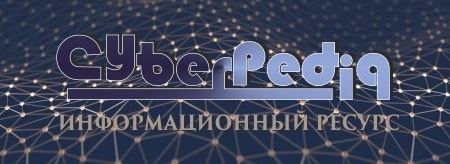
Индивидуальные и групповые автопоилки: для животных. Схемы и конструкции...
Общие условия выбора системы дренажа: Система дренажа выбирается в зависимости от характера защищаемого...
Топ:
Характеристика АТП и сварочно-жестяницкого участка: Транспорт в настоящее время является одной из важнейших отраслей народного...
Отражение на счетах бухгалтерского учета процесса приобретения: Процесс заготовления представляет систему экономических событий, включающих приобретение организацией у поставщиков сырья...
Теоретическая значимость работы: Описание теоретической значимости (ценности) результатов исследования должно присутствовать во введении...
Интересное:
Инженерная защита территорий, зданий и сооружений от опасных геологических процессов: Изучение оползневых явлений, оценка устойчивости склонов и проектирование противооползневых сооружений — актуальнейшие задачи, стоящие перед отечественными...
Финансовый рынок и его значение в управлении денежными потоками на современном этапе: любому предприятию для расширения производства и увеличения прибыли нужны...
Уполаживание и террасирование склонов: Если глубина оврага более 5 м необходимо устройство берм. Варианты использования оврагов для градостроительных целей...
Дисциплины:
![]() |
![]() |
5.00
из
|
Заказать работу |
Физическая сущность
Процесс электровзрывной обработки относится к методу обработки давлением. Быстрая деформация заготовки 1 (рис. 52) вызывается силами FЭ, действующими на ее поверхности. Заготовка деформируется и при ударе о стенки матрицы 2 принимает ее форму. Силы FЭ создаются вследствие взрывного испарения некоторого вещества 3 при пропускании через него кратковременного импульса тока I. Жидкость 4 служит для передачи механических усилий к заготовке 1, фиксируемой уплотняющими деталями 6: Импульсный ток I получают при разряде конденсаторной батареи 7, которая подсоединяется к электродам 5 с помощью переключателя 9. Конденсаторы предварительно заряжаются до высокого напряжения от выпрямителя 8. При деформации заготовки воздух из полости матрицы удаляется через отверстия 10.
Рисунок 52-Схема электровзрывной обработки
Известны две основные разновидности электровзрывного формообразования, в которых применяют: высоковольтный разряд при пробое диэлектрической жидкости, которая используется как испаряемое вещество, а также для передачи механических усилий к заготовке, и электрический взрыв проводникового испаряемого вещества, помещенного в жидкость, которая необходима только для передачи усилий к заготовке.
Электровзрывную обработку применяют как для формоизменения, так и для разделения заготовки, например для штамповки, гибки, чеканки, вытяжки, раздачи, а также для дробления хрупких материалов, очистки крупных отливок от пригара, резки, развальцовки труб. Оборудование просто переналаживается при мелко- или крупносерийном производстве. Сама обработка происходит очень быстро. Оптимальных показателей процесса добиваются подбором начальных условий.
К достоинствам электрогидравлического формообразования относятся: а) простота оснастки; б) равномерность нагружения заготовки; в) сохранение исходного качества поверхности листовой заготовки; г) возможность изготовления разнообразных деталей из заготовок одного вида. Электровзрывная обработка избавляет от выполнения дополнительных операций, а оборудование легко встраивается в автоматические линии.
История
При высоковольтном разряде, иначе называемом электрогидравлической обработкой, используют электрогидравлический эффект, впервые примененный для технологических целей Л. А. Юткиным.
