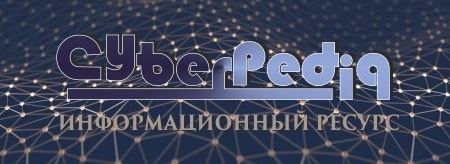
Особенности сооружения опор в сложных условиях: Сооружение ВЛ в районах с суровыми климатическими и тяжелыми геологическими условиями...
Типы оградительных сооружений в морском порту: По расположению оградительных сооружений в плане различают волноломы, обе оконечности...
Топ:
Эволюция кровеносной системы позвоночных животных: Биологическая эволюция – необратимый процесс исторического развития живой природы...
Особенности труда и отдыха в условиях низких температур: К работам при низких температурах на открытом воздухе и в не отапливаемых помещениях допускаются лица не моложе 18 лет, прошедшие...
Характеристика АТП и сварочно-жестяницкого участка: Транспорт в настоящее время является одной из важнейших отраслей народного хозяйства...
Интересное:
Финансовый рынок и его значение в управлении денежными потоками на современном этапе: любому предприятию для расширения производства и увеличения прибыли нужны...
Как мы говорим и как мы слушаем: общение можно сравнить с огромным зонтиком, под которым скрыто все...
Мероприятия для защиты от морозного пучения грунтов: Инженерная защита от морозного (криогенного) пучения грунтов необходима для легких малоэтажных зданий и других сооружений...
Дисциплины:
![]() |
![]() |
5.00
из
|
Заказать работу |
|
|
Понятие о взрыве и взрывчатых веществах
Взрывчатыми веществами (ВВ) называются вещества, способные под влиянием внешнего воздействия к чрезвычайно быстрому химическому превращению с выделением тепла и образованием сильно нагретых газов. Процесс такого химического превращения взрывчатого вещества называется взрывом.
Для взрыва характерны три основных фактора, которые определяют действие, производимое взрывом:
• очень большая скорость превращения взрывчатого вещества, измеряемая промежутком времени от сотых до миллионных долей секунды;
• высокая температура, достигающая 3–4,5 тыс. градусов;
• образование большого количества газообразных продуктов, которые, сильно нагреваясь и быстро расширяясь, превращают выделяющуюся при взрыве тепловую энергию в механическую работу, производя разрушения или разбрасывание окружающих заряд предметов.
Совокупностью указанных факторов и объясняется огромная, по сравнению с другими источниками энергии, кроме атомной, мощность взрывчатых веществ. При отсутствии хотя бы одного из перечисленных факторов взрыва не будет.
Для возбуждения взрыва необходимо воздействовать на взрывчатое вещество извне, сообщить ему некоторую порцию энергии, величина которой зависит от свойств взрывчатого вещества. Взрыв могут вызвать различные виды внешнего воздействия: механический удар, накол, трение, нагревание (пламенем, накаленным телом, искрой), электрическое накаливание или искровой разряд, химическая реакция и, наконец, взрыв другого взрывчатого вещества (капсюлем-детонатором, детонацией на расстоянии).
Основные формы взрывчатого превращения.
Взрывчатое превращение веществ характеризуется тремя показателями: экзотермичностью процесса (выделением тепла); скоростью распространения процесса (кратковременность) и образованием газообразных продуктов.
|
Экзотермичность процесса взрыва является первым необходимым условием, без которого невозможно возникновение и проявление взрыва. За счет тепловой энергии реакции происходит разогрев газообразных продуктов до температуры в несколько тысяч градусов, их сильное сжатие в объеме взрывчатого вещества и последующее активное расширение.
Образование большого количества газообразных и парообразных продуктов реакции обеспечивает создание в локальном объеме высокого давления и обусловленного им разрушительного эффекта. Вследствие нагревания до высокой температуры (3500 – 4000К) продукты взрыва оказываются в чрезвычайно сжатом состоянии (давление при взрыве достигает (20…40)*103 МПа) и способны разрушить очень прочные преграды. В процессе расширения продуктов взрыва осуществляется быстрый переход потенциальной химической энергии ВВ в механическую работу или в кинетическую энергию движущихся частиц
Быстрым сгоранием взрывчатого вещества обычно называют процесс, скорость распространения которого по массе ВВ не превышает нескольких метров в секунду, а иногда - даже долей метра в секунду. Характер действия в этом случае - более или менее быстрое нарастание давления газов и производство ими работы разбрасывания или метания окружающих тел. Если процесс быстрого сгорания происходит на открытом воздухе, то он не сопровождается сколько-нибудь значительным эффектом
Классификация ВВ.
