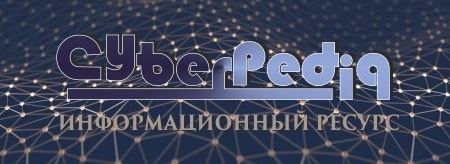
Кормораздатчик мобильный электрифицированный: схема и процесс работы устройства...
Организация стока поверхностных вод: Наибольшее количество влаги на земном шаре испаряется с поверхности морей и океанов (88‰)...
Топ:
Выпускная квалификационная работа: Основная часть ВКР, как правило, состоит из двух-трех глав, каждая из которых, в свою очередь...
Устройство и оснащение процедурного кабинета: Решающая роль в обеспечении правильного лечения пациентов отводится процедурной медсестре...
Основы обеспечения единства измерений: Обеспечение единства измерений - деятельность метрологических служб, направленная на достижение...
Интересное:
Отражение на счетах бухгалтерского учета процесса приобретения: Процесс заготовления представляет систему экономических событий, включающих приобретение организацией у поставщиков сырья...
Национальное богатство страны и его составляющие: для оценки элементов национального богатства используются...
Инженерная защита территорий, зданий и сооружений от опасных геологических процессов: Изучение оползневых явлений, оценка устойчивости склонов и проектирование противооползневых сооружений — актуальнейшие задачи, стоящие перед отечественными...
Дисциплины:
![]() |
![]() |
5.00
из
|
Заказать работу |
|
|
Отсутствуют “перерывы” на замену штучного электрода.Сварщик вынужден приостановить процесс работы, когда его положение становится неудобным или при достижении физического окончания шва. Это несет два основных преимущества:
- А. Заметно увеличивается время горения дуги и его доля, в общем времени выполнения работ.
- B. Устраняется значительное число дефектов, имеющих место при возобновлении сварного шва. Сварщик способен выполнить один непрерывный шов вместо последовательности коротких. Значительные затраты на ремонт подобных дефектов практически устраняются.
50% снижение времени зачистки сварных швов.
При четком соблюдении режимов сварки для электродов Innershield характерен низкий уровень разбрызгивания, что сокращает время на зачистку до 50% по сравнению с ручными электродами.
Отсутствие трещин в сварных швах.
Шлак, образуемый при сварке проволокой Innershield, обладает уникальным свойством нейтрализации серы, что понижает содержание сульфата железа в сварочной ванне и минимизирует объем связанных с этим дефектов. Спецификация сварочных материалов стандарта Американского общества сварщиков AWS A5.20-79 обращает особое внимание на высокие показатели трещиностойкости сварных швов, выполненных порошковой проволокой марки Innershield.
Случаи плохой сборки сварного соединения.
В некоторых случаях электроды Innershield специально рекомендуются для выполнения корневых швов недостаточно четко подогнанных соединений. По средством простого увеличения электрического вылета электрода глубина проплавления может быть заметно понижена.При этом Innershield
способна справляться с заполнением значительных зазоров с производительностью, недоступной ни одному другому методу дуговой сварки. В дополнение к прямому снижению затрат, электроды Innershield обеспечивают и некоторую косвенную экономию. Большинство марок позволяют вести сварку во всех пространственных положениях. При работе вне помещений Innershield не требует дополнительных приспособлений для поддержания надежной защиты дуги. Наконец, эта проволока весьма проста в обращении. Сварщики проще обучаются работе с Innershield, чем с ручным электродом. С любой стороны, порошковая проволока Innershield - это наиболее прогрессивное решение большинства сварочных проблем.
|
Исключение затрат на использование защитных газов и соответствующих аксессуаров.
При работе с Innershield исключается необходимость первоначальных инвестиций и последующих затрат, связанных с установкой и эксплуатацией системы снабжения защитных газов. Сокращаются затраты на приобретение газов и дорогих горелок. При этом следует учесть, что действительный расход защитного газа при проведении сварочных работ значительно выше чем расчетный. Исчезают проблемы с качеством сварки, вызываемые ранее потерей газовой защиты ванны при работе на открытом воздухе.
Широкий арсенал проволок Innershield
Семейство порошковых проволок Innershield, разработанных компанией Lincoln Electric, сможет предложить электрод, максимально удовлетворяющий требованиям практически любого случая сварки.
Сварные швы с переменой пространственного положения.
Выпускается широкий спектр электродов, удовлетворяющих этим требованиям: от предназначенных для работ общего назначения до удовлетворяющих требованиям повышенной ударной вязкости.
Основная часть.
Подготовка конструкции к сварке.