Технические подробности
При электрогидравлической обработкой рабочим веществом, как правило, служит техническая вода. Электрический разряд протекает в герметичной камере. В окрестности канала разряда происходит почти мгновенное испарение жидкости, образуется ударная волна. Силы, деформирующие заготовку, создаются главным образом ударной волной, а также высоким давлением в возникающем газопаровом пузыре. Энергия разряда может достигать десятков килоджоулей, а длительность составляет несколько десятков микросекунд, мгновенная сила тока достигает 50 кА при длине разрядного промежутка в несколько сантиметров. Скорость фронта ударной волны заметно превышает скорость звука в воде и доходит до 3000 м/с. Начальная скорость стенок газового пузыря может быть больше 100 м/с, наибольший радиус пузыря - несколько сантиметров, максимальное давление в нем - до 1010 Па. Размеры обрабатываемых листовых заготовок толщиной до 5 мм могут превышать 1 м.
Механизм пробоя рабочей среды, в общем, такой же, как при электроэрозионной обработке. Однако техническая вода обладает некоторой электропроводностью, благодаря чему происходит ее местное вскипание еще тогда, когда напряжение на электродах Uc<Unp. Поэтому заметная часть энергии расходуется еще до пробоя.
После пробоя в жидкости образуется канал разряда начальным диаметром в десятые доли миллиметра. В окружающей жидкости возникает ударная волна. Чтобы большая часть энергии конденсаторов преобразовалась в энергию ударной волны, необходим разряд с высокой скоростью нарастания силы разрядного тока I. Этого добиваются подбором параметров разрядной цепи.
При электрическом взрыве конденсатор разряжается, на проводник в виде тонкой проволоки, нескольких проволок, фольги или сетки. Проводник располагают в диэлектрической жидкости. Начальное напряжение разряда в данном случае несколько киловольт (значительно меньше, чем в первой разновидности процесса). При протекании тока большой силы проводник нагревается и происходит его взрывное испарение. Возникает газопаровой пузырь, давление в котором достигает 1010 Па. В качестве материала проводников применяют медь, константан, нихром и др. Длина прямой проволоки - до нескольких десятков сантиметров, диаметр 0,1... 0,3 мм.
Применяют еще одну разновидность электровзрывной обработки – электрический взрыв в вакууме электропроводного материала (обычно металлической проволоки) с целью нанесения покрытия. Покрытия наносят на различные материалы (в том числе керамику и стекло) без предварительного нагрева изделия. Этим способом изготовляют детали рентгеновской аппаратуры и электронных приборов, цилиндров автомобильных двигателей и др.
Оборудование
Батарея конденсаторов подключена к выходу выпрямителя через зарядный резистор.
В генераторах обычно применяют высоковольтные импульсные конденсаторы на основе бумажно-масляных диэлектриков или касторового масла.
Разрядник обеспечивает подключение конденсаторов к электродам рабочей камеры. Различают типы разрядников: вакуумные, с твердым диэлектриком, а также высокого и атмосферного давления. Рабочие электроды разрядника отделены диэлектрическим промежутком, который соответствующими внешними воздействиями переводится в проводящее состояние.
В вакуумных разрядниках требуется непрерывно откачивать и удалять продукты разряда из его рабочего объема. Это значительно усложняет как устройство, так и эксплуатацию разрядника.
Разрядники с твердым диэлектриком - это установки разового действия, поскольку после каждого разряда необходимо заменять диэлектрик.
Наиболее простым и распространенным является разрядник с воздушным промежутком под атмосферным или более высоким давлением. Существующие воздушные искровые разрядники рассчитаны на рабочее напряжение 5... 100 кВ и максимальную силу разрядного тока 5...500 кА. Эти разрядники применяют при длительности импульсов тока от нескольких десятков до сотен микросекунд.
Работа разрядника сопровождается значительным шумом с уровнем в 90...120 дБ. Благодаря применению воздушных прослоек и звукопоглощающих кожухов уровень шума снижают до 50...60дБ. Металлические кожухи одновременно позволяют уменьшить радиопомехи, возникающие при работе разрядника.
Технологические схемы
Формообразование при электрическом взрыве проводников. В установке для формовки электрическим взрывом (рис.55) сила тока I при разряде конденсатора протекает по прямолинейной проволоке 1. При ее взрыве на стенки трубчатой заготовки 2 действуют поверхностные силы Fn, благодаря которым производится деформация заготовки 2 по форме матрицы 3. Этот процесс происходит более стабильно, поскольку его параметры не зависят от электропроводности рабочей жидкости.
