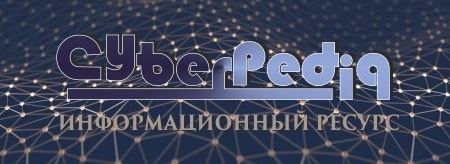
Двойное оплодотворение у цветковых растений: Оплодотворение - это процесс слияния мужской и женской половых клеток с образованием зиготы...
Общие условия выбора системы дренажа: Система дренажа выбирается в зависимости от характера защищаемого...
Топ:
Установка замедленного коксования: Чем выше температура и ниже давление, тем место разрыва углеродной цепи всё больше смещается к её концу и значительно возрастает...
Устройство и оснащение процедурного кабинета: Решающая роль в обеспечении правильного лечения пациентов отводится процедурной медсестре...
Когда производится ограждение поезда, остановившегося на перегоне: Во всех случаях немедленно должно быть ограждено место препятствия для движения поездов на смежном пути двухпутного...
Интересное:
Уполаживание и террасирование склонов: Если глубина оврага более 5 м необходимо устройство берм. Варианты использования оврагов для градостроительных целей...
Национальное богатство страны и его составляющие: для оценки элементов национального богатства используются...
Принципы управления денежными потоками: одним из методов контроля за состоянием денежной наличности является...
Дисциплины:
![]() |
![]() |
5.00
из
|
Заказать работу |
Содержание книги
Поиск на нашем сайте
|
|
Методика расчета себестоимости изготовленной или восстановленной детали.
Основной экономический показатель ремонтного производства – это себестоимость ремонта (машины, агрегаты, узлы и т.д.).
Себестоимостью называется затраты предприятия, приходящиеся на единицу выпускаемой продукции (отремонтированная машина, агрегат и т.д.).
Для определения себестоимости ремонтных работ проводят калькуляцию всех затрат.
Под калькуляцией понимают исчисление всех видов затрат на выпуск единицы продукции (одной машины). Себестоимость ремонта машины (С) складывается из прямых затрат и косвенных расходов (накладных):
С = П + Н,
где П – прямые затраты;
Н – накладные расходы.
«П» Прямые затраты – которые расходуются для ремонта данной машины.
К ним относятся:
а) оплата труда (зарплата) производственных рабочих (Зр);
б) налоги и отчисления на заработную плату (Пенсионный Фонд, страхование и т.д.) (Нз);
в) приобретение ремонтных материалов (Мз);
г) технологическое топливо (Рт);
д) электрическая энергия (Рэ);
ж) приобретение запасных частей и агрегатов (Зп);
з) оплата стоимости ремонта агрегатов, отремонтированных на стороне (Зст). Тогда:
П = Зр + Нз + Мз + Рт + Рэ + Зп + Зст.
«Н» Накладные расходы – это расходы, идущие на обеспечение ремонтного производства. Они складываются из цеховых расходов (Нрц), общезаводских (Нрз), внепроизводственных (Нрв):
Н = Нрц + Нрз + Нрв.
Особенности сварки деталей из алюминиевых сплавов электросваркой.
Детали из алюминия и алюминиевых сплавов характеризуются малой плотностью, сравнительно высокой прочностью, хорошей обрабатываемостью и способностью легко деформироваться. Поэтому они нашли широкое применение в авиации и судостроении, строительстве, транспортном машиностроении в производстве химической аппаратуры.
|
Особенности сварки деталей из алюминиевых сплавов газосваркой.
При сварке алюминиевых сплавов рекомендуется применять пламя газовой смеси О2: С22
Для защиты металла от окисления и удаления окислов с кромок свариваемых деталей применяют специальные флюсы. Наиболее распространен флюс АФ-4А состава: 28% NaС1, 50% КС1, 14% ZiСl, 8% NaF. При сварке флюс вводится или с присадочным прутком, или предварительно наносится на кромки в виде пасты, разведенной в воде. Хранить флюс длительное время (более 8—10 ч) в разведенном состоянии нельзя. В качестве присадочного металла применяют сварочную проволоку из алюминия или его сплавов. Диаметр присадочной проволоки зависит от толщины свариваемого металла.
|
Регулировка развала колес.
Развал — это угол между вертикалью и плоскостью вращения колеса автомобиля и считается отрицательным, если колёса направлены верхней стороной внутрь или положительным, если верхней стороной наружу.