Все ВВ, применяемые при производстве подрывных работ и снаряжении различных боеприпасов делятся на три основные группы:
· инициирующие;
· бризантные;
· метательные (пороха).
· ПС
ИНИЦИИРУЮЩИЕ - особо восприимчивые к внешним воздействиям (удару, трению, воздействию огня). К ним относятся:
· гремучая ртуть (фульминат ртути);
· азид свинца (азотистоводороднокислый свинец);
|
· тенерес (тринитрорезорцинат свинца, ТНРС);
БРИЗАНТНЫЕ (дробящие) - способные к устойчивой детонации. Они более мощны и менее чувствительны к внешним воздействиям и в свою очередь подразделяются на:
ВВ ПОВЫШЕННОЙ МОЩНОСТИ, к которым относятся:
· тэн (тетранитропентраэритрит, пентрит);
· гексоген (триметилентринитроамин);
· тетрил (тринитрофенилметилнитроамин).
ВВ НОРМАЛЬНОЙ МОЩНОСТИ:
· тротил (тринитротолуол, тол, ТНТ);
· пикриновая кислота (тринитрофенол, мелинит);
· ПВВ-4 (пластит-4);
ВВ ПОНИЖЕННОЙ МОЩНОСТИ (амиачноселитренные ВВ):
· аммониты;
· динамоны;
· аммоналы.
МЕТАТЕЛЬНЫЕ (пороха) - ВВ, основной формой взрывчатого превращения которых является горение. К ним относятся: - дымный порох; - бездымные пороха.
Пиротехнический состав — это смесь компонентов, обладающая способностью к самостоятельному горению или горению с участием окружающей среды, генерирующая в процессе горения газообразные и конденсированные продукты, тепловую, световую и механическую энергию и создающая различные оптические, электрические, барические и иные специальные эффекты
Классификация ПС. Требования к ПС.
КЛАССИФИКАЦИЯ
Пиротехническими составами снаряжают следующие виды средств военного назначения:
1) осветительные средства (авиабомбы, артиллерийские снаряды, авиационные факелы и др.), используемые для освещения местности в ночных условиях;
2) фотоосветительные средства (фотобомбы, фотопатроны), используемые при ночной аэрофотосъемке: и для других целей;
3) трассирующие средства, делающие видимой траекторию полета пуль и снарядов (и других подвижных объектов) и тем самым облегчающие пристрелку по быстро движущимся целям;
4) средства инфракрасного излучения, используемые для слежения за полетом ракет и в качестве ложных целей;
5) ночные сигнальные средства (патроны и др.), применяемые для подачи сигналов;
6) дневные сигнальные средства (патроны и др.), используемые для той же цели, но в дневных условиях;
7) зажигательные средства (бомбы, снаряды, пули и многие Др.), служащие для уничтожения военных объектов противника;
8) маскирующие средства (дымовые шашки, снаряды и др.), употребляемые для получения дымовых завес;
9) ракеты различного назначения и дальности полета, использующие твердое пиротехническое топливо;
|
10) учебно-имитационные средства, употребляемые как на маневрах и ученьях, так и в боевой обстановке. Они имитируют действие атомных бомб, фугасных снарядов и бомб, а также различные явления на поле боя: орудийные выстрелы, пожары и др., и могут этим дезориентировать службу наблюдения противника;
11) целеуказательные средства (снаряды, бомбы и др.), указывающие местонахождение объектов противника;
12) пиротехнические газогенераторы, используемые для различных целей. Пиротехнические составы используются также и в различных областях народного хозяйства
К пиротехническим составам военного назначения можно отнести следующие:
1) осветительные;
2) фотоосветительные (фотосмеси);
3) трассирующие;
4) инфракрасного излучения;
5) зажигательные;
6) ночных сигнальных огней;
7) цветных сигнальных дымов;
8) маскирующих дымов;
9) твердое пиротехническое топливо;
10) безпазовые (для замедлителей);
11) газогенерирующие;
12) воспламенительные, содержащиеся в небольшом количестве во всех пиротехнических средствах;
13) прочие: имитационные, свистящие и др. Многие составы применяются в самых различных видах средств; так, например, осветительные составы часто используют в трассирующих средствах; составы маскирующих дымов могут быть использованы и в учебно-имитационных средствах и т. д.
Пиротехнические составы можно также классифицировать по характеру процессов, протекающих три их горении.
Пламенные составы
1. Белопламенные.
2. Цветнолламенные.
3. Составы инфракрасного излучения.
Тепловые составы
1. Термитно-зажигательные.
2. Безгазовые (малогазовые).
Дымовые составы
1. Белого и черного дыма.
2. Цветного дыма.
Вещества и смеси, сгорающие за счет кислорода воздуха
1. Металлы и сплавы металлов.