Начальное напряжение конденсаторной батареи не превышает нескольких киловольт. Как и при электрогидравлическом формообразовании, параметры разрядной цепи подбирают так, чтобы наибольшая часть энергии конденсаторов выделилась в проволоке за первый полупериод разрядного тока. При за это время в промежуток поступает 30...40% энергии, накопленной в конденсаторах. При разряде конденсаторов резкое нарастание тока вызывает быстроменяющееся магнитное поле. Это поле создает поверхностный эффект, благодаря которому ток сосредоточен в узком внешнем слое проволоки. В этом слое выделяется теплота, которая передается как во внутренние области проволоки, так и в жидкость. Проволока плавится, окружающая жидкость испаряется - от проволоки отходит ударная волна. Скорость ее фронта тем больше, чем больше начальное напряжение. К центру проволоки распространяется волна сжимающих напряжений. Начинается тепловой взрыв проволоки: ток разряда очень быстро падает (рис.53), внешние слои проволоки испаряются, а фронт испарения перемещается к оси проволоки. Электропроводность насыщенного пара невелика, но иногда наблюдается образование плазмы.
Рис. 53. Процессы, протекающие во время перегорания проволоки
Разлет расплавленной перемычки предотвращается силами отдачи паров и индукцией магнитного поля, создаваемого разрядным током. Благодаря взаимодействию тока и поля на проволоку в радиальном направлении действуют сжимающие силы (пинч-эффект).
После падения тока возможен электрический разряд в канале, заполненном паром (рис. 53). Характер изменения силы тока I зависит от параметров разрядной цепи и продолжительности движения по проволоке фронта испарения. Тепловой взрыв проволоки обычно продолжительнее разряда в жидкости.
Параметры электрического взрыва прямолинейного проводника определяются индуктивностью и емкостью разрядной цепи, начальным напряжением конденсатора, длиной, диаметром и числом проволок. Спиральная проволока взрывается несколько быстрее, чем прямолинейная (обычно за 0.25 периода). Это объясняется тем, что магнитное поле В, вызываемое током I, имеет конфигурацию, которая слабее препятствует разлету электропроводной перемычки.
Явления, следующие за взрывом электропроводного вещества, в общем, такие же, как после электрического разряда в жидкости. Возникают ударная волна и газопаровая полость с высоким давлением. Как правило, КПД процесса выше, чем при разряде в жидкости. Объем взрываемой проволоки должен быть пропорциональным энергии, накопленной в конденсаторах.
Нанесение покрытий электрическим взрывом проводника. Данная разновидность электровзрывной обработки осуществляется в вакууме взрывом проволоки или фольги, изготовленной из электропроводного материала, которым покрывают изделие.
Физические процессы в разрядной цепи и электропроводной перемычке протекают аналогично электрическому взрыву электропроводных материалов в жидкости. В течение очень короткого времени электропроводный материал переходит в расплавленное состояние. Жидкая перемычка сохраняется благодаря силам отдачи паров, поверхностному натяжению и действию магнитного поля. Иногда происходит электрический разряд вдоль испарившейся проволоки. Тогда разрядный ток падает и затрудняется или вообще становится невозможным взрыв проводника. Такое явление характерно для тугоплавких веществ, например вольфрама.
Электрический нагрев поверхностных слоев проволоки приводит к плавлению, взрывному испарению и разлету частиц наносимого вещества. Для получения необходимой плотности потока частиц необходимо, чтобы плотность разрядного тока была выше некоторого определенного значения. В противном случае проволока лишь нагревается и распадается на крупные капли расплава.
Экспериментально получено, что диаметр частиц, на которые распадается проволока, составляет 10-9...10-5 м. Крупные капли возникают при распылении расплава, мелкие после конденсации пара или дробления более крупных частиц. С ростом энергии взрыва и скорости ее ввода в проволоку размер частиц уменьшается.