Переднее левое колесо (вид спереди автомобиля). Развал - это это разность расстояний Б и А. Если А больше Б, то это отрицательный развал. Если А меньше Б - развал положительный.
Для проверки развала колес нужно, чтобы давление воздуха в шинах колес было нормальным, диски колес не были погнуты, свободный ход рулевого колеса должен соответствовать норме. Перед проверкой развала убедитесь в исправности шарниров рычагов передней подвески, шаровых опор передней подвески, штоков амортизаторов.
Развал регулируется изменением числа прокладок между осью нижнего рычага и поперечиной или поворотом эксцентрика на передней стойке. Также существуют для отечественных автомобилей пластины развала задних колес.
Назначение ГРМ.
Газораспределительный механизм (сокращенное наименование – ГРМ) предназначен для обеспечения своевременной подачи в цилиндры двигателя воздуха или топливно-воздушной смеси (в зависимости от типа двигателя) и выпуска из цилиндров отработавших газов. Данные функции реализуются за счет своевременного открытия и закрытия клапанов.
На самых распространенных четырехтактных поршневых двигателях внутреннего сгорания применяются клапанные газораспределительные механизмы, поэтому устройство ГРМ рассмотрено именно на его примере.
Газораспределительный механизм объединяет клапаны с приводом и распределительный вал с приводом.
Замена зубчатого ремня ГРМ.
Ремень газораспределительного механизма располагается спереди двигателя и хорошо заметен. В некоторых моделях он устанавливается открыто, в некоторых – под крышкой, защищающей его и шкивы механизмов. В современных двигателях коленвал через ремень приводит в движение не только газораспределительную систему, но и многие другие устройства. Поэтому ремень проходит по сложному маршруту, для достижения максимальной компактности и оптимального натяжения он ограничивается регулируемыми валиками.
|
Для того чтобы снять ремень, необходимо ослабить подвижные валики, что снизит натяжение и позволит высвободить резиновую ленту, а на ее место установить новую. Далее нужно с помощью тех же валиков обеспечить максимальное натяжение ремня для обеспечения его наивысшей эффективности.
Следует отметить, что от состояния валиков и шкивов также во многом зависит работоспособность ремня и продолжительность его эксплуатации. Так что при обнаружении проблем иногда нужно менять и их. Для многих моделей автомобилей можно купить все валики сразу в комплекте с ремнем.
Замена цепи ГРМ.
Перед тем, как произвести замену цепи ГРМ, нужно с силового агрегата слить масло и охлаждающую жидкость. Также отсоединить кабели катушек и выкрутить свечи зажигания. Со стороны цепи авто нужно домкратом поднять переднюю часть авто.
Все навесное оборудование и приводные ремни с правой стороны (по ходу движения авто) требуется снять. После чего нужно открутить подушку крепления двигателя.
Следующей операцией по замене цепи ГРМ будет снятие клапанной крышки и шкива коленчатого вала. Сняв шкив, появиться доступ к кожуху привода. После этого нужно открутить крепление кожуха и извлечь его. Далее требуется выставить шестерню коленчатого вала и звездочки распределительных валов по меткам. Метки нанесены на шестерне, звездочках и самой цепи. Для этого нужно проворачивать коленчатый вал пока все метки не совпадут. Если этого не сделать, будет нарушено правильное функционирование газораспределительного механизма.
Чтобы заменить приводную цепь, ее для начала нужно послабить. Для этого потребуется открутить крепление натяжителя и успокоителей и извлечь их. Цепь провиснет, но снять ее будет пока невозможно. Но этого провисания будет достаточно, чтобы открутить и снять жидкостной насос.
Перед тем как снять старую цепь, следует еще раз проверить совпадение всех меток. После чего можно произвести замену цепи ГРМ. Устанавливать новую цепь нужно так, чтобы все метки совпали. Установив новую цепь и натянув ее, нужно еще раз покрутить коленвал, чтобы убедиться, что метки совпадают. Если все нормально и метки совпали, значит, замена цепи привода ГРМ проведена правильно, и двигатель можно собирать обратно.
|
Ремонт коленчатых валов.
Коленчатый вал,— одна из основных деталей двигателя, определяющая вместе с другими деталями цилиндропоршневой группы его ресурс. Ресурс коленчатого вала характеризуется двумя показателями: усталостной прочностью и износостойкостью. При эксплуатации двигателя в результате действия высоких и непостоянных динамических нагрузок вал подвергается кручению и изгибу, отдельные поверхности (шатунные и коренные шейки и др.) — изнашиванию. В структуре металла накапливаются усталостные повреждения, возникают микротрещины и другие дефекты.
