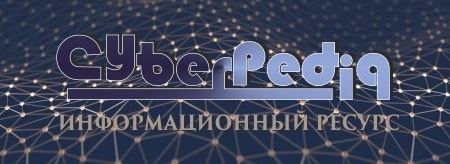
Папиллярные узоры пальцев рук - маркер спортивных способностей: дерматоглифические признаки формируются на 3-5 месяце беременности, не изменяются в течение жизни...
Адаптации растений и животных к жизни в горах: Большое значение для жизни организмов в горах имеют степень расчленения, крутизна и экспозиционные различия склонов...
Топ:
Установка замедленного коксования: Чем выше температура и ниже давление, тем место разрыва углеродной цепи всё больше смещается к её концу и значительно возрастает...
Проблема типологии научных революций: Глобальные научные революции и типы научной рациональности...
Интересное:
Отражение на счетах бухгалтерского учета процесса приобретения: Процесс заготовления представляет систему экономических событий, включающих приобретение организацией у поставщиков сырья...
Распространение рака на другие отдаленные от желудка органы: Характерных симптомов рака желудка не существует. Выраженные симптомы появляются, когда опухоль...
Мероприятия для защиты от морозного пучения грунтов: Инженерная защита от морозного (криогенного) пучения грунтов необходима для легких малоэтажных зданий и других сооружений...
Дисциплины:
![]() |
![]() |
5.00
из
|
Заказать работу |
Содержание книги
Поиск на нашем сайте
|
|
Закономерность геометрического ряда частот вращения позволяет проектировать коробки скоростей наиболее простой структуры, состоящей из элементарных двухваловых механизмов, последовательно соединенных между собой в одну или несколько кинематических цепей.. Такая структура называется множительной, так как кинематические условия настройки этих приводов определяются свойствами множительных групп передачи, а общее число скоростей получается перемножением чисел скоростей элементарных двухваловых передач.
Рассмотрим устройство на примере шестиступенчатой коробки скоростей. В результате последнего соединения элементарных механизмов при одной скорости ведущего вал I ведомый вал III может иметь шесть различных скоростей. Совокупность передач, связывающих вращение двух соседних валов, образует группу передач. Ее хар-ют два показателя: число р передач в группе и их передаточные отношения. В рассматриваемой схеме мы имеем две множительные группы: первая состоит из трех передач( вторая - из двух передач (
). Порядок чередования групп вдоль кинем-ой цепи хар-ет конструктивный вариант коробки. Его условно можно выразить в виде структурной формулы z = 6=3*2. В общем виде число ступеней скорости: Z= РаРь… Рт, где
- числа передач в первой, второй, m-й группах. Число конструктивных вариантов одной и той же структуры равно числу перестановок m групп, т. е.
=m!q!, где q - число групп с одинаковым числом передач.. Передаточные отношения передач зависят от так называемой хар-ки группы, обусловленной кинематич. порядком включения передач при переходе от одной частоты вращения шпинделя к другой. Примем такой порядок включения: используем все три положения блока
-
-
сначала при зацеплении колес
, а затеет повторим все сначала, зацепив колеса
. Если п — частота вращения вала I, то ряд частот вращения вала III можно выразить равенствами: n1 = n* z1/z2 • z7/z8; n2 = n • z3/z4 • z7/z8; n3 = n • z5/z6 • z7/z8; n4 = n • zl/z2 •z9/z10; n5 = n • z3/z4 • z9/z10; n6 = n • z5/z6 • z9/z10. Анализ этих равенств показывает, что при послед-ом переключении колес первой группы частота вращения вала III изменяется в
раз. Переключение же колес второй группы дает увеличение частоты вращения в
раз. В общем случае при переключении передач в какой-либо группе частота вращения выходного вала изменяется
раз. Показатель степени х называется хар-й множительной группы передач.
|
10. Порядок составления развертки и свертки приводов главного движения и подач м-р станков.
Чертеж привода главного движения представляют в виде двух изображений: развертки и свертки. На развертке (продольный разрез привода главного движения) все валы изображаются в одной плоскости.
В зависимости от пространственного расположения оси шпинделя на станке, на развертке валы изображаются горизонтально или вертикально. Например валы коробки скоростей токарно-винторезного, горизонтально-фрезерного станков располагаются горизонтально, а вертикально- и радиально-сверлильных станков - вертикально.
Рекомендуется развертку выполнить предварительно на миллиметровой бумаге. Если мощность двигателя меньше 10 кВт, чертеж желательно выполнять в масштабе1:1, при мощности выше 10 кВт - в масштабе 1:2. Необходимо решить, с помощью каких элементов будет передаваться вращение от двигателя к первому валу коробки скоростей.