2. Фосфор, его растворы и сплавы.
3. Смеси нефтепродуктов.
4. Различные вещества и смеси, загорающиеся при соприкосновении с водой или воздухом.
ТРЕБОВАНИЯ, ПРЕДЪЯВЛЯЕМЫЕ К ПИРОТЕХНИЧЕСКИМ СРЕДСТВАМ И СОСТАВАМ
Основное требование - это получение при действии пиротехнического средства максимального специального эффекта. Для различных средств специальный эффект обуславливается различными факторами. Этот вопрос подробно разбирается при описании свойств отдельных категорий составов и средств. Здесь же приводится только несколько примеров.
|
Для трассирующих средств, специальный эффект определяется хорошей видимостью полета пули или снаряда. Видимость, в свою очередь, определяется силой света пламени и зависит также от цвета пламени.
Для зажигательных средств хороший специальный эффект обуславливается (при наличии подходящей конструкции боеприпасов) созданием достаточно большого очага пожара, высокой температурой пламени, достаточным временем горения состава, а также количеством и свойствами шлаков, получающихся при горении.
Для маскирующих дымовых средств, специальный эффект определяется созданием возможно большей, густой и устойчивой дымовой завесы.
Пиротехнические средства не должны представлять опасности при обращении с ними и хранении. Получаемый при их действии эффект не должен ухудшаться после длительного хранения.
Материалы, используемые для изготовления пиротехнических средств, должны быть по возможности недефицитны. Технологический процесс изготовления должен быть простым, безопасным и допускающим механизацию и автоматизацию производства.
Пиротехнические составы должны обладать следующими качествами: 6
1) давать максимальный специальный эффект при минимальном расходовании состава;
2) иметь по возможности большую плотность (и в порошкообразном, и в прессованном виде);
3) сгорать равномерно с определенной скоростью;
4) обладать химической и физической стойкостью при длительном хранении;
5) иметь возможно меньшую чувствительность к механическим импульсам;
6) не быть чрезмерно чувствительными к тепловым воздействиям (не воспламеняться при небольшом подъеме температуры, при попадании искры и т. п.);
7) иметь минимальные взрывчатые свойства; редкие случаи, когда наличие взрывчатых свойств необходимо, будут оговорены ниже;
8) иметь несложный технологический процесс изготовления;
9) не содержать в себе компонентов, оказывающих токсическое действие на человеческий организм.
ИВВ. Общая характеристика
Инициирующие ВВ - это такие взрывчатые вещества, которые характеризуются чрезвычайно высокой чувствительностью к простым видам начального импульса и способностью детонировать в весьма малых количествах.
Когда скорость детонации ИВВ достигает максимального значения, скорость детонации БВВ значительно меньше скорости детонации ИВВ. Позднее, когда скорость детонации БВВ достигает максимальной величины, соотношение энергии изменяется в пользу БВВ, так как скорость детонации БВВ выше, чем у ИВВ. Ускорение взрывчатого превращения зависит от природы ИВВ, величины начального импульса, плотности заряда и плотности его оболочки.
|
Поэтому ИВВ применяются для инициирования (возбуждения) процессов взрыва разрывных зарядов или горения метательных и ракетных зарядов. В соответствии с этим назначением ИВВ часто называют первичными.
Все ИВВ делятся на индивидуальные и смесевые инициирующие смеси. Индивидуальные ИВВ представлены различными классами неорганических соединений. Из всего многообразия классов лишь немногие получили широкое применение в качестве ИВВ. К ним относятся фульминаты (соли гремучей кислоты), азиды (соли азотистоводородной кислоты), стифнаты или тринитрорезорцинаты (соли стифниновой кислоты или тринитрорезорцина), производственные тетразена.
Получение
Гремучую ртуть получают взаимодействием нитрата ртути с этанолом в разбавленной азотной кислоте. Реакция протекает по схеме:
Свойства
Белый или серый кристаллический порошок, нерастворим в воде. Имеет сладкий металлический вкус, ядовит. Насыпная плотность 1,22-1,25 г/см³. Теплота разложения 1,8 МДж/кг. Температура вспышки — 180 °C. Нижний предел чувствительности при падении груза 700 г — 5,5 см, верхний — 8,5 см. Гравиметрическая плотность 4,39 г/см³. Легко взрывается при ударе, действии пламени, раскалённого тела и т. п. При осторожном нагревании гремучая ртуть медленно разлагается. При 130—150 °C самовоспламеняется со взрывом. Влажная гремучая ртуть гораздо менее взрывоопасна. Влажность гремучей ртути, запрессованной в капсюль-детонатор, должна быть не более 0,03 %. Гремучая ртуть хорошо растворима в водных растворах аммиака или цианистого калия. Концентрированная серная кислота вызывает взрыв одной каплей. Температура взрыва гремучей ртути равна 4810 °C, объём газов 315 л/кг, скорость детонации 5400 м/сек.