1. Общие требования
Трубы, детали трубопроводов, запорная арматура и сварочные материалы применяемые при выполнении сварочных работ должны пройти входной контроль с оформлением соответствующих актов входного контроля в установленном порядке. Форма акта входного контроля сварочных материалов представлена в приложении Д к настоящему РД. Результаты контроля заносят в Журнал входного контроля.
|
При проведении входного контроля проверяется наличие сертификатов (паспортов) на трубы, соединительные детали трубопроводов, запорную арматуру и сварочные материалы, которые будут применены для сооружения объекта, а также соответствие маркировки обозначениям, указанным в сертификатах (паспортах). Документы, подтверждающие качество продукции, должны быть на русском языке или иметь перевод, оформленный в установленном порядке.
При отсутствии клейм, маркировки, сертификатов (или других документов, удостоверяющих их качество) трубы, соединительные детали трубопроводов, запорная арматура и сварочные материалы к сборке и сварке не допускаются.
При сварке трубопроводов проводится операционный контроль. Операционный контроль сварных стыков трубопроводов производится:
- систематическим операционным контролем, осуществляемым в процессе сборки и сварки трубопроводов;
- визуальным осмотром и обмером сварных соединений;
- проверкой сварных швов неразрушающими методами контроля;
Операционный контроль выполняется производителями работ и мастерами, а самоконтроль - исполнителями работ. При операционном контроле должно проверяться соответствие выполняемых работ рабочим чертежам, требованиям настоящего раздела, государственным стандартам и инструкциям, утвержденным в установленном порядке.
Подготовка труб, соединительных деталей и запорной арматуры к сварке
В процессе подготовки к сборке необходимо:
- очистить внутреннюю полость труб и деталей трубопроводов от попавшего грунта, снега и т.п. загрязнений, а также механически очистить до металлического блеска кромки и прилегающие к ним внутреннюю и наружную поверхности труб, деталей трубопроводов, патрубков запорной арматуры на ширину не менее 15 мм.
- осмотреть торцы труб (переходных катушек, переходных колец) и запорной арматуры. Внутренняя поверхность задвижек и обратных клапанов перед началом работ должна быть защищена от попадания грязи, брызг металла, окалины, шлака и других предметов согласно рекомендациям завода-изготовителя. Для этой цели могут быть также использованы резиновые коврики, заглушки из дерева и прокладки из несгораемых тканевых, пластиковых материалов.
|
- осмотреть поверхности кромок свариваемых элементов. Устранить шлифованием на наружной поверхности неизолированных торцов труб или переходных колец царапины, риски, задиры глубиной до 5 % от нормативной толщины стенки, но не более минусовых допусков на толщину стенки, оговоренных в соответствующих ГОСТах и Общих технических требованияхна трубы ОАО «АК «Транснефть».
- удалить усиление наружных заводских продольных и спиральных швов до величины от 0 до 0,5 мм на участке шириной от 10 до 15 мм от торца трубы.
При применении труб и деталей с заводской разделкой кромок следует проверить соответствие формы, геометрических размеров, общим техническим требованиям на трубы и соединительные детали ОАО «АК «Транснефть», действующих стандартов РФ в области производства трубной продукции и Техническими условиям на поставляемую продукцию. Соответствие подготовки кромок под сварку и размеры разделки проверяются инструментально.
В случае несоответствия заводской разделки кромок требованиям технологии сварки следует произвести обработку (переточку) кромок под сварку механическим способом с применением специализированных
станков. Форма специальной разделки кромок труб для автоматической и механизированной сварки приведена в соответствующих разделах по технологии сварки. Технологический процесс механической подготовки кромок представлен в приложении И. При применении труб с обработанными специальными станками кромками следует проверить соответствие формы, размеров и качества подготовки свариваемых кромок требованиям настоящего РД и Операционной технологической карты. Переточка торцов кромок деталей трубопроводов, запорной арматуры и т.п. допускается с официального разрешения завода изготовителя, по согласованной с ним инструкцией.
Форма разделки кромок для труб под сварку разнотолщинных соединений должна соответствовать одному из типов разделки, представленных рисунке 10.1.
Разрешается править трубы класса прочности К54 и менее с величиной овала не превышающей 4 % от номинального диаметра. Овальность труб определяется как отношение разности наибольшего и наименьшего диаметра к номинальному наружному диаметру. Исправление овала производится на расстоянии не более 200 мм от конца трубы. Технология исправления овала труб представлена в приложении И к настоящему РД.
|
Допускается правка плавных вмятин на концах труб с классом прочности К54 и менее, глубиной не более 3,5 % номинального диаметра трубы с помощью безударных разжимных устройств гидравлического типа с обязательным местным подогревом изнутри трубы до плюс 100+50 °С независимо от температуры окружающего воздуха.