Например, в токарно-винторезных, токарно-карусельных, токарно- револьверных станках вращение от двигателя на коробку скоростей передается клиноременной передачею.
В вертикально-сверлильных, горизонтально и вертикально-фрезерных радиаль но-сверлильных станках вращение на первых вал передается с помощью зубчатой передачи. В последнем случае с целью уменьшения динамических воздействий на зубчатые колеса коробки скоростей при пуске и реверсе шпинделя необходимо установить соединительную муфту с упругим элементом. Размеры муфт определяют по передаваемому крутящему моменту. В станках, на которых осуществляется нарезание резьбы резцами, метчиками, плашками необходимо предусмотреть реверсирование шпинделя. Реверс может быть электрическим или механический. Электрическое реверсирование осуществляется электродвигателем и используется в станках с малой инерционной массой вращающихся частей главного привода, если мощность электродвигателя не превышает 4,5 кВт
В остальных случаях применяют механический реверс в виде цилиндрических зубчатых колес. Для включения механического реверса применяют двухсторонние фрикционные муфты, которые могут быть сухие и масляные. Сухие муфты могут работать только в узлах, изолированных от масла, и требуют значительно меньших осевых усилий для включения, чем масляные. Однако в коробках скоростей и подач в условиях централизованной смазки применяют масляные фрикционные муфты. Число дисков муфты для включениярабочего хода определяется по передаваемому крутящему моменту, а для муфты холостого хода число дисков можно принять в 1,5 раза меньше. Фактическое число дисков муфт всех инерционных масс коробки скоростей, включая шпиндель с заготовкой. При известном числе дисков двухсторонней фрикционной муфты определяется ее осевой размер, что необходимо для вычерчивания развертки. В процессе первой компоновки стремятся разместить подвижные блоки зубчатых колес и неподвижных шестерен так, чтобы получить наименьшие осевые размеры. После ориентировочного определения осевой длины коробки по развертке можно найти диаметр шпинделя. При этом исходят из того, что жесткость двухопорного шпинделя у станков нормальной точности должна быть не менее 250 н/мкм. Для шпинделей станков нормальной точности, устанавливаемых в опорах качения, расстояние между опорами принимаю таким, чтобы оно приблизительно равнялось 4...5 диаметров шпинделя в передней опоре. Длина консольной части шпинделя должна быть минимальной и не превышать 1... 1,5 диаметра шпинделя в передней опоре. На поперечном я разрезе (свертке) показывается пространственное расположение валов коробки скоростей, а также механизмы управления, торможения, смазки, расположенные в шпиндельной бабке. Часто одного поперечного разреза бывает недостаточно, чтобы показать работу механизмов управления коробкой скоростей,n поэтому nрекомендуется делать
дополнительные разрезы и сечения. Если по условию задания необходимо разработать раздельный привод, используемый в токарно-винторезных станках повышенного и высоких классов точности, то необходимо выполнить отдельно развертку и свертку коробки скоростей различных групп металлорежущих станков.
|
|
11. Проектирование и расчет шпиндельных узлов м-р станков.
Основные требования, предъявляемые к шпиндельным узлам.
Шпиндели служат для закрепления и вращения заготовки или режущего инструмента и обеспечивают заданное положение их по отношению к другим узлам станка. Для обеспечения необходимой точности станка в пределах требуемого срока службы шпиндели должны обладать: а) жесткостью, достаточной длят предотвращения недопустимых деформаций от сил резания и привода;
б) стабильностью положения оси при вращении и поступательном движении;
в) износостойкостью шеек посадочных и базирующих поверхностей под патроны, планшайбы и инструмент.
По условиям работы шпиндели могут быть разделены на следующие группы:
1) шпиндели, подверженные изгибающим и крутящим воздействиям (токарных, фрезерных, шлифовальных и других станков);
2) шпиндели, подверженные преимущественно крутящим воздействиям и потому мало влияющие на точность и шероховатость обрабатываемых поверхностей (сверлильных, резьбонарезных, притирочных станков).
Точность обработки на многих станках определяется в значительной мере точностью вращения шпинделя, передающего движение закрепленному в нем инструменту или обрабатываемой детали.
В связи с этим к шпиндельным узлам станков предъявляются следующие основные требования:
1)Точность вращения- характеризуется обычно биение м среднего конца шпинделя. Для большинства станков общего назначения допускаемая велечина биения переднего конца шпинделя радиального и осевого- стандартизована; для специальных станков они назначаются с учетом требуемой точности обрабатываемой на станке детали.
|
2) Жесткость определяется правильностью положения шпинделя под действием рабочих сил. Слишком большие деформации шпинделя неблагоприятно отражаются на точности обработки и на работоспособности опор шпинделя и его привода.