Долговечность коленчатого вала автотракторного двигателя зависит от целого ряда конструктивных, технологических и эксплуатационных факторов. Определяющее влияние оказывают такие параметры, как жесткость коленчатого вала и его опор, остаточный прогиб вала в результате релаксации напряжений черновой и чистовой правки, метод обработки (упрочнения) галтелей, режимы нагружения двигателя, состояние смазки.
У четырехтактных четырехцилиндровых двигателей с пятиопорным коленчатым валом коренные подшипники по степени нагружения можно разделить на две группы. К первой группе относят первый, третий и пятый подшипники, ко второй — четвертый и второй. Наибольшие нагрузки испытывают нижние вкладыши подшипников второй группы. Шатунные подшипники нагружены одинаково у всех цилиндров. При работе двигателя минимальная толщина масляного слоя в соединениях (рис. 4.21) зависит от зазора в подшипнике и относительного эксцентриситета
С увеличением относительного эксцентриситета значение минимального зазора в соединении (минимальной толщины масляного слоя) уменьшается.
Установлено, что при обкатке двигателя после ремонта температура масла не должна быть выше 85...90 °С во избежание возможного задира поверхностей трения. У форсированных двигателей в силу большей нагруженности и шатунных подшипников значения относительного эксцентриситета выше, чем у обычных, что предъявляет более высокие требования к качеству ремонта коленчатых валов, так как критическая толщина масляного слоя (допустимое значение) тем меньше, чем выше точность обработки вала и ниже шероховатость поверхности шатунных и коренных шеек.
Режимы пуска и интенсивного разгона двигателя наиболее опасны для коренных и шатунных подшипников коленчатого вала. В эти периоды минимальный зазор в подшипниках не превосходит. 2...3 мкм, что при недостаточной смазке вызывает интенсивное изнашивание деталей соединений. Для улучшения условий смазки подшипников в периоды пуска и разгона форсированные двигатели СМД-62 и СМД-64 оборудуют насосами предпусковой прокачки масла.
|
Ремонт водяной помпы.
Помпа, она же водяная помпа двигателя автомобиля — это насос создающий принудительную циркуляцию охлаждающей жидкости в системе охлаждения ДВС. Предназначается водяной насос для организации круговорота антифриза или другого состава в системе охлаждения. Неисправность помпы ведет к серьезному нарушению внутреннего теплового режима двигателя, из-за чего он довольно быстро «закипает».
Доводить до этого нельзя, поэтому чтобы удостовериться, что помпа двигателя работает, нужно периодически слушать и осматривать мотор, чтобы вовремя выполнить ремонт или замену вышедшего из строя узла.
Конструкция водяной помпы
Устройство помпы в большинстве автомобилей очень похожее, особенно это касается отечественных машин. И искать, где находится помпа, долго тоже не придется, так как она приводится в действие ремнем ГРМ и располагается возле радиатора.
Конструктивно помпа выглядит следующим образом: в крышке крепится вал. На него насажена крыльчатка, движение которой инициирует перемещение жидкости в системе. С другой стороны вала монтируется приводной шкив, и в некоторых моделях автомобилей еще вентилятором. Через ремень ГРМ и приводной шкив на вал передается энергия вращения двигателя, вал приводит в действие крыльчатку и вся система работает.
Устройство помпы.
Между корпусом и крыльчаткой монтируется сальник, с износом которого связаны многие проблемы помп. Если этот сальник плохой, антифриз или тосол постепенно просачивается в полость к подшипникам, вымывая их смазку. Из-за этого подшипники начинают работать гораздо громче и быстро изнашиваются, что ведет к заклиниванию помпы.
Ремонт водяной помпы
Помпа двигателя является ремонтопригодным разборным узлом. Здесь есть возможность заменить как весь механизм, так и отдельные его элементы, например подшипники. То, что помпа автомобильная не обязательно должна заменяться полностью, не может не радовать, поскольку это позволяет существенно удешевить ремонт. Правда, доступ к этому узлу для его частичной или полной разборки бывает затруднен. Так, в некоторых моделях автомобилей для этого необходимо частично откручивать подушки двигателя, работая снизу из смотровой ямы. Очень часто замена помпы производится при каждой второй замене ремня/цепи ГРМ, но при возникновении симптомов неисправности водяного насоса меняют и раньше, все зависит от качества детали и уровня выполнения работы при предыдущей смене привода ГРМ и самой детали.