Допускается ремонт забоин, задиров фасок глубиной до 5 мм на трубах 1-й группы прочности (таблица 13.4) с толщиной стенки более 6 мм. Ремонт осуществляется электродами с основным видом покрытия типа Э50А
диаметром от 2,5 до 3,2 мм. Перед началом сварки осуществляется обязательный предварительный подогрев до 100+30 °С.
Ремонт сваркой труб, предназначенных для строительства подводных переходов, не допускается.
Отремонтированные поверхности и кромки труб следует зачистить абразивным инструментом путем их шлифовки, при этом должна быть восстановлена заводская разделка кромок, а толщина стенки трубы не должна быть выведена за пределы минусового допуска.
Концы труб с забоинами и задирами фасок глубиной более 5 мм или вмятинами глубиной более 3,5 % от номинального диаметра труб 1-й группы прочности, забоинами, задирами фасок и вмятинами любой глубины для труб с толщиной стенки менее 6 мм или труб 2-ой, 3-й группы прочности с любой толщиной стенки, а также любыми вмятинами с надрывами или резкими перегибами, имеющими дефекты поверхности, исправлению не подлежат и должны быть обрезаны.
Резка труб производится с применением специальных станков.
Допускается производить резку труб механизированной плазменной, кислородной резкой с последующей обработкой специализированным станком или шлифмашинкой. При этом металл кромок должен быть удален на глубину не менее 1 мм от поверхности реза.
Для резки труб диаметром менее 377 мм допускается применение шлифмашинок.
После вырезки участка с недопустимыми дефектами следует выполнить УЗК участка, прилегающего к торцу шириной не менее 40 мм по всему периметру трубы для выявления возможных расслоений.
Если в процессе УЗК выявлено наличие расслоений, должна быть произведена обрезка трубы на расстоянии не менее 300 мм от торца и произведен ультразвуковой контроль в соответствии с выше приведенными правилами.
Допускается выполнение «нутрения» (расточки кромок изнутри трубы) шлифмашинками. После «нутрения» следует проверить соответствие минимальной фактической толщины стенки в зоне свариваемых торцов допускам, установленным в общих технических требованиях и технических условиях на поставляемые трубы. Качество выполнения «нутрения» фиксируется соответствующим актом ВИК.
|
Сборка кольцевых стыков
При сборке запрещается любая ударная правка концов труб.
Все подготовительные и сборочно-сварочные операции следует производить в соответствии с операционными технологическими картами, указания которых должны быть подтверждены результатами аттестации технологии сварки.
Работу по сборке и сварке соединений «переходное кольцо (переходная катушка)+корпус арматуры», а также стыков «труба + переходное кольцо арматуры (переходная катушка)» рекомендуется выполнять на стадии подготовки укрупненных заготовок в стационарных условиях, обеспечивающих возможность позиционирования и фиксации стыков в удобном для сварки пространственном положении. Типовые варианты соединения «переходное кольцо плюс корпус арматуры» представлены на рисунке 10.1 (Б; В; Г), а типовой вариант соединения «труба плюс переходное кольцо арматуры» – на рисунке 10.1 (А).
В случае применения запорной арматуры без приваренных (заводских) переходных колец под сварку монтаж узлов трубопроводов следует начинать с приварки переходных колец или катушек к торцам запорной арматуры. Стыкуемый с корпусом торец переходного кольца, катушки должен иметь заводскую фаску или фаску после механизированной газовой резки и обработки СПК. Рекомендуемая длина катушки – не менее диаметра трубы. Минимально допустимая длина переходного кольца не менее 250 мм.
Сборка и сварка трубных элементов с запорной арматурой производится в открытом положении запорной арматуры.
Смещение кромок электросварных труб после сборки не должно превышать:
- для труб с толщиной стенки 10,0 мм и более - 20 % от нормативной толщины стенки, но не более 3,0 мм.
- для труб с толщиной стенки менее 10,0 мм - 20 % от нормативной толщины стенки трубы.
- при сборке труб с толщиной стенки более 10 мм, с применением внутреннего центратора, смещение кромок должно составлять не более 2,0
мм. Для труб с толщиной стенки более 15 мм допускаются локальные смещения кромок до 3 мм при общей протяженности участков с такими смещениями не более 1/6 периметра стыка.
Внутреннее смещение кромок в стыках бесшовных труб не должно превышать:
- 0,5 мм для труб с толщинами стенок от 1,0 до 3,4 мм;
- 1 мм для труб с толщинами стенок от 3.5 до 4,9 мм;
- 1,5 мм для труб с толщинами стенок от 5,0 до 8,0 мм;
- 2,0 мм для труб с толщинами стенок 8,1 мм и более.
