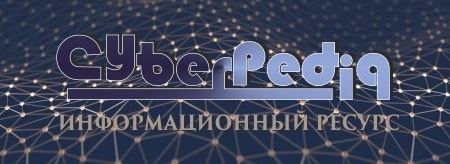
Таксономические единицы (категории) растений: Каждая система классификации состоит из определённых соподчиненных друг другу...
Типы сооружений для обработки осадков: Септиками называются сооружения, в которых одновременно происходят осветление сточной жидкости...
Топ:
Проблема типологии научных революций: Глобальные научные революции и типы научной рациональности...
Организация стока поверхностных вод: Наибольшее количество влаги на земном шаре испаряется с поверхности морей и океанов...
Основы обеспечения единства измерений: Обеспечение единства измерений - деятельность метрологических служб, направленная на достижение...
Интересное:
Инженерная защита территорий, зданий и сооружений от опасных геологических процессов: Изучение оползневых явлений, оценка устойчивости склонов и проектирование противооползневых сооружений — актуальнейшие задачи, стоящие перед отечественными...
Уполаживание и террасирование склонов: Если глубина оврага более 5 м необходимо устройство берм. Варианты использования оврагов для градостроительных целей...
Национальное богатство страны и его составляющие: для оценки элементов национального богатства используются...
Дисциплины:
![]() |
![]() |
5.00
из
|
Заказать работу |
Содержание книги
Поиск на нашем сайте
|
|
Порядок проектирования и расчета привода главного движения металлорежущего станка.
Кинематический расчет привода главного движения выполняется на базе следующих исходных данных: максимальная и минимальная частоты вращения выходного вала (числа двойных ходов); структурная схема станка; число скоростей привода; знаменатель ряда скоростей привода. Наилучшая структура привода, характеризующая передачу движения от двигателя до исполнительного механизма, выбирается на основе анализа.гаммы станков данной группы. Передача движения от двигателя может осуществляться посредством ременной передачи, с применением сменных колес, коробки скоростей.
Для приводов главного движения и подач станков общего назначения рекомендуется
применять простые множительные или сложенные структуры. На основе исходных данных выбирается структура и записывается лучший вариант структурной формулы для более короткой кинематической цепи, которая определяет число групп передач, число передач в каждой группе, последовательность переключения передач для получения
геометрического ряда скоростей привода главного движения, порядок конструктивного расположения различных групп в приводе, характеристику каждой группы передач. Для выбранной структуры чертят кинематическую схему, рассчитывают коэффициент полезного действия привода. На следующем этапе выбирают двигатель привода с учетом режима его работы в приводе. Согласно структурной схеме привода и кинематической схеме строят структурную сетку и график чисел оборотов (чисел двойных ходов), по которому определяют передаточные отношения групп передач с учетом ограничений (для привода главного движения 1/4 < i < 2, для привода подачи 1/5 </" <2,8). На следующем этапе кинематического расчета проводят расчет чисел зубьев передач привода. Расчет проводится аналитическим или табличным методами. После расчета числа зубьев передач проводят проверку соответствия действительного числа оборотов стандартным значениям. Полученные значения не должны отклоняться от табличных более чем на ±10 ( -1) %. Результаты проверки сводятся в таблицу. Вычерчивают кинематическую схему согласно условным обозначениям (ГОСТ 2.770-68) с учетом требований ГОСТ 2.701-76, 2.703-68, 2.721-77, намечаются места установки тормоза и элементов привода системы смазки, выявляется возможность уменьшения размеров привода.
|
В дальнейшем кинематическая схема дополняется данными, полученными в результате расчета ременной и др. передач.
Порядок проектирования и расчета привода подач металлорежущих станков.
Исходные данные для проектирования: Smax, Smin значения подачи.
1) Уточнение служебного назначения.
2) Выбор наилучшей структуры привода.
3) Q - определяем тяговое усилие.
4) Определяем крутящий момент.
5) Определяем Ыэлдв., п.
6) Кинематическая схема привода подач.
7) Определяем передаточное отношение передач.(стр. сетка, график числе оборотов)
8) Числа зубьев передач.