Контроль состояния ГБЦ
· По сути, в ГБЦ не так уж и много основных параметров, которые нуждаются в проверке, прежде, чем вы начнете ремонт головки блока цилиндров. Поэтому давайте начнем искать типичные неисправности головки блока цилиндров.
· Нижняя плоскость ГБЦ. Проверяется при помощи лекальной линейки и набора щупов. Линейка кладётся по диагоналям головки на плоскости и при помощи щупа определяется толщина зазора. Если зазор более, чем максимально допустимый зазор в 0,05-0,06 мм, то требуется шлифовка головки блока цилиндров.
· Износ опорных шеек кулачкового вала и подшипников. Все диаметры измеряются микрометром и сравниваются с показателями максимально допустимых, для той или иной модели двигателя. По результатам измерений принимается решение о виде ремонта или замены деталей. Не забываем визуально оценивать наружное состояние поверхностей. Они не должны иметь явных признаков механических повреждений: царапины, сколы, задиры, канавки и т.д.
Контроль износа стержней клапанов и втулок. Производится микрометром в нескольких контрольных точках стержня по окружности. Клапан меняется, если разница диаметров превышает максимально допустимые параметры определенные производителем. Если у вас отсутствует такой прибор, как нутромер, для определения изношенности направляющих втулок, то ее можно определить по люфту клапана (нового) во втулке. Как правило, втулки меняются на новые.
Износ таких деталей, как: сёдла, рычаги, коромысла, кулачки определяется визуально. Если фаска на клапане «провалена», но стержень в порядке, то её обрабатывают, и клапан может быть вновь использован.
Другие дефекты ГБЦ также можно определять визуально. Наличие на поверхности головки блока заусениц, засечек устраняется шлифовкой головки блока цилиндров для устранения негерметичного соединения ГБЦ с самим блоком.
Таким образом, ремонт головки блока цилиндров, мы с вами проводим одновременно с дефектовкой, как говорится, — по мере поступления неприятностей.
Ремонт блока цилиндров.
В процессе работы в блоке цилиндров появляются следующие дефекты:
износ, задиры и риски на зеркале цилиндров;
трещины цилиндров, водяной рубашки и головки цилиндров;
износ, трещины и раковины клапанных седел
поломка шпилек и болтов крепления головки цилиндров;
накипь в водяной рубашке;
нагар в головке цилиндров.
Под действием коррозии, повышенной температуры, трения поршней и поршневых колец стенки цилиндров приобретают овальную форму (эллипсность) в плоскости качания шатуна и конусность по длине цилиндра.
Такой износ происходит по следующим причинам.
1. При сгорании топлива в цилиндре газы прорываются в канавки поршневых колец и. с силой отжимают их к стенкам цилиндра; при этом сила давления колец по мере движения поршня вниз уменьшается, вследствие чего износ цилиндра в верхней части больше, чем в нижней (конусность); кроме того, условия смазки верхней части цилиндра из-за более высоких температур хуже.
2. Сила Р давления газов, действующая на поршень при рабочем ходе, разлагается на две составляющие: А (68, а), направленную вдоль шатуна, и Б, направленную перпендикулярно оси цилиндра и прижимающую поршень к левой стороне стенки цилиндра (если смотреть со стороны радиатора). При сжатии передаваемая от коленчатого вала шатуну сила также разлагается на две составляющие, из которых одна действует вдоль шатуна и сжимает рабочую смесь, а другая.прижимает поршень к правой стенке цилиндра (68,6). Боковые силы действуют также при тактах впуска и выпуска, но в меньшей мере. В результате действия боковых сил цилиндр изнашивается больше в плоскости качания шатуна и приобретает эллипсность. Более интенсивен износ левой стенки цилиндра вследствие того, что боковая сила при рабочем ходе наибольшая.
Кроме эллипсности, боковые силы вызывают и конусность, так как по мере движения поршня вниз они уменьшаются.
Риски и задиры на зеркале цилиндра образуются вследствие перегрева двигателя, недостатка смазки и ее загрязненности, недостаточного зазора
между поршнем и стенкой цилиндра, плохого крепления поршневого пальца и поломки поршневых колец.
Величину износов цилиндра (эллипсность и конусность) определяют индикатором.
