модули в скобках не являются предпочтительными
* - только при ![]() ![]() ![]() |
При окончательном выборе q учитывают его влияние на КПД передачи, на жёсткость и прочность тела червяка. Меньшие q дают больший КПД передачи, но жёсткость и прочность червяка при этом ниже.
Смещение червяка выполняют для получения стандартного межосевого расстояния при выбранных m, Z и q.
Коэффициент смещения червяка ,
Из условия неподрезания и незаострения зубьев колеса, коэффициент смещения x должен быть в пределах . Если коэффициент смещенияне укладывается в указанные пределы, то можно выбрать другой q (табл.4), соответствующий принятому модулю, и найти другой х по формуле (25). При наличии возможности выбора, коэффициент смещениялучше брать
, т.к. в этом случае прочность зуба колеса при изгибе выше.
Если же ни одно из рекомендуемых ГОСТом значений q не даёт нужного х, то можно изменить число зубьев колеса на 1 или 2 зуба. После этого следует уточнить передаточное число передачи u по формуле (2) и частоту вращения колеса
по формуле (3).
1.13.4. Расчет геометрических параметров червячной передачи
Рис.2 Схема цилиндрической червячной передачи при x> 0
Длина нарезанной части червяка (рис.2) , где С1и С2 –коэффициенты, которые выбирают из табл.7 по числу витков Z1 и коэффициенту смещения
Таблица 7
![]() | -1 | -0.5 | +0,5 | +1 | ||
Z1 = 1; 2 | С1 | 10,5 | ||||
С2 | 0,06 | 0,06 | 0,06 | 0,1 | 0.1 | |
Z1 = 4 | С1 | 10,5 | 9,5 | 12,5 | 12,5 | |
С2 | 0,09 | 0,09 | 0,09 | 0,1 | 0,1 |
Для шлифуемых червяков во избежание искажения рабочий части поверхностей витков червяка при входе и выходе шлифовального круга b увеличивают на 3m.
В таблице 5 приведены вычисляемые параметры червяка и формулы для их расчета.
В таблице 6 расчетные зависимости для определения параметров червячного колеса
Параметры червяка Таблица 5
Наименование | Разм. | Расчетные формулы | ||
Архимедов червяк ZA | Эвольвентный червяк Z I | |||
Делительный диаметр | мм | ![]() | ||
Начальный диаметр | мм | ![]() | ||
Диаметр вершин витков | мм | ![]() ![]() | ||
Диаметр впадин витков | мм | ![]() | ![]() | |
Делительный угол подъема | градус | ![]() | ||
Начальный угол подъема | градус | ![]() | ||
Основной угол подъема* (для червяка ZI) | градус | _____ | ![]() | |
Угол профиля в нормальном сечении на начальном цилиндре* | градус | ![]() | ____ | |
* Примечание. Угол профиля в осевом сечении витка червяка ZA aх =200; угол профиля в нормальном сечении зуба рейки, сопряженной с червяком ZI aп =200 (ГОСТ 19036-81). | ||||
Параметры червячного колеса Таблица 6
Наименование | Размерность | Расчетная формула | |
Червяк ZA | Червяк ZI | ||
Ширина венца | мм | ![]() ![]() | |
Условный угол обхвата червяка | град | 2δ= ![]() | |
Делительный диаметр | мм | ![]() | |
Начальный диаметр | мм | ![]() | |
Диаметр вершин зубьев | мм | ![]() ![]() | |
Диаметр впадин зубьев | мм | ![]() | ![]() |
Наибольший диаметр | мм | ![]() |
Делительный угол подъема линии витка γ для наиболее употребительных коэффициентов диаметра червяка q можно взять из табл. 7
Таблица 7
Z1 | q | |||||
12,5 | ||||||
![]() | ![]() | ![]() | ![]() | ![]() | ![]() | |
![]() | ![]() | ![]() | ![]() | ![]() | ![]() | |
![]() | ![]() | ![]() | ![]() | ![]() | ![]() |
1.13.5 Определение скоростей
Окружная скорость на начальном цилиндре червяка м/с (26)
Окружная скорость на начальной окружности колеса м/с (27)
В этих формулах диметр в мм, частота вращения мин -1.
Скорость скольжения в зацеплении м/с (28)
1.13.6 Уточнение КПД передачи, крутящего момента и мощности на червяке.
КПД червячного зацепления при ведущим червяке (29)
В последнюю формулу следует подставить , определив его по формуле (6) для уточненной по формуле (28) скорости скольжения.
Общий КПД червячного редуктора
, (30)
где - КПД, учитывающий потери мощности на разбрызгивание и перемешивание смазочного материала; обычно
= 0,97..0,99
Меньшее значение принимают для быстроходных передач с нижним расположением червяка.