Для получения хороших покрытий необходимо подобрать оптимальное расстояние от проволоки до поверхности изделия. Если расстояние слишком велико, то наносимое вещество охлаждается и качество покрытия снижается; если оно мало, то покрытие будет неравномерным по толщине.
Образование покрытия происходит благодаря осаждению на поверхности изделия большого количества частиц. При ударе о поверхность изделия возможны кавитация внутри капель и их вспучивание. Обычно капли расплющиваются, по краям образуется небольшой валик. Иногда крупные частицы разбрызгиваются или вскипают, что ухудшает качество покрытия.
Соприкасаясь с заготовкой, частицы привариваются к ее поверхности. Кинетическая энергия частицы преобразуется в теплоту и энергию поверхностных волн, активирующих окружающий участок поверхности изделия. Оценки показывают, что одна частица накладывается на другую примерно через 10-5 с. Покрытие толщиной до 15 мкм образуется за 10-4 с. Средняя толщина покрытия определяется объемом распыляемого материала:
Hп=πd2прlпр/(4Sизд)
где dпp и lпр - соответственно диаметр и длина распыляемой проволоки; Sизд - площадь покрываемой поверхности. Данным методом нельзя получить сплошные зеркально-гладкие покрытия. Прочность сцепления довольно высокая, например, для вольфрамовых покрытий со стальной подложкой она составляет около 240 МПа, а с медью 100 МПа. Пористость покрытия невелика, а содержание кислорода в нанесенном слое незначительно.
Электровзрывная обработка: штамповка. Одна из схем технологического процесса листовой штамповки электрическим разрядом представлена на рис. 54.
Рис. 54. Схема технологического процесса листовой штамповки электрическим разрядом
В камере 1 установлены изолированные электроды 2. Камеру 1 герметизируют от заготовки 8 резиновой прокладкой 9 Заготовку 8, прокладку 9 и камеру 1 крепят к матрице 10 и камере 11. При подаче напряжения от конденсаторной батареи на электроды 2, в жидкости 3 происходит электрический разряд. Механическое усилие через резиновую прокладку 9 передается на заготовку 8, которая прилегает к стенкам матрицы 10, образуя деталь 13 (на рисунке показана пунктиром)
Для удаления газа, возникающего после разряда, служит ресивер 6 Канал 5, соединяющий рабочую камеру 1 с ресивером 6, имеет криволинейную ось, чтобы погасить ударную волну. С помощью крана 7 накопившийся газ периодически удаляют. При отражении ударной волны в камере 1 могут образовываться кавитационные полости, что снижает общее усилие деформации.
Для устранения кавитации в камеру 1 по каналу 4, который также выполнен с криволинейной осью, под давлением нагнетают рабочею жидкость. Ее можно также вводить периодически, согласуя во времени с разрядом.
При деформации скорость перемещения заготовки v3 100 м/с. Воздух в пространстве между заготовкой и матрицей не успевает вытесняться через технологические отверстия 12 и создает противодавление, препятствующее плотному прилеганию заготовки 8 к матрице 10. Для повышения точности обработки воздух из камеры 11 откачивают вакуумным насосом. При штамповке особо точных деталей матрицу изготовляют из мелкопористого материала или создают на ее поверхности повышенную шероховатость.
Межэлектродный промежуток может располагаться как горизонтально, так и вертикально. Во втором случае одним из электродов обычно служит сама заготовка. При обработке крупных заготовок штамповка одним разрядом нецелесообразна, так как при этом необходимы мощные и громоздкие электрические устройства. Для обработки больших заготовок в различных местах камеры размещают несколько пар электродов или передвигают одну пару электродов вдоль поверхности заготовки. При первом способе возможна одновременная обработка всей заготовки благодаря сразу нескольким разрядам, при втором - обработка ведется последовательными разрядами.
Деформация заготовки - процесс инерционный, т. е. деформация продолжается и после непосредственного воздействия на нее ударной волны. Это явление используют, включая последовательно несколько пар электродов по заданной программе. В местах значительных деформаций следует предусмотреть либо многократные разряды, либо повысить энергию одного разряда.