- для труб с нормативной толщиной стенки 10,0 мм и более допускаются местные внутренние смещения кромок не превышающие 3,0 мм на длине не более 100 мм.
Измерение величины внутреннего смещения бесшовных труб следует выполнять шаблоном. Допускается измерение величины смещения кромок бесшовных труб по наружным поверхностям с одновременным измерением толщины стенки трубы в месте замера.
При сборке соединений «переходное кольцо плюс корпус арматуры» величина смещения кромок, измеряемого по внутренним поверхностям, должна составлять не более 2 мм.
При сборке заводские продольные швы следует смещать относительного друг друга не менее чем на 75 мм – при диаметре труб до 530 мм включительно, на 100 мм – при диаметре труб более 530 мм.
В случае технической невозможности соблюдения требований, (захлесты, приварка кривых холодного гнутья и т.д.) любое изменение расстояния между смежными швами в каждом отдельном случае должно быть подтверждено с представителем службы независимого технического надзора и отражено в исполнительной документации (в сварочном журнале).
При установке зазора в стыках, выполняемых различными способами сварки, следует руководствоваться требованиями таблицы 1.
Сборку стыков труб диаметром 377 мм и более следует производить на внутренних центраторах гидравлического или пневматического типов. Центратор не должен оставлять царапин, задиров, масляных пятен на внутренней поверхности труб.
Сборку на внутреннем центраторе стыков труб и деталей с заводской или подготовленной специализированными станками разделкой кромок следует осуществлять без прихваток. Если в процессе установки технологического зазора возникла объективная необходимость в установке прихваток, то они должны быть полностью удалены в процессе сварки корневого слоя шва.
На трубопроводах диаметром менее 100 мм, допускается не удалять выполненные прихватки, при условии запиливания мест начала и окончания прихваток с целью их последующего плавного сопряжения с участками выполняемого корневого слоя.
При выполнении захлестов, в том числе путем вварки катушки, стыков соединений труба - соединительная деталь, труба - запорная арматура, а также в случаях, когда применение внутренних центраторов технически невозможно, сборку соединений следует осуществлять на наружных центраторах (сборочных приспособлениях).
При сборке труб под двустороннюю автоматическую сварку поворотных стыков труб на трубосварочной базе допускается выполнение одной прихватки длиной 200 мм. Прихватка выполняется на режиме сварки первого наружного слоя шва, с обязательным запиливанием начального и конечного участка прихватки.
Таблица 1. - Величина зазоров в стыках, выполняемых различными способами сварки
Способ сварки | Диаметр электрода или сварочной проволоки, мм | Величина зазора, мм |
Автоматическая сварка в среде защитных газов на оборудовании CRC-Evans AW | 0,9 / 1,0 | Без зазора. Допускается наличие зазора не более 0,5 мм на участках стыка длиной до 100 мм |
Автоматическая сварка в среде защитных газов на оборудовании Serimer Dasa | 1,0 | Без зазора. Допускаются локальные зазоры до 1,0 мм на длине до 100 мм |
Автоматическая сварка в среде защитных газов на оборудовании СWS.02 | 1,0 | Без зазора. допускаются локальные зазоры до 0,5 мм на длине до 100 мм |
Автоматическая сварка проволокой сплошного сечения в среде защитных газов головками системы PWT и RMS | 1,2 | Без зазора. Допускается наличие зазора не более 0,5 мм |
Автоматическая сварка методом STT | 1,14 | 2,5 – 4,0 |
Автоматическая сварка методом УКП | 1,14 | 3,0 − 4,0 |
Двусторонняя автоматическая сварка под флюсом | 3,0 / 3,2 / 4,0 | Без зазора. Допускается наличие зазора не более 0,5 мм на участках стыка длиной до 100 мм |
Ручная дуговая сварка электродами с основным видом покрытия | 2,5 / 2,6 3,0 / 3,2 | 2,0 – 3,0 2,5 – 3,5 |
Ручная дуговая сварка электродами с целлюлозным видом покрытия (на спуск) | 3,2 4,0 | 1,0 – 2,5 1,5 – 2,5 |
Ручная дуговая сварка электродами с целлюлозным видом покрытия (на подъем) | 3,2 | 1,5 – 3,5 |
Механизированная сварка методом STT | 1,14 | 2,5 – 4,0 |
Механизированная сварка методом ВКЗ | 1,14 | 1,5 - 4,0 |
Механизированная сварка методом УКП | 1,14 | 2,5 – 3,5 |
Механизированная сварка самозащитной порошковой проволокой | 1,7 (1,6) | 2,5 – 3,5 |
Аргонодуговая сварка | 1,6-2мм | 1+0.5 для толщин 2,0-3,0мм 1,5 ± 0,5 для толщин 3,2-4,0мм |
Примечание: Сборка труб с силикатно-эмалевым покрытием независимо от способа сварки производится без зазора. |
В случае технической невозможности сборки стыков без прихваток разрешается их установка в соответствии с требованиями представленными в таблице 8.2, с последующим удалением в процессе выполнения корневого слоя шва.