Используя полученный КПД по формуле(30), уточняют крутящий момент на червяке
, Н*м (31)
Мощность на червяке , кВт (32)
1.13.7 Определение сил в зацеплении
Окружная сила на колесе (осевая - на червяке)
или
(33)
Окружная сила на червяке (осевая - на колесе)
или
(34)
Радиальная сила на червяке и колесе (угол профиля
)
2. ПРОВЕРОЧНЫЙ РАСЧЕТ ПЕРЕДАЧИ ПО КОНТАКТНЫМ НАПРЯЖЕНИЯМ
2.1 Коэффициент, учитывающий механические свойства материалов сопряженной червячной пары.
, Мпа0,5 (36)
где Е1 и Е2 - модули упругости материалов червяка и венца колеса, МПа
для стали Е1=2,06*105 МПа, для материала червячного колеса - по таблице 1; и
- коэффициенты Пуассона.
=0,3; для материала венцов колес Е2 и
см в табл. 12.2 Коэффициент, учитывающий форму поверхностей сопряженной червячной пары.
Для червяка ZI: (37)
Для червяка ZA:
(38)
2.3 Коэффициент, учитывающий суммарную длину контактных линий (39)
коэффициент торцового перекрытия =1,95-
(40)
коэффициент, среднего изменения суммарной длинны контактных линий.
2.4.Коэффициент, учитывающий условный угол обхвата,
(41) где
в градусах.
2.5 Уточнение коэффициента нагрузки
По формуле (10) для окончательно выбранных q и Z2 определяем коэффициент деформации червяка , далее по формуле (9) найти Кβ; по формуле (13) находим КV при действительной скорости скольжения, вычисленной по формуле (28); и по формуле (8) определяется уточненный коэффициент нагрузки К.
2.6 Уточнение допускаемого контактного напряжения
В зависимости от выбранного материала венца колеса по формуле (14), (20) или (21) определить окончательное допускаемое контактное напряжение, предварительно уточнив коэффициент СV () по скорости скольжения, вычисленной по формуле (28).
2.7. Действительные контактные напряжения
, МПа (42)
где в Мпа0,5,
в Н*м,
в мм
Сравниваем и с учетом фактической скорости скольжения в зацеплении
, производим окончательный выбор материала венца червячного колеса, устанавливаем твердость поверхности и вид окончательной обработки витков червяка.
2.8. Проверка зубьев колеса на статическую прочность по контактным напряжениям.
Проверка производится при действии неучтенных пиковых нагрузок по формуле
где Т2ПИК и Т2 - соответственно наибольшей неучтенный пиковый и максимальный расчетный моменты;
- контактное напряжение при Т2 по формуле(42);
-предельное допустимое контактное напряжения
Таблица 8
Материал колеса | ![]() | ![]() |
Оловянные бронзы | ![]() | ![]() |
Безоловянные бронзы и латуни | ![]() | |
Чугуны | ![]() | ![]() |
2. Проверочный расчет зубьев колеса на прочность при изгибе
3.
3.1. Коэффициент, учитывающий суммарную длину контактных линий,
(43)
3.2. Коэффициент, учитывающий условный угол обхвата, (44)
где δ в градусах (см. табл.8).
3.3 Коэффициент, учитывающий наклон зуба колеса, (45)
где γ в градусах (см.табл.5)
3.4. Коэффициент формы зуба ΥF
![]() |
Выбирается по графику (рис.3)
в зависимости от коэффициента смещения и
Рис.3
3.5. Коэффициент нагрузки К берется на основании расчетов в п.2.5.
3.6. Определение допускаемых напряжений изгиба
3.6.1.Условный базовый предел изгибной выносливости зубьев колеса
Для бронз и латуней при нереверсивной нагрузке
при реверсивной нагрузке
Для чугунов при нереверсивной нагрузке
при реверсивной нагрузке
3.6.2. Коэффициент безопасности: для бронз и латуней SF=1,75; (для чугунов SF=2,0)
3.6.3.Коэффициент долговечности (46)
где база испытаний NFO=106;
Эквивалентное число циклов нагружений зубьев колеса при изгибе
(47)
Суммарное число циклов определяется по формуле (19);
Коэффициент эквивалентного режима (48)
или при постоянной частоте вращени
|
|
Индивидуальные и групповые автопоилки: для животных. Схемы и конструкции...
История создания датчика движения: Первый прибор для обнаружения движения был изобретен немецким физиком Генрихом Герцем...
Индивидуальные очистные сооружения: К классу индивидуальных очистных сооружений относят сооружения, пропускная способность которых...
Типы сооружений для обработки осадков: Септиками называются сооружения, в которых одновременно происходят осветление сточной жидкости...
© cyberpedia.su 2017-2024 - Не является автором материалов. Исключительное право сохранено за автором текста.
Если вы не хотите, чтобы данный материал был у нас на сайте, перейдите по ссылке: Нарушение авторских прав. Мы поможем в написании вашей работы!