Известна также электрогидравлическая штамповка экструзией. Для этой цели несколько пар электродов располагают в пространстве последовательно. Если разряды в них возникают также последовательно с небольшой задержкой, то в камере можно получить высокое давление. Заготовку помещают за последними электродами в ресивере, в котором имеется фильера с выходом в атмосферу. Благодаря высокому давлению в ресивере возможно экструзионное выдавливание металла заготовки через отверстие фильеры.
Электровзрывная обработка: очистка изделий. Очистка изготовленных деталей - одна из самых распространенных операций в технологии машиностроения. Использование электрогидравлической очистки значительно повышает производительность этой операции для многих видов изделий.
В известных способах очистки, например литья, - гидропескоструйной, дробеструйной, дробеметной и др. - очень трудно добиться полной автоматизации процесса. С этой точки зрения при очистке литых деталей сложного профиля из высокопрочных материалов преимущества электрогидравлической очистки проявляются в полной мере.
Принцип электрогидравлической очистки изделий поясняется рис. 55. На основании 5 установлена ванна 4, в которой размещена решетка 6 с заготовками 7. Над ними по траверсе 3 перемещается тележка 2 с электродом 1. В нижней части ванны 4 расположен транспортер 8. На нем осаждаются частицы 9, удаленные с поверхности заготовок в результате разрядов, а затем извлекаются из ванны 4. Корпус ванны заземлен, и разряды возникают между заготовками 7 и электродом 1. Как и при штамповке, в данном случае можно использовать как один электрод, перемещаемый по заданному пути над ванной, так и несколько электродов, расположенных над заготовками 7.
Рис. 55. Схема электрогидравлической очистки
При использовании одного электрода необходимо поддерживать постоянную высоту его расположения над заготовками, так как от нее зависят параметры разряда, а, следовательно, и качество очистки изделий. Обычно для этого применяют механические копиры, с помощью которых электроды перемещаются в зависимости от изменения положения обрабатываемых поверхностей заготовок. Площадь поверхности заготовки, надежно очищаемая одним разрядом, обычно ограничена окружностью диаметром 150...400 мм. Поэтому необходимо согласовывать время между разрядами с расстоянием, пройденным электродом. Если очистку проводят несколькими электродами, то их устанавливают на расстоянии 300... 400 мм друг от друга.
Как показывает опыт, электрогидравлическую очистку лучше всего выполнять сразу после литья. Заготовки в опоках поступают в установку для очистки. Под действием разрядов формовочная земля отделяется от опок и литья и вместе со стержневыми составами выпадает через решетку 6 на транспортер 8 (рис. 55).
Электровзрывная обработка: Получение неразъемных соединений. Электрогидравлическую обработку используют для развальцовки, обжатия и в других подобных технологических операциях. Это позволяет механизировать наиболее массовые операции, ранее производимые вручную.
Чтобы улучшить рабочие свойства теплообменников, их изготовляют из высоколегированных сталей, плохо поддающихся сварке. Для крепления труб в трубных решетках стали применять электрогидравлическую запрессовку. Процесс осуществляют с помощью специальных патронов одно- или многоразового действия. На рис. 56 приведена схема запрессовки с патроном одноразового действия.
Внутри герметизированной резиновой трубки 1 установлены два электрода 2. Пространство между ними заполнено рабочей жидкостью 3, Патрон вставляют внутрь трубы 4, помещенной в трубной решетке 5.
Рис. 56. Схема запрессовки с патроном одноразового действия
Для повышения качества запрессовки необходимо соблюдать ряд условий:
- диаметральный зазор между внутренней поверхностью трубы и наружной поверхностью патрона не должен составлять более 4% внутреннего диаметра трубы;
- длина гильзы патрона равна или немного меньше длины запрессовки (толщины трубной решетки);
- зазор между трубой и стенкой отверстия в решетке не должен превышать 2% наружного диаметра трубы;
соединяемые поверхности должны быть тщательно зачищены и обезжирены.