Эллипсность цилиндра измеряют в поясе, расположенном на расстоянии 40—50 мм от верхней кромки цилиндра. Измерение производится в двух взаимно перпендикулярных плоскостях, имеющих износы: наименьший — по оси коленчатого вала и наибольший — в плоскости, перпендикулярной оси коленчатого вала. Разность размеров, показанных индикатором, есть величина эллипсности.
Для определения конусности индикатор перемещают вдоль цилиндра в плоскости, перпендикулярной оси коленчатого вала. Разность размеров в верхней и нижней частях цилиндра, показанных индикатором, есть величина конусности.
При измерениях индикатор нужно опускать строго по вертикали, не допуская его отклонений в стороны (69).
Если эллипсность превышает 0,04 мм, а конусность 0,06 мм и имеются риски и задиры, цилиндры необходимо ремонтировать.
При ремонте цилиндра увеличивают его диаметр до соответствующего ремонтного размера, затем устанавливают увеличенный поршень.
В зависимости от износа цилиндра применяют следующие
способы ремонта:
1) шлифование;
2) растачивание с последующей доводкой;
3) установку гильз (если износ цилиндра. превышает последний ремонтный размер).
Шлифование цилиндров производят на специальных внутришлифо- вальных станках. На этих станках шлифовальный камень устанавливают значительно меньшего диаметра, чем цилиндр. Шлифовальный камень имеет три движения: вокруг своей оси, со скоростью 2000—3000 об/мин, по окружности шлифуемого отверстия цилиндра со скоростью 200—300 об/мин и вдоль оси цилиндра.
Процесс шлифования цилиндров — сложный и длительный, особенно при необходимости снятия большого слоя металла. Поверхность цилиндра получается слегка волнистой и забивается наждачной пылью, которая проникает в поры чугуна, что в дальнейшем вызывает ускоренный износ поршневых колец и поршней. Шлифование цилиндров в настоящее время применяется редко.
Растачивание цилиндров производится на расточных станках стационарного или переносного типа. Вертикально-растбч- ной станок переносного тийа (70) прикрепляют при растачивании непосредственно к блоку цилиндров. При этом для растачивания первого и третьего цилиндров блока четырехцилиндрового двигателя станок укрепляют сверху блока болтами, пропущенными через второй цилиндр, а для растачивания второго и четвертого цилиндров — через третий. Перед окончательным закреплением станка на блоке его шпиндель центрируют четырьмя кулачками, раздвигаемыми конусом 12. Резец 10 шпинделя устанавливают на нужный размер по микрометру.
Вращение от электродвигателя 14 через червячную передачу 13 и вал передается на цилиндрические шестерни 2 и 3 и далее через второй вертикальный вал 4 на шпиндель, соединенный с валом посредством шпонки. После пуска электродвигателя включают автоматическую подачу гильзы 7 и производят растачивание цилиндра. По окончании растачивания гильза возвращается вверх при помощи рукоятки 8. Этот станок позволяет растачивать цилиндры диаметром от 85 до 120 мм при длине растачивания 300 мм.
Недостатком указанного вида растачивания является необходимость доводки, так как на расточенной поверхности остаются следы резца.
Доводка цилиндров производится на специальных или вертикально-сверлильных станках, а также электродрелями при помощи доводочной головки (71), в которой устанавливают абразивные камни в виде брусков.
Для разводки брусков внутри полого валика помещен стержень, соединенный шарнирно с винтом установочных конусов головки. На верхнем конце стержня имеется установочный диск. Поворот диска на одно деление изменяет диаметр на 0,005 мм. Доводочная головка свободно вставляется в цилиндр, а при ее вращении шлифовальные бруски под действием центробежной силы расходятся и прижимаются плотно к стенкам цилиндра. Наибольшая разводка камнедержателей не превышает 1,5 мм; поэтому камнедержатели надо подбирать в соответствии с диаметром цилиндра. Скорость вращения головки 200—300 об/мин. Возвратно-поступательное движение вверх и вниз равно от 60 до 80 двойных ходов в минуту.
В процессе доводки головку и стенки цилиндра следует обильно поливать керосином, который смывает частицы металла и камня, а также охлаждает полируемую поверхность цилиндра.
По окончании обработки конусность и эллипсность цилиндра не должны превышать 0,02 мм.