3) Виброустойчивость - это требование, предъявляемое к шпинделям скоростных станков особенно - предназначенных для выполнения отдельных операций.
4) Износостойкость трущихся опорных поверхностей если они предусмотрены на шпинделе, при наличие опор скольжения или при относительном продольном перемещении элементов привода и шпинделя (на сверлильных, расточных и других станках). Указанные требования обеспечиваются правильным выбором материалов и инструкции шпинделя и его опор.
Материалы и термическая обработка
Решающими факторами, определяющими выбор материала шпинделя, являются твердость и износостойкость рабочих шеек и базирующих поверхностей фланцев и стабильность размеров и формы шпинделя в процессе его изготовления и работы. Для шпинделей0 станков нормальной и повышенной точности (Hи П) устанавливаемых в подшипниках качения, в качестве основного метода упрочнения рекомендуется поверхностная закалка с индукционным нагревом до твердости HRC 48-56. Эта твердость обеспечивается при изготовлении шпинделей из марок сталей 40Х,45, 50. Объемная закалка, обеспечивающая твердость в пределах HRC 56-60, рекомендуется преимущественно для шпинделей сложной формы, например, при наличии конусных отверстий небольшого размера, фланцев и т. д., когда выполнение закалки индукционным нагревом представляет технологические трудности. Обычно объемной закалке подвергают только переднюю часть шпинделя. В этом случае шпиндели рекомендуют выполнять из сталей марок 40ХГР или 50Х. Если для рабочих поверхностей шпинделей требуется твердость в пределах HRC 54-59, а объемная закалка затруднена, шпиндели изготовляют из сталей 40ХФА и 18ХГТ с
последующим азотированием или из сталей 18ХГТ и 20Х с последующей цементацией. Для азотирования возможно также применение стали марок 40 X, но износостойкость в этом случае будет несколько меньше.
Выбор типа опор шпинделя
Подшипниковый узел шпинделя шлифовального круга должен удовлетворять трём основным требованиям: иметь большую нагрузочную способность, с тем чтобы не нарушался нормальных режим работы шпинделя при действии на него переменной нагрузки от сил шлифования; быть достаточно жестким, виброустойчивым и не нагреваться. С увеличением скорости вращения круга эти требования должны. быть более жесткими. Для шпинделей шлифовальных бабок обычно применяются подшипники скольжения и реже подшипники качения.
Недостаточная жесткость и износостойкость подшипников качения ограничивает область их применения в шлифовальных станках, хотя следует отметить, что в случае изготовления роликовых подшипников высокого качества, их применение значительно упростило бы конструкцию шпиндельного узла и расширило технологические возможности станка. К опорам шпинделей предъявляют следующие специфические требования для металлорежущих станков: 1) Точность направления (радиального и осевого) шпинделя; в связи с этим в опорах шпинделей допускаются незначительные зазоры при большой жесткости опор. 2) Приспособленность к переменным условиям работы; во многих станках опоры шпинделей должны воспринимать различные нагрузки в широком диапазоне, скоростей и при частых пусках и остановках. Кроме того, к опорам шпинделей предъявляются также требования общие
для опор валов достаточная долговечность, малые габариты, простота изготовления (подшипников скольжения), простота и удобство сборки, регулирования и разборки и т. д.
|
Из двух типов подшипников скольжения (гидростатических и гидродинамических) наибольшее распространение получили гидродинамические подшипники, особенно для высокоскоростных круглошлифовальных станков. Шпиндели, как правило, рассчитывают на жесткость, и лишь для тяжело нагруженных шпинделей производят поверочный расчет на прочность. Основным видом деформации шпинделя, влияющим на точность работы.
|
|
Адаптации растений и животных к жизни в горах: Большое значение для жизни организмов в горах имеют степень расчленения, крутизна и экспозиционные различия склонов...
История развития хранилищ для нефти: Первые склады нефти появились в XVII веке. Они представляли собой землянные ямы-амбара глубиной 4…5 м...
Семя – орган полового размножения и расселения растений: наружи у семян имеется плотный покров – кожура...
Типы оградительных сооружений в морском порту: По расположению оградительных сооружений в плане различают волноломы, обе оконечности...
© cyberpedia.su 2017-2024 - Не является автором материалов. Исключительное право сохранено за автором текста.
Если вы не хотите, чтобы данный материал был у нас на сайте, перейдите по ссылке: Нарушение авторских прав. Мы поможем в написании вашей работы!