Гремучую ртуть получают при действии азотнокислой ртути и азотной кислоты на этиловый спирт. Применяют в капсюлях-детонаторах и капсюлях-воспламенителях. В последнее время гремучая ртуть вытесняется более эффективными инициирующими взрывчатыми веществами — азидом свинца и др.
Свойства азид свинца
· Теплота взрыва: около 1,536 МДж/кг (7,572 МДж/дм³).
· Объем газов: 308 л/кг (1518 л/дм³)
· Скорость детонации: около 4800 м/сек.
Получение
Синтез азида свинца осуществляется в ходе обменной реакции между растворами солей свинца и растворимыми азидами щелочных металлов. Азид свинца в результате выпадает в виде белого кристаллического осадка:
Реакцию рекомендуется проводить с добавлением декстрина, глицерина, желатина или подобных веществ, препятствующих формированию крупных кристаллов азида свинца и уменьшающих опасность детонации.
Получение
Получают нейтрализацией горячего водного раствора стифниновой кислоты гидрокарбонатом натрия и последующим взаимодействием образовавшегося стифната натрия с соответствующими растворимыми солями свинца (напр. ацетатом, нитратом или хлоридом) при температуре около 70 °C.
· С6H(OH)2(NO2)3 + NaHCO3 → C6H(NO2)3(ONa)2 + CO2↑ + H2O
· C6H(NO2)3(ONa)2 + PbCl2 → C6H(NO2)3(O)2Pb + NaCl
· Тетразе́н — химическое соединение C2H6N10·H2O. Моногидрат 5-(4-амидино-1-тетразено)тетразола.
· Желтоватые клиновидные кристаллы. В насыпном виде представляет собой рыхлую кристаллическую массу с насыпной плотностью 0,45 г/см³. Почти не растворим в воде (0,02 г на 100 г воды при 22 °C) и в органических растворителях. Обладает сильными взрывчатыми свойствами.
· Инициирующее взрывчатое вещество, используемое в капсюлях накольного действия как сенсибилизатор (увеличитель чувствительности) к азиду свинца или тринитрорезорцинату свинца.
Свойства
· Плотность кристаллов 1,685 г/см³
· Теплота взрыва 2305 кДж/кг
· Температура вспышки 140 °C
· Объем газообразных продуктов взрыва 400—450 л/кг
Получение
Получают тетразен взаимодействием водных растворов нитрата или карбоната аминогуанидина NH2NHC(=NH)NH2 с нитритом натрия NaNO2.
БВВ. Классификация
Бризантные ВВ менее чувствительны к внешним воздействиям, но обладают большей мощностью, чем инициирующие ВВ. Они служат для получения разрушительного действия взрыва. Бризантные ВВ применяются в чистом виде, а также в виде смесей друг с другом для производства подрывных работ, снаряжения авиационных, артиллерийских и инженерных боеприпасов.
Бризантные ВВ подразделяются на:
· ВВ повышенной мощности (гексоген, ТЭН, сплавы тротила с гексогеном, октоген, тетрил);
· ВВ нормальной мощности (тротил, сплавы тротила с ксилитом, динамиты, пироксилин, пластические и эластичные ВВ);
· ВВ пониженной мощности (аммиачная селитра, смеси аммиачной селитры с горючими или взрывчатыми веществами).
Для сравнительной оценки взрывчатых свойств различных ВВ может быть использован тротиловый эквивалент, численно равный отношению теплоты взрывчатого превращения сравниваемого ВВ с аналогичной характеристикой тротила. Наиболее мощным ВВявляется октоген, тротиловый эквивалент которого равен 1,8.
ТЭН.
Физические свойства
· Плотность: 1773 кг/м³
· Температура плавления 140 °C, с разложением
· Температура вспышки 215 °C,
· Растворим в ацетоне, нерастворим в воде.
Взрывчатые свойства
· Более чувствителен к удару, чем гексоген,
· Скорость детонации 8350 м/сек.
· Теплота разложения 5756 кДж/кг[1]
· Бризантность
· по Гессу 24 мм
· по Касту 3,5 мм
· Фугасность 500 мл
· (Удельный) объём газообразных продуктов взрыва 790 л/кг
· Критический диаметр 1,5 мм
· тэн относительно стоек в химическом отношении
· Стабильность при хранении выше, чем у гексогена
· При температуре 215 °C взрывается.