Для операции обжатия взрывающуюся проволоку спирально наматывают на изолированную поверхность цилиндрической заготовки, предварительно покрытую, например, лаком. Шаг намотки и размеры проволоки выбирают так, чтобы необходимую деформацию заготовки получить за один разряд. При подаче импульсного напряжения проволока взрывается и деталь обжимает основу. При электрогидравлической запрессовке прочность соединений на 20... 30% выше, чем при запрессовке механическим способом. По сравнению с механической запрессовкой производительность повышается в 30 раз, во столько же раз уменьшается расход энергии. Себестоимость операции снижается в 2,5 раза.
Электровзрывной обработкой можно исправлять бракованные изделия: восстанавливать раздачей размеры изношенного поршневого пальца, править помятости на заготовке, помещаемой в контрольную форму, и т. д.
Электровзрывная обработка: Дробление материалов. Электрогидравлическое дробление применяют для измельчения только хрупких материалов. Известно два способа обработки: внешним или внутренним разрядами. При внешнем разряде один электрод устанавливают над размельчаемым материалом, который служит вторым электродом. При подаче импульсного напряжения происходит разряд, механическое действие которого приводит к раскалыванию частиц материала. При многократных разрядах материал постепенно измельчается и проваливается через сетчатое дно. Размером ячеек сетки задается степень измельчения.
При внутреннем разряде в измельчаемом теле просверливают отверстия, в которые вводят электроды (или один электрод, если вторым является заготовка). Дробление происходит вследствие разрядов в объеме самого тела.
Если необходимо измельчать куски металла, то их можно смешать с каким-нибудь вязким неэлектропроводным материалом, например с пластмассой, в объемном соотношении 1:5. В результате действия разрядов разрушаются преимущественно куски металла, которые затем отделяются от вязкого наполнителя благодаря разнице плотностей.
На показатели процесса дробления существенно влияет частота следования разрядов. При большой частоте снижается КПД процесса, поскольку свойства рабочей среды не успевают восстанавливаться. Если рабочая среда в зоне обработки не сменяется, то оптимальная частота следования разрядов fопт=15...25 Гц. При подаче свежей рабочей среды оптимальная частота разрядов выше. На степень измельчения влияет скорость поступления материала в рабочую зону. Избыток исходного материала приводит к его уплотнению, но не к измельчению.
При электрогидравлическом дроблении у измельченных частиц остаются острые края, возникающие при хрупком раскалывании более крупных кусков. Так, бетон, полученный на щебне, который измельчен на электрогидравлической установке, обладает повышенной прочностью. Абразив после электрогидравлической обработки не имеет плоских и игольчатых зерен, что улучшает его технологические свойства.
При электрогидравлическом дроблении зона обработки занимает небольшой объем. Поэтому можно использовать оборудование, не отличающееся высокой прочностью к ударным нагрузкам. Благодаря этому оборудование отличается простотой и низкой металлоемкостью.
Производительность электрогидравлического дробления мелких фракций достигает 450 кг/ч, крупных - до 2,5 т/ч. При этом средний расход энергии составляет 10...200 кВт-ч/т в зависимости от свойств исходного материала.
История развития хранилищ для нефти: Первые склады нефти появились в XVII веке. Они представляли собой землянные ямы-амбара глубиной 4…5 м...
Папиллярные узоры пальцев рук - маркер спортивных способностей: дерматоглифические признаки формируются на 3-5 месяце беременности, не изменяются в течение жизни...
Кормораздатчик мобильный электрифицированный: схема и процесс работы устройства...
Механическое удерживание земляных масс: Механическое удерживание земляных масс на склоне обеспечивают контрфорсными сооружениями различных конструкций...
© cyberpedia.su 2017-2024 - Не является автором материалов. Исключительное право сохранено за автором текста.
Если вы не хотите, чтобы данный материал был у нас на сайте, перейдите по ссылке: Нарушение авторских прав. Мы поможем в написании вашей работы!