Тонкое растачивание (алмазное) производится резцами из твердых сплавов при больших скоростях резания (150—200 м/мин) и малых подачах резца (0,01—0,02 мм) на один оборот шпинделя. Для растачивания используют специальные вер
тикально-расточные станки стационарного и переносного типов. После тонкого растачивания доводки не требуется.
Установка, гильзы применяется при износе цилиндра, превышающем последний ремонтный размер, или при наличии на его стенках глубоких рисок и задиров. При этом необходимо выполнить следующие операции.
1. Расточить цилиндр до диаметра, обеспечивающего установку гильзы, толщина стенок которой должна равняться 2—3 мм после ее растачивания под номинальный размер. В верхней части цилиндра делают кольцевую выточку под буртик гильзы.
2. Изготовить гильзу из материала, по возможности близкого к материалу цилиндра. По наружному диаметру гильза должна иметь припуск 0,05—0,15 мм на запрессовку.
3. Смазать гильзу и стенки цилиндра маслом и запрессовать гильзу при помощи гидравлического пресса под давлением 20—40 г; в процессе запрессовки наблюдать за показаниями манометра пресса и при резком повышении давления прессование прекратить, так как это указывает на перекос гильзы и может вызвать трещины в блоке.
При отсутствии пресса гильзы можно запрессовывать ручным приспособлением (72).
Затем следует расточить и прошлифовать гильзу под номинальный или уменьшенный размер цилиндра. Растачиванием под размер меньше номинального предусматривается возможность использования прошлифованных старых поршней.
Устранение трещин цилиндров и водяной рубашки
Трещины на стенках цилиндров и водяной рубашки являются следствием замерзания воды в блоке, заливки холодной воды в перегретый двигатель, неосторожного обращения с блоком при ремонте, запрессовки гильз с большим натягом.
Наличие трещин на стенке цилиндра сопровождается попаданием в него воды, что влечет за собой перебои в работе двигателя и падение мощности. При наличии трещин на стенке водяной рубашки получается подтекание воды по наружной поверхности двигателя. Трещины можно обнаружить путем испытания цилиндров и рубашки подкрашенной водой под давлением в течение 1—2 час. Цилиндры испытывают под давлением 20—25 ату а водяную рубашку — под давлением 2—3 ат.
Место и размер трещины определяются отложением красящего вещества.
Иногда удается установить наличие трещины и более простым способом. Для этого предполагаемое место трещины смачивают керосином, а затем насухо вытирают и посыпают сухим порошком мела. Через 1—2 часа керосин, проникший в трещину, выйдет на поверхность и даст отчетливую желтую полоску, по котор©й легко определить наличие и границы трещины.
Трещины цилиндра устраняют установкой гильз или газовой заваркой со стороны водяной рубашки (для этого специально вырезают кусок стенки водяной рубашки против трещины цилиндра); при этом подогревают весь блок цилиндров на древесном угле. Операция заварки — сложная и ответственная и поэтому применяется редко.
Трещины водяной рубашки заделывают штифтовкой, наложением заплат, металлизацией, замазкой и реже сваркой.
Штифтовка производится в следующем порядке.
1. Засверливают концы трещины сверлом 4,8 мм и просверливают отверстия по всей длине трещины на расстоянии 8 мм.
2. Нарезают резьбу в отверстиях метчиком б мм, затем завертывают в отверстия стержни из красной меди и обрезают их ножовкой так, чтобы о«и выступали на 1,5—2 мм.
3. Просверливают отверстия посредине между стержнями и нарезают в них резьбу, затем завертывают стержни, которые должны захватывать ввернутые раньше.
4. Зачеканивают шов легкими ударами молотка и опробуют блок водой под давлением 2—3 ат.
Наложение заплаты производят, когда имеются большие трещины или вывалившиеся куски. Для наложения заплаты нужно:
1) засверлить концы трещины сверлом 4—5 мм
2) вырезать заплату из мягкой стали толщиной 2—3 мм с таким расчетом, чтобы расстояние от трещины до края заплаты было не менее 20—25 мм;
3) по периметру заплаты просверлить отверстия сверлом 6 мм на расстоянии 10—15 мм одно от другого и раззенковать их.
4) наложить заплату на место трещины, легкими ударами пригнать ее по месту, пользуясь заплатой как шаблоном, накер- нить, просверлить отверстия в блоке сверлом 4,8 мм и нарезать в них резьбу метчиком 6 мм;
5) смазать заплату суриком, наложить на место и привернуть ее стальными винтами; при наложении заплаты на головку блока под заплату нужно установить свинцовую прокладку;
6) расчеканить края заплаты и опробовать блок водой под давлением 2—3 ат.