· Тротиловый эквивалент (RE) — 1.66
Все величины сильно зависят от условий эксперимента: плотности заряда, материала оболочки, дисперсности взрывчатого вещества, наличия флегматизаторов и т. п.
Получение
Получают путём взаимодействия четырёхатомного спирта пентаэритрита с концентрированными азотной и серной кислотами.
ТЕТРИЛ.
ТРОТИЛ
Физические свойства
· Плотность: от 1500 кг/м³ до 1663 кг/м³
· Температура плавления 80,85 °C
· Температура кипения 295 °C
· Температура вспышки 290 °C
· Теплота взрыва — от 4103 кДж/кг до 4605 кДж/кг (в среднем 4184 кДж/кг)
· Скорость детонации при плотности 1,64 — 6950 м/с
· Бризантность по Гессу — 16 мм
· Бризантность по Касту — 3,9 мм
· Фугасность — 285 мл
· Объем газообразных продуктов взрыва — 730 л/кг
· Имеет невысокую чувствительность к удару (4—8 % взрывов при падении груза 10 кг с высоты 25 см)[2].
· Срок хранения около 25 лет, после чего тротил становится более чувствительным к детонации.
Получение[править | править вики-текст]
Первый этап: нитрование толуола смесью азотной и серной кислот до моно- и динитротолуолов. Серная кислота используется как водоотнимающий агент.
Второй этап: смесь моно- и динитротолуола нитруют в смеси азотной кислоты и олеума. Олеум используется как водоотнимающий агент.
Излишек кислоты от второго этапа можно использовать для первого
Физические свойства
Гексоген — белый кристаллический порошок. Без запаха, вкуса, сильный яд. Удельный вес — 1,816 г/см³, молярная масса — 222,12 г/моль. Нерастворим в воде, плохо растворим в спирте, эфире, бензоле, толуоле, хлороформе, лучше — в ацетоне, ДМФА, концентрированной азотной и уксусной кислотах. Разлагается серной кислотой, едкими щелочами, а также при нагревании.
Плавится гексоген при температуре 204,1 °C с разложением, при этом его чувствительность к механическим воздействиям сильно повышается, поэтому его не плавят, а прессуют. Прессуется плохо, поэтому, чтобы его лучше спрессовать, гексоген флегматизируют в ацетоне.
Получение
Метод Герца (1920) заключается в непосредственном нитровании гексаметилентетрамина (уротропина, (CH2)6N4) концентрированной азотной кислотой (HNO3):
{\displaystyle \mathrm {(CH_{2})_{6}N_{4}+3HNO_{3}\longrightarrow \ (CH_{2})_{3}N_{3}(NO_{2})_{3}+3HCOH+NH_{3}} }
Производство гексогена по этому методу велось в Германии, Англии и других странах на установках непрерывного действия. Метод имеет ряд недостатков, главные из которых:
· малый выход гексогена по отношению к сырью (35-40 %);
· большой расход азотной кислоты.
Октоген (1,3,5,7-тетранитро-1,3,5,7-тетраазациклооктан, циклотетраметилентетранитрамин, HMX) — (CH2)4N4(NO2)4, термостойкое бризантное взрывчатое вещество. Впервые был получен как побочный продукт процесса получения гексогена конденсацией нитрата аммония с параформом в присутствии уксусного ангидрида. Представляет собой белый порошок кристаллического характера. Ядовит.
Физические свойства
· Плотность: 1960 кг/м³
· Температура плавления 278,5—280 °С (с разложением)
· Температура вспышки 290°С
Взрывчатые свойства
· Обладает высокой чувствительностью к удару.
· Скорость детонации 9100 м/с при плотности 1,84 г/см³.
· Объём газообразных продуктов взрыва 782 л/кг.
· Теплота взрыва 5,7 МДж/кг.
· Фугасность 480 мл
· Тротиловый эквивалент 1,7
Получение
Получают действием концентрированной азотной кислоты на уротропин в растворе уксусной кислоты, уксусного ангидрида и нитрата аммония в растворе азотной кислоты.
Пороха. Основные виды.
По́рох — многокомпонентная твёрдая взрывчатая смесь, способная к закономерному горению параллельными слоями без доступа кислорода извне с выделением большого количества тепловой энергии и газообразных продуктов, используемых для метания снарядов, движения ракет и в других целях[1]. Его относят к классу метательных взрывчатых веществ. И ещё порох находится в пуле.
Виды порохов
Различают два вида пороха: смесевые (в том числе самый распространенный — дымный, или черный порох) и нитроцеллюлозные (т. н. бездымные). Порох, применяемый в ракетных двигателях, называют твёрдым ракетным топливом. Основу нитроцеллюлозных порохов составляют нитроцеллюлоза и пластификатор. Помимо основных компонентов, эти пороха содержат различные добавки.