Сборка стыков труб, переходных колец и запорной арматуры производится с применением центратора, подготовленного для сборки стыка с различными наружными диаметрами соединяемых элементов.
Таблица 2. - Требования к количеству и протяженности прихваток.
Диаметр стыкуемых элементов, мм | Минимальное количество прихваток | Длина прихваток |
1067 и более | 150 - 200 | |
820 ÷ 1067 включительно | 100 - 150 | |
426≤ D ≤ 720 включительно | 60 -100 | |
219 ≤ D < 426 включительно | 40 - 60 | |
159 ≤ D< 219 включительно | 30 - 50 | |
14 ≤ D <159 включительно | 10 - 15 |
При сборке захлестов, труб с запорной арматурой диаметром 530-1220 мм количество прихваток следует увеличить на одну, а длину на 15-20 мм от максимальной длины прихваток.
Режимы сварки при выполнении прихваток должны соответствовать режимам сварки корневого слоя шва.
Установка прихваток и сварка соединений диаметром до 377 мм выполняются одним электросварщиком, а соединения большего диаметра – двумя электросварщиками одновременно.
Прихватка стыков диаметром до 377 мм должна производиться тем же сварщиком, который будет выполнять сварку корневого слоя шва.
Прихватки следует выполнять на следующем расстоянии от заводских продольных швов:
- для труб диаметром менее 100 мм – не менее половины диаметра;
- для труб диаметром более 100 мм – не менее 100 мм.
Выбор сварочных материалов.
Самозащитная порошковая проволока iNNERSHIELD:
Innershield NR-207-Н - оптимальная производительность при сварке на спуск при выполнении горячего, заполняющих и облицовочного проходов на стандартных трубопроводах и на трубопроводах, эксплуатируемых в арктическом климате. Прекрасное сопротивление растрескиванию, высокая ударная вязкость, отличные характеристики при испытаниях на изгиб.
Pipeliner NR-207+ - аналогична проволоке Innershield NR -207, отличается от неё большей производительностью и меньшим расходом. Предназначена для сварки методом сверху вниз горячих, заполняющих и облицовочных слоёв стыков магистральных трубопроводов из сталей класса Х42-Х70 API 5 L, в том числе арктического класса. Высокое значение ударной вязкости при низкой температуре, превосходная стойкость к трещинам.
Pipeliner NR-207XP - самозащитная порошковая проволока, аналогична проволоке Innershield NR -207, отличается от неё очень высокими значениями ударной вязкости при низких температурах, большей производительностью при меньшем расходе, предназначена для сварки методом сверху вниз горячих, заполняющих и облицовочных слоёв стыков магистральных трубопроводов из сталей класса Х42-Х70 API 5 L, в том числе арктического класса.
Innershield NR-232 - Высокая производительность одно- и многопроходной сварки во всех положениях. Отличная защита сварочной ванны в полевых условиях. Шлак самоотделяется. Высокое значение ударной вязкости.
Innershield NR-233 - Высокая производительность одно- и многопроходной сварки во всех положениях. Отличная защита сварочной ванны в полевых условиях. Шлак самоотделяется. Высокое значение ударной вязкости. Технология «Микрофлюс».
|
|
Эмиссия газов от очистных сооружений канализации: В последние годы внимание мирового сообщества сосредоточено на экологических проблемах...
Организация стока поверхностных вод: Наибольшее количество влаги на земном шаре испаряется с поверхности морей и океанов (88‰)...
Опора деревянной одностоечной и способы укрепление угловых опор: Опоры ВЛ - конструкции, предназначенные для поддерживания проводов на необходимой высоте над землей, водой...
Автоматическое растормаживание колес: Тормозные устройства колес предназначены для уменьшения длины пробега и улучшения маневрирования ВС при...
© cyberpedia.su 2017-2024 - Не является автором материалов. Исключительное право сохранено за автором текста.
Если вы не хотите, чтобы данный материал был у нас на сайте, перейдите по ссылке: Нарушение авторских прав. Мы поможем в написании вашей работы!