Металлизацией заделывают небольшие трещины, которые предварительно разделывают крейцмейселем, обезжиривают, после чего металлизируют посредством металлизатора.
Замазкой заделывают только небольшие трещины, причем замазку соответствующего состава (см. раздел «Вспомогательные материалы») наносят на подготовленную трещину и в течение 1—2 час. просушивают. Подготовка трещины заключается в зачистке ее и в обезжиривании
Мелкие волосяные трещины можно заливать соляной кислотой в смеси с нашатырем; при этом трещина затягивается отлагающейся ржавчиной.
Заварку трещины производят в следующем порядке:
1) расфасовывают трещину для получения скоса стенок под углом 45°;
2) медленно нагревают блок до температуры 650—700° в термической печи;
3) прогретый блок закрывают листовым асбестом, оставляя открытыми только места сварки;
4) заваривают трещины чугунными электродами;
5) помещают блок в печь и медленно его охлаждают (6—8 час);
6) производят механическую обработку шва, затем испытывают блок водой.
Замена лобового стекла.
Изначально вам нужно поставить свой автомобиль на ровной площадке. При возможности закройте кузов и салон защитной пленкой – это убережет его от возможных повреждений при рабочем процессе.
Подготовка поверхности.
Место для поклейки ветрового стекла автомобиля нужно подготавливать также согласно инструкции.
1) Избавьтесь от старого герметика полностью. Для этого воспользуйтесь ножом Так как молдинг вы купили новый, не бойтесь испортить этот.
2) Примерьте новое стекло, приложив его на свое будущее место. Сделайте небольшие пометки фломастером или маркером, если в этом есть необходимость. Некоторые модели оснащаются специальными упорами, благодаря которым установить стекло неправильно становится невозможно.
3) Если у вас не оказалось подставки для стекла, сделайте ее на капоте. Нужно лишь предварительно постелить на него что-нибудь мягкое.
4) Проведите обезжиривание поверхности. Вы можете заменить специальный обезжиривающий состав обычным «антисиликоном» (так называется антисиликоновый обезжириватель).
5) Нанесите грунтовку на место склеивания. Наносить нужно как на кузов, так и на стекло. Перед этим осмотрите место вклейки на наличие старого герметика еще раз. При наличии незначительных остатков герметик нужно обязательно удалить, а лишь потом наносить грунтовку.
Установка лобового стекла.
Для правильной установки нужно придерживаться следующей инструкции.
1) Разогрейте баллон с герметиком и тюбик с клеем в теплой воде. Можно сделать это при помощи фена.
2) Установите новый резиновый уплотнитель на стекло.
3) Отрежьте немного трубки-дозатора, оставив примерно 2 сантиметра.
4) Равномерно нанесите клей на поверхность кузова, хотя это можно делать и на контур стекла. Некоторые специалисты используют герметик для обработки. Но если у вас нет в наличии специальных присосок, тогда желательно проводить проклейку кузова. При этом сделанная полоса из герметика обязательно должна быть непрерывной с единственным стыком в центральной нижней части.
5) Нанеся клей, аккуратно приставьте подготовленное стекло в проем и слегка придавите его. Небольшого давления хватит для распространения герметика по всем пустотам.
6) Зафиксируйте стекло скотчем (для надежности).
7) Установите на место все детали, которые вы перед этим снимали. Не забывайте о солнцезащитных козырьках!
8) Следите за тем, чтобы не было лишних вибраций (не хлопайте громко дверями или капотом), поскольку это может повлечь за собой смещение стекла.
9) Оставьте автомобиль на сутки. За это время герметик полностью застынет.
10) Через сутки помойте лобовое стекло и всю переднюю часть автомобиля. Но перед этим нужно снять скотч. Проведите визуальный осмотр на качество получившегося шва. При обнаружении нарушения герметичности проклейте то место, как с наружной стороны, так и с внутренней. Лишь по достижению 100-процентной герметичности можно считать работу выполненной.
Лишь правильное выполнение всех инструкций и указаний обеспечит положительный результат. Разумеется, при работе могут допускаться мелкие ошибки, от которых не застрахован никто, но главное – это осваивать новые вершины по ремонту автомобиля!