Порох является взрывчатым веществом метательного действия. При соответствующем условии инициирования пороха способны к детонации аналогично бризантным взрывчатым веществам, благодаря чему дымный порох долгое время применяли в качестве бризантного взрывчатого вещества. При длительном хранении больше установленного для данного пороха срока или при хранении в ненадлежащих условиях происходит химическое разложение компонентов пороха и изменение его эксплуатационных характеристик (режима горения, механических характеристик ракетных шашек и др.). Эксплуатация и даже хранение таких порохов крайне опасны и могут привести к взрыву.
Современные дымные, или чёрные пороха производятся по строгим нормативам и точной технологии. Все марки чёрного пороха делятся на зернистые и пороховую пудру (т. н. пороховая мякоть, ПМ). Основными компонентами дымного пороха являются калия нитрат, сера и древесный уголь; нитрат калия является окислителем (способствует быстрому горению), древесный уголь горючим (окисляемым окислителем), а сера — добавочным компонентом (так же, как и уголь, являясь топливом в реакции, она из-за невысокой температуры воспламенения улучшает поджигаемость). Во многих странах пропорции, установленные нормативами, несколько отличаются (но не сильно).
Зернистые пороха изготовляются в виде зёрен неправильной формы в пять стадий (не считая сушки и дозирования): помол компонентов в пудру, их смешение, прессование в диски, дробление на гранулы и полировка.
Эффективность горения дымного пороха во многом связана с тонкостью измельчения компонентов, полнотой смешения и формой зёрен в готовом виде.
Сорта дымных порохов (% состав KNO3, S, C.):
· шнуровой (для огнепроводных шнуров)(77 %, 12 %, 11 %);
· ружейный (для воспламенителей к зарядам из нитроцеллюлозных порохов и смесевых твёрдых топлив, а также для вышибных зарядов в зажигательных и осветительных снарядах);
· крупнозернистый (для воспламенителей);
· медленногорящий (для усилителей и замедлителей в трубках и взрывателях);
· минный (для взрывных работ) (75 %, 10 %, 15 %);
· охотничий (76 %, 9 %, 15 %);
· спортивный.
Дымный порох легко воспламеняется под действием пламени и искры (температура вспышки 300 °C), поэтому в обращении опасен. Хранится в герметической упаковке отдельно от других видов пороха. Гигроскопичен, при содержании влаги более 2 % плохо воспламеняется. Процесс производства дымных порохов предусматривает смешение тонкоизмельчённых компонентов и обработку полученной пороховой мякоти до получения зёрен заданных размеров. Коррозия стволов при использовании дымного пороха намного сильнее, чем от нитроцеллюлозных порохов, поскольку побочным продуктом сгорания является серная и сернистая кислоты. В настоящее время дымный порох используется в фейерверках. Примерно до конца XIX века применялся в огнестрельном оружии и взрывных боеприпасах.
Нитроцеллюлозные пороха
Порох был первым известным «топливом» для огнестрельного оружия и ракет. В отличие от долгое время использовавшегося дымного (чёрного) пороха на основе угля, сегодня получили широкое распространение нитроцеллюлозные пороха, так называемый бездымный порох; главным преимуществом этого вида пороха является бо́льший КПД и отсутствие дыма, мешающего обзору после выстрела.
По составу и типу пластификатора (растворителя) нитроцеллюлозные пороха делятся на: пироксилиновые, баллиститные и кордитные. Они применяются для изготовления современных взрывчатых веществ, порохов, пиротехнических изделий и для подрыва (инициирования) других взрывчатых веществ, то есть в качестве детонаторов. Таким образом, в современных образцах вооружения в качестве топлива в основном используют бездымный порох (порошок нитроцеллюлозы, NC).
ДРП, свойства и получение.
Выстрел унитарного заряда
Свойства порохов.
Литье: виды,применение
Литьё — заполнение чего-либо (формы, ёмкости, полости) материалом, находящимся в жидком агрегатном состоянии.
Известно множество разновидностей литья:
· в песчаные формы (ручная или машинная формовка);
· в многократные (цементные, графитовые, асбестовые формы);
· в оболочковые формы;
· по выплавляемым моделям;
· по замораживаемым ртутным моделям;
· центробежное литье;
· в кокиль;
· литьё под давлением;
· по газифицируемым (выжигаемым) моделям;
· вакуумное литьё;
· электрошлаковое литьё;
· литьё с утеплением.
Так как разновидности литья различаются одновременно по многим разнородным признакам, то возможны и комбинированные варианты, например, электрошлаковое литьё в кокиль.