9) Расчет привода.
10) Разработка развертки и свертки.
11) Расчет и проектирование тягового устройств
Определение и обоснование основных технических характеристик оборудования.
Привод микроперемещений.
Основными техническими характеристиками станка, определяющими его производственные возможности, являются:
а) предельные частоты вращения шпинделя (числа двойных ходов столов и др.) nmax и nmin;
б) промежуточные значения частот вращения шпинделя (чисел двойных ходов столов и др.) между nmax и nmin;
в) предельные подачи smax и smin;
г) промежуточные значения подач между smax и smin;
д) мощность электродвигателя;
е) габаритные размеры заготовки.
Привод микроперемещений:
|
Упругосиловой привод использует для перемещения подвижного узла деформацию упругого звена, которая создается силовым воздействием. При достаточно большой жесткости упругое звено имеет ограниченную общую деформацию, и, следовательно, диапазон перемещения подвижного узла также небольшой.
Привод с растормаживанием основан на том, что под действием, системы управления вспомогательное устройство в течение определенного времени пропускает движение от основного электрического, гидравлического или механического двигателя. Дискретное управление растормаживанием от шаговых двигателей дает возможность применять подобные приводы в станках с программным управлением. Тормозящие устройства нередко называют механическими усилителями мощности, имея в виду, что управлять приходится мощностью двигателя во много раз меньшей, чем мощность основного двигателя.
Магнитострикционный привод использует свойство тел из ферромагнитных материалов изменять линейные размеры при намагничивании. В магнитное поле, создаваемое катушкой, помещен жесткий стержень. Один конец стержня жестко связан с неподвижной базовой деталью, а второй конец стержня закреплен в подвижном узле станка. С увеличением напряженности поля размеры стержня изменяются, что и приводит к перемещению подвижного узла.
Тепловой привод основан на том, что удлинение стержня и соответствующее перемещение узла происходят при непосредственном нагреве стержня. В исходное положение узел возвращается при охлаждении стержня жидкостью, пропускаемой через его внутреннюю полость.
Гидравлический привод с объемным регулированием имеет ограниченные возможности, так как малые стабильные подачи жидкости осуществимы до 2–3 см3/мин. Для малых точных перемещений в небольшом диапазоне перспективно использование регулируемых гидростатических опор.
Последовательность проектирования металлорежущих станков
Конструирование станка целесообразно проводить в следующей последовательности:
а) разработка технологического процесса обработки;
б) определение числа и характера исполнительных движений;
в) определение предельных режимов обработки, сил резания и эффективной мощности, а также величин рабочих и холостых ходов
г) определение основных технических характеристик станка;
|
д) предварительное определение мощности двигателя привода; это нужно для правильного выбора механизмов кинематики станка; после разработки кинематической, гидравлической, пневматической схем и конструкции станка мощность уточняется:
е) выбор типа привода и разработка кинематической, гидравлической, пневматической схем станка;
ж) разработка предварительной схемы компоновки станка;
з) разбивка станка на узлы и корректировка кинематической, гидравлической, пневматической схем;
и) выполнение прочностных и других расчетов и определение размеров основных элементов станка; после разработки конструкции узлов следует произвести проверочный расчет;
к) определение опорных и базовых поверхностей для всех узлов и разработка их конструкции;
л) составление чертежей общего вида станка, показывающих компоновку его узлов;
м) разбработка рабочих чертежей деталей и др.;
н) составление других технических документов, предусмотренных соответствующими ГОСТ и ОСТ.