Типы сварки
В кузовном ремонте чаще всего применяют электрическую сварку полуавтоматом. Но, до сих пор, в некоторых случаях, применяется и газовая сварка, либо контактно-точечная.
Контактная точечная сварка
Точечная сварка осуществляется сильным прижатием электродов аппарата к металлу кузова и комбинацией интенсивного нагрева, создаваемого очень высокой силой тока за короткий интервал времени. Металл панелей кузова расплавляется в одной точке и происходит сваривание.
Преимущество точечной сварки в быстроте действия, аккуратности получаемых сварных точек и прочности соединения.
Современные легковые автомобили имеют от 3000 до 4000 сварных точек, которые соединяют отдельные детали кузова в одну конструкцию.
Есть аппараты для точечной сварки, используемые в кузовном ремонте, электродами которых не нужно сжимать область сварки. Сила прилагается только к одному листу металла, а второй лист касается первого листа и подключён к массе. Такой аппарат удобно применять, когда невозможен доступ к обратной стороне металла, к которому приваривается другая металлическая панель.
Точки контактной сварки часто не защищены от коррозии, потому что места между соединёнными панелями, подвержены притягиванию влаги. Эта проблема усугубляется тем фактом, что при воздействии точечной сварки, в местах нагрева испаряются все элементы обработки металла, такие как оцинкованное покрытие. Эта проблема уменьшается при применении специального сварочного грунта между свариваемыми панелями. Такой грунт содержит высокий процент цинка. Он способен проводить ток. После воздействия точечной сварки ионы цинка защищают место сварки.
Третья группа показателей
Включает в качестве общего показателя отношение экономического эффекта от применения природоохранных мероприятий к общей величине затрат на их проведение и совокупность частных показателей.
К ним относятся:
§ доля капитальных затрат на природоохранные мероприятий в общем объеме капитальных затрат предприятия;
§ доля текущих затрат на природоохранную деятельность в общем объеме текущих затрат предприятия;
§ доля затрат на охрану воздушного бассейна в общем объеме затрат на природоохранную деятельность;
§ доля затрат на охрану и рациональное использование водных ресурсов в общем объеме затрат на природоохранную деятельность;
§ доля затрат на уничтожение и обезвреживание твердых и жидких отходов в общем объеме затрат на природоохранную деятельность;
§ доля затрат на разработку и внедрение прогрессивных технологий (малоотходных, безотходных, бессточных и т.п.) в общих затратах на НИОКР;
§ доля затрат на оплату услуг сторонних организаций на природоохранную деятельность в общем объеме этих затрат предприятия.
Составление экологического паспорта является достаточно сложной процедурой, поэтому обычно он составляется не самим предприятием, а по его поручению коммерческой организацией, имеющей соответствующую лицензию. Затем паспорт представляется в районное отделение охраны окружающей среды и природных ресурсов для проверки расчетов и согласования, после чего он направляется в региональное отделение Госкомэкологии для получения разрешения на выбросы (сбросы) указанных в экологическим паспорте объемов загрязняющих веществ.
Работа по составлению экологического паспорта оплачивается предприятием по договоренности с коммерческой организацией. При выдаче разрешения на выбросы (сбросы) загрязняющих веществ региональное отделение Госкомэкологии получает от предприятия сумму в размере 10% договорной стоимости составления экологического паспорта коммерческой организацией.
Экологический паспорт подписывается руководителем предприятия и руководителем районной организации охраны окружающей среды и природных ресурсов. В последующем этот документ уточняется, в него вносятся необходимые изменения.
Классификация отходов
Отходы произво
|
|
Индивидуальные очистные сооружения: К классу индивидуальных очистных сооружений относят сооружения, пропускная способность которых...
Папиллярные узоры пальцев рук - маркер спортивных способностей: дерматоглифические признаки формируются на 3-5 месяце беременности, не изменяются в течение жизни...
Двойное оплодотворение у цветковых растений: Оплодотворение - это процесс слияния мужской и женской половых клеток с образованием зиготы...
Автоматическое растормаживание колес: Тормозные устройства колес предназначены для уменьшения длины пробега и улучшения маневрирования ВС при...
© cyberpedia.su 2017-2024 - Не является автором материалов. Исключительное право сохранено за автором текста.
Если вы не хотите, чтобы данный материал был у нас на сайте, перейдите по ссылке: Нарушение авторских прав. Мы поможем в написании вашей работы!