Литьё в песчаные формы
Литьё в песчаные формы — дешёвый, самый грубый, но самый массовый (до 75-80 % по массе получаемых в мире отливок) вид литья. Вначале изготовляется литейная модель (ранее — деревянная, в настоящее время часто используются пластиковые модели, полученные методами быстрого прототипирования), копирующая будущую деталь. Модель засыпается песком или формовочной смесью (обычно песок и связующее), заполняющей пространство между ею и двумя открытыми ящиками (опоками). Отверстия в детали образуются с помощью размещённых в форме литейных песчаных стержней, копирующих форму будущего отверстия. Насыпанная в опоки смесь уплотняется встряхиванием, прессованием или же затвердевает в термическом шкафу (сушильной печи). Образовавшиеся полости заливаются расплавом металла через специальные отверстия — литники. После остывания форму разбивают и извлекают отливку. После чего отделяют литниковую систему (обычно это обрубка), удаляют облой и проводят термообработку.
Новым направлением технологии литья в песчаные формы является применение вакуумируемых форм из сухого песка без связующего. Для получения отливки данным методом могут применяться различные формовочные материалы, например песчано-глинистая смесь или песок в смеси со смолой и т. д. Для формирования формы используют опоку (металлический короб без дна и крышки). Опока имеет две полуформы, то есть состоит из двух коробов. Плоскость соприкосновения двух полуформ — поверхность разъёма. В полуформу засыпают формовочную смесь и утрамбовывают её. На поверхности разъёма делают отпечаток промодели (промодель соответствует форме отливки). Также выполняют вторую полуформу. Соединяют две полуформы по поверхности разъёма и производят заливку металла.
Литьё в кокиль
Литьё металлов в кокиль — более качественный способ. Изготавливается кокиль — разборная форма (чаще всего металлическая), в которую производится литьё. После застывания и охлаждения, кокиль раскрывается и из него извлекается изделие. Затем кокиль можно повторно использовать для отливки такой же детали. В отличие от других способов литья в металлические формы (литьё под давлением, центробежное литьё и др.), при литье в кокиль заполнение формы жидким сплавом и его затвердевание происходят без какого-либо внешнего воздействия на жидкий металл, а лишь под действием силы тяжести.
Основные операции и процессы: очистка кокиля от старой облицовки, прогрев его до 200—300°С, покрытие рабочей полости новым слоем облицовки, простановка стержней, закрывание частей кокиля, заливка металла, охлаждение и удаление полученной отливки. Процесс кристаллизации сплава при литье в кокиль ускоряется, что способствует получению отливок с плотным и мелкозернистым строением, а следовательно, с хорошей герметичностью и высокими физико-механическими свойствами. Однако отливки из чугуна из-за образующихся на поверхности карбидов требуют последующего отжига. При многократном использовании кокиль коробится и размеры отливок в направлениях, перпендикулярных плоскости разъёма, увеличиваются.
В кокилях получают отливки из чугуна, стали, алюминиевых, магниевых и др. сплавов. Особенно эффективно применение кокильного литья при изготовлении отливок из алюминиевых и магниевых сплавов. Эти сплавы имеют относительно невысокую температуру плавления, поэтому один кокиль можно использовать до 10000 раз (с простановкой металлических стержней). До 45 % всех отливок из этих сплавов получают в кокилях. При литье в кокиль расширяется диапазон скоростей охлаждения сплавов и образования различных структур. Сталь имеет относительно высокую температуру плавления, стойкость кокилей при получении стальных отливок резко снижается, большинство поверхностей образуют стержни, поэтому метод кокильного литья для стали находит меньшее применение, чем для цветных сплавов. Данный метод широко применяется при серийном и крупносерийном производстве.
Литьё под давлением
ЛПД занимает одно из ведущих мест в литейном производстве. Производство отливок из алюминиевых сплавов в различных странах составляет 30—50 % общего выпуска (по массе) продукции ЛПД. Следующую по количеству и разнообразию номенклатуры группу отливок представляют отливки из цинковых сплавов. Магниевые сплавы для литья под давлением применяют реже, что объясняется их склонностью к образованию горячих трещин и более сложными технологическими условиями изготовления отливок. Получение отливок из медных сплавов ограничено низкой стойкостью пресс-форм.
Номенклатура выпускаемых отечественной промышленностью отливок очень разнообразна. Этим способом изготавливают литые заготовки самой различной конфигурации массой от нескольких граммов до нескольких десятков килограммов. Выделяются следующие положительные стороны процесса ЛПД:
· Высокая производительность и автоматизация производства, наряду с низкой трудоёмкостью на изготовление одной отливки, делает процесс ЛПД наиболее оптимальным в условиях массового и крупносерийного производств.