3. Методика построения и анализа кинематической структуры оборудования. Кинематическая структура станка представляет собой совокупность кинематических групп. Группы могут быть соединены между собой разными способами; их соединение зависит от многих факторов. Наибольшее влияние на соединение кинематических групп оказывают общность их исполнительных органов и источника движения, а также необходимость координации во времени создаваемых группами движений. Всякое соединение двух кинематических групп осуществляется специальными дополнительными у строй-ми, такими, как суммирующие механизмы, реверсы, муфты и т.д. Главной и определяющей частью
кинематической структуры любого станка является его формообразующая часть, составляющая общее число и характер групп формообразования, а также их
кинематическое соединение. По этому признаку всё многообразие кинематических структур металлорежущих станков можно разделить на три класса:
1. Класс элементарных структур Э, к которому относятся станки с кинематической структурой, содержащей только простые группы формообразования, т.е. группы, создающие движение Ф(В) и Ф(П).
|
2. Класс сложных структур С, к которому относятся станки с кинематической структурой, содержащей только сложные группы формообразования, т.е. группы создающие движения Ф() и Ф(
) и т.д.
3. Класс комбинированных структур К, к которому относятся станки с кинематической структурой, содержащей одновременно и простые и сложные группы формообразования.
Каждый класс содержит определенное число типовых кинематических структур станков, которое можно условно записать буквой с последующими двумя цифрами. Буква указывает на класс, первая цифра 1 на число формообразующих групп, вторая цифра на суммарное число простых вращательных и прямолинейных движений, составляющих все формообразующие движения станка. Возможное число групп формообразования в струкгуре станка равно ТРЁМ. Составление и анализ структур кинематических групп станка проводят последовательно от одной к другой в следующем порядке:
1. Устанавливают число исполнительных органов; как правило, оно соответствует
числу простых движений, образующих, исполнительное движение.
2. Определяют внутреннюю кинематическую связь группы; для простых групп - это связь между звеньями кинематической исполнительной пары, а для сложной группы- функциональные цепи(цепь) между исполнительными органами.
3. Определяют источник движения и внешнюю кинематическую свзяь группы.
4. Устанавливают число и расположение органов настройки параметров движения.
5. Классификация движений в металлорежущих станках. Методы формообразования поверхностей на металлорежущих станках.
Все движения в станках, в том числе и формообразующие, называются исполнительными. По целевому признаку их можно разделить на движения: формообразования Ф, установочные Уст, деления Д, управления Упр, вспомогательные Всп.
Установочными называют движения заготовки и инструмента, необходимые для перемещения их в такое относительное положение, при котором становится возможным с помощью формообразующих движений получать поверхности требуемого размера. Иногда установочное движение, при котором отсутствует резание, называют наладочным. Если при установочном движении происходит резание материала, то такое движение называют движением врезания (обозначается Bp).
Делительными называют движения, необходимые для обеспечения равномерного расположения на заготовке одинаковых образуемых поверхностей. Делительные движения могут быть периодическими или непрерывными, что зависит в основном от конструкции режущего инструмента.
К вспомогательным движениям относятся движения, обеспечивающие установку, зажим, освобождение, транспортирование, быстрое перемещение заготовки и режущего инструмента в зону резания, охлаждение, смазывание, удаление стружки, правку инструмента и т.п. К движениям управления относят те, которые совершают органы управления, регулирования и координирования всех других исполнительных движений станка. К таким органами относятся муфты, реверсирующие устройства, кулачки, ограничители хода и др.
|
Определяющую роль в формировании кинематической структуры станка играют движения формообразования, установочные (врезания) и деления. Любое исполнительное движение в станке можно охарактеризовать пятью пространственными параметрами: траекторией, скоростью, направлением, путём и исходной точкой. Наиболее важными параметрами любого движения являются траектория и скорость.
|
|
Типы сооружений для обработки осадков: Септиками называются сооружения, в которых одновременно происходят осветление сточной жидкости...
Типы оградительных сооружений в морском порту: По расположению оградительных сооружений в плане различают волноломы, обе оконечности...
Индивидуальные очистные сооружения: К классу индивидуальных очистных сооружений относят сооружения, пропускная способность которых...
Двойное оплодотворение у цветковых растений: Оплодотворение - это процесс слияния мужской и женской половых клеток с образованием зиготы...
© cyberpedia.su 2017-2024 - Не является автором материалов. Исключительное право сохранено за автором текста.
Если вы не хотите, чтобы данный материал был у нас на сайте, перейдите по ссылке: Нарушение авторских прав. Мы поможем в написании вашей работы!