· Минимальные припуски на мехобработку или не требующие оной, минимальная шероховатость необрабатываемых поверхностей и точность размеров, позволяющая добиваться допусков до ±0,075 мм на сторону.
· Чёткость получаемого рельефа, позволяющая получать отливки с минимальной толщиной стенки до 0,6 мм, а также литые резьбовые профили.
· Чистота поверхности на необрабатываемых поверхностях, позволяет придать отливке товарный эстетический вид.
Также выделяют следующие негативное влияние особенностей ЛПД, приводящие к потере герметичности отливок и невозможности их дальнейшей термообработки:
· Воздушная пористость, причиной образования которой являются воздух и газы от выгорающей смазки, захваченные потоком металла при заполнении формы. Что вызвано неоптимальными режимами заполнения, а также низкой газопроницаемостью формы.
· Усадочные пороки, проявляющиеся из-за высокой теплопроводности форм наряду с затрудненными условиями питания в процессе затвердевания.
· Неметаллические и газовые включения, появляющиеся из-за нетщательной очистки сплава в раздаточной печи, а также выделяющиеся из твёрдого раствора.
Задавшись целью получения отливки заданной конфигурации, необходимо чётко определить её назначение: будут ли к ней предъявляться высокие требования по прочности, герметичности или же её использование ограничится декоративной областью. От правильного сочетания технологических режимов ЛПД, зависит качество изделий, а также затраты на их производство. Соблюдение условий технологичности литых деталей, подразумевает такое их конструктивное оформление, которое, не снижая основных требований к конструкции, способствует получению заданных физико-механических свойств, размерной точности и шероховатости поверхности при минимальной трудоёмкости изготовления и ограниченном использовании дефицитных материалов. Всегда необходимо учитывать, что качество отливок, получаемых ЛПД, зависит от большого числа переменных технологических факторов, связь между которыми установить чрезвычайно сложно из-за быстроты заполнения формы.
Основные параметры, влияющие на процесс заполнения и формирования отливки, следующие:
· давление на металл во время заполнения и подпрессовки;
· скорость прессования;
· конструкция литниково-вентиляционной системы;
· температура заливаемого сплава и формы;
· режимы смазки и вакуумирования.
Сочетанием и варьированием этих основных параметров, добиваются снижения негативных влияний особенностей процесса ЛПД. Исторически выделяются следующие традиционные конструкторско-технологические решения по снижению брака:
· регулирование температуры заливаемого сплава и формы;
· повышение давление на металл во время заполнения и подпрессовки;
· рафинирование и очистка сплава;
· вакуумирование;
· конструирование литниково-вентиляционной системы;
Также, существует ряд нетрадиционных решений, направленных на устранение негативного влияние особенностей ЛПД:
· заполнение формы и камеры активными газами;
· использование двойного хода запирающего механизма;
· использование двойного поршня особой конструкции;
· установка заменяемой диафрагмы;
· проточка для отвода воздуха в камере прессования;
Центробежное литьё
Центробежный метод литья (центробежное литьё) используется при получении отливок, имеющих форму тел вращения. Подобные отливки отливаются из чугуна, стали, бронзы и алюминия. При этом расплав заливают в металлическую форму, вращающуюся со скоростью 3000 об/мин.
Под действием центробежной силы расплав распределяется по внутренней поверхности формы и, кристаллизуясь, образует отливку. Центробежным способом можно получить двухслойные заготовки, что достигается поочерёдной заливкой в форму различных сплавов. Кристаллизация расплава в металлической форме под действием центробежной силы обеспечивает получение плотных отливок.
При этом, как правило, в отливках не бывает газовых раковин и шлаковых включений. Особыми преимуществами центробежного литья является получение внутренних полостей без при
|
|
Организация стока поверхностных вод: Наибольшее количество влаги на земном шаре испаряется с поверхности морей и океанов (88‰)...
История развития хранилищ для нефти: Первые склады нефти появились в XVII веке. Они представляли собой землянные ямы-амбара глубиной 4…5 м...
Двойное оплодотворение у цветковых растений: Оплодотворение - это процесс слияния мужской и женской половых клеток с образованием зиготы...
Эмиссия газов от очистных сооружений канализации: В последние годы внимание мирового сообщества сосредоточено на экологических проблемах...
© cyberpedia.su 2017-2024 - Не является автором материалов. Исключительное право сохранено за автором текста.
Если вы не хотите, чтобы данный материал был у нас на сайте, перейдите по ссылке: Нарушение авторских прав. Мы поможем в написании вашей работы!